Oil-free compressor pioneer marks 10 years as a wholly owned Danfoss company Danfoss Turbocor, manufacturer and pioneer of the world’s first oil-free, magnetic bearing compressor for the HVAC industry, is celebrating its 10th anniversary as a wholly owned Danfoss company. Initially founded in 1994 and later becoming a joint venture with Danfoss in 2004, its Read more
Industry News
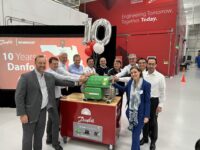
Oil-free compressor pioneer marks 10 years as a wholly owned Danfoss company
Danfoss Turbocor, manufacturer and pioneer of the world’s first oil-free, magnetic bearing compressor for the HVAC industry, is celebrating its 10th anniversary as a wholly owned Danfoss company. Initially founded in 1994 and later becoming a joint venture with Danfoss in 2004, its Turbocor® compressors have delivered versatile and unmatched efficiency, with low-Global Warming Potential compatibility, helping to reduce emissions while earning strong return on investment for customers.
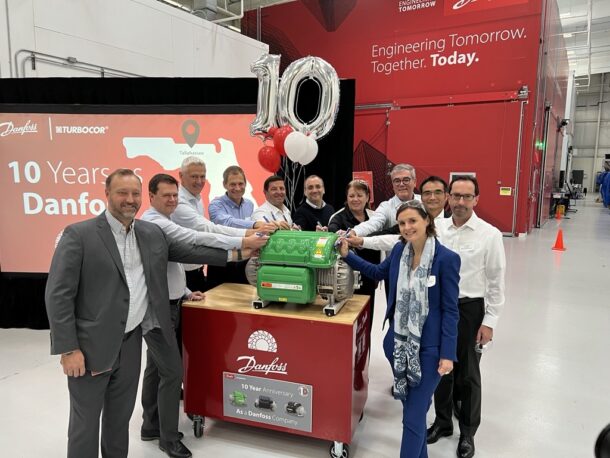
Ricardo Schneider, president of Danfoss Turbocor, stated: “From the beginning, we knew this technology was transformative; the cutting-edge technology combined with our strong manufacturing and sales network enabled us to provide our customers with solutions to improve operating performance and reach unprecedented energy efficiency levels.”
The unique oil-free, magnetic bearing technology of Turbocor compressors results in zero performance degradation over the life of the compressor, reducing maintenance and replacement costs. The permanent magnet motors and variable-speed drives provide efficiency at both full and part loads. Their flexibility to be used in air cooled, water cooled or evaporative cooled chillers operating across a wide range of applications such as comfort cooling, low temperature process, ice storage and heat recovery, has resulted in over 130,000 compressors being installed around the world.
Over the years, Turbocor compressors have been recognized with multiple industry awards, including the Alliance to Save Energy’s Innovative Star of Energy Efficiency award, the Air Conditioning, Heating and Refrigeration Institute’s 2022 Product of the Year and the U.S. Environmental Protection Agency’s Climate and Ozone Protection Award.
Globally, Danfoss Turbocor is continuing to grow its footprint, with an expanded facility in Haiyan, China opening next year, and the establishment of a configuration center in Nordborg, Denmark, at Danfoss’ corporate headquarters. The Nordborg site currently handles sales and service for Turbocor’s European customers; a new production facility is scheduled for completion in 2026.
At its headquarters in Tallahassee, Fla., Danfoss Turbocor continues to build collaborations with local institutions. In 2021, the company began a five-year partnership with FAMU-FSU College of Engineering, providing $750,000 of scholarships and research grants to first-generation or underrepresented minority students, to develop engineering talent in the local community and help students achieve their career goals. The company has also partnered with Tallahassee Community College on workforce development programs, such as its CNC machinist apprenticeship.
Soon, the company will celebrate another milestone: its new 167,000 sq ft manufacturing facility in Tallahassee is scheduled for completion in early 2024. The new facility will increase current manufacturing capacity to meet a fast-growing demand from American and international markets for high efficiency compressors for cooling and heating. The expansion is projected to create significant additional jobs in the Tallahassee area.
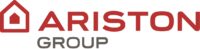
Ariston Thermo announced changes to its corporate identity in the United States and a move to new headquarters in Rhode Island. The company formally changed its name to Ariston USA. Formerly known as Ariston Thermo USA, the change reflects its identity as part of a global organization synonymous with change, innovation, and sustainability. Ariston USA Read more
Ariston Thermo announced changes to its corporate identity in the United States and a move to new headquarters in Rhode Island.
The company formally changed its name to Ariston USA. Formerly known as Ariston Thermo USA, the change reflects its identity as part of a global organization synonymous with change, innovation, and sustainability.
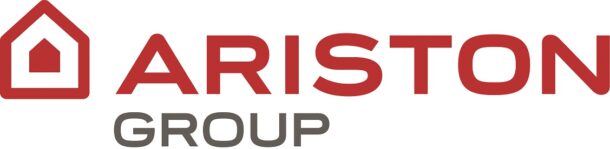
Ariston USA also announced it relocated its headquarters to the Innovation and Design District in Providence, R.I. As a business within the Cambridge Innovation Center (CIC) campus in the district, Ariston will be part of a building that creates a culture for innovation. CIC Providence offers shared and private workspaces that allow businesses to focus on cultivating new ideas and create new opportunities. Ariston USA was previously headquartered in New Bedford, Mass.
“Our new site is developed through state and local investment and created to promote technology, design and innovation,’’ said Andrea Monti Guarnieri, Ariston USA’s President and CEO. “Our office in the CIC building features a modern, open work environment to foster collaboration and teamwork.”
The office address is 225 Dyer St., 1st floor, Providence, R.I., 02903
“These moves provide an optimized environment for our current employees and improve our ability to find and attract future talent, setting Ariston USA on the path toward future, sustainable growth,’’ Monti Guarnieri said. “We look forward to continuing to create our future together with our partners as we remain true to our core values and our vision of sustainable comfort for everyone.”
Ariston designs, manufactures, and sells products under the brand names of HTP, Ariston and American Standard Water Heaters. The brands are recognized by homeowners, plumbing contractors, property owners and managers for providing reliable, energy-efficient, and innovative products to the market.
For more information, visit the Ariston Group website at www.aristongroup.com.
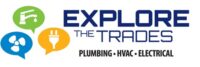
An industry-leading manufacturer of water heating and storage equipment gives $8,000 to further national nonprofit’s mission and raise awareness of skilled trades career opportunities Bradford White Corporation, an industry-leading manufacturer of water heaters, boilers and storage tanks, announces a new partnership with Explore The Trades that aims to bridge the technical talent gap in the service trades Read more
An industry-leading manufacturer of water heating and storage equipment gives $8,000 to further national nonprofit’s mission and raise awareness of skilled trades career opportunities
Bradford White Corporation, an industry-leading manufacturer of water heaters, boilers and storage tanks, announces a new partnership with Explore The Trades that aims to bridge the technical talent gap in the service trades and advance positive public awareness of the plumbing and HVAC industry.
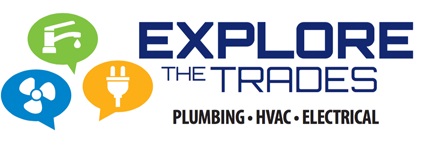
Explore The Trades, a nonprofit organization founded in 2005, is bridging the technical talent gap to the skilled trades of plumbing, heating, cooling, and electrical by raising awareness of the skilled trades, serving an integral role in lessening the skilled labor gap and acting as a partner to both education and industry with the goal of creating the next generation of technicians.
Through Industry Forward®, its signature charitable giving program developed to help advance the industry and raise awareness of career opportunities, Bradford White Corporation is donating $8,000 to Explore The Trades. The contribution supports the creation of 1,000 poster kits showcasing careers in the skilled trades that will be distributed to educators and counselors across North America.
“Over the past generation, awareness of the skilled trades has nearly become extinct,” said Kate Cinnamo, executive director at Explore The Trades. “Yet many students, parents and educators lack access to information about the career opportunities in the service trades, manufacturing and distribution that are vital to our communities. We’re proud to partner with Bradford White to close that information gap. Their support enables us to serve as the conduit between industry and education so we can engage the audiences who are vital to the growth of the trades.”
