For the company’s 85th anniversary, Freeborn Mower Electric Cooperative in Albert Lea, Minn., decided to build a brand-new facility to house all their equipment, trucks, and employees in one location. The new 97,000-square-foot, $17 million structure featured several high-tech, sustainable building practices, including radiant floor heating throughout the entire building. Being an electric cooperative that Read more
Featured
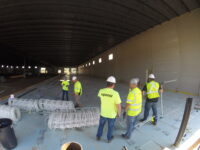
For the company’s 85th anniversary, Freeborn Mower Electric Cooperative in Albert Lea, Minn., decided to build a brand-new facility to house all their equipment, trucks, and employees in one location. The new 97,000-square-foot, $17 million structure featured several high-tech, sustainable building practices, including radiant floor heating throughout the entire building.
Being an electric cooperative that serves 21,045 members in two counties with 2,950 miles of line, they wanted the most energy-efficient method for heating their structure, which meant a radiant floor heating system using Wirsbo hePEX™ pipe along with an underground distribution system using Ecoflex® pre-insulated piping.
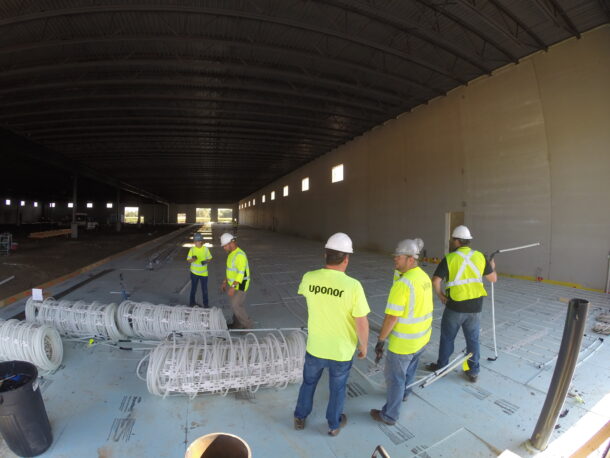
Despite construction being done during the height of the COVID-19 pandemic in 2021, all the construction partners came together to complete the project quickly and under budget. This was thanks, in part, to the efficiency of the Uponor Radiant Rollout™ Mats for the radiant heating system, which saved significant install time and labor costs.
Taylor Bestor of Valor Mechanical, the radiant contractor, had been installing commercial systems since 2007, but had always used traditional methods of wire ties or foamboard staples. When the engineer’s specification called for preassembled radiant mats, Taylor was curious about how the installation would go, knowing he needed to align with concrete-pour schedules to stay on the customer’s tight timeline.
To learn more about these preassembled radiant mats, Taylor met with Ryan Swanson of FourMation Sales, an Uponor manufacturer rep firm. Ryan told Taylor about the Uponor Radiant Rollout Mats and how they could “cut labor by one third.” Of course, after hearing about the incredible installation efficiencies, Taylor was interested in how this technology worked.
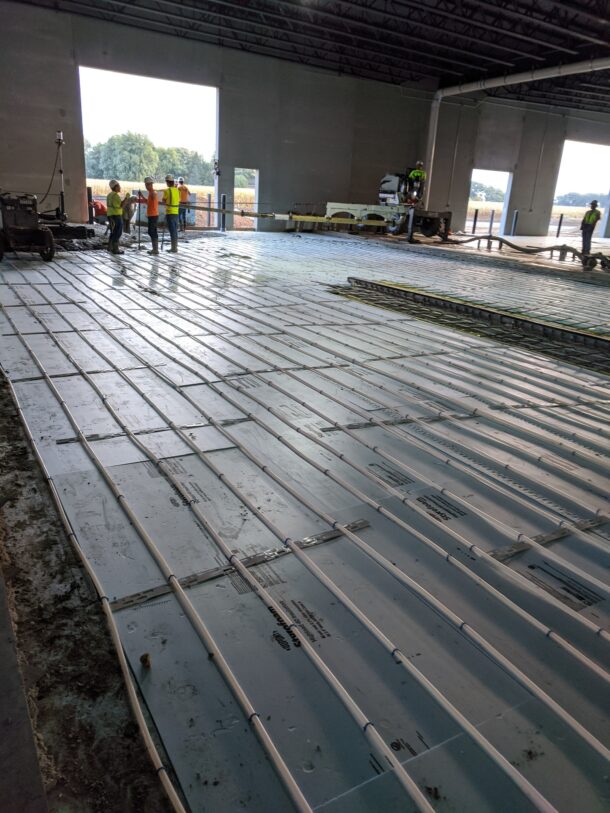
Once he learned that the mats are custom designed by Uponor Construction Services to fit the space and come to the job site preassembled and pre-pressurized, ready for installation, Taylor was on board with moving forward.
