By Thomas Renner For some residential customers, contractors are discovering product selection comes down to warranty. Roman Nino found such an example when recommending products for a California homeowner. Nino, the plumbing wholesale branch manager at Hirsch Pipe & Supply, explained to a customer the benefit of the 12-year warranty on a model from American Read more
ShopTalk
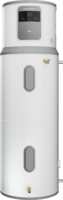
By Thomas Renner
For some residential customers, contractors are discovering product selection comes down to warranty. Roman Nino found such an example when recommending products for a California homeowner.
Nino, the plumbing wholesale branch manager at Hirsch Pipe & Supply, explained to a customer the benefit of the 12-year warranty on a model from American Standard Water Heaters. “If the unit leaks after 10 years, then the homeowner receives a new unit that could potentially last another 10 years,’’ he said. “With just one purchase, the homeowner could have a water heater that could last 20 years or more.”
Warranties differ widely in the water heater industry. Many wholesalers offer a “good, better, best” approach according to Chuck Rohde, Product Director for Ariston USA, which manufactures ASWH water heaters. “Contractors who are out looking at something more than a replacement are the ones who are killing it,’’ he said. “They’re trying to build a relationship with the client and gain their trust. The opportunity for a product with an extended warranty will give the customer longer peace of mind.”
When it comes to warranties, Nino said contractors can secure a lifetime customer by explaining the alternatives that best fit their budget. “Our mission is to provide the best customer service available to the homeowner,’’ Nino stated. “With the help of the manufacturer, sales team and contractor, we work together for the best outcome.”
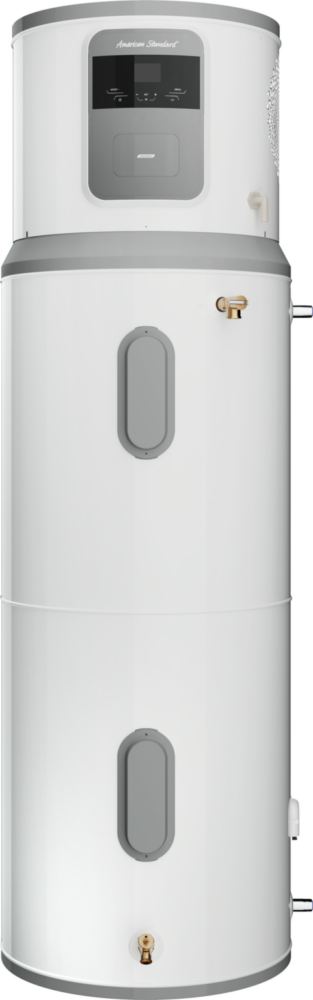
The American Standard Water Heaters Hybrid Heat Pump model comes with a 10-year limited
warranty, built-in leak detection and is available in 40-, 50-, 65- and 80-gallon capacities.
Establishing Purchase Confidence
As the wholesale branch manager at Hirsch’s location in Costa Mesa, Calif., Nino frequently finds himself explaining to customers about the advantages of a wide selection of water heaters. “Price point is a major concern for everyone,’’ he said. “An extended warranty backed by a great product gives the homeowner confidence with the purchase.”
According to Rohde, basic warranties on residential water heaters cover six years on parts. Most contractors, however, focus on replacing the balky unit with a model similar to the one currently in place.
“It’s an opportunity to sell a better model and gain the customer’s trust,’’ Rohde said. “It’s a good opportunity to build a relationship with them and discuss the different options with a customer. Most customers just pay the water bill and never worry about anything until they don’t get hot water.”
Rohde said wholesalers such as Nino can offer models that have different warranties, ranging from 6, 8, 10 and 12 years. Most heat pumps have a 10-year warranty.
American Standard Water Heaters has offered a model with a 12-year warranty for a number of years, according to Jason Alpert, Senior Warranty Manager at Ariston USA. “One of our biggest advantages is we use a thicker gauge steel for tank construction,’’ he said. “We’ve also refined our glass lining process. We also have great confidence in the choice of materials we use in the anode rode. We’re confident in the processes, the product and the way it’s designed.”
Communication is Key
One of the important roles for contractors is communicating with the homeowner to establish proper maintenance habits.
Flushing the tank every six months will allow fresh water to flow through and remove sediment buildup. Regular flushing can prevent issues and save on costly repairs or replacements. Failure to regularly flush the tank will eventually lead to sediment and sludge buildup at the bottom, and the debris will eventually cause tank corrosion.
“The sooner you are able to get the foreign material out of the tank, the better,’’ Alpert said. “The anode rod will help mitigate the effect of corrosion, but they have to be replaced over time.”
Water chemistry is different in every community and can even vary from home to home. “A lot of people focus on the hardness of water,’’ Alpert stated. “That’s an important factor, but there are other factors that come into play as well. As long as the water quality is government standard, homeowners should be OK. It can vary quite a bit in municipal systems.”
The most important task for a contractor is to inform homeowners about the importance and benefits of routine maintenance. “It’s critical to have a professional check out the water heater on an annual basis,’’ Alpert said. “When you’re dealing with gas water heaters, you want to have a professional make sure the combustion is working properly. You don’t want any buildup of materials.”
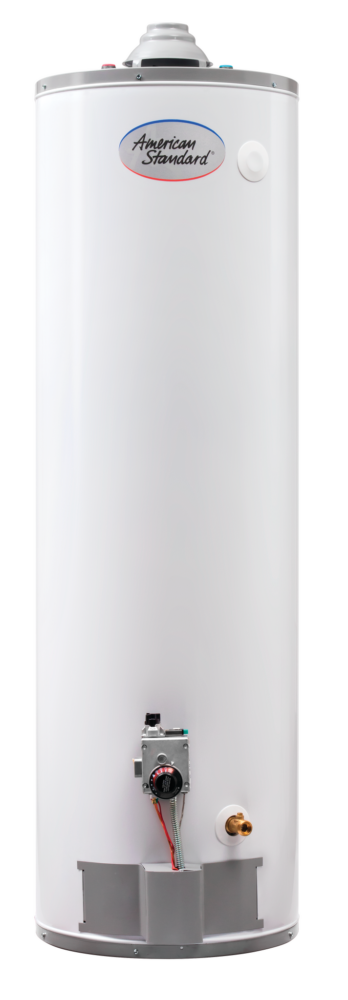
American Standard Water Heaters offers a tank warranty of up to 12 years on some products,
such as its Low NOx atmospheric unit, which also includes a 6-year warranty on parts.
Watch for Red Flags
For contractors and homeowners, there are some factors to make certain the warranty remains intact. The first step is to register the product with the manufacturer.
“One of the things we’ve done with American Standard Water Heaters is establish an online tool that makes it easier,’’ Alpert said. “We have a new tool designed to give customers the ability to check the warranty. Distributors can even send in warranty information digitally. Online registration with warranties eliminates the challenges that come with handwriting on forms.”
Rohde said most warranties are standard with minor nuances in language. Still, contractors and homeowners should pay attention to details. “For the most part the language is identical,’’ he said. “But there are some exclusions and modifications. It’s important to read the language, and in some cases, the warranty might be limited to the original owner. There may be some language around maintenance. The warranty is something that people need to pay attention to.
Thomas Renner writes on building, construction and other trade industry topics for publications throughout the United States.
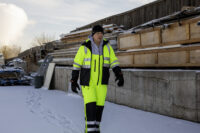
RefrigiWear, a 70-year pioneer in safety apparel and insulated PPE for winter workers, now delivers two high-visibility versions of its best-selling insulated softshell bib overalls. Available in high-visibility lime or high-visibility orange, the HiVis Insulated Softshell Bib Overalls are perfect for plumbers, pipefitters, tower climbers and road construction workers who need to stay warm and Read more
RefrigiWear, a 70-year pioneer in safety apparel and insulated PPE for winter workers, now delivers two high-visibility versions of its best-selling insulated softshell bib overalls.
Available in high-visibility lime or high-visibility orange, the HiVis Insulated Softshell Bib Overalls are perfect for plumbers, pipefitters, tower climbers and road construction workers who need to stay warm and visbile in cold, wet weather.
Ready for Rough Weather
HiVis Insulated Softshell Bib Overalls from RefrigiWear give workers the protection they need to get the toughest jobs done, even in temperatures as cold as -20°F. With a wind-tight and water-repellent outershell to guard against rain, sleet, snow and icy winds, these bibs help workers stay warm, dry and focused on the job.
Working through rough weather requires outerwear tough enough to take on the cold without falling apart. Abrasion-resistant patches and reinforcements help these insulated overalls stand up to tough work, especially when the job requires kneeling, squatting or climbing. Two rows of durable silver reflective tape are bonded, not stitched, on the legs to avoid snagging on equipment or unraveling with long use.
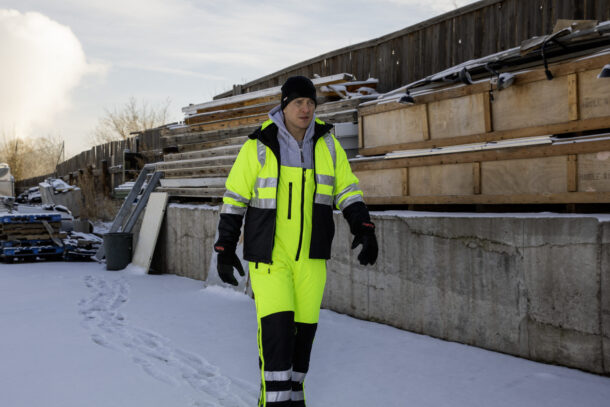
Warm, Comfortable & Functional
When the wind chill falls below freezing, most folks would rather head for home. For those who must stay and face the freeze, HiVis Insulated Softshell Bib Overalls deliver over 400 grams of lightweight, synthetic insulation. Plus, a silver heat-reflecting lining traps escaping body heat and reflects it back to the wearer for extra warmth and comfort.
Adjustable Y-back suspenders provide higher coverage for the back and torso. This design protects the vulnerable organs in the core from the cold without limiting range of motion in the shoulders, so workers can swing hammers, lift lumber or simply stretch their arms in complete comfort. Above-knee leg zippers make it quick and easy to step in or out of these overalls, so there’s no need to waste time removing boots when workers need to warm up or cool down quickly.
Safety Standards for Visibility
The high-visibility outershell materials and reflective silver tape on these bibs meet American and Canadian standards for safety on hazardous job sites. Both the high-visibility lime and high-visibility orange styles meet ANSI/ISA 107-2020 Class E and CSA Z96 Class 2, Level 2 standards.
Available in Extended Men’s Sizes
Available in extended men’s sizes from small to 5XL, HiVis Insulated Softshell Bib Overalls protect workers from cold, wet and windy conditions without compromising warmth, visibility or range of motion.
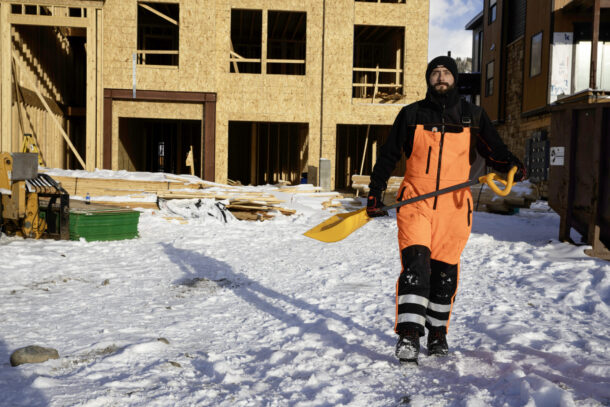
Complete Protection from Cold, Wet Winter Weather
When temperatures are freezing and falling fast, the secret to staying safe on the job is staying warm and staying visible. HiVis Insulated Softshell Bib Overalls coordinate perfectly with other garments, gloves and waterproof work boots from RefrigiWear, including the HiVis Insulated Softshell Jacket and several insulated hoodies and thermal sweatshirts in high-visibility colors.
Learn more about outfitting your team with weather-ready, high-visibility outerwear at pro.refrigiwear.com.
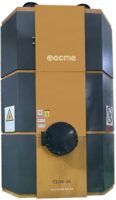
An international boiler expert helps industry professionals take advantage of high voltage electrode boilers’ virtually 100% efficient, zero-emission capabilities, providing guidance on selection and installation For consulting engineers tasked with planning, designing, and supervising construction projects for a wide range of industries, advanced electric boilers – particularly high voltage electrode boilers – offer numerous advantages Read more
An international boiler expert helps industry professionals take advantage of high voltage electrode boilers’ virtually 100% efficient, zero-emission capabilities, providing guidance on selection and installation
For consulting engineers tasked with planning, designing, and supervising construction projects for a wide range of industries, advanced electric boilers – particularly high voltage electrode boilers – offer numerous advantages over traditional fossil fuel burning boilers. Due to advances in technology, these boilers can match the capacity (up to 65 MW) and output (270,000 pounds of steam per hour) of traditional gas or oil-fired boilers in a much smaller footprint while converting almost all the energy to heat.
These zero-emission, high voltage electrode boilers are used in diverse environments for applications such as centralized heating, power plants, nuclear stations, swing-load balancing, solar/wind energy consumption, and fuel boiler replacement.
Today, there is growing interest in utilizing a new generation of these boilers as an environmentally friendly decarbonization solution. Companies across the globe are considering using electric boilers to become carbon neutral in alignment with COP26 UN Climate Change Conference targets. The transition to electric boilers also aligns with U.S. goals to achieve a carbon pollution-free power sector by 2035 and net zero emissions economy by 2050.
Electric boilers are emerging as more environmentally friendly solutions than traditional gas-fired units that emit not only the notorious greenhouse gasses carbon dioxide (CO2) and methane (CH4), but also dangerous nitrogen oxides (NOx), carbon monoxide (CO), and nitrous oxide (N2O), as well as volatile organic compounds (VOCs), sulfur dioxide (SO2), and particulate matter (PM).
“Communities and businesses appreciate the eco-friendly nature of ultra-efficient, electric boilers. Without combustion, these boilers are safe, clean, and emission free. The design eliminates many environmental issues associated with fuel burning boilers, such as fuel fumes, fly ash, and large obtrusive exhaust stacks,” says Robert Presser, Vice President of Acme Engineering, a manufacturer of industrial and commercial boilers.
However, the challenge for consulting engineers is that many have experience with gas-fired boilers but are less familiar with the selection and implementation of advanced electric boilers, especially the high voltage, high-capacity alternatives available today.
To bridge the knowledge gap, boiler technology expert Robert Presser explains what consulting engineers most need to understand about electric boiler technology, including its selection, implementation, and benefits. Acme, which has operations in the U.S., Canada, and Europe, provides state-of-the-art boilers and accessories for some of the world’s most renowned companies including Siemens, Toshiba, Bechel, PG&E, Power & Mine, and Hydro Quebec.
Types of Electric Boilers
The first factor to consider in selecting an electric boiler is how much capacity will be required by the user, business, or community.
According to Presser, lower voltage (480 KV) electric resistance heating element boilers are economical, compact, reliable sources to produce steam or hot water for industrial use. The units are well suited to supply these resources at lower capacities, from 9 to 3,600 kW.
However, there are design limitations when heating element boilers exceed 4 MW in capacity, as numerous flanges, elements, contactors, and fuses are typically necessary to function properly. The considerable amperage involved also requires expensive bars for distribution, step-down transformers, and large switch gear.
To avoid these complications at capacities of 4 MW or higher, high voltage jet type and immersed electrode boilers were developed.
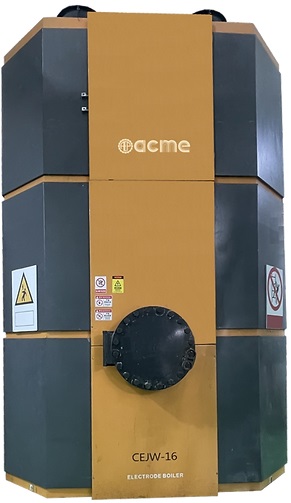
High Voltage Electrode Boilers
In the high voltage category, electrode boilers consist of two basic types: immersion and water jet.
In resistance element type boilers, current flows through a resistance wire, which generates heat. The heat is transferred through the element’s sheaf and into the water by conduction to produce hot water or steam.
