When Delta Electronics (Americas) expanded its headquarters in Fremont, Calif., they leaned on the company’s brand spirit: “Smarter. Greener. Together.” Founded in 1971, Delta’s mission is “To provide innovative, clean and energy-efficient solutions for a better tomorrow,” and the headquarters is a shining example of creative thinking paired with a desire to protect the environment. The company takes advantage of the latest in advanced energy-efficient research and product development, and the American headquarters is their 13th green building worldwide.
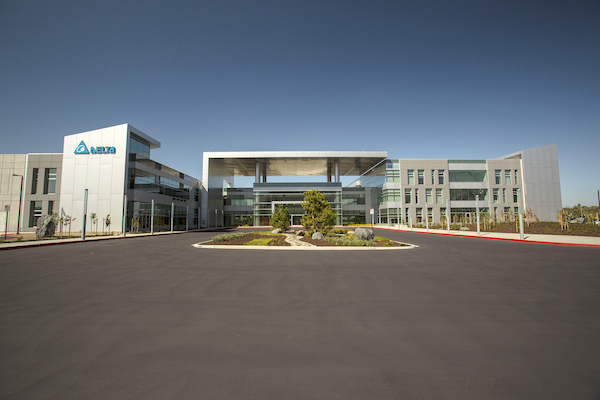
To help meet the LEED Platinum and net-zero energy building standards, the company chose to go with a radiant heating and cooling system from Uponor. Originally specified for a conventional radiant tubing installation, the mechanical contractor, ACCO Engineered Systems, a contracting firm with locations throughout California, suggested changing the specification to Uponor’s Radiant Rollout Mats for a faster, more efficient and consistent installation. ACCO had recently completed several large commercial projects using the mats, including the Pier 15 Exploratorium in San Francisco and SMUD (Sacramento Municipal Utility District) building.
ACCO, in conjunction with Sean Timmons at Timmons Design Engineers—now ALFATECH-Timmons—and Osborne Company—an Uponor rep firm—designed the radiant heating and cooling system using the mats for the 178,000-square-foot campus that includes a 38,000-square-foot warehouse. The radiant slabs are the primary cooling and heating systems in the campus buildings so it was crucial for the design to ensure comfort as well as the desired energy efficiencies.

Due to their previous experience with the Radiant Rollout Mats, ACCO spent a considerable amount of time up front designing the slab construction, the sequence of the slab construction and how the mats would be fabricated to align with the installation thought process. “We eliminated a lot of potential problems up front – lessons that we learned on other projects,” said Jonathan Bell, ACCO project manager.
It took five months for three dedicated crew members plus one runner to install 138,000 feet of tubing with the Radiant Rollout Mats. It would have taken much more time—and labor—to install the tubing using conventional PEX rails or tie-down methods.
The installers needed a bit of onsite training to get up to speed, and the first couple of circuits went in a little slower while Osborne Company helped demonstrate efficiencies and effective ways to speed up the installation. “But it didn’t take long for the crew to have a full understanding of the processes, and they quickly picked up the pace for the rest of the installation,” Bell said.
As with any project, there are challenges to overcome in buildings of this magnitude. “Having to accommodate physical building changes that occurred after we had procured the material was one of the challenges we had to work with,” Bell said. “And construction delays threatened to leave the tubing exposed to the sun for longer periods of time than we had anticipated. We had to do some quick thinking to make sure the tubing was protected from possible prolonged sun damage.”
Osborne, the Uponor rep firm, became an instrumental strategic partner in helping overcome and solve these unique challenges, and Bell is pleased with the process, the solutions and how quickly the crew installed the Radiant Rollout Mats.
“For large, open circuits, the installation of the Radiant Rollout Mats is much quicker than laying down regular tubing,” he said. “And the prefabricated and labelled mats allows for more efficient material handling onsite, which is very important in these large installations.”
Join the conversation: