Dozens of skilled trade workers from across Illinois recently gathered at United Association Local 149’s training center in Savoy, Illinois, for the prestigious Illinois Pipe Trades Association Committee on Training and Education (COTE) contest. Top apprentices, who earned their place by winning local competitions, put their expertise to the test through rigorous written exams and Read more
Industry Blogs

Dozens of skilled trade workers from across Illinois recently gathered at United Association Local 149’s training center in Savoy, Illinois, for the prestigious Illinois Pipe Trades Association Committee on Training and Education (COTE) contest.

Top apprentices, who earned their place by winning local competitions, put their expertise to the test through rigorous written exams and hands-on challenges. Competing in plumbing, welding, pipefitting, sprinkler fitting, and HVAC, they tackled complex projects and real-world scenarios, demonstrating the highest level of skill and craftsmanship.
“The statewide apprenticeship competition at Local 149’s newly expanded training center was a tremendous success, showcasing the talent of our apprentices and the strength of our commitment to training excellence,” said Matthew J. Kelly, Business Manager & Financial Secretary-Treasurer of Plumbers & Pipefitters Local 149. “Funded entirely by our dedicated members, our state-of-the-art facility ensures every apprentice receives top-tier education and hands-on experience. This competition is the pinnacle of their five-year journey, proving their expertise and preparing them for success as journeypersons. Local 149 is proud to invest in the future of our industry and the success of our apprentices.”

The event also drew strong industry support, with manufacturers like Milwaukee Tool and NIBCO backing the competition. “NIBCO was proud to sponsor the 2025 Illinois State Pipe Trades Apprenticeship Contest, continuing our strong partnership with UA plumber and pipefitter unions,” said Aaron Kilburg, NIBCO Commercial Sales Manager. “We support these skilled professionals with world-class products and training programs that advance craftsmanship, safety, and innovation across our industry. Congratulations to this year’s outstanding competitors and winners.”
The competition culminated in an awards ceremony at the I-Hotel in Champaign, where the top performers in each trade discipline were recognized. State champions will advance to the regional competition in Iowa, with hopes of earning a place in the international finals this summer.

Last year’s Illinois plumbing champion, Andrew Hall of Local 149, proved the strength of Illinois’ training programs by winning the international plumbing title—setting a high standard for this year’s competitors.
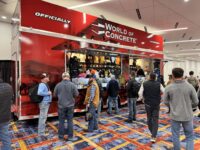
Mechanical Hub Media attended the World of Concrete (WOC) trade show in Las Vegas this week has been an enlightening experience, offering a comprehensive view of the latest advancements and trends in the concrete and masonry industries. Not too mention, it’s the show to see all the power tool manufacuters in one place, with their Read more
Mechanical Hub Media attended the World of Concrete (WOC) trade show in Las Vegas this week has been an enlightening experience, offering a comprehensive view of the latest advancements and trends in the concrete and masonry industries. Not too mention, it’s the show to see all the power tool manufacuters in one place, with their new product launches.
Held at the Las Vegas Convention Center from January 20 to 23, 2025, WOC 2025 marked its 51st anniversary, solidifying its reputation as the premier international event dedicated to these sectors.
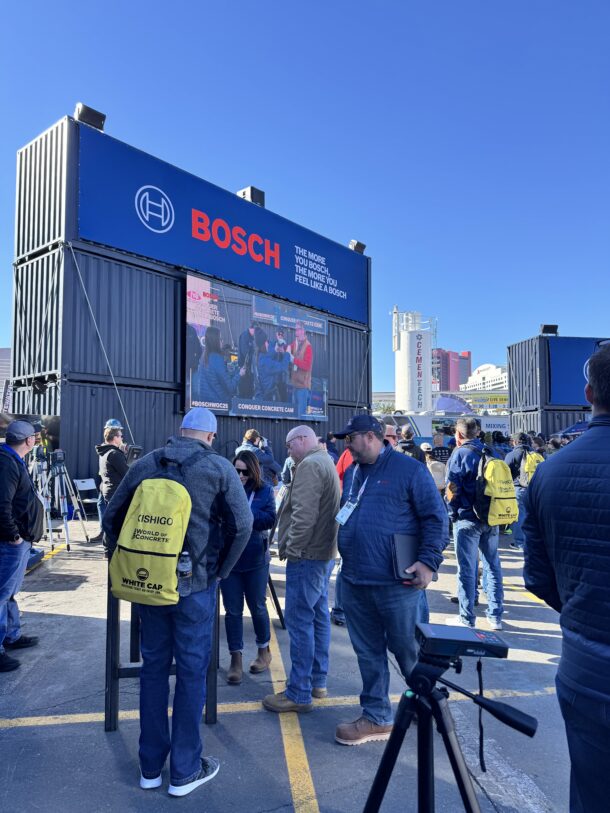
Event Overview
The event is structured into two main components:
- Education Sessions (January 20-23): These sessions provided in-depth knowledge on various topics, including new technologies, safety protocols, and business strategies. Industry experts led seminars and workshops, fostering a collaborative learning environment.
- Exhibits (January 21-23): The exhibition halls were bustling with over 1,500 exhibitors showcasing innovative products and services. From cutting-edge machinery to sustainable materials, the exhibits offered a glimpse into the future of the industry.
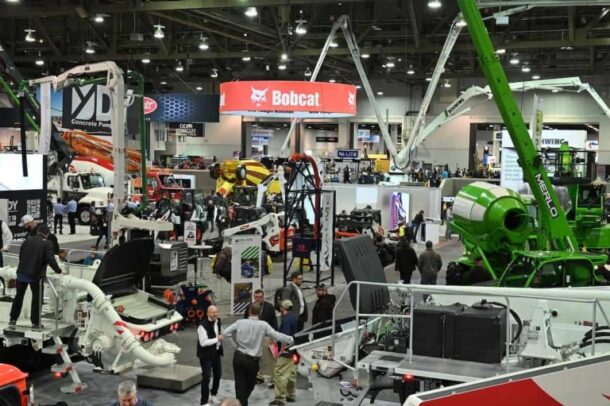
Key Highlights
- Innovative Product Launches: Many companies unveiled new products designed to enhance efficiency and sustainability. For instance, advancements in concrete admixtures promise to improve durability while reducing environmental impact.
- Live Demonstrations: The outdoor exhibit areas featured live demonstrations of equipment and techniques. Witnessing these applications in real-time provided practical insights into their benefits and implementation.
- Networking Opportunities: WOC facilitated connections among professionals from around the globe. Various networking events allowed attendees to exchange ideas, discuss challenges, and explore potential collaborations.
- Educational Seminars: Topics ranged from the integration of digital technologies in construction to the latest safety standards. These sessions were instrumental in broadening understanding and staying updated with industry best practices.
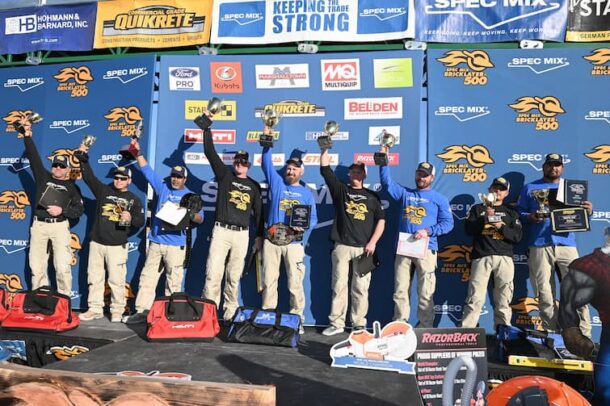
Conclusion
Attending the World of Concrete 2025 was a valuable experience, offering exposure to the latest industry innovations and fostering professional growth. The combination of educational sessions, product exhibitions, and networking opportunities provided a holistic view of the current and future state of the concrete and masonry sectors. For professionals committed to staying at the forefront of the industry, participation in WOC is highly recommended.
For more information on World of Concrete visit www.worldofconcrete.com.
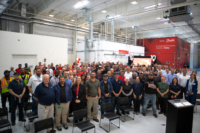
By Steffan Busch, Talent Acquisition Coach & Executive Recruiter You know you need people to grow your business. Everyone knows that. But hiring the right people for your open jobs requires a robust talent acquisition program. And not everyone knows that! If your talent acquisition program consists of posting jobs to Indeed for free and Read more
By Steffan Busch, Talent Acquisition Coach & Executive Recruiter
You know you need people to grow your business. Everyone knows that.
But hiring the right people for your open jobs requires a robust talent acquisition program. And not everyone knows that! If your talent acquisition program consists of posting jobs to Indeed for free and offering an employee referral bonus of a couple hundred dollars, you’re on the wrong end of the bell curve. A proper talent acquisition program is more than posting a free, bland job description on Indeed and praying for applicants. Moving your company to the right end of the bell curve requires an investment of time and money.
If you don’t like the idea of investing financial resources into talent acquisition, I hate to break it to you, but there’s already a financial cost.
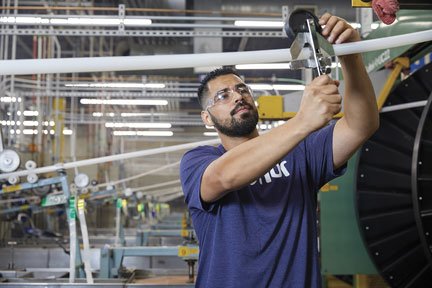
Consider the cost of being understaffed. Let’s look at plumbing and electrical service. Assuming a plumbing/electrical service technician is running three calls/day with an 85% conversion rate and an average ticket of $825, that comes out to $2,104 per day and $504,900 annually in missed potential revenue. And that’s for one service technician! Now let’s look at the cost of a single unfilled comfort advisor position. Three calls per day with a 50% conversion rate and $9,000 average ticket comes out to $13,500 per day. That’s $3,240,000 annually in missed potential revenue!
Now let’s consider the cost of losing people – the cost of turnover. Think about the cost of hiring the person who just left. Consider the cost of posting to job boards. Then add up pre-employment testing, interviewing time, drug test/background checks, and the time and administrative costs for onboarding the person who left. Think about their salary. Add up the base pay times the length of time they were on the job. Add bonuses/commissions, including sign-on bonuses. And don’t forget the cost of their health insurance, 401k, PTO, etc.
Now consider the cost of maintaining that person in the same job. What’s the cost of purchasing and maintaining uniforms, vehicles, tools, iPads, computers? How much did you invest in training them? Add that all up and you’ll come to a number that’s somewhere between six and fifteen times that person’s salary!
When it comes to hiring, your goal is to hire and retain as many high-performers as possible for your open roles. It’s critical to get it right the first time – you don’t want to have to keep going back to the drawing board. An intentional and fully developed talent acquisition program consists of the following components:
- Employer Value Proposition – What sets your company apart from the competition? Why should a high-performing HVAC installer leave their current company to work with you?
- Strategy – How are you going to broadcast your value proposition to the community?
- Process – Do you have a clearly defined, intentional, and effective hiring process? What’s your onboarding like?
- Metrics – Do you understand which metrics you need to track for effective talent acquisition?
- Compliance – Are you following established labor laws?
Honestly, this is a lot to consider. Who in your organization is going to manage all this and ensure it happens? How will they know what the best recruitment practices are? Do you have an in-house recruiter? Is it time to hire one?
I mentioned that being successful at talent acquisition requires an investment of time and money. But what exactly does that mean?
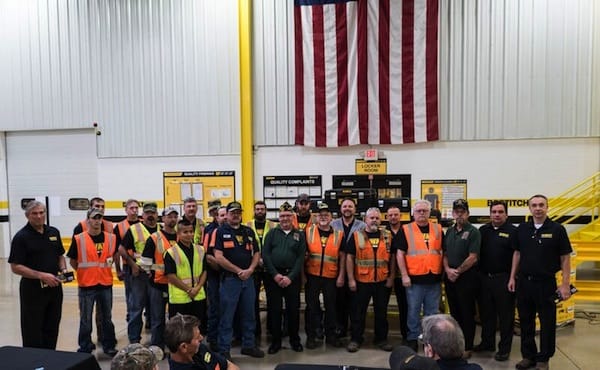
Let’s start with the time investment part. If you don’t have a recruiter, each member of your leadership team should spend a defined amount of time focusing on recruitment-related activities. These could be action items such as refreshing ads on job boards, screening applications, and networking for contacts. Be intentional with it. Perhaps dedicate five hours a week to it and adjust according to your hiring needs. A time investment in talent acquisition also includes properly vetting candidates.
If you already have a recruiter, provide them with opportunities to upskill by having them attend workshops, which allow them to learn and network with other recruiters. Every job requires a level of training; recruiting is no different.
Now let’s talk about the money investment for talent acquisition. This might mean investing in tools (such as applicant tracking systems) to help you effectively recruit. But what else?
Well, a common question I get is “What percentage of our budget should we dedicate to recruiting?” The answer is generally “No more than one percent of your budget, unless you’re planning to use more expensive media channels to get the word out, such as TV, radio or billboards.” Budgeted talent acquisition money should be put towards digital marketing, social media tactics, and sponsoring job ads on job boards. You’ll also want to invest in a robust employee referral program, if you truly want to hire great people quickly and you want them to stay. Tailor your referral program to reward employees for referring excellent and reliable candidates. And finally, if you don’t have a recruiter, it may be time to hire one or use outside recruiting agencies to help you reach your hiring goals.
Getting the right people in the right seat in a timely fashion is no small undertaking. You need people to grow your business, and that means investing in talent acquisition. I encourage you to consider the return on your investment! One percent of your budget is miniscule compared to the cost of being understaffed and the cost of employee turnover. An investment in talent acquisition is an investment well worth making.
Steffan Busch’s career in human resources and recruiting has spanned more than 14 years. He loves consulting with leaders on how to best position their companies so they can become employers of choice, which helps their recruitment of the best and brightest job candidates in the industry. In his role as Talent Acquisition Coach and Executive Recruiter at Nexstar Network, Steffan has been instrumental in launching NexHire, a tailored solution to help contractors improve their recruitment marketing, streamline their process, and identify professionals who are the right fit for their culture and their business for the long term.
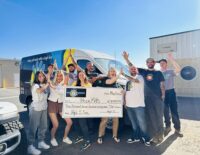
By Heather Ripley ‘Tis the season to be charitable. The holiday season often brings out our country’s most benevolent feelings, but it’s also a great time of year to publicize your company’s charitable donations. Many news outlets tend to focus on what local businesses are doing for the community as an example of the Christmas Read more
By Heather Ripley
‘Tis the season to be charitable.
The holiday season often brings out our country’s most benevolent feelings, but it’s also a great time of year to publicize your company’s charitable donations. Many news outlets tend to focus on what local businesses are doing for the community as an example of the Christmas spirit or as part of a year-in-review story.
As a plumbing contractor, you are looking for ways to stand out from your competition, and one way to do that is to publicize your company’s volunteer spirit.
Studies also show that younger generations take a company’s charitable giving into account when making purchasing decisions, and all generations look favorably at successful companies that give back to their community.
Here are three reasons why sharing information about your company’s altruistic programs can help you stand out from the crowd and heighten your reputation.
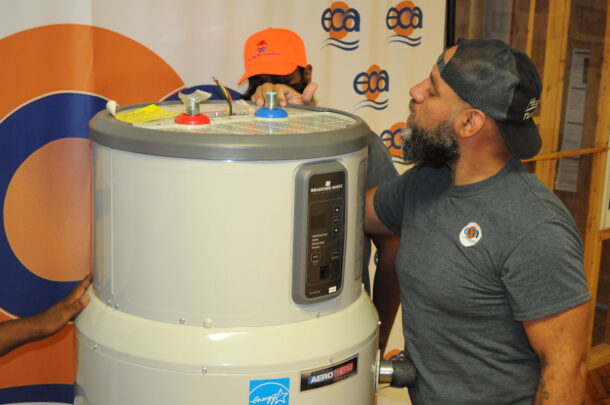
1. Attract Customers and Retain Talent
As a public relations professional, I speak to many business owners who feel like it’s self-serving to promote their own philanthropic efforts, but our agency highly recommends it, and here’s why: recent studies show that consumers want to know how businesses are supporting good causes. According to a YouGov poll, nearly half of consumers are more likely to buy from a brand that gives to a charity, while only 5% say they are less inclined to do so.
Given those odds, touting your efforts on your social media platforms, through press releases, and on your company’s blog will attract more customers who want to support businesses that care about the issues that are important to them.
In addition to consumer interest, most employees—65%—also prefer to work for companies that value social and environmental causes. Retention experts say that employees are happier when they work for a company that shares their personal values.
Collecting donations and offering volunteer opportunities boosts your employees’ morale and helps them connect with your company and its causes on a deeper level.
2. Boost Your Reputation
As a home service company, it’s imperative that you build trust in your community. Because you work with your customers in their most intimate settings, it’s important they have faith in your work and in your judgment.
By publicizing your philanthropic efforts, potential customers can see that you care. And, if your team also volunteers for activities to help the charities you’ve chosen to support, your company and its employees become more visible in the community.
This type of public relations (PR) associates your brand name with a cause and creates a positive image in the minds of consumers when they see your company name. A great example of this kind of PR is the Dawn Saves Wildlife campaign. As a result of news articles and an intense advertising campaign, people now associate the dish soap with the protection of wildlife after oil and chemical spills, and many consumers prefer to purchase that soap over others because they support the wildlife campaign.
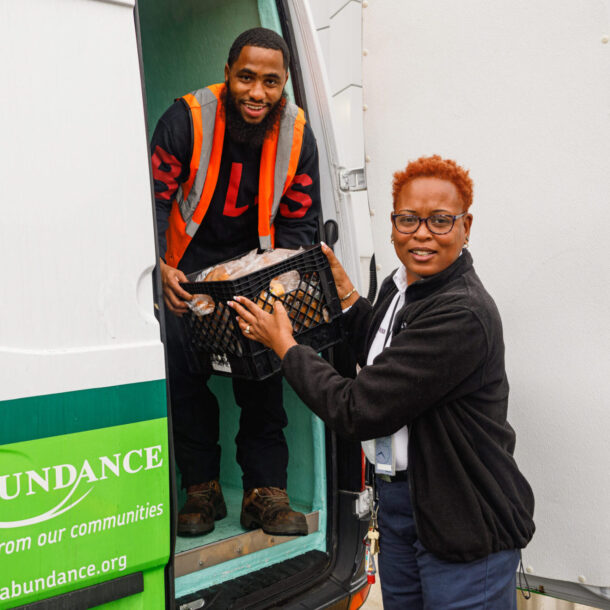
3. Differentiate Your Company
If you’ve ever Googled your industry to see how many competitors you have in your local market, you are aware that you are probably one of several plumbing companies in your service area.
Most likely, their marketing teams are also producing door hangers, designing cool truck wraps, and are monitoring the Search Engine Optimization (SEO) on your website to attract customers. That’s why you need to do something to differentiate your company from your competition, and that “something” involves public relations.
If you have an effective PR partner, they can help you develop stories, social media and blog posts, and press releases about your company’s good deeds and will work to garner media interest in these efforts.
This not only gets you noticed by your local media, it also improves your standing on Google’s search results—the more times your company’s name appears in links outside of your website, the higher you’ll be listed in those results.
The bottom line is that you shouldn’t be afraid to showcase your philanthropic endeavors. But you need to do it tastefully. Building a solid PR campaign or working with a professional PR team can help you differentiate your company and celebrate your efforts while avoiding the pitfalls of sounding insincere.
Heather Ripley is founder and CEO of Ripley PR, an elite, global public relations agency specializing in the franchising, skilled trades and B2B tech industries. Ripley PR has been listed by Entrepreneur Magazine as a Top Franchise PR Agency for seven consecutive years and was recently named as one of Newsweek’s America’s Best Public Relations Agencies for 2024. Heather Ripley was recently named as a 2024 PRNews Top Women honoree in the business entrepreneur category, and she was recently named as ACHR NEWS’ Top Women in HVAC. She is also the author of “NEXT LEVEL NOW: PR Secrets to Drive Explosive Growth for your Home Service Business,” which is now available on all audiobook platforms. For additional information, visit www.ripleypr.com.
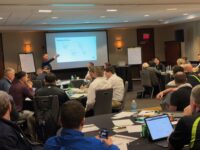
By Chris Hondl, Nexstar Network Sales Coach Before I got into sales, I was a teacher. I taught for five years at the elementary level. My wife was also a teacher. At the time, we were newly married, with no kids, and looking ahead to how we were going to afford kids, buy a house Read more
By Chris Hondl, Nexstar Network Sales Coach
Before I got into sales, I was a teacher. I taught for five years at the elementary level. My wife was also a teacher. At the time, we were newly married, with no kids, and looking ahead to how we were going to afford kids, buy a house, and put together all the other pieces that come along with the American Dream.
Unfortunately, our two little teacher paychecks didn’t add up to making that happen. So, I took a stab at getting a second job. I had seen advertisements for the Minnesota School of Bartending and I decided to enroll, with hopes of teaching by day and bartending on nights and weekends. I went through the program and achieved the lifetime certification, which proved I had mastered how to make more than 100 of the most popular cocktails and knew about all the top brand-name liquors.
That was almost two decades ago, and I have yet to make a single drink as an official and employed bartender. In fact, if you were to ask me for any of those 100+ drinks I am “certified” to make, the only one I think I would be able to make you would be one of the simplest: a rum and coke.

You see, I never adopted my newfound bartending skills into practice. I learned the skills, but I never used what I learned afterward.
We see the same thing in our own businesses, don’t we? We send an employee to a session, and they gain all of these new skills and ideas, and then what? They come back to work. And if we don’t actively apply what your employees learned in the field, it’s eventually as if the session never happened. What a waste of time and money!
Recently, I asked the 40+ previous attendees of the Sales Objection Bootcamp about the effectiveness of the bootcamp.
The results I got back from the attendees, four months after the session occurred, generally fall into three buckets:
- We haven’t done a thing with the information we learned at the Sales Objection Bootcamp since we left, and we’re seeing the same results we were getting before the training.
- We realized we have some process issues to fix before we continue with what we learned in the Sales Objection Bootcamp.
- We are following the plan we learned and seeing amazing results!
These answers aren’t in the least bit surprising. It’s just like me and my experience with bartending school. Had I attended the school and then immediately gone out and begun bartending, the skills I had learned at school would have become second nature and helped me realize my goal of making money as a bartender. But since I never practiced what I learned, I ended up in the same place I was in before I attended bartending school: with no results, not retaining what I had learned, and not making money as a bartender.
Participating in the bootcamp is only half of the journey. Putting what you learn into practice is the other, more important half.
There are a lot of sales-focused training courses out there for our industry. Take time to identify the right one for you and your team. For example, the Sales Objection Bootcamp we’ve developed here at Nexstar is an intensive three-day session where your dedicated sales coach comes to your location and works with your team to master their presentations and objections such as: Price, Spouse, Shopping Around and many more.
Want proof that it all works? Here’s feedback from a member who is following the plan and currently seeing incredible results:
Nathan Andreas, owner of , attended Sales Objection Bootcamp with his sales team. Since returning home and practicing what they learned, their closing rate has gone well above their budgeted goal, with one salesperson averaging 69% closing on tech leads and 55% closing on marketed leads. Nathan says the take-aways that have been key to their success are:
- Buying into having a strong sales process before presentation
- Maximizing skills-practice
- Clarifying the objection
- Digging deeper to uncover the real objection
- Using a trial close prior to asking for the sale
- Riding along with his team
So! Are you ready to dramatically increase your sales in FY25? It will take commitment and follow-through. Otherwise, would you prefer to keep getting the same results you’ve always gotten?
Chris Hondl serves as one of two Sales Coaches at Nexstar Network and has more than 15 years of experience in coaching, training, and sales. If you are a Nexstar member and are prepared to implement what you’ve learned in the Sales Objection Bootcamp, contact your Sales Coach for an assist. If you’re not a Nexstar member, but you’re curious to learn more, click here.