https://vimeo.com/1071965170 On this week’s Mechanical Hub weekly update, we talk about the unpredictability of the weather, Utah’s Fluoride ban in drinking water, April Fool’s jokes, a visit with our friends from Viega and the Appetite for Construction podcast, which features Jorge Arias, vocational plumbing instructor at the Correctional Training Facility (CTF) Soledad State Prison in Read more
Featured Articles
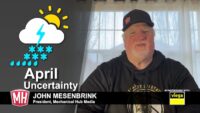
On this week’s Mechanical Hub weekly update, we talk about the unpredictability of the weather, Utah’s Fluoride ban in drinking water, April Fool’s jokes, a visit with our friends from Viega and the Appetite for Construction podcast, which features Jorge Arias, vocational plumbing instructor at the Correctional Training Facility (CTF) Soledad State Prison in California.
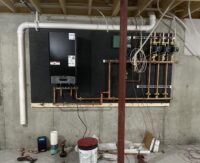
HTP Combi Boiler Adds Heating Security for New Construction Project By Thomas Renner In Waterboro, Maine, a community of slightly more than 8,000 residents, homeowners have to be prepared for the worst a winter storm can bring. For six months out of the year, the daily low-temperature average dips below the freezing point. Snow Read more
HTP Combi Boiler Adds Heating Security for New Construction Project
By Thomas Renner
In Waterboro, Maine, a community of slightly more than 8,000 residents, homeowners have to be prepared for the worst a winter storm can bring.
For six months out of the year, the daily low-temperature average dips below the freezing point. Snow? You betcha. In 2015, a January storm dumped 27 inches on York County, where Waterboro is located in southern Maine. In an average year, residents cope with more than five feet of snow during the winter months.
When Kyle Lagasse installed a heat and hot water system for a new construction, the property owner didn’t want to take any chances on a heating malfunction. Lagasse installed a heat pump as the primary source but supplemented the 2,500-square-foot house with a HTP combi boiler.
“They wanted a backup in the house,’’ Lagasse said. “A lot of homeowners are using heat pumps, but sometimes their performance in low temperatures can be impacted by snow and ice.”
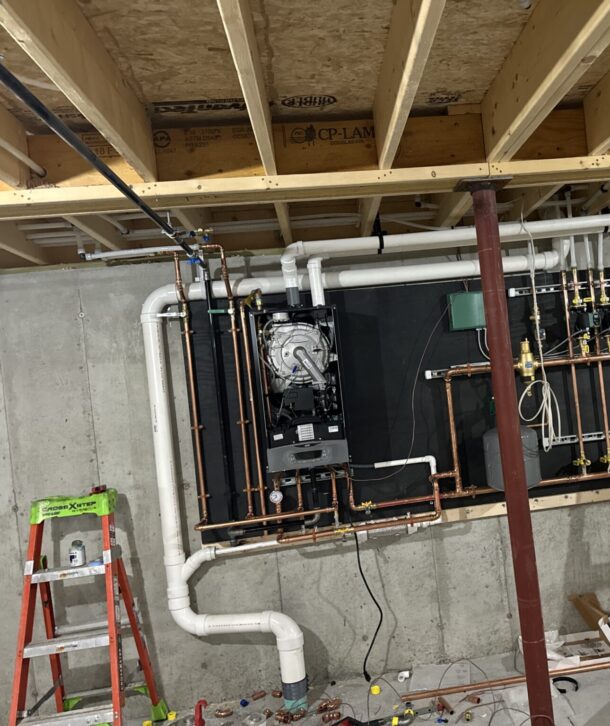
A newly-constructed 2,500-square-foot home in Maine includes an HTP combi boiler, which serves as an important backup to a heat pump.
Heating Hurdles
Lagasse jumped at the chance to take on a new construction project, but he also faced some tricky challenges in designing and installing the system for the 4-bedroom home.
The primary issue Lagasse faced was an open concept living area that included a fireplace and built-in units that limited the amount of space for baseboard heat. “When we did the heat calculations, we determined we needed 9-inch-high hydronic baseboard units,’’ Lagasse said. “That gives off the twice the value. We made sure to balance the heat with the BTUs that we needed from the boiler.”
He faced a similar issue in the master bathroom, where occupied wall space reduced the amount of room for baseboard heat. “We have to find a solution to have enough heat even when there is not a lot of available wall space,’’ Lagasse said.
Lagasse worked around the issue with low temperature, low profile baseboard heating units that have minimal intrusion on wall space.
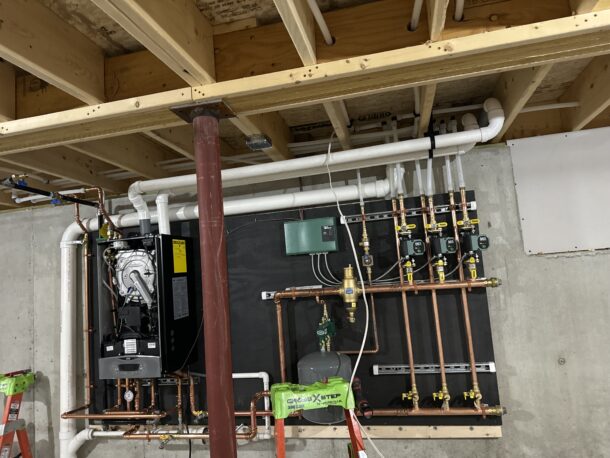
Backup Plan
While the heat pump is the primary heat source for heat, Lagasse and the homeowner felt it was important to have a secondary heat and hot water source.
Lagasse selected the HTP ELU-150WCN, a combi unit that delivers a maximum of 120,000 BTUs per hour for heating and 150,000 BTUs per hour for hot water.
The HTP unit provides up to 96 percent thermal efficiency and has an 11:1 turndown ratio that limits short cycling and provides efficient energy consumption.
“Having a combi unit was an important part of the selection process,’’ Lagasse said. “The house is set up pretty well with the heat pump for heat, but this is a way to have heat and an on-demand hot water system.”
Heat pumps work by pulling heat from the air outside and transferring the heat into the air circulating throughout the home. They are most effective in mild climates with moderate temperatures. When temperatures drop significantly, heat pumps work harder to extract heat from the outside air, reducing efficiency. Snow and ice can also hinder the effectiveness of heat pumps.
One of the other features that make the HTP unit a good solution for the project is a heat exchanger that ensures maximum quality at the heart of the boiler. “In Maine, one of the most unusual challenges is the water that’s coming in is much colder,’’ Lagasse said. “It takes hot water longer to heat up. That’s not going to be a problem with this unit.”
Lagasse also finds service from Tom Protasewich, his local HTP rep working for Emerson Swan, helpful in finding solutions to the challenges he regularly faces on the job. The unit also comes with HTP Link, a software feature that enables remote monitoring of the appliance and system.

The HTP unit provides up to 96 percent thermal efficiency and has an 11:1 turndown ratio that limits short cycling and provides efficient energy consumption.
Bringing the Heat
During the construction phase, the HTP boiler helped bring heat to the house as workers established drywall, painted rooms and applied other final touches before the owners moved in. The project took slightly more than two days to install and establish multiple zones.
“The basement is all open at this point and they don’t have a dedicated mechanical room,’’ Lagasse said. “It’s one of the first things people see when they visit the house. The homeowners made a good choice, and I think the heating and hot water solution will serve them well.”
Thomas Renner writes on building, construction and other trade industry topics for publications throughout the United States.

https://vimeo.com/1070103550 Did you know that on this date in 1979, the infamous Three Mile Island accident occurred, which was a partial meltdown of the Unit 2 reactor of the Three Mile Island Nuclear Generating Station, located on the Susquehanna River near Harrisburg, Pennsylvania. It is the worst accident in U.S. commercial nuclear power plant history Read more
Did you know that on this date in 1979, the infamous Three Mile Island accident occurred, which was a partial meltdown of the Unit 2 reactor of the Three Mile Island Nuclear Generating Station, located on the Susquehanna River near Harrisburg, Pennsylvania. It is the worst accident in U.S. commercial nuclear power plant history? |
Illinois’ Top Apprentices Showcase Elite Skills at Statewide Competition
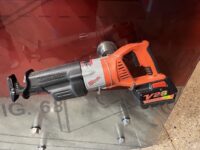
Welcome to Tech Transformation, a new feature showcasing the evolution of a technology or product over time. We start with Milwaukee Tool’s SAWZALL. Over the past 20 years, Milwaukee Tool has significantly advanced the SAWZALL®, a product that has set industry standards since its invention nearly 75 years ago. At the turn of the millennium Read more
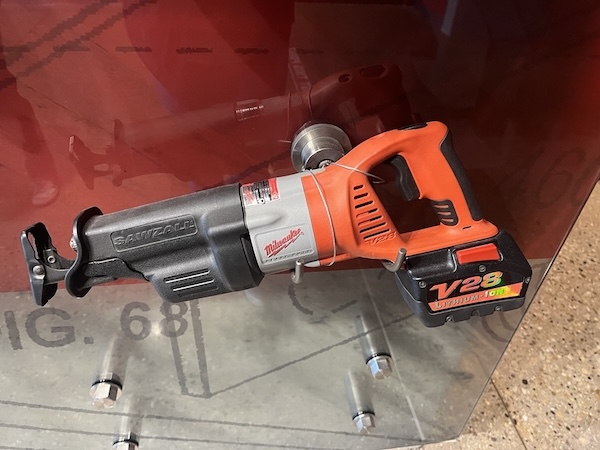
Milwaukee SAWZALL in 2008
Welcome to Tech Transformation, a new feature showcasing the evolution of a technology or product over time. We start with Milwaukee Tool’s SAWZALL. Over the past 20 years, Milwaukee Tool has significantly advanced the SAWZALL®, a product that has set industry standards since its invention nearly 75 years ago. At the turn of the millennium, Milwaukee® introduced the world’s first cordless SAWZALL® that could compete with its legendary corded counterpart, allowing professionals to cut the cord for the first time. Powering the 0719 model was the 28 Volt LITHIUM-ION battery pack, exclusively from Milwaukee, which marked a revolutionary leap in cordless tool technology at the time.
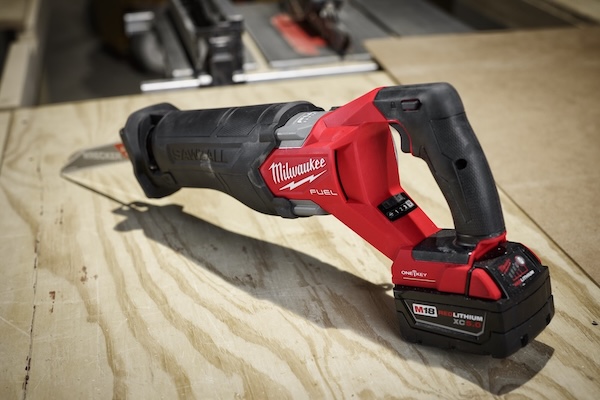
Today’s M18 FUEL™ SAWZALL® Recip Saw, Gen 2, w/One-Key
Milwaukee set out to change the lives of users introducing the M18™ cordless system and made a commitment that they continue to deliver on to this day: Milwaukee would continue to invest in new technology without the need for users to change platforms. This innovation paved the way for the game-changing M18 FUEL™ SAWZALL®.
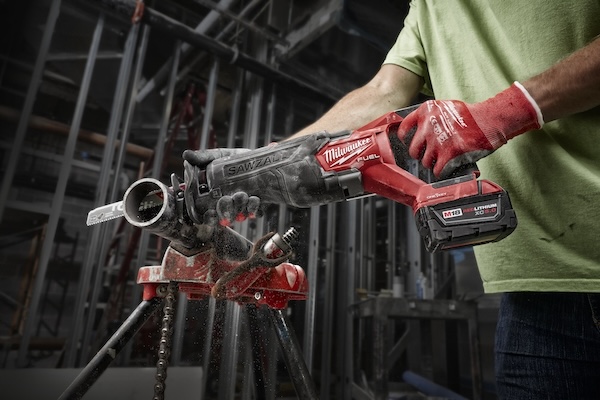
Since then, Milwaukee has continued to push the boundaries of performance and reliability. The current M18 FUEL™ SAWZALL® Recip Saw w/ ONE-KEY™ (2822-22) now boasts fastest cutting in class, improved durability, and lightweight designs for reduced fatigue. Leveraging a POWERSTATE™ Brushless Motor, this newest generation provides 3,000 SPM and a 1-¼” stroke length for faster material.
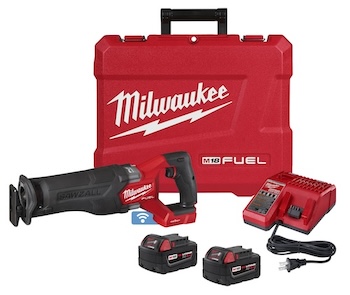
The gear-protecting clutch further enhances durability by safeguarding against impact, upholding the legendary SAWZALL® reputation. Additionally, the introduction of ONE KEY™ tracking technology and slider crank mechanism upgrades ensure that the SAWZALL® remains a leader in the industry, continually meeting the evolving needs of professionals.
For more information, www.milwaukeetool.com

https://vimeo.com/1067501692 On this week’s Mechanical Hub update: As I watched the recovery efforts—for the astronauts stuck in space for nine months—live off the coast of Tallahassee, Fla., all I kept thinking about was, “Where have these two astronauts been going to the bathroom for that extended period of time?” I guess I’m not alone in Read more
On this week’s Mechanical Hub update: As I watched the recovery efforts—for the astronauts stuck in space for nine months—live off the coast of Tallahassee, Fla., all I kept thinking about was, “Where have these two astronauts been going to the bathroom for that extended period of time?” I guess I’m not alone in that thought because it is one the most commonly-asked questions for astronauts visiting the space station.
Subscribe to the Mechanical Hub newsletter:
Podcasts:
Thermal Energy Networks:
Part 2 of 2: Thermal Energy Networks: Why TENs Are the Future
AHR with Caleffi