REGISTER HERE: https://www.eventbrite.com/e/coffee-with-caleffi-live-charting-the-course-for-lifelong-learning-tickets-771633776397 How do you keep up-to-date on industry trends? John Mesenbrink and Tim Ward of Mechanical Hub will lead a conversation as they interview BIG NAME industry leaders to uncover how they Chart the Course for Lifelong Learning. The panel features John Siegenthaler, P.E., Eric Aune and Andy Mickelson – touted as the “voices of today’s contractor” – and Bob “Hot Rod” Rohr. You’ll Learn Read more
Featured Articles
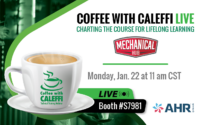
REGISTER HERE: https://www.eventbrite.com/e/coffee-with-caleffi-live-charting-the-course-for-lifelong-learning-tickets-771633776397
How do you keep up-to-date on industry trends? John Mesenbrink and Tim Ward of Mechanical Hub will lead a conversation as they interview BIG NAME industry leaders to uncover how they Chart the Course for Lifelong Learning.
The panel features John Siegenthaler, P.E., Eric Aune and Andy Mickelson – touted as the “voices of today’s contractor” – and Bob “Hot Rod” Rohr.
You’ll Learn:
- How to stay up to date on developing industry technology and trends.
- Formal, classroom training. Virtual training. Where are professionals “going” to learn?
- What is the impact of social media in lifelong learning?
Register to Win:
Register for free and join us to receive your limited edition Caleffi Gold Standard camo hat.
(Limit one per registrant, while supplies last.) Simply show your digital or printed ticket after the Coffee with Caleffi LIVE session.
All attendees of Caleffi LIVE events qualify for an opportunity to WIN one-of-a-kind custom sculpture by Bob “Hot Rod” Rohr. The drawing will take place on Wednesday, Jan. 24 at 11 am.
And, a full set of idronics technical journals signed by John Siegenthaler will be raffled during Charting the Course for Lifetime Learning event. Don’t miss out!
MCs:
John Mesenbrink and Tim Ward, Mechanical Hub
Panelists:
- John Siegenthaler, P.E., Appropriate Designs, NY
- Eric Aune, Aune Plumbing, MN & Mechanical Hub
- Andy Mickelson, Michelson Plumbing & Heating, MT
- Bob Rohr, a.k.a. “Hot Rod”, Caleffi North America, UT
Enjoy:
During Coffee with Caleffi LIVE, be sure to enjoy a specially prepared cappuccino, espresso or latte, made-to-order by our barista.
All this at Booth S7981 on Monday, Jan. 22 at 11 am CST. Register today!
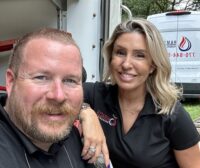
It’s that time of year again when people reflect on what they’re thankful for in the past year, and hope for a positive 2024. I cannot stress enough the job that Brent and Kathleen Ridley (@toolpros & @toolwife) do with Miracle Mechanical, a charitable organization dedicated to uplifting families in need, one at-no-cost-HVAC/plumbing repair at Read more
It’s that time of year again when people reflect on what they’re thankful for in the past year, and hope for a positive 2024. I cannot stress enough the job that Brent and Kathleen Ridley (@toolpros & @toolwife) do with Miracle Mechanical, a charitable organization dedicated to uplifting families in need, one at-no-cost-HVAC/plumbing repair at a time. “Honestly, it’s hard to put into words,” says Brent Ridley. “Seeing and feeling the gratitude from homeowners is an incredible feeling, and something that never gets old.”
Tool Pros began as tool review brand, as the brand grew and relationships with tool manufacturers were made, Ridley felt a need to use his platform for more. “Free tools and trips are great but I thought to myself. ‘let’s actually do something that matters.’”
Combined with his platform and what he knew best—HVAC /plumbing—Miracle Mechanical was born. Shortly after the concept, Ridley reached out to his contacts at RIDGID to gauge interest. “Thankfully they loved the idea and wanted to sponsor the very first project. Two months later we completed our first project, and the rest is history,” says Ridley.
Officially, the primary facilitators of Miracle Mechanical consist of Brent and his wife Kathleen. They also bring in a production crew of three to four people, and their team of HVAC / plumbing contractors—usually a 4-man crew—for a project day.
Ridley says that the goal is always to complete as many projects as possible; however, they are averaging four to five projects per year. In fact, Miracle Mechanical just completed a project this past October with Sharkbite.
And they have partnered with RIDGID for the next project taking place in early 2024. In the past, Miracle has teamed up with the AHR Expo but nothing for 2024. “We look forward to partnering with AHR for their work force development program in the future,” says Ridley.
But between working as an HVAC contractor, content creator, Miracle Mechanical facilitator, podcaster and Lowe’s Santa, finding time to take a deep breath can be difficult. “Sure, it can feel overwhelming at times,” says Ridley. “Thankfully, I have my wife who is a full-time manager and coordinator for the Tool Pros brand and Miracle Mechanical. Her dedication to the brand allows me to focus on my HVAC/plumbing business (H & M Services, Inc.), as well as other creative outlets—without dropping any balls in the process.”
The Miracle Mechanical concept is such a good one, and one that I know Ridley hopes he can provide nationally. At this time, logistics and funding for national projects have been a huge obstacle, but one that I’m confident we’ll overcome in the next couple of years,” says Ridley.
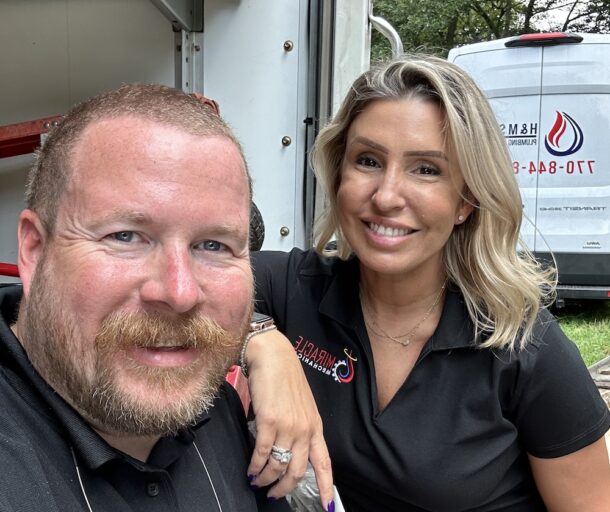
More About Brent Ridley
Ridley started into the trades right out high school in 2004. His girlfriend’s father, at the time, owned an HVAC business, and he started the summer after senior year doing commercial duct work and hated it. It was only until he found service and repair that he fell in love with the HVAC industry. “From there, I have always strived to make it more than just a ‘Job,’ but a lifestyle. If you want to get ahead in life, you can’t clock out at 5 pm.”
In the earier days before social media, Ridley wrote long-form, trade-specific tool reviews on a site called HVACTalk.com, which no longer exists. In 2017, Ridley started his successful Tool Pros Podcast. “Not long after, the social media portion of the brand quickly outgrew the podcast, leading to many opportunities that I am very grateful for, like Miracle Mechanical,” says Ridley.
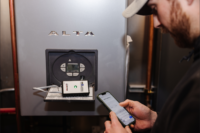
Anyone with a military background will recall the U.S. Government’s penchant for acronyms. MREs, BDUs, MRAPs, the list goes on. Unfortunately, this dynamic is also present when discussing the efficiency enhancing feature known as outdoor reset. ODT, SWT, LWT, etc. It’s enough to cause a BM in your BVDs! Well, U.S. Boiler Company has once Read more
Anyone with a military background will recall the U.S. Government’s penchant for acronyms. MREs, BDUs, MRAPs, the list goes on. Unfortunately, this dynamic is also present when discussing the efficiency enhancing feature known as outdoor reset. ODT, SWT, LWT, etc. It’s enough to cause a BM in your BVDs! Well, U.S. Boiler Company has once again developed a solution to make all this NBD.
First a few simple facts.
1. Flue gas will condense when temps are at or around 130° or less.
2. When vapor contained in flue gas condenses it releases a significant amount of heat.
3. Without question, optimal efficiency is achieved by heating a home using the lowest possible water temperature that will maintain the desired indoor target temperature, usually the thermostat set-point.
4. Using a Mod-Con, or high efficiency, gas boiler like the ALTA can take full advantage of the condensing action allowed by low water/flue temps.
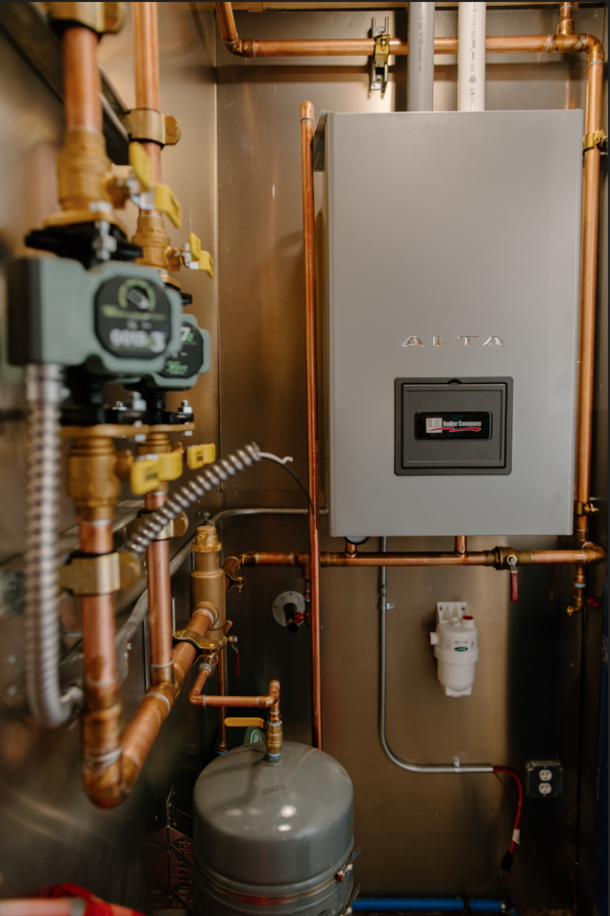
Outdoor reset sensors do a wonderful thing. They enhance efficiency by matching water temperature to varying conditions. For example, one would want to maintain indoor design temp, normally 70°, during outdoor design temps (in CT normally 7-10 degrees.) Assume a 7° ODDT, and required SWT of 180. This means the boiler must deliver 180° supply water consistently at a 7° outdoor design temperature to maintain the desired indoor temp (IDT). This all simply means we need the hottest water when it’s coldest outside. Good so far?
As Paul Harvey used to say, “And now-The rest of the Story!” We now all understand (hopefully) what happens in our heating systems on the coldest day of the year. What about the rest of the time? Sure, that 180° water will heat the house just fine on a 50 degree day. But what about all the energy used to unnecessarily heat the water way past what would be required to keep the home comfortable? This is a net negative on many fronts, but most significant is the increased wear and tear on the heating unit.
So, your now asking “Tom, how low can my water temp be?” The answer will likely surprise you. Standard fin tube radiation works ok down to 130° water temps in most applications. Same with cast iron radiators. For the fin tube baseboard system in my house the minimum boiler water temp on my ALTAC-136 is 125 degrees. Hydro-air (hydronic coils added to or contained within hot air furnaces or air handlers) can often be run around 130° as well, depending on the occupant’s expectations. Remember, these SWT’s are typically targeted when the ODT is ~70°. We don’t need to transfer much heat to maintain indoor setpoints at these conditions. How does all this magic happen? Outdoor reset. Using a thermistor mounted outside, typically out of the sun on the north facing wall we monitor ODT and adjust SWT temp accordingly. So my personal curve used to be 180° SWT @ 7° ODT, and 125°SWT@70° ODT, but no more. My ALTA figures this out automatically without an outdoor reset sensor.
While outdoor reset simply monitors outdoor temperatures, rate-based reset works by looking at boiler run time, firing rate, and other parameters and adjusting accordingly. Here’s a few examples. Say it’s a beautiful spring day. Nice and sunny with a gentle breeze and 50° outdoor temperatures. The boiler run times are likely short, and the firing rate is likely low. The boiler knows from these conditions the heat loss from the house is minimal, and adjusts, incrementally dropping the boiler water temp until the minimum setpoint is reached, or our algorithm (the “secret sauce”) calculates that based on run time and firing rate the water temp will deliver enough heat to match the rate of heat loss and maintain indoor temp setpoints at the lowest possible SWT. As night rolls in and the temperature drops, average run times and firing rates increase, and once again, rate-based reset will adjust (increase) SWT’s to maintain indoor comfort and optimal efficiency. “Brilliant!” you say. I agree. But wait-there’s more!
Conventional ODR has limitations. Say the calculated water temp for a 45 degree day is 142°. It’s a moderately windy day. Consider two different houses, both 2,500 ft. The first has a well-sealed envelope, double pane windows, and effective insulation. The second has old single pane windows, minimal (or no) insulation, and is as drafty as old fence. The boiler doesn’t know what the indoor conditions are, just that it must target 142 degrees. That 142° SWT might be fine for the first, but far too low for the second. Now to be fair, all U.S. Boiler products with outdoor reset offer a “boost” feature that will automatically bump the temperature up every “X” (boost time value) minutes, default being 20. This means every 20 minutes with an uninterrupted call, the SWT will rise 10 degrees until the max setpoint is reached. The benefit of rate-based reset is we are always looking at indoor conditions and adjusting accordingly. Rate-based reset always uses the lowest possible water temp that will maintain the desired indoor temp, and then has the boost feature if an increase above the calculated target temp is required. Like a samurai sword: simple, elegant, and effective!
There are other benefits as well. Remember the test I mentioned? Here it is. What factors showcase the benefits of rate-based reset? See the answers below. Correct your test answers accordingly…
1. No sensor to install. Rate-based wins!
A) No sensor for landscape professionals to damage.
B) No sensor for contractor to install (or throw away!)
C) No wire required from boiler to sensor.
D) No worries about where the contractor will mount the sensor, if it will be impacted by the sun, or heat migration from the interior affecting the sensor calibration.
E) Enabled from the factory. No worries for homeowner regarding whether the contractor enabled ODR. The Alta boiler is set up for maximum comfort and efficiency right out of the box!
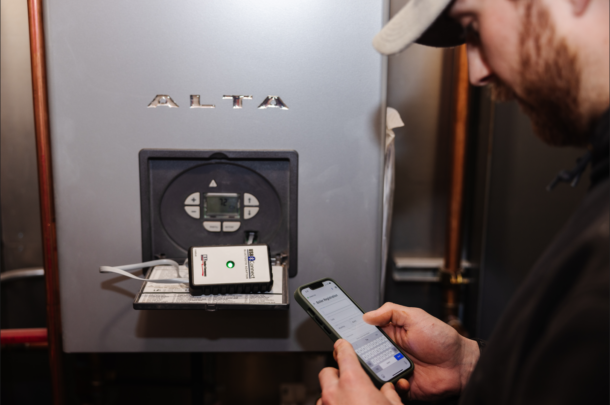
2. No Lemon Faces! Rate-based wins!
A) Always monitoring indoor temp. Onboard algorithms are constantly at work to meet heating demands while maintaining maximum efficiency. Tens of thousands of units installed with zero complaints about indoor temperature. When not writing informative and engaging articles such as this, I am a member of the renowned U.S. Boiler tech support team. I’ve honestly never received one complaint regarding rate-based reset. If you have, please contact me.
B) Not reliant on a technician with advanced, comprehensive knowledge of ODR curves. Works fine out of the box with no programming in most applications, and, where required, only minimal adjustments for almost all applications, including low temp radiant.
C) If the homeowner is made aware that during mild temperatures the radiators will not be the same temperature as the skin of the space shuttle during re-entry, and that these cooler temperatures mean more money in their pocket for candy/wine/shuffleboard, they will instead have smiles every time they touch the radiator. Or better yet, they will abandon the practice entirely…
3. Takes full advantage of condensing aspect of mod con boilers. Again, rate-based wins!
Regardless of ODT, rate-based reset always targets the lowest possible temp, thereby maximizing the potential for the boiler to run cool enough to operate in a range where flue gas condensation occurs.
I can almost feel grizzled old contractors firing up HP 386’s and waiting for the comforting squawk of their dial up modems connecting. I imagine most of the responses will begin with:
“Dear factory stooge/shill. Your article may fool the unwashed masses, but not me. My mom’s uncle’s grandmother has a hunting cabin with 1 radiator and 600 feet of ¾” pipe to connect the boiler to the house (it’s in the barn where we milk the squirrels). How does your new-fangled boiler work in my application? Hah!!! Gotcha!!!”
It will be this, or something substantially similar. There’s always at least one. For the rest of the world (and fortunately, most of the squirrels) these anomalies are rare. There is no magic solution for a poorly designed or installed system. But when a competent, capable, and progressive contractor is installing a new or replacement system, the advantage of rate-based reset over conventional sensor-based reset is clear. Reduced (or no!) programming required, no wires to pull, and no exposed exterior sensor susceptible to damage. Save time, money and aggravation. Go ahead and skip a step with ALTA.
For more information on the Alta boiler, visit our Alta Product Page.
GUEST BLOGGER: Tom Secondino is a Technical Sales Support Specialist for U.S. Boiler Company, a manufacturer of residential and commercial heating products, including condensing, non-condensing and electric boilers.
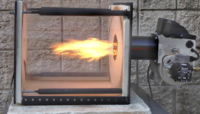
Heating oil doesn’t have the market share of some of the other fuels, but it’s used in about 4.5 million homes in U.S. Most of these homes are concentrated in the Northeast, but heating oil is in use to some degree in almost every state in the country. And the heating oil’s market share has Read more
Heating oil doesn’t have the market share of some of the other fuels, but it’s used in about 4.5 million homes in U.S. Most of these homes are concentrated in the Northeast, but heating oil is in use to some degree in almost every state in the country. And the heating oil’s market share has been shrinking over time in the face of climate change and a growing global awareness of environmental issues. The home heating oil industry is undergoing a remarkable transformation.
A quiet renaissance is taking place in the industry as communities, companies and individuals turn to a cleaner and more sustainable alternative to keep their homes warm during the cold winter months, while reducing their carbon output. That alternative is renewable liquid fuels. Electrification is often touted as the only decarbonization solution when there are many viable options, including renewable liquid fuels. Utilizing all options is the prudent approach to a worldwide problem of such immense scope.
The Need for Change: From Fossil Fuels to Renewable Liquid Fuels
For decades, homeowners have relied on traditional heating oil derived from fossil fuels to combat the chill of winter and provide abundant domestic hot water. However, with the environmental impact of these fuels becoming increasingly apparent, and with government mandates for carbon reduction, the need for a greener alternative has never been more pressing. Enter both biodiesel and renewable diesel—renewable energy sources that offer a solution to reduce carbon emissions and create a more sustainable future rapidly and economically.
The Rise of Renewable Liquid Fuels
Biodiesel, made from organic materials such as plant oils, animal fats or recycled cooking oil, is emerging as a game-changer in the heating industry. Unlike traditional heating oil, biodiesel produces up to 90% less greenhouse gas emissions, making it a cleaner and more environmentally friendly option. The shift toward biodiesel aligns with the global push for renewable energy sources and a reduction in dependence on fossil fuels.
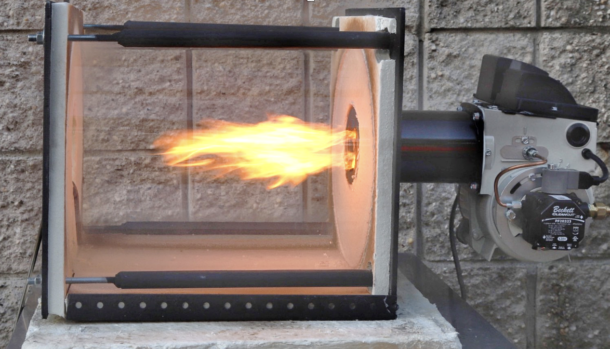
Renewable diesel is derived from the same biomass feedstocks as biodiesel but undergoes a different production process. Renewable diesel is gaining popularity as a low-carbon alternative to traditional heating fuels. Unlike conventional fuel, which is derived from crude oil, renewable diesel significantly reduces greenhouse gas emissions and promotes a more sustainable energy future. Renewable diesel is in wide use in Europe for space and domestic water heating, particularly in the UK where renewable diesel incentives and mandates are upcoming.
During the transitional phase, renewal liquid fuels are commonly blended with each other and conventional petroleum. These blends are referred to as BXX, the XX representing the portion of renewable fuel. For example, B20 would be 20% biodiesel and 80% petroleum. Blends of biodiesel and petroleum are often referred to as Bioheat®.
Initiatives Leading the Way
Manufacturers, as well as national and state associations, are taking the lead in this transition. Forward-thinking fuel dealers and individuals are driving change from the ground up. These initiatives focus on producing new burners, appliances and accessories that are rated for renewable liquid fuels, education, outreach, and the development of infrastructure to support the adoption of renewable liquid fuels for home heating.
In many cases, these initiatives are not only reducing the carbon footprint of communities but also contributing to local economic development. Renewable liquid fuel production often involves repurposing waste materials, creating new jobs, and supporting local businesses engaged in the sustainable energy sector. Utilizing waste products from agricultural production helps both the American farmer and the economy.
How to Transition?
Most fuel dealers and homeowners don’t jump immediately from heating oil to 100% biodiesel, they slowly transition the blend level upwards over time. This slow transition makes it a non-event; the homeowner and technician observe no noticeable differences and no changes in equipment are needed. As filters, gaskets and other components are replaced over time, they should be upgraded to versions rated for use with biofuels.
The same holds true for appliances—when they reach the end of their lifespan or are upgraded for efficiency purposes, renewable fuel rated boilers and furnaces should be installed. The Inflation Reduction Act (IRA) recognizes the advantages of renewable fuels and authorizes a $600 tax credit for a new liquid fuel furnace or boiler rated for at least B20.
Success Stories: Homes Heated by Biodiesel
There are more than 300,000 companies and consumers that have already made the switch to B20 or higher blends, and are experiencing firsthand the positive impact on both the environment and their wallets. Jacqueline Hart, Executive VP of Hart Home Energy in Oakdale N.Y., remarked, “Our family began injection blending biofuel more than 20 years ago because we felt it was the right thing to do to decrease our dependency on foreign oil sources and to make the environment cleaner for future generations.
Since that time, we have increased our blends, participated in every local field study conducted in our area, and have used B100 in our own homes and business. We have seen a large reduction in service calls. The Hart Family remains committed to providing the cleanest and most sustainable carbonless fuel of choice for our customers and neighbors.”
These benefits require little to no upfront capital investment unlike many other decarbonization options and provide immediate carbon reduction, not at some future time as other solutions promise.
Challenges and Future Prospects
While the transition to renewable liquid fuels presents numerous benefits, it is not without some minor challenges. Infrastructure updates, technician education and public awareness are hurdles that the industry must overcome. However, as technology advances and support grow, these challenges are becoming increasingly manageable. Technician education will play a vital role in this transition. Just as some were resistant to PEX and PVC replacing copper and cast-iron pipe or press technology replacing sweat, there will be those opposed to this future fuel.
Looking ahead, the future of the home heating oil industry seems destined for a renewable rebirth. Governments, businesses and individuals are recognizing the urgency of addressing climate change, and the home heating sector is a crucial battleground in this environmental struggle. In the pursuit of a greener warmth, the transition to renewable liquid fuels is not just an industry shift, it’s a collective effort to preserve the planet for generations to come.
As communities unite in this endeavor, the home heating oil industry, soon to be renewable liquid fuel industry, is proving that sustainable choices can keep us warm and comfortable while protecting the world we call home.
Robert O’Brien is Director of Education, National Oilheat Research Alliance (NORA).
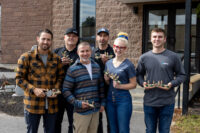
This past October, a select group of social media influencers that represent small or mid-sized, light commercial plumbing contractors attended a Watts two-day “Social Media Summit” at the company’s North Andover, Mass. and Franklin, N.H. locations. Guests included Mechanical Hub’s very own Eric Aune @mechanicalhub; Paige Knowles @plumber_paige; Travis Abaire @t.a.p.plumbingandheating; Matt Fleming @allstarplumbinginc; Evan Read more
This past October, a select group of social media influencers that represent small or mid-sized, light commercial plumbing contractors attended a Watts two-day “Social Media Summit” at the company’s North Andover, Mass. and Franklin, N.H. locations. Guests included Mechanical Hub’s very own Eric Aune @mechanicalhub; Paige Knowles @plumber_paige; Travis Abaire @t.a.p.plumbingandheating; Matt Fleming @allstarplumbinginc; Evan Berns; and Chris Sbrocco @chris_sbrocco.
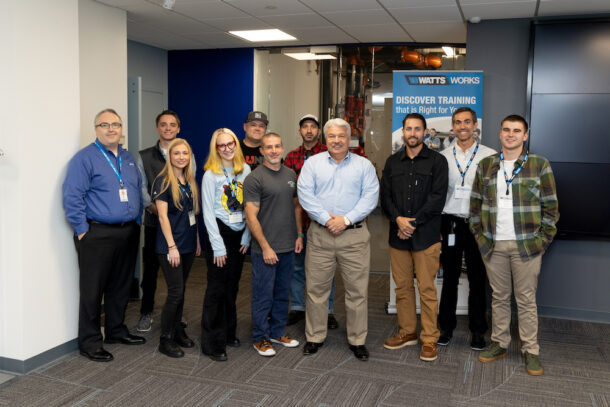
The Watts and social media crew
The purpose of the summit was to develop Watts’ own “rolodex” of online influencers who could help build Watts product excitement and awareness. Hosting a social media influencer summit provided the potential to deepen Watts’ social media influencer connections, assist in digital marketing, and gain contractor-level voice of customer. “Watts welcomed the group plumbers to discuss how social media can play a role in learning and collaborating within the plumbing and piping industry,” said Aune.
