John Siegenthaler, P.E., a seasoned industry expert with over 30 years’ experience designing modern hydronic heating systems, author and popular guest speaker for the Coffee with Caleffi™ webinar series, returns on Thursday, July 23 at 12 noon CDT discussing Utilizing Thermal Buffering in Hydronic Systems. There are many types of hydronic systems where the rate Read more
Hydronics
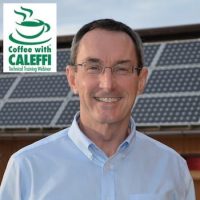
John Siegenthaler, P.E., a seasoned industry expert with over 30 years’ experience designing modern hydronic heating systems, author and popular guest speaker for the Coffee with Caleffi™ webinar series, returns on Thursday, July 23 at 12 noon CDT discussing Utilizing Thermal Buffering in Hydronic Systems.
There are many types of hydronic systems where the rate of heat generation is different from the rate at which the building requires heat. When only one or two zones require heating, the output of the boiler far exceeds the rate of heat demand. This can lead to heat source short cycling, reduced efficiency and shorter equipment life. Siegenthaler will explore how to avert such conditions by adding thermal storage to the system.
The one-hour educational webinars are free and are intended for contractors, designers and wholesalers. Please visit Caleffi’s website at www.caleffi.com for schedule details and registration.
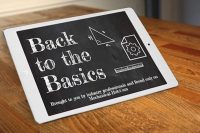
When Eric and John asked me to write a blog post on “Hydronics 101,” I have to admit I was a bit overwhelmed. Where on earth do you start? There’s boiler piping, pipe sizing, circulator selection, heat emitter selection, controls wiring, and so on. There are so many avenues to take when it comes to Read more
When Eric and John asked me to write a blog post on “Hydronics 101,” I have to admit I was a bit overwhelmed. Where on earth do you start? There’s boiler piping, pipe sizing, circulator selection, heat emitter selection, controls wiring, and so on.
There are so many avenues to take when it comes to “Hydronics 101” that choosing a starting point becomes quite a daunting task.
But then I thought of one of the very first training classes I ever did.
It was 1995 during a full-day program on radiant floor heating. We were going through the process of radiant design — figuring out installation method, tube spacing and water temperature. We were looking over charts and graphs to make heads or tails out of this radiant job when a fellow in the back of the room raised his hand.
“Don’t you have computer software that figures all this stuff out?”
Yep, we do.
“Then why are you wasting our time telling us all this? Just give us the software and we can go home.”
Ummm, it doesn’t quite work that way.
Design software, whether it’s for hydronics or forced air, is really nothing more than a fancy calculator. It does the arithmetic for you, and that’s about it. It doesn’t think for you, it doesn’t make decisions for you and it doesn’t tell you if you’ve input the wrong data.
It’s a calculator.
That’s it.
I like to ask folks in my classes how many of them have been formally trained in how to perform heat loss calculations. We call it “doing the math.”
As the years have gone by, fewer and fewer people raise their hands. No one’s teaching heat loss anymore, and I think it’s a shame. Knowing the actual heating load of a house or of a zone is the real “starting point” for beginning hydronics or for advanced hydronics.
How can you size a boiler if you don’t know the load? You can guess, but it’s just that: a guess. You can base your load on a standard BTU-per-square-foot multiplier, but that’s not a heat loss calculation. That’s just a guess with better PR. You can even measure the radiation, multiply by whatever multiplier you care to use and call that the load. But all that tells you is how much radiation is installed.
Good to know, but it doesn’t tell you the actual load of the house.
There’s no way around it: a good old-fashioned heat loss calculation is the only way of getting anywhere close to what the actual load of the house really is. Are “by-the-book” heat loss calculations 100% accurate? Nope — there’s so much fudge built in to the calculation methods out there that it’s a wonder we’re not all diabetic. But they’re still better than guessing.
During one of Taco’s Heat Loss classes a while back, the class was presented with a set of blueprints for normal, stick-framed house. There was nothing special about this house. It wasn’t super-insulated with super-low E windows or anything. It was a basic 2200 square foot ranch, with an outdoor design temperature of 7 degrees above Zero.
I asked the group, based on their years of knowledge and experience, to come up with their best, most accurate estimate for the heating load of the house. Their responses ranged anywhere from 55,000 BTUH on the low end to 125,000 BTUH on the high end.
The class then worked through an I-B-R based heat-loss analysis using the H-22 Heat Loss Design Guide (find it on Amazon under “Freaking Awesome Heat Loss Book!”). Using charts, graphs and real live, honest-to-goodness math, the class calculated the heat loss of that house to be a whopping 31,000 BTUH.
Well ain’t that a kick in the head!
Bottom line gang: any fundamentally sound hydronics system starts with the math. Heat load allows us to size our boiler and all of our piping as accurately as possible, which can have a major impact on materials costs. And only when we know the heating load and the size and length of the pipe that heat has to go through can we figure out what we need for a circulator, because load determines flow and pipe size and length determine head loss.
And weather impacts it all.
From there we can look at all the different types of circulators (steep curve, flat curve, single-speed, 3-speed, variable speed, Delta-T, Delta-P) and try to determine which one best fits the job we’re looking at – and no, there’s NO SUCH THING as “the only circulator you’ll ever need.” That’s a load of hogwash.
So where does “Hydronics 101” start? It must start with an accurate idea of what you’re trying to accomplish, which is to make sure this structure heats on what’s commonly referred to as “the coldest day of the year.” Now, if you’re simply replacing a dead circulator, there’s precious little math that needs to be done (but you still have to know about circulators and their impact on systems – that’s a future segment). But if you’re replacing a boiler or actually starting from scratch, the only right way to start is with a pad of paper, a scaled ruler, a pencil and a calculator. If John and Eric invite me back, we’ll walk through simple heat loss calculations done the old fashioned way. Software will do it quicker, but in order for software to be a tool and not a convenience item, it’s important to know why it came up with the numbers that it did.
As my old man used to say, “Knowing how is good, but know why is better. Because those who know ‘how’ will always work for those who know ‘why.’”
John Barba is training manager for Taco Inc.
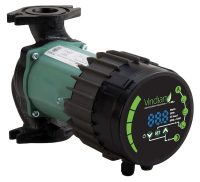
Taco’s now-expanded ECM, wet rotor Viridian line includes the VR3452 high efficiency wet rotor variable speed circulator for chilled and hot water applications, offering up to 34 feet of shut-off head and 52 gpm flow. All settings are accomplished with the user-friendly interface. The permanent magnet ECM motor saves up to 85% of the electrical Read more
Taco’s now-expanded ECM, wet rotor Viridian line includes the VR3452 high efficiency wet rotor variable speed circulator for chilled and hot water applications, offering up to 34 feet of shut-off head and 52 gpm flow. All settings are accomplished with the user-friendly interface. The permanent magnet ECM motor saves up to 85% of the electrical energy compared to conventional pumps.
The circulator offers auto mode (default), and proportional pressure control, constant pressure control, constant speed and night setback turndown. The LED displays watts, flow and RPM. It’s available in 115 or 230 volts and has standard flanges and is for easy installation.
The optional communication module provides: Ethernet and Modbus RTU communication, analog control input 0 – 10 V, three analog inputs/outputs, one relay output, main and standby operation. The VR3452 also comes with an industry standard flange.
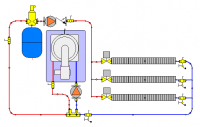
It’s a pretty common belief, at least in my neck of the woods, that condensing boilers and baseboard don’t “work well together” and the most cited reason is the need for high operating temperatures with baseboard. Of course they work, but how well? Awfully well in the vast majority of cases! Traditional boilers in the Read more
It’s a pretty common belief, at least in my neck of the woods, that condensing boilers and baseboard don’t “work well together” and the most cited reason is the need for high operating temperatures with baseboard. Of course they work, but how well? Awfully well in the vast majority of cases!
Traditional boilers in the USA are “non-condensing,” which means that they discharge flue gases at a high enough temperature that all water vapor is carried out of the flue. The water vapor is discharged with the other flue gases and never has a chance to condense to a liquid. The problem is that the hotter the flue gases, the more fuel is wasted and the less efficient the boiler.
So how does a condensing boiler work?
They absorb enough heat from the flue gases to drop the exhaust temperature below the point that the water vapor in the gases condenses into liquid and gives up its latent energy. Sounds great but the flue gas can only condense when the return water temperatures are 135F or less. The rated output of baseboard is realized at 180F.
How can this work at all, much less well? A few reasons!
First and foremost is the use of outdoor reset; can’t say I’m aware of any mod/con without integral ODR. Lowering the supply temperature by the use of ODR will of course yield lower return water temps, low enough to provide operation in the condensing mode for quite a bit of the heating season.
The second contributor to the viability of condensing technology with baseboard is the over-sizing of the baseboard itself; people have a pretty strong tendency to put in more baseboard than a heat loss calculation would indicate. While not as strong as the desire to over size boilers, the baseboard over sizing drive is definitely very dominant in the heating contractor genome. This, unlike boilers that are too big, is actually a good thing; more baseboard means the load can be met with lower water temperatures.
The third main factor is the design temperature; it really doesn’t get that cold all that often! That means the rest of the time, we don’t need to run 180F supply temperatures. Combine these and you will be running in the condensing range for the majority of the heating season, although certainly not all of it.
Dr T. Butcher of Brookhaven National Labs did a study on this topic in 2004 and found that 94% of the heating season time could be spent in condensing mode. It’s not light reading but if you are interested in an in-depth exploration of this topic, it’s available here: http://www0.bnl.gov/isd/documents/28709.pdf
There is another avenue of savings that mod/cons provide that is quite often overlooked: modulation. Modulation is varying the size of the fire in relation to the load. A cast iron boiler has two speeds — on and off. In comparison, a modulating boiler can vary its input, usually at a 4:1 or 5:1 ratio. A 100K Btu modulating boiler can operate from approx 20K Btu to 100K Btu. There is quite a bit of fuel to be saved by having the “right” size boiler on almost every day. I don’t know of any studies done to quantify the savings with modulation but based on anecdotal evidence over many years, I would place it in the 15% range.
A word of advice, don’t over size condensing boilers assuming the modulation will take care of it. I’ve seen 150K mod/cons in 50K heat loss homes and they never get off low fire except on DHW calls, not a recipe for efficiency. Properly applied mod/cons and baseboard can make for a long and happy marriage!
Robert C. O’Brien is the owner of Technical Heating Co. LLC in Mt. Sinai, NY. Robert serves as the Vice President of the national OESP chapter. See more from Robert in his blog “Boiler Sizing & Indirect Water Heaters”, “Converting from Oil to Natural Gas“ & “Heat Loss Calculation on Every Replacement?”
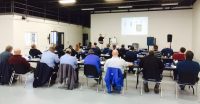
By John Mesenbrink Recently, Ron Passafaro, president & CEO of ECR International, was re-elected as Chairman of the Hydronics Institute through 2017. Passafaro, who has been a member of the Hydronics Institute his entire career and has served on its Executive Board since 2007, said, “I am honored and humbled to be re-elected by my Read more
By John Mesenbrink
Recently, Ron Passafaro, president & CEO of ECR International, was re-elected as Chairman of the Hydronics Institute through 2017.
Passafaro, who has been a member of the Hydronics Institute his entire career and has served on its Executive Board since 2007, said, “I am honored and humbled to be re-elected by my competitors and industry peers. Our industry continues to face increasing Federal and State regulation governing residential and commercial boiler efficiency standards. I am committed to working with both our government representatives and member companies to meet and exceed the North American market’s expectations.”
In the wake of this news, Mechanical Hub recently talked with Passafaro about ECR and the industry. The following is Ron Passafaro in his own words.
How did you get involved in the industry?
During the 1980s I was working for Abbott Laboratories selling medical equipment in New England when I received a phone call from John Reed of Dunkirk Radiator. John and I grew up together in the Dunkirk area and he told me that Dunkirk Radiator wanted to establish its own brand and start a national distribution channel to supplement their historical OEM business I had lived in Boston for five years and had no vision of ever moving back home to western New York but I took the time to meet with the Dunkirk management team and we talked about their objectives. After learning what they wanted to accomplish I found it very exciting and challenging to have the opportunity to create a national brand and distribution channel at age 29. I jumped at the opportunity and had a ball doing it. Clearly it turned out to be the best decision of my professional career.
What are some things you’ve learned throughout your career that have helped you in your current position?
I learned a long time ago about Servant Leadership and it is a philosophy that I very much believe in and try to live — not always successfully. Servant leadership is best explained graphically by turning the conventional corporate hierarchical triangle upside down. The most important persons in priority within a company is the customer and then those that interact and serve the customer directly (sales, tech support etc.) and then those that support the people that interact with the customer and so on. The CEO realizes that he or she is simply there to serve all the others and does so by ensuring they have the resources and support necessary.
Care — You won’t always be right and you won’t always get it right but if you care you’ll try hard enough to fix the times you miss.
Be Genuine — Don’t be who you think they want you to be because you’ll never be any good at it. No matter our position in life we are only good at being ourselves besides employees and customers can sniff out a phony in a heartbeat and you can’t ever recover from that. People forgive mistakes they don’t forgive deceit.
How has ECR navigated through the tough economy?
The tough economy has required us to get back to basics. We truly need to understand what the customer wants and what they are willing to pay for and that means asking good questions and listening. There isn’t time or resource to miss the mark on what the customer is willing to buy. In order for us to capitalize we need to develop solution based products that meet needs of today and the near future.
The market is changing so much faster than when I first started in the industry nearly 30 years ago. That is why roughly 1/3 of our salary workforce is dedicated to engineering and product development. Over the past four years we have been averaging three to four new or heavily modified product introductions per year. That’s pretty astounding when you think about it but that is what’s required by this demanding market. With that type of development activity we need to hold costs down and have done so by investing in our manufacturing operations to improve process control which increases throughput while increasing quality and reducing costs all at the same time.
How does business in the near term look?
We’re fairly bullish on the market over the near term and feel like the boiler market will continue to grow. I was traveling in New England during February calling on contractors this year and the common response to my question, “how’s business?” was if they could even get to the basements through the snow they had to repair versus replace because they couldn’t leave the homes without heat for that long. We have had two very cold, long winters in a row which has driven a lot of repair work that normally would have been replacement so I think the patch work is likely to give way to replacement in the near term.
Any new products or news in the offing?
Absolutely. We will be keeping with our recent trend of new product introduction and over the course of the next 12 months you’ll see us introduce a new product in each of our technology categories.
On the boiler side we’ll be introducing our first light commercial condensing models featuring our unique stainless steel heat exchanger design. Our Argo control platform will add the “Universal” switching relay that will feature a host of new features and technology in that segment.
The Olsen and Airco furnace platforms added a high efficiency, multi-positional low profile oil furnace this month that I suspect will redefine that segment.
And last we have just added our new 4-pipe chilled water recessed cassette air handler to our Comfortwave chilled water air handler line.
Describe the importance of contractor training.
I believe condensing furnaces were first introduced back in the late 1980s and over the past 30 years or so they have become a significant portion of the annual installed furnace base. Boiler installers didn’t have 30+ years to digest and get familiar with condensing technology. Though ECR was the first to offer a 95% AFUE boiler back in 1996 the rise of condensing boilers really has taken place over the last 10 years or so. Between technology and regulatory changes the entire residential boiler market has changed over the past several years. I have a tremendous amount of empathy for boiler installers today trying to keep up with that pace of change. The only way to keep up is through education so contractor training is hugely important to the dealer and the manufacturer. The contractor needs to understand the nuances of new equipment and technologies but more importantly how these new products are applied and what unforeseen challenges might result.
Our preferred method of training is to have contractors visit our corporate training center. This is our best venue for training hands on and they also see our research laboratory and manufacturing operations. Unfortunately, coming to Utica, N.Y., is not always possible so we have invested in additional live fire training centers at our newly opened offices in Hopkinton, Mass. and at in Dunkirk, N.Y. We believe in providing resources at the point of use so we invested in these additional facilities to spread our geographic coverage. Likewise, we continue to offer training in conjunction with our distributor partners at various locations around the country.
New for 2015, we introduced the Hydronic Boot Camp, which is a whole system approach to training our professional trade partners. We cover our condensing boiler products and technology but spend as much time covering system application and how to overcome commonly seen field installation issues. We bring together other component manufacturers like Taco, Centrotherm, Grundfos, Caleffi, Sentinel and others so that system component providers that installers use are in the same room training in a holistic, system approach. Ideally, students attend training at one of our 3-live fire facilities where they will learn while operating products. When contractors can’t come to training our locations we do offer many seminars around the country. If dealers go to www.hydronicbootcamp.com they can choose from the many dates and places for training by brand.
Boilers are now transforming themselves into intelligent, communicative integrated systems. In this era of the Internet of Things, how have ECR boilers and controls evolved?
So far most communicative controls have been focused on temperature monitoring and adjustment which has some sizzle for the end user but the actual value and utility to the trade is questionable.
Our Argo AR500 line has offered remote temperature monitoring with adjustment capability since the 1990s, mostly for snowbirds, so that functionality isn’t all that new. We have already proven out and deployed remote operation monitoring in one of our joint ventures the question is how to take that technology and know-how and adapt it in the boiler world where we typically do not develop the operating board.
More likely we will see boiler control intelligence sooner in the area of self-commissioning and adjustment within the modulating condensing segment. European control manufacturers are quickly developing these capabilities in an integrated structure that amalgamates all electronic and control functionality. This type technology begins to create a greater amount of value for the installer which is the customer group we are primarily focused on.
Finally, the last time you said, “Today is a great day,” you were doing what?
I’ve been very lucky and have been able to say that many times, but likely it would be just after sun up on an Adirondack lake ready to make my first cast or then again it might be on the first tee. Like I say, I’ve been lucky.
ECR International — In 1928 Earle C. Reed founded two separately owned and operated New York State companies, Utica Boiler and Dunkirk Radiator, the companies merged in 1999 and took our common founder’s initials as its corporate name — ECR International.