While hydronic system growth across most of the country is slow, Metro Detroit is seeing a bit of a water-side resurgence, at least in certain segments. And it’s appearing where people are demanding the best. “We’re installing more boiler systems now than ever before,” said Joe Sullivan, president of Paradigm Plumbing & Mechanical, Inc. “We’re Read more
A Paradigm Shift in Hydronics
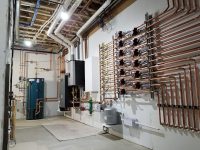
While hydronic system growth across most of the country is slow, Metro Detroit is seeing a bit of a water-side resurgence, at least in certain segments. And it’s appearing where people are demanding the best.
“We’re installing more boiler systems now than ever before,” said Joe Sullivan, president of Paradigm Plumbing & Mechanical, Inc. “We’re gaining market share, but the market is growing, too. Homeowners are demanding premium comfort with more regularity, and as a result, builders and architects are pushing hydronics. It’s the obvious answer.”
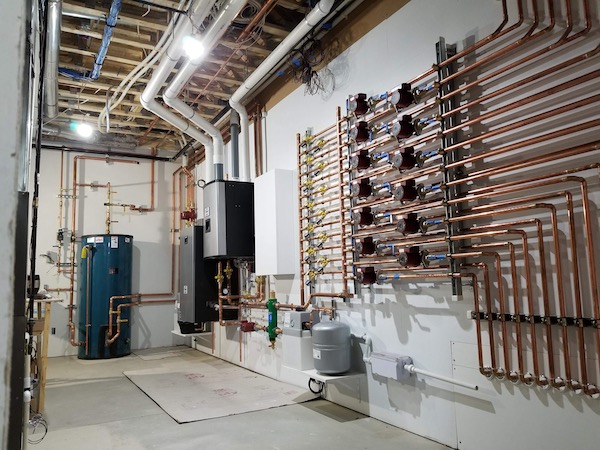
Paradigm Plumbing & Mechanical, Inc.’s niche is high-end new construction in the Detroit metro. During assembly of this mechanical room, the Aspen and Aspen Light Commercial boilers were installed early in the game.
Paradigm’s niche is high-end new construction. They call themselves a builder-based company. Founded 10 years ago, the ten-person company works exclusively for five or six general contractors. Radiant systems are common, and so are homes that require three or four different water temperatures.
“Our system designs might be a bit different that the competition, but we have a specific way we like to do things,” explained Sullivan. “Our market also allows us to install the best equipment available. We cut no corners. Comfort and reliability are the primary goals, and efficiency is close behind.”
Long timelines
Large custom homes are essentially small commercial projects. Paradigm’s involvement at a single residence can easily span two years, from design to start-up. They’ve partnered with rep HS Buy Van, and buy equipment through Hartsig Supply.
“HS Buy Van works on our piping and loop layouts,” said Greg Sharer, project manager and hydronic specialist at Paradigm. “With their help, we begin projects with a full MEP set. All of our electric and controls are done in-house.”
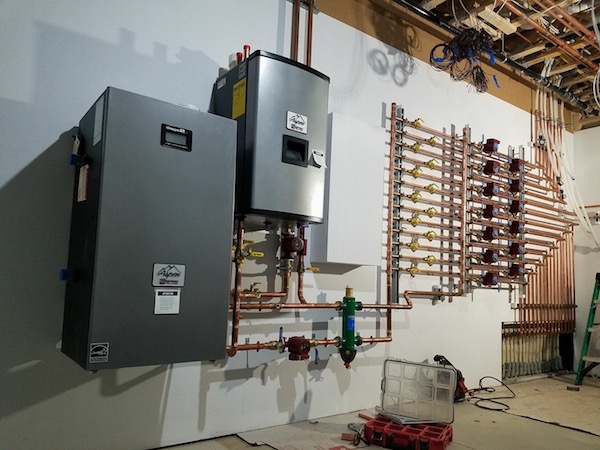
The 205 MBH Aspen boiler heats the home and provides DHW, while the 399 MBH Aspen Light Commercial provides heat for a snowmelt system.
Nearly a year ago, Paradigm started a new project with Eric Vogler on a 7,500-sq.-ft. residence in Orchard Lake, Mich., and they’ll be wrapping it up just before heating season this year.
Paradigm designed two separate hydronic systems for the home: one for in-floor radiant and DHW using a 205 MBH Aspen, and one for the snowmelt system, with heat provided by a 399 MBH Aspen Light Commercial. The home has a furnace in addition to radiant tubing throughout the floorplan, and a full tekmar control system.
https://youtu.be/u7RXZImuBOI
“Customers who’ve never experienced a well-designed radiant heating system are blown away when the first heating season rolls around,” said Sharer. “Every surface in the home is warm to the touch, even the countertops.”
Piped right
In the boiler room, mechanical components cover an entire 16-foot wall. The high-efficiency Aspen boilers are mounted next to an array of copper pipe and circulators.
“HS Buy Van recently changed hi-efficiency boiler brands, so when they picked up the US Boiler line, we gave the Aspen a close look,” said Sharer. “We still had access to our previous brand, but the appearance and the design of the Aspen are great, so we bought two for this project. They’ve proven easy to install, and we really like firetube heat exchangers.”
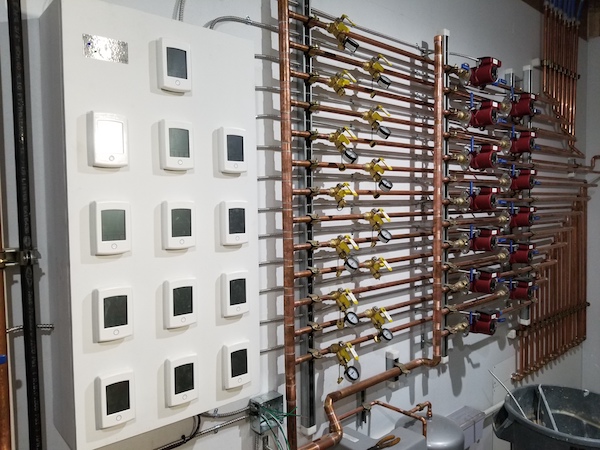
Paradigm is known for their meticulous installation of piping, pumps and controls.
The Aspen boiler offers up to 96% AFUE, comes in five sizes, and is available as a 155 MBH combi. The Aspen LC comes in two sizes and can be floor- or wall- mounted. Both units feature Sage2.3 controls and have a 10:1 turndown ratio.
The rest of the mechanical room is occupied by a 120-gallon Burnham Alliance SL tank, beautiful copper piping, a Caleffi hydro-separator and mixing valves, and numerous Grundfos circulators.
“Greg does phenomenal work,” said Sullivan. “He and I really love hydronics. We handle most of the boiler systems – which make up about 40 percent of our work – while the rest of the crew covers controls, electronics, plumbing and air-side.”
The system for the big custom home was built onsite, but Sharer and Sullivan often prefabricate systems at the company’s 5,000 square foot shop.
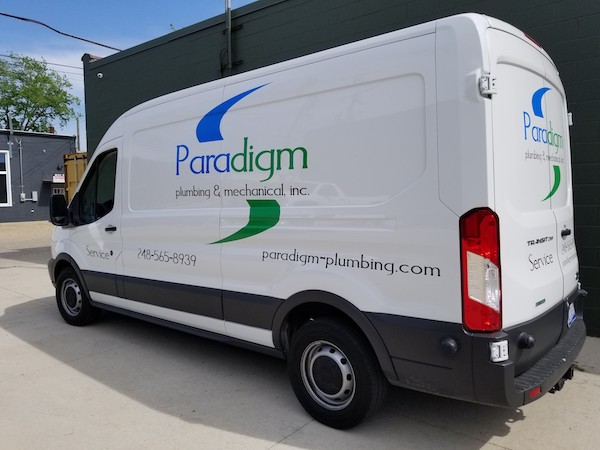
“Most of our manifolds are remote,” said Sharer. “We do this to keep loop lengths short, usually no more than 250 feet. And, despite what some people may think, we prefer to zone with pumps instead of zone valves. This offers a great deal of redundancy, but also makes balancing simple, as well as diagnosing issues after the fact.”
Half-inch Uponor PEX was used for the 12 zones of radiant, laid at six-inch centers. Most of the tubing is under tile, set in Portland cement. Plenty of care was taken to protect the tubing during construction, and the same attention to detail was given to the tubing outside.
Let it snow, just not yet
While high-end residential hydronics is an area of growth for Paradigm, so is one of its subcategories. The company has earned a reputation in the Detroit area as being a snowmelt specialist. Annual snowfall in the area is often between 45 and 100 inches.
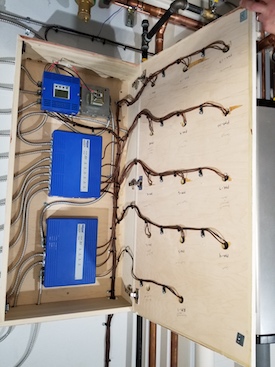
The home and snowmelt system are served by a full tekmar control system.
“There are plenty of wrong ways to install hydronic snowmelt systems, and a few ways to do it correctly,” said Sharer, who has been with the company for six years. “Over the years we’ve developed a method of designing, selling and installing these systems. All our systems operate as they should and offer great benefits to the owner. We’ve crunched the numbers thoroughly enough to give the perspective customer an accurate projection of operation expenses.”
The Paradigm snowmelt method includes years of experience, but there are a few rules of thumb they adhere to, some of which are universally accepted as best practice by the hydronic community, and some that aren’t.
“Maintaining proper loop length is one thing we’re careful about while installing tubing, and most everyone agrees on that,” said Sharer. “But our insistence on using individual pumps on all the zones in a snowmelt system is one that sometimes draws scrutiny. We have our reasons.”
“In the past, public opinion of snowmelt systems was that you had to be Bill Gates to own or operate one,” said Sullivan. “With the right design, piping, and control strategy, it can be cheaper to operate than most folks think.”
Sullivan admits that snowmelt systems are absolutely a luxury item, but clients still want to know what it’ll cost to run the system in addition to what it’ll cost to install. Of course, there’s a financial return on investment by offsetting salt and snow removal costs, but the true payoff is harder to quantify. Safety and convenience are difficult to assign dollar figures to.
The Aspen Light commercial was installed in early March, but the driveway work needed to wait several months until the weather improved. The two-zone snowmelt system included the concrete driveway and a paver walkway.
“High-end residential has been great for us, but we’re working on becoming more competitive, moving into lower-cost markets with hydronics,” said Sullivan. “It’s a slow transition, because we’re figuring out how to do that by eliminating a few bells and whistles without sacrificing any quality. It’s a marketing challenge as much as anything.”
But where there’s a will, Paradigm finds a way. They’ve proven this through their application of uncompromising hydronic system quality.