RLS LLC, manufacturer of the Rapid Locking System line of flame-free press-to-connect fittings for HVAC and refrigeration systems, announces that Milwaukee® Tool, in partnership with RLS, has introduced RLS-compatible jaws for use with its popular M18™ FORCE LOGIC™ Press Tools. Available in sizes from 1/4″ – 1-3/8″, these new RLS ACR Press Jaws will allow Read more
DEWALT
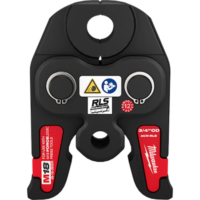
RLS LLC, manufacturer of the Rapid Locking System line of flame-free press-to-connect fittings for HVAC and refrigeration systems, announces that Milwaukee® Tool, in partnership with RLS, has introduced RLS-compatible jaws for use with its popular M18™ FORCE LOGIC™ Press Tools.
Available in sizes from 1/4″ – 1-3/8″, these new RLS ACR Press Jaws will allow M18 tool users to take advantage of the time-saving and safety benefits of flame-free RLS press connections for HVAC/R, without needing to invest in a new press tool. These are the industry’s first jaws approved to press RLS fittings using 32 kN (kilonewton) tools.
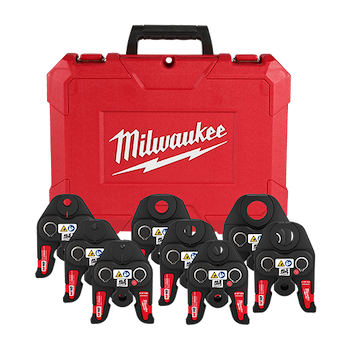
In addition, the new Milwaukee jaws are also compatible with a wide range of other 32 kN tools on the market, including those from manufacturers such as RIDGID, Klauke, Viega, Dewalt, NovoPress and Rothenberger. Contractors who already own any of these tools will only need to purchase the Milwaukee jaws to begin installing RLS fittings.
Milwaukee’s RLS-compatible jaws will be sold exclusively through Milwaukee distributors. Contact Milwaukee or visit milwaukeetool.com for details. For more information on RLS press fittings, and a complete RLS Tool & Jaw Compatibility Matrix, visit rapidlockingsystem.com.
About RLS Fittings
RLS press fittings connect in 10 seconds using a battery-powered tool and jaws, replacing the time-consuming process of manually brazing HVAC/R joints. The fittings result in faster, more consistent connections that reduce total installed costs, while also increasing jobsite safety by eliminating the use of an open flame. More than 10 million RLS fittings have been successfully installed since their introduction in 2015
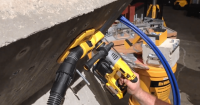
Dewalt’s newest anchor system, the Mini-Undercut anchor is the first of its kind to gain all approvals and seismic ratings for use in post-tension slabs and can be used in a variety of concrete base materials like thin slab, hollow-core pre-cast etc. The anchor itself requires only 3/4” drill depth and has seismic code ratings Read more
Dewalt’s newest anchor system, the Mini-Undercut anchor is the first of its kind to gain all approvals and seismic ratings for use in post-tension slabs and can be used in a variety of concrete base materials like thin slab, hollow-core pre-cast etc. The anchor itself requires only 3/4” drill depth and has seismic code ratings for holding values of up to 4” pipe. The drill bit has a fixed stop only allowing for 3/4” drill depth, the setting bit can be used in drill mode without damaging the anchor threads.
We learned of this anchoring system while attending the #toughinthesouth new tool event in Nashville, TN.
https://www.youtube.com/watch?v=YGH8T6acmSs
Video footage credit: Heather Aune, mechanical-hub.com
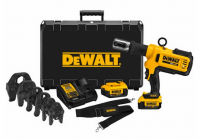
It’s been two months since I took delivery of the Dewalt DCE200 press tool and I’ve had the opportunity to put it to work on a handful of jobs now. This is a feature-packed tool unlike many on the market today. With capabilities of handling any and all press systems common in North America and Read more
It’s been two months since I took delivery of the Dewalt DCE200 press tool and I’ve had the opportunity to put it to work on a handful of jobs now. This is a feature-packed tool unlike many on the market today. With capabilities of handling any and all press systems common in North America and Europe team Black & Yellow pulled out all the stops in engineering their first at what I’m guessing will be a team of press tools to come.
First off I’d like to cover the important specs.
- Capable of pressing ½”-2” copper & stainless steel V-groove fittings
- Compatible with competitor jaw sets for Iron Pipe [Mega-Press]
- Compatible with competitor jaw sets for PEX press [Viega/Nibco]
- 4-ton pressing force
- Current online pricing searches average $1999.00
I first learned of this tool back in July/August of 2016 at the annual new tool event hosted by Dewalt. When I first put my hands on it I admit I was a little surprised of the physical size overall but after using it for both boiler and tankless water heater installations now I can honestly say the size of the tool has not proved to be an issue at all. Weighing in at 7.16lbs without a jaw it is lighter than other comparable tools common on the job today. Ergonomics may be a slightly different story and I do carry a bias toward in-line design press tools. This tool is front-end heavy, loaded with anything over 1″ jaws and it will not stand on it’s own. That may be partially due to the small footprint of the 20V battery or the handle angle and placement. Either way its a strain on the wrist and requires two hands to steady the tool most of the time.
Features
This pistol-grip press tool is packed with some new innovation to the market that should prove useful to many contractors working on commercial & residential projects alike. Notably, Dewalt’s proprietary software system Crimp Connect. This free software download allows the owner/user to connect the press tool via the onboard mini USB port providing ability to print detailed reports of the date, time, force, and successfully completed cycles of the presses completed by the tool as well as the tools calibration and service history.
Located on the top rear of the tool you’ll find a somewhat familiar interactive panel where the tool’s power is controlled along with LED light indicators showing the successful completion of a single press, battery indicator, low & high temperature warnings. There’s even a “service required” indicator light telling the user that the tool has reached the cycle limitations.
While the power panel is not unique to press tools of this caliber, the Crimp connect feature is. An added feature I found interesting is the double trigger.
The bottom trigger controls the start and completion of the press cycle. Dewalt went with a “manual” cycle operation here. You’ll need to depress the trigger completely for the duration to complete the press cycle. Cycle time is anywhere between 4-6 seconds depending on the diameter and type of material being pressed. The unique second trigger, the top trigger can be used to release the press cycle at any point. This is useful when a cycle has started but the operator decides [far various reasons] to stop the press. When pressed fully, the top trigger will release the pressure in the hydraulic cylinder and allow the ram to retract quickly. This would allow for repositioning of the tool or fitting when needed, potentially saving a fitting from incorrect attachment to the piping.
A shoulder strap and ring attachment point are included with the tool. Dewalt states in the manual that it should be used for transporting the tool on the jobsite. Some feedback I have received from other plumbers is the strap may be useful when working on a ladder, a situation that often lends to the possibility of dropping a tool like this….I’ve done that and it wasn’t pretty.
The tool is made in France but the jaw set is delivered to Dewalt from Germany. Dewalt is offering a 3 year limited warranty, 1 year service and 90 day money back guarantee. You’ll most likely have to order this tool from specialty tool suppliers offering the whole Dewalt lineup. You can also look to plumbing and mechanical supply houses for stock as well.
https://www.youtube.com/watch?v=WVIlalA-Abs
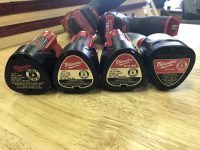
Cordless tools have nearly taken over the new construction and remodel jobsite entirely. With advancements like battery capacity, runtime and motor efficiency with onboard discharge monitoring today’s cordless tools are routinely performing at or above the level of production and power than their corded predecessors. Sure, everyone has said it myself included; there’s really no Read more
Cordless tools have nearly taken over the new construction and remodel jobsite entirely. With advancements like battery capacity, runtime and motor efficiency with onboard discharge monitoring today’s cordless tools are routinely performing at or above the level of production and power than their corded predecessors.
Sure, everyone has said it myself included; there’s really no need to lug an extension cord onto the job today. As old tools have reached the end of their useful and productive lifespan most are definitely being replaced with battery powered “upgrades”. As we all know not all tools are created equal the same should be said, and more often, about their power source; the battery.
With the multitude of choices in the cordless tool market I’m going to focus on one single platform to keep the message clear. I’m not choosing one brand over another out of preference or performance; my focus here is battery identification and what exactly we should be looking at to make the best purchasing choices with our hard-earned money.
Today’s manufacturers have invested entirely in lithium ion battery cell technology, long gone are the NiCad batteries of yesterday and to that I say good riddance. For the purpose of this article I’ll be using Milwaukee Tool’s M12 batteries in attempt to explain the differences in capacity and how to identify the right battery for your tool.
First, let’s get this out of the way, tool manufacturers in North America have long dropped the facts for the sake of marketing in labeling their tools lines. The 12V, 18V, 20V and 60V batteries produced by the major tool companies are all overrated in name and labeling. I’m not exactly sure why a 10.8V battery is labeled as a 12V but I’d guess it has more to do with the expected performance than graphics on packaging and more to do with 12 simply being the bigger number. Regardless, 60V [actually 54V] is the current king because it’s the biggest, right? We’re trained to think “bigger is better” and they’ve played into that 100%.
While it should go without saying that a typical 12V battery tool has less potential than its 18V bigger brother that’s not always the case for multiple reasons, one of them being the Ah [Amp Hour] ratings of the battery packs.
Runtime, potential power, voltage delivery etc are all tied back to or are related to this significant and often overlooked rating. The science behind the Ah is simple; a battery rated at 1Ah should be able to continuously supply a current of 1 amp to a load for exactly 1 hour, or 2 amps for 1/2 hour, or 1/3 amp for 3 hours, etc., before becoming completely discharged.
In an ideal battery, this relationship between continuous current and discharge time is stable and absolute, but real batteries don’t behave exactly as this simple linear formula would indicate. Therefore, when amp-hour capacity is given for a battery, it is specified at either a given current, given time, or assumed to be rated for a time period of 8 hours (if no limiting factor is given). Sometimes to understand the Amo Hour we need to also work with the Watt Hour [Wh]…just to further complicate things a little.
Let’s take for example the standard, lowest capacity M12 battery from Milwaukee. This battery is rated as 14 Wh [Watt Hours). Some simple math can convert Wh to Ah with this formula: (Wh)/(V) =(Ah). And you thought you left that back in 8th grade… When calculated out the Ah rating for this example is 1.1666 Ah. Meaning this pack should delivery 12V at 1A for slightly more than an hour. Of course when placed under higher or lower load conditions performance will change.
Milwaukee offers M12 batteries of multiple Ah ratings of course, as do other manufacturers but there seems to be different ideas on how to label these batteries so knowing how to identify the capacity will help you make an informed decision.
Moving up the M12 battery line the next offering is rated 16Wh and when plugged in to the formula we find out it’s a 1.333 Ah pack. That’s not a significant jump in power potential, a few minutes really but it comes at a price at the register. Moving even further up the M12 line takes us to a more recent product in the 2.0Ah labeled pack. It’s a 22Wh pack and has theoretically twice the capacity of the first two discussed so far.
Recent advancements in lithium cell technology, along with manufacturing processes have brought along even larger Ah capacity batteries of all voltages, not just the 12V batteries used for example here. As capacity increases so does the physical size to a point, further advancement of heat dissipation and cell quality is underway making it possible to assemble battery packs that are actually more powerful and physically smaller or the same size as lower rated packs.
A perfect example is the M12 XC 4.0Ah and M12 XC 6.0Ah battery packs. Both are the largest in physical size of all the Milwaukee 12V batteries but identical in size to each other. This is due to the type of lithium cells used in manufacturing and how those individual cells are assembled inside the rugged exterior shell. Quick math would show that the 6.0Ah pack has the potential runtime of almost 600% more than the 14Wh M12 pack. That capacity rating comes at a cost of course but in staying with the “bigger is better” philosophy you will definitely be getting longer runtime and possibly more bang for your buck.
Knowing what Wh and Ah really means and using that to compare one battery to another will hopefully help you select the best value for your cash and at the end of the day we all share the common goal of getting the most out of our time and money. Hope this helps.
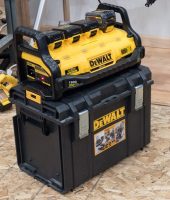
The new FLEXVOLT system from Dewalt has opened up a whole new line of tools and possibilities for the pro contractor looking to get more done in less time. We’ve had a few of the FLEXVOLT tools at work in our shop and in the hands of the ProStaff team for a couple months now Read more
The new FLEXVOLT system from Dewalt has opened up a whole new line of tools and possibilities for the pro contractor looking to get more done in less time. We’ve had a few of the FLEXVOLT tools at work in our shop and in the hands of the ProStaff team for a couple months now and continue to be impressed. The latest is the DCB1800 Portable Power Station.
The power station is a combination 4-bank parallel battery charger and DC power inverter capable of providing 1800 watts continuous power at 15A with a peak power rating of 3600 watts 120v. That’s some serious power, this thing is sick.
There are a still a lot of tools on the job that haven’t lent well to cordless technology yet. Core drills, large demo hammers, compressors and various saws. Add to that the many contractors still using corded tools where upgrades either haven’t been in the budget or replacement of a perfectly good tool is unwarranted and you’ve got the need for portable power.
The DCB1800 power station is a portable generator running off (4) 20v MAX batteries, not a gas engine so indoor use is not a problem. The inverter is silent in comparison to any other portable power solution as well making it a non-factor where noise is a obstacle to getting the job done. This is a gamechanger for those looking to knock out some punch list items at the end of the job or quickly get in and out to complete a task with a corded tool when cordless isn’t available.
I wanted to get an idea of how much power this thing has so I loaded it up with (1) FLEXVOLT 20/60v MAX pack and (3) 20v MAX batteries, all new and fully charged and plugged my DW734 thickness planer in to it. I ran (14) 2×8 Fir boards thru the planer before losing power supply. The low power indicator lights started flashing after 10 boards, giving me four more complete before shutting down. That’s 112 feet of planing 2×8’s! I’d imagine ripping some plywood for backing or chipping with a rotary hammer for 20-30 minutes is within reach with a power supply like that. I’ll be putting this to the test on the job soon so stay tuned, for now check out video proof of my test:
https://youtu.be/bHT9eJi9cvM