Pressure and Chlorine Ratings Revised Recent revisions led by the Plastics Pipe Institute, Inc. (PPI) Building & Construction Division resulted in improvements to the latest edition of the ASTM Standard, F2389 Standard Specification for Pressure-Rated Polypropylene (PP) Piping Systems, which establishes requirements for polypropylene (PP-R and PP-RCT) piping system components including pipe, fittings, valves, and Read more
Plastics Pipe Institute
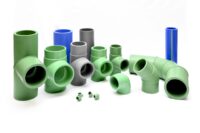
Pressure and Chlorine Ratings Revised
Recent revisions led by the Plastics Pipe Institute, Inc. (PPI) Building & Construction Division resulted in improvements to the latest edition of the ASTM Standard, F2389 Standard Specification for Pressure-Rated Polypropylene (PP) Piping Systems, which establishes requirements for polypropylene (PP-R and PP-RCT) piping system components including pipe, fittings, valves, and manifolds. The standard applies to hydronic heating and cooling, chilled water, water service lines, hot-and-cold water distribution, irrigation systems, and other related fluid transport applications.

PP-R and PP-RCT pipes and fittings discussed in the recently updated ASTM Standard F2389-24a are available in diameters from 16 mm to 710 mm, also known as nominal diameters 3/8 to 28 inches. Photo courtesy of PPI.
Originally issued in 2004, revisions to the latest edition of the standard published in July 2024, F2389-24a, include:
- Pressure-temperature ratings used for PP pressure pipe systems are clarified and harmonized by adding new definitions for “design stress” and “design coefficient” and then applying requirements for these factors in a new Section 5.6.1.
- Oxidative stability (i.e., chlorine resistance) classifications are revised from CL-TD and CL-R to Classes 0, 1, 3, and 5 for consistency with other pressure pipe standards (e.g., ASTM F876).
- Marking requirements are also revised.
According to Lance MacNevin, P. Eng., director of engineering for PPI’s Building & Construction Division, “As a result of these recent revisions, pressure ratings will be more consistent throughout the industry and classifications for resistance to hot chlorinated water will be consistent with other piping materials.”
MacNevin continued, “Polypropylene (PP) is a versatile piping material that is used in a wide range of applications. Two types of PP are used for pressure piping systems: PP-R (polypropylene random copolymer) and PP-RCT (polypropylene random copolymer with modified crystallinity and temperature resistance). With their high temperature and pressure capabilities, PP-R and PP-RCT pipes are suitable for demanding pressure piping applications, such as plumbing, hydronics, and chilled water in commercial high-rise buildings or data centers.”
PPI is the non-profit North American trade association representing the plastic pipe industry, including several manufacturers of PP pipes and fitting systems. PPI formed the Polypropylene Pressure Pipe Steering Committee in 2018 to collaborate on industry standards such as F2389, coordinate research programs, develop technical publications, and create educational information about these systems. The recent revisions to F2389 are the latest result of cooperation between PPI member firms, intended to help to grow this market in a technically correct and responsible manner.
The revised standard is available directly from ASTM at: www.astm.org/f2389-24a.html.
Additional information and data about the use and installation of PP is available from the PPI Building & Construction Division at www.plasticpipe.org/buildingconstruction.
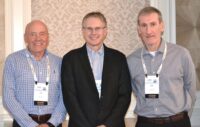
The Plastics Pipe Institute, Inc. (PPI) announced today that its Building & Construction Division (BCD) has elected Bill Melvin of Legend Valve (Auburn Hills, MI) as Division Chair and Jim Paschal of Aquatherm (Lindon, UT) as Vice Chair. Melvin, who will also represent the division on the PPI Board of Directors for the next two Read more
The Plastics Pipe Institute, Inc. (PPI) announced today that its Building & Construction Division (BCD) has elected Bill Melvin of Legend Valve (Auburn Hills, MI) as Division Chair and Jim Paschal of Aquatherm (Lindon, UT) as Vice Chair. Melvin, who will also represent the division on the PPI Board of Directors for the next two years, takes over from Joseph Poniatowski of Asahi/America. The changes took effect June 1, 2024. PPI’s BCD focuses on pressure piping materials for plumbing and mechanical applications.

Jim Paschal (left) of Aquatherm, new Vice Chair and Bill Melvin (right) of Legend Valve new Chair of PPI’s Building & Construction Division with Lance McNevin, the engineering director for the division.
Bill Melvin has served on the Management Committee in several roles, including the Communications Committee Chair and Vice Chair. Jim Paschal also serves as Chair of PPI’s Polypropylene Pressure Pipe Steering Committee and formerly served as R&D Projects Chair. That position will now be filled by Rick Stock of Uponor. Brian Conner of Charlotte Pipe and Foundry joins the committee as Codes & Governments Affairs Committee Liaison.

Rick Stock, Uponor
Adam Grier of iNOEX serves as the Communications Committee Chair, and also as Chair of the PPI Umbrella Marketing Committee. Jason McKinnon of Viega LLC serves as the PPI Education Committee Chair and also as the BCD Education Chair, a position he has held for more than eight years. Forest Hampton III of Lubrizol continues as Advisory Council Liaison & Strategic Planning Chair.
According to Lance MacNevin, P. Eng., director of engineering for PPI’s Building & Construction Division, “PPI’s management committee members provide significant guidance to staff on topics from research, codes and standards to education and advocacy. These new leadership positions solidify their continued commitments to PPI and the piping industry. We are grateful for the volunteer service of these dedicated members.”

Brian Conner, Charlotte Pipe and Foundry
PPI is the major North American trade association representing the plastic pipe industry. The Building & Construction Division represents plastic pressure piping materials such as CPVC, HDPE, PEX, PE-RT, PP-R, and PP-RCT.
More information can be found at https://plasticpipe.org/buildingconstruction
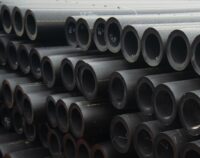
Covers Performance Requirements and Details Comparisons The Plastics Pipe Institute, Inc. (PPI) recently announced the publication of a new document that provides the technical basis for comparing PE 100-RC to PE4710 pressure pipe. Called PPI TN-68, Historical Review of the PE 100-RC Concept – How PE4710 Compares to PE 100-RC, it will provide a perspective Read more
Covers Performance Requirements and Details Comparisons
The Plastics Pipe Institute, Inc. (PPI) recently announced the publication of a new document that provides the technical basis for comparing PE 100-RC to PE4710 pressure pipe. Called PPI TN-68, Historical Review of the PE 100-RC Concept – How PE4710 Compares to PE 100-RC, it will provide a perspective on the Slow Crack Growth (SCG) resistance requirements for the PE 100-RC designation in comparison with the North American PE4710 designation. This publication offers a common basis and understanding to industry. PPI is the major North American association representing the plastic pipe industry.
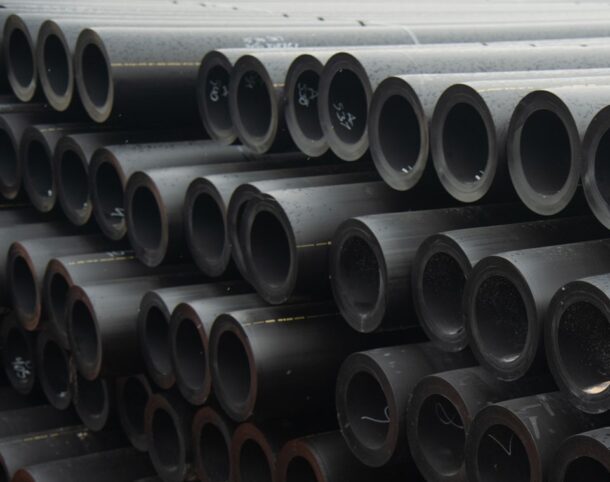
“The PE 100-RC concept has been around since 2009,” stated Patrick Vibien, P.Eng., technical director, PPI, “but there is a lack of clarity to the implications of the designation and a lack of consensus on whether a comparable designation has value for the North American industry given the already elevated SCG resistance requirements of PE4710. The development of the PE 100-RC designation was not due to documented performance issues with PE 100. This grade designation has been promoted internationally by the PE 100+ Association and is now being introduced into ISO and CEN standards. Although PE compounds are fairly similar, the test methods and requirements for assessing the performance of the designations differ significantly. Our new document goes into detail about this plus provides a comparison chart and other data that can be helpful and useful.”
TN-68 can be found on the Technical Notes page of the PPI website www.plasticpipe.org.
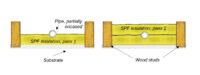
New Technical Document and Details Proper Steps for Use A new technical document that addresses techniques for the safe and proper use of spray polyurethane foam insulation on and around plastic pressure pipe materials has been published by the Plastics Pipe Institute, Inc. (PPI) with input from the Spray Polyurethane Foam Alliance (SPFA). Prepared by Read more
New Technical Document and Details Proper Steps for Use
A new technical document that addresses techniques for the safe and proper use of spray polyurethane foam insulation on and around plastic pressure pipe materials has been published by the Plastics Pipe Institute, Inc. (PPI) with input from the Spray Polyurethane Foam Alliance (SPFA).
Prepared by PPI’s Building & Construction Division, PPI TN-69 Recommendations when Applying Spray Polyurethane Foam Insulation on and around Plastic Pressure Pipes & Fittings discusses the proper application of spray polyurethane foam insulation to avoid damage due to heat generated by the foam. Pipe and fitting materials include CPVC, PEX, PEX/AL/PEX, PE-RT, PP-R, PP-RCT, PSU, PPS, PPSU, and PVDF.
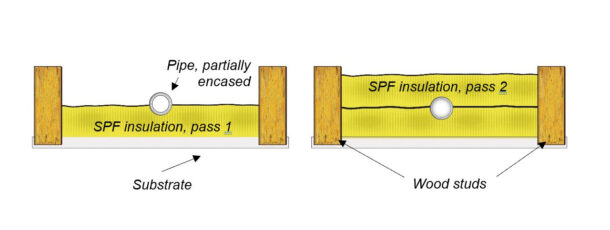
Figure 1: The first layer of SPF insulation is stopped when it reaches the pipe (left), just barely touching or encasing it. After sufficient cooling time, the second layer of SFP insulation is sprayed over the pipe to the required thickness (right).
PPI and SPFA recommend that when there are plastic pipes and fittings in a wall, ceiling, or floor cavity, the SPF installer should apply one layer of foam until it touches the pipe but does not encase the pipe. SPF installers should let the first layer of foam cure for a sufficient amount of time while heat is released from the foam and the pipe remains partially exposed before installing the second layer of foam. These procedures are described in detail within PPI TN-69.
Plastic pressure pipes and fittings are commonly used in applications such as hot- and cold-water plumbing, fire protection, and hydronic heating and cooling systems, including radiant distribution systems. In certain instances, pipes and fittings are installed inside areas that must be insulated, such as within a ceiling or wall cavity. In other installations, the pipes and fittings themselves must be insulated to reduce the transfer of heat through the pipe wall.
According to the SPFA, Spray Polyurethane Foam, or SPF, is a high-performance insulation material commonly used in homes and buildings of all types, and has been used as insulation for decades.
“The spray polyurethane foam curing reaction is exothermic,” explained Richard Duncan, Ph.D., P.E., executive director of SPFA, “which means that heat is generated during the foam reaction. The heat of reaction is highly dependent on the SPF formulation and is also based upon the overall intended application or lift (i.e., layer) thickness installed. Peak temperature within the layer of foam typically occurs within 5 to 15 minutes of application, followed by gradual cooling.”
According to SPFA documents, the chemical reaction that takes place during the application and curing of SPF will generate exothermic temperatures above the 120°F – 130°F setpoint temperatures of the proportioner and hoses. Peak temperatures at the mid-thickness of a pass can exceed 200°F for several minutes and reach peak temperatures 250°F – 275°F for a minute or two, especially for closed-cell SPF, when applied at the maximum pass thickness.
“Plastic pipes and fittings in both residential and commercial plumbing, residential fire protection, and most hydronic applications are typically required to have pressure ratings at 180°F (82°C) operating temperature,” explained Lance MacNevin, P. Eng., director of engineering for PPI’s Building & Construction Division.
MacNevin continued, “The plastic pipes and fittings referenced in PPI TN-69 will withstand short-term exposure to temperatures above 180°F. However, exposure to temperatures above the rated operating temperature of each material, which may occur if pipes are encased in a thick pass of closed-cell SPF, are likely to have negative effects on these materials, potentially leading to premature failure. It is important that SPF insulation is installed correctly to prevent overheating of pipes and fittings.”
Access the full content of PPI TN-69 at https://plasticpipe.org/common/Uploaded%20files/Technical/TN-69/PPI%20TN-69.pdf or by scanning:
Additional information and data about pressure pipe materials used for plumbing and mechanical systems are available from the PPI Building & Construction Division at www.plasticpipe.org/buildingconstruction