Complex hydronic systems are so 2008, at least according to Mechanical-Hub ProStaffer Andy Mickelson, who owns Mickelson Plumbing and Heating in Missoula, Mont. His three-man shop does plenty of high-end residential work, and even here—no—especially here, their recipe for success, serviceability and efficiency includes a heavy dose of “keep it simple.”
On a custom home, where some contractors may be tempted to stack the material list high and deep, Andy does the opposite. He takes a step back from the blueprints and figures out how to use the fewest components needed without any compromise. Numerous zones, DHW production, multiple supply temperatures and snowmelt loops can and are all handled without making things more complicated.
“There are a number of things you can do to keep systems simple,” said Mickelson. “I make sure to avoid ‘inadvertent’ redundancy: that is, two products that accomplish the same task.
Proper sizing of radiation, pipe, pumps and boilers accurately is obviously important, too. Picking a control system that accomplishes what you need and nothing more is helpful.
Another thing we began doing a few years ago—and have noticed an improvement since – is sizing and grouping our zones to the capacity of a specific pump, instead for creating a zone with no real parameters, and trying to find a pump that fits the zone or zone group.”
Like a round peg in a round hole, selecting your circulator first can save a lot of trouble, as well as the issues that come with over- or under-pumping a system.
Starting in late October of last year, Mickelson was hired for a job that would test his ability to “keep it simple.”
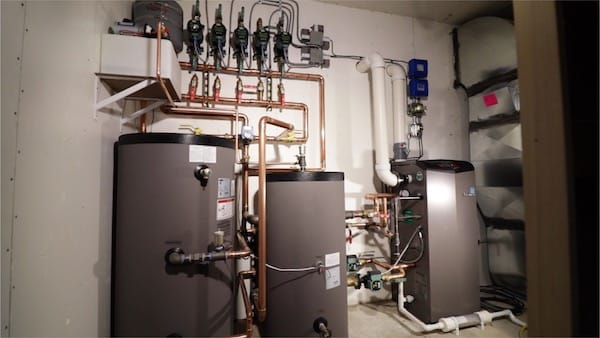
Mickelson’s work included installation of a mod-con boiler, seven zones of in-floor radiant, a hydronic unit ventilator, high-temp baseboard and 400 sq.-ft. of snowmelt.
Just out of town, the customer had purchased a nice lot with an older, 800-sq.-ft. home. The house was leveled and the basement foundation was re-used. The plan was to build a new 5,000-sq.-ft., two-story home on top of and around the original foundation.
Pick the pump first
“Like we do on all our jobs, I interviewed the homeowner long before we started the work, in order to really understand what they wanted,” said Mickelson. “Comfort was paramount, and budget not as much. So a thin concrete slab covers all radiant tubing, which is set at nine-inch centers.”
Before Mickelson started his loop layouts, he chose the Taco VT2218 variable speed circulator to serve all of the zones, with a total of six pumps. Additionally, Taco 007e single-speed ECM circulators are used on the 200 MBH fire-tube boiler and the indirect water heater.
“I like a Delta-T pump on a job like this, but another reason I used the VT2218 is for its broad pump curve, and we made use of it,” explained Mickelson. “It’s also very easy to program. Each radiant pump serves a group of zones. The zones are paired up according to the pump’s capacity, in terms of both head loss and flow rate. That way there aren’t any extra, underutilized circulators.”
Once the pump has been selected and the heat loss has been completed, the zones can be designed to fit the home. A common misconception about radiant circuits is that they must be as close to 300 feet long as possible, this just isn’t true. By dropping the length of each circuit, the head loss can be comfortably managed. The downfall to this is that the zone may require more circuits, but honestly the difference between five circuits and seven is minimal. It’s the same amount of tubing, no real noticeable increase in labor, just a larger manifold and a manageable head loss.
Low temp
Through zone valves, each pump supplies the appropriate amount of water and heat to a Watts Radiant stainless steel manifold, located remotely. Half-inch Watts RadiantPERT tubing was laid out before the gypcrete was poured.
“We chose the PERT instead of PEX because the radiant work was done throughout the winter. With spells of sub-zero weather, the increased flexibility of PERT was a huge benefit, especially considering our tight tube spacing.”
Because of the hydronic radiators, unit ventilator and snowmelt, the boiler maintains the buffer tank at 140°F at an outdoor design condition of -15°F. To make low temp water for the radiant zones, a Watts 4-way mixing valve with a tekmar 741 actuating motor was used. The 741 communicates with a tekmar 402 House Control in order to supply the exact radiant temperature need based on the outdoor temperature.
“The mixing valve sets the final delivery temp to all the low-temp zones,” said Mickleson. “It’s one of three elements at play here that really allow us to provide the exact temperature and flow rate to the radiant zones, so we’re really capitalizing on the primary/secondary piping, and squeezing every last ounce of comfort and efficiency out of the system. The other two elements are the outdoor reset on the higher temp boiler zones, and the variable-speed, Delta-T pumps. They all work hand in hand.”
The home has several areas with structural elements which made installing some of the tubing a challenging. Because of this, Mickelson had no choice but to run PEX supply and return piping through exterior walls. As a guard against the challenge of Montana winters, he wanted to run a glycol solution in the system. He installed a Neutra-Safe system feeder, which is an all-in-one reservoir, pump and control.
High temp
The fourth and fifth VT2218 circulators serve the home’s three high-temp zones directly out of the buffer tank. In the basement, where the existing, uninsulated slab is still in place, Runtal baseboard was used in lieu of radiant tubing. Mickelson had considered ceiling radiant, but there wasn’t enough height to allow it. The circulator used for the baseboard zone also supplies water to the 12,000 BTU Smith Environmental unit ventilator in the garage attic.
The last variable-speed circulator serves as the snow melt system pump on the loop side of the brazed-plate heat exchanger. Mickelson uses a tekmar 654 Snowmelt Control to manage automatic operation and maintain a 25°F Delta-T across the 400 square-foot zone. This control features a snow and ice sensor that’s set in concrete when poured. The snowmelt loops also utilize a second Neutra-Safe System Feeder.
“Because of the components used and a thoughtful design, we’re covering five different loads with one boiler while installing it in a relatively tight space, all without being overly complicated,” said Mickelson.
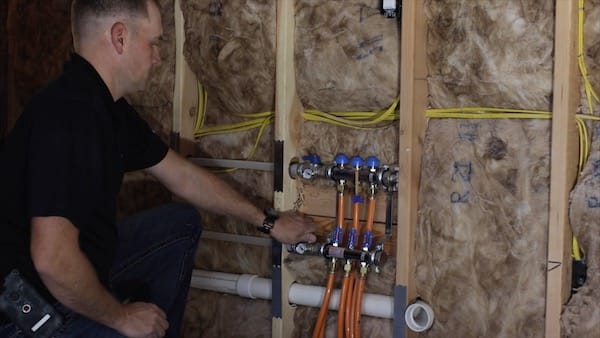
Each pump supplies the appropriate amount of water and heat to a Watts Radiant stainless steel manifold.
“In the case of an emergency, I only have to deal with a single control system or one replacement pump,” he added. And with all that said, I can’t think of a quieter, more comfortable, or higher efficiency heating system.”
Mickelson is now going over a punch list, and looking forward to the feedback from the customer. He’s expecting rave reviews about the comfort level, and complete satisfaction when the owner receives their first propane bill.
Join the conversation: