With energy costs up more than 50% over the past year and a half and forecasters expecting those numbers to remain high through 2024, commercial building owners and engineers are seeking alternatives to effectively condition large spaces in a more energy-efficient manner. This challenge has opened the doors for a new cooling-panel technology that significantly Read more
Featured Articles
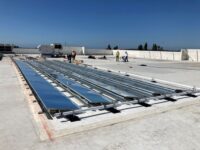
With energy costs up more than 50% over the past year and a half and forecasters expecting those numbers to remain high through 2024, commercial building owners and engineers are seeking alternatives to effectively condition large spaces in a more energy-efficient manner.
This challenge has opened the doors for a new cooling-panel technology that significantly decreases energy consumption and demand charges associated with cooling to maximize sustainability for higher-performing buildings.
The patented radiative cooling system essentially works opposite a solar panel system. Instead of harnessing energy from the sun, the cooling panels feature a multilayer film that reflects sunlight and emits infrared heat to the atmosphere, keeping the panels extremely cool — up to 15°F below the ambient temperature. A closed-loop hydronic piping system circulates a water/glycol mixture that brings warm water to the panels for cooling and then returns the cooled fluid back to the building’s existing HVAC system.
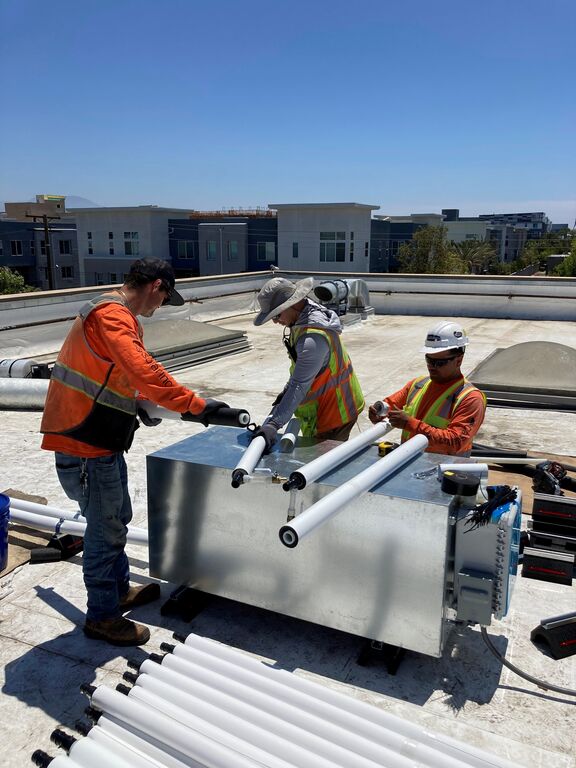
Installers insulate and jacket straight lengths of Wirsbo hePEX pipe to protect it from UV exposure.
“The system has the potential to yield up to 40 percent energy efficiency when added onto existing air conditioning and refrigeration systems, and the typical project is saving about 1,000 kilowatt hours per panel per year,” says Eli Goldstein, co-founder and CEO of SkyCool Systems, the company behind these radiative cooling panels.
The distribution piping system that connects to the panels consists of an oxygen-barrier crosslinked polyethylene (PEX) pipe called Wirsbo hePEX™, which is extremely flexible and durable to provide the proper medium needed to transport the water/glycol fluid. The piping system includes ProPEX® engineered polymer (EP) fittings as well as ProPEX copper sweat adapters for connections.
“We needed a pipe with an oxygen barrier to protect the aluminum panels from corrosion, and we also needed a product that was quick to install,” says Goldstein. “After talking with plumbing contractors, we learned PEX was far superior due to its installation speed.”
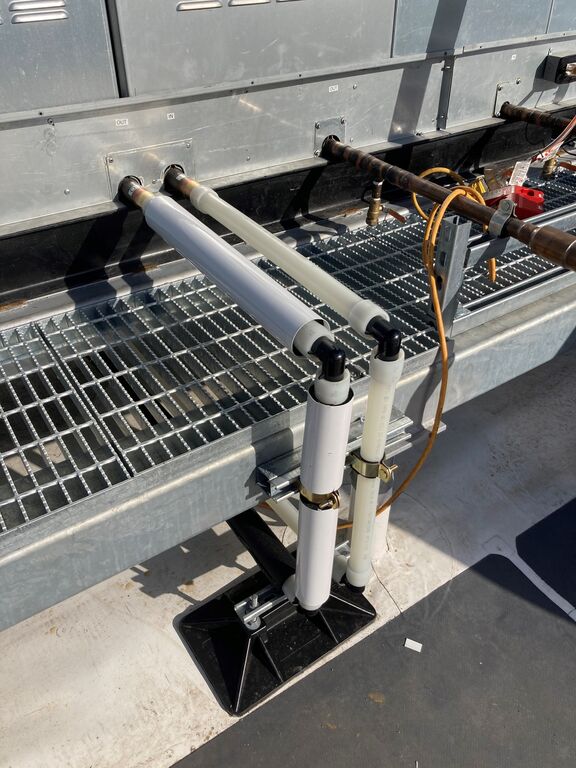
SkyCool Systems uses oxygen-barrier Wirsbo hePEX pipe and ProPEX fittings for the distribution piping.
After deciding on the pipe type, Goldstein says the next important decision was finding the right connection system that was efficient, dependable, and reliable.
“We chose to standardize the system with ProPEX expansion fittings to make sure we don’t have leaks,” he says. “We tried other fitting systems, but found they weren’t as reliable or as easy to install.”
Since these cooling-panel systems are being installed in various locations all over North America — and even in some foreign countries — SkyCool contracts the installation with local plumbing and heating contractors.
“We typically work with installers that have solar experience,” he says. “We provide the tools. We have a bunch of Milwaukee® ProPEX expansion tools in a job box that travels from site to site.”
With about a dozen projects complete by the end of 2022 and 40 to 50 projects slated for 2023, this cooling-panel trend is really beginning to take off in the commercial building industry.
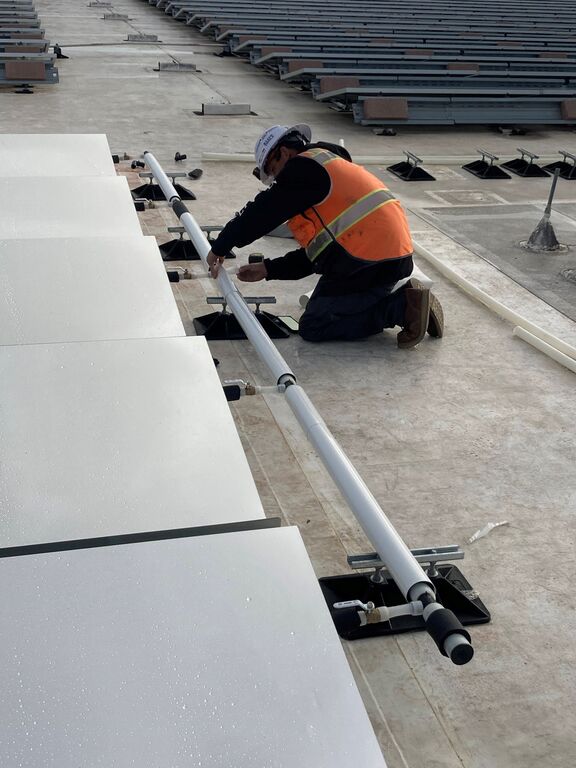
The distribution piping system features Wirsbo hePEX pipe along with ProPEX fittings and ProPEX ball valves.
From data centers to grocery stores to refrigeration warehouses, this technology is proving to be a great value to large commercial buildings that require constant cooling in an efficient manner.
“We anticipate most customers will get a return on their investment in three to five years,” he says. “Which, for commercial buildings, is relatively quick.”
With the incredible energy cost savings, the only question Goldstein typically receives from potential customers is the system longevity.
“The film on the panels has a projected life expectancy of around 15 years,” he says. “So, depending on where the system is located, the film will most likely need to be replaced after 15 years, give or take a couple years.”
He goes on to state that the rest of the system, including the aluminum panels, the racking system, and the piping system, have a much longer lifespan. PEX piping, depending on the manufacturer, typically has a life expectancy of around 50 years. So, the distribution piping is designed and manufactured to last for several decades.
“We’re insulating and jacketing the piping system, so it’s not exposed to UV,” he says. “That is one question we typically get when talking to customers. There is usually a concern about PEX and UV, but we make sure all the exposed piping is insulated to help ensure maximum longevity for the system.”
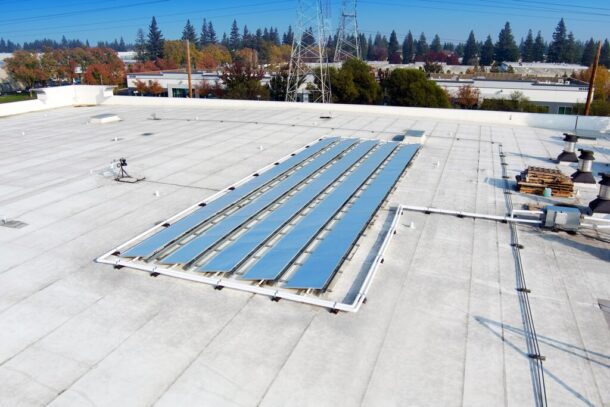
Here is the final installation with the supply and returning piping that includes the complete jacketing for UV protection.
As for future opportunities with this technology, Goldstein is working with partners all over the globe to find ways this innovation can help make cooling more sustainable.
“The opportunities are endless as to where we can use this reflective film to keep any outdoor surface cool,” he says. “From semitrucks to manufactured homes to outdoor electronics, it can be used to keep all different kinds of surfaces cooler than the outdoor air temperature.”
Kim Bliss is the technical and marketing content manager at Uponor. She can be reached at kim.bliss@uponor.com.
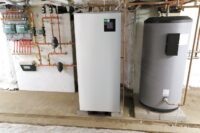
Taco’s System M air-to-water heat pump is meeting the demand for higher efficiencies and the inevitability of beneficial electrification. Coming off the heels of its 2023 AHR Expo Innovation Award for Sustainable Solutions, Taco’s System M’s air-to-water heat pump system is making waves in the field as well. “You really want to come out with Read more
Taco’s System M air-to-water heat pump is meeting the demand for higher efficiencies and the inevitability of beneficial electrification.
Coming off the heels of its 2023 AHR Expo Innovation Award for Sustainable Solutions, Taco’s System M’s air-to-water heat pump system is making waves in the field as well. “You really want to come out with innovative products that provide enhanced value in the marketplace. The System M is just that—the award is a great validation for the entire Taco R&D team,” says Mark Chaffee, Vice President, Product Management, Taco.
Why did Taco, a leading manufacturer of high efficiency indoor heating, cooling, and plumbing comfort systems, dive into the heat pump market? “We saw the trends in electrification coming so we wanted to include hydronically-based heat pumps to our line of already reliable comfort systems products. The last thing we need is more distributed refrigerant systems, if we are going fossil-fuel free and non-CO2 producing equipment, why not do it with water—with a GWP of zero,” says Chaffee.
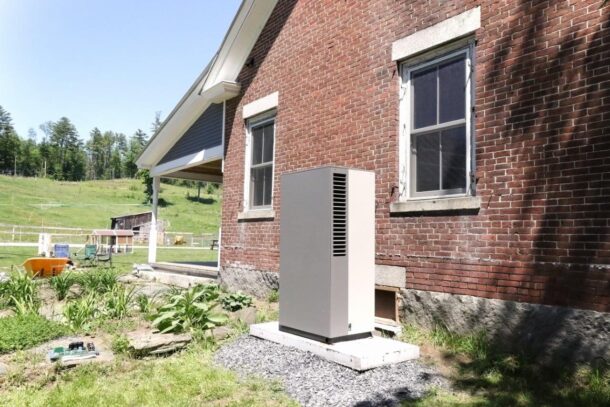
The System M outdoor unit
System M responds to increasing HVAC electrification trends while providing superior comfort, high efficiency and ease of installation. With just six pipe connections, the heat pump provides up to 44,000 BTUh, 3½ tons of cooling, and a max COP of more than four.
The technology is solar PV and smart grid ready, designed specifically for a low carbon society and built with the knowledge that water is the most efficient and natural energy transfer medium on the planet.
Rural Application
In a single-family, older brick farmhouse in Plainfield, a small town located in north central Vermont, the System M was piloted and installed in February 2020. Thanks to the ingenuity of Rick and Peter Lloyd of Lloyd Home Services, Emerson-Swan and Taco, another satisfied customer was converted to a non-fossil fuel powered heating and colling system with full PV integration.
But, because of Vermont’s extreme cold winter temperatures, the installation did not come without its challenges. “Here in Vermont, there are old homes with little to no insulation in many parts, such as this application before renovations. Though air sealing and spray foam upgrades were added to the home, the seasonal winter temps do offer challenges to heat pump systems holding comfort levels without a back-up or supplemental heat source,” says Rick Lloyd, service manager.
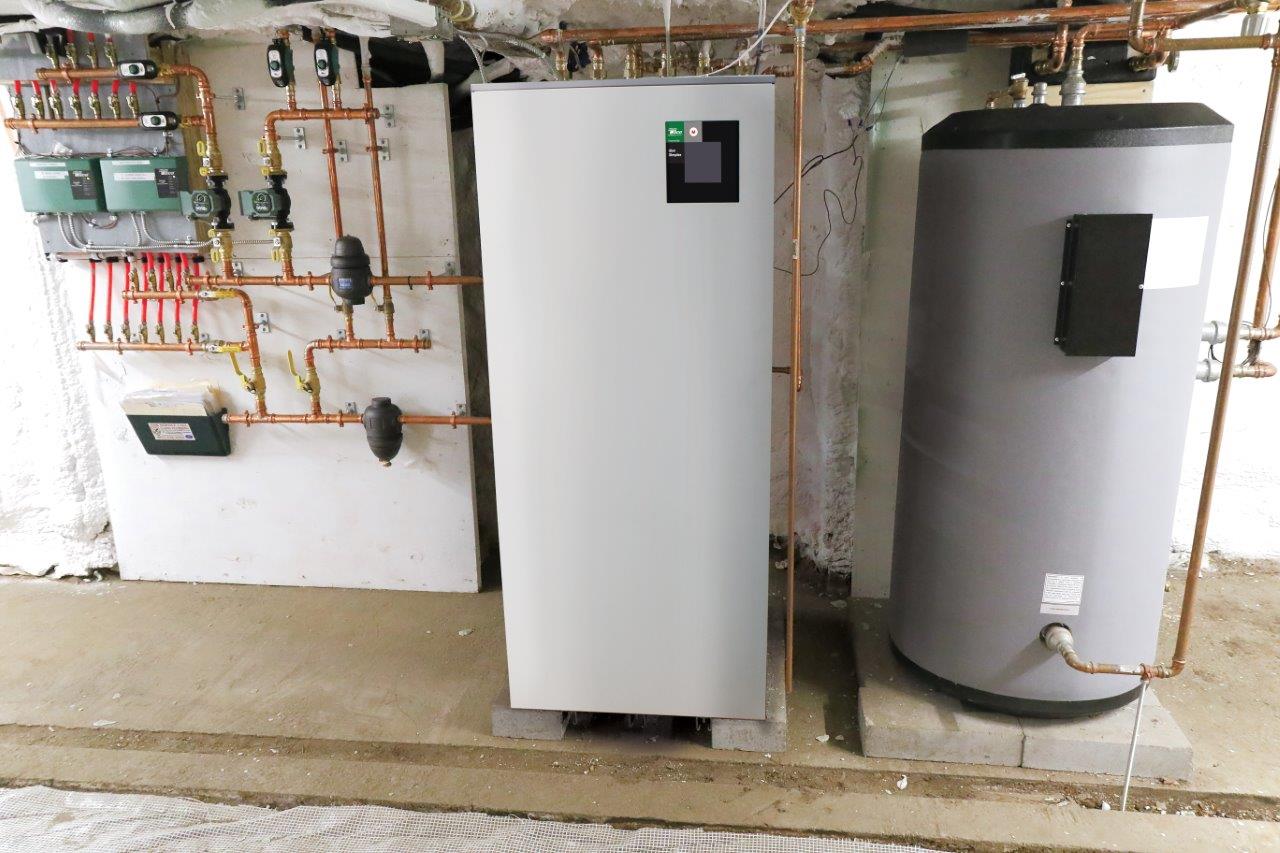
The mechanical room at the Vermont farmhouse
As was the case with Plainfield home, a homeowner’s insulation mistakes, and outdoor temperatures dipping to -20F for consecutive days, concern for supplemental heat was valid, and a back-up pellet boiler was part of the design. When the temperature outside dropped, the back-up pellet boiler kicked-in to provide a secondary natural source of heating. Balancing the two heat generation systems provided the ultimate efficiency throughout the year for a first of its kind fossil-fuel free instalation in Vermont.
There were some early assumptions on BTU heat loss for the historic building that turned out to not be true, says Lloyd. “The proper BTU heat loss survey and calculation in any high efficiency equipment upgrade is important, especially one where the hot and cold extremes are as wide as here in Vermont. As a company we strive to ensure any work—whether a system upgrade or a repair we do in association with heating or cooling—meets or exceeds the desired results,” says Lloyd.
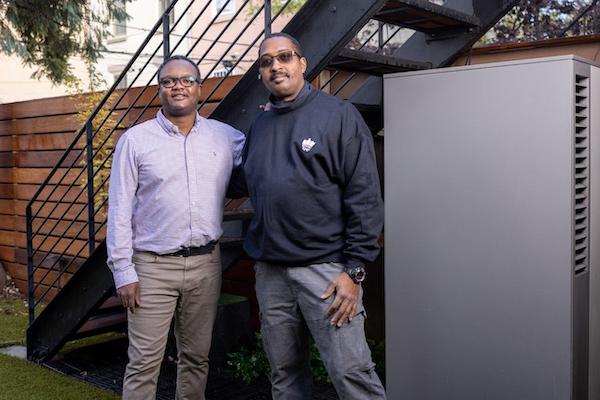
Chester Birchwood (r), owner, HVAC KINGS LLC, stands with the homeowner next to the exterior System M unit.
Because this particular example featured extreme frigid temperatures and excessive summer heat inside the brick house, coupled with inconsistant insulation, the team didn’t realize how much harder we had to work on this particular project, recalls Lloyd. However, “the System M package is well engineered and designed and made to attach easily to system piping, and because this was a 2020 pilot program, this particular system was closely monitored by Taco, and they were able to do most adjustments to the system remotely through the app, as needed to dial in the optimal performance,” says Lloyd.
“I will tell you this, if we’re talking a newly-built or well-insulated, slab home, the System M is definitely the cat’s meow,” says Lloyd. And, says Lloyd, the homeowner is extremely satisfied with the cooling of the home in the summer months using a hydronic-based system.
Big Apple Installation
To the south, a homeowner in Brooklyn, N.Y.—who was an early adopter of sustainable practices—purchased an old home in 2019 and quickly began demo work to gut the home prior to what would become a thorough renovation—removing layers of linoleum and vinyl flooring, and essentially all plumbing and wiring. As the work progressed, they began to specify high-performance windows and ample blown-in cellulose insulation. The home included mostly radiant floors and some in-floor convectors for supplemental perimeter “hydro-air” heat.
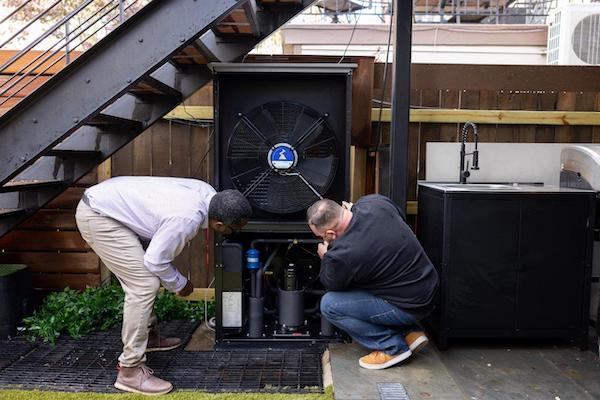
The homeowner called many New York City-area HVAC companies; however they were reluctant to move beyond their comfort work zone, and none were quick to accept the request to install an air-to-water heat pump system, like the System M. Eventually, calls and referrals led to Chester Birchwood, owner, HVAC KINGS LLC, who ultimately became the installation engineer.
Birchwood, in addition to installing a 3.9 Kw solar PV array atop the home, also installed the System M for cooling, heating and domestic hot water. “I’ve become a big fan of the System M, and its viability for residential installations nationwide,” says Birchwood.
The Efficient Choice
The System M technology is solar PV and smart grid ready, designed specifically for a low carbon society and built with the knowledge that water is the most efficient and natural energy transfer medium on the planet. “Water has a global warming potential of zero. The System M offers resiliency, higher efficiencies and lower long-term operating costs,” says Chaffee.
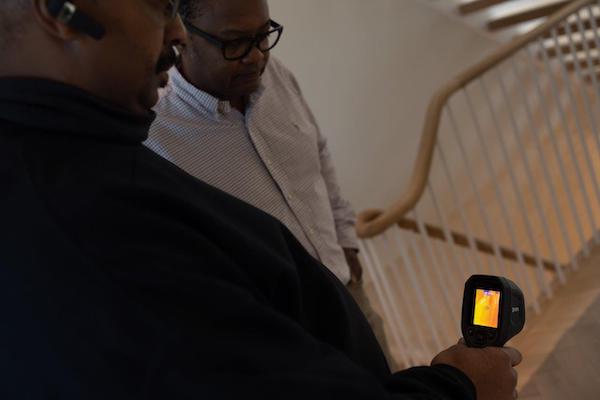
Chester Birchwood use an infrared camera to examine operation of the radiant floor system.
The outdoor portion of the heat pump (monobloc) features advanced inverter technology, a variable speed fan and quiet operation. The indoor HydroBox unit contains an integrated buffer tank, simplified wiring hub, user interface with smartphone app control, and a high-efficiency, dual-ECM pump piping module. The modular design provides turnkey functionality and reduces installation time. “This cuts installation time in half, and gives contractors more confidence that they can do it,” says Chaffee.
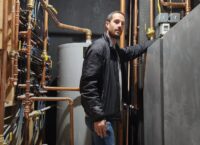
A Rolls Royce with a Veto Pro Pac tool bag in the trunk. Now that’s pretty drippy. For Moe Hirsch, Moes Consulting and Mechanical Services, Rockland County, N.Y., his bucket list item is a good representative mix of work and swaggy. Hirsch basically started off in the trades when he joined his cousins, who were plumbers Read more
A Rolls Royce with a Veto Pro Pac tool bag in the trunk. Now that’s pretty drippy. For Moe Hirsch, Moes Consulting and Mechanical Services, Rockland County, N.Y., his bucket list item is a good representative mix of work and swaggy.
Hirsch basically started off in the trades when he joined his cousins, who were plumbers, for a few days and he immediately loved the excitement. Eventually, when things began to slow down, “I went out on my own using the heating knowledge I had learned. I had the mentality that if someone was going to figure it out, it might as well be me.”
From there, Hirsch grew into a plumbing, heating and cooling company, and two years ago began distributing and installing Cummins generators. Currently, the company focuses on the mechanical trades but offers property services to its clients as well.
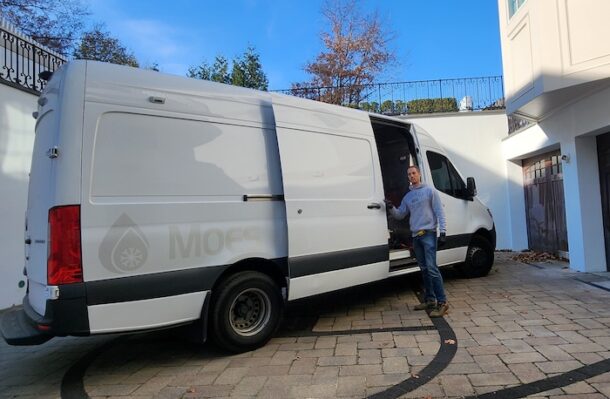
Hirsch says he’s learned a lot from so many that narrowing it down would be impossible to credit everyone. Having said that, “The trade leaders for me were Dan Holohan, Mark Eatherton, Bob Hot Rod Rohr and John Siegenthaler. In the business world, Grant Cardone and Brandon Dawson have showed me what my true potential is. You really can learn something from everyone,” says Hirsch.
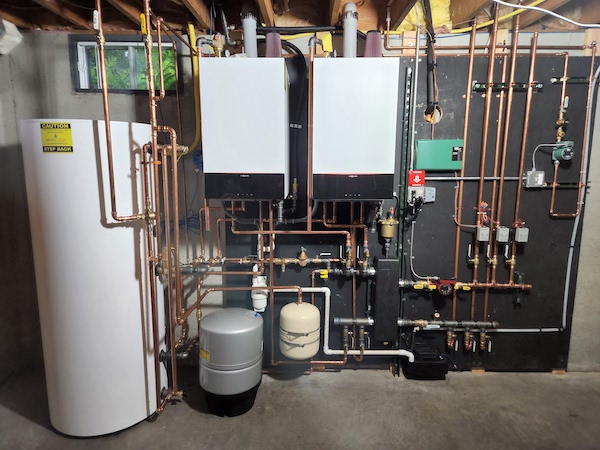
In addition to meeting and helping so many people, another rewarding aspect of the trades is that it can be very profitable. And while you can be in the trenches working hands-on, says Hirsch, you can use your skills to be a great manager, assistant or other asset to a company. “It’s not all wrenching knowledge. Business to me is 33% knowing your trade, 33% knowing business management, fact finding and sales, and the other 33% is just being a genuine, kind person.”
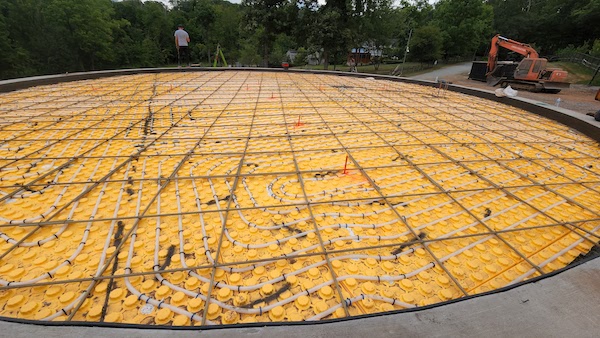
How can the PHVAC industry do a better job attracting people to the trades? Hirsch, you could say, practices what he preaches. As he prepares for every job, Hirsch makes sure he has his MacBook, latest smart phone, his personal CO detector and his loaded Veto bag, and says, “Make trades cool again; show kids the cool stuff. If they’re into muscle cars show them a tradesman driving his mustang to work. If they’re techy, show them someone performing a diagnostic using a computer.”
Moreover, social media, whose influence on young people can’t be denied, has opened many doors for tradespeople. “Social media is a free outlet to showcase your work—you can share your work, learn from others and link up with locals. Plus, social media can make the sale easier. The client feels they know you and is more willing put their trust in you,” says Hirsch.
As far as balancing work/leisure time, “I don’t balance them,” says Hirsch. “I try to do both to the max.” And that includes spending time with his wife and kids, training his new Golden Retriever, Marshmallow, and, of course, bumping into clients and seeing their happiness.
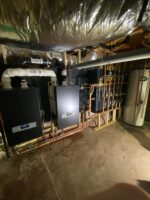
Cascading System Solves Heating Challenge for Huge Home on Massachusetts Shoreline Winters can be hard on home heating systems. Particularly so in New England coastal communities, where wind, snow and sleet, and bone-chilling temperatures force systems to work massive overtime. New England in summer is special. Winters? Not so much. In older homes it can Read more
Cascading System Solves Heating Challenge for Huge Home on Massachusetts Shoreline
Winters can be hard on home heating systems. Particularly so in New England coastal communities, where wind, snow and sleet, and bone-chilling temperatures force systems to work massive overtime. New England in summer is special. Winters? Not so much.
In older homes it can be particularly difficult to maintain heat throughout the house, especially in the region’s expansive, multi-story structures. Put all the ingredients together, and home heating contractors in New England and other frosty locales find it a challenging task to ensure everyone’s thermal comfort.
Working with Emerson Swan, the team at Jeff Potvin Plumbing & Heating installed a solution that uses cascading as an efficient heating source for a 4,000 square foot house, which was built in the late 1800s. “The homeowner had two 250K BTU boilers, but they were pretty old and worn out,’’ Potvin said. “It was time for a new system.”
Uncomplicated Install
To replace the existing boilers, Potvin’s team installed two Ariston HTP ELU 199K boilers. The boilers will provide heat for a house that includes five bedrooms and six baths. The house is steps away from Preston Beach in Marblehead, Mass., and the spacious living room overlooks the ocean. By every real estate metric, it is a premium property in a highly coveted location.
But with the heating units breaking down, it was critical to implement a new system. Potvin’s team decided to install a pair of cascaded boilers to help the homeowner maximize efficiency.
“These boilers are uncomplicated to install due to the large cavity inside, which will enable us to service its components in the future,’’ Potvin said. “We had a fluing issue, but we cascaded the boilers and also vented them, which solved the problem.”
One of the concerns for the homeowner was the noise of the units. The mechanical room is located near a living area. “One of the benefits of the HTP ELU boilers is they are very quiet,’’ Joe Savignano of Emerson Swan said. “They are common in European homes, and they are made to be super quiet. Even with a 3-way valve moving, you don’t hear a thing. The homeowner was pleasantly surprised by how quietly they operated.”
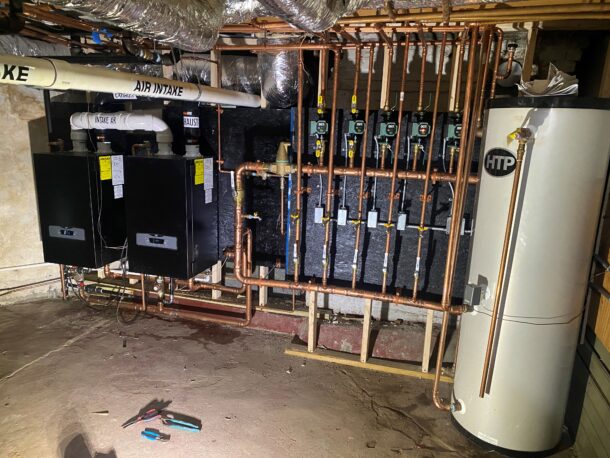
Jeff Potvin Plumbing & Heating installed two Ariston HTP ELU 199K boilers in a cascaded system to heat a 4,000 square foot house in Massachusetts.
Critical Redundancy
The benefit of the cascading system is that it ensures redundancy, so that a building or home retains access to hot water for heating in the event of a failure.
Cascading involves using multiple units to solve demand issues when one unit is incapable of generating the amount of heat required. Before installing a cascading system, it is important for the contractor to know the BTU heat load calculation. A bigger structure will generate more heat demand.
For example, a building might have a 10 million BTU heat load calculation. An Ariston HTP Elite Ultra XL boiler provides 2 million BTUs and would require five of them to meet the heating capacity of the building when 100 percent of the load is demanded.
Most of the time, however, 100 percent of the load is not required, and less heat is needed in short term duration. A zone might come on in the system that calls for 2 million BTUs. With cascading, all five boilers act as one to meet the demand. If the building needs 100 percent of the heat, all five units would fully activate.
One unit orchestrates the activities of an entire group. HTP calls it a Master and Follower installation. Follower heaters are controlled by the master unit and dictates when all units operate. Most cascade systems have lead/lag rotation grouping to spread the demand load evenly so that no one unit is used more than the others.
Worry-free system
For homeowners and businesses, cascading systems ensure hot water delivery when maintenance is required or unplanned downtime temporarily disables one of the units. That’s particularly important for a New England home, where a boiler stoppage in the middle of the night could lead to burst pipes, unheated bedrooms, and angry customers.
In the maintenance cycle, a building might use 5 boilers to produce 10 million BTUs of hot water. After two years, the first boiler is taken out of operation for maintenance. With the cascade design, the building can manage day to day activities to keep hot water available to the entire building with just four boilers.
If a unit fails due to an error code, the other units in a cascade system meet the demand. If a business has just one boiler for daily operations, and it fails or needs maintenance, the business must close. Homeowners who lose their heat might need to find temporary, alternative living arrangements until the heat is restored.
Cascading also spreads the load across multiple units, so that all boilers are actively supporting each call. HTP’s Elite Series has programming that shifts loads of a heat call when the first unit gets to 80 percent operation. Once a boiler hits that mark, it will split, and another unit will fire to divvy up the demand call.
Some units even include rotation clocks. Elite Ultra models can be programmed for specific hours of operation. For example, one boiler can be programmed for 6 hours. When that time expires, the next boiler in the rotation picks up the next 6-hour shift. By ensuring that all units are used equally, the system needs less maintenance and individual components will last far longer.
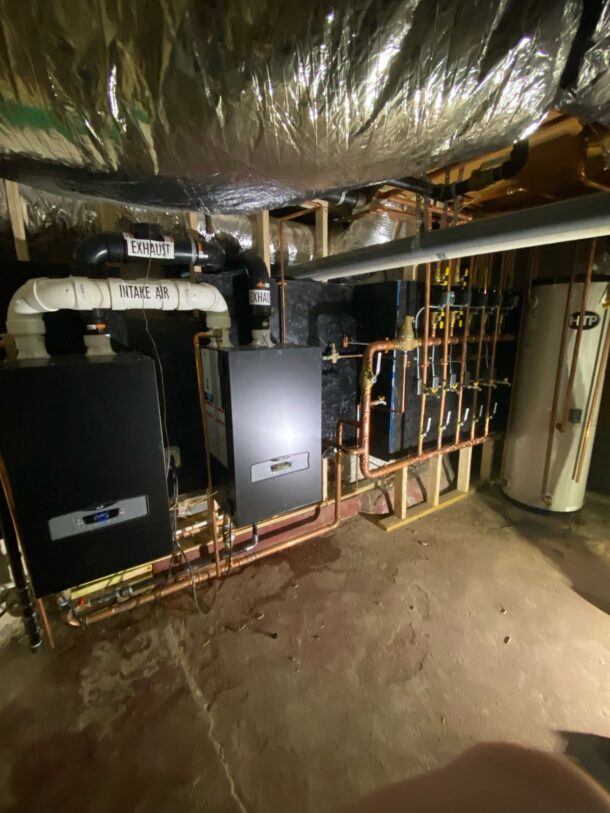
The cascaded system ensures redundancy, and multiple units solve demand issues when one unit is incapable of generating the amount of heat required.
Various applications
Cascading systems can be used in commercial and residential jobs. Hotels, hospitals and office buildings have high demand, so cascading systems give them an efficient and reliable option to meet that demand. The expansive Massachusetts home is also the perfect setting for a cascading system.
“One of the things that I like about the Elite Ultra is it’s the easiest to control,’’ Savignano said. “The Wi-Fi function enables remote monitoring of the system.”
Another residential application might be for a home that includes a snow melt system for the driveway. The heat load for the home could be 130,000 BTUs for the house and 250,000 BTUs for the driveway. The solution could be individual systems, or two Elite Ultra-199WBN models to cover the total heat load.
One more application demonstrates the benefit of a cascading system. An apartment complex in Derry, N.H. installed three Elite Ultra boilers in a tight footprint for an apartment complex. By using multiple units, installers have greater flexibility in irregular spaces. The mechanical room for the apartments had limited space, so a cascading system proved to be a good solution.
Potvin’s client can rest comfortably, knowing that the cascading system will keep the family comfortable all winter long. “This system made perfect sense for this job,’’ Potvin said. “We use the HTP products a lot for our jobs. They’ve got a good support system, and the Elite Ultra interface is easy to use and is remarkably efficient. It’s a durable product and the homeowner won’t have to worry about heating the home for a long time.”
Guest Author is Thomas Renner, who writes on a variety of trade industry topics for publications throughout the United States.
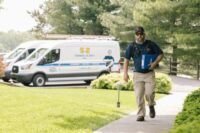
By Jason Richards, Hajoca Corp. I’ve seen a lot of creative ways to provide emergency heat to buildings during no-heat situations, but maybe none as original as a project we became involved with early this year at an upscale rural property near Reading, Pa. The 12,500-square-foot building, one of many on the 100-acre property, houses Read more
By Jason Richards, Hajoca Corp.
I’ve seen a lot of creative ways to provide emergency heat to buildings during no-heat situations, but maybe none as original as a project we became involved with early this year at an upscale rural property near Reading, Pa.
The 12,500-square-foot building, one of many on the 100-acre property, houses a heated pool, spa, full size tennis court, kitchen and locker rooms. When the old sectional boiler used to heat the facility failed mid-winter, maintenance staff turned the pool water temperature way up. This not only held the natatorium at a safe temperature, but waste heat from the pool heating equipment kept the adjacent tennis court from freezing.
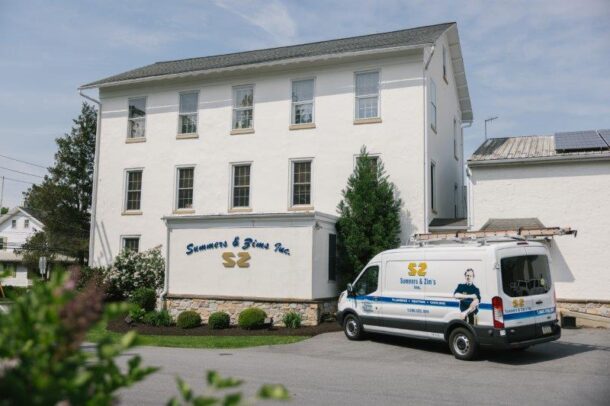
With 37 employees, Summers & Zims serves southeastern Pennsylvania from their headquarters in Atglen, Pa.
Mechanical contractor Summers & Zims, Atglen, Pa, was called in January to handle the no-heat call. The 37-person company had served the property owner in 2013 when they installed an extensive snowmelt system.
Joe Henderson, plumbing project manager, responded to the call and found that the large boiler was beyond repair; a replacement was needed immediately.
“Jason Richards, at Hajoca, and I began designing a replacement,” said Henderson. “There was a 500-gallon fuel oil tank on the property for the hydronic system and backup generator, and there was also an LP tank for the pool heater. The problem with replacing the original oil boiler with a propane unit was that the existing LP tank wasn’t large enough to handle the additional load. Plus, a second LP tank wasn’t immediately available.”
We didn’t know it then, but that was the first instance we experienced where major product availability issues would impact our decisions during the design process. Luckily, the supply chain challenges ultimately resulted in an even better system than we planned for initially.
Collaborative design
We continued the design with a multi-boiler approach. The original plan was to install a single large sectional boiler, but supply chain issues caused some trouble. I consulted with Dave Raabe, at ROI Marketing, and we learned that the boiler we wanted wouldn’t be available for a few weeks.
“This project took place at the height of the product availability challenge,” said Raabe. “The larger boilers weren’t available, so we looked at using three smaller MPO-IQ boilers, made by U.S. Boiler Company. These were immediately available. Ultimately, installing three boilers provides three stages of heat input for higher efficiency, and it also provides a level of redundancy. The smaller boilers also meant that the units could be wheeled into the mechanical on hand carts, instead of being field-assembled.
As a result, the design team selected three, 189 MBH boilers.
“We’ve come to love the MPO-IQ,” said Henderson. “We’ve installed tons of them. At 87 percent, they’re the most efficient, dependable oil boiler we’ve ever used.”
This design yielded a three-stage oil-fired system, which is uncommon in a residential/light commercial application. It provides some redundancy and, more importantly, allows the system to fire at lower input based on outdoor reset.
Controlling the boilers became the next question. Summers & Zims’ HVAC trainer and in-house tech support, Kenny Walker, has a great deal of experience with tekmar controls and had used the tekmar Boiler Control 274 for staging multiple boilers on numerous occasions. The property owner also wanted to remotely monitor the system through WiFi, so the new tekmar Smart Boiler Control 294 was selected.
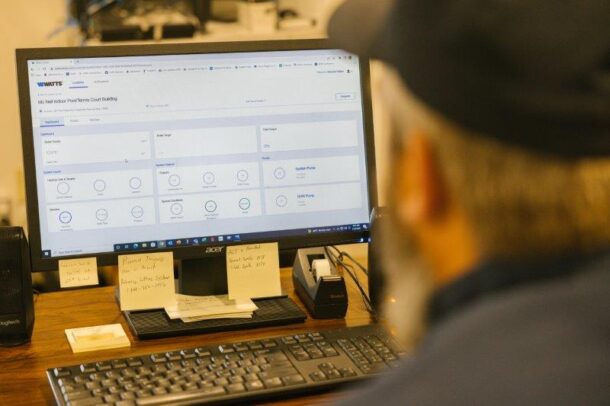
Using the Watts OnSite web or mobile applications associated with the tekmar Smart Boiler Control 294, Kenny Walker can monitor the boiler system from his desktop or mobile device.
Rapid installation
Summers & Zims, originally Summers Brothers Plumbing & Heating, has been in the business since 1930. They merged with Zim’s Sales & Service in the 70s, forming the company it is today.
I’ve known a lot of their people for a long time, and can speak to their professionalism. They’re what I’d call “do the right thing” kind of people. Joe Henderson and I go back 25 years, even before I joined Hajoca. He’s a very sharp hydronics guy. When it came time to install the system in a hurry, I knew they could handle it.
For the install, Walker was joined by Todd Lease, head plumbing technician, Andrew DiEugenio, journeyman plumber, and Austin McGhee, apprentice.
The boilers were rolled into the mechanical room and a primary-secondary piping configuration was used to connect them to the system loop. The fuel supply line to each boiler features a Tigerloop fuel oil deaerator.
“We install a Tigerloop on every oil-fired system we install,” said Walker. “They cut down on nonsense service and emergency calls by cleaning up ignition and burn, which creates less soot in the heat exchanger. We also like that they allow us to use spin-on oil filters, which catch small dirt particles and reduce nozzle failures.
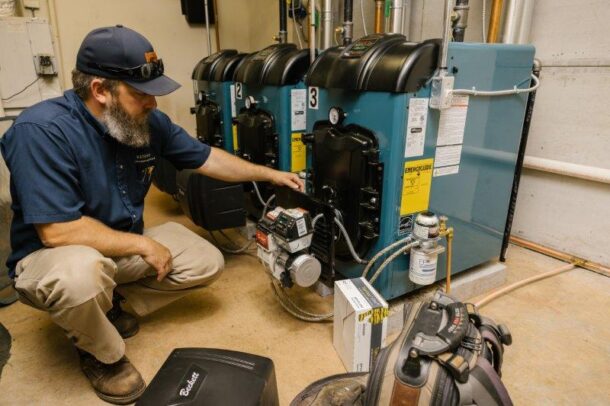
Kenny Walker, Summers & Zims HVAC trainer and in-house tech support, installs a Tigerloop Ultra oil line de-aerator.
“If the homeowner isn’t attentive to the amount of fuel they have left in the tank, running empty isn’t such a big deal,” he added. “The Tigerloop provides a two-pipe system from the oil pump to the unit. This way, the oil pump will self-prime, meaning the owner or the fuel delivery tech can simply hit the reset button on the primary control once oil has been delivered.”
Flexible fuel lines were used from the Tigerloop to the boiler’s Beckett burner. To provide easy access to the three-pass heat exchanger, the MPO-IQ features a hinged front door, where the burner is located. By using flexible lines instead of hard pipe, service techs can open the boiler without removing the fuel fitting at the burner.
“Providing deaeration is even more critical on a multi-boiler installation like this because the more times you Tee off of the fuel line, the more opportunity there is for air to enter the fuel supply,” continued Walker.
Venting the boilers was done as deliberately as supplying the fuel. The existing chimney was large enough, but common venting the three units had to be done carefully.
“We couldn’t just run three, six-inch vents into a common stack, because the distance between the boilers and the main stack were slightly different,” explained Henderson. “The first two boilers join into an eight-inch vent, which increases to 10 inches as it picks up the third boiler and exits to the chimney.”
Control
When the original boiler failed, the homeowner decided that he wanted to monitor the heating system regardless of where he was, and he also made the decision to sign a service agreement with Summers & Zims. For both of those reasons, Henderson wanted to find a control solution to stage the boilers and provide web-based monitoring. That said, they also wanted to avoid the use of a complex, costly building automation system.
“Jason had recently told us about the new tekmar 294,” said Walker. “So when we bought the boilers from Hajoca, we also bought the control. The 294 is similar to the 274, but with more features, a touch screen, and most importantly, remote monitoring capability. It can also send me texts, emails and push notifications for a wide variety of alerts.”
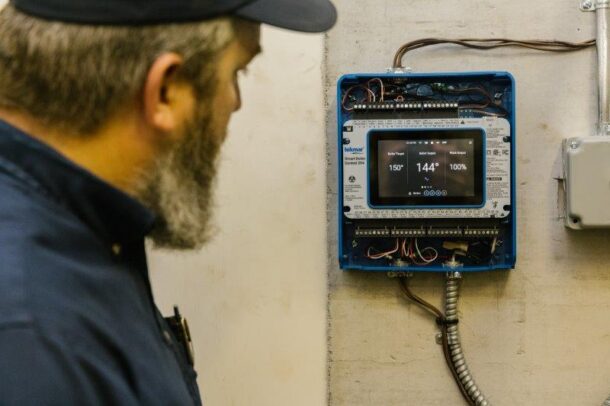
Kenny Walker installs the tekmar Smart Boiler Control 294.
The control stages and rotates the boilers, as well as handling outdoor reset, DHW priority, warm weather shutdown, etc.
In a typical MPO-IQ boiler installation, the onboard boiler control features optional plug-and-play cards to provide outdoor reset, low-water cutoff and aquastat. In this system, the tekmar 294 replaces all but the low-water cutoff card.
“The 294 was easy to install, and I can pull up and make setpoint changes to the customer’s system at my office or on my phone,” said Walker. “Right off the top of my head, we have half a dozen other systems in the field that would benefit from the use of this control. Each one can control four appliances, and they’re expandable to 16.”
Within a week of the old boiler failing, the new hydronic system was heating the building, and the pool heater was turned back down to its normal operating temperature.
I think this job—and the speed at which it came together despite supply chain issues—is a testament to Summers & Zims. The whole company shows up and honestly tries to do the very best they can.