What is corrosion?
We’ve all seen it and talked about it at some point, right? So, how well do we really understand it?
It is important to understand that corrosion is a natural process, and it will occur in every system where any type of metal is present. From pipes and fittings to major components, corrosion is part of a natural process for any metal that has been refined and then formed into a manufactured component.
Once formed, the clock begins! These metal parts and pieces are actively working on returning to their natural form, into a more stable state such as an oxide. This is how we end up with black iron oxide, or magnetite as one result of this natural process.
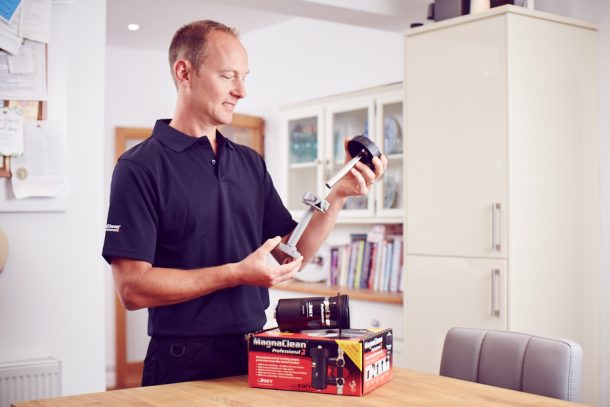
How does this apply to hydronic systems?
While there are many causes and contributing factors to corrosion, the biggest concern for any hydronic system is the risk of blockage. Blockages can not only dramatically reduce the efficiency of your system, they can prematurely shorten the functional life of your major components.
Knowledge is power, and a little extra effort now can yield years of higher efficiency and longer life for your systems’ components. Another important concept to realize, particularly in hydronic heating systems, is that heat accelerates the process of corrosion. That’s right, a hydronic heating system by its very nature is a catalyst for corrosion!
Black iron oxide or magnetite is often recognized as black water, black sludge, mud, dirt, or metal flakes in the water.
Counteract Corrosion
We can prevent corrosion from occurring in a new system, and we can even slow down the process in an existing system via three simple steps: Test, Clean, Protect.
Test
Testing is a vital step in understanding the quality of the water in the system. A test identifies whether corrosion is occurring, and also advises on what needs to be done to recover the system water and components. Read more about our water testing tools here.
Clean
Any system with corrosion occurring will need a clean. Our MC3+ cleaner is a neutral based cleaner, designed to lift and dislodge scale and iron oxide that has built up on system components and pipework. This cleaner also contains a small amount of inhibitor that will protect the components as it’s cleaning. For more information on our MC3+ cleaner, click here.
Flushing the system is also required after cleaning, and this can be done using our MagnaCleanse flushing machine. The unit works as a by-pass, allowing the system to be cleaned with no system shutdown; this also means that the system water remains hot, providing a better clean. Find out more about this money-making machine here.
Protect
Unfortunately the process of corrosion never stops, which is why any hydronic system will need the long-lasting, continuous protection of a magnetic filer. Our MagnaClean filters collect the iron oxide that has been loosened by the cleaner, and will continuously collect any future iron oxide to provide on-going protection for the system and its components. MagnaClean filters are available in a wide range of residential and commercial sizes for any type of hydronic system, whether it be a boiler, chilled water, or steam system.
Inhibitors are also vital in ensuring the on-going protection of the system. Our MC1+ protector provides a protective coating on all system components to prevent future corrosion from building up, and also contain pH buffering agents to neutralize pH levels which will prevent future acidic or alkaline corrosion. More information about our MC1+ protector can be found here.
Counteract corrosion: TEST. CLEAN. PROTECT.
Warning: Chemicals should not be used in steam systems due to higher temperatures. Magnetic filters can be used for steam system protection. For more information, please visit https://www.adey.com/us/corrosion
Join the conversation: