Speed and accuracy are the name of the game when it comes to a successful piping installation and a thriving business. Whether you’re installing potable plumbing or hydronic piping, the faster and more precise the job, the more time and money you potentially have to work on other projects. While there are hundreds of tips Read more
prefab
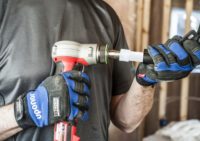
Speed and accuracy are the name of the game when it comes to a successful piping installation and a thriving business. Whether you’re installing potable plumbing or hydronic piping, the faster and more precise the job, the more time and money you potentially have to work on other projects.
While there are hundreds of tips and tricks out there to make your installs faster, easier, and more effective, I’m going to concentrate on the following three methods almost any plumbing or mechanical contractor can use to bring greater productivity to projects.
Flexible PEX pipe with bend supports
If you’ve never heard of PEX, it’s an acronym for crosslinked polyethylene. It’s a flexible, durable plastic piping product that provides numerous benefits over rigid CPVC or metallic systems, including faster installs, zero corrosion, and freeze-damage resistance.
Many residential contractors are already using PEX (considering it’s the most installed piping system for new-home construction over copper and CPVC combined). However, PEX is still a relative newcomer in the commercial industry.
The biggest benefit of PEX is its flexibility, which allows you to simply bend the pipe with each change in direction. With a tight bend radius of six times the pipe’s diameter, you can practically make 90-degree bends without the need for a fitting.
For times when you do have a tight bend that needs to stay in a particular place, PEX manufacturers offer bend supports. For those of you that prefer to watch rather than read, here’s a video that explains bend supports in detail.
These helpful products are available for ⅜”, ½”, ⅝”, ¾”, or 1″ PEX pipe. They hold the bend in place at the proper angle and take a fraction of the time compared to making a 90-degree elbow.
Most contractors agree that using flexible PEX with bend supports can eliminate most fittings in smaller-diameter pipe sizes 1″ and down, saving up to half the install time of a rigid piping system.
Expansion tools
When it comes time to make a connection with PEX pipe, the professionals’ choice is PEX expansion. Note that expansion connections are only designed for PEX-a pipe. If you’re using PEX-b or PEX-c pipe, you’ll need to use a different fitting type as PEX-b and PEX-c pipes aren’t made to expand like PEX-a pipe, and they will experience microcracking during expansion.
Expansion connections require one simple tool that expands the pipe and an expansion ring before inserting a fitting. As the pipe and ring shrink back down around the fitting, it creates a solid, strong seal that can withstand up to 1,000 pounds of radial force. It’s quick and easy to do and simple to learn, so it’s highly beneficial with the skilled-labor shortage that’s challenging the trades. Here’s a quick, 20-second video on how to make a connection.
Now, to make installs even faster, expansion tools have advanced to make connections even quicker. For up to 1″ connections, the Milwaukee® M12 FUEL™ ProPEX® Expander with RAPID SEAL™ Heads is the fastest tool yet — with up to 65% faster sealing times compared to previous models.
For larger-diameter pipe connections, the new Milwaukee M18 FUEL™ ProPEX Expander with ONE-KEY™ is taking commercial installs to a new level by offering 3X faster 2″ connections. To watch how much faster, check out this video from Milwaukee Tool.
Prefab
Finally, let’s talk about prefabrication. This is becoming a big trend for national residential builders or large commercial projects that have a lot of repeatability on the project. By prefabbing certain sections of a project, it can shave days, weeks, or even months off a timeline, depending on how big the project.
Prefabricating piping assemblies in a controlled factory environment not only adds more efficiencies, it also provides an additional benefit of greater accuracy. By doing a job repeatedly, it hones the skill and gives installers greater confidence in their work.
Plus, having rows and rows of prefabbed piping assemblies in a shop environment makes it a lot easier to perform quality checks. Instead of walking for miles on a job site, a supervisor can save significant time simply walking a shop floor.
And here’s another area where flexible, durable PEX provides additional benefits. Transporting prefabbed PEX piping assemblies is much easier than transporting rigid assemblies that can crack or break. Because PEX is super flexible, it can withstand the rigors of being transported to a job site without worry.
So, there you have it…just a few ideas to keep in mind the next time you have a project with a tight deadline, and you’re squeezed on time and skilled labor. Every little bit helps when it comes to adding productivity to projects. If you have other ideas, I’d love to hear them. Feel free to email me at kim.bliss@uponor.com.
Kim Bliss is the technical and marketing content manager at Uponor. She can be reached at kim.bliss@uponor.com.
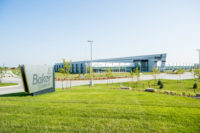
Conversations about the skilled labor shortage have become commonplace. And though high profile champions, like Mike Rowe, have given new visibility and importance to the looming challenge that threatens all trade professions nationwide, articles typically bemoan the lack of young people entering the trades while offering few solutions. The need for qualified technicians isn’t the Read more
Conversations about the skilled labor shortage have become commonplace. And though high profile champions, like Mike Rowe, have given new visibility and importance to the looming challenge that threatens all trade professions nationwide, articles typically bemoan the lack of young people entering the trades while offering few solutions.
The need for qualified technicians isn’t the only concern facing the trades, though. Others issues – such as quality of work and the time in which it’s completed – are as much a symptom of the first problem as they are challenges in their own right.
Many proactive, growing companies have squared off with the workforce shortage out of necessity, dealing it blows where they can. This often comes in the form of a bolstered recruiting game, or a train-your-own technician approach.
Local advocacy in high schools helps, too, though positive results come gradually as part of a longer-term effort. And, some companies implement systems and QC measures that help, to a degree at least.
If Baker Group, in Des Moines, IA, wasn’t already a mechanical force to be reckoned with over the past half century, this changed dramatically in early 2017.
Managers within the 650-person design-build firm, already intimately familiar with the advantages of prefabricating plumbing and mechanical systems offsite, made a bold move to expand their manufacturing space by nearly 150 percent. This, they say, has helped to solve several high-level concerns.

Baker Group is a 650-person, design-build mechanical firm in Des Moines, IA.
Manpower, quality, timeline
The decision to expand was made in order to produce higher quality products, in less time, without creating an unrealistic need for additional skilled manpower.
The firm’s new, 144,000 square-foot facility contains offices as well as manufacturing space, and is called Baker Group Advanced Manufacturing. As many as 75 craftsman can work during a single shift.
“We’ve done prefabrication work since the 1960s,” said Rob Cross, operations manager at Baker Group. “We added a large shop in 1998, and since then, we’ve steadily gained momentum. Our growth necessitated this new expansion last year.”
“The dynamic of the entire construction industry today is built on quality and speed,” says Tom Wengert, VP of Baker Group’s sheet metal business unit. “With this facility, we can prefab systems in a controlled environment, which improves quality while reducing labor costs.
“Additional benefits include increased safety, less congestion on construction sites, less jobsite trash and better scrap material recycling,” added Wengert.
While speed and quality are two major advantages to having a large manufacturing space at your disposal, the efficiency of off-site manufacturing means that fewer employees are needed to accomplish the same task.
Much of the in-shop sequencing implemented by Baker Group at the new facility was adapted from the automotive industry. For example, the flow of materials comes in west side of the shop and leave on the east side.
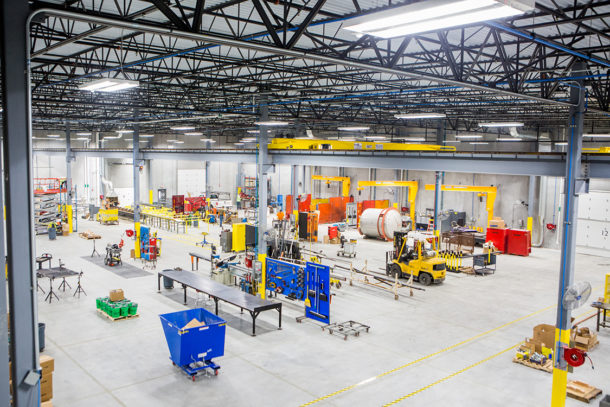
In 2017, Baker Group expanded their manufacturing space by 150 percent, or 144,000 square feet.
More than sheet metal
Completed in March of 2017, Baker Group Advanced Manufacturing includes 80,000 square-feet of fabrication space with almost 9,000 of that dedicated to multi-trade prefabrication alone.
The multi-trade space is located centrally among the sheet metal, piping and electrical shops. Here, trades work collaboratively in a weather-controlled environment to build to specifications and then ship to the job site.
The space features a 10-ton crane, allowing workers to construct large assemblies. By reducing on-jobsite time, this moves the entire construction timeline forward. The approach increases value to clients, and more than doubles Baker Group’s production capacity.
It’s in this centrally-located, multi-trade space that the various trades come together to assemble systems, sometimes even full mechanical penthouses. Welders work on framing and dunnage while pipefitters connect boilers, chillers, pumps and other equipment. Electricians wire the components and control technicians prepare everything to plug into a BAS.
“A good example of how we build to exact specifications in the shop can be seen in fabrication of gang restroom assemblies,” said Cross. “We can complete an eight-stall bathroom assembly in a little over a day, where it would take nearly a week onsite.”
Welders create an angle-iron framework, perfectly centering all the Watts closet carriers. Once assembled, the system is piped and hydro-tested. Waste water is also tested before the assembly is broken into several pieces for deliver to the job.

A Baker Group mechanic prefabricates large gang restroom assemblies at the new Advanced Manufacturing facility.
Baker Group has used the Watts back-to-back wall mounted, floor mounted and single closet carrier configurations for a wide variety of projects.
“We’ve standardized on the Watts carriers because the fab crews prefer them and they can be rapidly assembled,” said Cross. The Watts “industry standard closet carriers” come out of the box pre-assembled. The carriers feature a patented compression sealed nipple, which provides fast installation without the need for additional sealants. Adjustment is much easier than when threaded nipples are used.
“We never have any trouble with the closet carriers once they’re in the field, and the support we get from Jeff Howe, at Mack McClain & Associates – our manufacturer’s rep agency – is fantastic,” he continued
Cross has been with Baker Group for 23 years, and the relationship with rep firm Mack McClain goes back as long as he can remember. The firm supplies most of Baker Group’s plumbing components, including toilets, eyewash stations, backflow assemblies, drains and water heaters.
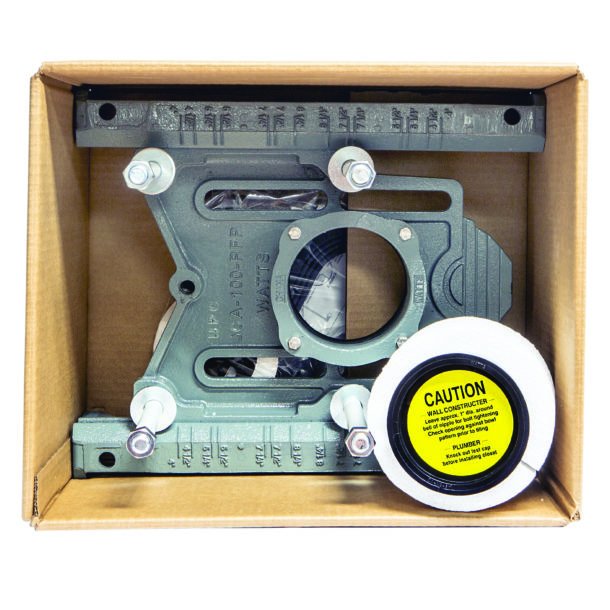
Baker Group has standardized on Watts closet carriers because the fab crews prefer them and they come out of the box pre-assembled.
Still adding capabilities
Toilet carriers aren’t the only plumbing systems that Baker Group prefabricates though. Like their ability to assemble boiler and chiller systems offsite, mechanics also build water service entrances, backflow assemblies, pump skids, pressure reducing stations and water purification systems. Once assembled, these items are broken down only as far as needed to be palletized, and the kits shipped to the jobsite.
“Every year we add something new to what we fabricate here on site,” Cross says, adding that Baker Group’s mechanical capabilities now include fabrication of ASME-rated vessels and components. “We’re equipped with the skills, knowledge, equipment and space to do this intricate and very strict code welding work.”
“Give us your biggest problem; the answer lies within the body of knowledge our people possess. We’ll find the solution,” he continued.

A premanufactured restroom assembly installed onsite.
Filling the new shop
While Baker Group Advanced Manufacturing allows the company to provide more capacity with reduced manpower, the need for new hires to fill the shop still requires ongoing effort.
“We’re a big local advocate for the trades,” said Cross. “We visit high schools and technical schools, invite people to take tours or do job shadowing programs. But we still can’t hire fast enough to fill the need.”
Baker Group is one of the largest, most capable design-build contractors in the Midwest, and they take that title seriously.
The content available on their website and YouTube channel speaks not only to potential clients, but also potential employees.
If the company’s dedication to recruiting parallels their insistence on delivering the best solution on time and on budget, staffing the new shop won’t be an unsurmountable task.
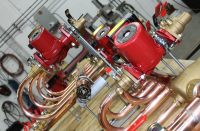
This edition of “They Said It” concentrates on prefabrication in construction of plumbing and hydronic systems. After attending numerous conventions and seminars over the course of the past six months, one topic resonated: prefab is the future of construction. We talked with industry experts from across the board—contractors and manufacturers—to share viewpoints on the benefits Read more
This edition of “They Said It” concentrates on prefabrication in construction of plumbing and hydronic systems. After attending numerous conventions and seminars over the course of the past six months, one topic resonated: prefab is the future of construction. We talked with industry experts from across the board—contractors and manufacturers—to share viewpoints on the benefits of prefabrication.
What are some of the major benefits of prefabrication?
Robert O’Brien, owner of Technical Heating Co. LLC, Mt. Sinai, NY.
Prefab speeds up installation time, shaves hours, and, quite often, a day from installation time. This is huge since all we do is replacements and not many homeowners want to spend a night or two without heat, particularly in the winter. We do in one day that others would take two days. Also, it is aesthetically pleasing, offers better serviceability. It has become a signature and a selling point.
Barry Campbell, vice president of marketing, Aquatherm
Prefabrication can save time and money on the jobsite, as well as help ensure consistent, high quality assembly. Prefabrication services allow a manufacturer to serve as an essential extension of a contractor’s team, easing the workload and helping a project meet its deadlines.
Time is money—and nowhere is that more evident than in today’s construction industry. Since plumbing and mechanical profit margins are tighter than ever, contractors need solutions that separate them from their competition. A good manufacturing partner that offers prefabrication services can add value and help make a contractor’s job easier.
By having systems prefabricated and shipped directly to the jobsite, the labor savings compared to onsite fabrication can be significant, as prefabricated parts can simply be moved into place and connected together to form a system. In addition, safety can be improved by removing the fabrication work from the jobsite and outsourcing it to the manufacturer. The prefabrication process can be as simple or as extensive as a customer and a project requires.
Aquatherm, for example, can take a simple hand drawing and turn it into an intricate digital design document. Or, the company’s extensive engineering expertise and fabrication skill can be extended as a service to help show a customer the best way of designing a mechanical system and providing complete fabrication drawings. The Aquatherm team brings an array of building information modeling (BIM) tools to the table, including a full Revit library and a team with the skills to use it.
Shane Fink, owner, Triple H Hydronics, Calgary, Alberta, Canada
One of the most overlooked benefits is having detailed layouts and extensive system planning done well before construction ever starts. Many systems today are designed “as you go” in a mechanical room, and there are many mistakes made in the haste of designing and building the system at the same time.
Another major benefit is time savings. We are able to help design and prefabricate the systems, sometimes before the building structure is even standing. By having a well-executed layout and design, we are able to cut time on site by more that 50%. Many times this saves money on temporary heating costs, as well.
Another great benefit is workmanship and attention to detail. When we are in a controlled environment with all of our tools at our fingertips and not in the elements—cold winters—we are able to take the time required to do an excellent job. In the field there are many pressures to “get it done” and use what you have, so sometimes that attention to detail can slip away.
One of my favorite benefits would be quality testing. In our shop, we are able to test every system before it leaves from the loading docks. We have to ability to hydro-test the systems @ 5 times working pressure, to ensure the systems are leak-free. We are also able to electrically test the systems for proper operation and pre-program settings to save time and money in the field.
For custom-built hydronic panels, for instance, take me through the process. Are you onsite consulting with the client? (Measurements, heat load calcs, etc.)
O’Brien: We make site visits to take measurements, size boiler, water heater and accessories. We take pics to facilitate panel construction, and most importantly, sell the job!
Campbell: Customers contact their Aquatherm representative to initiate the process, then the Aquatherm Design & Fabrication team works directly with the customer to obtain drawings and walks them through all the steps necessary to deliver final drawings for approval. The pieces are then meticulously created and shipped to the jobsite.
Whether it’s a detailed spool, large diameter elbows, or complex manifolds, Aquatherm offers a dedicated and experienced professional staff and a vast collection of high-tech design and heat fusion equipment to create it. The company also produces unitary spool fabrications that can help reduce a project’s bottom line.
Prefabrication with Aquatherm often is possible where it would not be with other materials, as Aquatherm pipe is considerably lighter than metal pipe. This results in an easier prefabrication process and simplified transportation to the jobsite.
A proper heat fusion connection results in a joint as strong as the pipe itself. Additionally, PP-R is incredibly sturdy, yet slightly flexible. So after Aquatherm prefabrication services has meticulously created a custom spool, it will be carefully shipped to a jobsite anywhere in the U.S. or Canada, typically resulting in significant material and/or labor savings. Often, the prefabbed pieces are simply flanged into place.
Aquatherm’s design coordination and fabrication process cab help ensure a smooth job. With an extensive list of past projects, Aquatherm’s fabrication services team will find a solution to fit any project’s needs. For more information, www.aquatherm.com.
Fink: Most of our clients have either worked with us for years, have been referred by another client or find us on social media. In most cases the process is the same. First we start with the blueprints. Our clients send over architectural drawings of the building proposed. We do a heat loss/heat gain calculation and start working with the client to determine their needs. This usually involves laying out zones for heating, determining domestic hot water consumption demands, ventilation requirements and other items such as snowmelt, heated towel bars, pools, spas, etc. Once we determine what the client requires, we complete a loop layout for all the floor heating so that they can be submitted with the heat loss calculations and building permit applications.

After the panel has been built and polished, we start the wiring and controls. This can sometimes range from a couple hours to a week or more, depending on the size and complexity of the system.
At this point an estimate is produced for the manufacture of the hydronic heating panel. Once the client has approved the estimate, we go to work on the design of the panel itself. The panel design has many considerations and we do our best to ensure a smooth installation. This design includes boiler/venting locations, condensate drain locations, floor or wall mounted boilers, which side of the pre-fabricated panel will the boilers be, will the panel be shipped in one piece, two or more. This helps us as we start to physically lay out the system on a work bench. At this time we have hand drawn boiler panel layout with the basic information. Pipe size, hardware etc. Now we can build the system. Most systems we can build in a few days. Some of the simple panels can be built in a day or less.
After the panel has been built and polished, we start the wiring and controls. This can sometimes range from a couple hours to a week or more, depending on the size and complexity of the system. After all the wiring is done and sensors are attached, we can test the panel. Testing is always done with two or more people present. This helps to ensure that the entire checklist is done correctly. If the tests all check out, the panel is dressed with any loose accessories, labeled and serial numbered and is ready for shipping. For more info on Triple H Hydronics, www.triplehhydronics.com.