Neutrasafe Corp., in Rockland, MA, now offers an automatic hydronic and thermal solar system feeder, in addition to their newly-expanded line of condensate neutralizers. The System Feeder introduces fluid and accurately maintains pressure in closed-loop systems. The easily-installed unit is designed for use with water or glycol solutions of up to 50 percent. A digital Read more
Whats Next
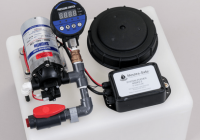
Neutrasafe Corp., in Rockland, MA, now offers an automatic hydronic and thermal solar system feeder, in addition to their newly-expanded line of condensate neutralizers.
The System Feeder introduces fluid and accurately maintains pressure in closed-loop systems. The easily-installed unit is designed for use with water or glycol solutions of up to 50 percent. A digital pressure control allows individually adjustable cut-in and cut-out pressures points between 1 and 50 PSI, with a secondary pressure switch cut-out at 60 PSI.
The System Feeder’s six-gallon tank is equipped with a set of dry contacts to connect to a remote alarm if the fluid level gets too low, and can be used with a standard 115VAC outlet. Because it features a commercial-grade diaphragm pump with internal check valve, it eliminates need for a PRV and backflow preventer. The System Feeder also limits the amount of fluid that can be lost in the event of a major break.
Neutrasafe now also offers vertical condensate neutralizers. The tube-type neutralizers provide all the benefits of their standard 2-inch models for applications where a horizontal configuration isn’t ideal. Two vertical models serve high-efficiency, gas-fired appliances up to 220 MBH, and feature a stainless screen and media-filled sack for simple recharging. The media-sack recharge kits, which can be used in all 2-inch Neutra-Safe® neutralizers allow for an easier recharge process.
All Neutra-Safe® products are designed by a Master Plumber with more than 30 years in the industry, and are built in the U.S.
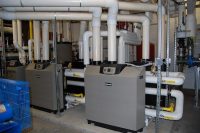
Property owners and facility managers can realize significant energy savings and improved comfort in a facility or building by upgrading a 20 to 30 year-old boiler with a new, more efficient unit. A more efficient new cast iron or high efficiency condensing boiler uses less fuel, and provides more comfort for the building occupants while Read more
Property owners and facility managers can realize significant energy savings and improved comfort in a facility or building by upgrading a 20 to 30 year-old boiler with a new, more efficient unit. A more efficient new cast iron or high efficiency condensing boiler uses less fuel, and provides more comfort for the building occupants while building owners benefit from years of trouble-free operation.

Breaking Down Commercial Boiler Efficiency Levels
Boilers are generally considered “commercial type” for having heating input between 300,000 Btu and 12,500,000 Btu. To be sold in the U.S., these boilers must meet the newest energy efficiency standards, effective since March 2, 2012, as defined by the Department of Energy (DOE) and specified in the Code of Federal Regulations, 10 CFR431.87:
Condensing boilers have efficiencies typically above 90% and thus greatly exceed the current DOE minimum prescribed efficiency levels.
Why should business owners and facility managers consider buying a more efficient boiler? For one, replacing a 65% efficient cast iron boiler with a new one that has 84% thermal efficiency or higher will result in significant fuel savings. Space heating combined with water heating accounts for 20.3% of the total energy bill making it the largest energy consuming systems in a commercial building.

Source: U.S. Department of Energy (DOE) Buildings Energy Data Book – table 3.1.4 2010 Commercial Energy End-Use Splits, by Fuel Type (Quadrillion Btu)
Property owners with high efficiency boiler systems often report energy cost savings of 25% and higher on their heating bills. Additionally, modern boilers are typically quieter in operation, more technologically advanced and simply better at heating the building. They also offer improved heating controls that can make rooms and offices more comfortable.
Choosing the Right Boiler
When choosing the right boiler, the specifying engineer has to answer the following questions:
1. Is it a new installation or replacement?
– The answer to this question will greatly influence most of the other variables such as the boiler size, type of fuel to be used, type of heating system (water or steam), required minimum floor space, access space (clearance) for maintenance and weight limitations. If the project is a retrofit, the building owner may ask the consulting engineer to determine if it will make sense to change the system from steam to water.
– In installations limited to heating, hot water boilers will be more efficient than steam simply because of their lower combustion temperatures, resulting in less energy consumption. Process installations, on the other hand, often require steam for high temperature applications such as sterilization in hospitals. Dehumidification would be another example where steam boilers would make more sense than water. Finally, existing steam systems are much easier to retrofit using one-for-one boiler replacements due to simplicity and lower overall project cost. At times, customers are sold on the idea of retrofitting steam systems to water systems. This is recommended in situations where the building operating engineer or servicing crew is not very experienced in steam applications and maintenance of these systems. Because of this issue, there are a large number of steam systems that are either underperforming or having frequent breakdowns. It should be noted, however, that the cost of converting a steam system to a water system can be quite high and may result in a long payback.
– Another important question for retrofit applications is: how difficult is the access to the mechanical room? Some condensing boilers offer narrow design (less than 33 inches wide), low height and can be split into two separate sections for easier navigation around tight corners and access to small elevators. Splitting the boiler will also reduce the overall weight, making it easier to move in areas with weight limits such as elevators. New constructions, on the other hand, have typically greater flexibility when it comes to choosing the boiler.
2. What type of fuel is going to be used (natural gas, propane or oil)?
– Natural gas is typically less expensive than propane or oil but it may not be readily available, especially when it comes to rural or remote areas. Oil prices have recently come down and this type of fuel is becoming more attractive and alternative solution to propane.
– Does the building owner need a back-up fuel? Alternative fuels such as propane or oil could provide heat when there is no natural gas available. In cases like this, dual fuel burners (gas and oil) offer alternative solutions. Most high efficiency boilers can be easily converted from natural gas to propane.
3. Is the initial installation cost and longevity of the boiler more important than the overall operating cost or efficiency?
– The cast iron (standard efficiency) boilers typically offer lower installation costs, a longer product lifecycle and require less maintenance than condensing boilers. The condensing (high efficiency) boilers tend to be more expensive but have more sophisticated controls and, under the right operating conditions, can offer higher return on investment. The amount of savings will vary and depend on the application (high temperature vs. low temperature systems), seasonal run hours, utility rates, part load conditions and boiler efficiency.
In high temperature systems (fan coil, finned tube baseboard, cast iron baseboard), there will be fewer opportunities for the boiler to condense. Savings, as a result, will be much lower than when the boiler is used in low temperature applications, such as under-the-floor radiant tubing. Cast iron boilers simply thrive in higher temperature systems, like those that utilize radiator and baseboard emitters. A condensing unit operating mostly in high temperature applications may still be more efficient than a cast iron boiler with the same heating output, but its efficiency won’t be fully maximized. The same condensing boiler operating in lower operating temperatures (part load applications, seasonal shoulders, multiple boiler oversized systems) will be much more efficient.
It should be noted that the newest models of non-condensing cast iron boilers today are far more efficient than the boilers made 20 years ago. To illustrate, the Weil-McLain 88™ Series 2 Commercial Gas Boiler line offers up to 87.5% combustion efficiency and is ideal for commercial applications that require energy efficiency and longevity. It can use different types of burners carefully matched for quieter ignition, longer life and improved combustion. These boilers have easily accessible controls, vertical flue ways, large combustion chambers and cleanout ports for easy and quick servicing.
Climate also plays a major role in boiler selection. Investing in the highest-efficiency heating system makes the most sense if the facility is located in a cold weather region with many run hours. In climates that are milder with lower annual heating costs, the extra investment required to go from 85% to 90 or 95% may be more difficult to justify.
Additionally, many local utilities offer rebates for boiler replacement. In some cases, the local efficiency rebate can offset 50% or more of the boiler price. Some quick research could help you take advantage of any available rebates in your area. Then, bring in a heating contractor to size the unit so that it’s most efficient for the space. This will ensure that the boiler operates at its optimum capacity and is most cost effective.
Know When It’s Time to Replace
It is not uncommon for property owners or managers to wait until a boiler completely breaks down and are suddenly faced with no heat. To make things worse, these types of failures happen when there is real need for heat (for instance, a very cold day) and since the failure is unexpected, there are rarely emergency funds allocated to fix the problem.
The following are some warning signs that it’s time to replace an old unit:
• Age: Condensing boilers haven’t been on the market for a long time and therefore it is hard to predict their longevity. With proper maintenance, they are expected to last at least 15 years or longer. Weil-McLain boilers come with a ten year non-prorated heat exchanger warranty and two year parts warranty. Cast iron boilers, on the other hand, should be considered for replacement if they have been operating for more than 20 or 30 years. Some of these boilers can last even up to 50 years or longer, but even with decent annual maintenance, their efficiencies are much lower than today’s cast iron boilers. Often times, the energy savings from a new boiler replacement alone practically pays for the cost itself within a year or two.
• Energy Expenditures: Be mindful of any increases in energy expenses. If energy bills are slowly rising it may be due not only to the age of the boiler but also due to increasing costs of the boiler maintenance. If a boiler requires constant servicing, the system has likely become less efficient. One should consider upgrading to a more reliable, durable unit such as a cast iron unit. Additionally, a noisy unit may also be a sign that it’s time for an upgrade.
• Increased frequency of failures: This is a clear indicator that the boiler is due for either a major overhaul or replacement.
• Leaks: A boiler that leaks or requires additional make-up water could be nearing the end of its lifecycle. By replacing the existing unit, the building manager or owner can avoid costly floods and critical boiler or property damage.
• Comfort: If you notice that some rooms in a building are too hot or too cold or have varying temperatures throughout the day, it’s possible that the unit and its controls are no longer effective or the facility may benefit from more efficient controls.
Conclusion
Even if a boiler isn’t immediately failing, upgrading to a new system can offer significant benefits. By planning the change, rather than facing an emergency in the throes of winter, building owners and managers can realize energy savings, a more comfortable facility, tenant retention, improved heating reliability and increased property value.
There are some great resources available online for facility managers and building owners to evaluate their return on investment (ROI) when purchasing a boiler. One of the most popular boiler ROI tools is Weil-McLain’s SlimFit ROI Calculator, available on the SlimFit website: http://slimfitboiler.com/roi-calculator/
John Kopf is Senior Product Manager with Weil-McLain, a leading North American designer and manufacturer of hydronic comfort heating systems for residential, commercial and institutional buildings. Founded in 1881, Weil-McLain is based in the Chicago suburb of Burr Ridge, Ill., with manufacturing facilities in Michigan City, IN. and Eden, N.C., and regional sales offices throughout the United States.
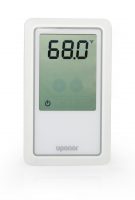
Available April 2016, the Uponor Heat-only Thermostat is designed for precise temperature control of hydronic radiant floor heating systems in residential applications. The thermostat includes a floor sensor to measure floor temperature for enhanced comfort and to protect the floor surface from overheating. The thermostat provides operative temperature sensing and two-wire power sharing for easier Read more
Available April 2016, the Uponor Heat-only Thermostat is designed for precise temperature control of hydronic radiant floor heating systems in residential applications. The thermostat includes a floor sensor to measure floor temperature for enhanced comfort and to protect the floor surface from overheating. The thermostat provides operative temperature sensing and two-wire power sharing for easier installation. Additionally, the capacitive touchscreen features a color-enhanced display for an intuitive user experience, all packaged in a slim, aesthetic design.
For more information about the Heat-only Thermostat with Touchscreen, visit us at www.uponorpro.com
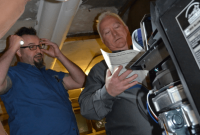
Recently, I had the chance to “participate” in an onsite boiler training session at Northwestern University, Evanston, Ill. There I found Mike Gambill, commercial sales specialist, Weil-McLain, training the in-house university facility maintenance staff on one of the seven WM Ultra™ boilers Northwestern currently uses. Accompanying him was Julian Webb, product manager with Weil-McLain and Read more
Recently, I had the chance to “participate” in an onsite boiler training session at Northwestern University, Evanston, Ill. There I found Mike Gambill, commercial sales specialist, Weil-McLain, training the in-house university facility maintenance staff on one of the seven WM Ultra™ boilers Northwestern currently uses. Accompanying him was Julian Webb, product manager with Weil-McLain and Jon Sabin, HVAC sales Engineer, RC Sales and Service. “We make ourselves available to our customers for on-site assisted start-up training and maintenance training. It’s important to us for building and maintaining relationships with our customers—and it helps their relationships with their customers,” says Gambill.

Mike Gambill (r), walks through the Ultra set-up with a maintenance employee at Northwestern University.
“We’re confident in the abilities of the contractors and installers responsible for installing and maintaining Weil-McLain products and believe that being on-site to show them a few more ins-and-outs and extra features they might not have known about otherwise helps to increase their familiarity and confidence levels with our products,” says Greg Pickens, director of learning and development.
Training, especially onsite—whether it is going out to the jobsite or bringing the contractor in—is so important in this era of keeping up with the technology, keeping on top of the troubleshooting, and keeping one step ahead of the competition. And I know this may sound cliché, but it is important to have guys get their hands on the equipment. “We are willing to get our hands dirty in the field to make sure our customers understand our products the way we do. We think it’s important to show that we stand by our products and are there when our customers need us,” says Gambill.
Training, training and more training
At the School Of Better Heating, offered at regional locations in addition to Weil-McLain locations, the company offers a broad course outline that extends beyond its products, including partnered training with some key component suppliers such as Taco® and Sentinel®.

Don Gregory, Weil-McLain Machine Shop and Maintenance Manager, leads a tour of the boiler foundry at Michigan City, IN.
Weil-McLain offers training and factory visits to design professionals and engineers at both of its manufacturing locations (Eden, NC and Michigan City, IN) and several tiers of technical training based on the individual expertise of the professional. Commercial boiler sales training is offered multiple times per year at its factory in Michigan City, Ind. to ensure that the organizations and sales people who represent its products are fully equipped to meet market needs and nationwide distribution.
The School of Better Heating runs from March to September. It is a one- or two-day event where topics like Hydronics 101, Circulator Relays, Multiple Boiler Setup, High Efficiency Control Logic and Operation, etc. are covered. Weil-McLain does this in a different location each month, including its facilities in Eden and Michigan City.
Weil-McLain also offers a free one-day training event for contractors called Weil-McLain Open House, hosted at its Mid-Atlantic office in Mount Laurel, New Jersey every other year in the fall. The main function of this event is to create a training environment for contractors with 45-minute hands-on outdoor sessions that cover high efficiency condensing gas boilers, steam, hydronics 101, commercial boilers and more as well as partnered training with manufacturers such as Beckett®, Hydrolevel®, Honeywell® and Carlin®, just to name a few.
Weil-McLain spends a large amount of time and energy training a variety of industry professionals. They have training for basic product overviews as well as content for multiple zone wiring in a commercial environment. Although online training currently doesn’t exist, it is definitely on the radar and is important for the future of training at Weil-McLain.
The Buzz
Weil-McLain has been busy lately. Just this past year, Weil-McLain introduced its newest and most advanced high-efficiency condensing boiler: the 95% AFUE Evergreen™. The Evergreen features cutting-edge technology with simple controls, flexible functionality for multiple applications, simple installation and maintenance, and a durable design. “Our new Evergreen boiler was built with contractors in mind. It was developed after detailed analysis and testing by Weil-McLain engineers plus extensive feedback from customers,” said Julian Webb, product manager with Weil-McLain. “The durable unit is adaptable for most heating demands to effortlessly extend comfort levels to every area of a property from multiple in-home zones to pools for years to come.”
Weil-McLain also recently enhanced its line of popular SlimFit™ high-efficiency condensing gas boilers with improved controls, communication and usability.
In fact, All Weil-McLain commercial high efficiency boilers feature connectivity for building automation systems (BAS) and its broad product line interfaces with various smart thermostats such as Nest. Both boiler-to-boiler and boiler-to-building connectivity is built into its products.
As heat loads become smaller with better building practices, Weil-McLain is designing boilers with smaller overall input ratings, as seen the Evergreen boiler, which is designed around control capabilities to meet large residential to light commercial heating comfort needs. Flexible (in various regards) in a compact design. All but one of its condensing boilers has modulation capability to match the building heat load.
Boiler Bucks
The contractor loyalty program, Boiler Bucks—launched in mid-2015—was created to reward contractors for purchasing products as well as to provide more opportunities for contractors to be heard and give feedback. In addition to receiving Boiler Bucks, or points, for registering their Weil-McLain purchases on the Boiler Bucks website, contractors may participate in surveys and quizzes to earn points and can redeem them on the site for rewards like tools, gift cards, work gear and apparel. Customers can stay up-to-date on its latest promotions by signing up on the Boiler Bucks website (www.wmboilerbucks.com).
Weil-McLain History
Weil-McLain®, a division of the Marley-Wylain Company, is a leading North American designer and manufacturer of hydronic comfort heating systems for residential, commercial and institutional buildings since 1881. We have manufacturing facilities in Michigan City, Indiana and Eden, North Carolina, along with regional sales offices throughout the United States and an administrative office in Burr Ridge, Illinois. Building on a reputation of quality and innovation, we are committed to creating Simplified Solutions for our Complex World™.
Weil-McLain is one of the oldest boiler manufacturers in the United States and it is celebrating its 135th anniversary this year! The company has a foundry in Michigan City, Indiana, which is something you rarely see these days with American manufacturers. In addition to cast iron, Weil-McLain manufactures its boilers with stainless steel and aluminum heat exchangers.
Architects, engineers, contractors, facility managers and homeowners alike rely on Weil-McLain for their comfort heating needs. Installed in homes, offices, schools, restaurants, hotels and other facilities throughout North America, the Weil-McLain brand is among the most respected and often used in the building industry.
Weil-McLain’s hydronic boilers and indirect-fired water heaters integrate the latest in advanced controls and materials including cast iron, stainless steel and aluminum heat exchanger technologies. The reliability and energy efficiency of its products has helped to make Weil-McLain industry leaders. Products are engineered with aesthetics, functionality, safety and structural tolerance in mind. By combining expertise with the responsiveness of support operations, Weil-McLain provides its customers with added value and peace of mind.
To learn more, visit www.Weil-McLain.com.
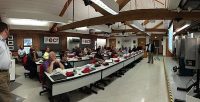
ECR International, with headquarters in Utica, manufactures heating and cooling products under a family of brand names including: Dunkirk, Utica Boilers, Olsen, Airco, Pennco, RetroAire, Argo and EMI. The company markets its products in the U.S., Canada and China. In December of 2015, company shareholders approved the sale of the company to BDR Thermea, Dutch Read more
ECR International, with headquarters in Utica, manufactures heating and cooling products under a family of brand names including: Dunkirk, Utica Boilers, Olsen, Airco, Pennco, RetroAire, Argo and EMI. The company markets its products in the U.S., Canada and China.
In December of 2015, company shareholders approved the sale of the company to BDR Thermea, Dutch heating products group with its global headquarters in Apeldoorn, the Netherlands. BDR Thermea is the parent company of international heating brands, including De Dietrich, Baxi, Remeha, Brötje, Chappée and Baymak.
“We are pleased that ECR shareholders have supported this transaction which now allows us to access the tools necessary to compete in all technology and market segments,” said Ron Passafaro, president and CEO of ECR International.
“I’m excited to welcome ECR International to our family of leading, international brands,” added Rob Van Banning, CEO of BDR Thermea. “BDR Thermea is on its way to become the leading heating manufacturer and distributor in the U.S. For us, this acquisition represents a first step of a bigger strategy to increase market share and presence worldwide.”
All BDR North American operations will be integrated into the newly established company, which will continue to operate under the ECR International name and be managed by the current ECR team led by Passafaro.

The current management structure and manufacturing facilities in Dunkirk and Utica, N.Y. will also remain the same. Products will continue to be sold under the ECR family of brands, which customers have known since 1928.
Continued investment into engineering and manufacturing has helped ECR to remain innovative and competitive in an ever-changing industry. New and innovative products will be added to ECR’s brands and facilities, which was the subject matter of an initial visit by BDR CEO Rob Van Banning and other leaders to the company in January.
ECR distributors and installing contractors will soon have access to a robust product offering with more choices to meet residential and commercial customer’s needs and applications. “The relationship allows BDR to get mature manufacturer and distribution channels in the U.S., and for ECR it allows for volume and critical mass leverage,” said Passafaro.
Products & Services
As an expert in hydronics, says Don DeCarr, product manager, ECR capitalized on its unique heat exchanger designs and developed a larger boiler for the light commercial market with the new 399 Model modulating condensing boiler, which features 96% thermal efficiency, a 5:1 turndown ratio and a 399 MBH input with a small footprint. There is a polypropylene flue collector and the unit is tested at 150 psi MAWP. It is approved for PVC, CPVC and polypropylene venting.
The unit is also CSD 1 compliant with built-in manual reset low water cut off and manual reset high temperature limit, and an outdoor temperature sensor is included. The user display interface is easy to program and has a text display. The main component of the boiler is the innovative patent pending heat exchanger that utilizes 316L/444 Stainless Steel fin tubing. It is vertically positioned, low maintenance, and self-cleaning. ECR’s engineers at the Research and Development Center, located in Utica, designed the heat exchanger.
“We have many new products that we are working on in the near future,” said DeCarr. At the top of the list is a commercial condensing boiler, product complements to the oil fired furnace line, and high SEER variable speed heat pump ductless split systems.
“ECR is also excited to be working on high-efficiency wall-hung boilers to add to the product lineup in 2016. We are looking at high efficiency, a modulation level of 7:1, self-calibration, gas adaptive control and other great features in a combi/space heat only wall hung application,” added DeCarr.
Training Programs
ECR is fully committed to a robust training program. “We have been training the installing contractors since we first introduced condensing boilers back in 1996. In 2014 ECR expanded our training program with the introduction of the Hydronic Boot Camp training program and I am pleased to say that this program is still going strong into 2016. Course content includes many aspects of modern condensing boilers including product selection, meeting with the customer, commissioning techniques, efficiency of the heating equipment/system and troubleshooting,” said DeCarr.
In 2015, ECR revamped its training centers and added a third in New England. Live firing is now available in a classroom setting in Utica and Dunkirk, N.Y. locations and Hopkinton, Mass.
Bet You Didn’t Know
ECR stands for the initials of the company’s founder Earle C. Reed. Reed founded Dunkirk Radiator and Utica Radiator in 1928. Today the Utica and Dunkirk brands are still very strong in the hydronics industry.
ECR is has a long history of innovations: the company was the first to introduce 95% efficiency boilers to North America in 1996; it was the first to introduce integral draft diverters to gas boilers; the first to introduce swing-out burner doors on oil boilers; and ECR was also the first to feature a full line of condensing wall-hung boilers with built-in primary/secondary piping in 2010.