By Kolyn “Coach” Marshall
No matter where we go these days it seems as if there’s always someone trying to upsell us on something.
Truth is, the art of upsell is nothing new. Walk into a fast food restaurant and you’re asked if you want to super-size it. Go to the theater and you’re asked if you want to make your popcorn a combo deal. Heck, even Amazon’s in on the program.
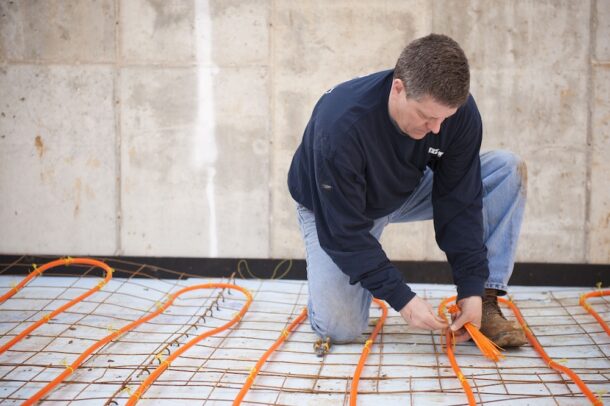
Ubiquitous upsells can be awfully annoying, especially when it’s something you know a lot about. But, what if it’s something you know nothing about? Or, better yet, didn’t know to even ask?
This last question is where I find a lot of potential radiant buyers. They simply don’t know enough about what’s out there to ask.
This is where you—Neighborhood Radiant Installer—come into play.
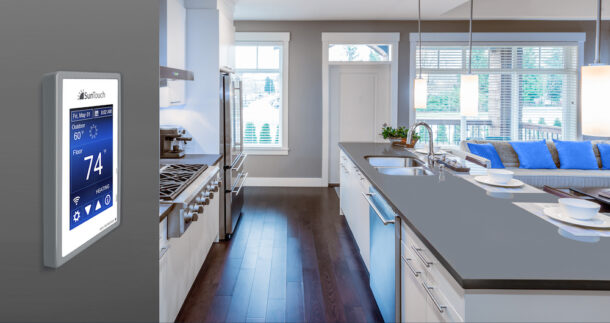
It’s your opportunity to throw out the option of radiant floor heating or snowmelting. Sounds easy, right? Well . . . sort of. In order for you to be able to effectively talk about radiant, it can be helpful to know what there is to talk about.
Understanding the want
Depending on the audience, say, home or a business owner, the want or need may vary. For homeowners, they may want to be more comfortable. There’s a factor of efficiency or cost savings, but those are typically secondary to comfort. People really don’t like being cold.
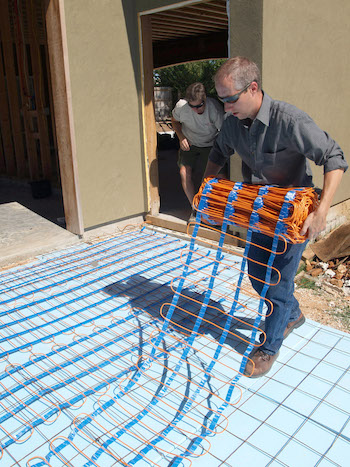
Comfort, however, takes on many forms. But, as the Neighborhood Radiant Installer, it’s important to know what comfort means. One aspect is keeping the room temperature between 68 and 70 degrees. The other facet is knowing how occupants interact with the interior space. The key driver for comfort is floor temperature.
Ever step out of the shower onto a cold tile floor? In that instant it’s pretty easy to connect to what cold is. Oddly enough, our feet dictate our comfort more than air temperature. It’s the main reason why we have slippers and wool socks. If our feet are warm we feel warmer.
So the easiest way to feeling comfortable is to keep the floors from being cold. Radiant heat does that with most radiant systems maintaining a floor temperature between 75 and 85 degrees.
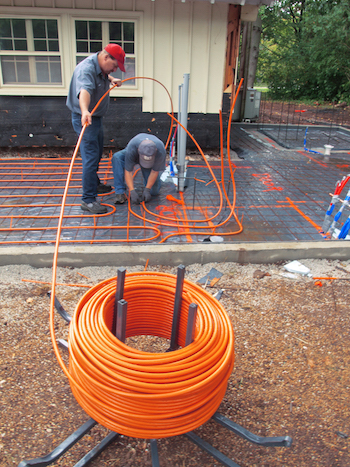
Business owners tend to have a slightly different goal in mind. Their focus is more on customer safety, especially when the weather turns cold and the freezing rain and snow start to fall. Or: employee satisfaction, a great incentive in retaining, and attracting, employees.
As for safety, injuries due to slips and falls plague business owners constantly. It’s a seasonal risk, and source of concern.
Radiant snowmelting systems help keep walkways, parking lots, and access ramps ice and snow free all winter long. This means no more early morning labor; shoveling snow is a thing of the past. No more chemical ice melt. This alone eliminates another key concern: icemelt tends to get picked up by customer’s shoes and tracked inside, eventually taking its toll on the floor.
The upgrade package
So a spark is struck. Warm floors are something that wasn’t expected but is now very much wanted.
How are these once cold floors now warmed? There are two main ways to provide radiant floor heat: hydronically with water, or through electric resistance.
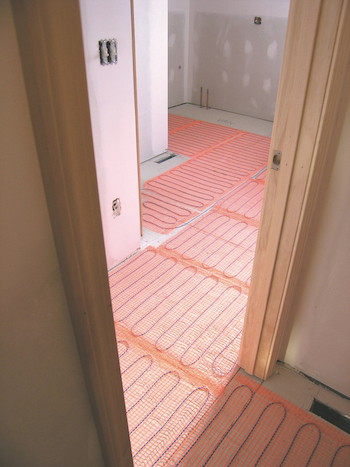
Hydronic systems rely on tubing being installed in the floor and connected to a heat source. Tubing options range from PEX, to PE-RT, to EPDM rubber. Tubing is connected to a series of manifolds, then those manifolds connect to a boiler, or other equivalent heat source.
If the area to be heated is small, say only a kitchen or bathroom, then an electric product may be best; these use electrical resistant wire or cable to generate heat. Wire is embedded in a lightweight concrete or thinset generally under tile or other masonry material. One of the advantages of electric is there is no need for a mechanical room and no need to physically run piping back through a home or facility. Electrical installations tend to be less invasive but also tend to be reserved for smaller areas.
With both electric and hydronic systems there are options for controls and thermostats. Most of today’s systems incorporate some form of connectivity feature, giving remote access to users.
Delivering the Goods
Congratulations Neighborhood Radiant Installer! The Enlightened Customer has decided to go with the radiant upgrade. Now what?
Now it’s time to figure out how to get all those tubes and wires where they’re supposed to go.
Hydronic tubing is generally installed in one of two ways, either in a concrete slab or under a frame floor. In a concrete slab, tubing is typically 6, 9, or 12 inches on center with the tubing approximately 2 inches down from the top. In a frame floor, the tubing is secured to the subfloor, often with heat transfer plates. These plates secure the tubing (usually PEX or PE-RT) to the subfloor while providing good conductive heat transfer to the floor.
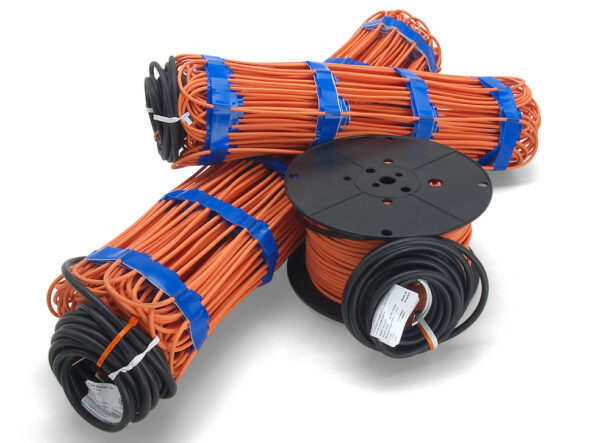
Electric systems are installed in a similar fashion to hydronic slabs with the difference being the wire is generally installed on top of the floor in ½ inch thinset with tile or other stone material as the finished floor covering. An electric system is then connected a controller or thermostat.
Both hydronic and electric systems then operate in the same way any forced air system does. The controller or thermostat is set to the desired temperature and the system operates automatically.
Satisfied Customers
So how does our Neighborhood Radiant Installer know the system is working as expected and the customer is happy? It’s simple: our Honorable Customer won’t be able to stop talking about the most comfortable heat they’ve ever experienced.
Becoming the go-to radiant expert is the best way to keep the future looking warm and bright.
Kolyn “Coach” Marshall, based in Springfield, Mo., is Systems Engineering Manager at Watts Radiant.