Bradford White partners with nonprofit organizations and technical schools to educate individuals and families on the importance of the skilled trades and the role that industry professionals provide in the health, safety, sanitation, and infrastructure of their communities through strategic grant funding that supports workforce development training and education programs and industry career opportunities, events, and partnerships.
“We are thrilled to partner with Explore The Trades and expand our reach by connecting with students, parents and educators in an exciting new way,” said Rebecca Owens, senior communications manager for Bradford White. “As more teens and young adults consider the financial impact of attending a four-year college, we will continue to advocate for the option of a stable career in an essential industry. Joining with Explore The Trades to pursue our shared mission helps us reach more individuals that may be interested in the plumbing and HVAC fields than ever before.”
For more information about Bradford White Corporation’s Industry Forward® initiative, visit www.bradfordwhitecorporation.com/giving/.
Explore The Trades is a nonprofit with a mission of bridging the technical talent gap to the service trades of plumbing, heating, cooling, and electrical. For more information, please visit explorethetrades.org/who-we-are/.
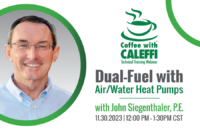
Air-to-water heat pumps provide a way to migrate existing hydronic heating systems supplied by fossil fuel boilers to sustainable electric energy. In many projects there are compelling advantages for retaining the existing boiler and adding the heat pump to create a “dual-fuel” system. These systems will likely be the most common application for air-to-water heat Read more
Air-to-water heat pumps provide a way to migrate existing hydronic heating systems supplied by fossil fuel boilers to sustainable electric energy. In many projects there are compelling advantages for retaining the existing boiler and adding the heat pump to create a “dual-fuel” system. These systems will likely be the most common application for air-to-water heat pumps in the near future as carbon reduction regulations reshape the market.
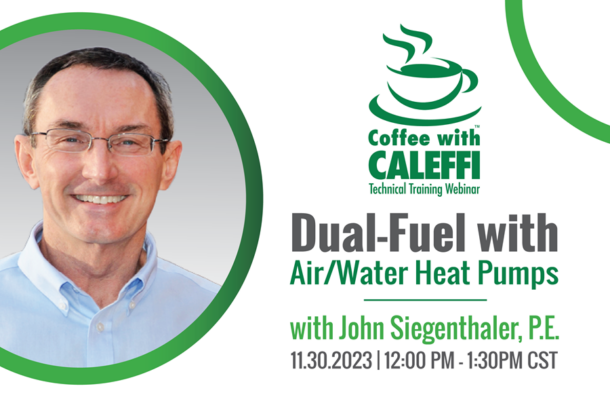
You’ll learn:
→ What’s the highest water temperature an air-to-water heat pump can produce?
→ Are buffer tanks always needed in systems with air-to-water heat pumps?
→ Should air-to-water heat pumps be connected in series with boilers?
→ Can air-to-water heat pumps be retrofitted to systems that use fin-tube baseboard?
Hydronics guru John Siegenthaler, P.E. will discuss the benefits of dual-fuel systems while examining the technical details for piping and controls in this 90 minute extended Coffee with Caleffi webinar edition on Thursday, Nov. 30 at 12:00 p.m. CST.
Siegenthaler is a seasoned industry leader and passionate teacher, eager to share his over 40 years’ experience in the understanding and proper application of water-based engineering principles with our audience.
A Certificate of Attendance is emailed to attendees following the event for continuing education audits. The monthly educational webinars are free and are intended for engineers, contractors, designers and wholesalers.
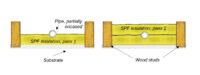
New Technical Document and Details Proper Steps for Use A new technical document that addresses techniques for the safe and proper use of spray polyurethane foam insulation on and around plastic pressure pipe materials has been published by the Plastics Pipe Institute, Inc. (PPI) with input from the Spray Polyurethane Foam Alliance (SPFA). Prepared by Read more
New Technical Document and Details Proper Steps for Use
A new technical document that addresses techniques for the safe and proper use of spray polyurethane foam insulation on and around plastic pressure pipe materials has been published by the Plastics Pipe Institute, Inc. (PPI) with input from the Spray Polyurethane Foam Alliance (SPFA).
Prepared by PPI’s Building & Construction Division, PPI TN-69 Recommendations when Applying Spray Polyurethane Foam Insulation on and around Plastic Pressure Pipes & Fittings discusses the proper application of spray polyurethane foam insulation to avoid damage due to heat generated by the foam. Pipe and fitting materials include CPVC, PEX, PEX/AL/PEX, PE-RT, PP-R, PP-RCT, PSU, PPS, PPSU, and PVDF.
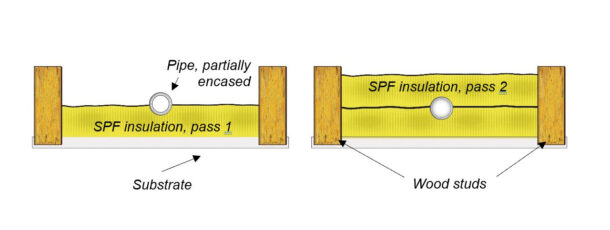
Figure 1: The first layer of SPF insulation is stopped when it reaches the pipe (left), just barely touching or encasing it. After sufficient cooling time, the second layer of SFP insulation is sprayed over the pipe to the required thickness (right).
PPI and SPFA recommend that when there are plastic pipes and fittings in a wall, ceiling, or floor cavity, the SPF installer should apply one layer of foam until it touches the pipe but does not encase the pipe. SPF installers should let the first layer of foam cure for a sufficient amount of time while heat is released from the foam and the pipe remains partially exposed before installing the second layer of foam. These procedures are described in detail within PPI TN-69.
Plastic pressure pipes and fittings are commonly used in applications such as hot- and cold-water plumbing, fire protection, and hydronic heating and cooling systems, including radiant distribution systems. In certain instances, pipes and fittings are installed inside areas that must be insulated, such as within a ceiling or wall cavity. In other installations, the pipes and fittings themselves must be insulated to reduce the transfer of heat through the pipe wall.
According to the SPFA, Spray Polyurethane Foam, or SPF, is a high-performance insulation material commonly used in homes and buildings of all types, and has been used as insulation for decades.
“The spray polyurethane foam curing reaction is exothermic,” explained Richard Duncan, Ph.D., P.E., executive director of SPFA, “which means that heat is generated during the foam reaction. The heat of reaction is highly dependent on the SPF formulation and is also based upon the overall intended application or lift (i.e., layer) thickness installed. Peak temperature within the layer of foam typically occurs within 5 to 15 minutes of application, followed by gradual cooling.”
According to SPFA documents, the chemical reaction that takes place during the application and curing of SPF will generate exothermic temperatures above the 120°F – 130°F setpoint temperatures of the proportioner and hoses. Peak temperatures at the mid-thickness of a pass can exceed 200°F for several minutes and reach peak temperatures 250°F – 275°F for a minute or two, especially for closed-cell SPF, when applied at the maximum pass thickness.
“Plastic pipes and fittings in both residential and commercial plumbing, residential fire protection, and most hydronic applications are typically required to have pressure ratings at 180°F (82°C) operating temperature,” explained Lance MacNevin, P. Eng., director of engineering for PPI’s Building & Construction Division.
MacNevin continued, “The plastic pipes and fittings referenced in PPI TN-69 will withstand short-term exposure to temperatures above 180°F. However, exposure to temperatures above the rated operating temperature of each material, which may occur if pipes are encased in a thick pass of closed-cell SPF, are likely to have negative effects on these materials, potentially leading to premature failure. It is important that SPF insulation is installed correctly to prevent overheating of pipes and fittings.”
Access the full content of PPI TN-69 at https://plasticpipe.org/common/Uploaded%20files/Technical/TN-69/PPI%20TN-69.pdf or by scanning:
Additional information and data about pressure pipe materials used for plumbing and mechanical systems are available from the PPI Building & Construction Division at www.plasticpipe.org/buildingconstruction