Artificial Intelligence (AI), digital twin, VR & AR, hydrogen fuel—all technologies pointing to the future of our industry. It’s really no wonder that the circulator industry—with the addition of Bluetooth-enabled technology and accompanying apps, for example—is moving into the 21st century as well. Couple that with US DOE mandates for efficiency, and you have the Read more
Featured Articles
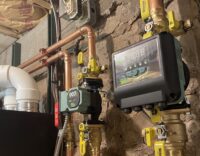
Artificial Intelligence (AI), digital twin, VR & AR, hydrogen fuel—all technologies pointing to the future of our industry. It’s really no wonder that the circulator industry—with the addition of Bluetooth-enabled technology and accompanying apps, for example—is moving into the 21st century as well. Couple that with US DOE mandates for efficiency, and you have the perfect storm of advancement. According to Taco’s John Barba, Director, Sales, Training, North America, the U.S. Department of Energy is tentatively setting mid-2025 as the date that mandated minimum circulator efficiency standards will be implemented. What that means on the specified date, manufacturers like Taco, Grundfos, Xylem, and others will no longer be able to manufacture and sell circulators that don’t meet a minimum efficiency standard.
“That doesn’t necessarily mean ECM technology, but as of right now Electronically Commutated Motor (ECM) is the only technology we have available that meets those standards; ECM is undoubtedly the direction our industry is going,” says Barba.
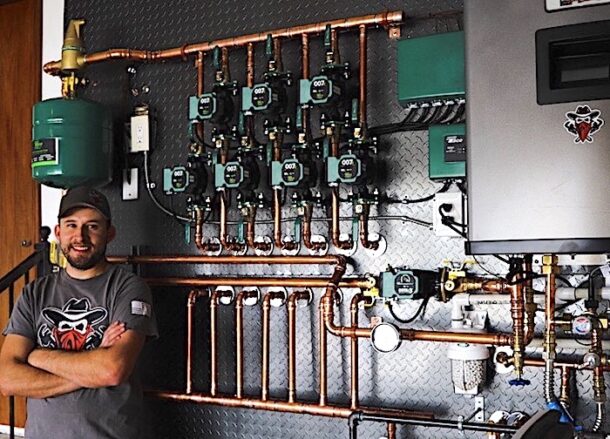
Keefer Rader, Outlaw Mechanical
According to Keefer Rader, owner, Outlaw Mechanical, Albuquerque, N.M., ECM will be the future as standard motor technology will no longer meet energy efficiency criteria. “I don’t know if Bluetooth technology will be the future, but it sure is nice to be able to monitor the equipment. I think Bluetooth and Wi-Fi technology will be a must for building management system (BMS) in our state.”
But by moving pumps and circulators into the “digital age,” some would ask, “why bother?” and “if it ain’t broke, why fix it?” “That’s an excellent question,” says Barba. “Part of me thinks back to something Henry Ford said a long, long time ago. ‘If you keep doing what you’ve been doing, you’ll keep getting what you’ve been getting.’ That’s the flipside to ‘If it ain’t broke, don’t fix it.’ The ‘if it ain’t broke’ idea is hard to argue with, but that doesn’t mean things can’t be made better, more efficient and more effective. After all, if good enough was truly good enough, we’d still be dealing with coal boilers and fireplaces. Those weren’t broke, either,” suggests Barba.
According to Barba, the fundamental truth is that building a hydronic system, putting pipe together so the water stays on the inside, connecting it to a boiler and having it make fire so people don’t freeze to death isn’t all that hard to do. A reasonably competent handyman could probably pull it off. But what makes a professional a professional is his or her ability to not only keep people from freezing to death, but to also create a system where the whole is greater than the sum of the parts; where the whole is designed to operate at peak efficiency and provide years of trouble-free operation. Variable-speed ECM circulators, when properly programmed and installed, are great tools to help achieve that goal.
“Of course, Henry Ford also said that he saw no advantage in new clocks” says Barba. “They run no faster than the ones made 100 years ago.” But again, it’s important to remember what we’re trying to accomplish. “Heck, cast iron boilers aren’t ‘broke,’ and they’re certainly less expensive, but modulating condensing boilers are more common now than ever before in residential hydronics. They’ve become ‘standard.’
“However, it makes zero sense to install a high-efficiency modulating condensing boiler and then not installing the outdoor sensor or enabling the outdoor reset. Even if the boiler has to run up to 180 degrees for fin-tube baseboard, it can still modulate and reset the water temperature as it gets warmer outside. Not doing so is basically wasting your customer’s money. “
By the same token, says Barba, all of the components you install with that modulating-condensing boiler—or even a cast-iron boiler, for that matter—should be purpose-chosen, meaning they are specifically selected in order to enhance the overall performance of the system—to make the whole greater than the sum of the parts.
“One thing variable speed technology has taught the industry is that the circulator plays a bigger role in overall system efficiency than we’ve ever given it credit for,” says Barba. “Sure, the boiler makes the heat, and sure, the heat emitters deliver the heat. But it’s the circulator that facilitates the journey. If we are overpumping, and even with ECM technology, we’re almost always overpumping, we’re limiting the overall performance and efficiency of the system, not enhancing it. A typical three-speed, standard efficiency circulator is almost always set to high speed or, as we like to call it, ‘contractor no-callback mode.’
“On the one hand, unless there’s velocity noise, there’s no immediate downside to doing so. However, pumping 5 gallons per minute through a zone that only needs 2 gallons per minute under design conditions means you’re pumping at a rate 2.5 times more than is required. In a perfect world, you’d have a 20-degree Delta-T under design conditions, but in this example, the best Delta-T you’ll ever see in that system is 8 degrees. That would mean with a mod-con boiler sending out 140-degree water on the coldest day of the year, the return water temperature would be about 132. We’re not condensing nearly as much as we could be, and we’re leaving an awful lot of efficiency on the table, but no one will complain about being cold.”
“Cavemen! I don’t understand why people are afraid of new things,” shouts Rader. “I’m a big proponent because I know Taco tests everything stringently so I know when it comes out of the box, I’m not likely to have an issue with it. I love having four circulators on my truck that I can typically adapt to any system and make it more efficient and work better. The double 0015e, 0018e, vt2218—this is my favorite, because people can see data in front of their face and understand the value—and 0026e.”
But Bluetooth?
As for Bluetooth technology and its associated app, it’s simply a way for an installer to make sure the ECM circulator he or she is using is, in fact, doing what he or she wants it to do. The myths and misinformation about ECM and variable speed technology that are common in our industry are astounding, says Barba. No, they do not size themselves and no, they do not always give you the right flow. What ECM and variable speed technology allows us to do is properly program a circulator so that it performs as close to what a system requires as possible. These things aren’t magic and they don’t “do the thinking for you,” or “take the thinking out of it.”
“You can’t just slap one of these things in, push a button and let it do the rest,” says Barba. “This isn’t the Hogwarts School of Hydronic Magic. ECM circulators don’t think and they aren’t magic. But what they are is obedient. They will do what you tell them to do – and the benefit of Bluetooth technology is it allows the installer to make sure a circulator—in Taco’s case the 0018e Delta-P technology circulator—operates as close to the actual system requirements as possible.”
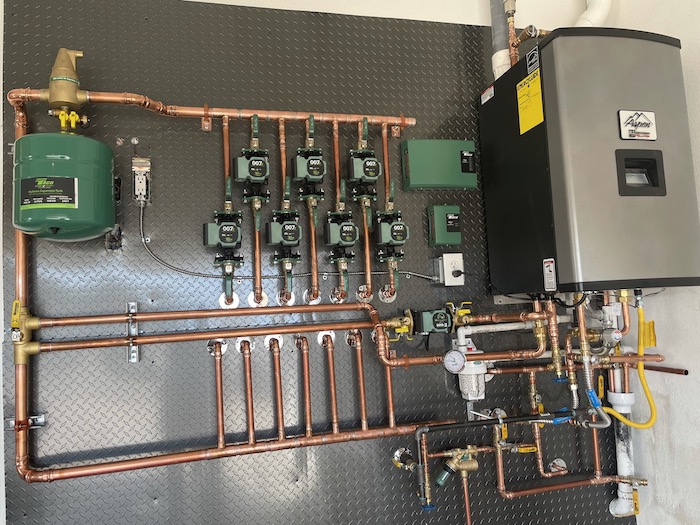
Additionally, residential hydronics has a chronic overpumping problem, continues Barba. Pick any residential hydronic system and chances are it’s WAY overpumped. Overpumping is one of those insidious problems—no one will ever complain about being cold, but over pumping means more GPM is being pumped through a zone or a system than it needs. When that happens, the system Delta-T is small and gets smaller as the outdoor temperature increases.
This isn’t supposed to happen and it’s not needed to make a system work, although you’ll hear people mistakenly make that claim. What a shrinking Delta-T does do is it sends warmer and warmer water back to the boiler. We don’t want that to happen at all with a modulating-condensing boiler, and we really don’t want it to happen with a cast iron boiler, either (as long as we’re above the condensing point). When that return water temperature is higher than necessary, boilers tend to short cycle and, in the case of a mod-con, it won’t “con” as much as it could. It’s almost impossible to quantify mathematically, but it’s reasonable and logical to presume that overall system efficiency (and fuel consumption) will suffer.
“And short-cycling doesn’t do any of the moving parts in a system any favors. It won’t take long for any key—and expensive—component in a mod-con boiler to fail prematurely. At that point, someone is left with some ’splaining to do,” says Barba.
Bluetooth technology has to be useful and hold value to the contractor, and that we’ll see about, says Barba. “What we’ve found in the five years we’ve had Bluetooth technology in the market is there are contractors who get the value right away, and others who question the value. That’s to be expected. When we show all of the capabilities of the circulator, show them how easy it is to set up the circulator to optimize system performance and—most importantly— what that optimization is important, we see more who see the value and fewer who question it,” says Barba.
“That said, we do see contractors who roll their eyes at the word ‘app’ and don’t want anything to do with it, and that’s fine. We have the VR 1816, which we’ve had since 2014, the 007e, which we’ve had since 2015, the 0015e3—which we’ve had since 2017 and the VT-2218, a Delta-T variable speed circulator that we’ve had since 2011. Different strokes, meet different folks.”
“I’ll tell you what I wish they put a small screen on the 0018. I really love this circulator because I can get real time data on my iPad and set a circulator to pretty much exactly what that zone needs,” says Rader. “I prefer to use them on zone pump systems. I also like to use them on the head scratcher systems so I can try to compile as much data as possible. A lot of times it becomes more of a tool than product.”
And beyond initial setup? “Initial setup isn’t just a throw-away item; it’s the most important element of using, and maximizing, variable speed circulators. And Bluetooth connectivity gives you stark visuals and really numbers of what it is you’re doing. As my co-trainer Dave Holdorf says, Bluetooth for the first time lets you see what’s actually happening inside the pipe. It’s real and it’s now knowable and quantifiable,” says Barba.
Added Costs?
Let’s face it, with new technology inevitably there’s going to be added costs. “There are added costs, but I have found when selling a new circulator—when I explain to the customer, the benefits of a properly sized circulator—that their buyback should be within a year. For instance, if I have a circulator that speeding up and slowing down based upon how many zones are opened or closed at that time, we are not wasting fuel. We are directing the heat at the proper speed to hit maximum efficiency,” says Rader.
People do ask all the time, “How do it sell this to my customer?” says Barba. There are two answers to that. The short one is if it’s a simple swap out—a new circulator for a dead one—it can simply be a matter of explaining these new circulators are much more electrically efficient than the standard models, use about half the electric and can make the system work better and more efficiently for the long haul. Often, that’s enough of an explanation.
If someone wants particular, the Hydraulics Institute has created labeling for ECM circulators that all of the major manufacturers have adopted, indicating relative efficiency ratings (the higher the number, the more efficient the circulator—although once you reach a certain point, the practical differences are minimal). By using a formula provided by the Hydraulics Institute, one can show how quickly the more efficient circulator will offset the higher purchase price— it’s usually within two, maybe three heating seasons.
If it’s a full boiler change out, the difference in price between a standard circulator or circulators compared to ECM circulators—in the overall picture of the job—isn’t huge and gives the contractor talking points as to why he or she has chosen specific circulators, and why it’s best for the system to do the job right. “I’ve had customers tell me that their customers aren’t asking for ECM technology, so there’s no market for them and besides, they’re too expensive. I’ll go with another Henry Ford quote: ‘If I’d asked people what they wanted, they’d have said ‘faster horses,’” says Barba.
Depending on where you live and work, Barba says, ECM circulators may actually be less expensive than standard efficiency circulators. Many states offer instant, at-the-counter rebates from utility companies to incentivize ECM adoption. It makes sense—if wider adoption of lower-wattage circulators takes place, that’s less of a load on the power grid. The utilities are simply buying efficiency—it’s no different than with light bulbs or other low-consumption appliances.
In non-rebate states, the comparative purchase cost is higher—anywhere from a little bit to a lot, depending on what you want for a particular job. We’ve had great success with the 007e and 0015e3—both variable speed Delta-P ECM circulators—that only have the features and operating parameters that people might need for a particular job. If you like 007s and want similar performance in an ECM circulator, the 007e is virtually identical in performance. The 0015e3 is a seamless transition from your typical 3-speed circulator and works great with zone valves or as a zone pump. The multi-feature, multi-function circulators offer more features, but that comes at a higher purchase price.
Ultimately, ECM, variable speed and Bluetooth technology isn’t a matter of making the water go round-and-round the pipes better, says Barba. It’s simply a matter of using the latest technology to make sure a key part of the system is doing its job to ensure that system is working as efficiently and effectively as possible, ensuring the system itself remains as trouble-free as possible for as long as possible, and that the customer is getting the most out of what they’re paying for. “We’re all consumers in one way or another, and none of us want to pay top dollar and then get only 80 percent of what we’re paying for.”
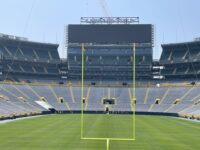
What was once the Frozen Tundra is now the Heated Tundra? This sneak peek into the latest from the Hub on the Road series that takes the team to contractor Tweet/Garot’s Wrightstown, Wis. prefab shop and a visit to the mechanical room at Lambeau Field to see how this venerable stadium keeps its visitors comfortable Read more
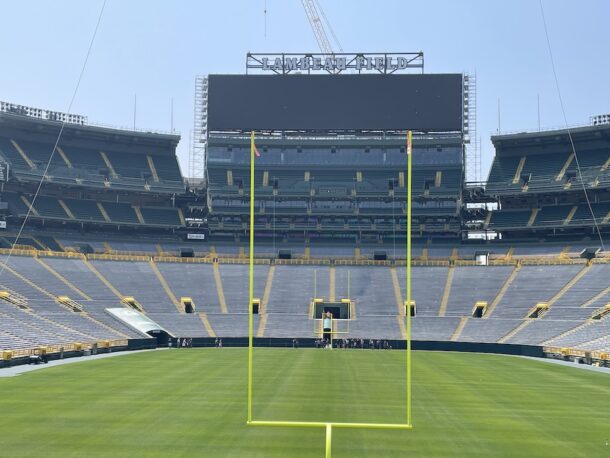
What was once the Frozen Tundra is now the Heated Tundra? This sneak peek into the latest from the Hub on the Road series that takes the team to contractor Tweet/Garot’s Wrightstown, Wis. prefab shop and a visit to the mechanical room at Lambeau Field to see how this venerable stadium keeps its visitors comfortable. Stay tuned for the full length Hub on the Road video coming soon.

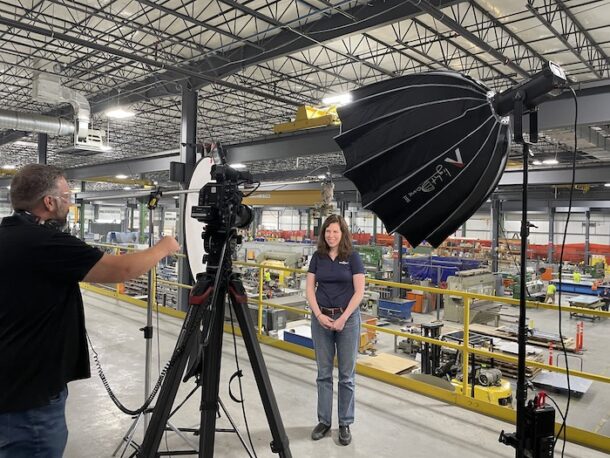
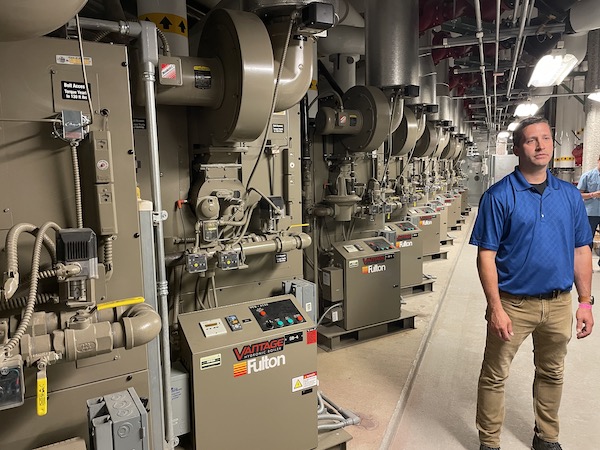
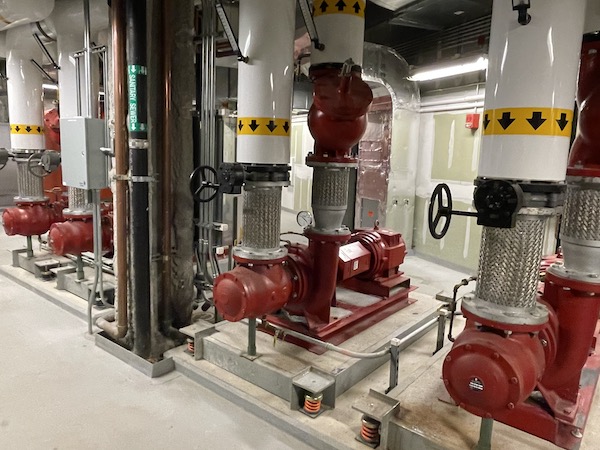
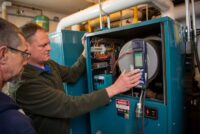
“Submarine duty taught me well.” Born in San Jose, Calif., Jeff Seveland thrived amid the lush warmth of central California. His father was a Navy man, and it seemed that every other kid in school grew up in a military household. So it only made sense that, shortly after completing high school, then two years Read more
“Submarine duty taught me well.”
Born in San Jose, Calif., Jeff Seveland thrived amid the lush warmth of central California. His father was a Navy man, and it seemed that every other kid in school grew up in a military household. So it only made sense that, shortly after completing high school, then two years of automotive tech school, he enlisted in the U. S. Navy.
Seveland spent five of his best years (’95 to ’99) as a machinist’s mate in the Navy. At 6’3”, he’s no easy fit for submarine duty, but that was the assignment.
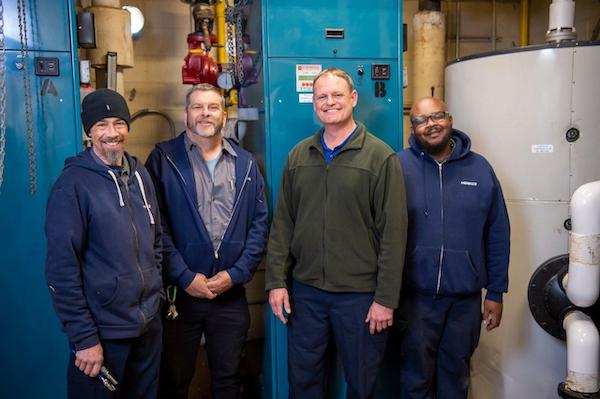
The team from l to r: Robert “Rob” Orsinger, HVAC mechanic; Ron Dotson, HVAC mechanic; Jeff Seveland, site supervisor; and Daniel Abbott, HVAC mechanic.
“As it turned out, Navy submarine duty was a great fit for me despite the dozens of head wounds I suffered hitting the bulkhead,” Seveland recalled, his hand involuntarily moving to his rub his scalp. His duty included seven months at sea in both South America and in the Mediterranean Sea.
“One thing’s for sure,” he quickly added. “Working on a submarine and its wide range of equipment was the perfect entry point, and training, for my jump into boiler work as a civilian. He explained that, on the sub as an “A-Ganger” (critical services crew), he serviced refrigeration equipment, oxygen generators, CO2 scrubbers, high pressure air and hydraulic systems, and a wide range of other mechanical and HVAC equipment. Choosing not to reenlist, Seveland was quickly hired as a building technology and commissioning technician with energy services companies.
Quantico-bound
It was while Seveland was in his early years in the energy services industry that he was assigned to Quantico, Va. where he commissioned and installed new commercial boilers. “Funny how things change: I expected automotive, but boilers won the decision. The jobs I took were a great fit for me, made to order for the type of work I like most and am good at.”
Quantico is headquarters for many training institutions, including the Marine Corps, the Naval Criminal Investigative Service and the FBI and DEA academies—though is best known as the largest Marine Corps base with 12,000 Marines.
“There was plenty of low pressure cast iron equipment, high pressure steam systems and an assortment of firetube and watertube boilers that needed attention at Quantico. “I guess that’s what they call job security,” he said, smiling.
Soon after, Seveland joined Framingham, Mass.-based Ameresco, a leading renewable energy and energy efficiency company offering Energy Savings Performance Contracts (ESPC) for federal agencies, funds used to provide energy solutions for public and private organizations.
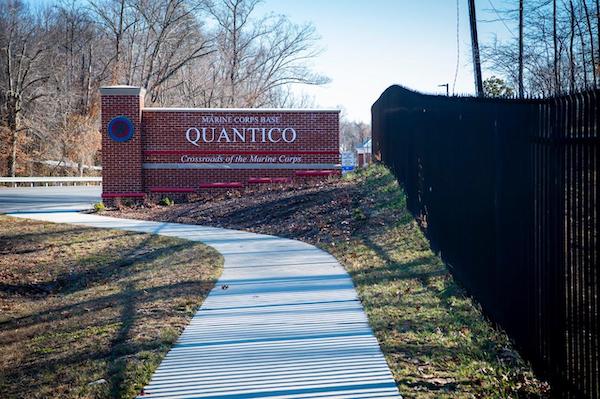
“Fortunately, after so many years of preparing for the perfect job—with training and experience that fit me like a glove—the move to Ameresco was the best fit of all.” Today, as Ameresco’s O&M Site Supervisor for Quantico, Seveland—now 19 years into fulfilling the company’s 25-year, $1.1 million annual contract there – directs the efforts of a team of employees on the base.
Today, Quantico includes 80+ Marine Corps buildings for a total of more than 1.2 million square feet. Through its ESPC contract, Ameresco provides predictive and preventive maintenance, condition monitoring, commissioning, repair and equipment replacement services. Boiler maintenance is an important facet of this, one that also includes maintenance and replacement of pumps and circulators, valves, controls and water treatment systems.
Building 15
Among the many Marine Corps facilities at Quantico, Building 15 is a typical residential quarters. According to Seveland, Building 15 is served by three boilers—two for space heating and one for domestic hot water (DHW).
“As is often the case, if one boiler failed, another could jump in to meet heat demand,” he said. “Even if the DHW boiler would go out, either one of the other space heat boilers could be adjusted for service.
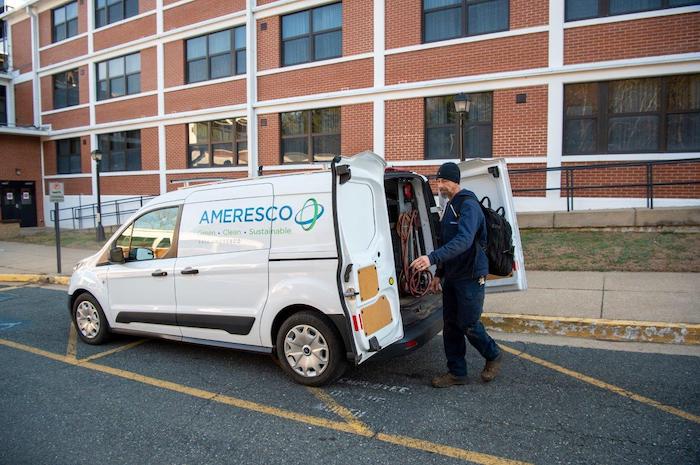
At the entrance to Bldg. 15, Orsinger gets tools for the monthly preventive maintenance.
“All three boilers have served the facility well since their installation in 2003, so we plan to replace the three units soon, preventively,” he added. Building 15, he explained, consists of three floors, including the basement and rooftop levels, 80,816 square feet, and 114 residential rooms, each with its own bathroom, and many other common area bathrooms.
With so many Marines on base, it doesn’t take a military strategist to understand the need for many residential buildings at Quantico. Banish from your mind any recollection of WWII-type boot camp barracks. The Marines on this base have earned the right to a good night’s sleep in real beds, hot meals, and bathrooms with plentiful hot water.
Boiler of Preference
“The provision of space heat and domestic hot water is our key focus at Quantico,” added Seveland. “With so many large boilers and volume water heaters on base, we know a thing or two installing, maintaining and servicing hydronic heating systems.”
Ameresco teams, including Seveland’s, work to find the most innovative and best fit equipment and technology for each project. They found the best-fit for installations at Quantico to be Thermal Solutions’ Evolution boiler. “We were first introduced to these systems back in 2006.” The boiler he refers to is a copper fin-tube constructed, with water-backed tube sheets and maintenance-free burner.
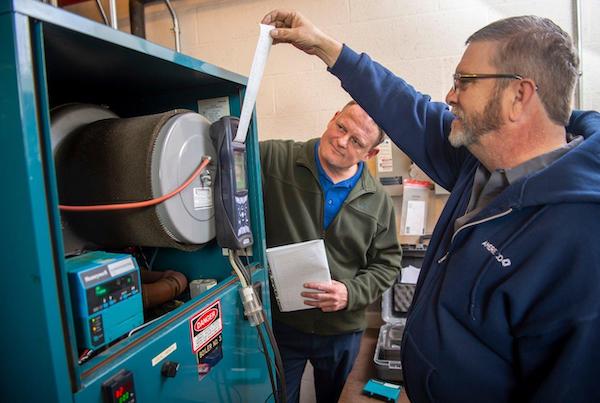
Ron Dotson and Jeff Seveland perform monthly combustion analysis and review data. Says Seveland, “We collect printouts and put them in our annual measurement and verification reports.”
The Evolution boiler’s burner features a large surface area and lower flux that allows for high heat transfer and more uniform heating, extending the life of its copper tubes. A sturdy cast-aluminum blower assembly, fitted with a replaceable combustion air filter is used to keep the burner free of contaminants. The Evolution boiler can be operated with its jacket panels removed during inspection to avoid nuisance problems associated with pressurized compartments.
Ameresco Knows a Thing or Two
By design, the low NOx, modulating boiler’s ceramic radiant burner rarely requires inspection or maintenance. The non-condensing boiler’s (with 250, 500, 750, 1,000 or 2,000 MBH sizes) provide up to 87% efficiency.
Seveland explained that, at Ameresco, experts are on call 24/7/365. “There’s no real downtime. Sure, things tend to quiet down during the holidays, but because of our ongoing, routine maintenance and our familiarity with the equipment, we’re still on call.”
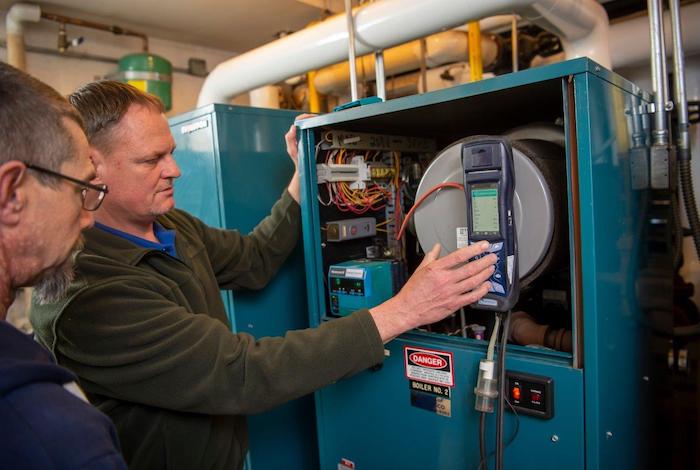
Rob Orsinger, HVAC Mechanic and Jeff Seveland, Site Supervisor, perform monthly combustion analysis and review data. Thermal Solutions recommends doing this annually, but Jeff Seveland’s AMERESCO team does them monthly.
“All of the equipment on base must be properly and consistently serviced and maintained,” he continued. “I take great pride in having a tight maintenance program. In addition to the routine boiler service work—and thanks to sophisticated building automation controls and fiber optics—we continuously monitor temperatures and pressure in all of Quantico’s buildings. If any temperature goes out of range, sensors alert us. We reply long before an alarm goes out, long before base personnel know of an active issue.”
Old and New
The existing storage tank at Building 15 is more than 50 years old, but is still doing its job well. A shell and tube heat exchanger works in concert with a 1,500-gallon storage tank. “It’s aging, but continues to perform well,” he said. “It dates back to the days when the base had a central heating plant that’s since been decommissioned. In this case, the old adage applies: If it ain’t broke, don’t fix it.
“We helped decentralize heating operations many years ago when it was recognized how much heat was being lost in the distribution of heat throughout the base,” added Seveland.
Seveland explained that, early in his tenure at Quantico, many of the boilers were large, cast iron, low-pressure behemoths, and some high-pressure steam boilers, with an assortment of firetube and water-tube boilers.
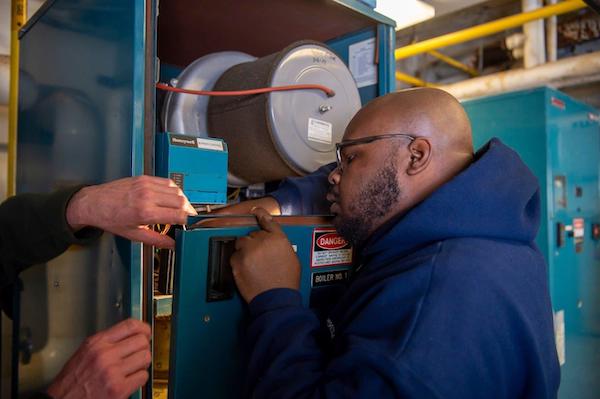
Daniel Abbott removes the Siemens RWF40 (compact universal boiler modulation control) from a boiler’s the front panel.
Many of the Evolution boilers are 1,500 MBH in capacity. Some of them contribute to both the space heating and DHW loads. Typically, for residential buildings there, Seveland and his crews pair-up- a heat exchanger to a boiler to heat domestic water that’s stored in large, insulated storage tanks.
All boilers installed during the big ESPC project at Quantico receive routine combustion efficiency testing by Ameresco pros, and monitoring of water quality. He added that, every 10 years, the Evolution boilers are taken apart—an easy task given their removable jacket design—serviced, cleaned, and reassembled. The service work includes a re-sealing of the combustion chamber.
“We’ve settled on a good recipe for reliable heat production at Quantico,” concluded Seveland. “After all—if you were responsible for keeping 12,000 Marines comfortable—wouldn’t you choose equipment you could rely on?”
Sidebar
Quantico—unique among military bases
Since its establishment in 1917, Quantico has been home to many of the nation’s most innovative, intelligent and patriotic men and women. It’s there, at the Crossroads of the Marine Corps, that vital concepts, training and equipment of the future are developed. Some of the most important techniques in warfighting were born there, including expeditionary warfare, for which the Marine Corps is best known.
In 1917, with the US just entering the largest war the world had ever known to date, the small town of Quantico, Virginia became the home of Marine Barracks Quantico, with a complement of 91 Marines and four officers. The barracks was a training center for recruits, and eventually grew into the nation’s largest Marine Corps base, having an excellent position near Washington DC.
In the 1920 and 1930s, Quantico was the center of the development of amphibious assault doctrine, and where some of the early amphibious vehicles were developed. This doctrine gave the USA an advantage in beach assaults over any of the Axis powers in World War Two.
Today the base has completely surrounded the town in almost every way, and in addition to Marine training, hosts the FBI Academy, FBI Lab, the FBI Hostage Rescue Team, the Army CID HQ, the Air Force Office of Special Investigations HQ, the Naval Criminal Investigative Service HQ, the DIA, and the DEA training facility. They are undoubtedly secure under Marine guard.
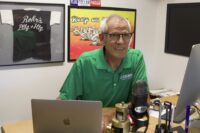
A Carlson-Holohan Industry Award of Excellence honoree, Bob “Hot Rod” Rohr travels across the country as a trainer for Caleffi North America, sharing his 40+ years’ of experience as a plumbing, radiant heat and renewable energy contractor, all while bringing his rubber-to-the-road experiences to life. Be honest, do what you say you will do. It’s that simple Read more
A Carlson-Holohan Industry Award of Excellence honoree, Bob “Hot Rod” Rohr travels across the country as a trainer for Caleffi North America, sharing his 40+ years’ of experience as a plumbing, radiant heat and renewable energy contractor, all while bringing his rubber-to-the-road experiences to life.
Be honest, do what you say you will do. It’s that simple, really.
If you bill your training as a technical event or class, make it that. Certainly, everyone of your attendees has an opinion, and that is a good thing. So at class end they get to decide if it checked the boxes they brought along to have filled. For example, a boiler piping presentation needs to have schematics of piping. I’d take it further and make the drawings as generic as possible.
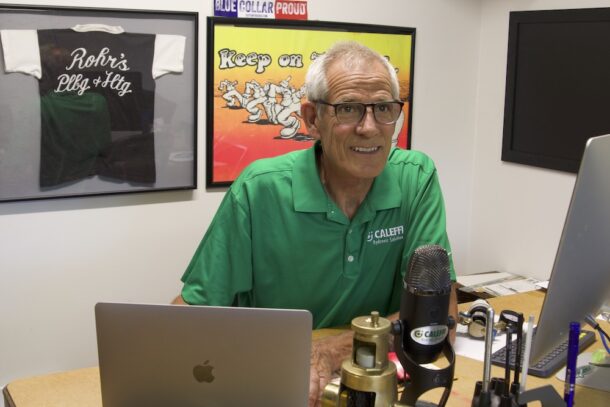
Fortunately I work for a manufacturer that publishes a very generic, non-biased trade journal. This makes for some excellent content for the classes.
But also be realistic in your expectations; not everyone in the room will be at the same level, and have the exact same expectations. Promote the event as basic, intermediate or advanced to help clear up the content. A trainer should, poll the room right off to get a feel of the experience level of the class. Ask occasionally if the info is meeting the needs or expectations. A trainer needs to be prepared to shift gears
Keep additional PPTs ready to go on your desktop if you need to raise or lower the content level, or bounce around to assure everyone gets something from their time commitment.
Know also that generous giveaways and CEU offerings will get some attendees that are there for the “goods” more so then the content. It’s easy to spot folks like that. They spend a lot of time looking at their phone.
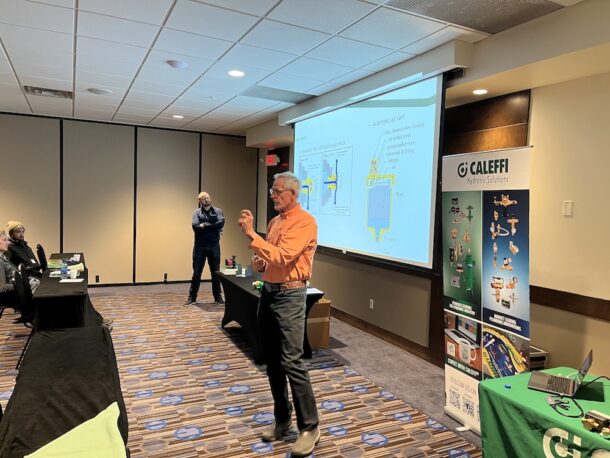
Someone is paying the trainer to get to the event and spend a few nights on the road. Expect the sponsor to have a product table, or some handouts that are brand specific. A few questions on a form or link to QR code to get feedback is helpful for trainers.
Timely topics help fill a room. Clever course names help people click on the training promos.
Like any trade, time on the job helps a trainer learn what works and what flops, so be prepared to change up your presentations or presentation style occasionally. A Toastmasters class can sharpen your presentation skills. Speak loud and clearly. Move around the room.
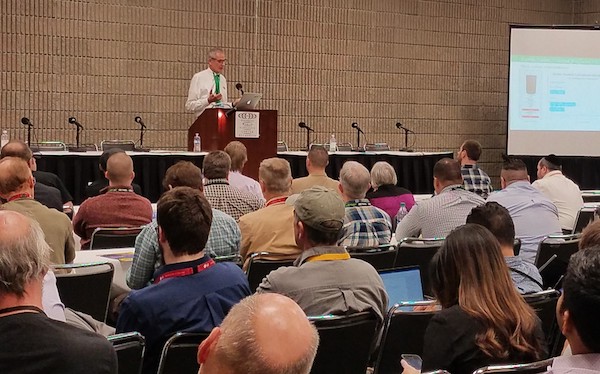
Watch big name, professionally-trained presenters. See how they move and observe the techniques they use to keep the room’s attention. Who is your favorite actor and why?
Got any tips or suggestions? Pass them along.
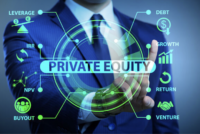
Over the past few years—wink, wink COVID—the industry has seen a rise in purchasing activity between plumbing and HVAC companies and private equity firms and other outside influences—coming in and gobbling up already successful contracting shops with a message of making them better. Sure, it’s a smart exit strategy as well for those looking to Read more
Over the past few years—wink, wink COVID—the industry has seen a rise in purchasing activity between plumbing and HVAC companies and private equity firms and other outside influences—coming in and gobbling up already successful contracting shops with a message of making them better. Sure, it’s a smart exit strategy as well for those looking to hang up the wrenches.
But why the flurry of activity now? “What we’ve seen from COVID is that the trades are pandemic-proof and to some extent recession proof. When money gets tight, consumers may hold off on that new car, going out to eat, but when that water heater goes out, it’s a necessity,” says Dan Foley, Foley Mechanical, Lorton, Va.
Foley continues, “Artificial Intelligence (AI) will never be able to take over this industry. You will always need someone to walk into someone’s home and make a repair, and that’s not easy to do. It’s the technician’s skill that AI cannot replace.”
According to Mike Prencavage Jr., president/owner, The Family Plumber, Los Alamitos, Calif., president, PHCC ORSB, director, PHCC National Business Development, “Working on margins is crucial for any business to succeed; however, in the plumbing industry most companies aren’t struggling with tight margins to turn a profit.”
As an example, Prencavage Jr. says restaurants and bars can stand to lose greatly if more than two ounces of alcohol is poured into any drink or if larger than accounted for portions of food are served on any plate. These private equity firms have seen that plumbing companies have a greater amount of sold labor income per invoice that can offset losses on jobs allowing for much wider margins to run a profitable business.
“Private equity firms are also looking to the future of renewable energy. With the electrification of the nation soon to be at every state’s doorstep, government grant funding has already become available to plumbing companies who are leading the way by installing energy efficient products. These grant programs. combined with the opportunity to capitalize on wider margins, are creating a buzz of interest from private equity groups to get more involved in the plumbing industry sector,” says Prencavage Jr.
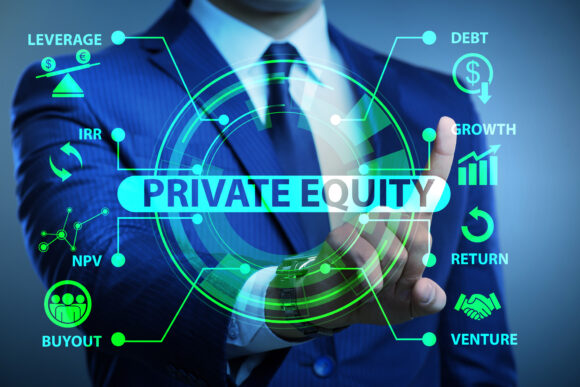
Speaking of grants, on a national level, the Infrastructure Bill and Inflation Reduction Act, are ripe for the taking, if eligible.
On the flipside, private equity firms offer contractors security, not only monetarily, but though the expansion of their reach and service offerings across their respective regions, expand evolving customer bases and refine overall strategic growth initiatives.
Just last month, Grove Mountain Partners—a private equity firm investing in lower, middle market home service companies and specialty business service companies—announced the sale of Unique Indoor Comfort Holdings LLC to Ace Hardware. Nate Kukla, CEO, and the entire management team, including the brand presidents, will continue to lead the company as it embarks on its next growth phase.
Grove Mountain brought together 12 independent service-providing businesses, beginning in June 2021, with the acquisition of three related companies: Moncrief Heating & Air, Unique Indoor Comfort of Philadelphia, and Werley Heating & Air. It added nine other companies in the Eastern region of the U.S., including Clay’s Climate Control, Detmer & Sons, Canella Heating & Air, A-Total Plumbing, All Phase Electrical, Dick Hill & Son, Carolina Custom, Rye Heating and Air, and Jackson Plumbing and Heating & Air.
“We are grateful for our partnership with Grove Mountain and are proud of what we have built and accomplished,” said Nate Kukla, CEO. “Now, we are excited to be part of the Ace team which will allow us to leverage their combined financial and operational capabilities and expertise. Since day one, Unique has been passionately dedicated to an employee-centric, high-integrity, and customer-focused culture. Ace shares in our mission and values and brings a plethora of resources to allow us to continue and grow the business.”
Also, this month, Auctus Capital Partners—a leading financial services and investment banking firm focused exclusively on creating value for the lower middle market, which specialize in merger and acquisition advisory, institutional private placements of debt and equity, financial restructuring, valuation, and strategic consulting—announced its role as exclusive advisor to The Precision Group and its affiliated entities, supporting the environmental and infrastructure services leader in completing a majority recapitalization by PowerVac, a Pillsman Partners LLC and Peninsula Capital Partners, LLC portfolio company.
The Precision Group is comprised of three separate yet complementary companies that serve a diverse array of commercial, industrial, and municipal customers. Founded in 1992, Precision Industrial Maintenance, Inc. provides environmental remediation, industrial cleaning services, hazardous and non-hazardous waste transport and disposal, and other industrial waste services. Martin Environmental Services, Inc. was acquired by Precision Group in 2002, adding new services in asbestos and lead abatement, and disposal services. Precision Trenchless, LLC was formed in 2013 to focus on environmentally-friendly pipe rehabilitation using less disruptive technologies, such as UV-Cured and other Cured-in-Place Pipe Lining (CIPP) methods, potable water line rehab to minimize air, water and soil pollution and support advanced monitoring services.
The group of companies operate as a unified provider of services to several broad regional markets with strong projected growth through 2026 — including the sewer and pipeline rehabilitation market with a compound annual growth rate (CAGR) of 4.6%, as well as trenchless pipe rehabilitation (4.8% CAGR), and liquid waste management (3.7% CAGR).
“Underpinned by significant government support for the repair of aging infrastructure, pipeline rehabilitation and wastewater management services are seeing record investment. In addition, an ever-growing awareness of ESG issues has been driving strong investor demand,” says Muhammed Azfar, CEO and managing partner, Auctus.
More to come on this topic.