In the dynamic world of heating and cooling, hydronic systems have established themselves as unsung heroes. By using water or other liquids as heat carriers, these systems offer an energy-efficient, eco-friendly solution for temperature regulation. Their brilliance, however, isn’t solely in their design; it’s in their heart—filtration. Proper filtration ensures a clean, debris-free flow, acting as the guardian of efficiency and the protector against wear and tear. By ensuring that water circulates free of contaminants, filtration ensures that the entire system remains efficient, robust, and long-lasting, ultimately offering unparalleled performance day in and day out.
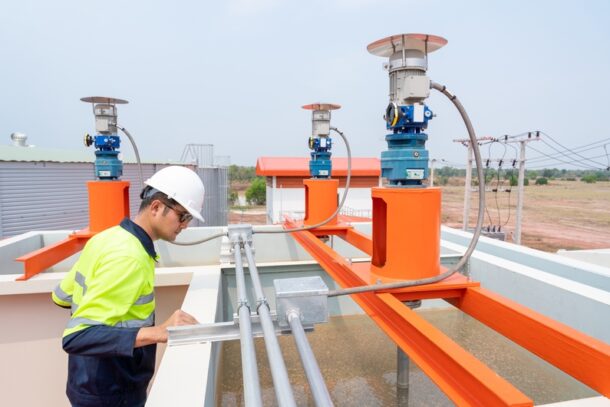
Classifications of Hydronic Systems
The intricacies of hydronic systems are often deeply rooted in their design variations. Each classification serves specific purposes, with unique advantages tailored to diverse applications. Grasping the diversity of hydronic systems not only provides clarity during installation but also ensures optimization of maintenance efforts for each specific design.
- Open Piping Systems: Characterized by a direct connection to the atmosphere, usually through an expansion tank.
- Direct Return Piping Systems: A straightforward design with water returning directly from the terminal to the boiler.
- Reverse Return Piping Systems: More balanced than direct returns, as the water travels the same distance, regardless of where it starts or ends.
- Closed Piping Systems: Isolated from the atmosphere, these systems reduce the risk of contamination.
- Direct Reserve Combination Return Systems: A blend of direct and reverse returns, offering flexibility.
- One Pipe Systems: A simple setup where a single pipe serves both the supply and return.
- Two Pipe Systems: Features separate pipes for the supply and return, providing more precise temperature control.
- Three Pipe Systems: Incorporates an extra pipe to boost heating or cooling capabilities, often used in more complex applications.
- Four Pipe Systems: Offers ultimate flexibility with separate pipes for heating and cooling, allowing simultaneous operation of both functions.
- Radiant Panel Systems: Leveraging radiant heat transfer, they warm or cool surfaces rather than air.
The Imperative of Regular Filtration Maintenance
Maintaining a hydronic system’s efficiency isn’t just about periodic check-ups; it’s fundamentally rooted in robust filtration maintenance. Every component of a hydronic system relies on the purity and consistency of the liquid it circulates. Without diligent filtration maintenance, impurities can accumulate, leading to blockages, reduced efficiency, and long-term system damage. Beyond the health of the machinery, when systems aren’t optimized, they can consume more energy, raising operational costs substantially.
The U.S. Department of Energy’s Energy Saver Guide underscores the significance of regular maintenance for heating and cooling equipment, stating that it’s vital for ensuring efficiency. Diligent care ensures potential issues are detected early, keeping systems running smoothly and reducing unforeseen expenditures. With regular attention to filtration, operators can guarantee that hydronic systems deliver peak performance while making a significant impact on their bottom line.
Inspections Are Key
While regular maintenance sets the stage for optimal system functioning, it’s through rigorous inspections that the true health of a hydronic system is gauged. By methodically examining each component, operators can pinpoint minor issues before they escalate into costly problems. Inspections provide a comprehensive overview, from the cleanliness of the filters to the efficiency of the pumps.
During these assessments, technicians often encounter subtle signs of wear or potential failure points that might go unnoticed during regular operation. Armed with the insights from these inspections, operators can implement proactive measures, ensuring longevity and consistent performance. For a hydronic system to thrive, a meticulous inspection regimen is non-negotiable. It’s the bridge between everyday operations and the assurance of system durability.
Choosing the Right Filter System
Selecting the proper filter system for your hydronic setup isn’t just a technical task; it’s foundational to the longevity and efficiency of the entire operation. There are a few key factors that you need to consider when selecting the system that is the right fit:
- Consider the specific demands of your hydronic system. Is it a commercial setup with high volume needs or a more modest residential system?
- Take stock of the kind of contaminants you’re primarily dealing with. Different locales and water sources might introduce varied impurities, from mineral deposits to organic matter. Understanding these variables will guide you to the right filtration granularity and type. Remember, over-filtration can be as detrimental as under-filtration, leading to undue pressure on the system and increased energy costs.
- Think about future scalability. Systems grow, demands shift, and an ideal filter system can adapt without necessitating an overhaul. Aligning your choice with not only your current needs but also future projections ensures that your hydronic system operates at peak efficiency today and well into the future. Making the right choice in the beginning can save you significant time and money down the line.
Maintenance Tracking: Don’t Leave It to Memory
In the bustling world of hydronics, where efficiency meets innovation, it’s crucial to keep a meticulous record of every maintenance activity. But let’s face it, relying on memory or scattered notes is a path laden with oversights. With the high-tech nature of modern hydronic systems, maintenance isn’t just about swapping out parts; it’s about understanding trends, foreseeing potential issues, and optimizing operations.
Using dedicated tracking tools or software can be a game-changer. Not only do these tools ensure that no maintenance milestone is missed, but they also provide invaluable data over time. This data can be used to understand the system’s behavior, predict when parts might wear out, and even optimize the entire operation for better efficiency. In the event of unforeseen malfunctions, having a comprehensive maintenance log can expedite troubleshooting, getting your system back up and running in no time.
Guest Author: Mark Ligon is the Marketing Manager at Commercial Filtration Supply, a provider of industrial filtration products at discount prices. Mark enjoys writing about various liquid filtration applications, and he believes educating customers on liquid filtration best-practices ensures they have the best experience possible with the product they decide on.
Join the conversation: