When people think of Alaska, they think of cold weather, vast expanses of wilderness and small communities. While they’re correct about the wilderness and weather, there are a few communities in the state that can’t possibly be called “small.” Anchorage is home to almost 300,000 people, or roughly the size of Cincinnati, Newark or Pittsburgh Read more
Featured Articles
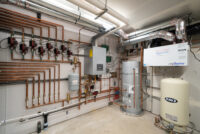
When people think of Alaska, they think of cold weather, vast expanses of wilderness and small communities. While they’re correct about the wilderness and weather, there are a few communities in the state that can’t possibly be called “small.”
Anchorage is home to almost 300,000 people, or roughly the size of Cincinnati, Newark or Pittsburgh. But unlike its Lower-48 counterparts, the city stands apart with its weather.
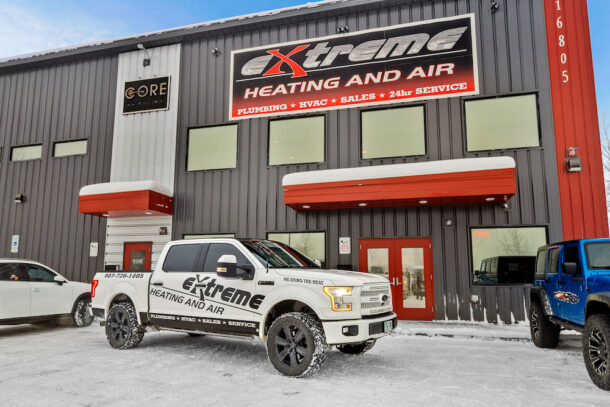
While not the coldest region in Alaska, Anchorage typically experiences between 7,000 to 8,000 heating degree days per year. Cincinnati, for comparison, averages 3,000 to 3,500 heating degree days.
“We install about four boilers per week,” said Thomas Jurancich, plumbing manager at Extreme Heating & Air. The 40-person mechanical company is the largest contractor in the Anchorage area, and likely in the state.
The biggest little state
Like all big cities, Anchorage has its bedroom communities, such as Eagle River.
When Shane Thom founded Extreme Heating & Air in Eagle River in 2009, it was after serving a four-year Air Force enlistment, where he learned the HVAC trade.
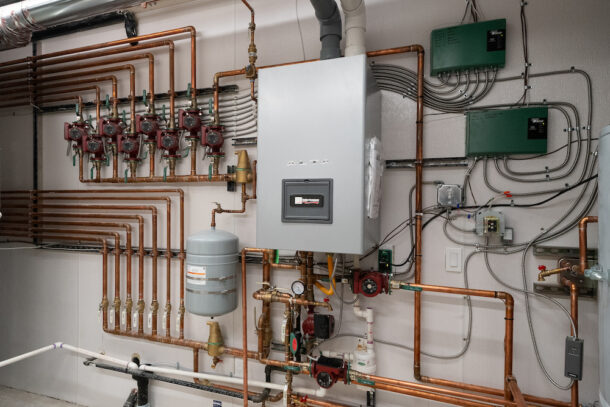
Almost all of the residential boilers installed by Extreme Heating & Air are 180 MBH, a product of Alaska’s severe winter conditions.
“I was in the civil engineering department and left the service as a Senior Airman,” said Thom. “Our primary task was setting up temporary cities, whether in Okinawa, Japan, Texas or Alaska.”
When Shane hung his shingle in 2009, Extreme was strictly focused on HVAC installations. Two years later, he added a plumbing department, and in 2013, he opened the company’s service department, along with their supply house and retail store. They serve all sorts of customers within a 300-mile radius.”
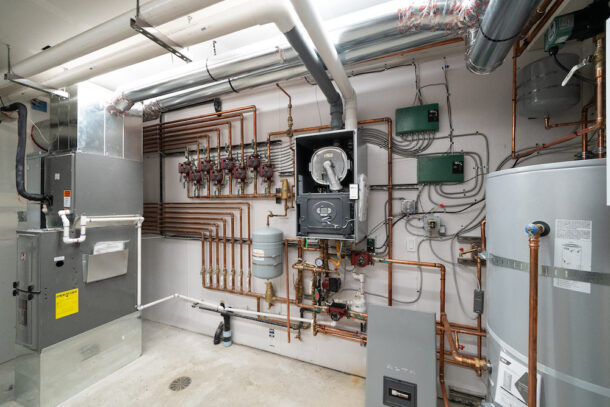
A 180-MBH Alta condensing boiler is used to supply all heat and domestic water to the large home.
Alaska’s remoteness (from supply chains), vast coverage areas, and the extreme cold temperatures (often dipping below -30°F), are the greatest challenges. Boilers are quite popular, thanks to the severe winter conditions.
Custom residential
“Our plumbing division is the largest segment of the company,” said Thomas Jurancich, plumbing manager. “Boiler work is big business here, both residential and commercial.”
Extreme has great relationships with most of the custom homebuilders in the Anchorage area. One of those, Michelsohn & Daughter, is the source of half a dozen hydronic projects each year. These homes are typically $1 million or more.
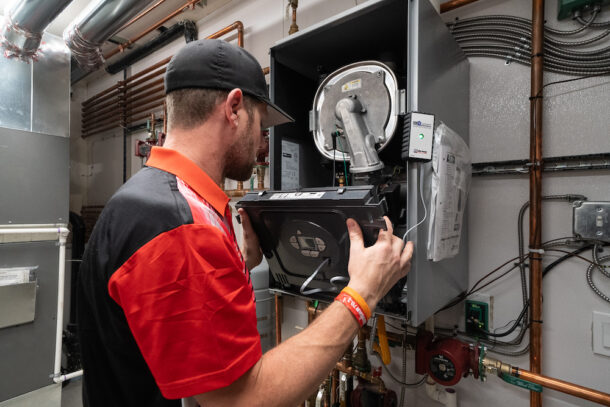
Thomas Jurancich, plumbing manager at Extreme Heating & Air, opens the Alta 180 boiler.
“New homes in Alaska with a seven-figure budget typically feature in-floor heat, and maybe snowmelt, too,” said Jurancich. “Both were included in our most recent Michelsohn project.”
The 4,7000-sq.-ft. home includes an art studio and three bay-garage, one of which is large enough to park the family’s RV. In-floor heat is used throughout, and the front walkway accounts for one small zone of snowmelt.
“All told, we have 11 zones here, including the snowmelt and 85-gallon indirect water heater, which is needed for multi-head showers and a giant freestanding tub,” said Jurancich. “We added a Rheem air handler for AC and to circulate environmental air through a Lifebreath HRV, but the only source of heat is the boiler.”
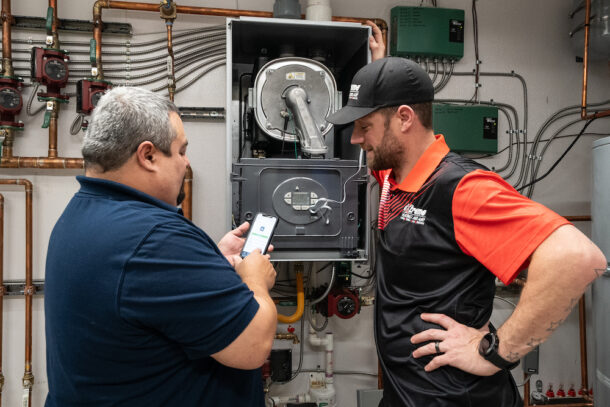
Nate Uson, territory manager with Ridgeline Mechanical Sales (left), walks Thomas Jurancich through various features of the USB-Connect Bluetooth adaptor.
A 180-MBH Alta condensing boiler, made by U.S. Boiler Company, is used to supply all heat to the home and DHW.
“We’ve been installing the Alta since Nate Uson, territory manager at Ridgeline Mechanical Sales introduced it to us,” said Jurancich. “We probably have 200 of them in the field, almost all of which are 180 MBH. New product releases are always a little worrisome with our winters, but the Alta has been exceptional.
Jurancich is quick to admit that the gas-adaptive technology and the rate-based reset features of the Alta—both new to the hydronic industry in North America—felt “too easy.” It took a few installations before the Extreme technicians felt comfortable trusting the technology, but there’s never a second thought anymore.
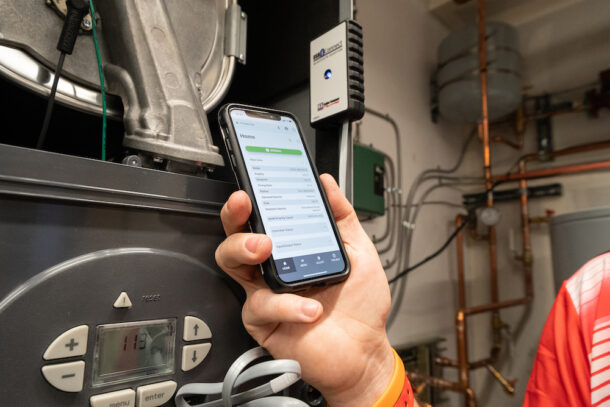
Thomas Jurancich, plumbing manager at Extreme Heating & Air, connects his phone to the Alta boiler via the USB-Connect Bluetooth adaptor.
Hot water is distributed to remote manifolds throughout the house. The radiant zones require 80°F at outdoor design temperature, and the snowmelt zone, isolated by a heat exchanger, calls for 110°F water. Chad Moore, lead boiler installer, and Joe Potter, apprentice, built the entire boiler room in three days.
“The homeowner loves the system,” said Jurancich. “He told me he takes guests into the mechanical room to show it off. I can’t think of a better endorsement of our work!”
Supply chain: end of the road
Jurancich was an outside sales rep for Ferguson before joining Extreme in 2017. This put him in frequent contact with Uson and others at Ridgeline, and that relationship has served them both well for years.
“Shane and Thomas have been great customers, and we’ve done our very best to support them, especially through the pandemic,” said Uson. “Contractors in the Lower-48 had supply chain issues, but not as bad as those in Alaska. We’re at the end of the proverbial road. Extreme has never been one to complain about price. Availability is the key concern here.”
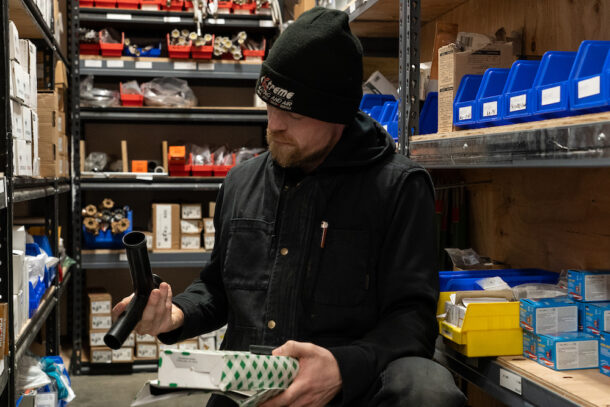
Ryan Beck, service technician, pulling product from the Extreme warehouse.
Ridgeline helped ensure that Extreme had boilers to install throughout the supply chain crunches of the past few years. Other times, Extreme reaped the benefits of their own deep warehouse. In 2016, Extreme opened their own supply house and retail store.
“We’re halfway between Anchorage and the Matanuska-Susitna Valley,” explained Thom. “Alaska is different from other states in that people here are very independent, and there’s a long way to go between supply houses. Some of our competitors buy product from us. So do plenty of DIYers.”
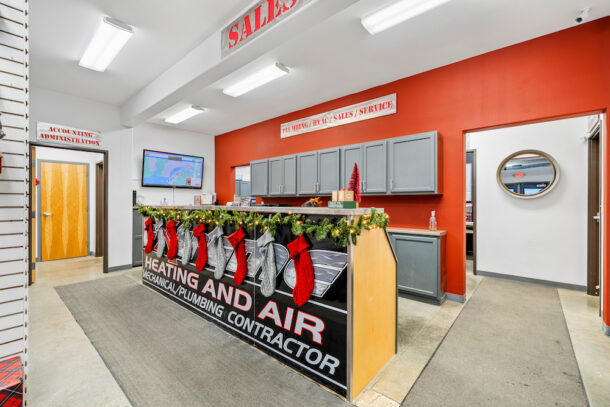
Extreme Heating & Air has 40 employees that serve a 300-mile radius of Eagle River, AK.
With good manufacturer’s reps, a fleet of roadworthy vans and a stout supply of plumbing and heating products in-house, Extreme keeps a lot of Alaskans warm throughout the winter. And none so much as in their own little town of Eagle River.
Not all residential new construction
In the 1950s, back before the roads in Eagle River were paved, activity in town revolved around the grocery/general store. That building still stands, though it’s been expanded and modified an untold number of times. It’s now a strip mall, housing a tax preparation office, dry cleaner, and more, having been converted to the Eagle River Shopping Center in the 1990s.
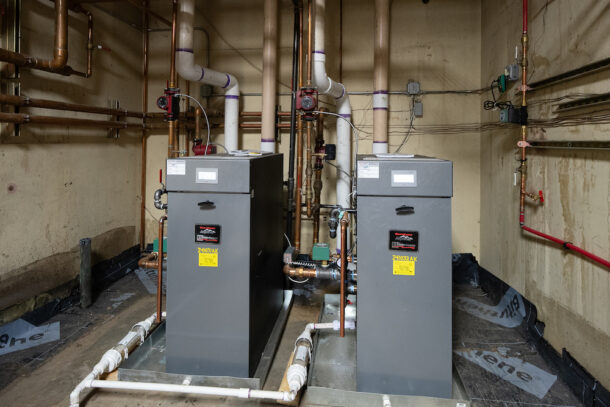
Two, 399 MBH Alpine condensing boilers are used to heat the Eagle River Shopping Center.
Extreme Heating & Air has serviced the facility’s central hydronic system for almost a decade. Doing so has always been a challenge. Its two condensing boilers were a constant source of headache, requiring nearly $10,000 worth of parts over the years. Because the building had been remodeled, changed and retrofitted so many times, zoning was less than straightforward.

The USB-Connect Bluetooth adaptor connected to one of the shopping center’s modulating boilers.
In May of 2023, the shopping center’s owner decided to fix the problems for good. Extreme was hired to gut the mechanical room and replace it with a properly sized, newly piped system.
Extreme installed two U.S. Boiler Company Alpine 399 MBH modulating boilers in lead-lag operation. The entire building uses 15 zones of fin-tube baseboard radiation and a 119-gallon indirect tank supplies hot water to each retail space.
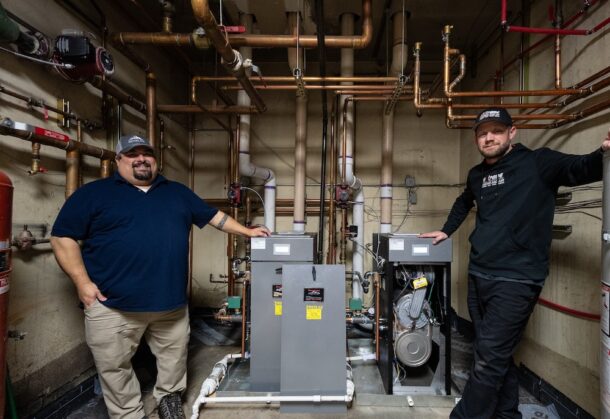
(Left to right) Nate Uson and Thomas Jurancich in the boiler room at the Eagle River Shopping Center.
“We’re fairly young guys, so we’re always looking for the newest technology to try,” said Jurancich. “Last year, Nate showed us the USB-Connect Bluetooth smartphone app, and the shopping center was the first job we tried it on. We connected the Alpine to the adaptor with a Cat 5 cable and adjusted the flow rates and supply temperatures on my phone. The guys love it for the Alpine and the Alta, so our service manager, Jacob Way, ordered eight more.”
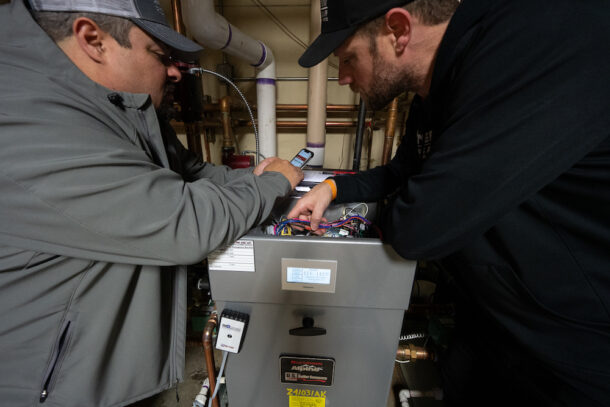
Nate Uson, territory manager with Ridgeline Mechanical Sales (left), changes boiler setpoint temperatures using the USB-Connect Bluetooth adaptor.
Over the course of three days, four Extreme technicians straightened out the piping issues and replaced the entire mechanical system. The main challenge was that the boiler room was tucked in the back of the building, separate from the retail spaces. After a full season in operation, Extreme has only received good feedback.
“They love the system because it finally works as intended,” said Jurancich.
Steady growth despite challenges
Extreme Heating & Air is growing, keeping pace with the city.
“Our biggest challenges are procuring material and manpower,” said Thom. “We’ve largely resolved our material inventory by dealing with good reps and owning our own warehouse. The manpower struggle isn’t unique to Alaska, by any means, but we’re taking that challenge head-on, too.”
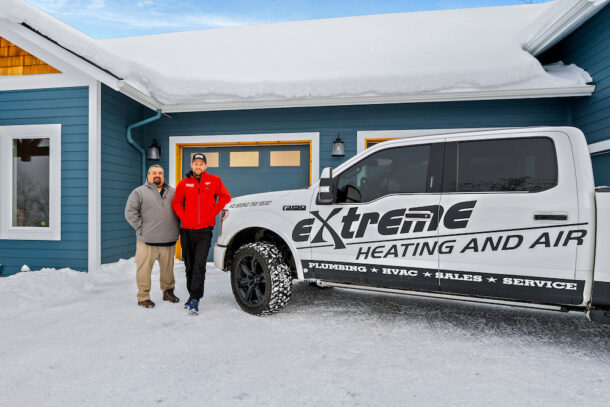
(Left to right) Nate Uson and Thomas Jurancich, their most recent custom home project with local builder Michelsohn & Daughter.
The company recruits in cold climates in the Lower 48, hoping to draw young adventure-seekers to Alaska. There are great opportunities for those looking to relocate.
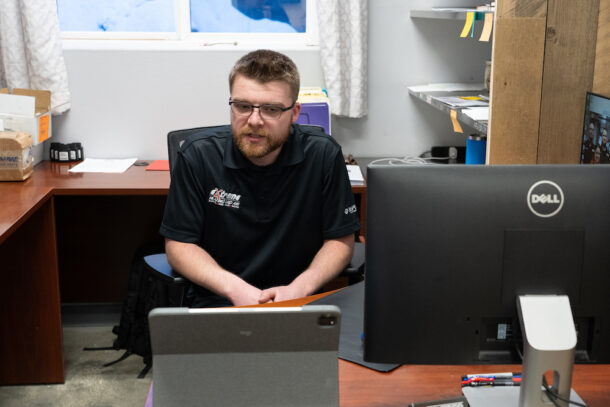
Jacob Way, Extreme Heating & Air service manager.
“We’re booked out for more than a month.” said Jurancich. “Next week we have five combi boilers going into a 5-plex apartment downtown. It’s a good problem to have. Much better than the opposite.”
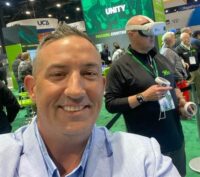
Virtual and simulation training isn’t necessarily new to the industry but its acceptance has been met with intrigue, and trepidation. But to say that this is the future of training? Not so fast. The consensus thoughts regarding this type of training is that will never replace in-person or on-the-job training, but it will become a Read more
Virtual and simulation training isn’t necessarily new to the industry but its acceptance has been met with intrigue, and trepidation. But to say that this is the future of training? Not so fast. The consensus thoughts regarding this type of training is that will never replace in-person or on-the-job training, but it will become a cog in the overall “wheel” for training assets.
According to Taco Comfort Solutions’ Product & Application Instructor-East, Dave Holdorf, Taco doesn’t want to change its training necessarily, rather seek to enhance the training experience.
“We ask many attendees how we can improve our classes and seminars. One of the most frequent replies is: ‘Add a hands-on section to the class; the theory is great and useful, but I want to install.’
“In a classroom setting, this can sometimes be difficult for the space needed, the time it takes, and to accommodate the different skillsets of attendees. We believe we’re now on a track with virtual reality (VR) training to give that experience to attendees—whether they’re seasoned pros, or new to the trade. VR can help to guide participants in what to look for, and more importantly what not to do on a project,” says Holdorf.
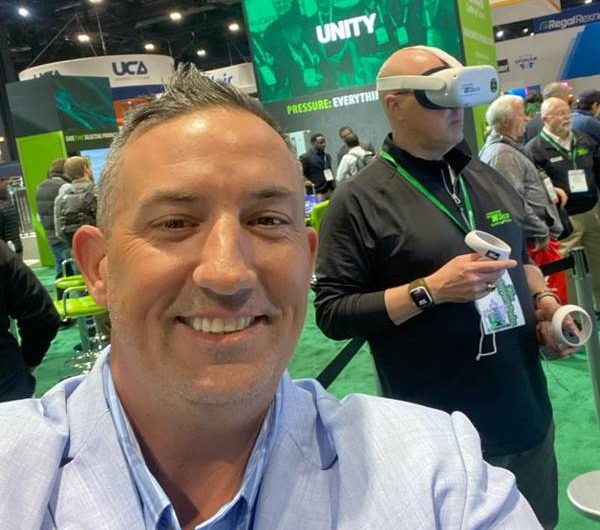
F.W. Webb’s Michael DelConte checks out the VR display at the Taco booth during the AHR Expo.
Ken Midgett, former teacher and apprenticeship Instructor, Lehigh Career & Technical Institute, now Plumbing, Marketing Director with Interplay—whose mission statement is “Better Careers Better Lives”—believes that they can play a part in a person’s career trajectory with that person using Interplay’s content. “When a person engages in learning and increases both their fundamental knowledge and the steps to do a task, we are helping that person upskill and creating more career opportunities for them. The value of a product that interplay offers is the demand function. You do not have to wait until a class is offered you can just connect and learn,” says Midgett.
Adaptation to simulation and on-demand training is paramount to success for the learner and the business. Midgett says that traditional classroom learning for skilled trades is becoming more and more challenging for several reasons:
- Finding good instructors: Many think that because they know a skill, they can teach it effectively. As a former educator, this is not always the case. This leads to poor instruction and marginal learners who are not engaged.
- The cost: The cost of running and maintaining a hands-on training center is much higher than instructor salaries and consumables.
- Change or die: Young learners are not inept at learning from lectures. Most skilled trade learners need to be engaged with learning and it must represent meaningful learning.
- The disruption of classroom learning to the workday: A rationale for going to class in the evening for 2-3 hours is losing traction to young learners. Business owners become frustrated with learning times and days as they view this as unproductive time. Young learners need to be met where they are with training that fits their lifestyle.
Interplay Learning training, combined with the new employee with the right attitude who is coachable and willing to learn, can be an explosive combination with a win-win result. “Taking an apprentice and having them spend time training and learning with on-demand training and then pushing that person into the field with a skilled person to watch and do in the real world is the best way to train this person or persons at scale,” says Midgett, who says there are numerous other advantages to this model:
- On-job efficiency increases as the apprentice now possesses the foundational knowledge and skills to perform a given task.
• Relationships are better between the journeymen and the apprentice, as the journeyman perceives the apprentice as engaged and productive.
• Business owners experience low turnover, better culture, and increased revenue as these new hires have direction and are leaning at scale.
• Technicians feel confident in their work due to training and upskilling.
• Callbacks are reduced and remediation training for the technician to increase their confidence
• Service managers can focus on coaching and maintaining technician stats instead of being the only technical lifeline for numerous techs.
• When sending these apprentices to “factory training,” they can engage and understand this much better due to the foundational knowledge.
Nonetheless, Midgett says there are a few things to note and understand about simulation and on-demand training:
• On-the-job or hands-on training with higher skilled supervision cannot be replaced.
- Simulations are great at teaching steps and muscle memory of a task.
- Simulation or any on-demand training cannot teach “feel.” As an example, simulation training cannot teach the skill of what “tight” feels like with a pair of wrenches on threaded steel piping or how tight to make a tank-to-bowl connection on a closet, or how tight a screw should be on the control board. This is what the onsite skilled person or journeyman must understand and teach effectively on site.
“While VR, AR and simulation-based technology are great resources, I do not think that any one particular learning system or style is the future,” says Rich Camacho, CEO & Co-Founder, BlueRecruit. Having said that, Camacho utilizes Interplay’s services (all of Interplay’s certifications and courses live on BlueRecruit, and when a person completes an Interplay course, they can then add that qualification to their BlueRecruit profile to strengthen their profile for Employer) and he thinks Interplay is a fantastic tool to augment in-class learning and a great launch point for someone either just entering the trades or seeking to upskill a particular technique.
“However, at the end of the day true craft mastery will occur in the field with a wrench. As technology continues to improve and costs continue to decline, Interplay will play a larger and larger part of building the next generation of skilled trades professionals and we’re excited to work alongside them in building “Better Careers and Better Lives,” says Camacho.
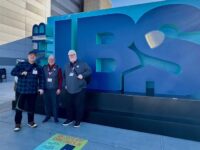
If last month’s attendance during the IBS/KBIS Show in Vegas is any sort of indicator for anything, in-person trade shows are still thriving. We’re hearing that this was the most attended show of the past 15 years. According to the National Association of Home Builders (NAHB), more than 76,000 builders, remodelers, developers and other home Read more
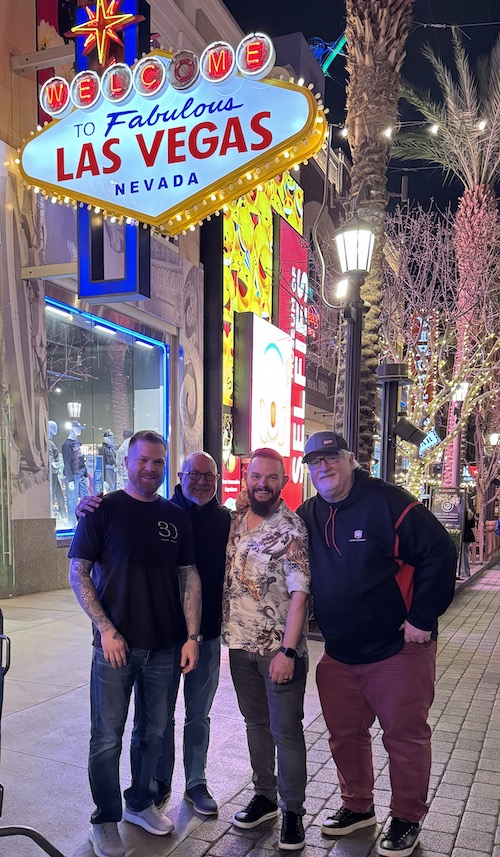
Running into friends while enjoying the Vegas nightlife.
If last month’s attendance during the IBS/KBIS Show in Vegas is any sort of indicator for anything, in-person trade shows are still thriving. We’re hearing that this was the most attended show of the past 15 years. According to the National Association of Home Builders (NAHB), more than 76,000 builders, remodelers, developers and other home building professionals filled the halls, “the highest level since 2009, which reflects the bullish outlook of the residential construction industry.”
This year also marked the 11th anniversary of Design & Construction Week® (DCW), the co-location of IBS and the National Kitchen & Bath Association’s (NKBA’s) Kitchen & Bath Industry Show (KBIS). DCW drew over 117,000 attendees, and more than 2,400 exhibitors occupied over one million net square feet of indoor and outdoor exhibits.
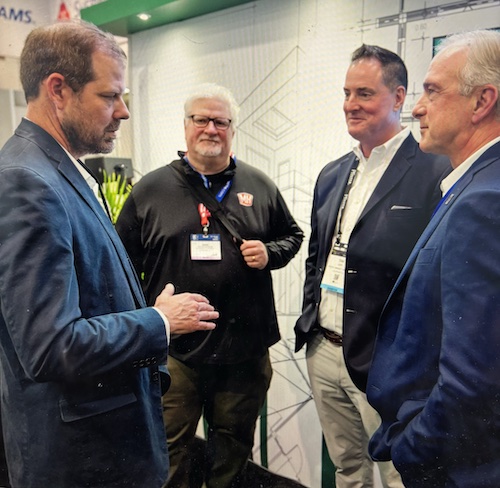
Pfister Faucet’s Spencer Brown, the Hub’s John Mesenbrink, Tim Goff, Pfister Faucets, and Dominic Sims, ICC, talk about the importance, and popularity, of the American Plumber Stories series.
Anyone who has visited the Las Vegas convention center knows that there are basically four separate halls—North, Central, South and West. I am of the opinion that the Central Hall usually gets the influx of traffic initially—over the course of the three-day event—with crossover to the North Hall fairly fluid. The North Hall is generally reserved for big bathroom players, and Central and South are filled with construction/builder booths. The West Hall, honestly, is almost at a different location where, in order to get there most of the time, you are sent underground, blindfolded and whisked through a tunnel via a manned Tesla. Pretty cool experience, actually, but not necessarily ideal if you are exhibiting in West because that’s where the trickle or “if I have enough time” traffic goes. My opinion, of course.
Oh, I almost forgot. There are a number of exhibitors set up outside—our friends from the Propane Education & Research Council (PERC), for example—right in front of Central Hall. The blue sky, 70° temps didn’t hurt those outdoor experiences either.
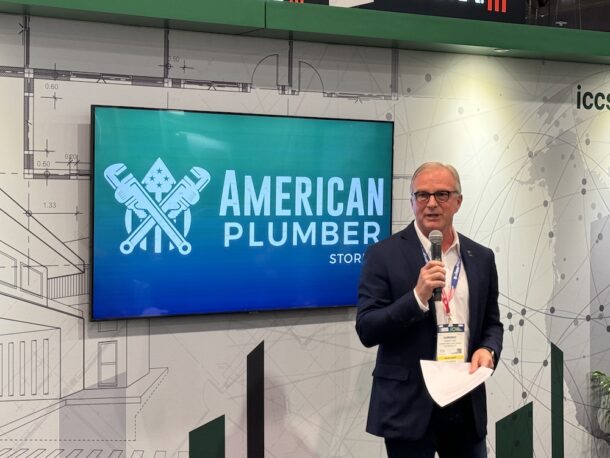
Dominic Sims CEO, International Code Council (ICC), talks about the partnership with American Plumber Stories for upcoming season 5 of the wildly popular docuseries.
Just a note of interest here, getting the show is getting easier with access to the monorail, which makes stops to a number of hotel locations—if it looks full, just keep nudging, you’ll find space—and hotel bus routes, which can be found in front of the Central Hall and to the side of the South Hall. Depending on when you are entering or leaving the show, Uber and taxi at your own risk.
Now, if you’ve been to the IBS/KBIS trades shows in recent past, you’ll know that the setup is pretty formulaic, but it was brought to my attention that this year they pretty much simplified the approach with similar products located near each other so you don’t have to break your Fitbit traversing the LVCC universe trying to find something.
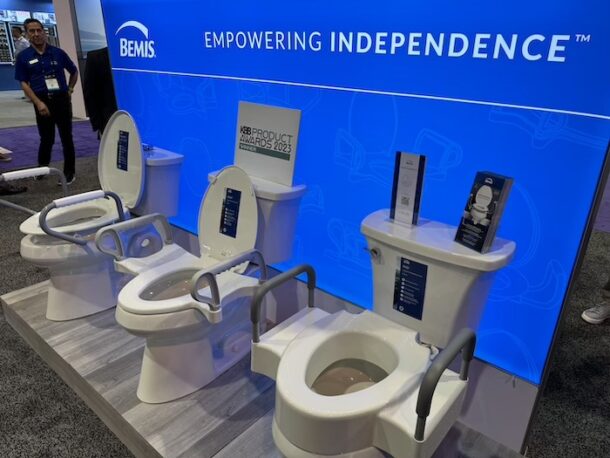
Everything from low-flow toilets, ADA & Living in Place to the latest in bidets, KBIS had it all. From the Bemis booth.
Invariably during every trade show I attend I get asked, “what was the most interesting thing you saw on the show floor?” Well, I gotta say it was the Genesis Systems WaterCube 100, which basically creates water out of the air. I was fairly shocked when I saw the size of this unit—large—to be installed on the exterior of the home. The company contends that the product sustainably generates more than 100 gallons of fresh water daily from the air around it—enough for a household of four, and it operates in humidity ranges of >40-100% and ideal climate temperatures of >59 degrees F.
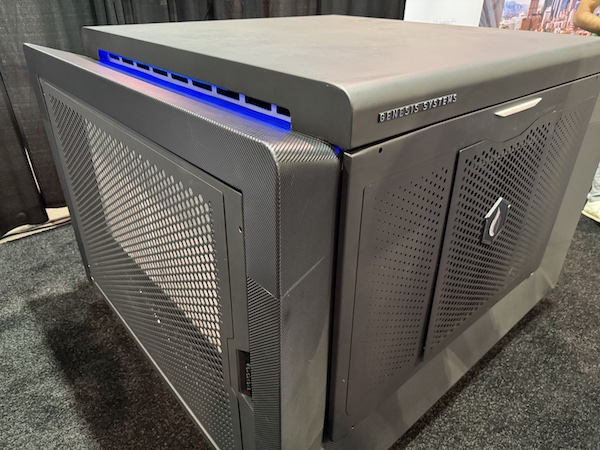
Genesis Systems WaterCube 100
In the North Hall, we saw everything from the latest in bidets, low-flow toilets, high-end kitchen and bathroom fixtures to fancy multi-colored bathtubs—a kitchen and bath designer’s fantasy space, if you will.
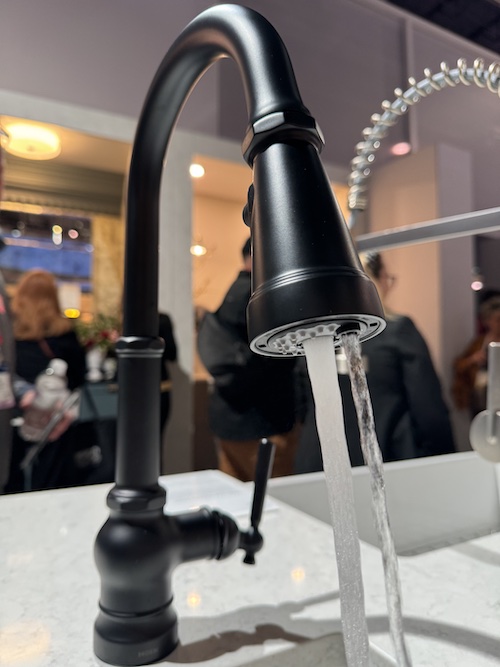
Moen’s 3-in-1 Water Filtration Pulldown faucets dispense filtered cold water and hot and cold tap water, including a three-function pultdown wand. 3-in-1 Water Filtration Kitchen Pulldowns pair with any Moen filtration system and are available in many styles and finish options.
“2024 marks the 60-year anniversary of KBIS—a tremendous accomplishment and an opportunity to not only celebrate our growth but to set goals for how we want to continue to elevate the show and help drive the industry forward,” said Bill Darcy, Global President & CEO of NKBA|KBIS. “We’ve had great success collaborating with NAHB and IBS and are proud to announce our continued partnership as part of this milestone year. As the kitchen, bath, and wider residential building, architect, design, and remodeling sectors continue to grow it’s more important than ever to provide a central source for inspiration and innovation.”
NAHB and NKBA announced an agreement to extend the co-location of IBS and KBIS for four years through 2030.
Next year, DCW will return to Las Vegas, Feb. 25-27.
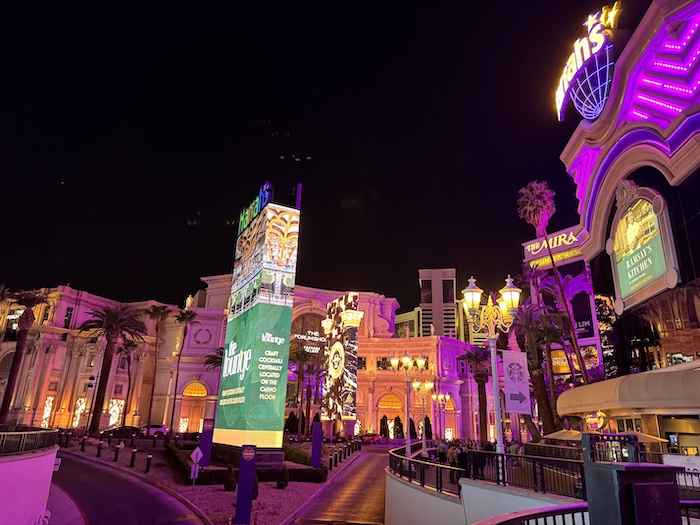
See you next year in Vegas!
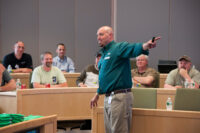
Training in 2024 is just as important as ever. How do you integrate training, education and continued learning with today’s busy contractor? Power Points, sales pitches and doughnuts. Tried and true methods of training gone by, that’s for sure. But what does today’s training look like, especially in the purview of the younger generation of Read more
Training in 2024 is just as important as ever. How do you integrate training, education and continued learning with today’s busy contractor?
Power Points, sales pitches and doughnuts. Tried and true methods of training gone by, that’s for sure. But what does today’s training look like, especially in the purview of the younger generation of contractors that digests information in 90 seconds or less?
“What was that? Sorry, I was looking at my phone,” jokes Max Rohr, Director, Education and Technical Marketing, Caleffi. “Five years ago, a three-minute-long video was a good option, now it will seem long if it is over that 90-second threshold. Ideally, you get to the point in the first five seconds and work the explanation back from there. Like showing the cake and then going back to bowls of ingredients.”
According to, Dave Holdorf, Residential Trainer & Rep Training Manager—Eastern Region, Taco Comfort Solutions, it’s a challenge. “We’ve found that it helps to bring different instructors in for specific segments of the training. Each instructor brings their own perspective; even hearing a different voice in the room makes for a more compelling presentation. Every facet of our training is now geared to maintain the attention of participants. We also make sure to schedule breaks so that the attendees can attend to business, or need at home. By creating the curriculum with attendees in mind, their focus remains with the topic in front of them.”
Nevertheless, the training department at Taco has always looked at training not from a product view but from an application perspective, giving attendees the information they need to do their job better, and to give their customers the comfort they deserve. “We use real world experiences to solve real world problems with personal experiences and a bit of humor—as you know, John, it ain’t worth doing if you’re not having fun as well,” says Holdorf.
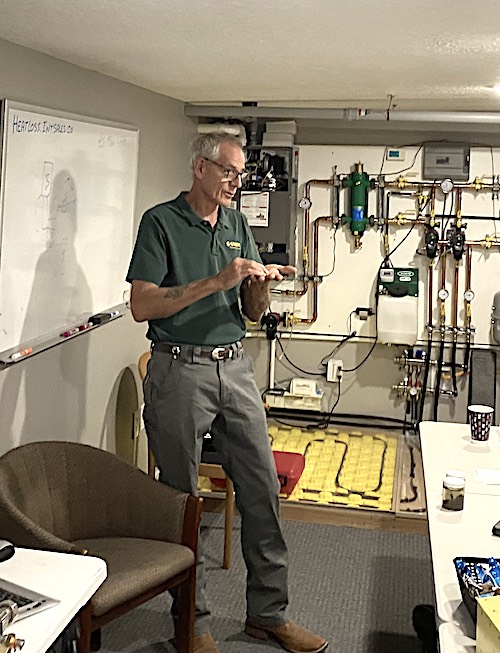
Caleffi’s Bob “Hot Rod” Rohr brings his props and his wealth of experience and knowledge to trainings.
But what about those PowerPoints and doughnuts? “Every learning style is different, so you have to be adaptable. If you see the audience tuning out a PowerPoint, stop and grab a product to bring to an attendee and talk about a case study that is related instead,” says Rohr.
In addition, everything falls apart for a trainer if the audience gets the impression they are overpromising, adds Rohr. For example, “Honesty is something Hot Rod is specifically good at in contractor training sessions. As a former installer, he always has tips for getting the job done and workarounds that are really tangible,” says Rohr.
The New Normal?
The Covid pandemic saw what we thought was going to be a new normal with virtual training, but what we are now seeing is the importance, and return, of in-person training.
This past year Taco saw a huge jump of in-person training, on the road as well as at Taco HQ in Rhode Island. So much so that the company had to dramatically increase the number of sessions back in Rhode Island to accommodate. “However, that does not mean to diminish the virtual training, Taco Tuesday and Taco After Dark webinars are still posting a large number of attendees that are hungry for information in bite size chunks, not as large as when we all locked down at home, but still popular,” says Holdorf.
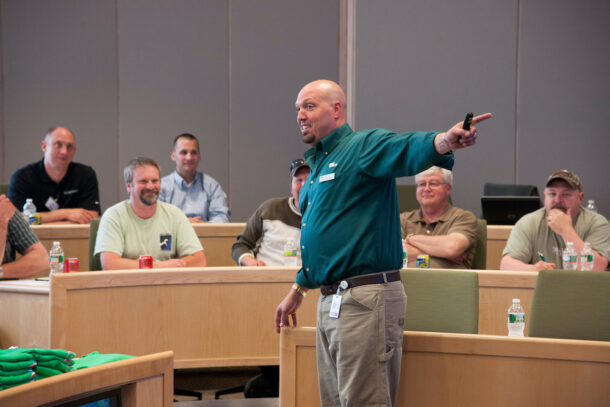
Taco’s Holdorf conducts a training at the Cranston, R.I. HQ.
Nonetheless, “when we’re online, we know it’s so easy to stray off to the next shiny thing online, so to keep attendees engaged, we encourage two-way communications. If participants have questions, we want them to ask immediately,” continues Holdorf.
In fact, Holdorf says that people who attend Taco’s webinars typically take it to the next level and seek live training. A combination of both virtual and live training can help attendees dial in on what they want to learn—or perhaps didn’t initially develop a full understanding of what it is they most needed to know. “These options allow them to fine-tune their training experience to make them as good as they want to be. And, ideally, we help them raise the bar. We routinely heard from trade pros who came to us for a better understanding of a single application or concept, and through that experience come away with an energized desire for much more,” says Holdorf.
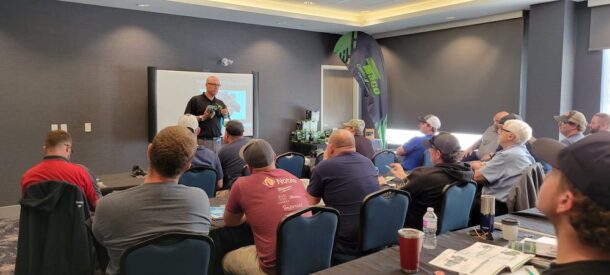
In 2023, Caleffi performed almost a 50/50 mix of in-person and virtual. Contractors like hands-on training, says Rohr, so it is good to be back on job sites for that type of interaction. And, engineers didn’t all go back to the office after COVID. “Many of the engineering sessions we do are virtual because that firm may be scattered all over the region. You might catch 20 people in a virtual training, where only 10 of them are in the office that day,” says Rohr.
Know-It-Alls
What about those who are stubborn enough to think that they don’t need further education and training? “I love this question and see and hear it often in the industry,” says Ken Midgett, L.M.P, Plumbing, Marketing Director, Interplay Learning, and former Teacher and Apprenticeship Instructor, Lehigh Career & Technical Institute.
Those in skilled trades should embrace the concept of being “lifelong learners,” consistently expanding their knowledge in their current specialty and exploring related disciplines. Whether licensed or not, individuals in skilled trades should assess their goals, career paths and professional growth within their field. It’s common for some to reach a point where they feel adequately skilled and think further education is unnecessary. According to Midgett, this assumption is misleading for several reasons:
• For example, a residential plumber could benefit from learning about commercial plumbing, Med Gas, Backflow, Water Well work, Water Conditioning, HVAC, Electrical, etc. Diversifying skills not only enhances one’s expertise but also increases their marketability across various skill sets, intern boosting income and long-term employability.
• Despite advancements in safety measures within the construction industry, the misconception that skilled trades workers are immune to injuries persists. While the overall safety landscape has improved, life-changing injuries can still occur. In such unfortunate instances, if an individual can only rely on skills specific to their trade and lacks versatility, their career may face irreparable damage. Therefore, investing in ongoing training, education, and professional development becomes crucial for ensuring resilience in the workforce and mitigating the impact of unforeseen challenges. Repurposing skillsets may be challenging when there has been no prior skill or professional development planning before the injury event.
• The industry, codes, tools, and methods to do a task are constantly changing. Skilled trades workers need to educate themselves and stay on top of new developments. This is critical to the success of a technician and company.
In the end, it’s what ends up in the ol’ noggin as useful information that translates to the jobsite. “Students only retain a tiny amount of the information that you present to them, but they will remember their feelings about the trainer for a very long time,” says Rohr. “It is hard to know if a bigger win is when customers retain a piece of information you presented or if they remember that you seem like you know what you are talking about. “If they trust that you did a good job, that memory will stay with them for a career, potentially.”
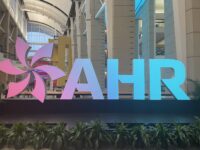
Are we beyond using the COVID pandemic years of 2020-2021 as a benchmark for anything moving forward? Ok, this will be my last but I felt that AHR 2024 knocked it out of the park, with attendance numbers equaling that of shows past, pre-pandemic. I actually heard, and this hasn’t been verified as of yet Read more
Are we beyond using the COVID pandemic years of 2020-2021 as a benchmark for anything moving forward? Ok, this will be my last but I felt that AHR 2024 knocked it out of the park, with attendance numbers equaling that of shows past, pre-pandemic. I actually heard, and this hasn’t been verified as of yet, but the day one on-site registration was nearing record levels. And day two crowds were still buzzing as traffic on the floor filled the aisles. (THIS JUST IN FROM AHR: It was clear to anyone filling the halls on Monday morning of the show that attendance was strong, welcoming 48,034 attendees there to interact with the 1,875 exhibitors spread across North and South Halls. )
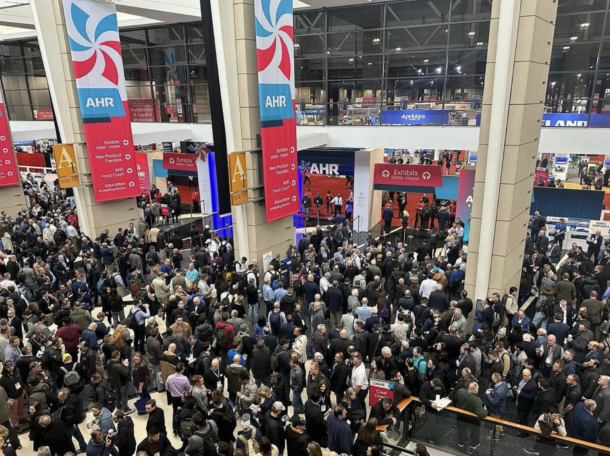
To a booth, everyone was satisfied with the turnout and conversations during the show. The show marked a return to business as usual, at a much more accelerated pace. And to think, this is during mid-January, polar vortex temps, no less. (Don’t miss next year’s show February 10-12 in Orlando.)
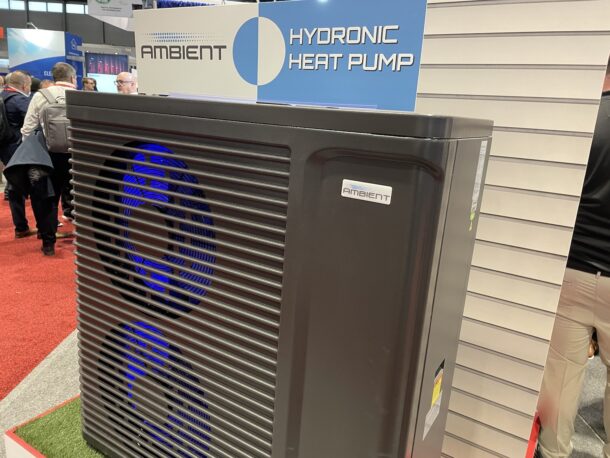
U.S. Boiler Co.’s Ambient Heat Pump
Technology, innovation and new products dazzled, with heat pumps and the push toward electrification still dominating the topics of conversation. We heard more of VR and simulation training as a trending topic as well, with Artificial Intelligence, Workforce Development, Decarbonization all playing big parts at the show.
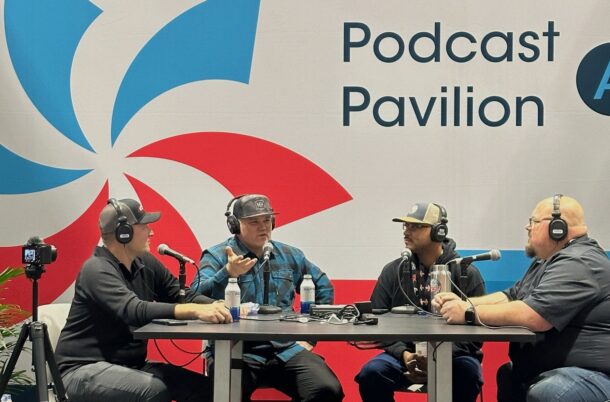
The Mechanical Hub team had a busy three days shooting videos in-booth, recording both Make Trades Great Again and Appetite for Construction podcasts, and we were even asked to emcee—and be a part of—a Coffee with Caleffi panel in the Caleffi booth on Monday morning. There, hosts John Mesenbrink and Tim Ward talked with industry bigs John Siegenthaler, Bob “Hot Rod” Rohr, Eric Aune and Andy Mickelson.
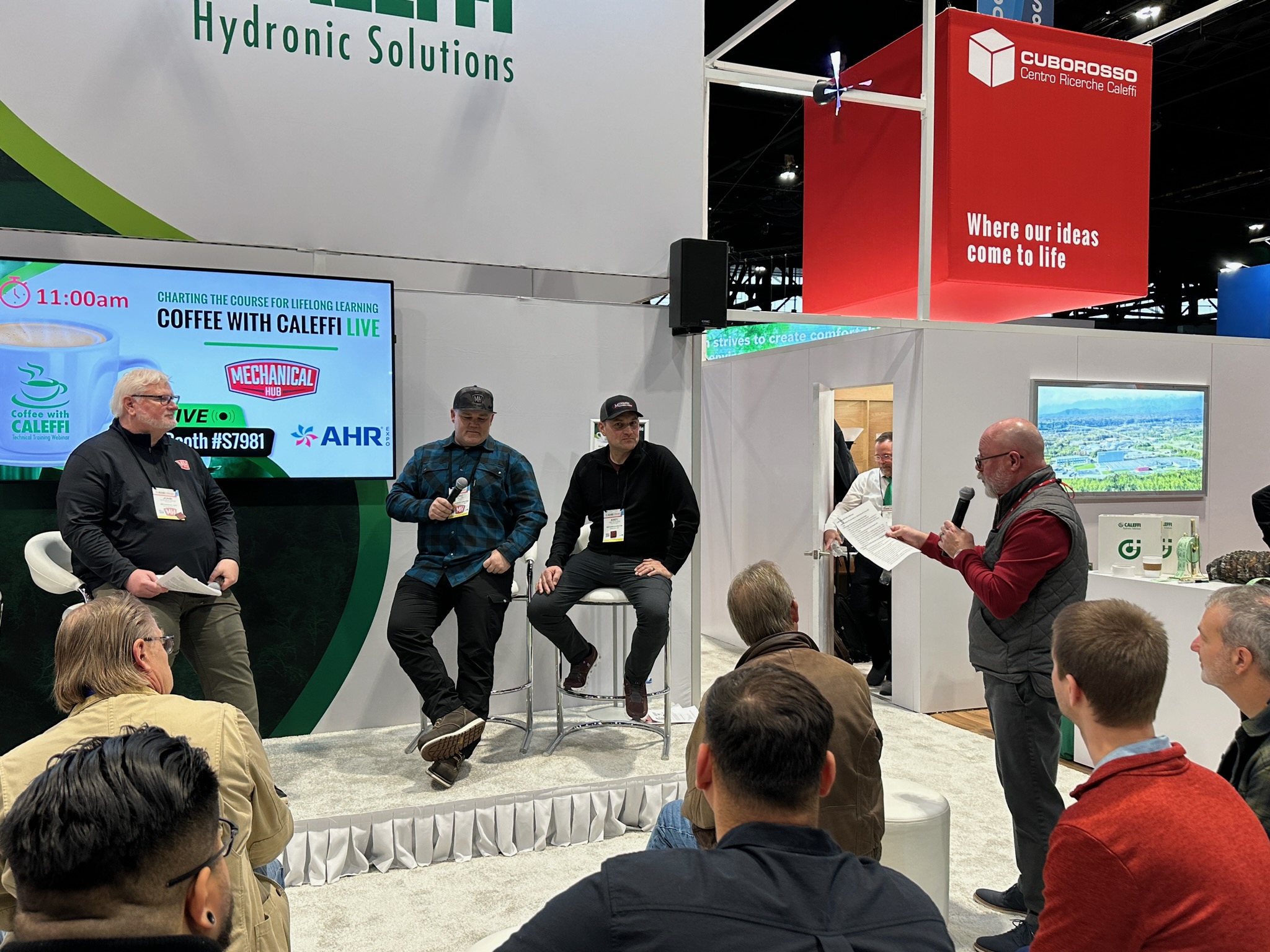
The discussion revolved around lifelong learning in the trades: where do these legends go to learn? Forgetting more than most of us will ever learn, Siegenthaler and Rohr talked about outlets for learning and continued training. Aune and Mickelson gave the point of view from a current business owner and working contractor, and the impact of social media in today’s PHVAC trades.
We can’t forget about the after-parties and the go-to for us has always been the Taco event Monday evening. It’s a chance to meet up with old and new friends alike.
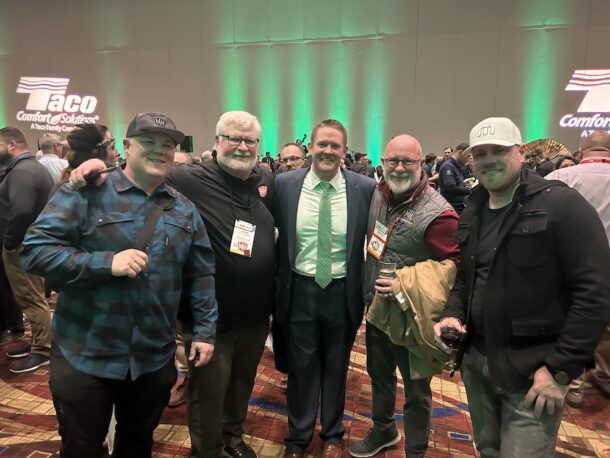
From l to r: Eric Aune, John Mesenbrink, Ben White, Tim Ward, Mike Prencavage, Jr.
One event I had the pleasure of attending—and it was my first time—was the HVAC Tactical Awards extravaganza held at the Planetarium downtown Chicago. I believe this was the fourth annual event, and the tagline, “It’s a mindset” is turning into “It’s a movement.” This was another great event to see good friends, and the idea of night of “Blue Collar Goes Black Tie” can’t be overstated.
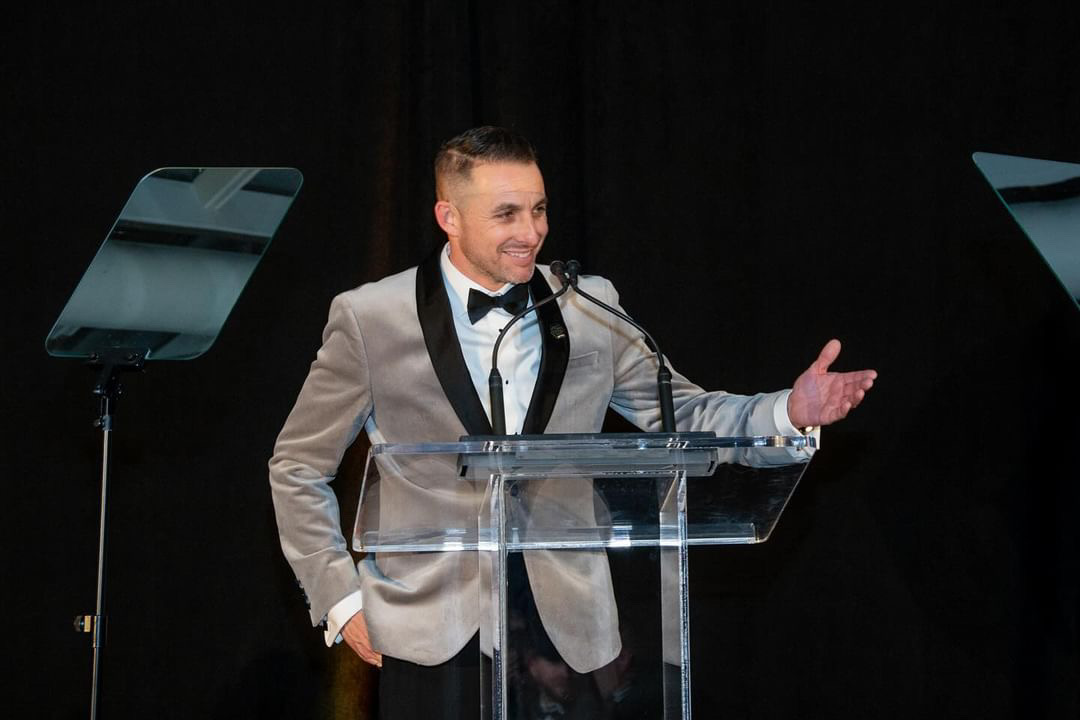
Ben Poole, HVAC Tactical
The industry needs events like this to showcase the trades in the best, shining light there is. And this event, with the red-carpet entry, exclusive red-carpet interviews, cocktail parties pre and post, and the awards ceremony, give this a gala-type feel, with everyone dressed to the nines, and I think everyone digs that vibe, at least for one night.
Links to AHR Expo Videos: