While he’s not busy with his day job working on hydronic heating systems, commercial and residential plumbing, backflow prevention and gas work, Chris Massaro (@nwo_plumber) loves playing guitar and recording music. Admiring the recent tattoo to commemorate his daughter’s birth, “I was in a bunch of bands throughout high school and recorded an album once Read more
Featured Articles
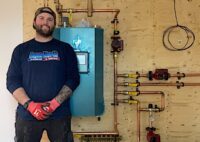
While he’s not busy with his day job working on hydronic heating systems, commercial and residential plumbing, backflow prevention and gas work, Chris Massaro (@nwo_plumber) loves playing guitar and recording music. Admiring the recent tattoo to commemorate his daughter’s birth, “I was in a bunch of bands throughout high school and recorded an album once. I don’t get around to it as much as I used to or like to, but I’m definitely making more time for that now,” says Massaro, owner/lead tech at Aqua North Plumbing and Heating Ltd., Thunder Bay, Ontario, Canada.
I take that back. Massaro also enjoys hanging out with friends and family, golfing and mountain biking. And, he definitely needs to get that grill time in—grill, smoke, BBQ. “Sometimes in that order, in one cook. Most of the time I do use the smoker though. I’ve been on a pulled pork kick lately. My favorite is some nice pork shoulders on the Traeger. It’s the ultimate dad activity, in my opinion,” says Massaro.
The work\life balance has been a struggle for Massaro; he realized one day that when you are running your own small business sometimes there isn’t a balance. You have to make the time and prioritize it. “Do what’s important to you and make time for the people and activities you love. And most importantly, take care of yourself! Because you’re worth it. Time stands still for no one so spend it wisely,” says Massaro.
And that’s why staying physically fit and active is important to Massaro. “I’m always lifting, bending, up and down the stairs all day so it’s helpful to have a training regimen that supports that. And, it really helps to keep me in mental shape as well,” say Massaro.
Even more important is eating right, says Massaro. “We use a lot of energy in a day in the trades so we have to keep that fire fed. All of this allows me to stay energized all day and still have plenty of gas in the tank when I get home for family time,” continues Massaro.
Massaro’s foray into the trades started when he starting working for the family business as a plumbing apprentice at the age of 13. “Made best friends with my shovel and we went to work. Thankfully, I graduated from digging trenches and went on to start really learning about the ins and outs of the trade,” recalls Massaro.
Over the next few years, Massaro spent most days plumbing residential systems with a few commercial jobs sprinkled in here and there while working for my father. “It was nice to be doing a bit of everything and not just strictly one area of the trade, which I felt was important to be a well-rounded tech.
Once Massaro had a few years under his belt, he did a lot of remote northern work for fly-in communities. “Those big jobs we did up there really sharpened my time and material management skills,” says Massaro.
In addition, the high school Massaro attended offered a cooperative education program where he was able to gain work experience hours toward his apprenticeship if he chose to stick with plumbing. “I would go to regular classes for the morning periods then co-op at Aqua North in the afternoon,” says Massaro.
As a side note, Massaro says that if your local high school offers a cooperative education program, he highly recommends getting involved. “It’s a really pressure-free way to get your feet wet in whatever trades the school offers,” says Massaro. “I always try to take on one co-op student per year and leave them with a positive experience in the trade. I feel that’s the best way for kids to feel out what they want to do. And, don’t be afraid to ask questions!”
Next, after getting all of his trade school and work hours complete, Massaro then wrote his exam for his certificate of qualification in plumbing. Shortly thereafter, Massaro bought the family business, and the rest is history.
As fourth-generation plumber, Massaro has had some great mentors in his career, with plenty of help and guidance from his father and grandfather in learning new and old ways of plumbing. “If my great grandfather was around then I’m sure he would have some real old school stuff to show me.”
And while Massaro doesn’t consider himself a role model, he’s always willing and ready to help others to do their best at work, and life in general. “I’ve learned a lot over the years and sharing the experiences and knowledge with up-and-coming tradespeople is paramount,” says Massaro.
For Massaro, he loves building something from nothing and executing the job. “Sometimes just sitting back after the job is done and being like ‘damn we really did that.’”
Perception Change
The perception of the industry needs to change, says Massaro. “I think the wheels are turning on that as we speak but we’ve got a long way to go.”
Social media is that vehicle for the instrument of change as it’s an easy way to showcase contractor work, and connect with other professionals. “There’s a solid amount of tradespeople out there doing an amazing job. If we can show people that there’s more to plumbing than just plunging toilets, fixing leaks, and back-breaking work, then I think that’s a win,” says Massaro.
Whether it’s new and better tools, techniques, business knowledge, etc., Massaro has learned so much on social media. “It’s awesome that we can connect with people and have such a great community sharing tricks of the trade, meet-ups or even debate if it’s tape then dope—which it is—or dope then tape,” says Massaro.
In the end, as Massaro sets his sights on his career and further enriching his life, a good bucket list item to check off would be getting a recreational pilot’s license. “Always wanted to get into aviation in some way.”
The sky’s the limit.
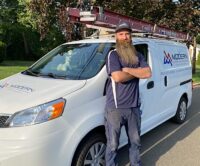
You might say his affinity for the Bonsai arts helped channel his inner Zen, patience and attention to detail. But you’d have to ask him yourself. “I studied Bonsai for years, even went out to Oregon to study the craft,” says Tom Castagna, install department supervisor, Modern Heating & Air Conditioning, LLC, Milford, Conn. Working Read more
You might say his affinity for the Bonsai arts helped channel his inner Zen, patience and attention to detail. But you’d have to ask him yourself. “I studied Bonsai for years, even went out to Oregon to study the craft,” says Tom Castagna, install department supervisor, Modern Heating & Air Conditioning, LLC, Milford, Conn.
Working part time as an auto mechanic throughout high school, upon graduation, Tom Castagna (@tstags on IG) was approached and offered a job at Shelton oil as an apprentice where he primarily serviced and installed oil-fired equipment, and dabbled in a small amount of air conditioning. “Having no knowledge of what the trade actually consisted of, nor what my new position would entail, I couldn’t resist $1/hr. more an hour than what I was then making. This started my love affair with HVAC,” says Castagna.
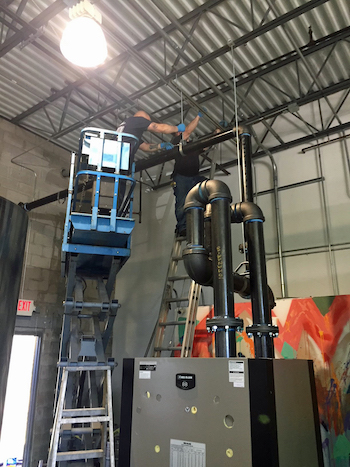
From there, Castagna moved to a mechanical company for eight years where he service and installed residential and commercial systems and also worked on refrigeration, ranging from kitchen equipment, vending machines, walk-in cooler/freezers to tooling/CNC machining.
Castagna has been at Modern for the last seven years where he started as lead service technician, and would occasionally install when needed, to now managing the install department for the past two years.
Along Came a Mentor
Castagna soaked up as much as he could early on as he has been lucky to have worked with some extremely knowledgeable guys in the trade. Castagna says he’s picked up something from everyone he’s worked with, whether that be knowledge of trade, or aspects of life.
“The first couple months being in the trade I rode along with a very old school oil tech named Jeff. Jeff was tough, extremely tough. My first day of work he picked me up and the first words out of his mouth as I sat in the van—pointing at the radio and all dashboard controls—’see all this, you don’t touch this, ever.’ At first, I hated this man for his short temper, general distain for the world, and teaching style, but his general knowledge and skill was something I’d never experienced before so I shut up and took it all in—the good and the bad,” says Castagna.
But it’s current boss, Matt Sando, who has molded Castagna into the man he is today. “We worked together at a previous company where we both weren’t thrilled with the direction the company was going and he knew he could do better. I remember being on a job with him days before he was leaving and he was showing me different van designs and logos and wanted help choosing. I knew once he was established, I’d be making the jump. And here we are seven years later, and the company treats everyone as a family, a modern family,” says Castagna.
According to Castagna, Sando taught him how to be a leader, and he’s matured immeasurably under his guidance. “I would like to think I’m a good role model. Trying to learn and navigate a new trade in my later teens and early 20s, along with training apprentices, was difficult to say the least. I think I may have carried on some of Jeff’s earlier teaching styles but luckily, I always had a tough group of apprentices that could endure my lack of patience. I’ve learned a lot about myself as well as a ton of life skills in this trade,” says Castagna.
Paying it forward can be just as rewarding. Setting a good example and being able to teach and watch someone’s timeline and rise to success is a great feeling says Castagna.
“As a service tech, I walked into a job with four items— a Klein HVAC 10-1, Klein wire strippers, a Fluke 902 meter and a good flashlight. Being in HVAC, we have to carry an immense amount of tools and instruments because of the variety of things we work on, but at the most basic, you can do a lot of damage with those four tools, and your mind.” — Tom Castagna
While Castagna says the industry does a pretty decent job of providing education and opportunity for all, he thinks a lot of tradesmen like to blame lack of work force on a generational laziness. “People just need to be better mentors and be more outgoing with recruiting young talent. I wasn’t looking for a job in HVAC at 17 years old, but someone approached me with an opportunity.”
However, on the flipside, people thinking of entering the trades need to have thick skin and a willingness to learn and work harder than ever before. In return, says Castagna, you can create a very comfortable life for you and your family.
Work/Leisure Balance
Early on, Castagna did not have a healthy work/life balance. “Everything was all or nothing for me and I put it all into my work. On my ‘days off,’ I was still at the shop or organizing my van or finding something to do,” says Castagna. “But as we know, that can’t last forever; you’ll reach a breaking point. I think I needed to get myself to that point to actually realize that I needed a life outside work. I really cherish my time off now.”
His advice? “Start your day early! There’s a lot you can get done before the average person wakes up. Stay organized and MAKE TIME for yourself/family.”
And for Castagna, this includes anything outdoors—concerts, fishing, hiking, hunting, working on cars and motorcycles. Also, playing darts and billiards with friends.
Oh yeah, I hope one day Castagna gets that 90-point ride for eight seconds.
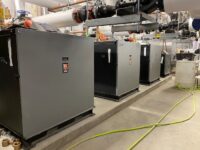
By Greg Hughes Three boiler types loom large among conventional (non-condensing) commercial water boilers used for process or space heat, with input sizes of 400 MBH and up: those with cast iron sectional, fire-tube and water-tube heat exchangers. For a variety of reasons, the latter two have been most prevalent in the commercial process heating Read more
By Greg Hughes
Three boiler types loom large among conventional (non-condensing) commercial water boilers used for process or space heat, with input sizes of 400 MBH and up: those with cast iron sectional, fire-tube and water-tube heat exchangers.
For a variety of reasons, the latter two have been most prevalent in the commercial process heating market. Advantages include relatively compact size, lower standby heat loss, and the speed with which heat can be generated and delivered into distribution piping.
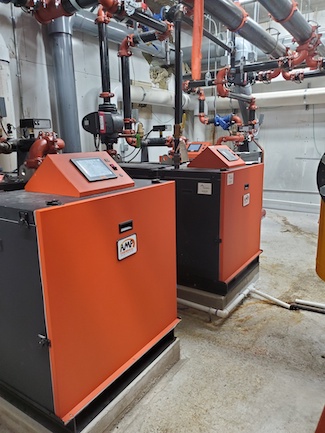
A Thermal Solutions AMP water-tube boiler is rated at 97% efficient. The stainless steel, modulating-condensing boiler line offers a size range of 1,000-4,000 MBH.
First out of the gate for a wide range of uses was the fire-tube boiler—with early design dating back centuries. Hollywood gave great prominence to horizontal fire-tube boilers, though few producers, actors or moviegoers were aware of it. Every time a steam locomotive—aka the iron horse—blew its whistle or raced across the great plains, an uncelebrated fire-tube boiler was doing its part.
Still today, fire-tube boilers offer a wide range of uses. Within these boilers, fire tubes are immersed in water; hot flue gases produced by the combustion chamber flow inside them. The hot flue gases transfer their heat to the outside water through the conduction.
Water-tube boiler designs, introduced later, essentially invert the fire-tube boiler construct: water is contained within the boiler’s internal tubes.
Water-tube advantages
In water-tube boilers, combustion occurs within the shell that surrounds the tubes, forcing combusted gas over the water tubes for exceptionally fast, efficient heat transfer.
Water-tube boilers offer quick startup and response time to changing conditions with very little standby loss. By design, comparatively little water passes through the heat exchanger; this translates into a smaller footprint and broader range of capabilities and output ranges.
“Their ability to make steam, or hot water, very rapidly, from a cold start, and without damaging the boiler is a beneficial asset,” said Lane Blackwell, Sales Engineer, Service, for Peru, Ind.-based Thornton & Associates,. Inc., a manufacturer’s rep firm. “This is valuable in applications where the systems aren’t running 24/7.”
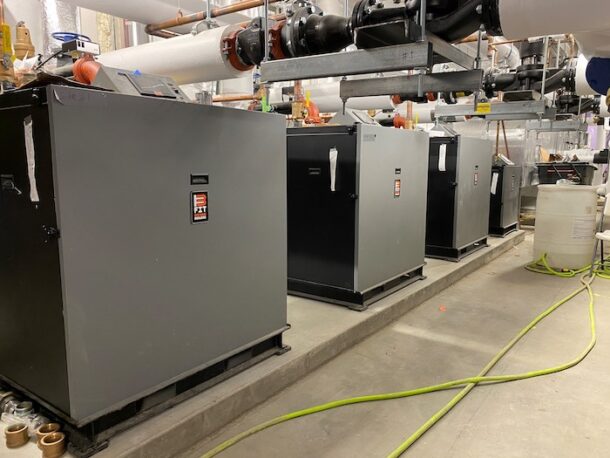
Bryan Boilers’ BFIT commercial condensing water-tube boiler series is a stainless steel, modulating-condensing boiler line with ranges from 1,000-4,000 MBH with optional racking system. Image courtesy of Bryan Boilers.
Because the burner in a water-tube boiler is located centrally, most water-tube designs provide higher temperature outputs and higher operational pressures than fire-tub boilers—key advantages for process heating application. Another advantage to the design of these systems is that, as a result of the requirement for water to flow continuously during operation, hot spots in the heat exchanger don’t threaten the operation or lifespan of the boiler.
Water-tube heat exchangers also operate at higher pressures, a capability that can—for steam-producing systems—produce saturated or superheated steam depending on the design and application they’re required for.
Blackwell also points to the advantage of water-tube maintenance, “Or, rather, lack of it. A surprisingly high number of water-tube systems may go several years without more than occasional attention to the water quality [within them], he said. “And, if there would be a need to replace individual tubes, that can be accomplished with hand tools; no rolling or welding. It’s not uncommon for a well-maintained water-tube boiler to last 40+ plus years with little maintenance.”
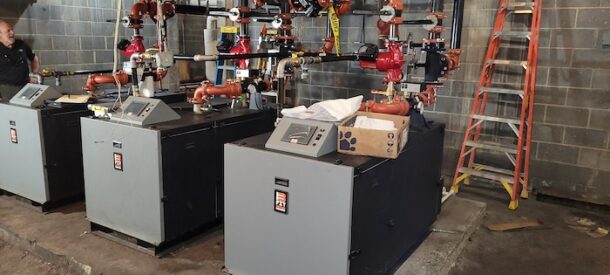
– Bryan Boilers’ BFIT commercial condensing water-tube boiler series is a stainless steel, modulating-condensing boiler line with ranges from 1,000-4,000 MBH with optional racking system. Image courtesy of Bryan Boilers.
“A few years ago, we specified two non-condensing water-tube boilers for a high school expansion project in Cass County [IN],” added Blackwell. “The boilers were 72 and 50 HP in size, and it wasn’t long before facility managers found that they could provide heat for the rest of the school with them, so they decommissioned two old, enormous—and way oversized—firetube boilers. The following year, they added another 100 HP water-tube system and, within a few years, they verified 30 to 40 percent annual fuel savings. I could reel-off countless instances where water-tube boilers have exceeded expectation.”
Water-tube systems are designed to work with high-ash fuels that, when combined with soot blowers, typically meet environmental regulations. This also means that they’re well-suited for biomass applications and waste-to-energy plants.
The primary factor that determines heat transfer is the heat transfer coefficient, based on the transfer fluid’s flow pattern, characteristics and chemistry (including density, conductivity and viscosity), geometry of the flow passage, and surface conditions. Of these factors, the most important to thermal efficiency in a water-tube boiler is flow through the water tubes and the fluid’s velocity and density. When all of these variables are optimal, water-tube boilers provide exceptionally reliable operation, while offering performance and efficiency that is difficult to match with any other heat exchanger design.
For these and other reasons, water-tube boilers are the equipment of choice for many industrial process applications. Their ability—in a steam boiler configuration—to handle greater pressures and very high temperatures provides superior steam generation in the millions of pounds/hr.
Caveats
Most advantages come with a counterbalance; water-tube boilers are no exception.
The initial cost for a water-tube boiler is usually higher than that of a fire-tube boiler of similar capacity. And, depending on size, some water-tube boilers can be assembled on site, which can add to the cost and the time required for installation.
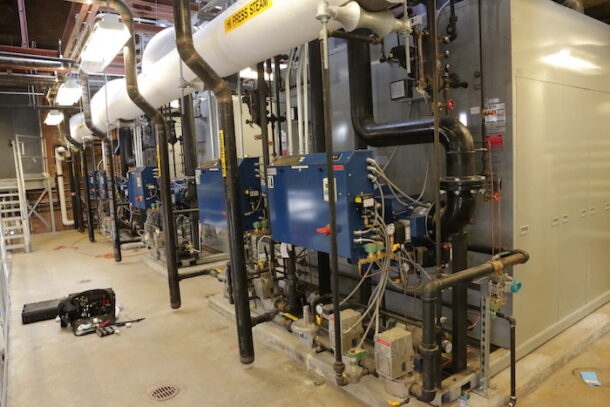
Bryan’s RV600 flexible water-tube steam boilers are a great fit for many commercial heat or process steam application. The systems offer 3,500,000 to 8,000,000 BTUH with forced-draft gas, oil or dual fuel. Image courtesy of Bryan Boilers.
By design, the concern of heat transfer fouling—typically in the form of accumulated mineral scale—is heightened. For that reason, fill-water quality and the steady monitoring and maintenance of water chemistry are essential to peak operation.
The accumulation of scale is by no means specific only to the water-tube design. Scale can accumulate faster because of the water-tube boiler’s lower water mass, but it’s still a concern across all heat exchanger types. “But, reduced water volume also equates to savings on chemical treatment,” added Blackwell.
Finally, the reduced volume of water affects the water-tube boiler’s ability to meet the call for sudden changes in heat demand. This shortcoming is often remedied by the addition of an indirect water storage tank.
Fire-tube advantages
Advantages include their simple construction and the ability to easily meet rapid fluctuations in the need for heat. As a lower cost alternative to water-tube boilers, they’re often used for smaller commercial or industrial facilities with lower operating pressures.
Fire-tube boilers are designed with water in the unit’s main vessel, achieving higher mass. Because of their higher water volume, system design also offers the benefit of a less urgent need to maintain tight control of water quality. If water quality deteriorates and isn’t corrected quickly, there’s less chance— when compared to water-tube technology—that system performance will be affected.
Another advantage to fire-tube boilers may be lower upfront cost. “However, said Blackwell, “In our market, there’s very little, if any, difference in pricing.”
Caveats
A fire-tube boiler’s higher water volume and lower flow rates also mean that they may offer less efficient heat transfer. Likewise, the greater water volume requires a longer wait for system start-up, and may also challenge the boiler’s ability to meet demand for constant water flow—and heat transfer—at peak conditions. Standby losses are greater because of the boiler’s higher volume of water.
The main disadvantage of fire-tube boilers is that they tend to have smaller capacities and can’t handle internal pressures over 250 psig (the steam capacity range of fire-tube steam boilers is approximately 5,000 to 75,000 pounds/hr.) Or, if configured as a hot water boiler, hot water capacity is between 2 million to 100 million BTUs.
Traditional, horizontal fire-tube steam boilers may offer a capacity as low as 690 pph—pounds (of steam) per hour. Traditional fire-tube steam boilers in a vertical configuration will go smaller—offering as little as 207 pph, for example.
Boiler Safety—be warned
Operationally, water-tube boilers are known to be safer than fire-tube systems. This is because of the much greater volume of water held within fire-tube boilers—containing as much as 10 times the volume of a water-tube boiler of similar capacity.
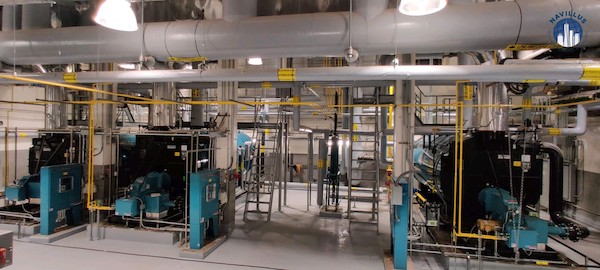
Burnham Commercial Boilers offers a convenient solution with efficient, easily portable, mobile boilers. Image courtesy of Burnham Commercial Boilers
When fire-tube boilers are inadvertently operated with low water volume, very dangerous risks can develop. Initially, the metal in the boiler warps and contracts. Then, if cold fill-water enters the boiler in a hot, low-water condition, the metal could rapidly expand, causing an explosion.
Should a similar scenario take place in a water-tube boiler with lower internal water volume, an explosion would be much less severe. In most instances— should fill-water enter a hot water-tube boiler with an insufficient fluid level— conditions would likely lead to metal fatigue, a crack, and leakage.
Service and maintenance
Some boiler designs are built to facilitate ease of service and maintenance. The assumption, however, is that a newly-installed boiler is ready for the rigors of duty, 24-7-365. Yet, all mechanical equipment is not created equal. Service and maintenance work ideally happens systematically to maintain optimal performance and efficiency—not to deal with challenges that arise as a result of faulty or compromised design.
Commercial boilers should be designed to ensure long-term durability and optimal performance. Ideally, the burner is mounted front and center, fully accessible and serviceable. Removable panels around the boiler should provide access to the burner chamber and entire heat exchanger. There should be no need to disconnect blowers or gas piping.
Commercial Condensing Systems
As with all technology, improvements emerge to enhance operation, durability or efficiency. The emergence of condensing capability—often going hand-in-hand with “turn-down” (or modulation, offering very efficient, partial firing)— are the most substantial enrichments to boiler systems in decades.
Condensing boilers are based on a remarkably simple concept. They achieve higher efficiencies by condensing the flue gasses. In contrast—in a conventional boiler, latent heat contained in the flue gas escapes through the flue vent. They’re also quite effective at reducing NOx, COx and other harmful emissions.
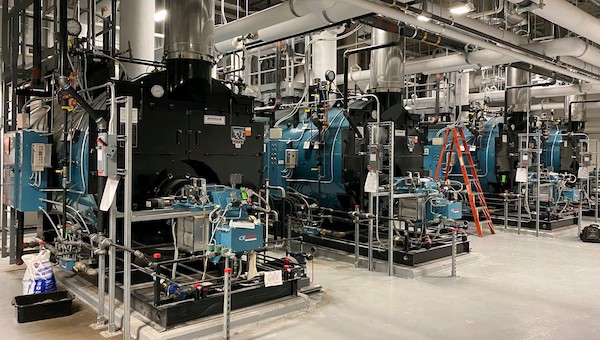
Burnham Commercial Boilers offers a convenient solution with efficient, easily portable, mobile boilers. Image courtesy of Burnham Commercial Boilers
Modulating condensing boilers (AKA “mod-con” boilers) earned “greatest achievement” recognition as a result of their dramatic contribution—pushing fuel efficiency from 80 percent for non-condensing boilers, and up into the 90+ percent range for mod-con systems. Condensing water-tube boilers achieve efficiencies of up to 98 percent, higher than most condensing fire-tube systems—a result of their better heat transfer. With modulation, they provide a range of firing rates to match the variable heating load of the building.
However, mod-con boiler efficiency depends on the temperature of the water returning to the boiler. The lower the return water temperature, the higher the efficiency. Low boiler return water temperature depends on the overall boiler system design, not just the boiler.
Condensing boilers cost 40 to 50 percent more, on average, than conventional systems. However, the difference in cost is typically recovered in four months to four years, depending on a wide range of variables. Substantial cost-saving incentives may apply.After the initial cost recovery period, the fuel savings are quite significant over the life of the boiler.
There are a few disadvantages. For instance, one fire-tube boiler design change involved the arrangement of internal tubing from a horizontal format, to vertical. The revision was warmly welcomed by facility owners and installers alike because their now-smaller size permitted movement through a standard door frame. As a result, the products of combustion and condensate were redirected: rather than gradually absorbing heat as flue gas passes through tubes, the contemporary vertical fire-tube burner sits inches away, forcing heat directly on the tube sheet, welds, and tube tops. All materials expand and contract as they’re heated and cooled, and these internal components of the vertical fire-tube boiler are no exception. The design tends to concentrate too much heat on metal components.
Cleanings and reparability
If a condensing boiler’s panels are easily removed, providing complete access to the entire heat exchanger, byproducts of combustion can be easily removed with a service brush. This is an important facet to maintaining a boiler’s original high-efficiency rating.
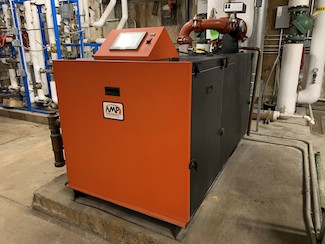
A Thermal Solutions AMP water-tube boiler is rated at 97% efficient. The stainless steel, modulating-condensing boiler line offers a size range of 1,000-4,000 MBH.
Should repair work be required, all components of the heat exchanger should be easily accessible for service or replacement—including even the possibility of changing one or more internal tubes in the field.
With properly isolated equipment, service work could and should be completed within hours, not days or weeks.
Systems that offer the greatest resistance to cleaning are those with tight, top access and—when opened—may have many welded tubes. Those that do typically require entirely new heat exchangers, sometimes costing as much as 60 percent of the original install.
Knockdown rewards
Knockdown condensing boilers were, for good reason, greeted enthusiastically by the commercial market. Some of these systems use no welds in securing tubing to the header.
The “knockdown” moniker stems from the ability to assemble or disassemble a boiler of any size with relative ease and precise repeatability. The systems arrive on jobsites, similar to old cast iron sectional boilers, or partially assembled based on space requirements.
Even elevator weight constraints pose no challenge to getting the boilers in place. If there’s a need to maximize mechanical room space, some systems are available with reverse construction models to optimize clearance space between units or to be placed side by side, to be serviced from outside.
Greg Hughes is the Internal Sales Manager, Thermal Solutions and Burnham Commercial. He can be reached at ghughes@heatingsolutionssales.com
Additional sources:
Jim Knauss – jknauss@burnhamcommercial.com (retired but now consulting) Engineer for Burnham Commercial (firetube merits)
Joe Tinney – jtinney@heatingsolutionssales.com Internal Sales Manager for Bryan Boilers (watertube merits)
Rick Constantino (rconstantino@bresales.com) – Owner/COO Boileroom Equipment Company
Theodore (Ted) Dreyer (TDreyer@WHGardiner.com) – Sales for Gardiner
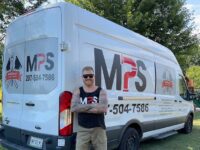
Welcome to another edition of our Hub Spotlight series where do a deep dive into the men and women who make the trades great. This spotlighted tradesperson tells us that he really enjoys trashy reality TV. “Nothing like kicking your feet up and watching someone making horrible life decisions on 90-Day Fiancé on a Sunday Read more
Welcome to another edition of our Hub Spotlight series where do a deep dive into the men and women who make the trades great. This spotlighted tradesperson tells us that he really enjoys trashy reality TV. “Nothing like kicking your feet up and watching someone making horrible life decisions on 90-Day Fiancé on a Sunday evening.” Joking aside, for Keith McGillivary (@mps_207)—full-time business owner of McGillivary’s Plumbing Services (MPS), Gardiner, Maine, for the past two years—his story into the plumbing trades is an interesting one.
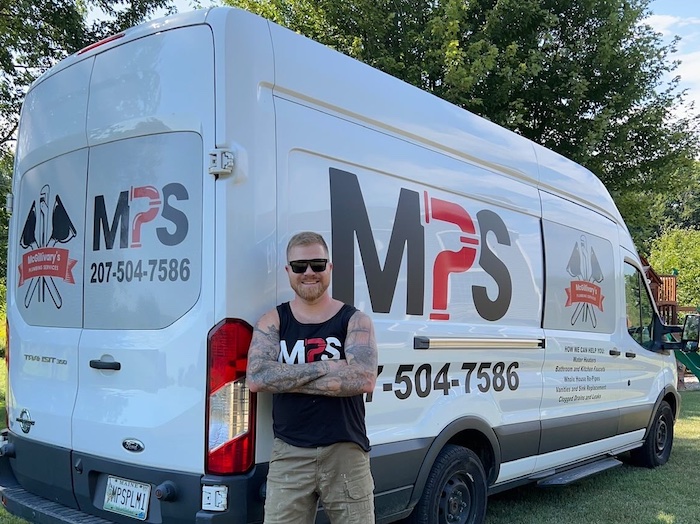
McGilivary’s path started in a small town when a small plumbing business was looking for a helper, and he was looking for a job. “Little did I know it would be the start of where I am now,” says McGillivary. Before college, McGillivary started working for a small plumbing business that primarily focused on service work. The owner, Russell, was/is a great mentor and really took the time to help him understand not only what they were doing, but why they were doing it.
After deciding to pursue plumbing, McGillivary attended Southern Maine Community College (SMCC) for its plumbing and heating program. Through college, he continued to work alongside his mentor, and after graduation, continued to work for him full time for three years. McGillivary then took a job at Bath Iron Works (BIW) as a pipefitter building destroyers, ships for the United States Navy. “The piping systems were complex, and although it was “plumbing on a ship,” it was completely different. I found it fun to learn the ins and outs of that particular plumbing,” says McGillivary.
Eventually, McGillivary joined the Pipefitter Test Crew and tested the piping systems after they were built. He worked there for six years, but the whole time he continued to work nights and weekends doing plumbing work on the side. “This allowed me to gain hours and knowledge for my Master’s test. After passing my Masters, I decided to make the plunge into self-employment because I wanted the schedule flexibility for my family,” says McGillivary.
In fact, McGillivary’s biggest motivation for self-employment was time, rather than money. “I have learned to set firm boundaries for myself when scheduling and taking on jobs. I have been able to take more time off for my family than ever. Being a service plumber, in this day in age, you could work 24/7 if you wanted. I try to work ‘normal’ hours, and if I can take a day off for family stuff, I always do,” says McGillivary.
Shout Out to Mentorship
According to McGillivary, Russell taught him everything he knows about plumbing and owning a business. “He taught me all the hands-on work, how to write estimates & bid on jobs, customer relations, and how to balance a small business/family life,” says McGillivary.
And McGillivary wants to pay it forward. “I definitely consider myself a role model for others looking to join the trade. I feel I am a good example that hard work and dedication pays off,” says McGillivary. “My mentor was so important to my journey that I try to give back what I can by being transparent about my plumbing knowledge.”
Uplifting the Trades
Recently, there has been a big push for kids to attend trade school so there has been a shift in younger people showing interest, says McGillivary. “Trade school was beneficial for me to learn the code side of things, in an environment different from the hands-on work. I think we could get more interest in the trades if the schools showcased all the different avenues someone could go once they completed their schooling, and the financial opportunities that come with them. Everyone expects a doctor to make six figures, but not everyone knows you can make that in the trades without massive student loan debt,” says McGillivary.
“Everyone expects a doctor to make six figures, but not everyone knows you can make that in the trades without massive student loan debt.”
Social media can also be used to attract more people to the trades. “I see it all too often when guys in the trade are way too harsh on people for asking questions on Facebook plumbing pages. There are so many people asking questions for the purpose of learning and gaining knowledge. We were all there at some point, so be kind enough to answer the questions in a helpful manner. Social media can also be used to form “new-to-the-trades” communities and to provide seminars,” says McGillivary.
Social media also has played a huge role in the growth of McGillivary’s business. Starting as a small, part-time business with the help of word-of-mouth recommendations on small town Facebook pages, which made McGillivary realize that social media could be used to showcase the work he is doing on a day-to-day basis. “I use my Instagram to show what I am about as a business and the work I put out. I have found that if a customer can see why you are more expensive than the other guy, then they are more likely to go with you. I use it as an open-door insight to my business both in reels and daily stories,” says McGillivary.
McGillivary uses social media to learn little tricks of the trade that he just wouldn’t have been exposed to, being from such a small town. For McGillivary, it is extremely beneficial to be able to have conversations with such great tradesmen. He also talks to apprentices daily or weekly about projects, and gives them advice. “I wish when I was learning, I had this platform to learn and meet others. As visual learners, much like a lot of trades guys I know, it’s changed the way we can learn,” says McGillivary.
Making Time
Summers in Maine are short, so McGillivary tries to spend every nice weekend camping in his camper. In the winter months you can find him on his snowmobile at camp. “I would love to ride my snowmobile from camp in northern Maine to the Gaspe Peninsula to complete the “Great Gaspe Snowmobile Tour,” a six-day, 1,500-mile ride around some of the best trails,” says McGillivary.
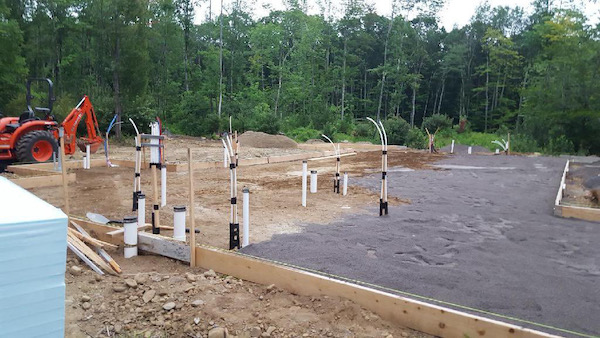
And the last day McGillivary said it was a great day? “You know it’s funny, as I look back on just yesterday—camping with my family, beautiful weather, everyone smiling, does it get much better than that? So, the answer to that question would be yesterday!”
Go-To Tools on the Job
According to McGillivary, his go-tools are a couple pairs of Knipex Cobra pump pliers, a 6-in-1 screwdriver, and an adjustable wrench. Any good service plumber can fix most things with those!
Also, I find myself feeling naked if I don’t have my Leatherman Wave on me. Another great tool that has many uses.
Lastly, if there was one tool that changed the service plumbing game, it’s the M12 Milwaukee press tool. If you’re running a service company and don’t have one, you’re late to the party.
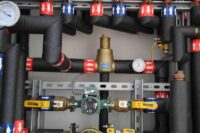
The word separation was being used in hydronic circles back when I started in the business. Of course, I am old, so there is that. Many manufacturers and trainers are in the separation bandwagon now, rightfully so, from my view. Let’s take a look of how the word and the technology come together. The action Read more
The word separation was being used in hydronic circles back when I started in the business. Of course, I am old, so there is that. Many manufacturers and trainers are in the separation bandwagon now, rightfully so, from my view. Let’s take a look of how the word and the technology come together. The action of moving of being moved apart will work to describe the value of separation in hydronics or piping systems in general.
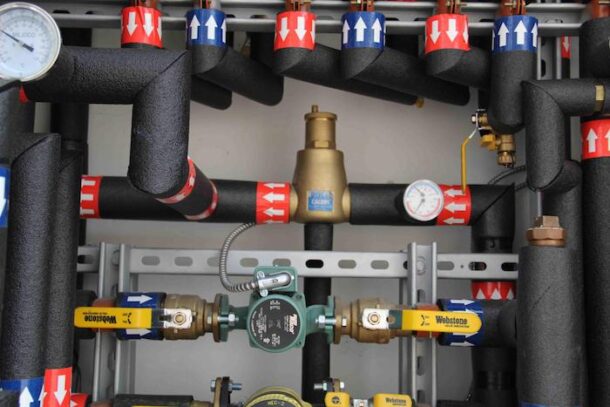
Photo: Bayshore House (Newport Beach, CA) Submitted by: David Mayo
Back in the day, we used a device called an air purger. We’ve all seen them, sometimes described as a camel hump. Commonly made from a casting, the “air purger” basically builds a wide spot in the road. As such, as fluid flows through it, the speed or velocity slows. Slowing the fluid allows air to rise up to the top of the “hump” to be vented away. It can, and does, some air removal in a system. A few important details. It likes to have some straight piping upstream, maybe 18” or so. This helps get the air going to where it can best be removed, at the top of the piping.
The velocity or speed is also critical. Water or fluids, flowing above 4 fps feet per second, tend to blow through the camel hump like bad leaves in the desert. Lastly, they have a tougher go grabbing the micro bubbles. If you fill a glass at the kitchen sink and notice cloudy water at first, those are micro bubbles. In your glass, since the top is open, this air escapes. It escapes quickly as the pressure has been taken off the fluid form when it was captive in the piping under 60 psi, or some pressure.
Some smart fellow decided there must be a better way to rid 95% or more of all air out of a closed loop piping system. The wide spot in the road had validity. Why not put something inside that wide spot to aid the collection. The microbubble resorber was born. The “stuff” in the chamber becomes a coalescing media. Simply the air bubbles, of all sizes cling to the media inside instead of blowing through like grass through a goose.
The concept works amazing well. Air can be successfully removed in a matter of minutes or hours on larger systems as it passes across the coalescing media. The microbubbles that were present in systems with camel humps, now have been captured and removed.
View this post on Instagram
Why all of a sudden is this so “in Vogue”? High efficiency boilers are one great reason to use microbubblers. The fluid content is way down, the HX metals are much thinner, and the flame is in close proximity to the boiler wall. As such, any layer of micro bubbles stuck on the metal surfaces reduce or impede the energy from the flame getting to the fluid. You have a miniature bubble wrap layer around the boiler surfaces if you are not getting the small air gone.
You may have seen failed mod con boilers. Darkened, brown or black metal instead of shiny stainless or aluminum. That HX has been overheated. Often lack of flow is to blame. And also, often the lack of flow is related to air bubbles slowing or stopping the perfect contract between fluid and hot metal surface. You take an efficiency hit also when you have this going on in your boilers. Circulators, the wet rotor type, especially like to be free of air, both from a performance and lubrication standpoint.
So, doesn’t it make sense that the same phenomena happen in your heat emitters? Microbubble air layers in your radiators, fin tube, air handler coil, coil in your indirect tanks.
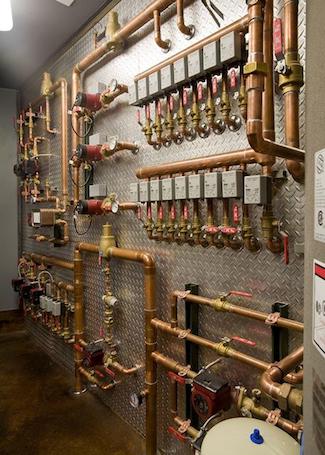
Telluride Custom Home (Telluride, CO) Submitted by: Pete Cassidy
The microbubble resorbers aka air separators bring a few other advantages. They do not require straight piping upstream to work efficiently. This can be a big asset when you need to cram 10 lbs. of potatoes in a 1-pound sack, i.e., small mechanical closets. They are not as sensitive to over-pumped conditions, high velocities above 4 fps for example. The large chamber combined with the media inside work together to grab bubbles from speeding fluids. They are brass or composite construction, so corrosion issues are mitigated. Ever see a camel hump with the air vent port rusted close when you pull the 1/8 auto vent off the top? It was handicapped from first installation; the plugged vent hole renders it a “boat anchor.”
Yeah, I know they cost more than a chunk of iron than your great grandfather used his entire career, but times have change, my friends. Why not give your customers a system with the very best equipment and conditions to be highly efficienct. A simple device that removes 95% of air in systems almost instantly is what you need to consider.
So, you took my suggestion and STILL have an air/ noisy system. Now what? Look for places where air is getting in. Yes, air can enter a closed loop system, even a pressurized one. Those float type auto air vents allow air to move in both directions, in and out. IF one were to be installed in a point in the system that sees sub-atmospheric conditions you are seeping air into the loop. The most common occurrence is when you have the expansion tank misplaced. This can get worse with high heads circulators creating large pressure differential. The tank MUST be on or near the suction side of the circulator(s) to avoid pulling a vacuum in your system. Make it right or cap off auto vents in the negative pressure part of the system.