Guests were initially greeted to a hearty welcome from Watts CEO, President, and Chairperson of the Board, Bob Pagano. “We were greeted warmly by members of the Watts social media and marketing team, and heard a message from CEO Pagano about his vision for what’s coming next at Watts,” said Berns.
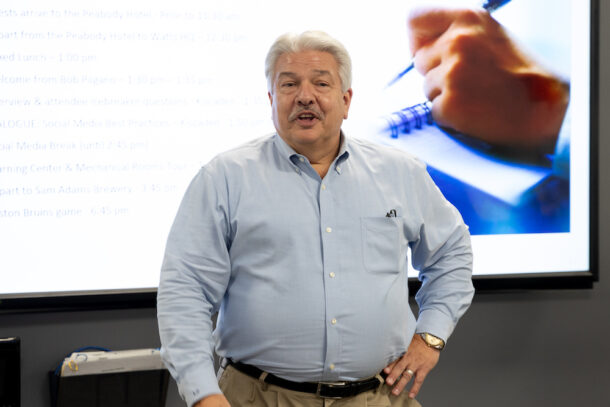
Watts CEO Bob Pagano
Following the opening remarks from Pagano, by an open dialogue on influencer benefits was held hosted by Ryan Kiscaden, Manager, Sales Enablement, with a quick breakdown of the Watts family of products from Shashwat Nath of the Watts Product Team. “After touring their state-of-the-art facility, we were able to ask questions and get our hands on products in their training room,” said Berns.
Abaire continued, “I’ve always liked the products that Watts put out, but to see firsthand the level of care, precision, and pride that actually goes into making their products gave me a whole new level of respect and trust in the Watts brand.”
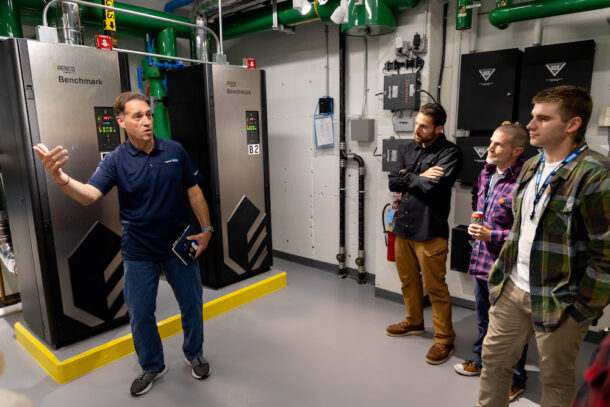
Director of Training, Greg Gyorda, gives the group a tour of a working Watts mechanical room.
In the afternoon of that first day, the group toured the mechanical rooms and learning center and met with Greg Gyorda, Director of Training, and members of the Watts training team, including Kari Stocks, Training Campaign Manager. “Watts has built a world-class training facility at their headquarters where hands-on technical training is a main focus,” said Aune.
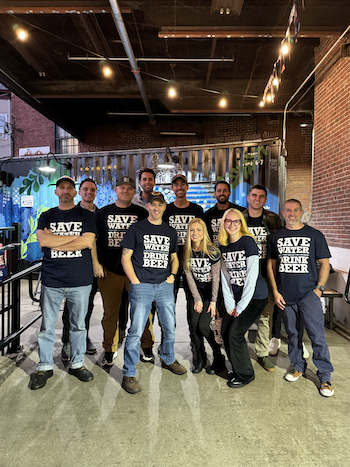
The gang at the Sam Adams brewery
Moreover, “I was impressed with the training facility, as I didn’t realize how many brands are under the Watts umbrella. They had a bit of everything at the training facility to check out and with which to get hands-on,” said Fleming.
Day one concluded with some authentic Boston flavor. “The Watts team showed us some of what Boston has to offer with a tour of Sam Adams brewery and a Boston Bruins game,” said Berns.
On the second day, the group took a one-hour trip to Watts’ Franklin Manufacturing Facility in Franklin, N.H. This facility is a center of excellence in manufacturing Watts’ specialty products that require some level of fabrication. This includes Watts-branded plumbing flow control products. The products that are manufactured at this state-of-the-art, lean facility are used worldwide in various residential and commercial applications. “We were able to tour their incredible manufacturing facilities, and got a look at the many steps that the Watts products go through before we see them on the shelf. It was great to see some of the smiling faces behind the products that we all know and love,” said Berns.
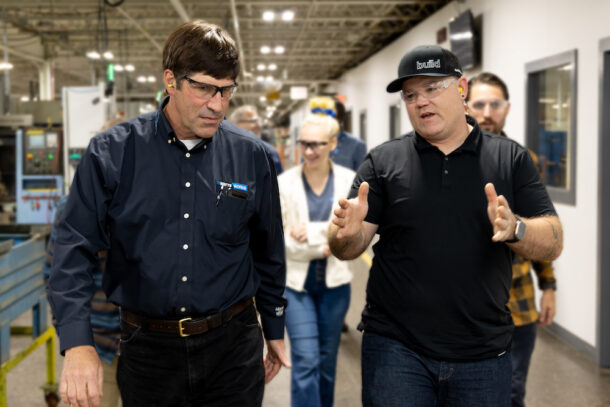
The Hub’s Eric Aune talks with Franklin Manufacturing Facility tour guide Pete Bertagna.
Tour guide Pete Bertagna captivated the group with some of the foundry’s processes, including how the world-renowned backflow preventers are made. “The Franklin factory tour gave us the opportunity to assemble our own backflow preventer from the parts manufactured on site; it was so cool to see the whole process from start to finish,” said Aune.
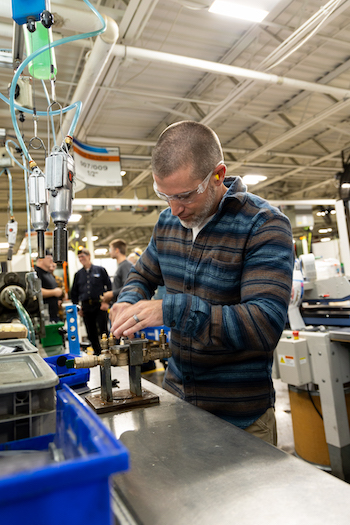
Fleming assembles his very own backflow preventer.
Fleming concurred, “The factory was also cool seeing all the backflow preventers that I’ve installed for years actually come to life.”
There is a need to continue to simplify plumbing systems and experiences over time. Online social media influencers are a “cog in the wheel” to positively influence the next generation and change perceptions. The Social Media Summit and those content creators that participated are cogs on the Watts messaging wheel. There is a growing need for training programs and education and Watts is taking training very seriously and believe it is key to its success.
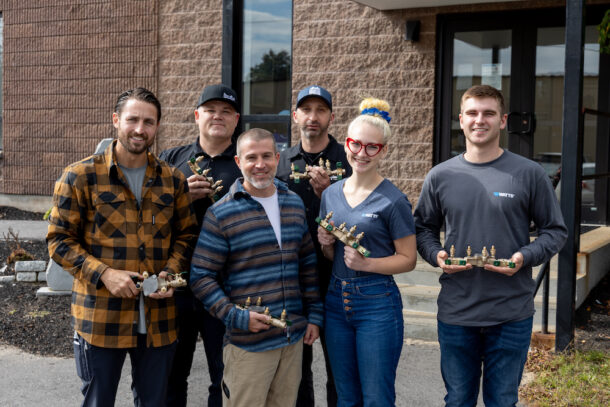
The social media crew from l to r: Chris Sbrocco, Eric Aune, Matt Fleming, Travis Abaire, Paige Knowles, and Evan Berns
Overall impressions from the Social Media Summit:
- Eric Aune @mechanicalhub:
“Watts has been present in the industry for decades longer than my 25-year plumbing and heating career. Connecting with people who make, design and distribute the products was a special experience of which I’m thankful to have taken part.”
- Matt Fleming @ allstarplumbinginc:
“At the end of the day, it was great to get to hang out with all my plumbing peers from across the country. I definitely value the friendships I’ve made through social media, and I always look for to an opportunity to hang with everyone.”
- Evan Berns @re.plumb
“The trip was a great opportunity to connect with some of the plumbing and heating industries leading professionals. Overall, it was a great event for Watts to get more involved with the online community and develop their social media presence.”
- Travis Abaire @t.a.p.plumbingandheating
“It was really a great and educational experience, and I’m thrilled I was asked to be a part of it.”
- Paige Knowles @plumber_paige
“I learned a lot about their environment and training opportunities. Seeing how backflow preventers were made, and being able to make one, was awesome!”