HTP Combi Boiler Adds Heating Security for New Construction Project By Thomas Renner In Waterboro, Maine, a community of slightly more than 8,000 residents, homeowners have to be prepared for the worst a winter storm can bring. For six months out of the year, the daily low-temperature average dips below the freezing point. Snow Read more
Featured
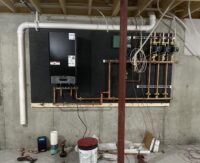
HTP Combi Boiler Adds Heating Security for New Construction Project
By Thomas Renner
In Waterboro, Maine, a community of slightly more than 8,000 residents, homeowners have to be prepared for the worst a winter storm can bring.
For six months out of the year, the daily low-temperature average dips below the freezing point. Snow? You betcha. In 2015, a January storm dumped 27 inches on York County, where Waterboro is located in southern Maine. In an average year, residents cope with more than five feet of snow during the winter months.
When Kyle Lagasse installed a heat and hot water system for a new construction, the property owner didn’t want to take any chances on a heating malfunction. Lagasse installed a heat pump as the primary source but supplemented the 2,500-square-foot house with a HTP combi boiler.
“They wanted a backup in the house,’’ Lagasse said. “A lot of homeowners are using heat pumps, but sometimes their performance in low temperatures can be impacted by snow and ice.”
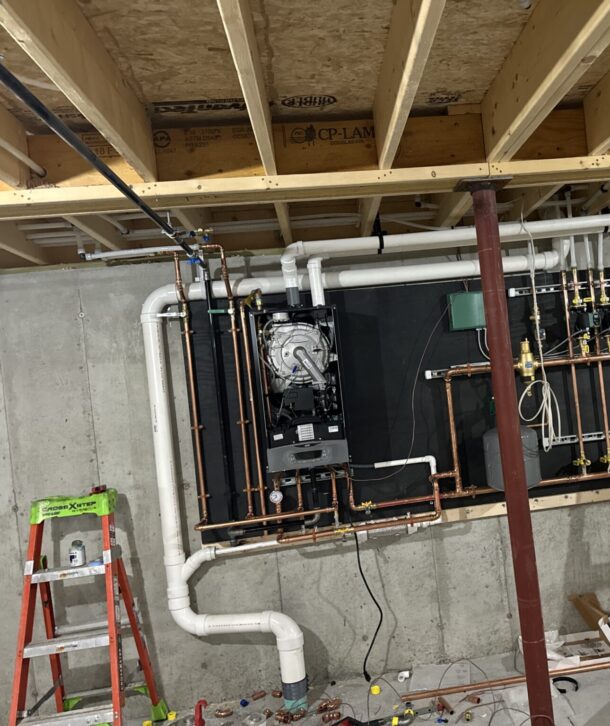
A newly-constructed 2,500-square-foot home in Maine includes an HTP combi boiler, which serves as an important backup to a heat pump.
Heating Hurdles
Lagasse jumped at the chance to take on a new construction project, but he also faced some tricky challenges in designing and installing the system for the 4-bedroom home.
The primary issue Lagasse faced was an open concept living area that included a fireplace and built-in units that limited the amount of space for baseboard heat. “When we did the heat calculations, we determined we needed 9-inch-high hydronic baseboard units,’’ Lagasse said. “That gives off the twice the value. We made sure to balance the heat with the BTUs that we needed from the boiler.”
He faced a similar issue in the master bathroom, where occupied wall space reduced the amount of room for baseboard heat. “We have to find a solution to have enough heat even when there is not a lot of available wall space,’’ Lagasse said.
Lagasse worked around the issue with low temperature, low profile baseboard heating units that have minimal intrusion on wall space.
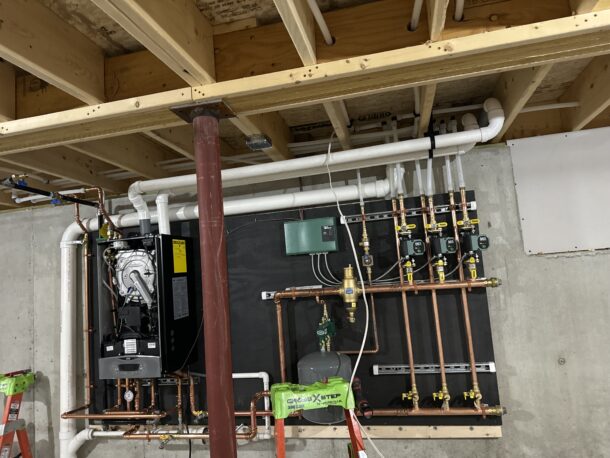
Backup Plan
While the heat pump is the primary heat source for heat, Lagasse and the homeowner felt it was important to have a secondary heat and hot water source.
Lagasse selected the HTP ELU-150WCN, a combi unit that delivers a maximum of 120,000 BTUs per hour for heating and 150,000 BTUs per hour for hot water.
The HTP unit provides up to 96 percent thermal efficiency and has an 11:1 turndown ratio that limits short cycling and provides efficient energy consumption.
“Having a combi unit was an important part of the selection process,’’ Lagasse said. “The house is set up pretty well with the heat pump for heat, but this is a way to have heat and an on-demand hot water system.”
Heat pumps work by pulling heat from the air outside and transferring the heat into the air circulating throughout the home. They are most effective in mild climates with moderate temperatures. When temperatures drop significantly, heat pumps work harder to extract heat from the outside air, reducing efficiency. Snow and ice can also hinder the effectiveness of heat pumps.
One of the other features that make the HTP unit a good solution for the project is a heat exchanger that ensures maximum quality at the heart of the boiler. “In Maine, one of the most unusual challenges is the water that’s coming in is much colder,’’ Lagasse said. “It takes hot water longer to heat up. That’s not going to be a problem with this unit.”
Lagasse also finds service from Tom Protasewich, his local HTP rep working for Emerson Swan, helpful in finding solutions to the challenges he regularly faces on the job. The unit also comes with HTP Link, a software feature that enables remote monitoring of the appliance and system.

The HTP unit provides up to 96 percent thermal efficiency and has an 11:1 turndown ratio that limits short cycling and provides efficient energy consumption.
Bringing the Heat
During the construction phase, the HTP boiler helped bring heat to the house as workers established drywall, painted rooms and applied other final touches before the owners moved in. The project took slightly more than two days to install and establish multiple zones.
“The basement is all open at this point and they don’t have a dedicated mechanical room,’’ Lagasse said. “It’s one of the first things people see when they visit the house. The homeowners made a good choice, and I think the heating and hot water solution will serve them well.”
Thomas Renner writes on building, construction and other trade industry topics for publications throughout the United States.
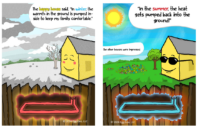
In the United States, there are three general types of electrical suppliers. They are: Investor-Owned Utilities (IOU) Municipally Owned Utilities (MUNI) Customer Owned Rural Cooperatives (Co-op) Investor-Owned Utilities include big names in Electrical & Natural Gas distribution such as Con Ed, Florida Power and Light, and Pacific Gas & Electric. These are investor-owned utilities. There Read more
In the United States, there are three general types of electrical suppliers. They are:
- Investor-Owned Utilities (IOU)
- Municipally Owned Utilities (MUNI)
- Customer Owned Rural Cooperatives (Co-op)
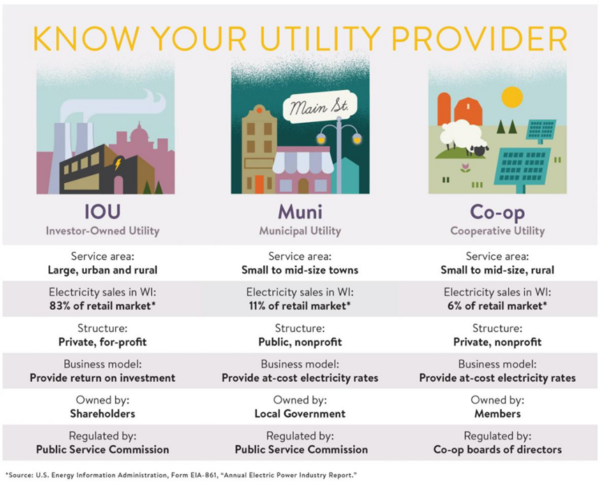
Investor-Owned Utilities include big names in Electrical & Natural Gas distribution such as Con Ed, Florida Power and Light, and Pacific Gas & Electric. These are investor-owned utilities. There are 168 IOUs in the US that serve about 110 million customers. They are regulated by their respective Public Service Commissions (PSCs) and must conform as a regulated monopoly.
Municipally Owned Utilities (there are 958 of them) include names like Rochester Public Utilities, Tampa Electric Company, and Philadelphia Gas Works. Since these utilities are owned by a municipality or another government agency, they are regulated by their owners, meaning the city or community.
Customer Owned Rural Cooperatives (there are 832 of them) include names like Texas-based Pedernales Electric Cooperative, The Nebraska Rural Electric Association, and New Jersey’s Sussex Rural Electric Cooperative. These utilities exist to bring the best services possible to their consumers, and they are run by the folks that pay also pay for the energy.
Investor-owned electric utilities are typically regulated and operate as vertically integrated monopolies with oversight from public utility commissions. They may operate in deregulated markets in which electric energy prices are set by the market and are subject to federal oversight of their wholesale market.
Before 1990, most investor-owned electric utilities were regulated and vertically integrated. That means that the utilities own electricity generators and power lines (both distribution and transmission lines). Presently about 30% of US electricity demand is serviced by these fully integrated utility markets. In much of the US, states have abandoned this system in favor of deregulation.
In traditionally regulated regions, utilities operate as a monopoly in their territories. That means that customers only have the option to buy power from them. To keep electricity rates reasonable, state regulators oversee these electric utilities and set electricity prices. Retail electricity prices are set based on the utility’s operating and investment costs alongside a fair rate of return, which is called a “revenue requirement”. This revenue is approved by the state’s public utilities commission and prevents utilities from overcharging customers for energy.
Smaller rural electric cooperatives power 56% of the American landscape, serving 42,000,000 residents, including 92% of impoverished counties.
There has been tremendous publicity for geothermal technologies. Direct use and enhanced geothermal systems are providing incredible baseload electricity and thermal energy for infrastructure. Geothermal technologies are strategically vital toward management of peak demand on the grid. The wide-spread power outages in Texas (2021) are an example of a runaway peak demand in the heating season.
“Ground Source Heat Pumps (GSHPs) are the key to managing demand on the electrical grid.”
With the high demand for air conditioning in the summertime, why would a wintertime freeze cause the electrical grid to “spike” as we saw in Texas in 2021? Most people know that air conditioning loads in the middle of August usually drive the greatest demand on the grid. However, electric heaters & air source heat pumps (ASHPs) are often used to handle peak heating loads, and they can double or triple that peak demand in the wintertime, when compared with summertime demand. Here’s a primer on how and why that is:
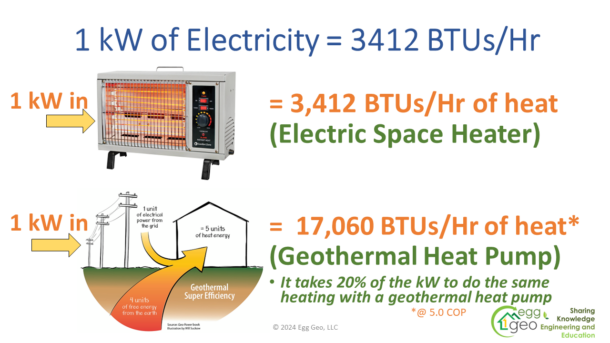
Energy Facts:
- 1 watt of electricity = 3.412 BTUs
- I kW of heat consumed by an electric heater = 3,412 BTUs of heat output
- I kW of heat consumed by an electric Geothermal Heat Pump (GHP) = 17,060 BTUs of heat*
- It takes 20% the kW to do the same heating with a GHP *(@5.0COP)
As it gets colder outside, Air Source Heat Pumps (ASHPs) must work harder to extract heat from the air. Geothermal Heat Pumps (GHPs) continue to have high efficiency operation regardless of outdoor temperature (because underground temps are reasonably stable).
Cold temperatures can reduce the efficiency of heat pumps, simply because it’s hard to extract heat from outside air as it gets colder. The efficiency of ASHPs drops as it gets colder outside, just as the gas mileage efficiency of a car drops when it’s climbing a hill. Geothermal heat pumps are not normally subject to drastic temperature fluctuations, because they’re coupled with the temperature in the shallow earth, which ranges between about 45 and 75 degrees in the US.
There have been a few Customer-Owned Rural Cooperatives (Co-ops) in recent decades that have been able to capitalize on reduced demand in summer, and increased revenue from electric GHPs in the winter. Look at the demand of two identical office buildings in Oklahoma. One has air-source heat pumps (ASHPs), the other, geothermal heat pumps (GHPs):
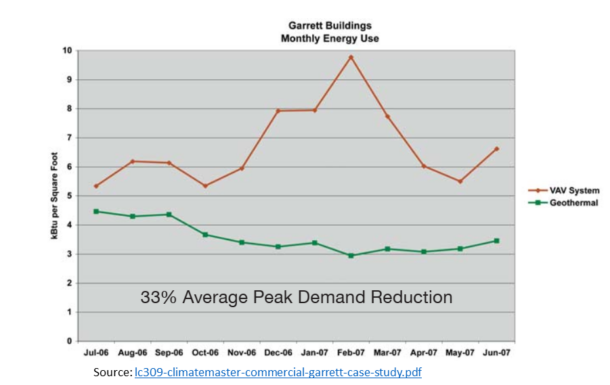
It’s obvious that there is a demand reduction in the summer, but the winter savings & peak demand reduction are remarkable. Here are some figures from Boyd Lee, an employee of CKenergy in Oklahoma:
- 2000 new GHPs replaced (both new construction and replacing gas furnaces)
- 4800kW Demand Reduction = $835,000/year.
- New sales totaled an additional 2,600,000 kWh, or about $260,000.
- Net annual increased revenue = $1,095,200.
What this means is that the electrical cooperative has more than $500 per year per home in additional income by going with a geothermal solution when compared to air sourced heat pumps. Electrical utilities typically look for payback in 60 years or less for infrastructure improvements such as power plants or distribution lines. Using that same logic, the utility has $30,000 per home to pay for the upgrades. That will more than cover the cost of the geothermal solution. And while ASHPs last 10 to 15 years, the GHP will last closer to 30 years because it can be installed all-indoors, and has a more stable heat exchange source, meaning it has much better working conditions.
Geothermal Exchangers Extract Energy from the Earth
The geothermal heat pump solution in the CKenergy case totaled 5142 Tons of capacity, and reduced demand by 0.65 kW per ton. That represents a 3.4 MW peak energy generation by the geothermal exchangers in the CKenergy case. Note that they see the geothermal exchangers as a source of energy, producing 3.4 MWs, removing that electrical load from the grid.
Energy Poverty
1 in 4 households served by electric co-ops have an annual income below $35,000. Electric co-ops delivered 4.8% more electricity in 2022 than in the previous year.
Unlike the rest of the electric sector, electric co-ops sell most of their power — 53% — to households. Keeping rates affordable is especially important for these consumers at the end of the line. -NRECA analysis U.S. average annual residential electricity bill: $1,644
Electrical co-ops are perfectly poised to create demand side management (DSM) program setting include deep subsidies for geothermal heat pump (GHP) installations. The numbers seem to bear out a model that could allow the Co-op to pay for the entire ground loop exchanger and offer “on bill financing” for the GHP, electrical, and distribution upgrades needed. With 92% of persistently impoverished communities paying energy bills to electrical cooperatives, these are the folks that could truly benefit with some relief from high energy costs. The cure to energy poverty can be partially met through this demand side management since their energy bills will be drastically reduced with GHPs.
What’s next? We will see electrical co-ops begin to take advantage of this remarkable opportunity, and millions of geothermal heat pumps will be installed over the next 20 years in cooperative communities. As these cooperatives begin to understand the demand side value of GHP’s, they will embrace the opportunity to utilize the energy source that is the earth for heating and cooling within their service areas.
Jay Egg is a geothermal consultant, speaker, writer, and the owner of Egg Geo. He has co-authored two textbooks on geothermal HVAC systems published by McGraw-Hill Professional. He can be reached at jaye@egggeo.com.
Mimi Egg is a social media marketing professional, writer and media technical consultant for Egg Geo, focused on building online connections and educating on social media platforms. Her desire to educate the rising generation about green, sustainable living is a major focus in her career. Egg may be reached at mimieggshell@gmail.com
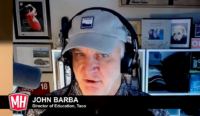
https://vimeo.com/1012594655 In today’s edition, we’ll talk mandates on circulator efficiency as we welcome back Taco’s John Barba. We’ll scratch the surface with heat pump water heaters, and Eric Aune talks about our weekly podcasts, and a cool incentive from Navien Read more
In today’s edition, we’ll talk mandates on circulator efficiency as we welcome back Taco’s John Barba. We’ll scratch the surface with heat pump water heaters, and Eric Aune talks about our weekly podcasts, and a cool incentive from Navien.
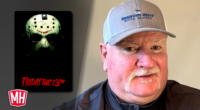
https://vimeo.com/1008155465?share=copy On this week’s update we address the fear of Friday the 13th, chat with AHR Expo director of marketing Nicole Bush about the AHR Expo 2025 in Orlando in February, and highlight Taco After Dark with Joha Barba, Taco Comfort Solutions’ director of training. We finish up with sharing the latest Make Trades Great Read more
On this week’s update we address the fear of Friday the 13th, chat with AHR Expo director of marketing Nicole Bush about the AHR Expo 2025 in Orlando in February, and highlight Taco After Dark with Joha Barba, Taco Comfort Solutions’ director of training. We finish up with sharing the latest Make Trades Great Again and Appetite For Construction podcasts and how to connect with Mechanical Hub Media on ideas and topics that resonate in the industry. Make it a lucky Friday the 13th!
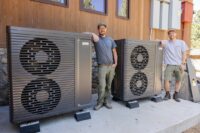
In 1971, Chicago native James Guercio, a musician and producer, purchased a 2,000-acre ranch in Nederland, CO, with plans to turn the property into a recording studio and rural escape for the biggest names in the music business. He modified the property’s old barn into a recording studio. In ‘72, Joe Walsh recorded “Rocky Mountain Read more
In 1971, Chicago native James Guercio, a musician and producer, purchased a 2,000-acre ranch in Nederland, CO, with plans to turn the property into a recording studio and rural escape for the biggest names in the music business.
He modified the property’s old barn into a recording studio. In ‘72, Joe Walsh recorded “Rocky Mountain Way” while the barn still had a dirt floor. This was the first of many hits that would be produced at Caribou Ranch, as Guercio called the estate. Other stars followed, including Elton John, Stevie Wonder, Chicago, John Lennon, Michael Jackson and hundreds more.
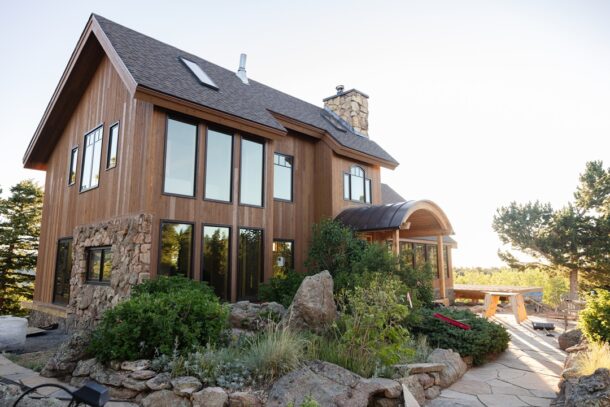
The 3,300 square foot home was a guest residence for musicians recording at the Caribou Ranch Studio.
On a parcel adjacent to the ranch sits a 3,300 square foot home built in 1973, where many of the travelling artists took up residence while writing and recording music. Fast forward to 2022: the home – and the piece of music history it represents – was sold.
The new owner found one of the old boilers leaking and called Peak to Peak Plumbing & Heating.
“We’re one of only a few shops that regularly travel up the Peak to Peak Highway to serve rural customers,” said Joe Ryan, 33 years old and owner of the company.
Ryan found that neither the old cast iron boiler nor the electric boiler was leaking. Instead, the water came from a foundation leak. To address that issue, Ryan called a general contractor he works with on a regular basis, Tom Akins, who owns AP Construction.
After some deliberation, the owner decided to renovate the entire home.

Joe Ryan, owner of Peak to Peak Plumbing.
Ground-source or air-source
Plans were drawn to update the house as well as the dual-fuel hydronic system installed years earlier. The owner’s two requirements were that heat pumps be used and radiant heating be installed throughout.
“Our first conversation about the heating retrofit took place two years ago,” said Ryan. “Both the homeowner and I were torn between installing geothermal units or an air-to-water heat pump system. Whenever I have questions like that, I reach out to Tommy Carroll at Boulder Winnelson.”
“Tommy’s about my age, casual and humble, which can be misleading, because he’s an hydronic mastermind,” he continued. “He’s an engineer by training and he designs hydronic systems in his sleep.”
Nearby Boulder is one of the greenest towns in the country, so it’s no surprise that local supply houses might have someone on staff to design high-efficiency, high-comfort hydronic systems.
“We compared air-to-water heat pumps with a geothermal system,” said Carroll. “In the end, it wasn’t a hard decision.”
Using an outdoor design temperature of -2°F, the home required 81,000 BTU/H. Given the ground temperature at 8,700 feet above sea level, a geothermal system would have required five, 500-foot boreholes. That expense alone made air-to-water heat pumps more attractive.
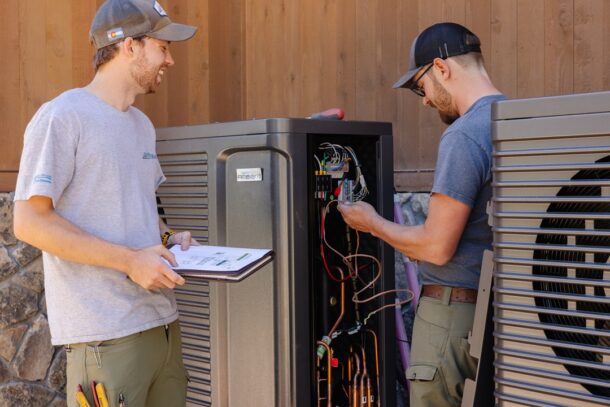
(left to right) Tommy Carroll and Joe Ryan connect thermostat wires.
BTU Wrangler
“Air-to-water systems have come far enough along that they’re somewhat comparable in capacity and COP to geothermal heat pumps,” said Carroll. “In the long run, air-to-water just made more sense. Air-to-water adds some cost to the plumbing side of the project, but the overall cost is significantly less.”
Customers go to Boulder Winnelson with tricky hydronic projects. Carroll’s business card reads “BTU Wrangler” for good reason.
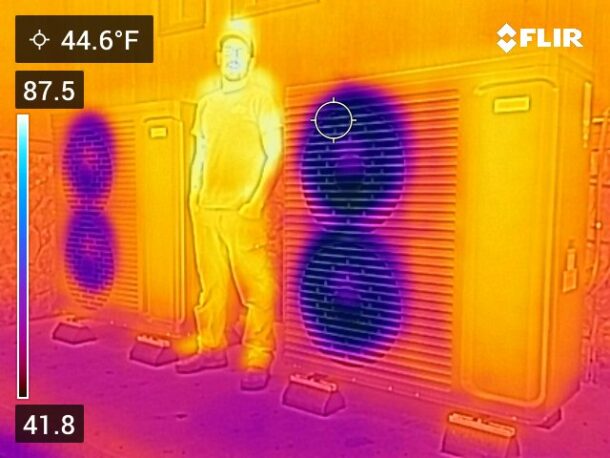
Installer Joe Ryan stands between the Ambient Heat Pumps.
Carroll conducted the heat-loss analysis based on the improvements that AP Construction was making to the building envelope, designed the heat pump system and put together a plan for the controls, allowing Ryan to install two air-to-water heat pumps with a condensing boiler for backup.
“Joe and I have worked together on a few projects in the past,” said Carroll. “He counts on us for experience and expertise, but he’s so competent that he doesn’t need help often.”
Quick pivot
Typical of old, custom homes, the renovation work proceeded slowly, thanks to surprises that kept coming up during construction. Ryan and Carroll had their system design finished in 2023 but were waiting until they could fully implement it. Not much changed until early 2024, when U.S. Boiler Company’s Dave Hansen called on Boulder Winnelson.
“Dave showed me their new Ambient air-to-water heat pump, and the specs on it matched what we needed perfectly,” said Carroll. “So, we changed the design. We’ve had a relationship with U.S. Boiler Company for decades. We knew we could count on them if we needed help.”
Almost a year before the release of the Ambient heat pump, Peak to Peak Plumbing & Heating had already piped many of the indoor components, including a 155 MBH condensing boiler, 70-gallon buffer tank, circulators, sidearm tank, HBX heat pump controller, and more. For this reason, Ryan didn’t need the complete Ambient heat pump package. He just needed the outdoor units.
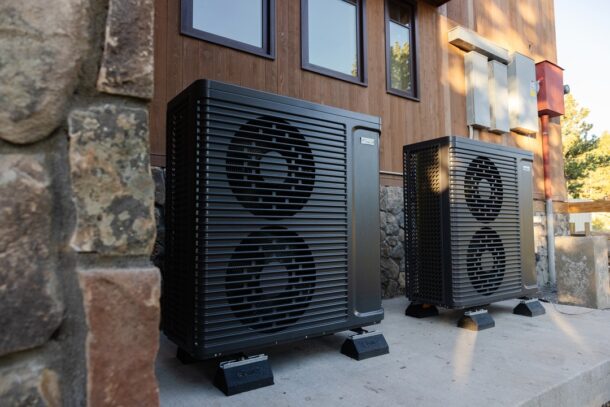
Two, five-ton Ambient air-to-water heat pumps are used to heat the 3,300 square foot home, which was built in 1973.
“There was an old electric boiler here before I arrived, so the heat pumps didn’t require an electrical service upgrade,” said Ryan. “We just poured a slab outside and core-drilled through the wall to run water lines to the mechanical room.”
Akins, the builder, was mildly concerned that noise or vibration from the heat pumps would transfer through the slab and into the home, but only time would tell.
On the inside
The entire system is freeze-protected by a 35 percent Enviro-Frost glycol mixture. Supply and return lines run from the outdoor units to the large buffer in the mechanical room. This tank has an electrical element but plans to hook it up were discarded when the Ambient heat pumps were selected.
“The Ambient heat pumps are five tons in capacity each,” said Ryan. “They’re capable of supplying up to 140°F water and continue operating down to an outdoor temperature of -13°F. We designed the radiant system to require only 121°F supply water on a design day, and there’s a gas boiler piped to the buffer tank in the unlikely event the home needs supplementary heat.”
When operating at full capacity, 15.3 GPM is pumped through each Ambient heat pump and into the 70-gallon AltSource buffer tank, which also contains a reverse-indirect coil for DHW.
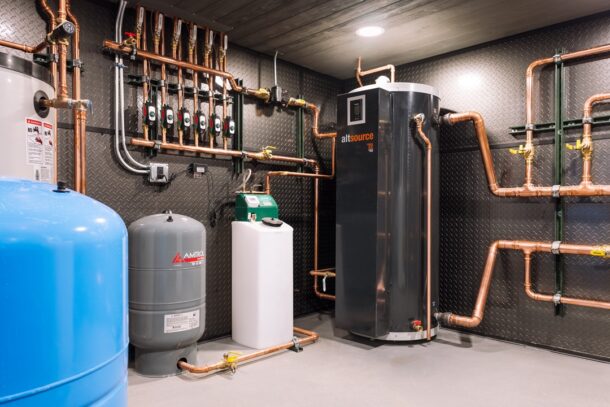
The mechanical room, designed by Ryan and Carroll, uses hot water from the heat pumps for the radiant system and to pre-heat domestic hot water.
“The buffer tank won’t cover the DHW load, simply because it sits at about 120°F on design day,” explained Carroll. “That’s great for radiant floors, but too cool to heat the DHW to final temp. Instead, the coil in the buffer tank just pre-heats the water on its way to the sidearm tank. We went with the reverse indirect coil because it is an easy way – requiring no pumps or moving parts – to use the heat pumps to cover some of the DHW load by preheating the incoming cold water on its way to the sidearm tank. The boiler will always have to raise the DHW to final temp.”
On the space heating load side of the buffer tank is a single Grundfos Alpha circulator distributing water to six zones, which are controlled by a bank of Taco zone panels and Zone Sentry valves.
The entire floorplan is heated with half-inch Uponor PEX, held in place by Legend Valve’s VersaTherm floating floor panel system.
The new mechanical room, wrapped in grey diamond plate aluminum and tongue-and-groove pine, occupies what had previously been a large closet. The 200-square foot room that used to contain the messy old mechanical system is now storage space.
“One of our big draws for making this a dual fuel system with a propane back-up boiler was that the gas boiler can be run off a battery back-up or small, cheap generator in the event of a prolonged power outage,” explained Carroll. “This makes the system more resilient than an all-electric system, which is important up in the mountains where the weather is unpredictable, and the power grid is less robust.
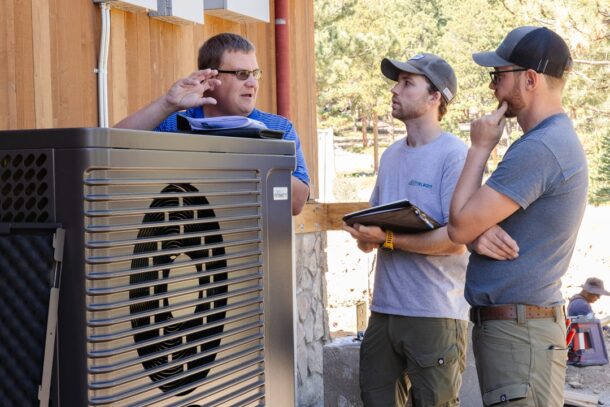
(left to right) – Chris Altenderfer, Tommy Carroll and Joe Ryan.
Evolution
Chris Altenderfer, manager of electric heating development at Burnham Holdings Engineering Company, joined Hansen, Ryan, Carroll and Akins onsite for system start-up. Watching through a Flir infrared device, they waited only a minute to see the heat pumps’ discharge fans turn purple, and the inch-and-a-quarter supply water lines turn red.
“I saw immediately that my concern about noise was unfounded,” said Akins.
“Even running at full speed, the Ambient units are quieter than any mini-split I’ve seen,” he added. “But this was completely new to me. This is the future of hydronics, and most of the homes we build have radiant systems. Peak to Peak Plumbing & Heating is on the cutting edge of the heating industry. Boulder is slowly forcing residents away from fossil-fuel appliances, so I’m excited that Joe is on the front end of the electric hydronic evolution.”
The homeowner is excited, too.
“As we undertook a big renovation, we knew that we wanted to plan for the future,” said the homeowner. “We went with this system for a combination of energy efficiency and the comfort of radiant heat. It helped that we have a great team, led by Joe Ryan and Tom Akins, who are both excited about the system. We couldn’t be happier.”