“With the immersed electrode design, electric current is passed through the water from the electrodes to the counter electrodes [grounded via the vessel’s shell]. The more direct the exposure between counter electrode shield and the electrode, the greater the current draw [amperage] and the more power is produced in hot water or steam,” explains Presser.
Modern jet type electrode boilers utilize the conductive and resistive properties of water to carry electric current and generate steam. An AC current from the grounded central column to a minimum of one electrode box per phase, using the water as a conductor. Since the water has electrical resistance, the current flow generates heat directly in the water itself.
“The more current [amps] that flows, the more heat [BTUs] is generated, and the more steam is produced,” says Presser.
High voltage jet or immersed electrode boilers directly connect to high voltage supply lines from 4.16 KV – 25 KV. Hot water boilers are filled with treated water to create a closed loop system.
According to Presser, the maximum capacity of the boiler can be adjusted by varying the conductivity, which is determined by the temperature and boiler capacity. Typically, a conductivity monitor is installed in the piping and any adjustments are automatically made with chemical treatment.
When it comes to installation, consulting engineers need to consider whether there is sufficient high voltage power, and if a new transformer will be required.
“For these high voltage electrode boilers, the incoming voltage typically required by code is a 4-Wire, three-phase wye wiring configuration, and the phases must be balanced,” says Presser.
In addition, it is necessary to ensure that there is sufficient available space to bring in and install the electrode boilers. This includes determining that there is adequate access into buildings and elevators as well as enough clearance through hallways and doors. When space is limited, Acme’s Slim Series resistance boilers units are designed to produce ample hot water while easing conversion and installation with an ability to “squeeze through” narrow passageways and fit into smaller spaces without costly demolition.
The Benefits of Electric Boilers
For consulting engineers considering the use of electric boilers, there are numerous advantages over gas fired units. These include very high energy efficiency and output control, along with increased safety and other benefits.
Energy Efficiency
Although traditional gas fired boilers are familiar, the design is inherently less efficient than modern electric units. Within this category, the energy efficiency of electrode boiler technology offers extraordinarily efficient power-to-heat generation capability.
“With an electrode boiler, you get out of it what you put into it. Basically, you don’t have a decline in efficiency,” says Presser.
With electrode boilers, almost all the electrical energy is converted into heat with no stack or heat transfer losses. This level of efficiency is not achievable in fuel-fired steam boilers even when using an economizer.
In the case of Acme’s CEJS, which has a boiler capacity from 6MW to 68MW, the electrode boiler operates at distribution voltages from 4.16 to 25 KV. The unit is up to 99.9% efficient at converting energy into heat. The boiler can produce steam in capacities up to 270,000 pounds per hour, with pressure ratings from 75 PSIG to 500 PSIG.
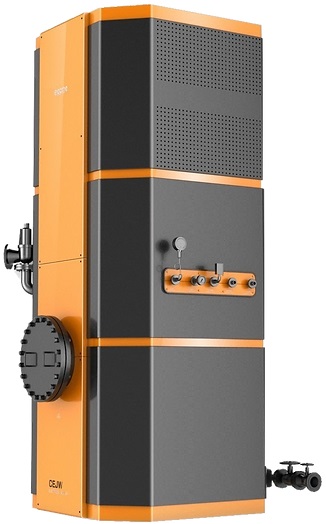
Output Control
High voltage electric boilers also offer superior control of energy output. The control system automatically monitors factors such as water level, steam pressure, conductivity, and electrical imbalances so energy input and adjustment is precise, and virtually immediate.
“In contrast, increasing or decreasing the temperature in a gas fired boiler is a slower process because it takes time for the heat in the boiler to rise or dissipate before reaching the targeted output,” says Presser.
As an example, advanced high voltage electrode steam boilers like Acme’s CEJS can control the capacity progressively from 0%-100% and have a 100% turndown ratio (the ratio between a boiler’s maximum and minimum output). Most gas boilers have a ratio of 10:1 or 5:1, which means the units require a much higher minimum output level to function and take a significant time to reach full capacity.
“With a 100% turndown ratio [in a high voltage jet-type electrode unit], you can leave the boiler in standby at low pressure and bring it to full capacity in about 90 seconds as needed, which no other boiler type can achieve today,” says Presser.
High voltage immersion steam boilers like Acme’s CEJWS can control the capacity progressively from 10%-100%.
“From hot stand-by, both the CEJS and the CEJWS steam boilers reach 100% capacity in one minute,” says Presser. He adds that stand-by insulation losses never exceed 10KW even for large boilers.
Increased Safety
High voltage electric boilers are inherently much safer to use than traditional, combustion-fueled boilers, which can emit harmful vapors, leak gas, and even cause explosions and fires.
“With gas burning boilers, any gas leak can increase the risk of an explosion wherever there are fuel lines, fumes, flames, or storage tanks. So, gas units must be continually monitored or periodically inspected,” says Presser.
In gas-fired boilers, explosions can result in the ignition and instantaneous combustion of highly flammable gas, vapor, or dust that has accumulated in a boiler. The force of the explosion is often much greater than the boiler combustion chamber can withstand. Minor explosions, known as flarebacks or blowbacks, can also suddenly blow flames many feet from firing doors and observation ports, seriously burning anyone in the path of a flame.
Natural gas-fired boiler emissions also pose potential hazards in the form of emissions. In addition, fossil fuel burning boilers can face potentially dangerous operational issues stemming from excessive heat accumulation.
Modern electric boilers eliminate many of these risks, so can dramatically improve both operator and environmental safety.
“With the jet type electrode boilers, there are no combustion hazards because there are no flames, fumes, fuel lines or storage tanks, which minimizes the risk of explosions and fires,” says Presser. In case of an electrical short, the breaker that protects the high voltage circuit trips in a matter of milliseconds, protecting the boiler and the electrical network. There is no chance of electrical mishap or fire from the boiler.
“Electric boilers, and specifically the electrode units, are inherently the safest boiler design today. These units do not need an operator because if anything goes wrong, the breaker trips, preventing further escalation of the issue,” says Presser.
Since the design does not rely on combustion, it does not create emissions that would endanger the operator or environment. In addition, the design eliminates common environmental problems associated with fossil fuel burning boilers such as fuel fumes, fly ash, and large obtrusive exhaust stacks.
Although consulting engineers are experts in their designated fields of expertise, keeping up to date with the latest developments in advanced electric boiler technology can provide significant advantages in providing hot water and steam for a variety of industrial purposes.
Understanding how to select, specify, and install electric boilers for the specific situation will conserve substantial energy, space, and resources compared to fuel-fired options. In addition, it will not only facilitate project success but also a safer environment that helps combat global warming.
For more info, contact Robert Presser at Acme Engineering via e mail: rpresser@acmeprod.com; phone: (514) 342-5656; or web: acmeprod.com/hv-electrode-boilers.
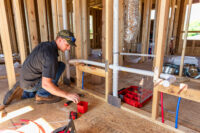
Written by Chris Carrier, RWC Senior Marketing Director The shortage of plumbers our industry is dealing with has become so serious, it’s making headlines in the business world. An article in Bloomberg Businessweek’s March 2024 issue puts the problem in a national context: “America’s Plumber Deficit Isn’t Good for the Economy.” The article elaborates with a slew of Read more
Written by Chris Carrier, RWC Senior Marketing Director
The shortage of plumbers our industry is dealing with has become so serious, it’s making headlines in the business world. An article in Bloomberg Businessweek’s March 2024 issue puts the problem in a national context: “America’s Plumber Deficit Isn’t Good for the Economy.” The article elaborates with a slew of stats that back up this subheading: “Young people are shunning an occupation that’s physically demanding and sometimes dirty, though well paid.
While the labor shortage isn’t new to those who have been in the industry long, it’s worth exploring the main cause of it and ways to get more people into the trade right now.

Understanding the plumbing recruitment crisis: The age factor
Age plays two roles in the plumber shortage. A large portion of the current plumbing workforce is nearing retirement age, and recruiting young people into plumbing is proving difficult. Although the recruitment pipeline is leaking at both ends, the jobs are there for the taking, with plenty of new opportunities opening. The latest data from the U.S. Bureau of Labor Statistics (BLS) projects there will be nearly 43,000 job openings for plumbers, pipefitters and steamfitters each year through 2032. These jobs mostly result from the need to replace workers who retire, change occupations or leave the workforce.
Knowing plumbing is one of the steadiest industries, how can plumbing business owners stay staffed with good plumbers? The truth is that it’s going to take some convincing.

Images courtesy of SharkBite Plumbing Solutions.
Repairing the leaky recruitment pipeline through education
If you run a plumbing company, the most concerning consequence of the labor shortage is the challenge of keeping enough good plumbers on your team. In the skilled trades, recruiting hinges on educating recruits. Raising awareness of opportunities is foundational. Many young Americans are simply unaware of the specialty options, job security and earning potential in plumbing. As an industry, we must invest more resources in promoting the plumbing profession. Just ask Mark Brown, a Philadelphia high school plumbing program instructor.
“There are so many people in our country who struggle with finding a suitable career path for them, and I believe it’s due to lack of exposure to career choices such as plumbing,” Brown said. After telling young people an opportunity exists, we need to convince them to explore it. To be persuasive, explain why plumbing is an excellent career option. Then dispel the myths and be open and truthful about the hard parts. Any recruiting efforts—whether joint or solo, online, printed or spoken—should start by selling the benefits, including:

Clint McCannon owns Cannon Plumbing in Braselton, Georgia.
Job security and stability
When you need a plumber, it’s rarely optional. Plumbing is an essential service with consistent demand, providing long-term job security and protection against economic downturns. For example, when the COVID pandemic put millions out of work, plumbers stayed on the job with a steady income.
“I was really nervous when COVID hit,” said Clint McCannon, owner of Cannon Plumbing in Braselton, Georgia. “I didn’t know what was going to happen. Our numbers were up over 35%, and it didn’t slow down. It sped up. Even when the economy is going down, if it’s something they can’t handle on their own, they’re going to call you.”
Given the plumber shortage, it’s highly unlikely that this career benefit will change anytime soon. Even as technological advances disrupt other trades, in plumbing, new technology tends to make the work easier rather than displacing the workers.
High earning potential
Plumbers enjoy competitive wages, and many have opportunities for overtime and bonuses. Their extent varies depending on the employer and specific job role. Even without pursuing overtime or bonuses, plumbers can enjoy a financially rewarding career free from the burden of student debt.
A high school diploma or equivalent is the standard education requirement for starting paid training or trade school. The BLS lists the 2023 median pay at $61,550 per year ($29.59 per hour), up from $60,090 in 2022 ($28.89 per hour), with plumbers at the high end of the spectrum earning a six-figure salary.
Geography greatly influences earnings, with average wages varying by state, based partly on the cost of living. According to Consumer Affairs, Illinois ranks highest with an annual average wage of $88,000, while Arkansas is at the bottom with plumbers earning $47,000 on average. Nationally, the top 10% of wage earners made more than $101,000 annually, and industry wages have been climbing steadily since at least 2012.
Paid training as an apprentice plumber
You don’t need any prior experience to start training to become a plumber, and once you apply for and secure an apprenticeship, it’s paid training on the job. Vocational-technical schools and unpaid pre-apprenticeships are the most common routes people take before getting on-the-job experience.
Choosing a paid plumbing apprenticeship over attending college with an unpaid internship can be a game-changer. With an apprenticeship, you’re earning money from day one while learning a valuable trade, rather than racking up student debt. You earn hands-on experience, real-world problem-solving skills and a direct path to a rewarding career in a high-demand field.
Apprenticeships also provide a structured learning environment where mentors are invested in your success, ensuring you gain both practical knowledge and industry credentials. For anyone looking to build a stable and prosperous future without the financial burden of college, a paid apprenticeship offers a practical and lucrative track.
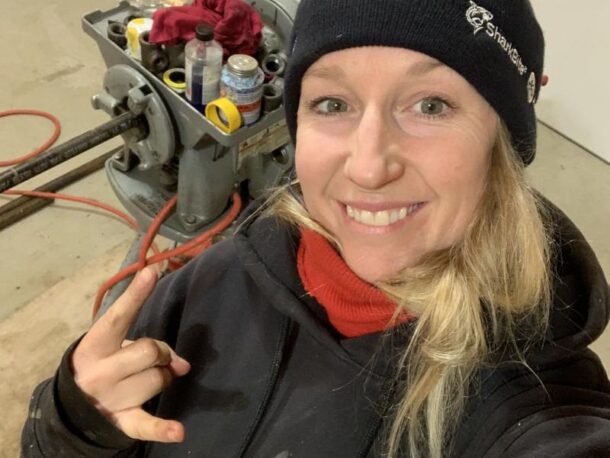
Leslie McGlenen owns Pipe Wench Plumbing & Heating.
Career advancement opportunities
The plumbing profession also offers clear pathways for advancement, including opportunities to become a well-paid master plumber, start your own business or move into management roles. After finishing a plumbing apprenticeship, career advancement in the U.S. plumbing industry typically follows a structured path.
First, you become a journeyman plumber, gaining more responsibilities and independence. With experience and further certification, you can advance to a master plumber, which opens doors to higher-paying jobs and leadership roles. Any apprentice can become a master in this trade if they’re dedicated, and it pays to work your way up. An HR technology company called PayScale reports that in 2023, the median pay of a master plumber went up to $82,700—a jump of 21% from 2022.
Some plumbers eventually become contractors or specialize in areas like pipefitting, leading to even more career opportunities. Some of the most profitable plumbing businesses are owned or managed by plumbers who started as apprentices. Lesley McGlenen owns and operates Pipe Wench Plumbing & Heating in British Columbia, Canada.
“I got a lot of experience as a young apprentice,” she said. “Most of the time, I was the only apprentice at this company, so I got to work under three skilled journeymen who did different parts of the job. Depending on who I was working under, I learned different techniques.”
Successful franchise owners like Lesley can expand their businesses, creating a comfortable income and good jobs.

Kim Yeagley owns Gold Canyon Plumbing in Gold Canyon, Arizona.
Job satisfaction and community impact
Plumbers play a vital role in maintaining public health and safety. Being an essential part of your community’s workforce provides a sense of pride and fulfillment for those who appreciate making a tangible difference in people’s lives, homes and workplaces.
“When you leave, you’ve fixed their problem, you’ve made their day. That’s a good feeling inside,” said Kim Yeagley, owner of Gold Canyon Plumbing in Gold Canyon, Arizona. Despite the occasional dirty conditions, the satisfaction of solving problems and providing essential services to your community is genuinely rewarding. And like other skilled trades, plumbers take pride in their craftsmanship and enjoy building something from scratch. As a plumber, you can also choose to prioritize family and personal time.
“I don’t live to work. I work to live,” said Russel Sweeney, owner of Sweeney Remodeling and Plumbing in Jacksonville, Florida. “Through the years, I’ve learned that there is a necessity for work-life balance.”
Flushing fears and reconfiguring perceptions of plumbing
While there are many benefits in plumbing, there are still a lot of misconceptions and valid concerns that must be addressed in recruitment, including:
Physical demands
Don’t sugarcoat it. Plumbing is physically strenuous, often involving heavy lifting, strong tool work, awkward positions and repetitive movements. But desk jobs aren’t for everyone either. Plumbing can be a great career fit for people who love working with their hands. Former plumbing apprentice Anna Pearson said an office job just wouldn’t suit her.
“Forty hours out of my life every single week, being stuck in a cubicle, it’s just my actual nightmare,” she said.
Modern equipment helps with the physically challenging aspects. Advancements in technology and tools have made most tasks easier and more efficient than in decades past. For example, push fittings like SharkBite Max make it easy for new plumbers to start repairing and reconfiguring pipes with minimal instruction, performing smaller jobs in just minutes. They also help plumbers get in and out of tight or uncomfortable spaces more quickly so they can put minimal strain on their bodies.

Russel Sweeney owns Sweeney Remodeling and Plumbing in Jacksonville, Florida.
Safety and working conditions
The job sometimes involves working in dirty and confined environments, which can be unappealing or seen as hazardous. Fortunately, plumbers of all types get paid to earn comprehensive safety training through their certifications that prepare them to handle potentially dangerous job site situations safely. Plus, safe working conditions are required by law. The Occupational Safety and Health Administration (OSHA) enforces federally mandated safety standards that plumbing employers must comply with, which apply to both service and commercial plumbers. Employers provide all the necessary protective gear and equipment to ensure safety and comfort on tough jobs, including water-proof gloves, knee pads, safety glasses, hard hats and respirators.
Serious injuries are very rare for plumbers, pipefitters and steamfitters. Nonfatal injuries are also exceptionally rare for both residential plumbers and commercial plumbers who work on new builds, even though working in people’s homes is generally considered safer than plumbing on a construction site. In 2022, BLS data shows that out of 865 reported fall injuries, including slips and trips, only 27 involved plumbers (3%). The BLS lumped plumbers in with HVAC contractors. This group had no reported injuries that year from exposures to harmful substances or environments, and no injuries caused by contact with objects or equipment.
Social stigma and perception
The reality is that many college graduates have student debt and still earn less than the plumber they call to fix their toilet, but there’s a strong societal push toward college degrees in high school, leading many young people to overlook the trades as they’re considering a career path. In the absence of hard facts, students often view trades like plumbing as a less prestigious career compared to white-collar jobs.
However, plumbers earn competitive salaries with excellent job security because they’re essential to our homes, businesses and critical infrastructure. Remind recruits that this trade offers opportunities for entrepreneurship and a stable, upward career path, with the added satisfaction of helping people every day. Another perk is that you can live almost anywhere and still have excellent job prospects.
Job security concerns
Some mistakenly perceive plumbing as less stable compared to careers in rapidly growing tech and service sectors where layoffs are actually far more common. Layoffs are very rare in plumbing, even during recessions, and the labor shortage shows that’s unlikely to shift.
“It’s a very recession-proof job,” Sweeney said. Research firm IBISWorld reports that “constant demand keeps direct competition low.” Industry analysts expect a steady demand for plumbing services in new construction, and IBISWorld states that “refurbishment and maintenance of aging plumbing systems have remained steady streams of income for independent plumbers and companies alike. This will not change in the near future.”
If you encounter stability concerns as you do outreach, set the record straight and back it up with facts. The U.S. Department of Labor provides a helpful resource with its Occupational Outlook Handbook for Plumbers, Pipefitters and Steamfitters. This periodically updated handbook answers every question a plumbing recruit is likely to ask.
Training requirements
Extensive apprenticeships and on-the-job training can deter those looking to enter the workforce quickly. Plumbing apprenticeships can indeed last up to 5 years, but they allow you to earn a living while gaining hands-on experience in the field, providing valuable training without the high costs of a traditional degree.
Another option is vocational-technical programs that fast-track your plumbing career, offering practical skills, recognized certifications and employment immediately after graduating.
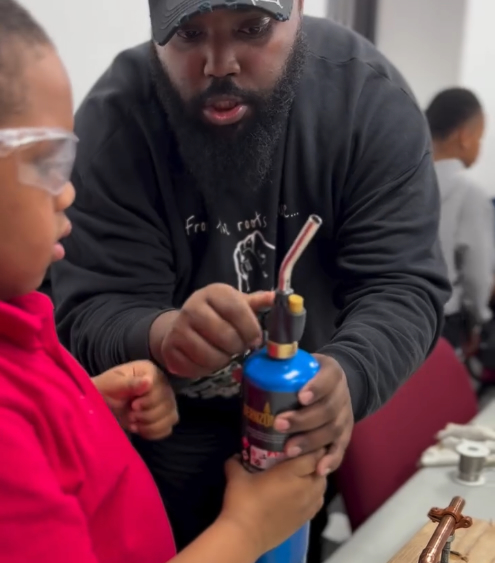
Mark Brown, a Philadelphia high school plumbing program instructor.
Take advantage of the facts
Whether it’s educational social media videos, partnering with trade schools or hosting open- house demonstrations in your community—whichever format, strategy or platform you choose for your recruiting efforts—take a fact-based approach. Reality is your ally in persuasion. With excellent job prospects and rising pay, it’s a great time to join the plumbing profession, and having the facts on your side can make recruiting a little easier. Take it from Pearson.
“I researched it for a few days, I saw nothing but good things,” the former plumbing apprentice said. “And so, I decided to go ahead and take the plunge.”
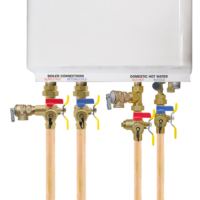
In a hydronic system, every installation is an opportunity to improve efficiency. The products you select for the job not only impact the installation of today but the performance of tomorrow. This is especially true when installing a boiler; the components you pair with the unit can mean the difference between a simple installation and Read more
In a hydronic system, every installation is an opportunity to improve efficiency. The products you select for the job not only impact the installation of today but the performance of tomorrow. This is especially true when installing a boiler; the components you pair with the unit can mean the difference between a simple installation and a smarter installation.
Auxiliary boiler accessories range in both form and function. The best products for the job should be designed to save time, space, and labor during installation. They should also provide controls to ease future maintenance and should protect the boiler and system components over time.
With these goals in mind, Webstone has developed the most complete selection of under boiler solutions available today. Its under boiler program is a single source for better installations, with products that also simplify and reduce the number of maintenance callbacks.
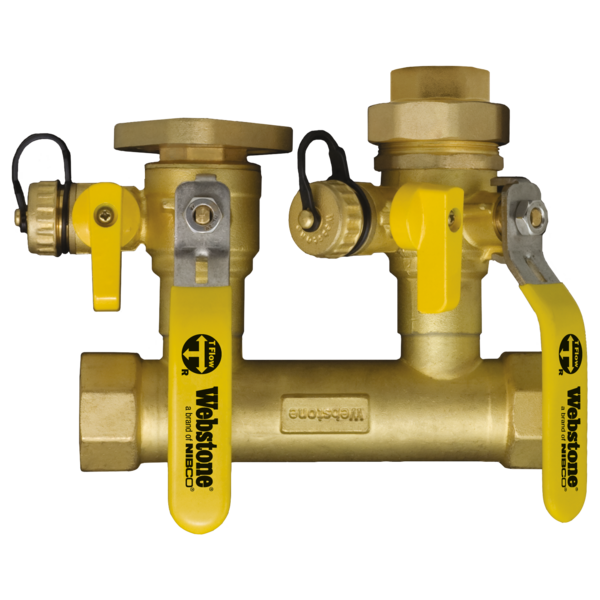
The Hydro-Core™ manifold simplifies the installation and service of the primary heating loop. This solution combines closely-spaced tees with isolation valves to achieve hydraulic separation for the heating loops, isolates the components within the loop, and purges the system. A T-Flow ball directs the flow into either the boiler or the drain, which can be configured in a number of ways to assist with purging, filling, and descaling/cleaning. Its compact, forged-brass body replaces up to 17 individual components, eliminates 16 leak paths, and saves over two hours of labor.
To improve overall system performance, the Air Separator uses a unique stainless-steel coalescing medium that captures both microbubbles and static air. The separated air collects in the top of the unit, where it forces a pin-guided float to drop down and open a vent. Once the air is released, the float rises once again and closes the vent. This reduces noise as well as wear on system components caused by trapped air in the pipes. The vertically mounted model is ideal for installing on the boiler outlet, where the air can be separated and vented before it reaches the rest of the system.
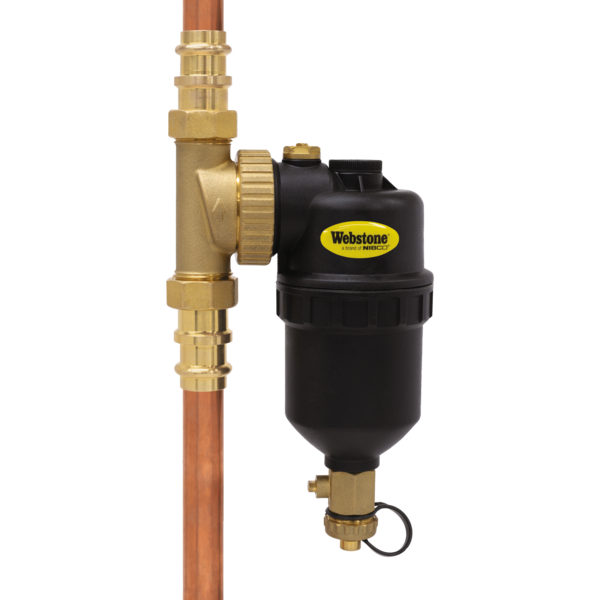
To protect the boiler from iron sludge that can accumulate in a hydronic system, consider the Magnetic Boiler Filter. Installed on the system return line, it captures ferrous and non-ferrous debris before it can reach the boiler using a high-powered 12,000 Gauss magnet and plastic filter. The drain makes it simple to remove accumulation, with a strapped cap that can be used to actuate the drain valve. A universal diverter allows the Magnetic Boiler Filter to be used in both horizontal and vertical piping orientations. The service tool is also included to help install and maintain the filter with ease.
Both the vertical mount Air Separator and Magnetic Boiler Filter are outfitted with removable G1 threaded end connections (available in sizes ¾” and 1”, with MIP, FIP, SWT, or Press ends), offering added versatility to any installation. These threads allow the installer to easily add isolation valves for future service, or a temperature gauge to verify boiler output right at the source.
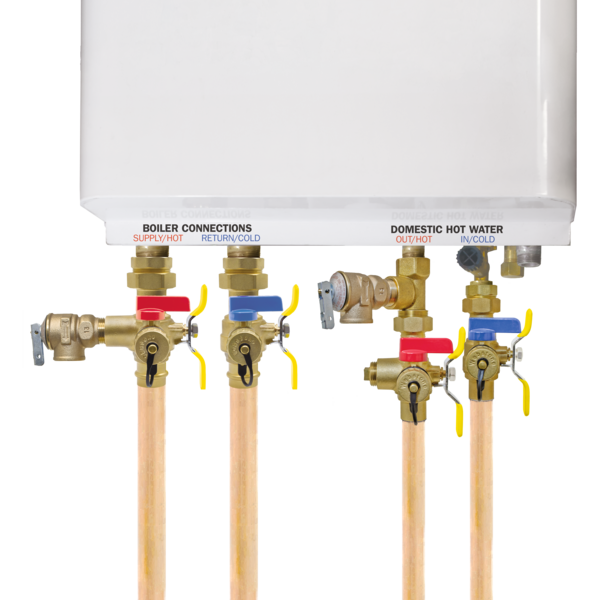
A full-featured under the boiler installation from Webstone requires no more than 22” of space and delivers cleaner, more professional-looking results. Solutions are also available for boilers with external pumps and combi domestic hot water connections from the E-X-P™ Series of Tankless Water Heater Service Valves. To find all of these products and more, visit www.webstonevalves.com.