Panasonic, an industry-leading manufacturer of air conditioning, heating and indoor air quality systems, announces a new collaboration with Trumbull Campbell Associates, Inc., an independent manufacturers’ rep firm selling applied commercial heating, ventilation and air conditioning equipment and parts, to distribute Panasonic VRF equipment to its commercial customers in Eastern Massachusetts, Maine, New Hampshire and Rhode Island. As one Read more
VRF
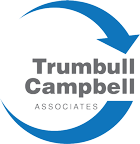
Panasonic, an industry-leading manufacturer of air conditioning, heating and indoor air quality systems, announces a new collaboration with Trumbull Campbell Associates, Inc., an independent manufacturers’ rep firm selling applied commercial heating, ventilation and air conditioning equipment and parts, to distribute Panasonic VRF equipment to its commercial customers in Eastern Massachusetts, Maine, New Hampshire and Rhode Island.
As one of New England’s most respected manufacturers’ rep firms, Trumbull Campbell provides sales, application and service support to customers across a variety of industries, including healthcare, biotech, hospitality, elderly care and higher education. Founded in 2006, Trumbull Campbell has delivered cost-effective end-to-end solutions to its customers, offering assistance with installation, design, and reliable products that address the complexity of maintaining an HVAC system.
“We are grateful for the opportunity to represent a company not only of innovation and quality, but one of integrity,” said Tom Trumbull, Co-Founder, Trumbull Campbell Associates, Inc. “The level of support we’ve received from Panasonic is a true differentiator from other manufacturers. Our foothold in the territory paired with Panasonic’s brand and reputation offer a winning combination.”
“Trumbull Campbell is able to provide exceptional support for their customers in New England seeking applied equipment solutions,” said Nathan Oliver, Eastern U.S. Sales and Business Development Manager, Panasonic Appliances Air-Conditioning North America. “We are pleased to align with a company that can provide our customers with a personalized experience, satisfying their VRF application needs from design and selection to commissioning and service.”
For more information about Panasonic heating and air conditioning, please visit na.panasonic.com/us/home-and-building-solutions/heating-air-conditioning/.
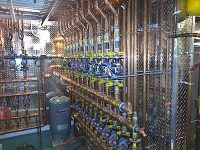
Making the case for hydronics: three advantages of water-based HVAC systems over VRF In an ongoing effort to meet the comfort, cost and energy-efficiency expectations of the commercial building industry, design engineers, building owners and mechanical contractors are constantly re-examining the technology and components of HVAC systems. Hydronic systems and variable refrigerant flow (VRF) systems Read more
Making the case for hydronics: three advantages of water-based HVAC systems over VRF
In an ongoing effort to meet the comfort, cost and energy-efficiency expectations of the commercial building industry, design engineers, building owners and mechanical contractors are constantly re-examining the technology and components of HVAC systems.
Hydronic systems and variable refrigerant flow (VRF) systems are two heating and cooling systems often compared in terms of energy consumption and system performance. Since entering the U.S. market, VRF systems have garnered interest for their space-saving ductless technology and claims of exceptional energy efficiency. However, industry studies demonstrate how hydronic systems are more energy efficient than VRF systems.
About the systems
Hydronic systems provide water-based heating and cooling through pipes and other components such as pumps, drives, controls, heat exchangers and valves that deliver heated or cooled air via an air-handling unit through ductwork and air terminals. VRF systems, on the other hand, use refrigerant as the primary heating/cooling medium and are comprised of a main compressor unit connected through refrigerant lines to multiple indoor cassette units than can be individually controlled.
Whether selecting HVAC systems for new construction or retrofits, there are three main advantages to choosing a hydronic system versus VRF.
- Lower costs
Hydronic systems are budget friendly. Upfront, maintenance and lifestyle costs are low compared to VRF systems.
When designing a hydronic system, mechanical contractors and specifying engineers can control costs based on selection of technology. With few options available, there is virtually no variation in the upfront cost of VRF systems.
Hydronic systems are also affordable to maintain. Designed with universal components, the systems can be installed and serviced by any trained HVAC service technician. What’s more, hydronic systems are upgradeable and expandable.
Conversely, VRF systems are proprietary. This restricts the ability to substitute components from different manufacturers. The proprietary nature of VRF systems also requires specialized technicians for the life of the system, from installation to adjustments to repairs, adding to the lifecycle costs.
It is important to note that hydronic systems have a longer life expectancy than VRF systems. A hydronic system has been known to last 25 to 30 years, whereas VRF systems may need to be replaced 10 to 15 years after installation.
- Versatility
Hydronic systems are easily adaptable to a wide range of energy sources from natural gas and propane to solar thermal collectors and biomass boilers. In contrast, VRF systems are solely sourced by electricity.
Additionally, hydronic systems are less affected by extreme temperature changes than VRF systems. The efficiency of a VRF system is reduced as the ambient temperature increases in the cooling mode and decreases in the heating mode. In cold climates, VRF systems may require a supplementary heat source, such as hot water from a boiler, which may negate the energy efficiency of the system.
Water-based hydronic systems like a water-sourced heat pump system can draw the heat or chill from a room and carry that energy back to the system for later use. This reduces energy consumption and costs. Although a VRF system can provide zoned comfort, recovering heat from one zone to use it in another, it does not have thermal storage capabilities.
- Safety and reliability
While it’s possible for leaks to develop in both hydronic and VRF systems, a leak in a VRF system is potentially life threatening because a VRF system usually contains a high volume of refrigerant that can asphyxiate building occupants. Refrigerant leaks also cannot be detected by sight or smell, making them difficult to locate and repair.
Hydronic systems with cooling units require refrigerant to operate, however they use 66 to 75% less refrigerant on average according to the Hydraulic Industry Alliance. Refrigerant circuits in a hydronic system are factory-sealed, meaning the units are assembled in a controlled environment and subjected to rigorous standards and testing prior to installation. Conversely, VRF systems use both factory-sealed and field-installed circuits, which require brazing and soldering of copper piping on site. The quality of installation depends on the technician’s level of expertise. VRF technicians must be qualified to work with refrigerants under extremely high pressure and be knowledgeable about leak detection and ventilation requirements per ASHRAE Standard 15.
As the most comfortable, cost-efficient and reliable heating and cooling source available today, hydronic systems will continue to be the leading technology for commercial applications.
Kyle DelPiano is market development manager, Southeast Territory, Xylem Inc. He is an active ASHRAE member and LEED AP certified.
The information conveyed in this article are the views of the author.
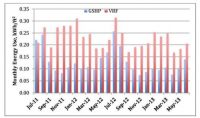
• Annual Energy Use with Geothermal Heat Pumps is 44% Less than with a Variable Refrigerant Flow System Dec. 15 – Definitive scientific research has shown that a geothermal heat pump system offers far more efficiency in a large commercial building than a variable refrigerant flow system. In January 2013, the Geothermal Exchange Organization (GEO)—with Read more
• Annual Energy Use with Geothermal Heat Pumps is 44% Less than with a Variable Refrigerant Flow System
Dec. 15 – Definitive scientific research has shown that a geothermal heat pump system offers far more efficiency in a large commercial building than a variable refrigerant flow system.
In January 2013, the Geothermal Exchange Organization (GEO)—with financial assistance from Southern Company—contracted a research team from Oklahoma State University and Oak Ridge National Laboratory to evaluate the relative performance of GHP vs. VRF heating and cooling systems installed at the American Society of Heating Refrigeration and Air-conditioning Engineers (ASHRAE) International Headquarters Building in Atlanta, GA. (ASHRAE provided data for this study, but the organization does not endorse, recommend or certify any equipment or service used at ASHRAE International Headquarters).
When ASHRAE contracted a major renovation of their two-story, 31,000-sq.-ft. building in 2008, they established a “living lab” to offer the chance to evaluate commercial building energy and sustainability performance. In addition to improvements to its envelope, floor plan and sustainability features such as lighting, the building uses three separate heating, ventilation and air-conditioning (HVAC) systems:
· A variable refrigerant flow (VRF) system for spaces on the first floor;
· A geothermal heat pump (GHP) system, primarily for spaces on the second floor; and,
· A dedicated outdoor air system (DOAS), which supplies fresh air to both floors.
The GEO research team studied the relative performance of the GHP and VRF systems, determining energy consumption of each, and heating and cooling required by the building.
“There’s no question about it – GHPs trump VRF systems for efficiency and cost savings,” said GEO President and CEO Doug Dougherty. “Our study of heating and cooling performance at the ASHRAE Building proves that over a two-year period—with all variables accounted for—energy use by the geothermal system averaged 44% less than the VRF system.”
The first-floor VRF system includes three dedicated split systems and two multi-zone inverter driven heat-recovery units. The multi-zone heat-recovery units are connected to a total of 22 fan coil units (FCUs). Cooling capacity of the heat-recovery units is 28 tons, while the three dedicated systems have an additional 10 tons of capacity. The second-floor GHP system includes 14 individual water-to-air heat pumps (two ¾-ton units, six 2-ton units and six 3-ton units) connected to a ground loop heat exchanger consisting of twelve 400-ft. deep vertical boreholes, for a total of 31.5 tons of cooling capacity.
To facilitate efficiency studies like that performed by GEO, the ASHRAE Building renovation included an array of 1,600 sensors that monitor heating, ventilation and air-conditioning operations and conditions in each building zone.
Historical and current data from these sensors were available to the GEO research team, led by Dr. Jeff Spitler, Regents Professor of Mechanical Engineering at Oklahoma State University. His colleagues Included Dr. Xiaobing Liu, Staff Scientist at Oak Ridge National Laboratory and Laura Southard, Oklahoma State Mechanical Engineering graduate student. Southern Company provided the services of a power engineer to assist with onsite data measurements.
The researchers concentrated on determining actual heating and cooling provided by the GHP and VRF systems; data analysis; and computation of measured and experimental metrics. They collected two years of operational data (July 1, 2011 – June 30, 2013) for the HVAC systems. Data points included operating mode (off/heat/cool); zone temperature; and discharge air temperature for each individual FCU or heat pump. The researchers gathered data on ground loop water supply, return temperatures and flow rates for the geothermal system.
The team also collected metered energy used by each system. For the GHP system, that included power for all 14 heat pumps, as well as the ground loop water circulation pumps. For the VRF system, power is metered and recorded only for the two heat-recovery units and the 22 FCUs connected to them. Power for the three dedicated split systems is metered through a different panel that also includes power used for computer servers and other equipment. All such differences were taken into account for comparison.
“Though the energy consumed by each system is affected by several factors—including floor space; heating and cooling loads; control strategies; and operating conditions/efficiencies—the efficiency implications of each system are clear,” said Spitler. “Raw data show that the VRF system used twice as much energy as the geothermal system during the two-year study period.”

Total monthly energy use by each HVAC system
The areas served by the GHP and VRF systems have different heating and cooling loads, so the research team estimated the loads provided by each based upon individual unit air flows. The graph below shows that when differences in floor space were normalized, energy use (kWh/sq. ft.) by the GHP system was an average 44% less than the VRF system.

Normalized monthly energy use per square foot
“During the two-year study period, the GHP system used 29% less energy in the summer and 63% less energy in the winter/shoulder seasons than the VRF system, while maintaining similar zone temperatures,” said Spitler.
“The underlying difference between the geothermal system and the air-source VRF system lays in the heat sink and source—ground vs. ambient air,” Spitler explained. “Though the control strategy for the VRF system resulted in longer runtimes compared to the geothermal system, it is clear that ground loop water supply temperatures were more favorable than ambient air temperatures for heat pump operation. This allows the geothermal equipment to operate at higher efficiencies.”
“Final Report, Performance of the HVAC Systems at the ASHRAE Headquarters Building” is available at the GEO website, here. Two peer-reviewed articles by Spitler et al. describing the project and its results were published this year in the ASHRAE Journal (September and December2014 issues). The articles can be accessed online at the ASHRAE website, here, and here. GEO will offer a free webinar about the research in early February 2015. (Editor’s Note: ASHRAE stipulates that anyone publishing links to their Journal articles include the following statement: “Use of the data published in ASHRAE Journal regarding performance of ASHRAE International Headquarters may not state nor imply that ASHRAE has endorsed, recommended, or certified any equipment or service used at ASHRAE International Headquarters.”)