With failing oil-fired boilers and an aging, inefficient heating system, Elm Street School in Gardner, Mass., turned to modulating boilers from Weil-McLain to spark energy efficiencies and lower heating costs for the school. Built in 1923, Elm Street first served as a high school, but over the course of numerous years, the district converted the Read more
Mass.
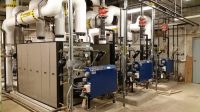
With failing oil-fired boilers and an aging, inefficient heating system, Elm Street School in Gardner, Mass., turned to modulating boilers from Weil-McLain to spark energy efficiencies and lower heating costs for the school.
Built in 1923, Elm Street first served as a high school, but over the course of numerous years, the district converted the facility into an elementary school. Today, the 130,000-square-foot facility houses more than 500 students.

“Our heating system consisted of two nearly 20-year-old boilers that were in constant need of repair,” said Robert O’Brien, director of facilities for Gardner Public Schools. “We found ourselves changing out cast iron sections on an annual basis. In addition to the maintenance issues, we wanted to decrease our overall heat load.”
To assist with project funding and help cover boiler replacement costs, the school applied for and received a green repair grant from the Massachusetts School Board Authority (MSBA). The MSBA Green Repair Program offers districts the opportunity to repair or replace roofs, windows and/or boilers in public school facilities that are otherwise structurally, functionally and educationally sound.
With funding in place, the school selected, MacRitchie Engineering, based in Braintree, Mass., which provides HVAC, plumbing and electrical design services, to handle the boiler replacement.
“We sought a dual combination gas and oil commercial boiler and Weil-McLain was my primary choice,” said O’Brien. “We also wanted units with the ability to modulate with a control package that could be implemented into a building management system.
“We received three competitive offerings when the project was put out for bid and we chose Weil-McLain because the equipment had the best load matching characteristics,” said O’Brien.
The team chose three Weil-McLain 88 Series low pressure steam boilers as the optimal choice to match heating load requirements with two carrying the building load and one installed for redundancy. MacRitchie also was tasked with handling oil conversion to add gas for dual fuel firing, boiler room valves, boiler feed unit, fuel oil pumps and controls, and associated electrical and plumbing work.
The Weil-McLain 88 Series boilers offer up to 85.7% thermal efficiencies, are operational in single or multiple systems as gas, oil or gas/oil, and feature modulation control.
The old oil-fired burners were removed and replaced with the Weil-McLain dual fuel boilers and configured with gas as the main fuel source and oil as a backup. Each boiler was installed with its own pump plus a common manually valved standby pump.
The project was completed and the units were placed in operation in October 2015.
Numerous benefits realized
According to O’Brien, the installation went smoothly and the school already is experiencing benefits.
“We expect to save anywhere from 20% to 25% of our fuel costs with these new boilers because they are more energy efficient, feature low-range pressure controls and have the ability to modulate,” said O’Brien.
Modulating burners are designed to control the burner output to match the boilers’ variable load requirements to ensure maximum combustion and boiler efficiencies during large heating demands. The modulation feature also has decreased the system pressure.
“Thanks to modulation, we reduced the amount of operating pressure from about 10 pounds on a cold day to about 5 pounds,” said O’Brien. “Dropping the pressure created a lot of savings, yet we are still maintaining the temperature inside the building so that’s a definite plus.”
Other benefits O’Brien and building staff are realizing include the adoption of a building management system that will send notifications via email and sound an audible alarm in the school if an issue should arise.
“If a boiler burner should misfire, for example, I immediately get an email and an audio alarm goes off in the school,” said O’Brien. “This alerts school custodian staff that an issue is happening, and it’s an important safety feature to have.”
The expected duration and life of the boilers are another plus, according to O’Brien.
“The life expectancy is typically 30 or more years for these boilers,” he said.
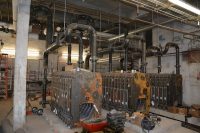
The 130,000-sq.-ft. Elm Street School in Gardner, Mass.—built in 1923—had failing oil-fired boilers, and a stack that defied physical principles and noise complaints. “One of the owner complaints was wet steam and banging. The previous system had a reputation for noise at certain points in the operation, notably start-up,” says Bradford White, senior mechanical engineer Read more
The 130,000-sq.-ft. Elm Street School in Gardner, Mass.—built in 1923—had failing oil-fired boilers, and a stack that defied physical principles and noise complaints. “One of the owner complaints was wet steam and banging. The previous system had a reputation for noise at certain points in the operation, notably start-up,” says Bradford White, senior mechanical engineer, MacRitchie Engineering, Inc.

What the stack will serve. Three Weil-McLain low pressure steam boilers. I insisted on dropped headers, full equalizers and extended boiler risers. In addition, the 8 inch risers to the building header also is effectively a drop header configuration. System will run on 2.2 psig. Full modulating fire.
MacRitchie Engineering, Inc., a small but nimble consulting engineering firm providing HVAC, plumbing, fire protection and electrical design services, was called for boiler replacement, oil conversion to add gas for dual fuel firing, new stack, boiler room valves, boiler feed unit, fuel oil pumps and controls, plus associated electrical and plumbing/gas work.

Stack arrives ready for off-loading. A 60 foot stack in two pieces, all 304 and 316 stainless to be assembled and rigged in one piece. White designed the stack for optimal draft with two or three boilers firing. The height will typically mean too much draft so we have a draft control system, dampers on each boiler.
According to White, “We sized the boilers based on a triangluated combination of connected radiation plus analysis of fuel bills and weather data as a cross-check.
“We went with extra-tall risers (60 inches off the boiler waterline), a dropped header and header outfeed to the building header also dropping into the top as is good practice,” says White.

New LPR return header and pad for the boiler feed unit. 374 gallons, quadplex pumps with manual standby.
Boiler room trap replacement, new insulation, boiler feed unit, condensate pumps and fuel pumps were installed to replace the existing. An engineered combustion air system was installed. Each boiler will have a 1″ F&T trap for waterline control and each boiler will have a dedicated feed water pump. The fourth pump will be a manual valve-over/switch-over should any one fail. This fourth pump valve arrangement can be directed to any of the boilers in parallel.
Once they get the horizontal breeching and draft control dampers installed, they will be installing that small-bore piping (blow-down, boiler feed and overflow control) which will cross the volume and floor space behind the boilers. The floor is clear for staging now.
A new stack, 60 feet tall, double wall insulated with one-inch air space, and of stainless steel construction was recently rigged into place.
With the project starting in July 2015 and wrapping up this month, as for energy savings, it is too early to project. “The main maintenance supervisor is a former mechanical contractor who knows steam. Nothing predicted specifically, but with fully modulating boilers and low-range pressure controls plus current code insulation thicknesses and new traps at least in the boiler room, they will do as well as they possibly could,” says White.

Aligned to be inserted into an existing 60 inch masonry chimney. Base is three stories below. Base flange was bolted to a reinforced pad.
Inside the Jobsite
Boiler — Three (3) Weil-McLain 1288 low pressure steam boilers. Two carry the building, one is standby.
Pumps — Shippensburg (Shipco) quad-plex boiler feed unit with epoxy lined tank. Each boiler will have its own pump plus a common manually valved standby pump.
Piping — All steam and condensate is A106 carbon steel with welded fittings for sizes 2.5 inches and larger. Smaller pipe is the same but malleable iron fittings. Pumped condensate and blowdown piping is A53 Grade B carbon steel.
Stack and Breeching — Schebler Chimney Systems, Bettendorf, IA. Included 2-piece chimney stack, breeching system and pressure-responsive draft control system for each boiler.
Date started:
July, 2015
Date Finished:
October, 2015
Workers onsite: Varied, ranging from two to six pipefitters, electricians and plumbers.
Budget: $960,000 for the steam plant work and stack.