Classes to be held in Colorado and New Hampshire Viega, LLC has announced its Fall 2019 lineup of courses at its seminar centers in Broomfield, Colo., and Nashua, N.H. The offerings include topics from radiant design and LoopCAD software to press technology. With two fully equipped state-of-the-art seminar centers, Viega is an industry leader in Read more
Viega
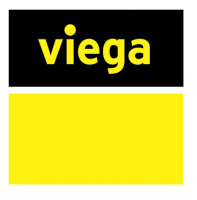
Classes to be held in Colorado and New Hampshire
Viega, LLC has announced its Fall 2019 lineup of courses at its seminar centers in Broomfield, Colo., and Nashua, N.H.
The offerings include topics from radiant design and LoopCAD software to press technology. With two fully equipped state-of-the-art seminar centers, Viega is an industry leader in supporting the trades and helping contractors become more versatile, skilled and efficient. To date, more than 40,000 people, from self-employed contractors to employees of large firms, have taken courses at the centers.
The classes are taught by experts with years of experience in the field and offer ample hands-on experience. Attendees leave with skills and knowledge that will show immediate benefits on the job.
Training seminars are listed below:
Radiant Design, Piping and Controls
Oct. 1-3, Nashua, N.H.
Dec. 4-6, Broomfield, Colo.
Covers design theory and practice, piping arrangements and control strategies. Includes hybrid systems, multiple temperature piping arrangements and system component placement.
LoopCAD
Oct. 29-30, Nashua, N.H.
Sept. 23-24 and Nov. 11-12, Broomfield, Colo.
How to use LoopCAD software for radiant design and layouts. Covers heat loss, drawing layout, material selection and snow melt.
Commercial Piping Solutions
Oct. 8-9 and Dec. 3-4, Nashua, N.H.
Oct. 2-3, Broomfield, Colo.
Covers Viega systems and products and their appropriate uses. Includes PureFlow, ProPress and MegaPress; hybrid systems; installation techniques; project savings; hands-on installation and competitive information.
Hydronics 101 & Radiant Systems
Oct. 22-23, Broomfield, Colo.
Provides a basic understanding of how hydronic systems work. Topics include methods of heat transfer, piping materials and components, control strategies and installation methods.
Carbon Steel Press Technology
Oct. 15, Nashua, N.H.
Covers the use of carbon steel press systems for residential, commercial and industrial piping applications.
Stainless Steel Press Technology
Nov. 14, Nashua, N.H.
Covers the use of stainless steel press systems for commercial and industrial plumbing, heating and piping applications. Properties and chemical compatibility of 304 and 316 stainless steel will be covered.
For more information and to register, click here.
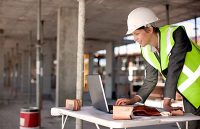
The cost of consumables can seem minor when calculating a job. Compared to the costs of labor, tools, material and transportation, the expenditure for consumables can seem unavoidable and of relatively minor importance. But when using traditional methods of joining pipe, such as welding, soldering and threading, consumables are a constant cost and one that Read more
The cost of consumables can seem minor when calculating a job.
Compared to the costs of labor, tools, material and transportation, the expenditure for consumables can seem unavoidable and of relatively minor importance.
But when using traditional methods of joining pipe, such as welding, soldering and threading, consumables are a constant cost and one that can easily cut into profit margins.
This sample bill of materials explains it well:
Say a job requires a contractor to make 1,500 x ½” pipe connections and, based on material and application, he chooses to use threading to join the pipe.
Consumables for the job are a cutting die, cutting oil, Teflon tape and pipe thread compound. Let’s look at the quantities involved:
- The ½” cutting die has a 1,500-cut life span.
- For those 1,500 cuts, two gallons of cutting oil are used.
- Three wraps of Teflon pipe are used on each pipe joint.
- One pint of pipe thread compound lasts five times as long as the Teflon rolls.
At face value, here are the price points associated with each of these consumables:
- Die: $123.48
- Cutting oil: $33.27
- Teflon tape: $15.78
- Pipe thread compound: $10.32
When you spread these numbers across 1,500 connections, you end up with a total cost of $0.318 per joint.
If you think about this from a long-term perspective, it’s easy to see where the dent in your budget forms. Perform the same job above 50 times over and the consumable bill reaches nearly $24,000.
Now, consider a scenario where you need a 2″ pipe joint to perform the above job. In this case, you have a total cost of $0.749 per joint. Perform this same job 50 times and your consumable bill stretches to more than $56,000.
(While on the topic of costs, it’s also worth mentioning that a threading machine alone will run you about $7,000.)
While the above example uses threading, other traditional pipe-joining techniques like soldering and welding introduce the same concerns over consumable costs. Whether you need spools of solder, flux and fuel or welding sticks, grinding discs and a galvanizing spray, you’ll have payments that never cease and are bound to add up.
The best way to eliminate consumable costs is to use press tool technology. While the greatest efficiencies with press technology comes with reduced labor costs, the savings on consumables will add up, job after job, year after year.
In addition, there’s no need for open flame and you’ll have the ability to install in any weather conditions, so you’ll avoid the cost of fire watches and hot work permits, as well as potential costly delays in project schedules due to environmental conditions.
Will Dutcher, Associate Product Manager – Industrial, has been with Viega LLC for three years, beginning as a product engineer. He holds a bachelor’s degree in mechanical engineering from The State University of New York at Buffalo (UB) and has engineering experience in a variety of industries, including pharmaceutical, high-end jewelry and consumer plastics.
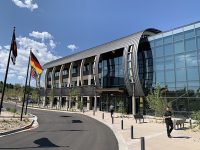
Recently, the Mechanical Hub team took part in a two-phase, two-state trip to visit Viega’s North American manufacturing in McPherson, Kansas, and toured the brand new HQ and Seminar Center in Broomfield, Colo. Impressive is the first thing that comes to mind when describing both facilities. The McPherson manufacturing facility exudes the company’s philosophy of Read more
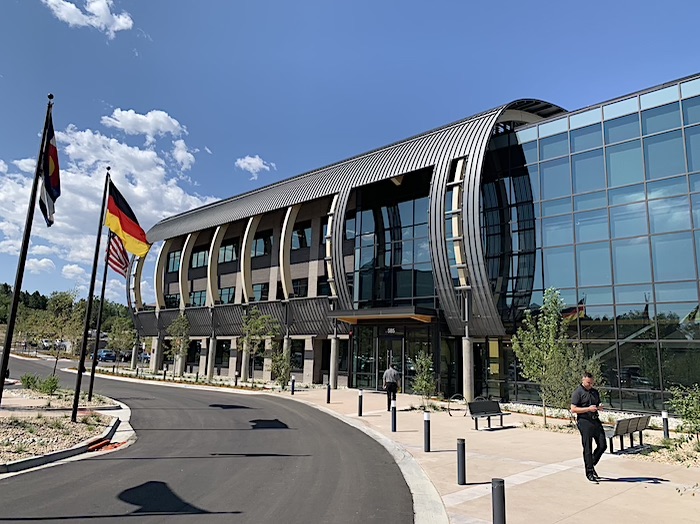
The new Viega North American headquarters in Broomfield, Colo., was designed to look like a fitting.
Recently, the Mechanical Hub team took part in a two-phase, two-state trip to visit Viega’s North American manufacturing in McPherson, Kansas, and toured the brand new HQ and Seminar Center in Broomfield, Colo. Impressive is the first thing that comes to mind when describing both facilities.
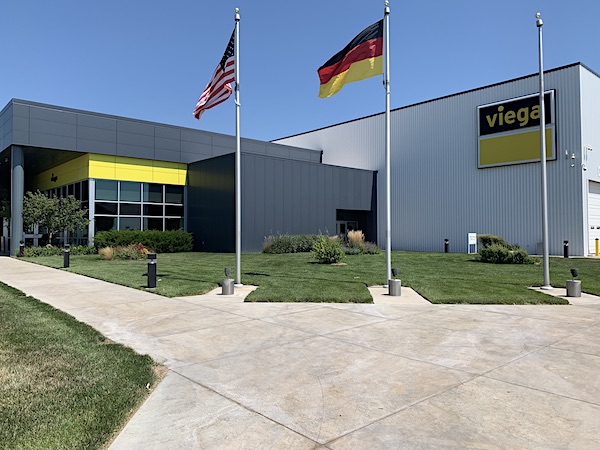
One of the Viega manufacturing facilities in McPherson, Kansas.
The McPherson manufacturing facility exudes the company’s philosophy of both progress and vision for the future. “We are constantly looking past the immediate future and into the distant future,” Eric Wicker, director, manufacturing, Viega.
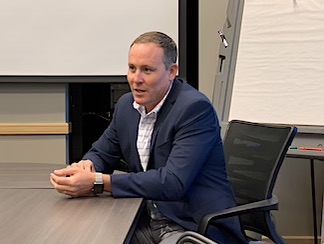
Eric Wicker, director, manufacturing, Viega
This summer, Viega completed a two-year building program in McPherson that included: a 90,000-sq. ft. expansion of a manufacturing plant, completed in Dec. 2017; a new 205,000-sq.-ft. manufacturing plant, completed in June; and a new 25,000-sq.-ft. tool shop and apprentice building, completed in July. And, the company is currently building a 55,000-sq.-ft. logistics expansion—a high-bay storage and retrieval area for inventory.
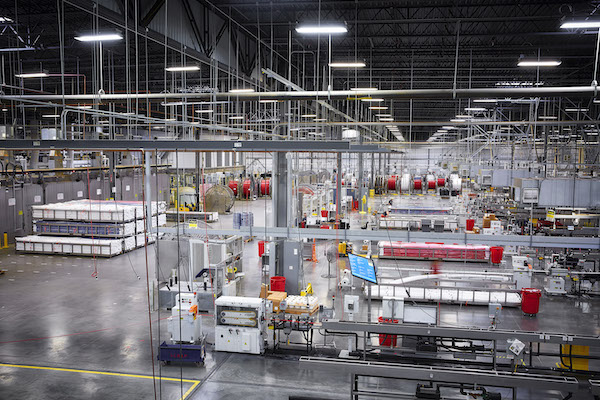
The manufacturing floor at the McPherson facility is as meticulous as it gets.
Mimicking some of the processes from its global HQ in Germany, robotics and machining take center stage throughout the meticulous McPherson plant. Fear not, all of this new-fangled technology is not taking jobs away, rather increasing them. Currently at approximately 300 employees, the company hopes to hit the 500 mark by years ’23-’24.
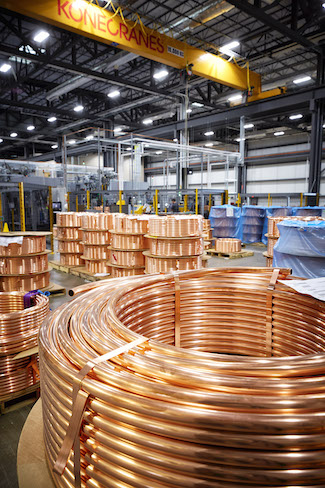
Some of the copper inventory, now produced in the states.
McPherson is where Viega produces its PureFlow line of PEX product, as well as select fittings from the ProPress Copper and 80,000 sq. ft. dedicated to its MegaPress product lines. McPherson is also home to Viega’s master distribution center for North America.
Continued expansion is a testament to the company’s progressive philosophy. For instance, the company has dedicated 270,000 sq. ft. to the copper fitting production. “The goal is to be producing the majority of copper fittings sold in the U.S. right here in the states,” says Wicker.
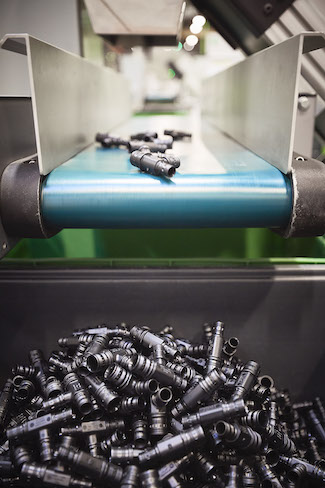
Plastic fittings rolling off the line. Seven million per month made in Kansas.
The state-of-the-art distribution center incorporates the latest technology and automation, as well as an upgraded warehouse management system that provides faster product turnaround. With additional metals products being manufactured in McPherson, a larger distribution center for both metals and PEX products was necessary.
Although media wasn’t allowed to shoot photography inside the plants—understandably—the tour started in the 36,000-sq.-ft. Plastic Injection Molding area which exemplified the company’s high investment in tooling. Twenty machines produce approximately seven million fittings per month. This particular building was well lit and comfortable, due, in part, by the implementation of its own radiant heating and cooling technology.
Quality is never understated at Viega; we strolled through the Quality Assurance Lab where dedicated staff monitor product and equipment through a series of rigorous testing.
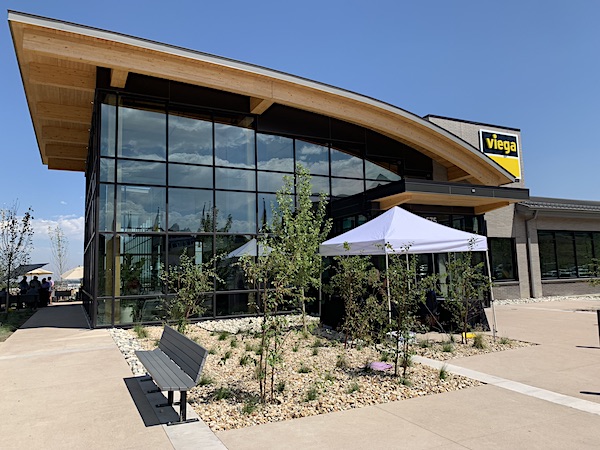
The Broomfield Seminar Center
Next, we toured the 200,000-sq.-ft. Extrusion Area where the plastic piping is made. Once made and exported from Georgia, Viega now produces its own resin—which is transformed into pellets—onsite. The rejected pellets are not repurposed, yet recycled and sold.
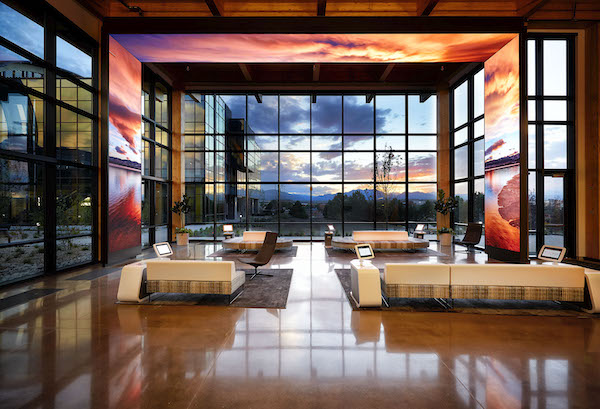
Whoa! Check out the beautiful seminar center, and the frickin’ view!
There is a Special Extrusion Area where plastic metal plastic tubing extrusion is performed. The only company in America making this, the plastic piping is integrated with aluminum so it can better hold its shape rather than returning back to its original form. (Nearby is a 40,000-sq.-ft. dedicated machine shop.)
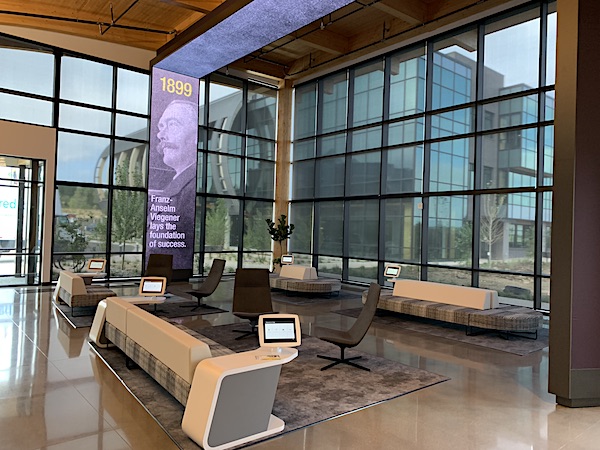
Another angle of the entrance to the seminar center with the HQ in the background.
We then toured the 270,000 sq. ft. of ProPress copper fittings production area and 80,000 sq. ft. of the MegaPress/Metals production area. Strategically, it makes sense for Viega to start producing here in the states. With press technology introduced here in 1999, education and awareness of the process and technology have helped contractors nationwide run a more efficient business. Viega system solutions are designed to work together in plumbing, heating, cooling and pipe joining applications, making the contractor’s work fast, easy and safe.
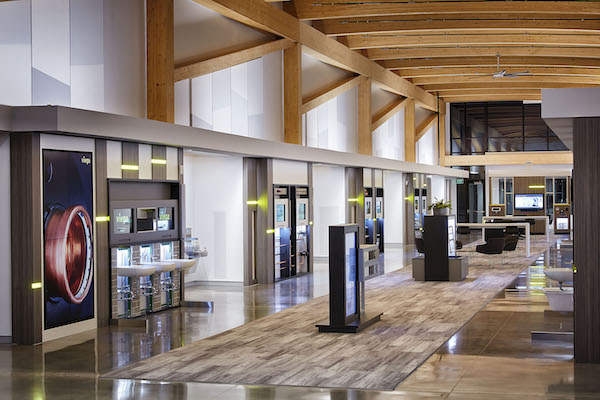
The seminar center features an interactive display area chock full of Viega products.
The following day we were flown to Denver to tour the recently opened Viega North American headquarters and Seminar Center in Broomfield, Colo. The 55,000-sq.-ft. headquarters resembles a pipe fitting, and its interior is the real testament to Viega innovation. I can’t express enough how beautiful these two buildings are, and, of course, amid the breathtaking backdrop of the Rocky Mountains. The HQ building opened in January and the first official training took place April 8, and weekly training is booking fast. “Viega is absolutely committed to its customers and their success in the field,” says Bo DeAngelo, manager, technical training at the center.
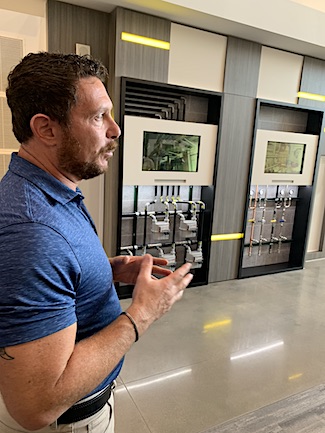
Like a proud new papa, Bo DeAngelo gives the tour of the new seminar center.
Yet, I am always interested: when a new facility is built, does it incorporate its own products? While the cross-laminated timber beams are imported from Austria, the exposed ceilings give employees and visitors a clear view of the many uses of Viega’s innovative technology.
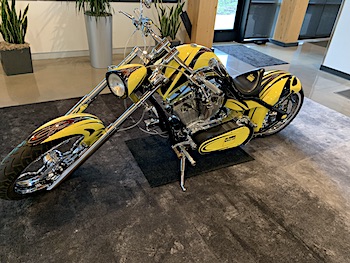
We’ve located the custom Viega chopper! It was taken in the middle of the night from the McPherson facility and relocated to Broomfield where it sits proudly on display. Who has the keys?
Potable water is carried through copper pipes connected with ProPress fittings. The carbon steel fire sprinkler system is joined with MegaPress fittings. Radiant heating and cooling keeps the building comfortable, while a snowmelt system keeps the courtyard free of ice and snow. Manifolds ensure the systems operate smoothly and efficiently. The restrooms feature wall-hung bowls and no exposed tanks, thanks to in-wall carrier systems and Visign style flush plates.
The new 23,000-sq.-ft. Broomfield Seminar Center next door supplements Viega’s Nashua, New Hampshire Seminar Center, which has trained thousands of people since opening in 2006. The new center is an innovative training experience and is equipped with four classrooms, two hands-on labs, and interactive displays throughout, which allows attendees to see, touch and experience Viega products. “Demand for training has been increasing steadily. This facility will allow us to continue to provide and expand on the training that our industry deserves,” says CEO Dave Garlow.
Viega experts lead single- and multi-day classes in everything from radiant system design and fire protection to hydronics and pathogen prevention. Despite being open only since April, it is on track to host more than 2,100 students this year, says DeAngelo.
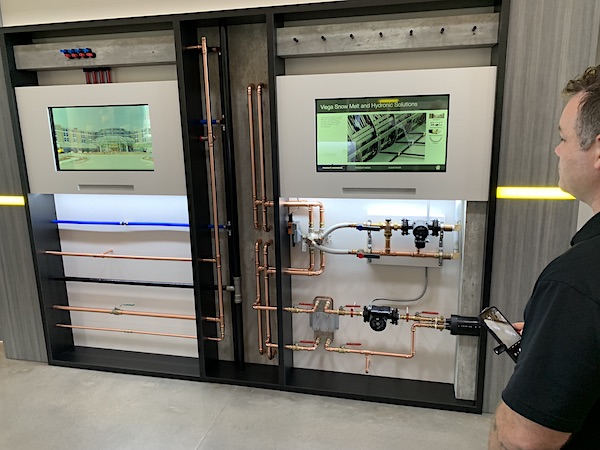
The Hub’s Eric Aune checks out the hydronics and snowmelt display.
I walked away very impressed, telling DeAngelo I—and I’m sure the clients that visit—can’t help but feel energized the minute I walk in this facility. Shaking his head in agreement, “That’s what Dave Garlow tells me every day he walks in here,” responded DeAngelo.
Make no mistake, there is a lot of money, time and resources invested in Viega North America. But it’s a huge testament to the dedication the company believes is its biggest investment: its customers and its employees.
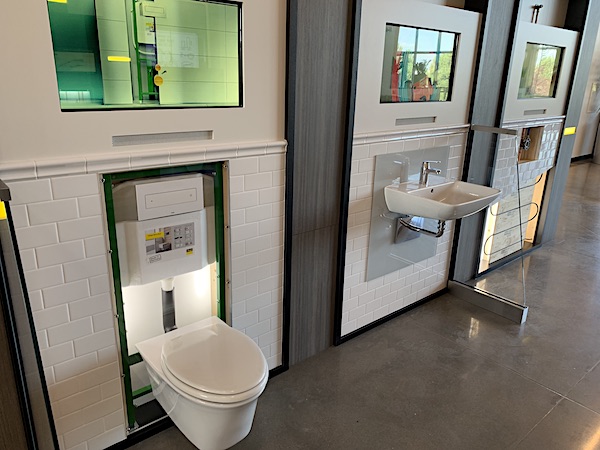
The interactive display at the Broomfield Seminar Center features a breadth of innovative Viega products.
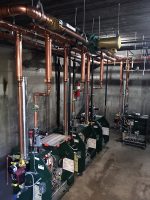
When meeting a crucial deadline, many contractors know that using Viega products will get the job done well and without worries of missing a deadline. It’s why Moe Saavedra, General Manager of Devix Heating and Cooling in West Allis, Wisconsin, called on Viega ProPress and MegaPress fittings for a boiler repiping project. In September, when Read more
When meeting a crucial deadline, many contractors know that using Viega products will get the job done well and without worries of missing a deadline.
It’s why Moe Saavedra, General Manager of Devix Heating and Cooling in West Allis, Wisconsin, called on Viega ProPress and MegaPress fittings for a boiler repiping project. In September, when a 60-year-old large boiler at the Contessa Apartments in Milwaukee, Wisconsin, quit working, a fix was needed – and fast.
“It was all natural gas, and it was an oversized unit, so we converted the one very large boiler into a staged multi-boiler system,” explained Saavedra. “They work in stages, depending on the outdoor ambient temperature.”
Saavedra said there was a 2 ½” carbon steel water main coming in from the building, but everything else was 2” copper tubing, so his crew used Viega transition fittings to connect 2 ½” carbon steel into 2” copper. Their vendor, Ferguson, helped gather all the parts needed quickly so they could get the work done.
“Viega made this job happen quickly, because typically we’d cut back and use a threaded fitting, but in this situation it was all welded pipe, so MegaPress was the best repair option for this. We’ve used Viega ProPress for about three years, but this was our first time to try MegaPress,” Saavedra said.
Devix Heating and Cooling uses ProPress for nearly all its water heater and boiler repairs and installations. Saavedra said the fittings are a big benefit to the company.
“A job that might take us six days can take us just two or three (with ProPress), which means that it cuts our labor in half. And that means we can pump out twice as much work! It’s a huge win,” he said.
Saavedra admitted that after being introduced to Viega initially, he still wasn’t exactly sure what to expect from the products, but after putting Viega press fittings to work on a job, he became a believer.
“Everyone loved it. The job was done super quick. It was just phenomenal,” he said.
One of Devix’s customers is a building management company in Milwaukee that owns 40 to 50 buildings. The company regularly calls on Devix to do maintenance, repairs and replacement work, such as the Contessa Apartments. Before switching to Viega, Saavedra said they did things “the old school way” via solder and flux. Their clients are seeing the return on investment they’re getting by way of Devix using Viega.
“They love that we can replace a boiler in a day. We’re not a big company, but is allows us to cut and press and we’re done,” he said. “The only reason we can pump out these things so fast is because of Viega.”
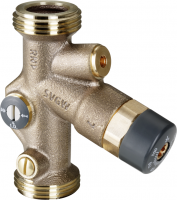
Viega LLC’s new Automatic Recirculation Balancing Valve ensures a balanced domestic water recirculation system by dynamically changing with varying conditions. The Automatic Recirculation Balancing Valve is a modification of a Viega product that has been used successfully in Europe for years. It helps keep water temperatures more uniform by adjusting flow with changes in temperature Read more
Viega LLC’s new Automatic Recirculation Balancing Valve ensures a balanced domestic water recirculation system by dynamically changing with varying conditions.
The Automatic Recirculation Balancing Valve is a modification of a Viega product that has been used successfully in Europe for years. It helps keep water temperatures more uniform by adjusting flow with changes in temperature. The results are faster hot water delivery, minimized waste energy and water and less stagnation and chance of contamination. Among the valve’s features:
- Unlike with manual valves, temperature can be set once and be maintained automatically.
- Settings can be changed easily, if needed.
- Can be installed on risers or branches
- Remote monitoring with temperature sensor
- Optional thermometer provides visual indication of valve setting
- Threaded ends allow it to be used with Viega ProPress or Viega PureFlow fittings systems
- Includes bypass for thermal disinfection
Additional accessories that can be used with the valve include a thermometer, drain valve and optional insulation sleeve.
“Viega is committed to providing hot water quickly and efficiently while improving water quality and the new Automatic Recirculation Balancing Valve is a significant step toward that goal,” said Paige Riddle, product manager, valves. “This valve offers more features than any other on the market while requiring minimum work on the part of designers, engineers, installers and building maintenance personnel.”
To learn more about Viega and its work to improve water quality, click here.