https://vimeo.com/1029812860 On this Mechanical Hub weekly update, we’re on the road in Elkhart, Indiana to celebrate NIBCO Inc.’s 120 years in business, and another huge surprise from that event. I’ll update you on our latest podcasts, and a partnership worth sharing Read more
Featured Articles
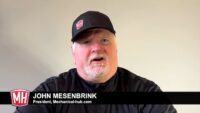
On this Mechanical Hub weekly update, we’re on the road in Elkhart, Indiana to celebrate NIBCO Inc.’s 120 years in business, and another huge surprise from that event. I’ll update you on our latest podcasts, and a partnership worth sharing.

Elkhart, Indiana-based NIBCO Inc. celebrated in style this week as esteemed guests were invited to dinner, drinks and dancing in what was a wedding reception-like ceremony that included a multi-piece band. The following day, invitees were treated the ribbon cutting of the new Rex Martin NIBCO Interactive Museum, and took the tour. The museum offers Read more
Elkhart, Indiana-based NIBCO Inc. celebrated in style this week as esteemed guests were invited to dinner, drinks and dancing in what was a wedding reception-like ceremony that included a multi-piece band. The following day, invitees were treated the ribbon cutting of the new Rex Martin NIBCO Interactive Museum, and took the tour.
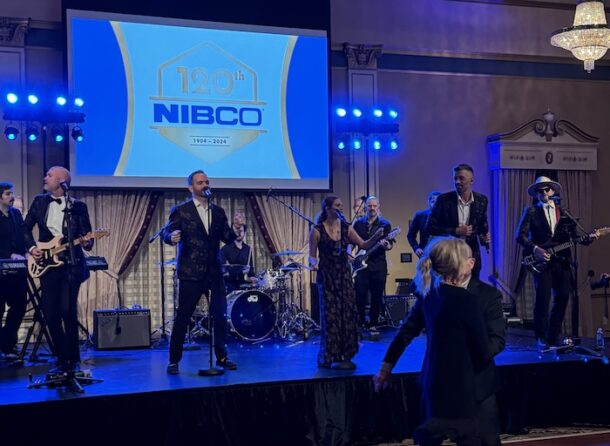
The museum offers a unique and enriching experience from a historical perspective, interactive learning, inspiration, community impact, and career opportunities. Not just a place to learn about the past, it’s a place to get excited about the future of plumbing and the opportunities it holds.
“Our decision to build the NIBCO Interactive Museum and name it after my father is a tribute to his remarkable contributions to the plumbing industry and a continuation of a legacy that began with my great-great-grandfather in 1904,” said NIBCO’s President and CEO Ashley Martin. “This ambitious project was something I wanted to complete and dedicate on NIBCO’s 120th anniversary to make it extra special. The museum is not just about preserving our history; it’s about showcasing the profound impact we’ve had on the evolution of plumbing and our philanthropic efforts within the community.”
Martin continued, “I want our NIBCO associated, our customers, local school kids to be able to come here and use this so it needed to be interactive. We also highlighted plumbing: where our products go, how they bring water to you, take waste away, but it also highlights our four manufacturing processes—plastics, copper, bronze and iron.”
The museum offers a unique and enriching experience from a historical perspective, interactive learning, inspiration, community impact, and career opportunities. Not just a place to learn about the past, it’s a place to get excited about the future of plumbing and the opportunities it holds.
Artifacts, representing various aspects of the history of plumbing, as well as the history of NIBCO, are exhibited throughout the museum, including:
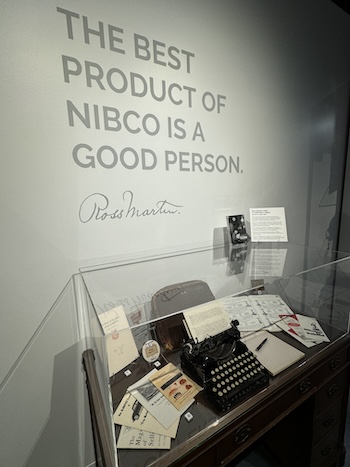
- Early foundry tools
- Original crown jewels of NIBCO
- Original early fittings including the first fitting from 1927 and early valves
- Original product blueprints from the 1930s
- Items from Lee Martin’s collection
- Original printings of Ross Martin’s collection of booklets
- Philanthropic contributions
- Collectibles and promotions
The 8,845-square-foot building was completely renovated beginning in 2023. The museum portion of the space is 3,254 square feet, and additional space in the building will be used as a training area for customers, distributors, and NIBCO associates.

https://vimeo.com/1027108697 On this update, we’ll talk PFAS, our podcasts where on the Make Trades Great Again, Eric and Andy shift from shop talk to van talk, and on the Appetite for Construction podcast, Tim and John talk with Ryan Shikhman about Trades Over College, and we update you on what’s trending on social media the Read more
On this update, we’ll talk PFAS, our podcasts where on the Make Trades Great Again, Eric and Andy shift from shop talk to van talk, and on the Appetite for Construction podcast, Tim and John talk with Ryan Shikhman about Trades Over College, and we update you on what’s trending on social media the past few weeks.
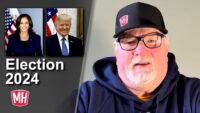
https://vimeo.com/1025087361 We hope you all had a great Halloween with plenty of little visitors dressed up in their most creative costumes. This week we’ll talk presidential election, where the race for the White House is certainly heating up. Key battle ground states are still undecided. If you haven’t already, get out and vote. Election day Read more
We hope you all had a great Halloween with plenty of little visitors dressed up in their most creative costumes. This week we’ll talk presidential election, where the race for the White House is certainly heating up. Key battle ground states are still undecided. If you haven’t already, get out and vote. Election day is next Tuesday.

https://vimeo.com/1022947522 This week we talk ASPE, which just took place this week actually. Tim Ward gives an update from the show floor and we visit with our friends from Uponor. We have a new Contractor Spotlight on the site. We talk American Plumber Stories Season 5, Episode 2. And, of course, we’ll talk podcasts Read more
This week we talk ASPE, which just took place this week actually. Tim Ward gives an update from the show floor and we visit with our friends from Uponor. We have a new Contractor Spotlight on the site. We talk American Plumber Stories Season 5, Episode 2. And, of course, we’ll talk podcasts.