By joining forces with Uponor, GF is set to become a global leader in sustainable water and flow solutions. To support this ambition, complementary businesses will be grouped together under one roof: the new division GF Uponor will focus on Building Technology, whereas the infrastructure and utility business will move to GF Piping Systems. Michael Read more
PEX piping
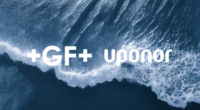
By joining forces with Uponor, GF is set to become a global leader in sustainable water and flow solutions. To support this ambition, complementary businesses will be grouped together under one roof: the new division GF Uponor will focus on Building Technology, whereas the infrastructure and utility business will move to GF Piping Systems. Michael Rauterkus will join GF’s Executive Committee and will lead the new division together with his Uponor leadership team.
After all conditions of the tender offer have been fulfilled, GF closes the transaction as of 13 November 2023.
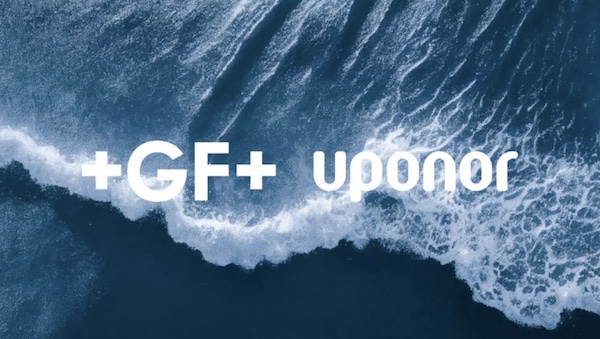
To accelerate the implementation of GF Piping Systems’ Strategy 2025 and to further benefit from global megatrends, GF will start an ambitious value creation program to unleash the full potential of this acquisition. GF Piping Systems will focus on the industrial and utility business, providing its customers with sustainable leak-free piping solutions for numerous end markets such as microelectronics, water treatment, energy, chemical processing, marine, data centers or water & gas utilities. Uponor’s infrastructure business will become part of GF Piping Systems and will further strengthen the division’s portfolio to provide customers with combined solutions.
In the new division, GF Uponor, the building technology businesses will be combined to offer a complementary portfolio for safe and clean water, as well as energy efficient heating and cooling. The consolidation of complementary businesses provides an ideal platform to develop markets with high potential for both divisions. As the brand Uponor stands for high quality and innovation, it will drive growth in intelligent Building Flow Solutions.
These organizational changes will be implemented during the course of 2024 while GF will ensure operational excellence and business continuity to customers.
“We will continue to implement our strategy, and leverage powerful global trends, such as the need for safe and clean water, or more efficient energy use,” GF CEO Andreas Müller said. “On behalf of all my colleagues, I am happy to welcome Uponor employees and start this new chapter together.”
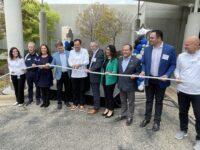
“It’s like Disney World for engineers and contractors,” said one visitor on the tour. The Mechanical Hub team made a quick visit to Apple Valley, Minn., to visit Uponor North America as the company celebrated the grand opening of its newly constructed Uponor Experience Center with a “pipe-cutting” ceremony. The team was treated to a Read more
“It’s like Disney World for engineers and contractors,” said one visitor on the tour. The Mechanical Hub team made a quick visit to Apple Valley, Minn., to visit Uponor North America as the company celebrated the grand opening of its newly constructed Uponor Experience Center with a “pipe-cutting” ceremony.

Andres Caballero (fifth from left) performs the pipe cutting for the new Uponor Experience Center.
The team was treated to a behind-the-scenes tour of the new 4,500-sq.-ft. customer experience center, which features hands-on displays, full-scale residential and commercial training areas, and cutting-edge innovation showcases, and a place to bring MEP students from the area to get a taste of the trades. The new Uponor Experience Center is a flexible education and discovery space designed to advance the technical skills of current and potential customers. In addition, it will help foster innovation within the plumbing and HVAC industry and provide an immersive experience for employees and visitors alike.

Some displays mimicked true applications.
The new Uponor Experience Center occupies the company’s previous customer training area, which was originally built in 2000 and renovated in 2010. It is at the center of the North American headquarters campus, surrounded by corporate offices, an R&D facility, and manufacturing space.
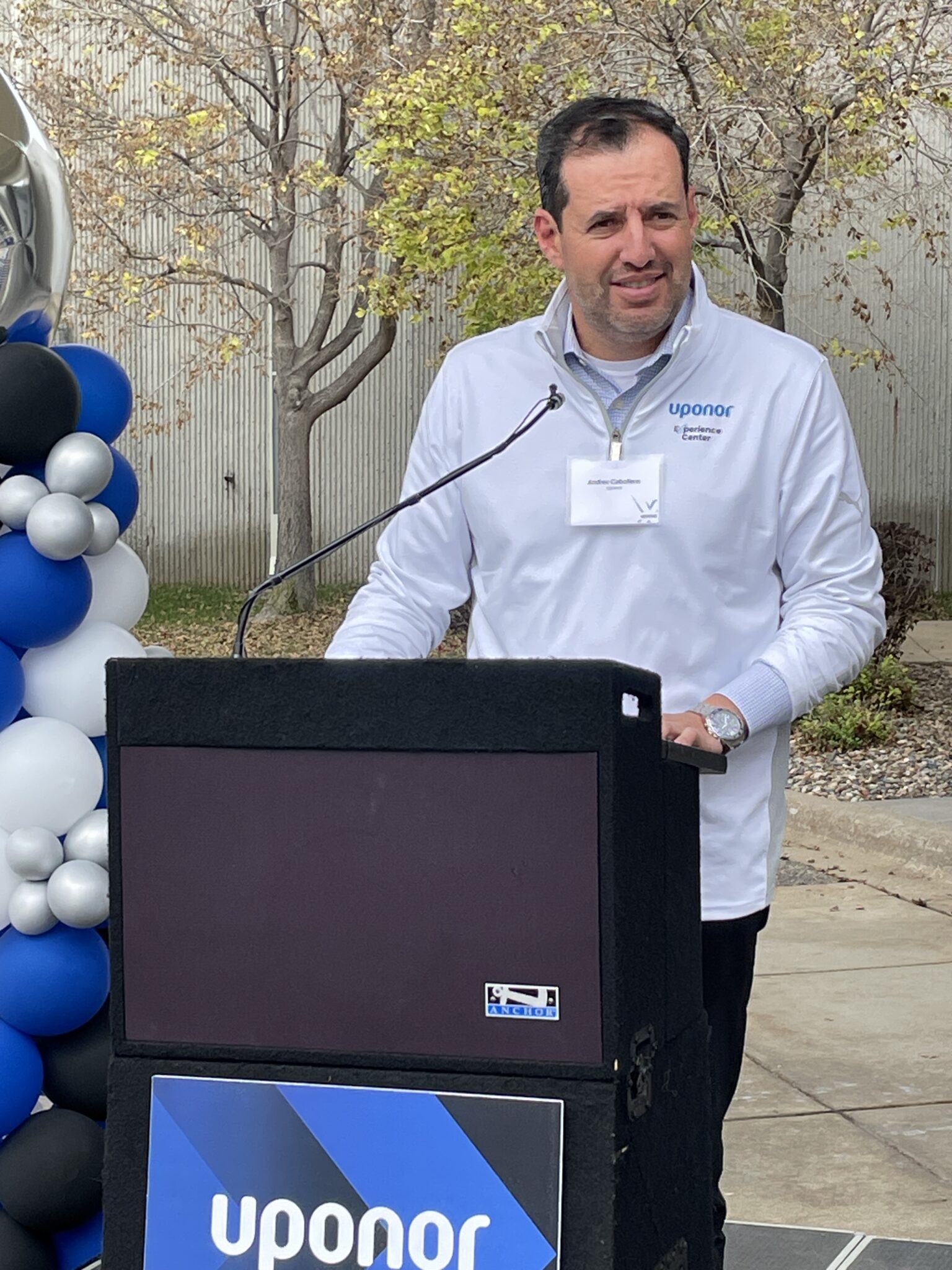
Andres Caballero thanks his staff for all of the hard work and dedication that went into planning and constructing the experience center.
“The opening of our new Uponor Experience Center signifies the importance we place on keeping the needs of our customers, employees, and key stakeholders top of mind as we continue our mission of becoming the global leader in sustainable water and energy solutions,” says Uponor North America President Andres Caballero. “The ‘X’, as our employees have begun to call it, is a culmination of our rich history and decades of innovation coming together to generate awareness and create enthusiasm for moving water more efficiently, effectively, and sustainably.”
With original concepts beginning back in 2020, the Uponor Experience Center was several years in the making. The thoughtful design, which takes into consideration the company’s rich Finnish roots, resulted from many months of internal team collaboration, as well as feedback from customers, partners, and industry influencers.

Mechanical Hub took the opportunity to record parts of the Appetite for Construction podcast with Des Clancy, director of training, Uponor, and the “architect” for the new center.
As guests move through the front doors toward the back of the space, they first experience displays depicting who Uponor is as a company along with the customers served and the unique value provided to key audiences and the industry.

Experience center visitors will get the full hands-on treatment as seen here with one of its gracious partners Milwaukee Tool and its PEX Expander.
Then, there are product showcases and interactive displays for plumbing, fire safety, radiant heating/cooling, hydronic piping, and pre-insulated piping system solutions for residential and commercial markets. Finally, there is an oversized training area, featuring both wood and steel structures, where professionals will learn proper hands-on installation techniques as well as how Uponor’s emphasis on problem-solving and productivity delivers results for their businesses.
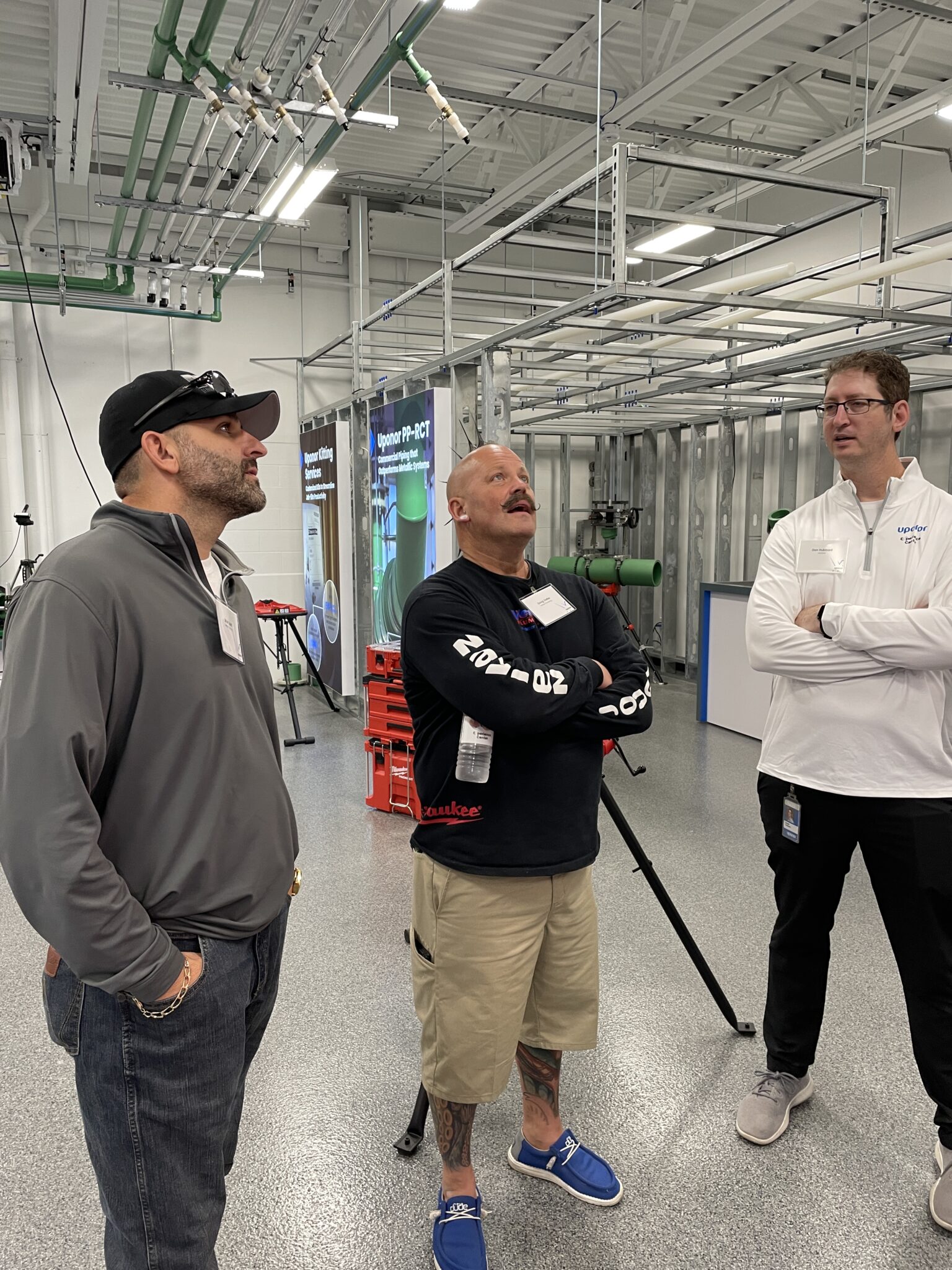
Doug Vetter, center, and Brian Spjut, left, from Vetter Plumbing, came all the way from Seattle to get a first glimpse of the space. (Pictured right is Uponor’s Dan Hubbard.)
“We wanted the Uponor Experience Center to extend beyond simply training customers on our products and systems,” says Vice President of Sales Matt Bahr. “As a result, we’ve created a holistic experience that spans a broad spectrum of who we are as a company, showcasing the depth and breadth of our product portfolio and sustainable solutions as well as providing access to the best trainers in the industry.”
With the focus not only on customers but also employees and those in the community, Director of Training Des Clancy says the planning team was very thoughtful about creating an elevated experience for everyone.
“At any given time, we will have contractors, builders, engineers, owners, students, employees, civic leaders, and other guests coming through the doors,” he says. “From tours and training, to onboarding and education sessions, the Uponor Experience Center offers something for everyone, and we are proud to showcase all we are offering to the industry and our community.”

Mechanical Hub’s John Mesenbrink (l) and Tim Ward (r) complete the “Uponor sandwich” as they also toured Uponor’s Distribution Center in Lakeville, Minn., with tour guide and director of logistics and warehousing, Nate McIntosh.
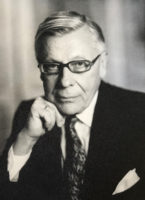
Courageous creator and unwavering visionary, REHAU mourns the loss of company founder Helmut Wagner. REHAU is mourning the loss of company founder and honorary president Helmut Wagner. He passed away last Sunday at the age of 95 in Switzerland surrounded by his family. The news of the death of the popular founding father, who was highly Read more
Courageous creator and unwavering visionary, REHAU mourns the loss of company founder Helmut Wagner.
REHAU is mourning the loss of company founder and honorary president Helmut Wagner. He passed away last Sunday at the age of 95 in Switzerland surrounded by his family. The news of the death of the popular founding father, who was highly committed to the end, has moved REHAU employees around the globe.
“The great sympathy for the passing of our father comes from many regions of the world. We are very touched by this as a family,” says Jobst Wagner, president of the REHAU supervisory board. “It shows the great the legacy that Helmut Wagner has left behind as one of the pioneers of modern industry, a courageous creator and unwavering visionary. We will honour the memory of Helmut Wagner by resolutely continuing his impressive work. His entrepreneurial spirit will continue to guide us,” says Wagner.
Helmut Wagner has been shaping the world of plastics since 1948 and has thus given important stimuli to an entire industry. His founding of the company in the city of Rehau, Upper Franconia, Germany, marked the beginning of polymer product manufacturing and the success story of a family-owned company that is still strongly characterized by the pioneering spirit of its founder.
After five decades of successful development, Helmut Wagner handed over the management of the corporation to his sons in 2000: Jobst Wagner became chairman of the supervisory board and Dr. Veit Wagner became vice chairman. The third generation is already active in shaping the family business. In 2015, Rehau city council paid a special tribute to the founder of REHAU: Helmut Wagner was appointed the first honorary citizen since the end of the Second World War.
Today, REHAU is an independent, privately held company with 20,000 employees at more than 170 locations worldwide. “We owe this in particular to the vision and courage of Helmut Wagner,” says William Christensen, CEO of the REHAU Group. “In deep mourning and sincere gratitude for the achievements of our founder, the REHAU family is especially united in these days,” Christensen said.
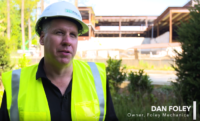
My company, Foley Mechanical, Inc. was invited to bid on a large commercial radiant project in a new healthcare facility being built in suburban Maryland, about 20 miles north of Washington, D.C. We would be the subcontractor of the primary mechanical contractor. After considering doing the work in house, the primary contractor decided it would Read more
My company, Foley Mechanical, Inc. was invited to bid on a large commercial radiant project in a new healthcare facility being built in suburban Maryland, about 20 miles north of Washington, D.C. We would be the subcontractor of the primary mechanical contractor. After considering doing the work in house, the primary contractor decided it would be quicker and easier to bring us in as radiant is our specialty.
We submitted a proposal and were awarded the contract. As this was a commercial project, full documentation was required which included design, shop drawings, and submittals. The radiant tubing manufacturer, Mr. PEX, was instrumental in working with me to put together the design and submittal package. After several revisions, the design package was approved and materials were ordered.
Several coordination meetings were held on site to determine scheduling, installation techniques, installation sequence, coordination with the concrete sub and other trades, and manifold locations.
We installed radiant floor heat in two areas of the building: the cafeteria, which is slab on grade, and the main entry mezzanine, which is concrete poured over steel decking. It was imperative for system operation to specify the correct insulation. We used 2” extruded polystyrene under the slab on grade zone. The mezzanine zone will have spray foam insulation under the steel decking.
Scheduling was critical. We had one day for rough-in on each zone. We arrived on site at 6am for a mandatory safety meeting. Full safety gear was required: work boots, hard hats, safety vest, eye protection and ear protection. The first step was mounting the manifolds. Then we started laying the loops, 14-loops for the first zone and 10-loops for the second zone.
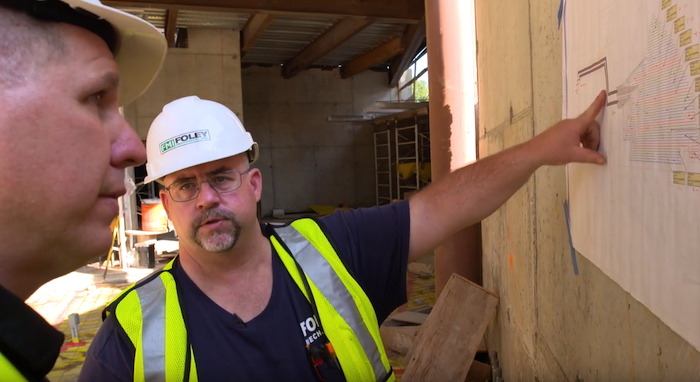
We invested in three Pex-Gun tie tools to increase speed and productivity over cable ties or squiggies. One man lays out the tubing while two men follow behind tying the tubing to the rebar with the Pex-Guns. The tubing installation follows a scaled tubing layout design provided by Mr. Pex. Another man attaches the tubing to the manifolds. This set-up makes quick work of tubing rough-in. My crew really liked the flexibility of the Mr. Pex tubing and the simplicity and ease of installation of the Mr. Pex manifolds.
After the tubing rough-in was complete, the entire system was pressurized with air to 100 PSI. It had to hold pressure for 24 hours before the concrete was poured. This pressure test was observed and documented by the primary mechanical contractor, the GC and the owner’s agent/engineer.
The concrete slab was poured the next morning. We had one of our techs on site to confirm the pressure test and observe the pour. This was a pumped pour so we wanted to make sure the concrete was poured without damaging the tubing. Pressure was monitored continuously during the pour. A repair kit was on hand in case the tubing was cut or damaged. Luckily, it was not needed.
Both slabs were poured without incident and are holding pressure. We will return when the building is complete and the mechanical system is started. We will flush and purge the radiant loops, coordinate the controls and motorized valves, and test & balance the radiant system. We have 10-turn balance valves on the return mains. In addition, the Mr. Pex manifolds allow for micro-balancing on each loop.
The building owner is looking forward to warm comfortable floors once the building is occupied. By partnering with the mechanical contractor, we both came out ahead. The job was done quicker and easier as we do radiant on a regular basis. We could not have done it without the help and support of Mr. Pex.
Dan Foley is owner of Foley Mechanical, Lorton, Va.
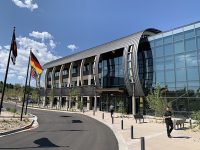
Recently, the Mechanical Hub team took part in a two-phase, two-state trip to visit Viega’s North American manufacturing in McPherson, Kansas, and toured the brand new HQ and Seminar Center in Broomfield, Colo. Impressive is the first thing that comes to mind when describing both facilities. The McPherson manufacturing facility exudes the company’s philosophy of Read more
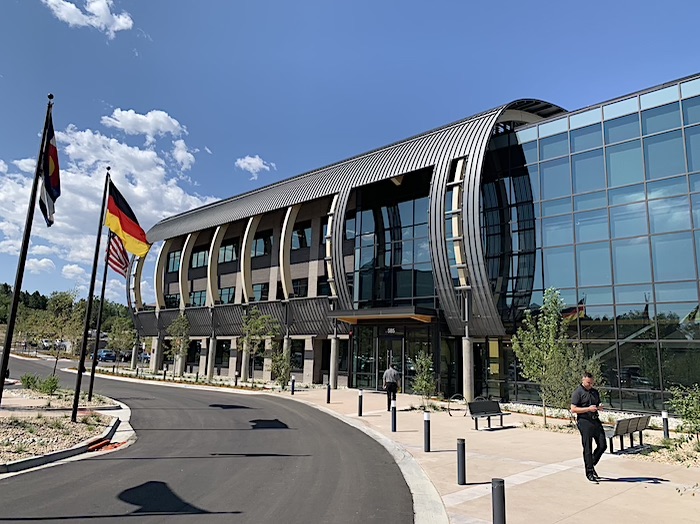
The new Viega North American headquarters in Broomfield, Colo., was designed to look like a fitting.
Recently, the Mechanical Hub team took part in a two-phase, two-state trip to visit Viega’s North American manufacturing in McPherson, Kansas, and toured the brand new HQ and Seminar Center in Broomfield, Colo. Impressive is the first thing that comes to mind when describing both facilities.
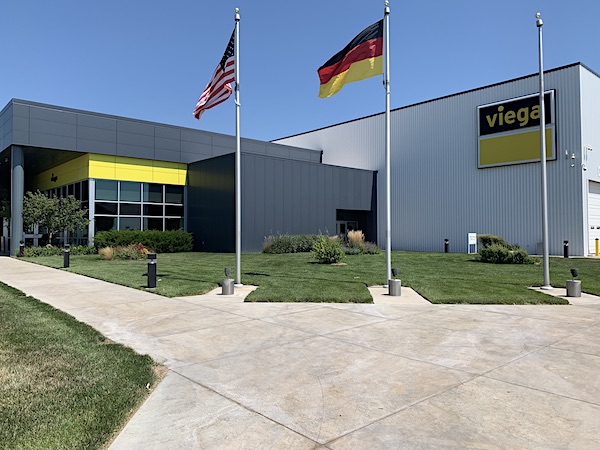
One of the Viega manufacturing facilities in McPherson, Kansas.
The McPherson manufacturing facility exudes the company’s philosophy of both progress and vision for the future. “We are constantly looking past the immediate future and into the distant future,” Eric Wicker, director, manufacturing, Viega.
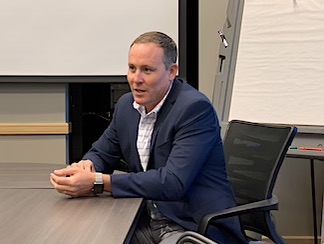
Eric Wicker, director, manufacturing, Viega
This summer, Viega completed a two-year building program in McPherson that included: a 90,000-sq. ft. expansion of a manufacturing plant, completed in Dec. 2017; a new 205,000-sq.-ft. manufacturing plant, completed in June; and a new 25,000-sq.-ft. tool shop and apprentice building, completed in July. And, the company is currently building a 55,000-sq.-ft. logistics expansion—a high-bay storage and retrieval area for inventory.
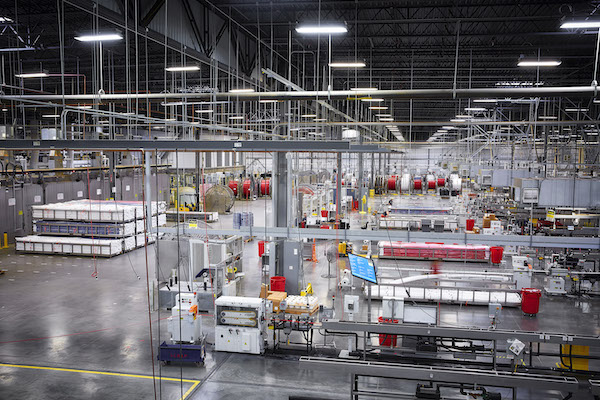
The manufacturing floor at the McPherson facility is as meticulous as it gets.
Mimicking some of the processes from its global HQ in Germany, robotics and machining take center stage throughout the meticulous McPherson plant. Fear not, all of this new-fangled technology is not taking jobs away, rather increasing them. Currently at approximately 300 employees, the company hopes to hit the 500 mark by years ’23-’24.
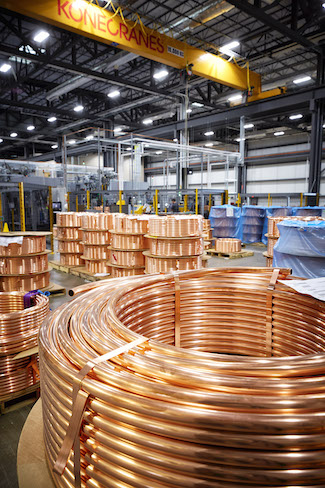
Some of the copper inventory, now produced in the states.
McPherson is where Viega produces its PureFlow line of PEX product, as well as select fittings from the ProPress Copper and 80,000 sq. ft. dedicated to its MegaPress product lines. McPherson is also home to Viega’s master distribution center for North America.
Continued expansion is a testament to the company’s progressive philosophy. For instance, the company has dedicated 270,000 sq. ft. to the copper fitting production. “The goal is to be producing the majority of copper fittings sold in the U.S. right here in the states,” says Wicker.
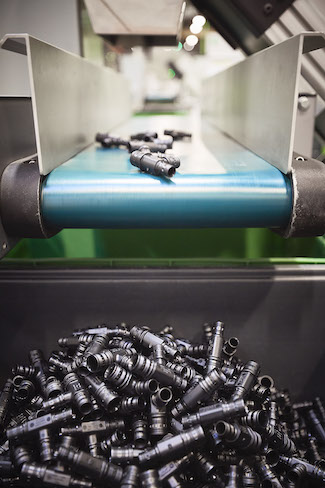
Plastic fittings rolling off the line. Seven million per month made in Kansas.
The state-of-the-art distribution center incorporates the latest technology and automation, as well as an upgraded warehouse management system that provides faster product turnaround. With additional metals products being manufactured in McPherson, a larger distribution center for both metals and PEX products was necessary.
Although media wasn’t allowed to shoot photography inside the plants—understandably—the tour started in the 36,000-sq.-ft. Plastic Injection Molding area which exemplified the company’s high investment in tooling. Twenty machines produce approximately seven million fittings per month. This particular building was well lit and comfortable, due, in part, by the implementation of its own radiant heating and cooling technology.
Quality is never understated at Viega; we strolled through the Quality Assurance Lab where dedicated staff monitor product and equipment through a series of rigorous testing.
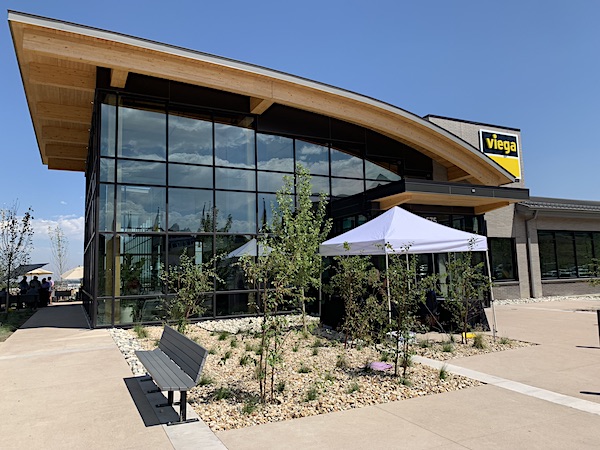
The Broomfield Seminar Center
Next, we toured the 200,000-sq.-ft. Extrusion Area where the plastic piping is made. Once made and exported from Georgia, Viega now produces its own resin—which is transformed into pellets—onsite. The rejected pellets are not repurposed, yet recycled and sold.
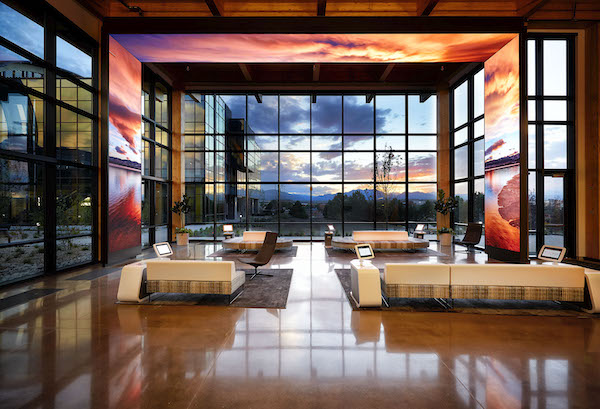
Whoa! Check out the beautiful seminar center, and the frickin’ view!
There is a Special Extrusion Area where plastic metal plastic tubing extrusion is performed. The only company in America making this, the plastic piping is integrated with aluminum so it can better hold its shape rather than returning back to its original form. (Nearby is a 40,000-sq.-ft. dedicated machine shop.)
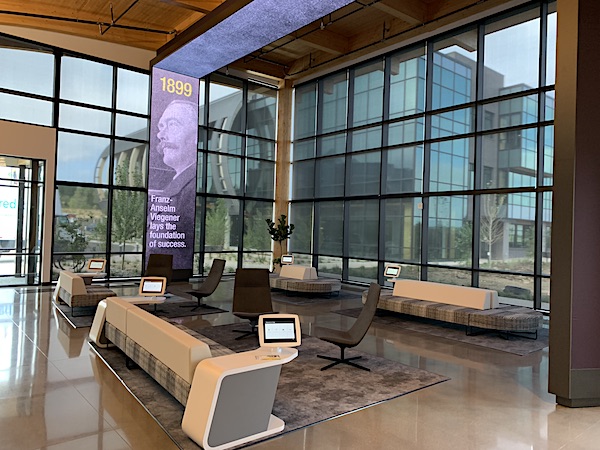
Another angle of the entrance to the seminar center with the HQ in the background.
We then toured the 270,000 sq. ft. of ProPress copper fittings production area and 80,000 sq. ft. of the MegaPress/Metals production area. Strategically, it makes sense for Viega to start producing here in the states. With press technology introduced here in 1999, education and awareness of the process and technology have helped contractors nationwide run a more efficient business. Viega system solutions are designed to work together in plumbing, heating, cooling and pipe joining applications, making the contractor’s work fast, easy and safe.
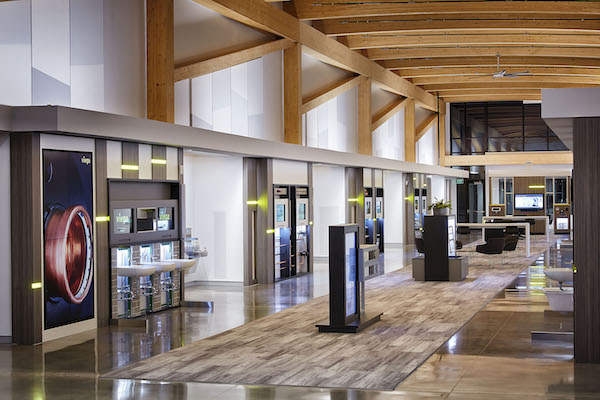
The seminar center features an interactive display area chock full of Viega products.
The following day we were flown to Denver to tour the recently opened Viega North American headquarters and Seminar Center in Broomfield, Colo. The 55,000-sq.-ft. headquarters resembles a pipe fitting, and its interior is the real testament to Viega innovation. I can’t express enough how beautiful these two buildings are, and, of course, amid the breathtaking backdrop of the Rocky Mountains. The HQ building opened in January and the first official training took place April 8, and weekly training is booking fast. “Viega is absolutely committed to its customers and their success in the field,” says Bo DeAngelo, manager, technical training at the center.
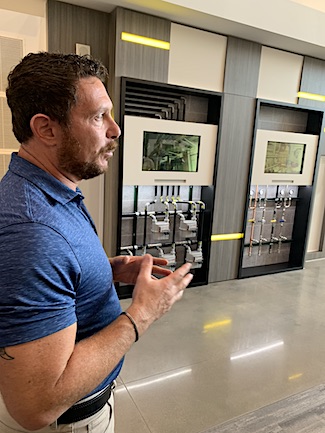
Like a proud new papa, Bo DeAngelo gives the tour of the new seminar center.
Yet, I am always interested: when a new facility is built, does it incorporate its own products? While the cross-laminated timber beams are imported from Austria, the exposed ceilings give employees and visitors a clear view of the many uses of Viega’s innovative technology.
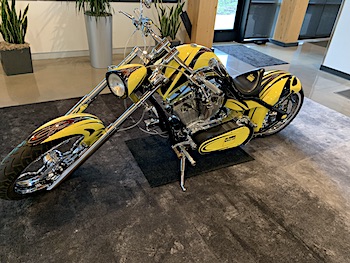
We’ve located the custom Viega chopper! It was taken in the middle of the night from the McPherson facility and relocated to Broomfield where it sits proudly on display. Who has the keys?
Potable water is carried through copper pipes connected with ProPress fittings. The carbon steel fire sprinkler system is joined with MegaPress fittings. Radiant heating and cooling keeps the building comfortable, while a snowmelt system keeps the courtyard free of ice and snow. Manifolds ensure the systems operate smoothly and efficiently. The restrooms feature wall-hung bowls and no exposed tanks, thanks to in-wall carrier systems and Visign style flush plates.
The new 23,000-sq.-ft. Broomfield Seminar Center next door supplements Viega’s Nashua, New Hampshire Seminar Center, which has trained thousands of people since opening in 2006. The new center is an innovative training experience and is equipped with four classrooms, two hands-on labs, and interactive displays throughout, which allows attendees to see, touch and experience Viega products. “Demand for training has been increasing steadily. This facility will allow us to continue to provide and expand on the training that our industry deserves,” says CEO Dave Garlow.
Viega experts lead single- and multi-day classes in everything from radiant system design and fire protection to hydronics and pathogen prevention. Despite being open only since April, it is on track to host more than 2,100 students this year, says DeAngelo.
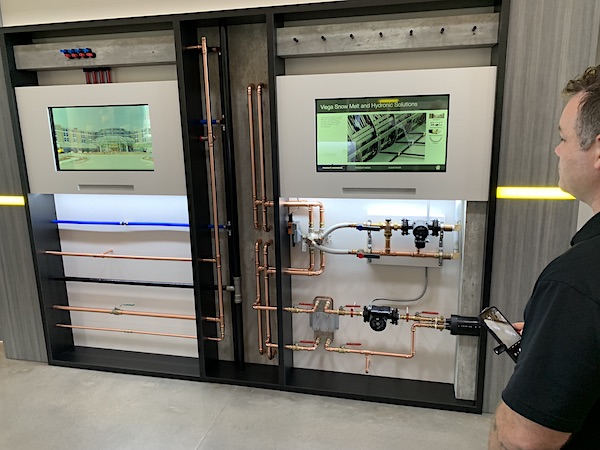
The Hub’s Eric Aune checks out the hydronics and snowmelt display.
I walked away very impressed, telling DeAngelo I—and I’m sure the clients that visit—can’t help but feel energized the minute I walk in this facility. Shaking his head in agreement, “That’s what Dave Garlow tells me every day he walks in here,” responded DeAngelo.
Make no mistake, there is a lot of money, time and resources invested in Viega North America. But it’s a huge testament to the dedication the company believes is its biggest investment: its customers and its employees.
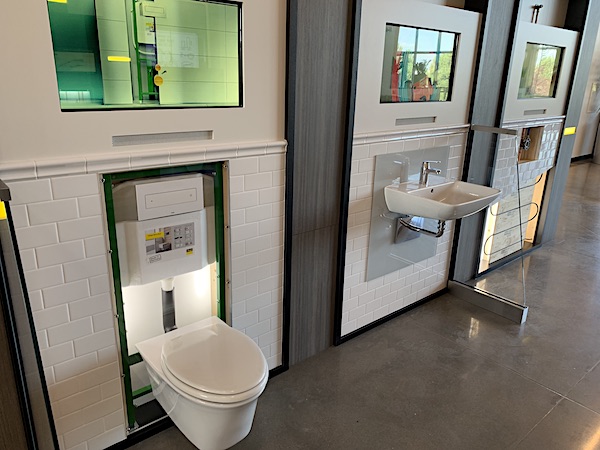
The interactive display at the Broomfield Seminar Center features a breadth of innovative Viega products.