Businesses that entrust their data storage to the state-of-the art Novva data center outside of Salt Lake City will benefit from a location chosen for its many data center-friendly attributes. The area offers outstanding connectivity, low power costs, and a central-western site with easy access to a major international airport. In addition, the site’s climate Read more
Featured Articles
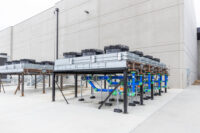
Businesses that entrust their data storage to the state-of-the art Novva data center outside of Salt Lake City will benefit from a location chosen for its many data center-friendly attributes. The area offers outstanding connectivity, low power costs, and a central-western site with easy access to a major international airport. In addition, the site’s climate and 5,000-ft. altitude allow for many hours of free cooling annually.
Just as important to Novva’s clients, the new data center has a low disaster risk. The area is not prone to earthquakes, floods, or adverse weather events such as hurricanes.
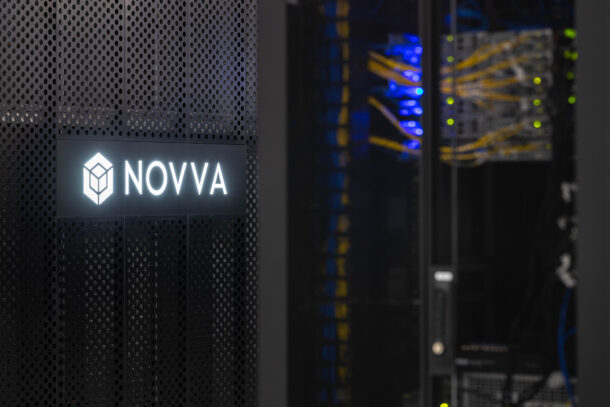
And finally, for the additional peace-of-mind that makes this data center truly start-of-the-art, the cooling system for the computer servers boasts Aquatherm PP-RCT piping that will provide virtually leak-free service for decades to come. The Aquatherm piping will never scale or corrode, and the cooling water flow will remain unchanged throughout the anticipated 50-year lifespan of the pipe. All of this data adds up to a win for Novva and its clients.
The “hyperscale” data center in Salt Lake City will be Novva’s flagship data center. The 100-acre Utah campus is planned to ultimately include more than 1.5 million square feet of data center space and will accommodate 250kW to 30 MW clients. The construction is taking place in four phases. The first phase, which includes a 300,000-sq.-ft. data center, a 120MW substation and an 80,000 sq ft headquarters office building for Novva, was completed in December 2021.
Beating the Heat
Reliable cooling systems are an essential component of modern data centers. Computer servers are notorious for generating heat—and heat is notorious for being an enemy of computer servers.
The decision to install Aquatherm pipe as part of the new data center’s cooling system was driven by Steven Boyce, vice-president of infrastructure and design at Novva Data Centers. Boyce has been involved in the IT and data center space for more than 20 years, and has worked on multiple successful startups during that time.
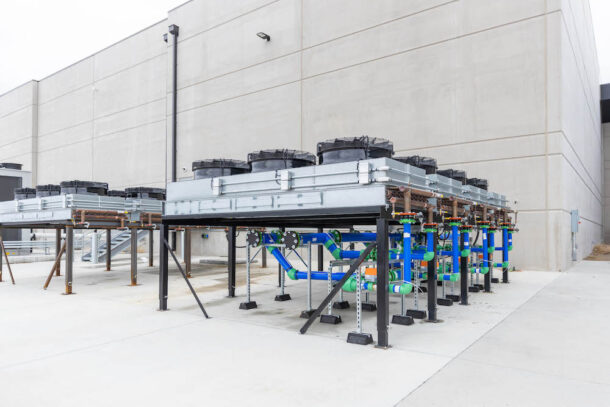
When I first learned about Aquatherm, it was a no-brainer,” Boyce said. “I had been using steel pipes in my builds, which would corrode and rust, and in turn, fill my equipment with sediment and pieces of rust. Efficiencies would be diminished, and the pipes would eventually have to be replaced. Aquatherm’s total installed costs are lower, and their warranty is something that no steel vendor could match.”
Once the decision was made to trust the cooling system’s performance to Aquatherm pipe, Novva turned to the Salt Lake City branch of Harris Mechanical for the installation.
Harris had experience installing Aquatherm pipe, although the Novva data center represented the company’s largest data center Aquatherm installation to date. To handle the first phase of the Novva system, Harris installed a BASX custom chiller package (which included the pumps and controls), the Aquatherm pipe for computer system cooling, and the comfort system piping and plumbing. The piping work for phase 1 began in mid-May 2021 and was completed in October 2021. The system was commissioned and turned over to the owner in December 2021.
Fast and Furious
Jeff Reading, operations manager, construction, Harris Mechanical, explained that the Novva data center started out as a core and shell project, with the office built first and the data hall scheduled to be built out later. However, as anyone in construction work knows, it’s always best to expect the unexpected.
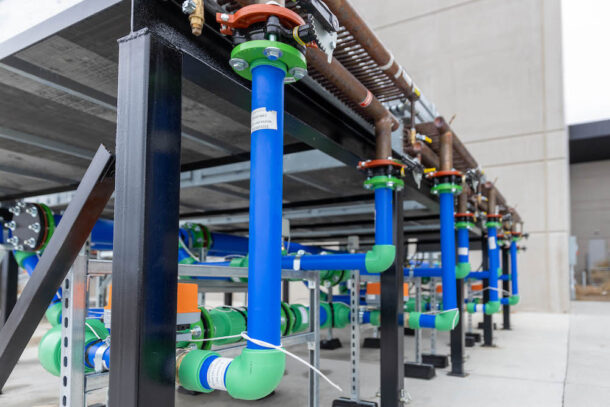
“We finished the core and shell construction in May 2021, and the data hall was right on its heels as a change order to the original project. So it came at us fast and furious,” Reading said. “The original plan was to complete the entire chilled water loop, which runs underneath the floor on both sides of the building. However, it was decided to install the piping in stages as the facility is built out. So far we have installed about half of the piping that will ultimately go in there.”
The installation to date has included 4,418 ft of Aquatherm Blue Pipe SDR 17.6. The main system piping is 10-in., and the takeoffs are 4-in.
Training Professionals
To handle such a large project. Harris Mechanical sent several installers to Aquatherm’s U.S. headquarters in nearby Lindon, Utah, for training.
Having Aquatherm-trained technicians opens up new opportunities for HVAC and plumbing companies. The company gains differentiation in the market, and enjoys the time- and labor-savings associated with installing polypropylene pipe.
Aquatherm training is the most intensive, comprehensive training in the polypropylene piping industry. Attendees receive both classroom training and hands-on training with multiple fusion machines, and must pass a rigorous test using all the fusion tools correctly.
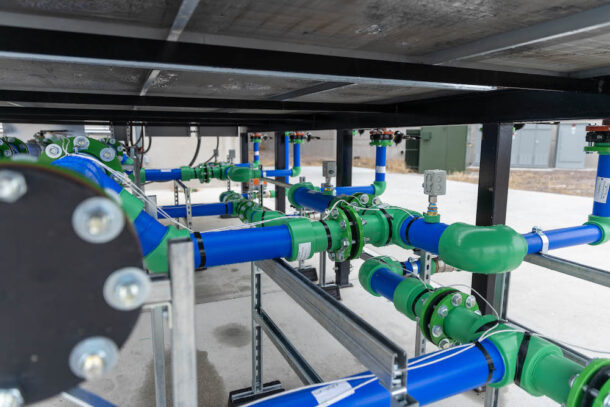
After the training, Harris completed the installation using McElroy fusion tools and a combination of socket fusion for the 4-in. pipe and butt fusion for the 10-in. pipe. The system runs at a low pressure (35 to 45 psi); the cooling system supply water runs at 55°F and returns to the chiller at about 60°F.
According to Reading, Harris Mechanical had a good experience with Aquatherm piping at the Novva data center, and the ease of installation compared to steel pipe helped Harris stay ahead of the project’s tight schedule.
“It was a smooth process,” he said. “We definitely gained experience and confidence with the pipe throughout the project, and our installers became accustomed to ‘leapfrogging’ and working with more than one [fusion] machine at a time.”
A Smooth Path
The underfloor piping system presented one of the major installation challenges at this project. The floor is raised 5-ft., and all of the facility’s piping, wiring, HVAC ducting, and utilities run through the raised space.
Aquatherm’s building information modeling (BIM) capabilities and Scan-to-Fab service helped ensure that the installation went smoothly by preventing underfloor conflicts and collisions.
“Using 3D BIM and Revit really helped with coordinating this installation,” said Autumn Turner, a fabrication drafter at Aquatherm. “Not only was all the HVAC and plumbing under the floor, there were floor stands every square foot. It took a lot of coordination to avoid all those potential obstacles.”
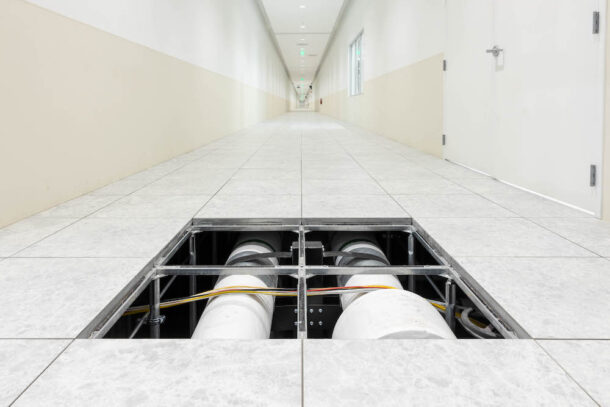
Turner noted that careful coordination enhanced the already-fast heat-fusion installation of Aquatherm pipe, and that less time and money spent on welders is a major benefit of choosing Aquatherm.
“Aquatherm is just easier work with than steel pipe,” she said. “It takes a lot less time to weld, and when you add in the BIM support and drafting it was easier for the installers to get situated into the floor and navigate the space.”
Turner added that Aquatherm’s BIM and Revit capabilities will ensure the future installation phases of the massive project also go smoothly.
Rhett Coles, Aquatherm’s fabrication drafting/scan-to-fab manager, said that Aquatherm’s Scan-to-Fab service and in-house fabrication makes any piping installation easier and smoother. Spools can be custom made in any size or configuration and shipped to the jobsite ready to install. In addition, any pieces fabricated by Aquatherm are covered by a comprehensive 10-year warranty.
“In the case of the Novva data center, we were in constant communication with Steven Boyce and the owner’s group,” Coles said. “We were not providing a cookie cutter system to them. They would tell us whatever they wanted or needed and we would work directly with them to help them fully accomplish their goals.”
A reliable, leak-free piping system with a long life span, and a smooth installation in any space, including challenging underfloor designs? The data are in: Aquatherm is the right choice for data centers.
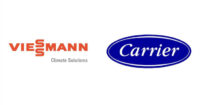
Viessmann and Carrier align; Uponor rebuffs Aliaxis. Are we seeing a renewed “trend” toward consolidation in the PHVAC industy? Inflation, fuel prices, war, supply chain, electrification, and economy woes are all factors for potential wholesale changes. Over the past month, there has been heavy movement in the industry to suggest such a thing. In a Read more
Viessmann and Carrier align; Uponor rebuffs Aliaxis.
Are we seeing a renewed “trend” toward consolidation in the PHVAC industy? Inflation, fuel prices, war, supply chain, electrification, and economy woes are all factors for potential wholesale changes. Over the past month, there has been heavy movement in the industry to suggest such a thing. In a week that saw big movement, we learned recently that two major players in the PHVAC industry have been active in talks.
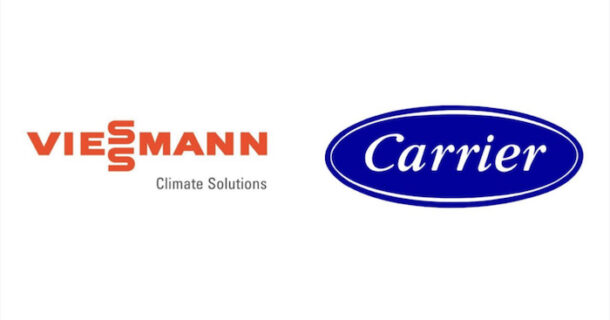
The first, just officially confirmed, Carrier will acquire Viessmann Climate Solutions, the largest segment of Viessmann Group, in a cash and stock transaction valued at €12 billion, subject to working capital and other adjustments. According to the release, Viessmann Climate Solutions provides Carrier with an iconic, premium brand in the highest growth segment of the global heat pump and energy transition markets. In addition, Carrier announced plans to exit its Fire & Security and Commercial Refrigeration cabinet businesses.
“The acquisition of Viessmann Climate Solutions is a game-changing opportunity,” said Carrier Chairman & CEO David Gitlin. “Climate change, sustainability requirements and geopolitical factors are driving an unprecedented energy transition in Europe. Accelerated by government regulations and incentives, the transition creates a significant, long-term growth opportunity.
“Viessmann Climate Solutions is uniquely positioned to capitalize on this opportunity with its premier brand, highly differentiated distribution channel and innovative product offerings. With 70% of its business consisting of heat pumps and related accessories, solar PV, batteries and services, Viessmann Climate Solutions is a critical leader in Europe’s energy transition. We look forward to welcoming its 11,000 team members to the Carrier family and Max Viessmann, CEO of Viessmann to the Carrier Board of Directors at closing, which is expected around the end of 2023.
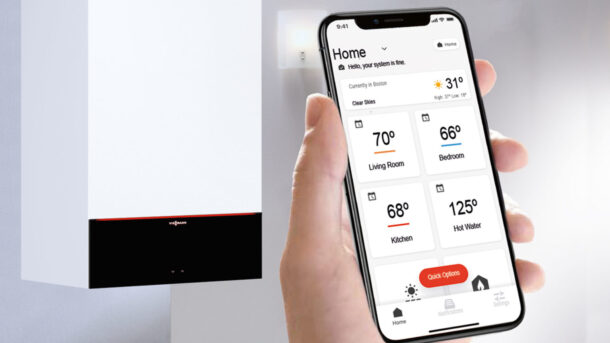
But a recent announcement from Viessmann found on LinkedIn read, “the new transatlantic partnership underlines the importance of international, cross-border collaboration in the fight against global climate change. Both companies are fully committed to take more responsibility for a sustainable energy transition in the building sector, focusing on our purposes: Viessmann Group’s purpose is to co-create living spaces for generations to come. Carrier’s vision is to create solutions that matter for people and our planet. We both regard the climate goals in North America and Europe as a once-in-a-century opportunity to make a positive impact, by actively shaping sustainable climate and energy solutions for future generations.
“The Viessmann Group will continue to remain an independent family business in full ownership of the Viessmann entrepreneurial family. Today, the Viessmann Group—excluding its Climate Solutions business area—generates a total revenue of EUR 1 billion in sales—including non-consolidated entities—with around 4,000 employees. Looking ahead, the clear goal and ambition of the Viessmann Group is to grow to a size that is larger than the Climate Solutions business area today, latest by the end of the decade.”

How does this affect contractors? The Hub’s Eric Aune, who is an ardent Viessmann installer, was sent this message: By combining Viessmann Climate Solutions and Carrier, we are co-creating one of the leading climate solutions companies in the world. Through the combination of both companies, we are forming a resilient, fast-growing innovation leader in a highly competitive market environment. All partners and customers of Viessmann Climate Solutions will significantly benefit from this new partnership:
- Viessmann Climate Solutions’ premium integrated offering will be complemented by electrified products and services from Carrier and its sub brands (heat pumps, battery storages, cooling and ventilation solutions as well as after-sales-services, digital and value-added solutions). This will lead to a wider product range for you.
- Viessmann Climate Solutions will get better access to suppliers via the global network of Carrier, especially its subsidiary Toshiba Carrier Corporation in Asia. This will lead to a faster delivery for you, in the long run. Thereby, you can significantly shorten your time to installation completion—a decisive component for the decarbonization of the building stock both in Europe and beyond.
- The iconic brand of Viessmann will be continued. All your respective contact persons at Viessmann will remain in charge. The Climate Solutions Executive Board and leadership team of Viessmann Climate Solutions, led by CEO Thomas Heim will continue to run the business. Viessmann Climate Solutions will become a major driver of Carrier’s growth strategy in Europe. Its headquarters will remain in Allendorf, Germany. The Viessmann Group will become one of the largest shareholders in Carrier. Consequently, Viessmann Group CEO Max Viessmann will become a new member of the Board of Directors of Carrier.
Meanwhile, according to an industry insider close to Mechanical Hub, Putin’s iron grip on the fuel supply in Europe could be a contributing factor to sell now. And, will Viessmann alter its path to market? One observer asked, “Will it be through the DCNE wholesale network?” We will see how things shake out in the next few weeks to months.
PEX Power
On the piping side, there have been tremors of a major shake-up in the PEX world. But all for naught, it turns out. Mechanical Hub has learned that Belgian company Aliaxis, a manufacturer of advanced fluid management solutions—with IPEX already a part of the company—had approached Uponor in its interest to sell. According to information acquired by Mechanical Hub, Aliaxis had announced a non-binding intention to make a tender offer to acquire all shares in Uponor.
Finland’s Uponor said on Wednesday (4/26/23), it rejected an unsolicited offer from Belgian rival Aliaxis, adding that the suggested price of 25 euros per share did not reflect the company’s value and long-term prospects.
According to Reuters and from sources within Uponor, the company’s board unanimously rejected the offer, but said it would consider any further proposals made by Aliaxis or any other party, if it was in the best interest of its shareholders.
Aliaxis last Monday made a $2 billion unsolicited offer to buy Uponor, seeking to form a global water management group, and the following Monday raised its stake in the Finnish company to 10.6%.
Oras Invest, Uponor’s largest shareholder with about 25.7% of the company’s shares, said on the day Aliaxis made its unsolicited offer that it had no intention of accepting it.
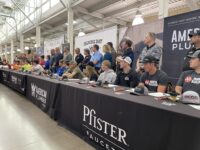
Last week, the Mechanical Hub Team was onsite to visit the Iowa Build My Future event, where 5,500 kids from across the state were bussed to experience the hands-on trade job fair. Here is a video that accurately describes the event. https://youtu.be/rWG8JLM07k4 Read more
Last week, the Mechanical Hub Team was onsite to visit the Iowa Build My Future event, where 5,500 kids from across the state were bussed to experience the hands-on trade job fair. Here is a video that accurately describes the event.
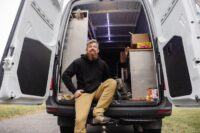
The past few years have been good for contracting businesses, barring component availability and skilled labor woes. For anyone in the trades, operating a plumbing and mechanical company profitably looks different today than it did 20 years ago, but there are still plenty of similarities. Joe Tull, 36, founded Straight Plumbing, LLC seven years ago Read more
The past few years have been good for contracting businesses, barring component availability and skilled labor woes. For anyone in the trades, operating a plumbing and mechanical company profitably looks different today than it did 20 years ago, but there are still plenty of similarities.
Joe Tull, 36, founded Straight Plumbing, LLC seven years ago, and feels as though he’s settled into a sweet spot. Right now, that includes running two trucks and focusing on Maryland’s Hartford County and northern Baltimore County. The company used to be bigger, but not necessarily better, according to Tull.
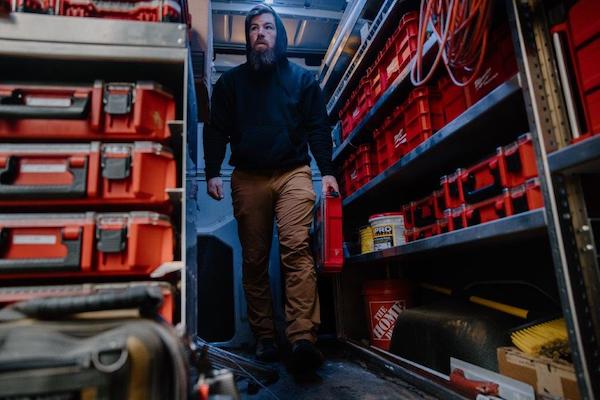
Roughly 30 percent of Straight Plumbing & Heating’s work is hydronic heat. The rest is residential and commercial plumbing service.
“I’ve always preferred quality over quantity,” he explained. “When I had more employees, I spent a lot of time going behind them and fixing their mistakes or shortcuts. Right now I have a fantastic apprentice, Robert Howard, who’s been with me four years. He’s always respected me and done things my way, which simply means not cutting corners. I’d hire 20 like him, if I could find them.”
Joe grew up working for his father’s plumbing company, but after a while, the two Tulls couldn’t see eye to eye. So Joe left and spent several years on the plumbing service crew for a large company before hanging out his own shingle in Jarrettsville, Md.
Specialization
“Specialization gives the people . . . the opportunity to go further in any direction of study than any other human has gone before.” – Ryan North
“Service is what I knew best, and what I could build a reputation on most rapidly,” said Tull. “Service work also provides the greatest opportunity to solve people’s problems. The new construction side of the business is more volatile. So I specialized in plumbing service, and as soon as I was up and running, I dug into hydronics to expand our offering.”
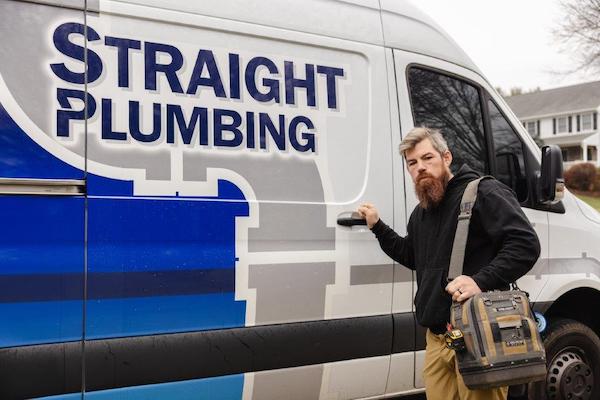
Joe Tull founded Straight Plumbing, LLC in 2016, after working for his family’s company and several other plumbing firms in the area.
Today, 30 percent of Straight P&H’s work is hydronic heat. The rest is plumbing service, both residential and commercial. Due to the rural nature of his territory and the presence of hard and harsh water, many of their service calls involve well pumps and water conditioning. A deep understanding of water quality has infinity improved Tull’s hydronic and plumbing work.
Forging relationships
“Technology does not run an enterprise, relationships do.” – Patricia Fripp
Tull learned early in his career that relationships are critical to the success of a business. In addition to learning from his father, he had mentors at supply houses, rep firms and within his social circle.
“I had a lot to learn when I first started installing boilers” said Tull. “Jim Bull, at Thomas Somerville became a mentor. He has a wide range of heating knowledge and was always generous with that information. He’d even stop at my jobs in the evening and set me straight if I was in a bind.”
Relationships are as important to Tull today as they were then, when he was still building his portfolio of experience.
“I try to be an information sponge and do my best to become an asset to the people who add value to my life,” said Tull. “Over the past three years, I’ve worked closely with the reps at ROI Marketing, specifically Dan Byrne, district manager, and Dave Raabe, sales manager. Those guys are never more than a phone call away.”
Byrne has known Tull for more than 20 years, but has only been his hydronic rep for about three years, after helping Straight P&H sort out some technical issues on a particularly challenging project. Tull installs their line of U.S. Boiler Company condensing and cast iron boilers, ComfortPro PEX, State water heaters and Webstone valves. Some of that equipment comes through Jordan Mitchell, at Northeastern Supply, while some is sourced at other supply houses throughout the area.
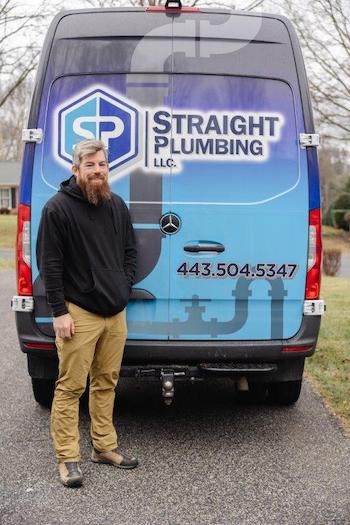
Straight Plumbing & Heating used to be a larger company, but Tull intentionally reduced it to two trucks for the sake of quality and consistently.
“Dave and Dan rock,” said Tull. “Their support, and the help I’ve received from the factory tech support at U.S. Boiler has been outstanding. I’ve used other boiler brands with less success and non-existent customer service.”
Byrne and Raabe visit Tull’s jobsites a dozen times or so each year, often on the front end, to provide sizing assistance, system concepts, etc.
“What I observed when I first met Joe was a young guy that wanted to install stuff properly,” said Raabe. “He’s very talented and his work is extremely professional, yet he’s humble and not afraid to ask for help.”
“I wish all our customers were like Joe,” added Byrne. “He takes real pride in his work.”
Referral marketing
“Courteous treatment will make a customer a walking advertisement.”
– James Cash Penney
“I left my previous job because I saw customers being taken advantage of,” Tull said. “I don’t hard-sell anyone. I present their options along with fair pricing and let them decide what they prefer. I want customers for life. If I’m fair and I do the job to the best of my ability, my customers become my salesforce.”
Tull doesn’t just talk the talk. His 38 five-star reviews on Facebook are proof enough. One review states, “Joe came to my house and fixed me up. After I got estimates from other plumbers that were way too expensive, Joe fixed my old water treatment system without pushing me to buy a new one. He simply stated ‘Please think of me when you decide to upgrade.’ And you bet your butt I will.”
Create value
“You don’t get paid for the hour. You get paid for the value you bring to the hour.” – Jim Rohn
Straight Plumbing and Heating creates value as well as anyone in the business. Homeowner Steve Shelley learned this when he first hired Tull to solve some minor plumbing issues. Years later, when it came time to replace the home’s oil-fired boiler, Joe was his first and only call.
“Joe is very responsive, knowledgeable and thorough,” said Shelley. “He doesn’t try to oversell, he’s happy to answer questions, and he’s never in a rush to get things done. I didn’t have to think twice about hiring him to convert our home from oil to propane, which we did mainly for the energy savings.”
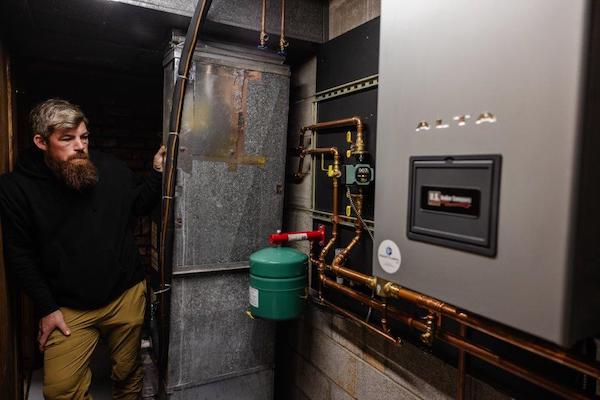
The combi boiler system Tull installed heats the home through a hydronic air handler, while also providing more hot water than the homeowner had ever had in the past.
The home is heated by hot water fan coils, and the existing boiler used to provide DHW through a 40-gallon indirect tank. Shelley estimates that the unit burned 800 gallons of oil each year, or roughly $3,200.
Tull buried a large propane tank in the yard, replaced the existing unit with a 200 MBH Alta Combi boiler, and sidewall vented the new unit.
The retrofit took place in June last year, giving Shelley nearly a year to calculate the energy savings that Straight Plumbing and Heating had provided.
“We used 400 gallons of propane over the winter, and I’m sure we’ve consumed a little more through the fall and spring for hot water,” he Shelley. “With LP at $2.00 per gallon, we’re saving somewhere around $2,000 per year.”
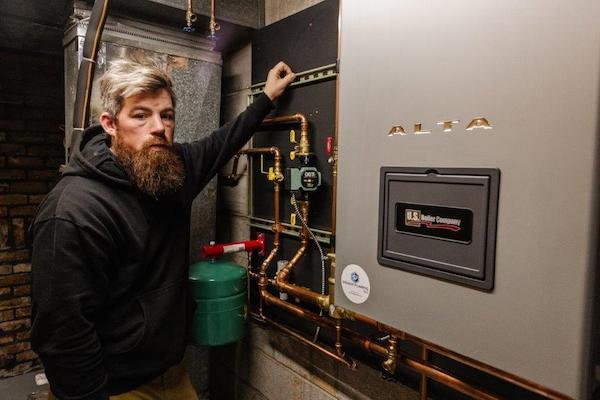
Tull replaced an oil-fired boiler with a new Alta condensing combi boiler for an annual savings of $2,000.
Shelley also noted that the family used to run out of DHW quickly. Now they can shower as long as they want and run multiple taps.
“We have all the hot water we need,” Shelley explained. “We can’t smell oil in the basement anymore, and we don’t hear the boiler start up like we used to.”
“We have about a dozen Alta boilers in the field,” said Tull. “They work very well on LP. Most of the installations in Hartford County are on propane. The Alta is also easy to clean, and access is fantastic because the side panels are removable.”
There’s another reason that Tull installs the Alta. Much like other models in the U.S. Boiler Company lineup, the Alta is available at a variety of local supply houses, including Northeastern Supply, Thomas Somerville and R.E. Michel.
“When it’s cold and a customer needs heat, I can’t come up empty-handed on parts and product,” said Tull. “Having equipment that’s readily available is extremely important.”
Overcoming challenges
“A challenge only becomes an obstacle when you bow to it.” – Ray Davis.
Last heating season, Straight Plumbing and Heating installed 35 boilers. This year, only 20. He suspects the economy has something to do with that, but he’s certain there’s another reason.
According to Tull, many big HVAC companies are pushing homeowners toward inexpensive heat pumps. There are lots of “house flippers” in his territory, as well. Typically, flippers install the cheapest heat pump on the market.
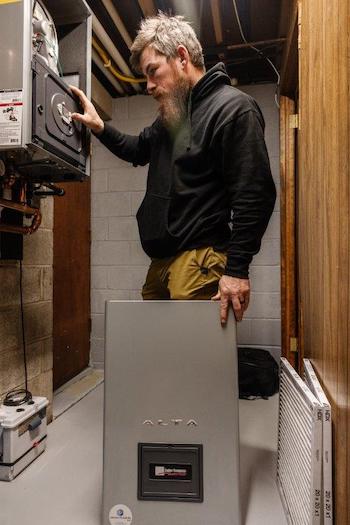
Straight Plumbing & Heating has a dozen Alta boilers in the field, and he’s found them to be reliable and very easy to work.
“I’m not talking about high-efficiency, low-ambient temperature systems,” he said. “I mean the cheap, undersized unitary systems. I’ve had homeowners call me after buying a house with a new heat pump, asking if I can install ‘a real heating system.’ Once winter hits, they’re uncomfortable and their electric bill spikes because the units constantly run on emergency heat.”
It’s hard to sell a premium system against a budget option when the customer doesn’t know the difference before signing the contract.
“I know it will all come full circle,” said Tull. “You only make that mistake once. If I was trying to grow rapidly, I’d be concerned about it, but I’m happy with where the company is. It’ll grow gradually. We’ll continue solving harsh water problems and creating extremely comfortable heating systems. If we do that and remain transparent with our customers, the company will continue to do well.”
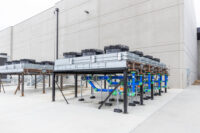
Businesses that entrust their data storage to the state-of-the art Novva data center outside of Salt Lake City will benefit from a location chosen for its many data center-friendly attributes. The area offers outstanding connectivity, low power costs, and a central-western site with easy access to a major international airport. In addition, the site’s climate Read more
Businesses that entrust their data storage to the state-of-the art Novva data center outside of Salt Lake City will benefit from a location chosen for its many data center-friendly attributes. The area offers outstanding connectivity, low power costs, and a central-western site with easy access to a major international airport. In addition, the site’s climate and 5,000-ft. altitude allow for many hours of free cooling annually.
Just as important to Novva’s clients, the new data center has a low disaster risk. The area is not prone to earthquakes, floods, or adverse weather events such as hurricanes.

And finally, for the additional peace-of-mind that makes this data center truly start-of-the-art, the cooling system for the computer servers boasts Aquatherm PP-RCT piping that will provide virtually leak-free service for decades to come. The Aquatherm piping will never scale or corrode, and the cooling water flow will remain unchanged throughout the anticipated 50-year lifespan of the pipe. All of this data adds up to a win for Novva and its clients.
The “hyperscale” data center in Salt Lake City will be Novva’s flagship data center. The 100-acre Utah campus is planned to ultimately include more than 1.5 million square feet of data center space and will accommodate 250kW to 30 MW clients. The construction is taking place in four phases. The first phase, which includes a 300,000-sq.-ft. data center, a 120MW substation and an 80,000-sq.-ft. headquarters office building for Novva, was completed in December 2021.
Beating the Heat
Reliable cooling systems are an essential component of modern data centers. Computer servers are notorious for generating heat—and heat is notorious for being an enemy of computer servers.
The decision to install Aquatherm pipe as part of the new data center’s cooling system was driven by Steven Boyce, vice-president of infrastructure and design at Novva Data Centers. Boyce has been involved in the IT and data center space for more than 20 years, and has worked on multiple successful startups during that time.
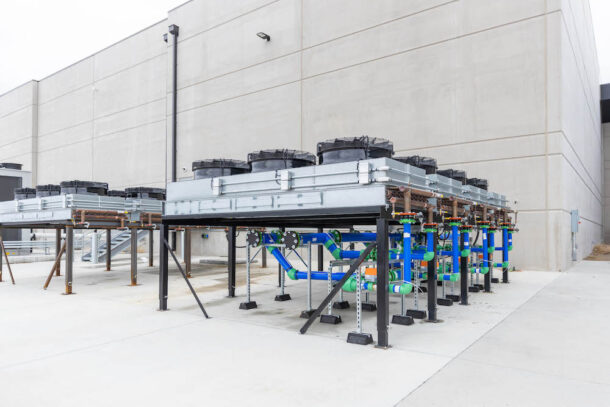
When I first learned about Aquatherm, it was a no-brainer,” Boyce said. “I had been using steel pipes in my builds, which would corrode and rust, and in turn, fill my equipment with sediment and pieces of rust. Efficiencies would be diminished, and the pipes would eventually have to be replaced. Aquatherm’s total installed costs are lower, and their warranty is something that no steel vendor could match.”
Once the decision was made to trust the cooling system’s performance to Aquatherm pipe, Novva turned to the Salt Lake City branch of Harris Mechanical for the installation.
Harris had experience installing Aquatherm pipe, although the Novva data center represented the company’s largest data center Aquatherm installation to date. To handle the first phase of the Novva system, Harris installed a BASX custom chiller package (which included the pumps and controls), the Aquatherm pipe for computer system cooling, and the comfort system piping and plumbing. The piping work for phase 1 began in mid-May 2021 and was completed in October 2021. The system was commissioned and turned over to the owner in December 2021.
Fast and Furious
Jeff Reading, operations manager, construction, Harris Mechanical, explained that the Novva data center started out as a core and shell project, with the office built first and the data hall scheduled to be built out later. However, as anyone in construction work knows, it’s always best to expect the unexpected.
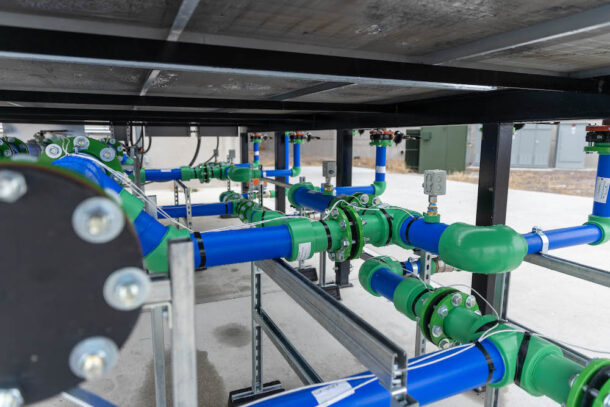
“We finished the core and shell construction in May 2021, and the data hall was right on its heels as a change order to the original project. So it came at us fast and furious,” Reading said. “The original plan was to complete the entire chilled water loop, which runs underneath the floor on both sides of the building. However, it was decided to install the piping in stages as the facility is built out. So far we have installed about half of the piping that will ultimately go in there.”
The installation to date has included 4,418 ft of Aquatherm Blue Pipe SDR 17.6. The main system piping is 10-in., and the takeoffs are 4-in.
Training Professionals
To handle such a large project. Harris Mechanical sent several installers to Aquatherm’s U.S. headquarters in nearby Lindon, UT, for training.
Having Aquatherm-trained technicians opens up new opportunities for HVAC and plumbing companies. The company gains differentiation in the market, and enjoys the time- and labor-savings associated with installing polypropylene pipe.
Aquatherm training is the most intensive, comprehensive training in the polypropylene piping industry. Attendees receive both classroom training and hands-on training with multiple fusion machines, and must pass a rigorous test using all the fusion tools correctly.
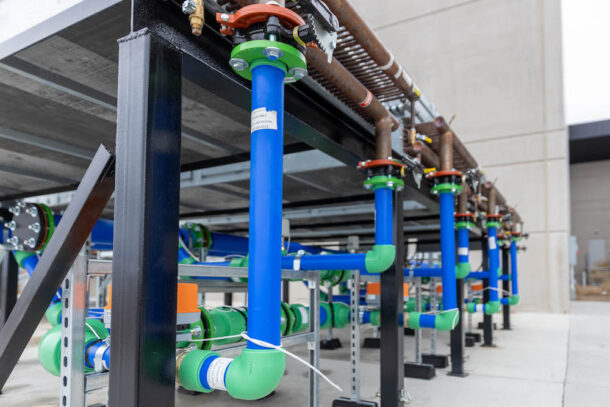
After the training, Harris completed the installation using McElroy fusion tools and a combination of socket fusion for the 4-in. pipe and butt fusion for the 10-in. pipe. The system runs at a low pressure (35 to 45 psi); the cooling system supply water runs at 55°F and returns to the chiller at about 60°F.
According to Reading, Harris Mechanical had a good experience with Aquatherm piping at the Novva data center, and the ease of installation compared to steel pipe helped Harris stay ahead of the project’s tight schedule.
“It was a smooth process,” he said. “We definitely gained experience and confidence with the pipe throughout the project, and our installers became accustomed to ‘leapfrogging’ and working with more than one [fusion] machine at a time.”
A Smooth Path
The underfloor piping system presented one of the major installation challenges at this project. The floor is raised 5-ft., and all of the facility’s piping, wiring, HVAC ducting, and utilities run through the raised space.
Aquatherm’s building information modeling (BIM) capabilities and Scan-to-Fab service helped ensure that the installation went smoothly by preventing underfloor conflicts and collisions.
“Using 3D BIM and Revit really helped with coordinating this installation,” said Autumn Turner, a fabrication drafter at Aquatherm. “Not only was all the HVAC and plumbing under the floor, there were floor stands every square foot. It took a lot of coordination to avoid all those potential obstacles.”
Turner noted that careful coordination enhanced the already-fast heat-fusion installation of Aquatherm pipe, and that less time and money spent on welders is a major benefit of choosing Aquatherm.
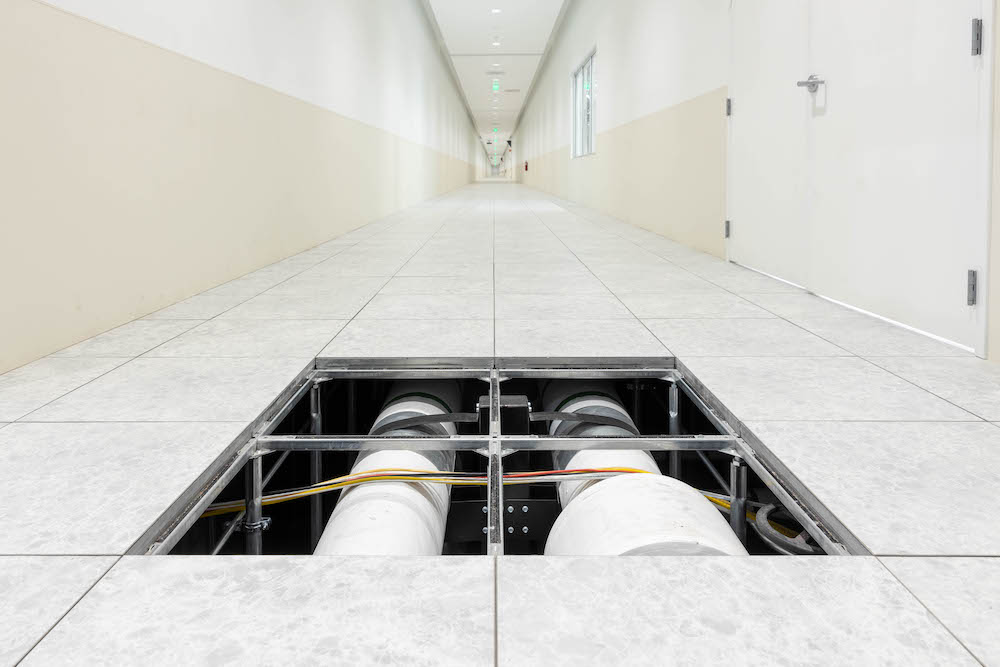
“Aquatherm is just easier work with than steel pipe,” she said. “It takes a lot less time to weld, and when you add in the BIM support and drafting it was easier for the installers to get situated into the floor and navigate the space.”
Turner added that Aquatherm’s BIM and Revit capabilities will ensure the future installation phases of the massive project also go smoothly.
Rhett Coles, Aquatherm’s fabrication drafting/scan-to-fab manager, said that Aquatherm’s Scan-to-Fab service and in-house fabrication makes any piping installation easier and smoother. Spools can be custom made in any size or configuration and shipped to the jobsite ready to install. In addition, any pieces fabricated by Aquatherm are covered by a comprehensive 10-year warranty.
“In the case of the Novva data center, we were in constant communication with Steven Boyce and the owner’s group,” Coles said. “We were not providing a cookie cutter system to them. They would tell us whatever they wanted or needed and we would work directly with them to help them fully accomplish their goals.”
A reliable, leak-free piping system with a long life span, and a smooth installation in any space, including challenging underfloor designs? The data are in: Aquatherm is the right choice for data centers.