Property owners and facility managers can realize significant energy savings and improved comfort in a facility or building by upgrading a 20 to 30 year-old boiler with a new, more efficient unit. A more efficient new cast iron or high efficiency condensing boiler uses less fuel, and provides more comfort for the building occupants while Read more
Save energy costs by upgrading to higher efficiency commercial boiler
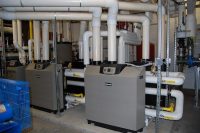
Property owners and facility managers can realize significant energy savings and improved comfort in a facility or building by upgrading a 20 to 30 year-old boiler with a new, more efficient unit. A more efficient new cast iron or high efficiency condensing boiler uses less fuel, and provides more comfort for the building occupants while building owners benefit from years of trouble-free operation.

Breaking Down Commercial Boiler Efficiency Levels
Boilers are generally considered “commercial type” for having heating input between 300,000 Btu and 12,500,000 Btu. To be sold in the U.S., these boilers must meet the newest energy efficiency standards, effective since March 2, 2012, as defined by the Department of Energy (DOE) and specified in the Code of Federal Regulations, 10 CFR431.87:
Condensing boilers have efficiencies typically above 90% and thus greatly exceed the current DOE minimum prescribed efficiency levels.
Why should business owners and facility managers consider buying a more efficient boiler? For one, replacing a 65% efficient cast iron boiler with a new one that has 84% thermal efficiency or higher will result in significant fuel savings. Space heating combined with water heating accounts for 20.3% of the total energy bill making it the largest energy consuming systems in a commercial building.

Source: U.S. Department of Energy (DOE) Buildings Energy Data Book – table 3.1.4 2010 Commercial Energy End-Use Splits, by Fuel Type (Quadrillion Btu)
Property owners with high efficiency boiler systems often report energy cost savings of 25% and higher on their heating bills. Additionally, modern boilers are typically quieter in operation, more technologically advanced and simply better at heating the building. They also offer improved heating controls that can make rooms and offices more comfortable.
Choosing the Right Boiler
When choosing the right boiler, the specifying engineer has to answer the following questions:
1. Is it a new installation or replacement?
– The answer to this question will greatly influence most of the other variables such as the boiler size, type of fuel to be used, type of heating system (water or steam), required minimum floor space, access space (clearance) for maintenance and weight limitations. If the project is a retrofit, the building owner may ask the consulting engineer to determine if it will make sense to change the system from steam to water.
– In installations limited to heating, hot water boilers will be more efficient than steam simply because of their lower combustion temperatures, resulting in less energy consumption. Process installations, on the other hand, often require steam for high temperature applications such as sterilization in hospitals. Dehumidification would be another example where steam boilers would make more sense than water. Finally, existing steam systems are much easier to retrofit using one-for-one boiler replacements due to simplicity and lower overall project cost. At times, customers are sold on the idea of retrofitting steam systems to water systems. This is recommended in situations where the building operating engineer or servicing crew is not very experienced in steam applications and maintenance of these systems. Because of this issue, there are a large number of steam systems that are either underperforming or having frequent breakdowns. It should be noted, however, that the cost of converting a steam system to a water system can be quite high and may result in a long payback.
– Another important question for retrofit applications is: how difficult is the access to the mechanical room? Some condensing boilers offer narrow design (less than 33 inches wide), low height and can be split into two separate sections for easier navigation around tight corners and access to small elevators. Splitting the boiler will also reduce the overall weight, making it easier to move in areas with weight limits such as elevators. New constructions, on the other hand, have typically greater flexibility when it comes to choosing the boiler.
2. What type of fuel is going to be used (natural gas, propane or oil)?
– Natural gas is typically less expensive than propane or oil but it may not be readily available, especially when it comes to rural or remote areas. Oil prices have recently come down and this type of fuel is becoming more attractive and alternative solution to propane.
– Does the building owner need a back-up fuel? Alternative fuels such as propane or oil could provide heat when there is no natural gas available. In cases like this, dual fuel burners (gas and oil) offer alternative solutions. Most high efficiency boilers can be easily converted from natural gas to propane.
3. Is the initial installation cost and longevity of the boiler more important than the overall operating cost or efficiency?
– The cast iron (standard efficiency) boilers typically offer lower installation costs, a longer product lifecycle and require less maintenance than condensing boilers. The condensing (high efficiency) boilers tend to be more expensive but have more sophisticated controls and, under the right operating conditions, can offer higher return on investment. The amount of savings will vary and depend on the application (high temperature vs. low temperature systems), seasonal run hours, utility rates, part load conditions and boiler efficiency.
In high temperature systems (fan coil, finned tube baseboard, cast iron baseboard), there will be fewer opportunities for the boiler to condense. Savings, as a result, will be much lower than when the boiler is used in low temperature applications, such as under-the-floor radiant tubing. Cast iron boilers simply thrive in higher temperature systems, like those that utilize radiator and baseboard emitters. A condensing unit operating mostly in high temperature applications may still be more efficient than a cast iron boiler with the same heating output, but its efficiency won’t be fully maximized. The same condensing boiler operating in lower operating temperatures (part load applications, seasonal shoulders, multiple boiler oversized systems) will be much more efficient.
It should be noted that the newest models of non-condensing cast iron boilers today are far more efficient than the boilers made 20 years ago. To illustrate, the Weil-McLain 88™ Series 2 Commercial Gas Boiler line offers up to 87.5% combustion efficiency and is ideal for commercial applications that require energy efficiency and longevity. It can use different types of burners carefully matched for quieter ignition, longer life and improved combustion. These boilers have easily accessible controls, vertical flue ways, large combustion chambers and cleanout ports for easy and quick servicing.
Climate also plays a major role in boiler selection. Investing in the highest-efficiency heating system makes the most sense if the facility is located in a cold weather region with many run hours. In climates that are milder with lower annual heating costs, the extra investment required to go from 85% to 90 or 95% may be more difficult to justify.
Additionally, many local utilities offer rebates for boiler replacement. In some cases, the local efficiency rebate can offset 50% or more of the boiler price. Some quick research could help you take advantage of any available rebates in your area. Then, bring in a heating contractor to size the unit so that it’s most efficient for the space. This will ensure that the boiler operates at its optimum capacity and is most cost effective.
Know When It’s Time to Replace
It is not uncommon for property owners or managers to wait until a boiler completely breaks down and are suddenly faced with no heat. To make things worse, these types of failures happen when there is real need for heat (for instance, a very cold day) and since the failure is unexpected, there are rarely emergency funds allocated to fix the problem.
The following are some warning signs that it’s time to replace an old unit:
• Age: Condensing boilers haven’t been on the market for a long time and therefore it is hard to predict their longevity. With proper maintenance, they are expected to last at least 15 years or longer. Weil-McLain boilers come with a ten year non-prorated heat exchanger warranty and two year parts warranty. Cast iron boilers, on the other hand, should be considered for replacement if they have been operating for more than 20 or 30 years. Some of these boilers can last even up to 50 years or longer, but even with decent annual maintenance, their efficiencies are much lower than today’s cast iron boilers. Often times, the energy savings from a new boiler replacement alone practically pays for the cost itself within a year or two.
• Energy Expenditures: Be mindful of any increases in energy expenses. If energy bills are slowly rising it may be due not only to the age of the boiler but also due to increasing costs of the boiler maintenance. If a boiler requires constant servicing, the system has likely become less efficient. One should consider upgrading to a more reliable, durable unit such as a cast iron unit. Additionally, a noisy unit may also be a sign that it’s time for an upgrade.
• Increased frequency of failures: This is a clear indicator that the boiler is due for either a major overhaul or replacement.
• Leaks: A boiler that leaks or requires additional make-up water could be nearing the end of its lifecycle. By replacing the existing unit, the building manager or owner can avoid costly floods and critical boiler or property damage.
• Comfort: If you notice that some rooms in a building are too hot or too cold or have varying temperatures throughout the day, it’s possible that the unit and its controls are no longer effective or the facility may benefit from more efficient controls.
Conclusion
Even if a boiler isn’t immediately failing, upgrading to a new system can offer significant benefits. By planning the change, rather than facing an emergency in the throes of winter, building owners and managers can realize energy savings, a more comfortable facility, tenant retention, improved heating reliability and increased property value.
There are some great resources available online for facility managers and building owners to evaluate their return on investment (ROI) when purchasing a boiler. One of the most popular boiler ROI tools is Weil-McLain’s SlimFit ROI Calculator, available on the SlimFit website: http://slimfitboiler.com/roi-calculator/
John Kopf is Senior Product Manager with Weil-McLain, a leading North American designer and manufacturer of hydronic comfort heating systems for residential, commercial and institutional buildings. Founded in 1881, Weil-McLain is based in the Chicago suburb of Burr Ridge, Ill., with manufacturing facilities in Michigan City, IN. and Eden, N.C., and regional sales offices throughout the United States.