Demineralizing water will prevent corrosion from occurring in a hydronic system, right?
Wrong
By demineralizing, we mean removing the ions from the water until it is purified and has zero conductivity. In theory, this sounds ideal for the system however, where there’s oxygen; there’s corrosion!
Regardless of how purified the water is, oxidation of the water will start the process of corrosion. Keeping water purified requires 0.1 PPM or less of oxygen in it, which is A. pretty much impossible, even in a closed loop system, and B. is hard to measure.
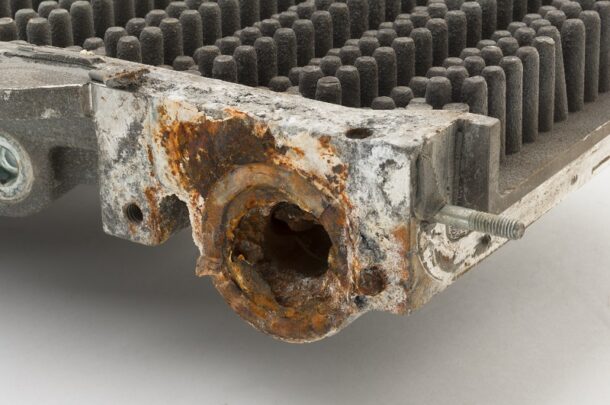
How does oxygen enter a closed loop hydronic system?
Oxygen can enter a system, old or new, in multitude of ways. Membranes, rubbers, joints, and faulty AAV’s can suck oxygen into the water. Not forgetting that most boilers now have auto-fill valves, and as soon as new water is introduced to a new system, so is oxygen.
All new components are exposed to oxygen and other contaminants during the manufacturing, transportation, and storage process. Fluxes can build up on the inside of components such as pipework during installation, and air pockets are very common when filling a new system. All of these factors lead to an introduction of oxygen in the system, and that’s when the process of corrosion begins. Remember – corrosion is a natural process that cannot be completely stopped, but it can be prevented in new systems and significantly slowed down in existing systems.
How does oxygen in a system cause corrosion, and what affect can it have on the system?
As oxygen enters a system and mixes with the dissimilar metals and the water, it oxidizes which leads to an increase in iron levels. Oxygen can also bring ions into the water, therefore increasing conductivity, causing further corrosion.
This process can also lead to magnetite build up, which is insoluble iron and is the number one cause of hydronic heating system issues such as faulty thermostats and controls, fouled EMCs, worn pump seals, heat exchanger failures, pipework pin-holes, and system blockages.
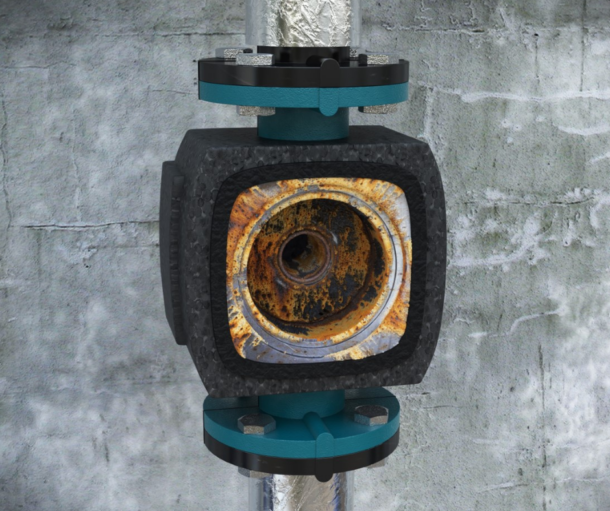
So, if purifying the water isn’t the solution, what is?
The ideal solution is to test, clean, protect and maintain the system. This controls pH, the oxygen, and the alkalinity of the water, preventing reactions and corrosion to occur.
Test
The first step to diagnosing the root cause of systems issues or preventing any damage/failures from occurring in new systems is to test the quality of the water. ADEY’s corrosion, pH, and inhibitor will identify whether corrosion has built up, or is building in the system, and provides recommendations on how to restore/treat the system water.
Will a TDS test not identify this?
Testing for TDS (total dissolved solids) tests for everything dissolved in the water which includes iron, copper, chlorides, nitrates, and sulfates. Even cleaner residues, flux residues, and the addition of inhibitor can increase TDS and conductivity, so the answer is no, testing for TDS should not be used to test for corrosion in a system. Testing for TDS should also not be used to identify water hardness. Calcium and magnesium salts cause hardness, but TDS is for all dissolved solids rather than just calcium and magnesium salts specifically, so this is not a true indication of hardness levels in a system. A specific hardness test should be used to test for hard or soft water.
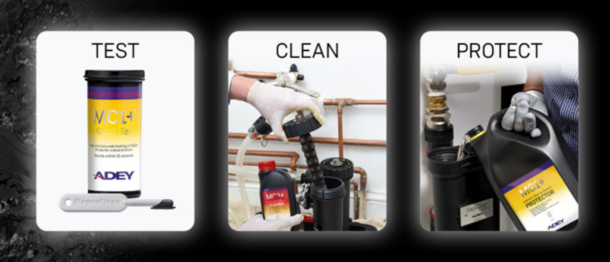
Clean
On any system, it is key to have an air eliminator. An air and dirt separator should be installed on the supply side of the system to aid air removal. On an existing system, first try bleeding any radiators, upgrade failing parts, fix any leaks, and fully cleanse the system a cleaner such as ADEY’s MC3+® cleaner. The cleaner will lift and hold any existing magnetite, scale, and sediment in suspension, ready for it to be flushed out of the system. Similar to cleaning dishes with washing up liquid, adding heat will also aid the clean, so circulating the cleaner around the system while the system is on will increase the effectiveness of the clean.
Protect
For protection, a combination of a magnetic filter such as the MagnaClean® should be installed, and inhibitor such as ADEY’s MC1+® protector should be dosed into the system. Magnetic filters should be installed on the return just before the heat exchanger or boiler to prevent any magnetite from entering this most expensive component. It is also key to choose a filter with a larger magnet directly in the flow of water to aid capture, and of course, one that is easy-to-service.
This 3-step solution is the only way to truly prevent the buildup of magnetite and the costly problems it can cause.
Join the conversation: