Spanning 305 feet across the I-15 freeway, the 17-foot-wide Utah Valley University Bridge soars up to 35 feet above ground and provides access to and from campus for up to 6,000 students a day. The structure includes a pedestrian path, bicycle lanes, and elevators to make it ADA-compliant, in addition to a radiant-heated deck to keep snow and ice off the walkway during the winter months.
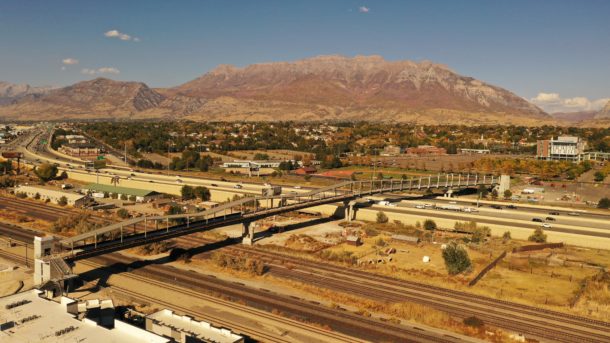
When the project first began, the university and the Utah Department of Transportation (UDOT) felt that a snow-melt system was imperative to ensure the safety of those crossing the bridge as well as those commuting underneath.
Aron Frailey of Thermal Engineering LLC recalls the day he first heard about the project. “My salesperson walked into my office and said, ‘How do you feel about quoting a snow-melt job for a thousand-foot bridge?’ Wow, I thought: A bridge? Can that even be done?”
Thermal Engineering began communicating with engineering firms, WSP and Kraemer, submitting load calculations based on the engineer’s initial design concepts. However, it took some time for the project to gain traction.
“Looking at the project in its initial stages on paper, it was difficult to see how we would do it,” says Frailey. “Even with 3D models, we struggled to understand how we would thread roughly 2,000 feet of pipe through all the girders of this bridge structure. There is a whole steel truss we had to work around and through, and I feared it could be a disaster from the standpoint of safety.”
Changing the spec
Part of the challenge was the structure’s height. Then there was the original specification, which called for 4″ steel pipe for the hydronic distribution piping. Because a standard length in that diameter weighs more than a ton, it would require numerous installers and a lot of welding.
So, Thermal Engineering began investigating — and eventually recommended — PP-RCT as a worthy alternative. A non-corrosive polymer would be better able to withstand the salt and magnesium chloride Utah uses for snow and ice melting on its highways. Even with the bridge more than 30 feet in the air, this was a major concern, because the hydronic piping would be installed in the structure’s underside, facing fast-moving traffic below.
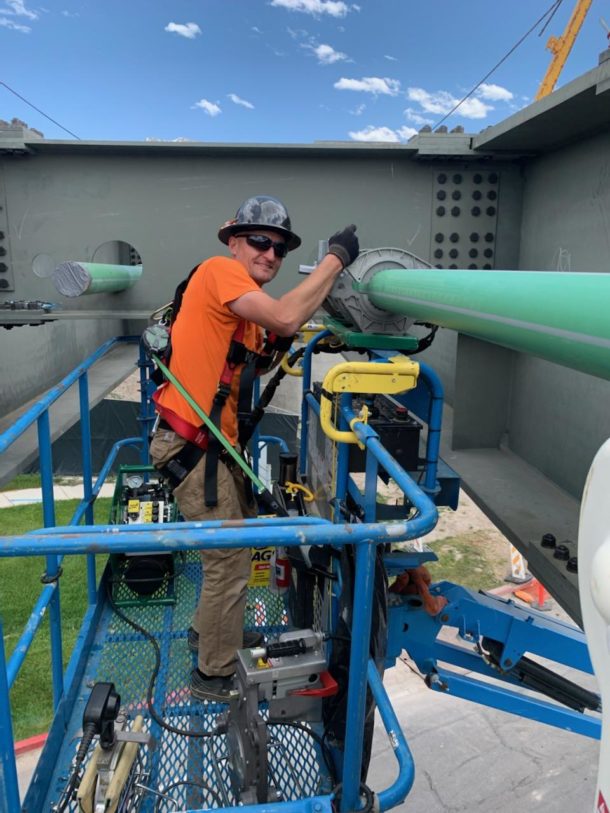
UVU Bridge in Orem, UT, Uponor PP-RCT install, Installed by Scott Layland with Thermal Engineering out of SLC, UT, photo by Stu Lorton
Moreover, PP-RCT would be far easier to handle and therefore less labor-intensive than steel. Shipped in 19-foot lengths, a stick of 4″ PP-RCT weighs a mere 63 pounds — a fraction of its steel counterpart. Plus, PP-RCT uses heat fusion for connections as opposed to welding with an open flame.
PP-RCT also offered one other critical advantage over steel: the ability to move in unison with the bridge. “The structure is intended to move as much as 18″ in every direction all the time — left to right, backwards and forwards, up and down,” says Frailey. “I was concerned about the joint integrity of a steel piping system with all that movement, and I really liked the flexibility of PP-RCT to handle it.”
For all these reasons, Thermal Engineering formally asked the engineer to change the specification to PP-RCT. After due consideration, the change was made.
“The engineer understandably had lots of questions,” says Frailey, who came to appreciate the “high level of trust” that flourished among his firm and Kraemer North America, WSP, and the rest of the build team.
“We sent samples and demonstrated how to make a heat-fusion connection,” he says. “We also cut some joints apart, so the engineer could confirm how completely the materials bonded. When we began reviewing the flow and weight characteristics, as well as the integrity of the joints and the ability to flex with the bridge, PP-RCT won the day.”
PP-RCT and PEX
The UVU project is the largest use of PP-RCT with 1,900 feet of 2½” to 4″ PP-RCT for supply-and-return piping, and it is also the first full-scale use of PP-RCT from Uponor North America. In addition to PP-RCT, the project also included 36,000 feet of ⅝” Wirsbo hePEX™, also from Uponor.
Frailey’s crew threaded the majority of the PP-RCT through the bridgeworks while it sat on the ground in the pre-fab steelyard, located roughly a mile and a half from the job site. Using a lift truck fitted with a winch for moving the pipe laterally, the team created a workstation for the McElroy Acrobat™ heat-fusion machine to connect the 19-foot lengths of PP-RCT.
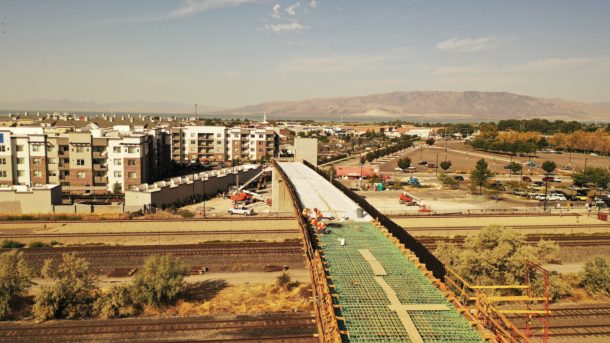
Although the heat-fusion process normally requires only two fitters, according to Frailey, “we needed a three-man team for this job” to reach the underside of the bridge. The first pipefitter’s task was to maneuver the 19-foot piece of PP-RCT off the ground and up into the bridge’s girder diaphragms.
Project superintendent Scot Layland was in an airborne workstation, hooking each length of pipe to the fusion machine and butt-fusing it to another length ahead of it in the line. Meanwhile, a third person operated the boom truck and the winch, pulling the pipe assembly through the bridge.
“Our men ran a rope through the girders and attached it to the pipe, pulling it through the girders while working on opposite ends of the bridge, rather than right over the highway,” says Frailey. Because of the PP-RCT’s weight, “the crane pulled the pipe easily — no big deal,” he says.
After the challenges of the hydronic piping, the PEX portion of the snow-melt job was smooth and easy. “For us, PEX for snow-melt systems is a known entity and installed without any problems,” he says.
Once the project was complete, Frailey was pleased with the results. “PP-RCT is an awesome product — the flow characteristics of the pipe, its light weight and flexibility, the ease of lifting and maneuvering it — all these benefits are huge compared with steel. In fact, we’re already using it on other projects.”
To learn more about Uponor PP-RCT, visit www.uponor-usa.com/pprct.
Join the conversation: