Founded by the English Benedictine community in 1926, the Portsmouth Abbey School is a coeducational, 9 – 12 academy that sits on a bucolic 500-acre campus on the shores of Narragansett Bay in Rhode Island. Dedicated to the rigors of the Western intellectual tradition, the School is also a residence for its 360 students and to the monks who live at its monastery. For the Abbey’s director of operations, Paul Jestings, the institution represents both an extraordinary heritage and an extraordinarily complex heating and hot water challenge: sixty buildings served by a mix of individual units and central heating plants, fueled by oil, propane, solar and soon, natural gas.
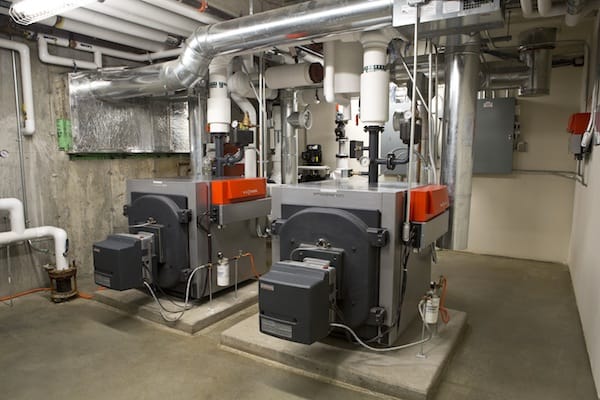
“I can’t go into the red to go green.” When Jestings first arrived at the campus as an independent contractor in 1976, he confronted an array of steam boilers that had been in service since the mid-1960s. In 1990, when he assumed full-time responsibilities at the Abbey, Jestings was charged with a mission: save energy and money through appropriate upgrades. “The steam boilers didn’t modulate; they always ran at full blast,” says Jestings. “In the winter, that means a lot of short cycling. In the summer, when all we needed was hot water, we got a lot of overkill. Either way, it’s waste.” The administration, faced with aging boilers and high fuel costs, agreed that it was time for a change — but it had to be of the right kind. “We needed something that could manage an extremely diverse load, from a heavy use of showers in the morning to almost nothing the rest of the day.” The objective: match load to demand.
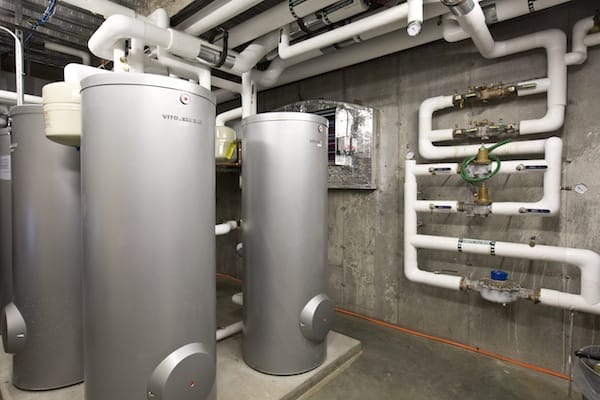
But Jestings had another consideration in mind. Every significant capital purchase requires approval from the school’s board of directors. With each purchase, Jesting’s reputation and credibility is on the line. “This school can’t afford to buy equipment that lasts only eight or ten years,” he says. “We have to get at least 20 or more years from our units — and the financial numbers have to work: I can’t go into the red to go green.” He was tired of replacing boilers that failed prematurely, tired of hearing the same very first thing out of the boiler rep’s mouth, “you know the warranty has passed.” No concern of why it failed prematurely because it did what it was designed to do…last past the warranty!
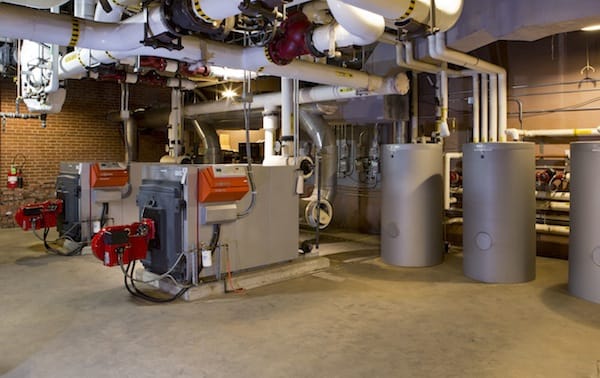
Efficiency has rolled out at Portsmouth Abbey in waves, beginning almost two decades ago by replacing approximately 20 steam and hot water boilers with more efficient Viessmann hot-water boilers. By coupling the units to outdoor reset controls, the boilers modulate supply water temperature output based on outside temperatures, increasing fuel savings by 20% on top of the highest efficiencies available for oil boilers – 87% to 89%.
In the second wave, Portsmouth Abbey incorporated solar panels to provide domestic hot water (DHW). Through an enhanced hybrid design that integrates with the boiler system, the solar panels provide supplemental space heating in warmer weather; in the coldest months, the boilers offer the necessary boost for hot water.
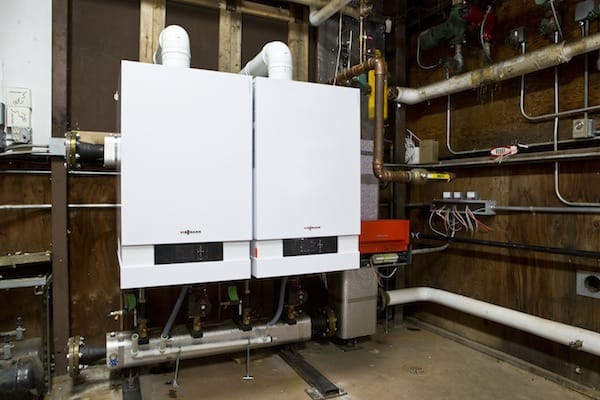
Today, Portsmouth is anticipating access to natural gas by installing Viessmann boilers that can accommodate any gas source without requiring any burner modifications; these will run on propane until natural gas becomes available. With natural gas or propane , the condensing boilers can gain an additional 10% increase in efficiency over oil, reaching efficiencies of 97% – 98%.
Some of the retrofits have saved 20% – 25% in fuel costs; others have achieved as much as 45% improvement in fuel efficiency. “We always outperform the estimates we give to the board,” Jestings says. “We love our boilers. Our guys wax them! Who does that? It shows pride of ownership.”

Fuel efficiency, and the elimination of the need to re-invest in its equipment every eight to ten years, are not the only ways the Abbey saves money. “Back in the old days, we went through a lot of growing pains,” Jestings says. “This is a boarding school, open 365 days a year. We can’t have boilers go down. We used to do a lot of night calls — and that means wear and tear on my staff. Now my crew never comes out at night, at least not for a boiler failure. I tell the new guys, you don’t know how lucky you are!”
Low maintenance is not just a boon to Jesting’s crew; it is one of the keys to fiscal responsibility. “This stuff just doesn’t break,” says Jesting. “With Viessmann, we haven’t had a service contract in 18 years. The money we save is put towards other upgrades in the physical plant — it’s all self-funded.”
Portsmouth Abbey has become a model for other institutions struggling to control costs and achieve a greener environmental profile. Other facilities managers turn to Jestings for advice. “I tell them they have to get past that initial increase in investment. The difference between the best equipment and the rest is in the fuel savings and in the reduced service,” says Jestings. “Some people say they can’t afford to go with Viessmann. I say you can’t afford not to.”
Join the conversation: