Electrode boilers are ideal for quickly, efficiently supplying auxiliary steam and hot water to meet surges in demand In industry, fossil fuel-fired boilers are commonly used to produce steam or hot water for space and process heating. However, traditional boilers may not be flexible enough to respond quickly to demand surges during peak periods. To Read more
Featured
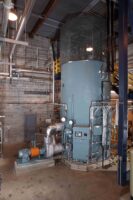
Electrode boilers are ideal for quickly, efficiently supplying auxiliary steam and hot water to meet surges in demand
In industry, fossil fuel-fired boilers are commonly used to produce steam or hot water for space and process heating. However, traditional boilers may not be flexible enough to respond quickly to demand surges during peak periods.
To compensate, processors and manufacturers often keep more than the required number of boilers running – usually at less than full capacity. When more steam or heat is required, the units are already in operation and so require less time to increase output. Even if burning at 75% however, fossil fuel boilers take time to heat up internally.
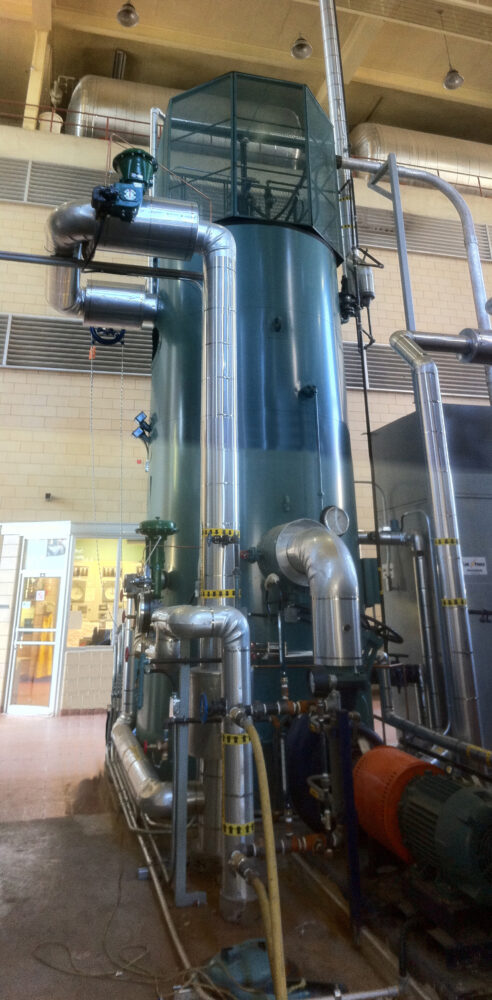
Using electrode boilers as an auxiliary system minimizes the number of gas-burning boilers on standby, provides greater operational flexibility, and reduces operating and maintenance costs.
“If you want to use a gas-fired boiler as an auxiliary, you’d better know in advance when you will need it since it takes time for the heat to rise and disperse before reaching the target output [of steam or hot water]. If you have gas-fired boilers run at 75% capacity and there is an increase in demand, you cannot quickly reach 100% capacity, says Robert Presser, Vice President of Acme Engineering, a manufacturer of industrial and commercial boilers with operations in the U.S., Canada, and Europe.
Today, a much more efficient and cost-effective approach is available: auxiliary electrode boilers. These modern electrode boilers can almost immediately provide supplemental steam or hot water as required. The approach minimizes the number of gas-burning boilers on standby, provides greater operational flexibility, and reduces operating and maintenance costs.
The components of these auxiliary high-voltage electrical systems – boilers, superheaters, secondary pressure vessels, and associated control systems – are readily available from experienced suppliers and can be customized to specific industrial needs.
“A gas-fired boiler cannot go from zero to 100% capacity in less than two minutes – but an electrode boiler can,” says Presser. He points out that modern electrode boilers are designed so temperature, pressure, and output can quickly rise or fall as needed with no “flywheel effect.”
Electrode boilers have existed in various forms for many decades. However, recent design improvements have closed the output gap while surpassing conventional units not only in terms of efficiency and simplicity but also responsiveness and safety.
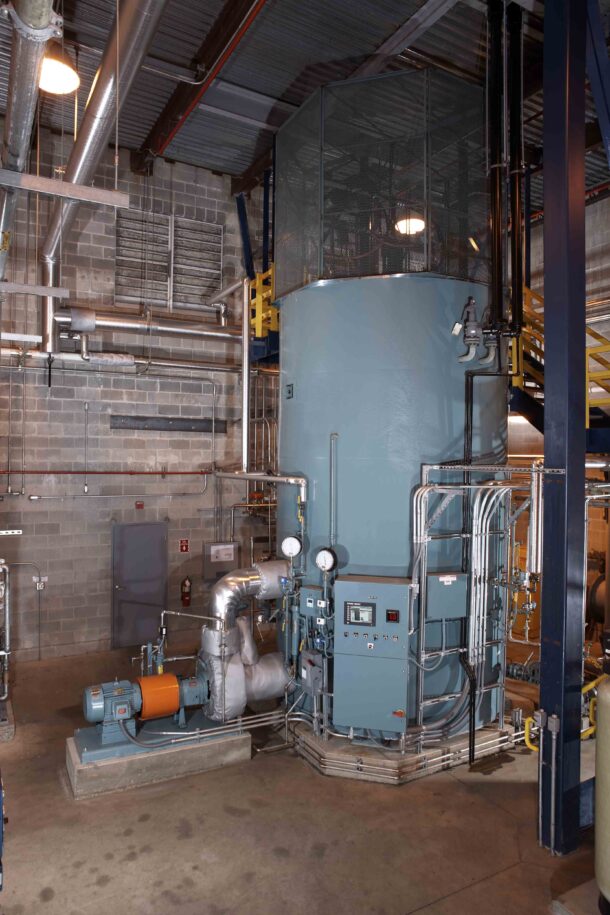
Electrode boilers like those from Acme Engineering are ideal for quickly and efficiently supplying auxiliary steam and hot water to meet surges in demand.
Modern electrode boilers utilize the conductive and resistive properties of water to carry electric current and generate steam. In a jet boiler, water jets flow from a central column to electrodes of each phase, using chemicals in the water to create resistance and generate heat and steam as the water passes from ground to phase. More steam is produced as the water flows from the electrode to the counter electrode placed below the electrode box, before the water returns to the reservoir at the bottom of the vessel.
“The more current [amps] that flows, the more heat [BTUs] is generated and the more steam produced. Nearly 100% of the electrical energy is converted into heat with no exhaust stack or heat transfer losses,” says Presser.
As an example, in the CEJS High Voltage Jet Type Steam Boiler from Acme Engineering, the electrodes are vertically mounted around the inside of the pressure vessel, which enables the unit to produce maximum amounts of steam in a minimum amount of floor space.
The electrode boilers operate at existing distribution voltages, 4.16 to 25 KV with exceptional efficiency – up to 99.9% efficient at converting energy into heat. The boilers can produce steam in capacities up to 270,000 pounds per hour, with pressure ratings from 75 psig to 500 PSIG. All CEJS boilers are designed to ASME Code or EU Pressure Vessels Directive and are certified, registered pressure vessels. Electrical standards meet CSA, UL, or CE requirements.
The advanced steam boilers have a 100% turndown ratio, the ratio between a boiler’s maximum and minimum output. Most gas boilers have a 10:1 or 5:1 ratio.
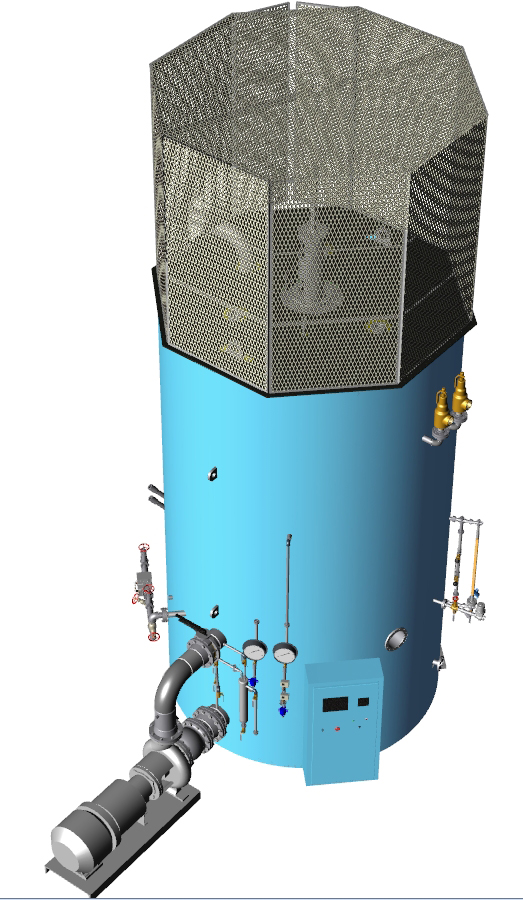
Modern electrode boilers can go from zero to 100% capacity in less than two minutes, almost immediately providing supplemental steam or hot water as required.
“The turndown means you can leave the boiler in standby at low pressure and, when needed, bring it to full capacity in about 90 seconds, which no other boiler type can achieve today,” says Presser. “With the electric boilers, the energy input and adjustment are very precise and virtually immediate.”
The ability to rapidly increase or decrease boiler capacity “on demand” can save industrial processors and manufacturers a substantial amount in operational and maintenance costs.
“Instead of running five gas-fired boilers on moderate capacity, you can run three or four boilers at full capacity, which maximizes their efficiency, and have an electrode boiler on standby. The electrode boiler can be used in short bursts only when you need peak performance. This is less expensive than running more gas-fired boilers,” says Presser.
The economics of using auxiliary electrode boilers further improve when utilizing discounted off-peak electricity at night when demand is low.
Electrode boilers also lower the costs of installation, operation, and maintenance. Gas-fired boilers require fuel lines, storage and handling equipment, economizers, and emission control equipment. Advanced jet type electrode boilers have a minimal number of components and electrical controls, with fewer parts. Under normal operation, the absence of excessive temperatures and electrode burnout assures long operating life.
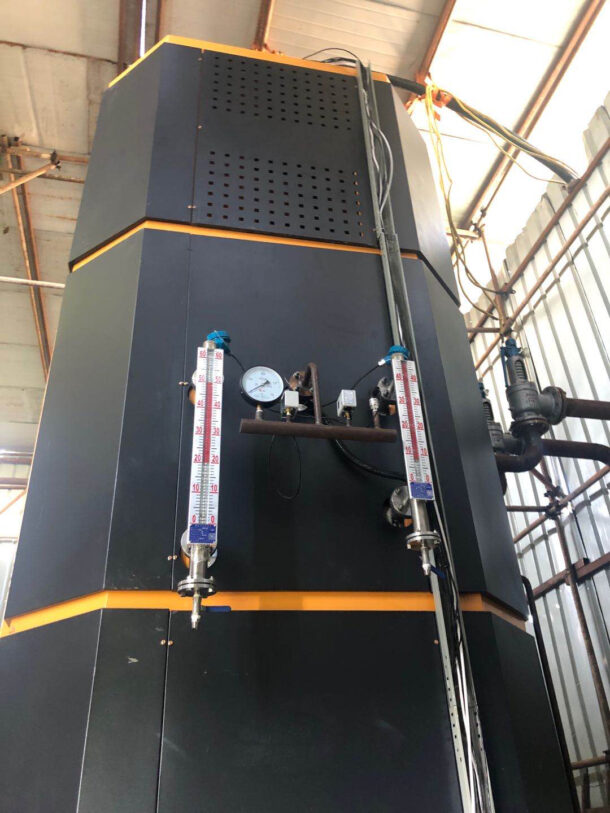
Advanced jet type electrode boilers have a minimal number of components and electrical controls, with fewer parts, resulting in the absence of excessive temperatures and electrode burnout.
The units further lower operating costs with automatic controls that reduce the need for operating personnel.
Presser points out that the most advanced types of these boilers, such as Acme’s CEJS, also operate more safely than traditional fuel burning models.
“With the jet type electrode boilers, there are no combustion hazards because there are no flames, fumes, fuel lines, storage tanks, or hazardous emissions. There are no problems with heat buildup or electrode burnout even if scaling should occur, and thermal shock is eliminated. There is also no ‘low water’ danger since the current cannot flow without water,” says Presser.
With all the advantages of high-output auxiliary electrode boilers, industrial processors and manufacturers that utilize them will have a competitive advantage over rivals relying on gas-fired boilers alone.
The flexibility, precision, and responsiveness of electrode boilers will allow cost-effective “on demand” steam and process heating, eliminating the need for extra traditional units to be continually kept online at low capacity, ready to be “fired up” during peak periods. This approach will minimize operating costs including energy, labor, and maintenance.
For more info, contact Robert Presser at Acme Engineering via e-mail: rpresser@acmeprod.com; phone: (888) 880-5323 or (514) 342-5656; or web: https://www.acmeprod.com/jet-type-steam-boiler .
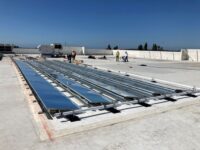
With energy costs up more than 50% over the past year and a half and forecasters expecting those numbers to remain high through 2024, commercial building owners and engineers are seeking alternatives to effectively condition large spaces in a more energy-efficient manner. This challenge has opened the doors for a new cooling-panel technology that significantly Read more
With energy costs up more than 50% over the past year and a half and forecasters expecting those numbers to remain high through 2024, commercial building owners and engineers are seeking alternatives to effectively condition large spaces in a more energy-efficient manner.
This challenge has opened the doors for a new cooling-panel technology that significantly decreases energy consumption and demand charges associated with cooling to maximize sustainability for higher-performing buildings.
The patented radiative cooling system essentially works opposite a solar panel system. Instead of harnessing energy from the sun, the cooling panels feature a multilayer film that reflects sunlight and emits infrared heat to the atmosphere, keeping the panels extremely cool — up to 15°F below the ambient temperature. A closed-loop hydronic piping system circulates a water/glycol mixture that brings warm water to the panels for cooling and then returns the cooled fluid back to the building’s existing HVAC system.
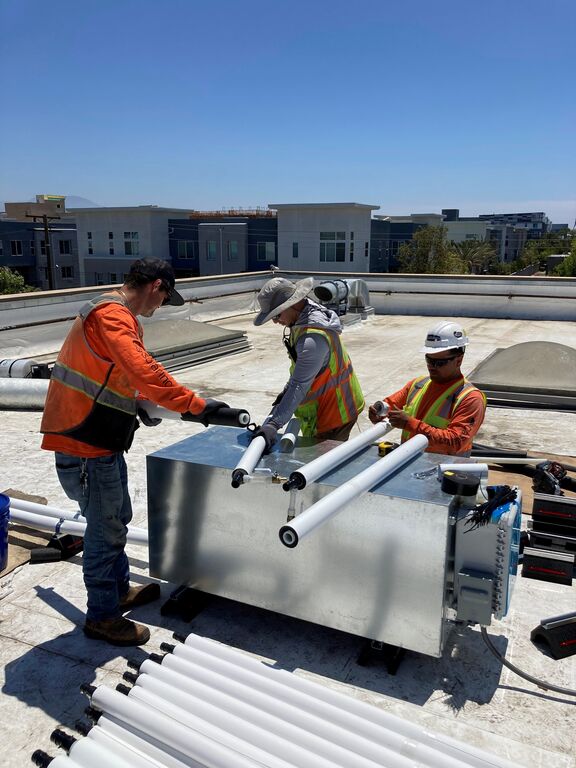
Installers insulate and jacket straight lengths of Wirsbo hePEX pipe to protect it from UV exposure.
“The system has the potential to yield up to 40 percent energy efficiency when added onto existing air conditioning and refrigeration systems, and the typical project is saving about 1,000 kilowatt hours per panel per year,” says Eli Goldstein, co-founder and CEO of SkyCool Systems, the company behind these radiative cooling panels.
The distribution piping system that connects to the panels consists of an oxygen-barrier crosslinked polyethylene (PEX) pipe called Wirsbo hePEX™, which is extremely flexible and durable to provide the proper medium needed to transport the water/glycol fluid. The piping system includes ProPEX® engineered polymer (EP) fittings as well as ProPEX copper sweat adapters for connections.
“We needed a pipe with an oxygen barrier to protect the aluminum panels from corrosion, and we also needed a product that was quick to install,” says Goldstein. “After talking with plumbing contractors, we learned PEX was far superior due to its installation speed.”
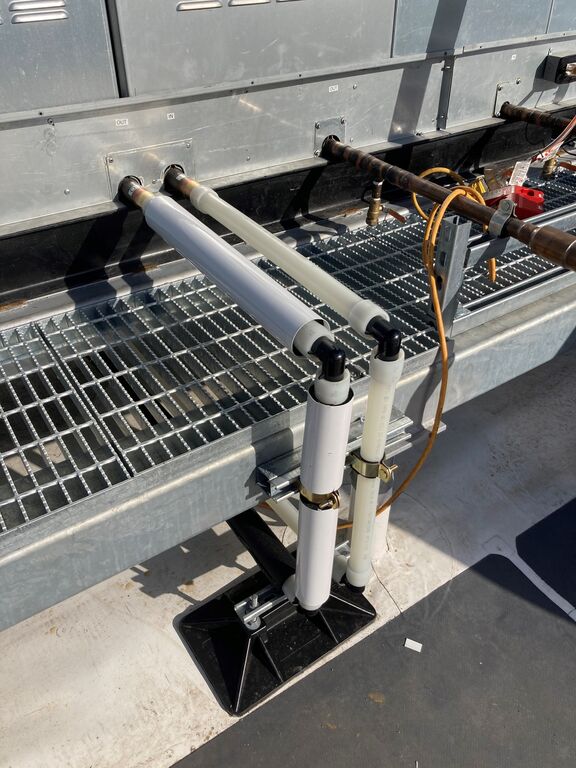
SkyCool Systems uses oxygen-barrier Wirsbo hePEX pipe and ProPEX fittings for the distribution piping.
After deciding on the pipe type, Goldstein says the next important decision was finding the right connection system that was efficient, dependable, and reliable.
“We chose to standardize the system with ProPEX expansion fittings to make sure we don’t have leaks,” he says. “We tried other fitting systems, but found they weren’t as reliable or as easy to install.”
Since these cooling-panel systems are being installed in various locations all over North America — and even in some foreign countries — SkyCool contracts the installation with local plumbing and heating contractors.
“We typically work with installers that have solar experience,” he says. “We provide the tools. We have a bunch of Milwaukee® ProPEX expansion tools in a job box that travels from site to site.”
With about a dozen projects complete by the end of 2022 and 40 to 50 projects slated for 2023, this cooling-panel trend is really beginning to take off in the commercial building industry.
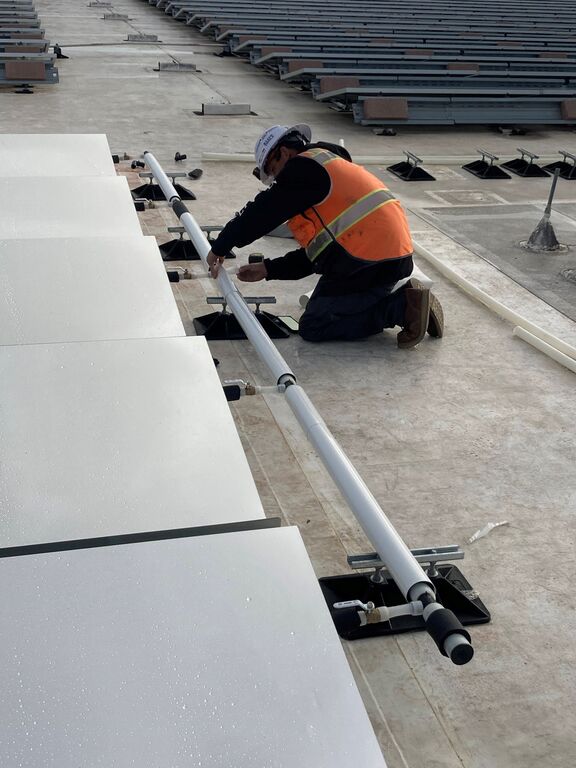
The distribution piping system features Wirsbo hePEX pipe along with ProPEX fittings and ProPEX ball valves.
From data centers to grocery stores to refrigeration warehouses, this technology is proving to be a great value to large commercial buildings that require constant cooling in an efficient manner.
“We anticipate most customers will get a return on their investment in three to five years,” he says. “Which, for commercial buildings, is relatively quick.”
With the incredible energy cost savings, the only question Goldstein typically receives from potential customers is the system longevity.
“The film on the panels has a projected life expectancy of around 15 years,” he says. “So, depending on where the system is located, the film will most likely need to be replaced after 15 years, give or take a couple years.”
He goes on to state that the rest of the system, including the aluminum panels, the racking system, and the piping system, have a much longer lifespan. PEX piping, depending on the manufacturer, typically has a life expectancy of around 50 years. So, the distribution piping is designed and manufactured to last for several decades.
“We’re insulating and jacketing the piping system, so it’s not exposed to UV,” he says. “That is one question we typically get when talking to customers. There is usually a concern about PEX and UV, but we make sure all the exposed piping is insulated to help ensure maximum longevity for the system.”
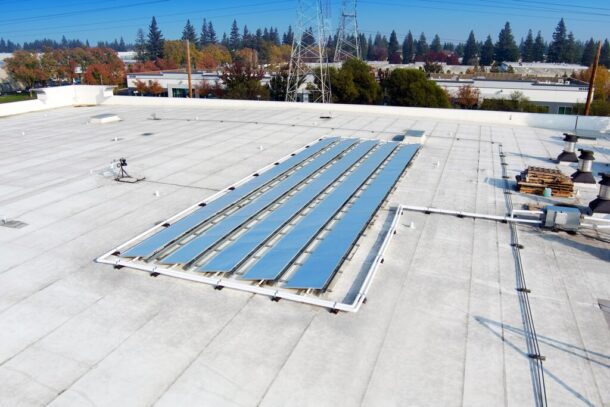
Here is the final installation with the supply and returning piping that includes the complete jacketing for UV protection.
As for future opportunities with this technology, Goldstein is working with partners all over the globe to find ways this innovation can help make cooling more sustainable.
“The opportunities are endless as to where we can use this reflective film to keep any outdoor surface cool,” he says. “From semitrucks to manufactured homes to outdoor electronics, it can be used to keep all different kinds of surfaces cooler than the outdoor air temperature.”
Kim Bliss is the technical and marketing content manager at Uponor. She can be reached at kim.bliss@uponor.com.
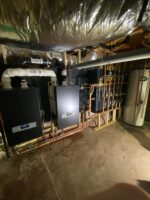
Cascading System Solves Heating Challenge for Huge Home on Massachusetts Shoreline Winters can be hard on home heating systems. Particularly so in New England coastal communities, where wind, snow and sleet, and bone-chilling temperatures force systems to work massive overtime. New England in summer is special. Winters? Not so much. In older homes it can Read more
Cascading System Solves Heating Challenge for Huge Home on Massachusetts Shoreline
Winters can be hard on home heating systems. Particularly so in New England coastal communities, where wind, snow and sleet, and bone-chilling temperatures force systems to work massive overtime. New England in summer is special. Winters? Not so much.
In older homes it can be particularly difficult to maintain heat throughout the house, especially in the region’s expansive, multi-story structures. Put all the ingredients together, and home heating contractors in New England and other frosty locales find it a challenging task to ensure everyone’s thermal comfort.
Working with Emerson Swan, the team at Jeff Potvin Plumbing & Heating installed a solution that uses cascading as an efficient heating source for a 4,000 square foot house, which was built in the late 1800s. “The homeowner had two 250K BTU boilers, but they were pretty old and worn out,’’ Potvin said. “It was time for a new system.”
Uncomplicated Install
To replace the existing boilers, Potvin’s team installed two Ariston HTP ELU 199K boilers. The boilers will provide heat for a house that includes five bedrooms and six baths. The house is steps away from Preston Beach in Marblehead, Mass., and the spacious living room overlooks the ocean. By every real estate metric, it is a premium property in a highly coveted location.
But with the heating units breaking down, it was critical to implement a new system. Potvin’s team decided to install a pair of cascaded boilers to help the homeowner maximize efficiency.
“These boilers are uncomplicated to install due to the large cavity inside, which will enable us to service its components in the future,’’ Potvin said. “We had a fluing issue, but we cascaded the boilers and also vented them, which solved the problem.”
One of the concerns for the homeowner was the noise of the units. The mechanical room is located near a living area. “One of the benefits of the HTP ELU boilers is they are very quiet,’’ Joe Savignano of Emerson Swan said. “They are common in European homes, and they are made to be super quiet. Even with a 3-way valve moving, you don’t hear a thing. The homeowner was pleasantly surprised by how quietly they operated.”
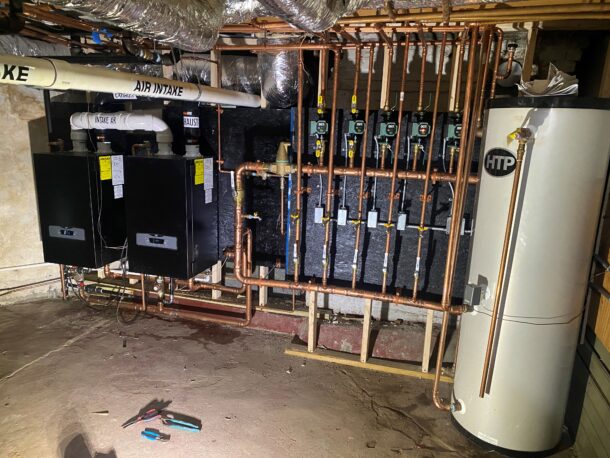
Jeff Potvin Plumbing & Heating installed two Ariston HTP ELU 199K boilers in a cascaded system to heat a 4,000 square foot house in Massachusetts.
Critical Redundancy
The benefit of the cascading system is that it ensures redundancy, so that a building or home retains access to hot water for heating in the event of a failure.
Cascading involves using multiple units to solve demand issues when one unit is incapable of generating the amount of heat required. Before installing a cascading system, it is important for the contractor to know the BTU heat load calculation. A bigger structure will generate more heat demand.
For example, a building might have a 10 million BTU heat load calculation. An Ariston HTP Elite Ultra XL boiler provides 2 million BTUs and would require five of them to meet the heating capacity of the building when 100 percent of the load is demanded.
Most of the time, however, 100 percent of the load is not required, and less heat is needed in short term duration. A zone might come on in the system that calls for 2 million BTUs. With cascading, all five boilers act as one to meet the demand. If the building needs 100 percent of the heat, all five units would fully activate.
One unit orchestrates the activities of an entire group. HTP calls it a Master and Follower installation. Follower heaters are controlled by the master unit and dictates when all units operate. Most cascade systems have lead/lag rotation grouping to spread the demand load evenly so that no one unit is used more than the others.
Worry-free system
For homeowners and businesses, cascading systems ensure hot water delivery when maintenance is required or unplanned downtime temporarily disables one of the units. That’s particularly important for a New England home, where a boiler stoppage in the middle of the night could lead to burst pipes, unheated bedrooms, and angry customers.
In the maintenance cycle, a building might use 5 boilers to produce 10 million BTUs of hot water. After two years, the first boiler is taken out of operation for maintenance. With the cascade design, the building can manage day to day activities to keep hot water available to the entire building with just four boilers.
If a unit fails due to an error code, the other units in a cascade system meet the demand. If a business has just one boiler for daily operations, and it fails or needs maintenance, the business must close. Homeowners who lose their heat might need to find temporary, alternative living arrangements until the heat is restored.
Cascading also spreads the load across multiple units, so that all boilers are actively supporting each call. HTP’s Elite Series has programming that shifts loads of a heat call when the first unit gets to 80 percent operation. Once a boiler hits that mark, it will split, and another unit will fire to divvy up the demand call.
Some units even include rotation clocks. Elite Ultra models can be programmed for specific hours of operation. For example, one boiler can be programmed for 6 hours. When that time expires, the next boiler in the rotation picks up the next 6-hour shift. By ensuring that all units are used equally, the system needs less maintenance and individual components will last far longer.
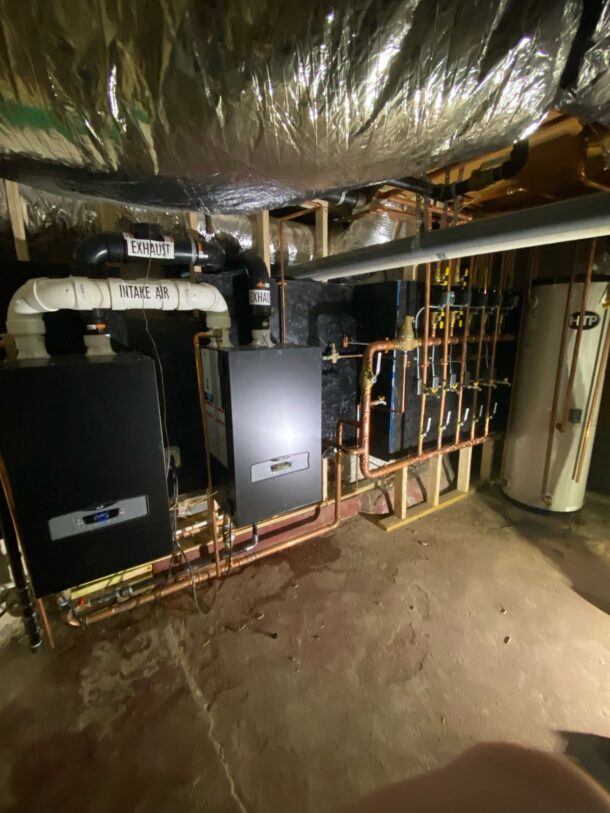
The cascaded system ensures redundancy, and multiple units solve demand issues when one unit is incapable of generating the amount of heat required.
Various applications
Cascading systems can be used in commercial and residential jobs. Hotels, hospitals and office buildings have high demand, so cascading systems give them an efficient and reliable option to meet that demand. The expansive Massachusetts home is also the perfect setting for a cascading system.
“One of the things that I like about the Elite Ultra is it’s the easiest to control,’’ Savignano said. “The Wi-Fi function enables remote monitoring of the system.”
Another residential application might be for a home that includes a snow melt system for the driveway. The heat load for the home could be 130,000 BTUs for the house and 250,000 BTUs for the driveway. The solution could be individual systems, or two Elite Ultra-199WBN models to cover the total heat load.
One more application demonstrates the benefit of a cascading system. An apartment complex in Derry, N.H. installed three Elite Ultra boilers in a tight footprint for an apartment complex. By using multiple units, installers have greater flexibility in irregular spaces. The mechanical room for the apartments had limited space, so a cascading system proved to be a good solution.
Potvin’s client can rest comfortably, knowing that the cascading system will keep the family comfortable all winter long. “This system made perfect sense for this job,’’ Potvin said. “We use the HTP products a lot for our jobs. They’ve got a good support system, and the Elite Ultra interface is easy to use and is remarkably efficient. It’s a durable product and the homeowner won’t have to worry about heating the home for a long time.”
Guest Author is Thomas Renner, who writes on a variety of trade industry topics for publications throughout the United States.
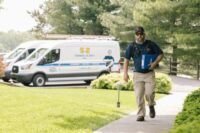
By Jason Richards, Hajoca Corp. I’ve seen a lot of creative ways to provide emergency heat to buildings during no-heat situations, but maybe none as original as a project we became involved with early this year at an upscale rural property near Reading, Pa. The 12,500-square-foot building, one of many on the 100-acre property, houses Read more
By Jason Richards, Hajoca Corp.
I’ve seen a lot of creative ways to provide emergency heat to buildings during no-heat situations, but maybe none as original as a project we became involved with early this year at an upscale rural property near Reading, Pa.
The 12,500-square-foot building, one of many on the 100-acre property, houses a heated pool, spa, full size tennis court, kitchen and locker rooms. When the old sectional boiler used to heat the facility failed mid-winter, maintenance staff turned the pool water temperature way up. This not only held the natatorium at a safe temperature, but waste heat from the pool heating equipment kept the adjacent tennis court from freezing.
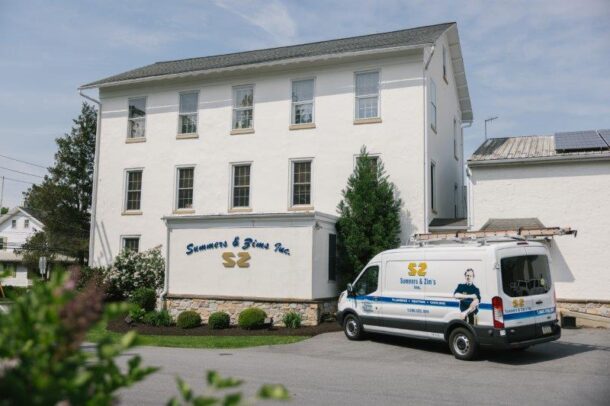
With 37 employees, Summers & Zims serves southeastern Pennsylvania from their headquarters in Atglen, Pa.
Mechanical contractor Summers & Zims, Atglen, Pa, was called in January to handle the no-heat call. The 37-person company had served the property owner in 2013 when they installed an extensive snowmelt system.
Joe Henderson, plumbing project manager, responded to the call and found that the large boiler was beyond repair; a replacement was needed immediately.
“Jason Richards, at Hajoca, and I began designing a replacement,” said Henderson. “There was a 500-gallon fuel oil tank on the property for the hydronic system and backup generator, and there was also an LP tank for the pool heater. The problem with replacing the original oil boiler with a propane unit was that the existing LP tank wasn’t large enough to handle the additional load. Plus, a second LP tank wasn’t immediately available.”
We didn’t know it then, but that was the first instance we experienced where major product availability issues would impact our decisions during the design process. Luckily, the supply chain challenges ultimately resulted in an even better system than we planned for initially.
Collaborative design
We continued the design with a multi-boiler approach. The original plan was to install a single large sectional boiler, but supply chain issues caused some trouble. I consulted with Dave Raabe, at ROI Marketing, and we learned that the boiler we wanted wouldn’t be available for a few weeks.
“This project took place at the height of the product availability challenge,” said Raabe. “The larger boilers weren’t available, so we looked at using three smaller MPO-IQ boilers, made by U.S. Boiler Company. These were immediately available. Ultimately, installing three boilers provides three stages of heat input for higher efficiency, and it also provides a level of redundancy. The smaller boilers also meant that the units could be wheeled into the mechanical on hand carts, instead of being field-assembled.
As a result, the design team selected three, 189 MBH boilers.
“We’ve come to love the MPO-IQ,” said Henderson. “We’ve installed tons of them. At 87 percent, they’re the most efficient, dependable oil boiler we’ve ever used.”
This design yielded a three-stage oil-fired system, which is uncommon in a residential/light commercial application. It provides some redundancy and, more importantly, allows the system to fire at lower input based on outdoor reset.
Controlling the boilers became the next question. Summers & Zims’ HVAC trainer and in-house tech support, Kenny Walker, has a great deal of experience with tekmar controls and had used the tekmar Boiler Control 274 for staging multiple boilers on numerous occasions. The property owner also wanted to remotely monitor the system through WiFi, so the new tekmar Smart Boiler Control 294 was selected.
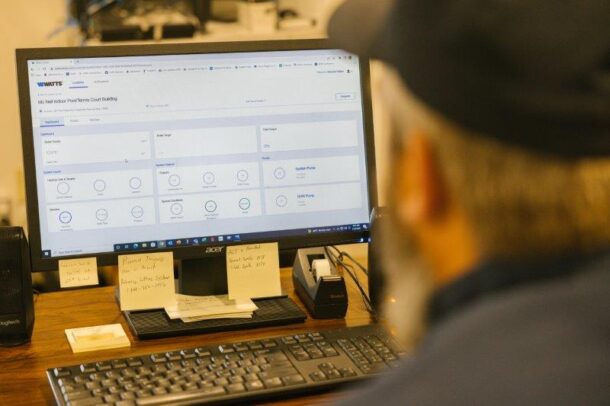
Using the Watts OnSite web or mobile applications associated with the tekmar Smart Boiler Control 294, Kenny Walker can monitor the boiler system from his desktop or mobile device.
Rapid installation
Summers & Zims, originally Summers Brothers Plumbing & Heating, has been in the business since 1930. They merged with Zim’s Sales & Service in the 70s, forming the company it is today.
I’ve known a lot of their people for a long time, and can speak to their professionalism. They’re what I’d call “do the right thing” kind of people. Joe Henderson and I go back 25 years, even before I joined Hajoca. He’s a very sharp hydronics guy. When it came time to install the system in a hurry, I knew they could handle it.
For the install, Walker was joined by Todd Lease, head plumbing technician, Andrew DiEugenio, journeyman plumber, and Austin McGhee, apprentice.
The boilers were rolled into the mechanical room and a primary-secondary piping configuration was used to connect them to the system loop. The fuel supply line to each boiler features a Tigerloop fuel oil deaerator.
“We install a Tigerloop on every oil-fired system we install,” said Walker. “They cut down on nonsense service and emergency calls by cleaning up ignition and burn, which creates less soot in the heat exchanger. We also like that they allow us to use spin-on oil filters, which catch small dirt particles and reduce nozzle failures.
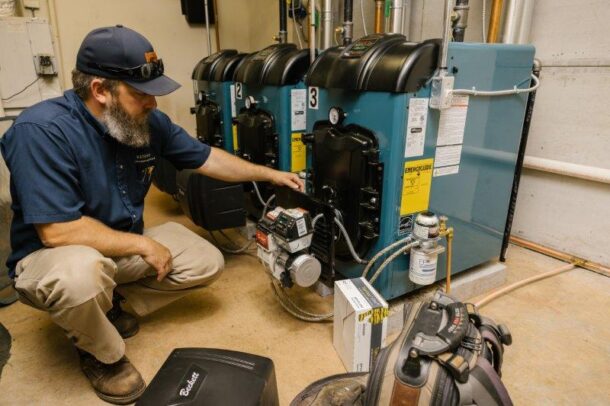
Kenny Walker, Summers & Zims HVAC trainer and in-house tech support, installs a Tigerloop Ultra oil line de-aerator.
“If the homeowner isn’t attentive to the amount of fuel they have left in the tank, running empty isn’t such a big deal,” he added. “The Tigerloop provides a two-pipe system from the oil pump to the unit. This way, the oil pump will self-prime, meaning the owner or the fuel delivery tech can simply hit the reset button on the primary control once oil has been delivered.”
Flexible fuel lines were used from the Tigerloop to the boiler’s Beckett burner. To provide easy access to the three-pass heat exchanger, the MPO-IQ features a hinged front door, where the burner is located. By using flexible lines instead of hard pipe, service techs can open the boiler without removing the fuel fitting at the burner.
“Providing deaeration is even more critical on a multi-boiler installation like this because the more times you Tee off of the fuel line, the more opportunity there is for air to enter the fuel supply,” continued Walker.
Venting the boilers was done as deliberately as supplying the fuel. The existing chimney was large enough, but common venting the three units had to be done carefully.
“We couldn’t just run three, six-inch vents into a common stack, because the distance between the boilers and the main stack were slightly different,” explained Henderson. “The first two boilers join into an eight-inch vent, which increases to 10 inches as it picks up the third boiler and exits to the chimney.”
Control
When the original boiler failed, the homeowner decided that he wanted to monitor the heating system regardless of where he was, and he also made the decision to sign a service agreement with Summers & Zims. For both of those reasons, Henderson wanted to find a control solution to stage the boilers and provide web-based monitoring. That said, they also wanted to avoid the use of a complex, costly building automation system.
“Jason had recently told us about the new tekmar 294,” said Walker. “So when we bought the boilers from Hajoca, we also bought the control. The 294 is similar to the 274, but with more features, a touch screen, and most importantly, remote monitoring capability. It can also send me texts, emails and push notifications for a wide variety of alerts.”
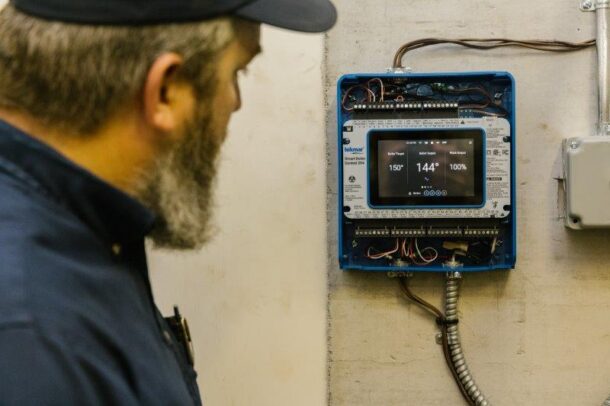
Kenny Walker installs the tekmar Smart Boiler Control 294.
The control stages and rotates the boilers, as well as handling outdoor reset, DHW priority, warm weather shutdown, etc.
In a typical MPO-IQ boiler installation, the onboard boiler control features optional plug-and-play cards to provide outdoor reset, low-water cutoff and aquastat. In this system, the tekmar 294 replaces all but the low-water cutoff card.
“The 294 was easy to install, and I can pull up and make setpoint changes to the customer’s system at my office or on my phone,” said Walker. “Right off the top of my head, we have half a dozen other systems in the field that would benefit from the use of this control. Each one can control four appliances, and they’re expandable to 16.”
Within a week of the old boiler failing, the new hydronic system was heating the building, and the pool heater was turned back down to its normal operating temperature.
I think this job—and the speed at which it came together despite supply chain issues—is a testament to Summers & Zims. The whole company shows up and honestly tries to do the very best they can.
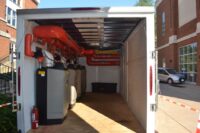
The University of Virginia sought a way to quickly provide temporary heat during construction projects while also reducing boiler rental expenses. The solution was the development of two innovative mobile boiler trailers that provide on demand heat where it’s needed. The University of Virginia is a public research university in Charlottesville, Va., founded in 1819 by Thomas Read more
The University of Virginia sought a way to quickly provide temporary heat during construction projects while also reducing boiler rental expenses. The solution was the development of two innovative mobile boiler trailers that provide on demand heat where it’s needed.
The University of Virginia is a public research university in Charlottesville, Va., founded in 1819 by Thomas Jefferson. It is the flagship university of Virginia and home to the Academical Village, a UNESCO World Heritage Site.
Like many large, historic universities across the country, especially in the Midwest and Northeast, the University of Virginia utilizes central steam heating plants that pipe steam and heating water to campus buildings.
The university is in the second year of a five-year project to convert its steam systems to low temperature hot water for more efficient heating across the grounds.
“During a pipe or heat exchanger replacement, we would typically rent boilers to heat the affected buildings,” said Cameron Ratliff, associate director of utilities distribution with the University of Virginia. “However, boiler rental costs were expensive, and so we were looking for a more cost-effective solution for temporary heat.”
The university team came up with an innovative idea: build its own custom mobile boiler trailer.
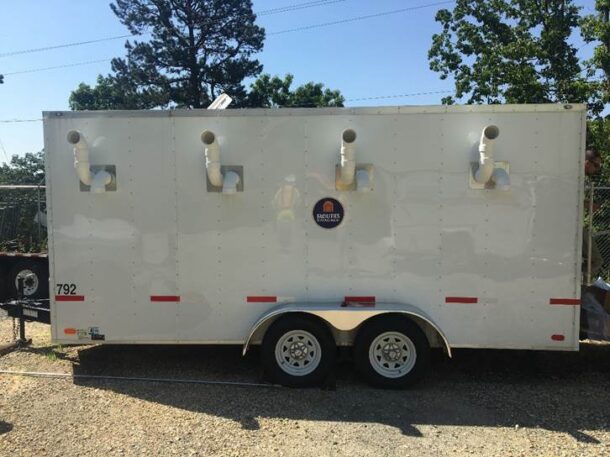
Building the Trailers
Collaborating with Ferguson Plumbing Supply, its main supplier for pipes and fittings, and SE Burks, an HVAC solutions and equipment company, the university facilities team came up with the idea to develop a mobile heating system using a 7½ x 20 ft. trailer and an 8½ x 24 ft. trailer as the housing. The team selected four Weil-McLain boilers to serve as the heart of each system.
“We developed our first mobile heating trailer with four Weil-McLain Ultra boilers for a total output of 1.2 million BTUs to provide temporary heat if a building’s heating went down,” said Ratliff.
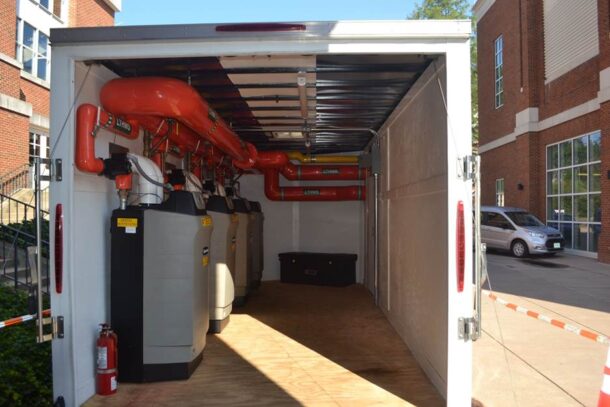
The Weil-McLain Ultra boiler is designed to operate in low temperature condensing applications and features a coated cast aluminum heat exchanger, up to 94% AFUE efficiency and high- grade stainless steel burner with quiet operation. In addition to the boilers, the trailer was outfitted with connections for fuel, water and electricity.
It didn’t take long for the University of Virginia to put the mobile boiler trailer into action.
“Carruthers Hall lost its boilers during the winter, and we had our 1.2 million BTU trailer connected in one day to provide temporary heat while we serviced the boilers,” said Ratliff.
With the success of the first trailer, the University was determined to build a second mobile heating trailer with even more heating capacity.
“The design for our second trailer required a powerful, efficient boiler that could meet our target BTUs while also fitting in an 8½ x 24 ft. trailer,” said Ratliff. “I researched the Weil-McLain SlimFit unit, and it seemed perfect for the application. We chose the 750K BTU SlimFit models as they were the largest units we could fit and because they operate on either propane or natural gas.”
Wes Collings from SE Burks offered guidance on selecting the boilers, and the facilities department teams installed the boilers.
“The SlimFit was an ideal choice for the small footprint of these trailers and because of the unit’s easy serviceability,” said Collings. “The university included extra pipe connections so two more units can be added to increase the capacity even more.”
The SlimFit boiler’s narrow housing enhances maneuverability for confined spaces and weight restricted areas. The design also increases usability and access for installing contractors, consulting engineers and facility managers for commercial retrofit projects.
With the four SlimFit units installed, the University now has a second boiler trailer with a total heating capacity of 3 million BTUs with the option to add two more boilers to increase it to 4.5 million BTUs if needed, for larger heating season applications.
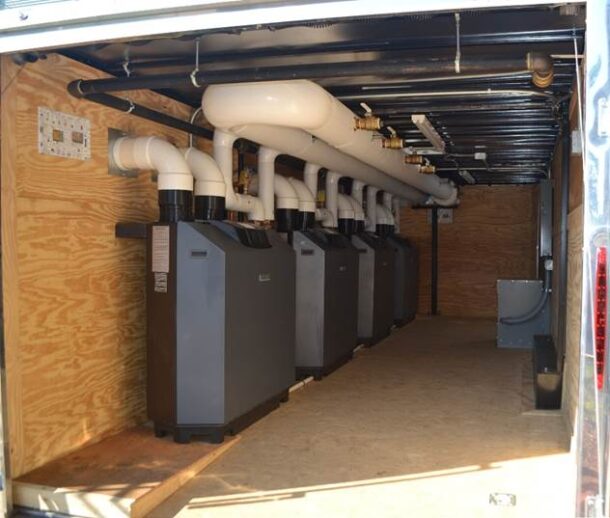
As the university transitions from steam heat, the facilities team also is creating temporary connections for easy connectivity to the trailers.
“We are removing heat exchangers and inserting blending loops with PICV valves and temperature regulators, so all of our buildings are directly connected to the plants,” said Ratliff. “Should we have an emergency breakdown, we can simply pull up the trailer and it’s plug and play.”
Temporary Heating on Demand
“We now can heat the majority of our facilities on grounds at any time with these trailers without having to rent boilers,” said Ratliff. “Waiting for a rental boiler is not an ideal option during the heating season when these systems are in peak demand.”
Ratfliff also notes that the small size of the trailers is advantageous, too.
“The trailers are easy to move around the grounds,” he said.
Besides having on-demand heat as needed, the university is experiencing significant expense savings from expensive boiler rentals.
“Our University CFO is not only intrigued by these trailers but also quite thrilled with the cost savings,” Ratilff added.
Ratliff noted it was a team effort to design the mobile heating systems.
“We really enjoyed putting out heads together to build these trailers,” he said. “It really is the perfect application for our university; the cost savings alone make it so worth it.”