Paul McCulloch from Uponor, along with Ryan, were there for the first install to guide Taylor and his team with the mats. The crew made a plan to complete the radiant tubing install in thirds to work with the concrete pours.
“We started out by training about 10 guys to get an understanding of how the mats worked,” says Taylor. “By the last third of the project, we were able to do the entire install with three guys in one day. Using traditional wire ties or staples would have taken more than double the workers and triple the time.”
Because the project included complete layout designs from Uponor Construction Services, Taylor and his team were able to efficiently and effectively install the Radiant Rollout Mats as well as the radiant perimeter, which used a staple-down method. They also installed Ecoflex pre-insulated pipe for the underground piping to the Uponor TruFLOW™ manifolds, which, Taylor says, “worked out perfectly for the install”.
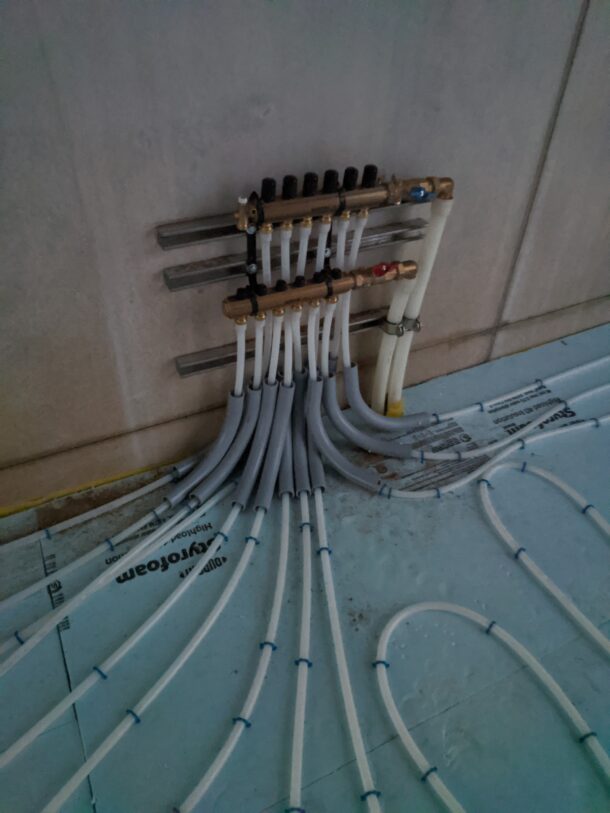
After his experience with the extreme efficiency of the Radiant Rollout Mats, along with the support from the Uponor sales team and Uponor Construction Services, Taylor is convinced of their effectiveness and is anxious to use them again in a future large commercial radiant project.
To learn more about Uponor Radiant Rollout Mats or other radiant installation methods, visit www.uponor.com.
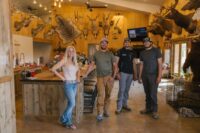
Hunting is a lot like many outdoor pursuits in that you can’t control the weather. Hunting guides and outfitters also know that you can’t control the animals, so they control what variables they can: the food and the lodging. Fred and Michele Eichler operate Fulldraw Outfitters in southern Colorado where they host hunters looking to Read more
Hunting is a lot like many outdoor pursuits in that you can’t control the weather. Hunting guides and outfitters also know that you can’t control the animals, so they control what variables they can: the food and the lodging.
Fred and Michele Eichler operate Fulldraw Outfitters in southern Colorado where they host hunters looking to harvest elk, deer, bear, antelope and turkey in fair-chase pursuit.
Fred, arguably one of the greatest bow hunters alive today, became the first person to harvest all 29 North American big game species with a recurve bow, completing his Super Slam. Michele, who’s also been a bow hunter since childhood, was CEO of Muzzy Products, an archery brand that all bow hunters in the country are familiar with.
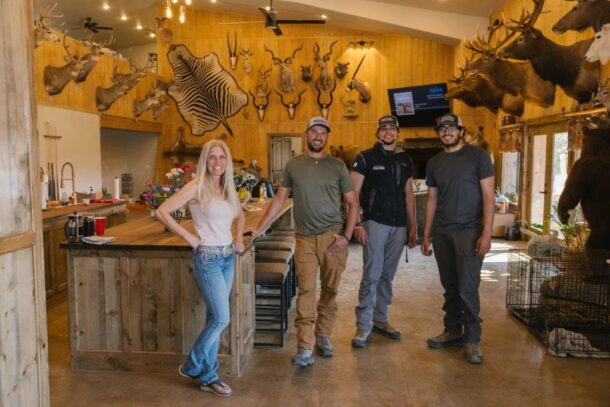
(L-R) Michele Eichler, Steve Fernandez, Ty Fernandez, Federico Orozco.
The hunting on the properties where the Eichlers outfit is exceptional, and the accommodations have always been very good, but in early 2020 the family made a decision to raise the stakes. They wanted to build a new lodge to host guests, with all the amenities that a professional hunting outfit might need – 11 bedrooms, a walk-in cooler for game, vaulted ceilings for hanging trophies, entertainment space and a giant kitchen complete with two expansive hardwood islands.
Michele designed the lodge with comfort and environmental sustainability in mind. The dream materialized over the course of two years. After ordering the steel frame building, the Eichlers called Steve Fernandez, owner of Twin Peaks Plumbing & Hydronics, in Trinidad, CO. Fernandez is also a very successful big game hunting guide and has known the Eichlers for decades.
“Steve was one of the first people we called,” said Michele. “He quickly suggested using spray foam to insulate the whole building, and to install an in-floor heating system. We hired him for both the plumbing and heating work.”
Twin Peaks, a six-person company, has a fantastic reputation in the Spanish Peaks area of Colorado. Steve’s son, Ty, is the fourth generation plumber in the family.
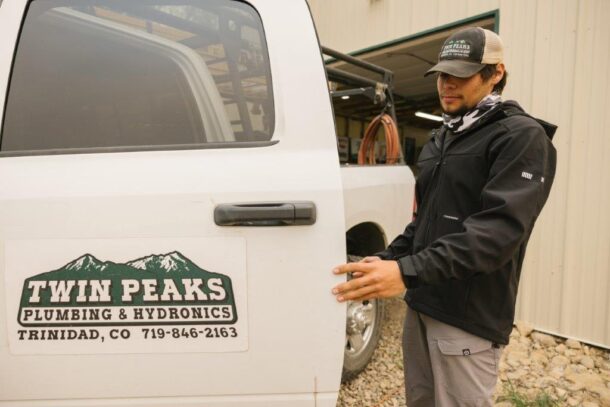
Twin Peaks plumber Ty Fernandez prepares to head to Eichler’s lodge.
Simple radiant, outstanding comfort
Trinidad might be close to the New Mexico border, but its elevation of 6,000 feet above sea level means that the region sees serious winter conditions. Temperatures can plunge as low as -20°F.
The 6,000 square foot building – not including the offices, gym and storage space on the second story – is divided into six zones. The entire space is heated from below with half-inch MrPEX oxygen barrier tubing, with the exception of the 225 square foot walk-in cooler. This portion of the slab is isolated from the rest of the polished concrete slab with the same two-inch rigid foam used beneath the pour.
Heat is provided by a propane-fired, 96 percent efficient Aspen condensing boiler, made by U.S. Boiler Company. Fernandez prefers the firetube Aspen over other modulating boilers because it’s easy to program and even easier to service.
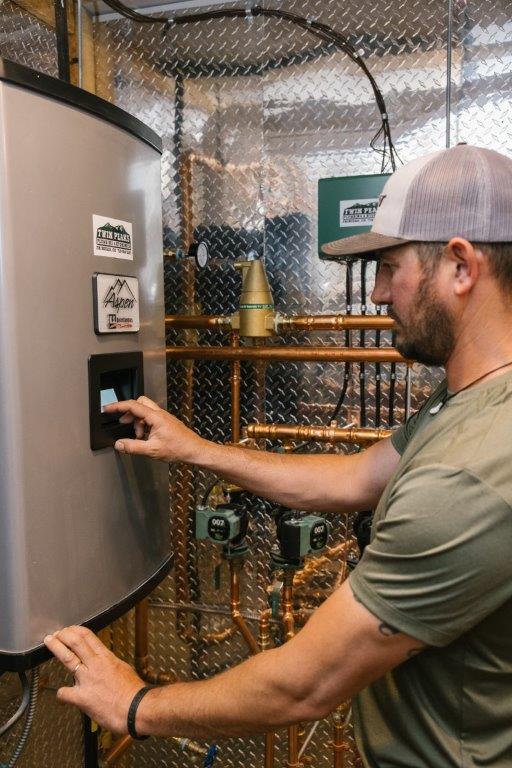
Steve Fernandez, owner of Twin Peaks Pluming & Hydronics programs the 270 MBH Aspen condensing boiler.
“We have 30 or more Aspen boilers in the field, all of them at high altitude,” said Fernandez. “Their design is so intuitive that my apprentices have caught onto them very quickly.”
Most of the 20 loops in the slab enter the main mechanical room, but Twin Peaks placed two, three-quarter-inch remote manifolds at either end of the 100-foot-long long building. Each zone is circulated by a Taco 007e ECM pump. With outdoor reset and a maximum supply temperature set at 130°F, the system provides a 12°F Delta-T.
“Our loops here are all between 280 and 290 feet long, so there was no need to use balancing manifolds,” said Fernandez. “The ports on balancing manifolds severely raise head pressure by constricting flow, especially with a high glycol mixture. We isolate all our loops with ball valves to help purge the system. That said, there are times I feel balancing manifolds are necessary, especially when we didn’t install the tubing and we have no idea what’s under the slab.”
Before firing the system, Fernandez injected the radiant system with Fernox F1 Protector. This helps guard system components against the low pH water and high hardness common to Colorado and other parts of the Southwest. To provide burst protection down to -20°F, Twin peaks used Fernox Alphi-11 antifreeze.
The system, which covers two diamond-plate aluminum walls, also incorporates Taco’s Near Boiler Trim Kit. This includes air separation, an expansion tank, combination backflow preventer and boiler feed valve, and the brass fittings needed to assemble the components.
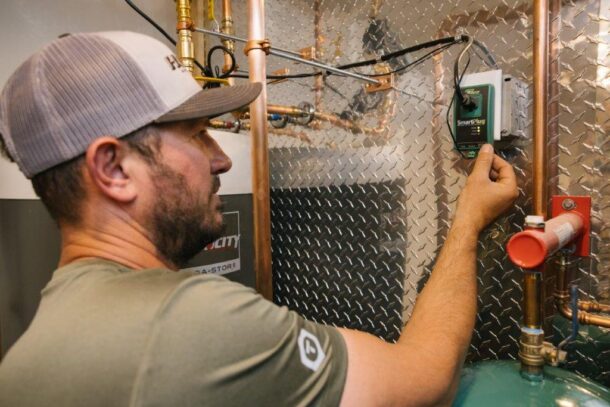
Steve Fernandez connects a Taco SmartPlug domestic hot water control for the recirculation loop.
Conserving water, ensuring supply
Fernandez installed the largest of the wall-hung Aspens available, 270 MBH, mainly to handle the massive DHW load. The Aspen is also available in 320 and 399 MBH floor-mounted light commercial sizes, but with the 75-gallon indirect fired water heater installed at Eichler’s, the extra boiler capacity wasn’t needed.
The home’s domestic hot water load is comprised of five bathrooms, a large laundry, kitchen, commercial pot filler and wash-down hoses in the game processing area.
“The amount of laundry my boys create is unbelievable,” said Michele. “When the lodge is full, hunters all come back at roughly the same time, expecting hot showers, a meal, and likely game to process. I told Steve that I never wanted to run out of hot water.”
The floorplan made the use of a domestic hot water circulation system an easy decision. Twin Peaks installed a three-quarter-inch recirculation line, with a stainless steel Taco 006e3 circulator set on medium, plugged into a SmartPlug instant hot water control. Using a temperature sensor that mounts to the hot water supply pipe, the control monitors water use patterns in the home and runs accordingly; no programming, timers or aquastat required.
The large indirect water heater, set to priority, is maintained at 170°F. Water is then mixed down to 135°F before entering the recirculation loop.
“We had 20 guests here at one point and never ran out of hot water,” said Michele. “Hot water arrives immediately at any tap in the lodge. There’s no fresh water being wasted. It actually took a bit of getting used to, after years of waiting for hot water to arrive at a tap.”
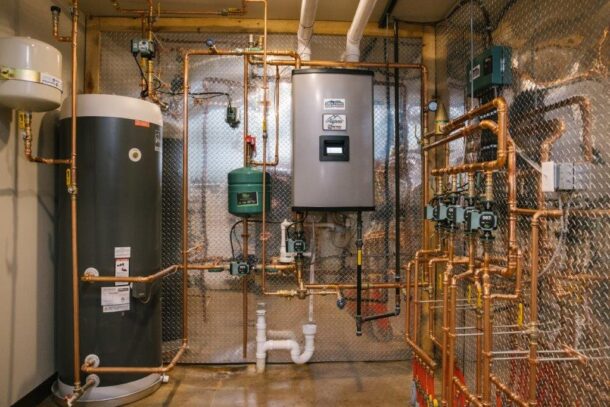
The in-floor hydronic system at Eichler’s lodge features a condensing boiler, ECM circulators, a 75-gallon indirect fired water heater and a large DW recirculation loop.
Stewardship
The lodge was occupied in March of 2022 and the Eichlers hosted turkey hunters the next month.
“The heating system has been amazing,” said Michele. “The floors are warm, everything is comfortable, and this building makes a big difference for our guests, Fred, the boys and myself. We have the space to be organized, entertain, and be the best hosts we can.”
From an energy and water conservation perspective, the new lodge demonstrates Fulldraw Outfitters’ environmental responsibility.
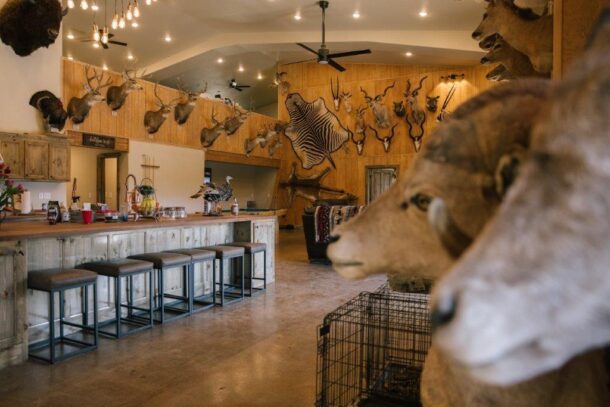
The lodge is designed to host and entertain numerous hunting parties at a time.
“Few non-hunters know it, and anti-hunters won’t admit it, but the vast majority of conservation dollars in the United States are raised by hunters,” said Fernandez. “Whether those funds are used for research to combat wildlife sicknesses like Chronic Wasting Disease, improve and protect wildlife habitat, or re-establish wildlife populations, such as we’re seeing with Bighorn Sheep today, the work is largely funded by, and depends on volunteer manpower of, American sportsmen and sportswomen.”
“As hunters, we’re more invested in the health of wildlife populations and preservation of the places they call home than anyone else,” he added.
By reducing their carbon footprint, selecting high-efficiency products and water-saving technologies, and using as many renewable building materials as was feasible, Fred and Michele Eichler have continued to demonstrate their commitment to conservation.
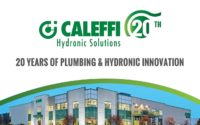
Twenty years ago, Caleffi S.p.A. (Fontaneto d’Agogna, Italy) began an exciting adventure, opening its North American headquarters in Franklin, Wisc. The company soon established wide acceptance of its high quality products in the U.S. and Canadian plumbing and hydronic marketplaces. With investment in people, innovative products, creative branding and state-of-the-art facilities, the company has enjoyed Read more
Twenty years ago, Caleffi S.p.A. (Fontaneto d’Agogna, Italy) began an exciting adventure, opening its North American headquarters in Franklin, Wisc. The company soon established wide acceptance of its high quality products in the U.S. and Canadian plumbing and hydronic marketplaces. With investment in people, innovative products, creative branding and state-of-the-art facilities, the company has enjoyed increasing demand and rapid growth. To honor this milestone, Milwaukee Mayor Cavalier Johnson has proclaimed Thursday, May 19, 2022 to be CALEFFI DAY throughout the City of Milwaukee.
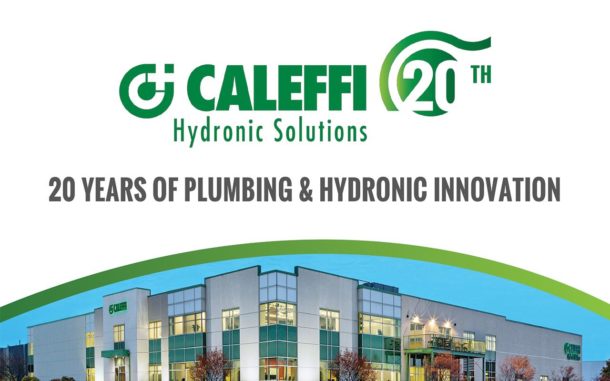
In 2007 Caleffi North America built a new 35,000 sq. ft. facility in the Menomonee Valley to house its main offices, technical laboratory, warehousing and assembly operations. Twelve years later, an additional 8,300 sq. ft. was added to the building, doubling the office space and assembly area. This latest expansion was awarded Top Projects of 2020 by The Daily Reporter, a news source for commercial construction projects in Wisconsin. The creation of appealing work spaces with the ability to easily transform a space into a training venue is a testimony to Caleffi’s commitment to industry education including complimentary resources such as hybrid training opportunities, the popular idronics™ journal series, and Coffee with Caleffi™ – a first of its kind webinar series.
“Caleffi’s core values remain steadfast: commitment, passion, innovation and love for the local community. We will leverage our reputation built these first 20 years to continue expanding our family of customers and employees,” said General Director, Mark Olson.
We welcome our industry partners, employees and neighbors to join us in raising a toast on CALEFFI DAY to celebrate with us our anniversary and the unveiling of our new Training Center while enjoying a tour, a taste of Italy and refreshments:
WHEN: Thursday, May 19, 2022 | 3:00 – 7:00 PM
WHERE: 3883 West Milwaukee Road | Milwaukee
A ceremony will be held featuring Mark Olson, Special Guests from our Italian H.Q. and the Milwaukee Mayor’s office at 5:00 PM. Thank you for your RSVP to sharon.alexander@caleffi.com.
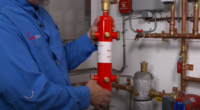
Foley Mechanical worked with the owner of a 1920 home in the Cleveland Park section of Washington, D.C. on a heating system upgrade. The project included a 95% AFUE condensing gas boiler that replaces an existing conventional cast iron gas boiler. https://youtu.be/O_rQ1JOw6f0 Resideo hydronic products that are highlighted included the following: Hydro-Separator ECM Pumps Zone Read more
Foley Mechanical worked with the owner of a 1920 home in the Cleveland Park section of Washington, D.C. on a heating system upgrade. The project included a 95% AFUE condensing gas boiler that replaces an existing conventional cast iron gas boiler.
Resideo hydronic products that are highlighted included the following:
- Hydro-Separator
- ECM Pumps
- Zone Valves
- Relay Controls
- Expansion Tank
- Fill Valve and Backflow Preventer
Radiant floor heat was added to a new basement concrete slab. The existing cast trim radiators on the three upper floors were RE-piped and RE-valved. Foley Mechanical used this opportunity to zone by floor using Resideo zone valves. Nearly six months in and in February the owner shared that he had never been more comfortable in his home.
For more information about the Resideo products in this sponsored installation, please visit HERE.
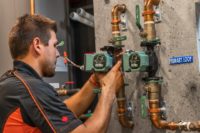
In our continuing Industry Forecast series, we talk with John Hazen White, Jr. – Executive Chairman & Owner of Taco Comfort Solutions, on topics such as the short-term economy, supply chain issues, and lessons learned over the course of the pandemic. Here is our exclusive Q & A with John Hazen White, Jr.: Read more
In our continuing Industry Forecast series, we talk with John Hazen White, Jr. – Executive Chairman & Owner of Taco Comfort Solutions, on topics such as the short-term economy, supply chain issues, and lessons learned over the course of the pandemic. Here is our exclusive Q & A with John Hazen White, Jr.:
MH: We’ve all experienced supply chain shortages, whether it’s industry related or things such as computer chips, plastics, bacon, etc., for example. Do you project a turnaround soon or within the next 6-12 months for certain materials that relate to your specific company?
JHW: Due to the China’s current COVID lockdowns and further supply chain disruptions caused by the war in Ukraine, we believe that chain issues are going to get worse over the next several months. Much of the processing of base raw materials and secondary materials has been shut down, further straining the supply chain. Exacerbating these issues, the skyrocketing costs of fuel and transportation are going to make the delivery of goods more costly.
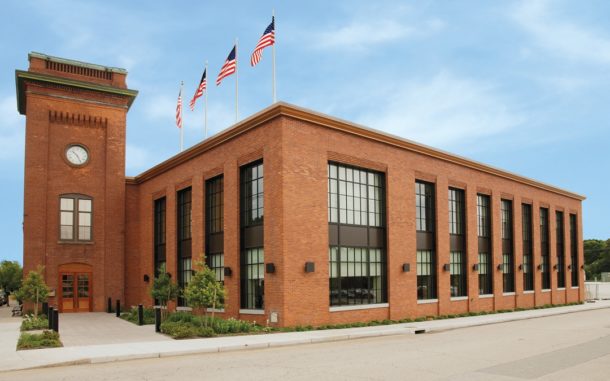
MH: We are in the midst of some of the highest inflation rates since the early ‘80s. Do you think that higher inflation becomes a “newer normal”? Explain.
JHW: Eventually costs will temper demand and inflation will slow. Unfortunately, this will be accompanied by an economic downturn. The risk is that governments may try to artificially stimulate the economy, which could potentially prolong the inflationary upturn.
MH: In general, how do you see the economy short-term? Give a few examples of how you draw that conclusion (housing starts, commercial construction, etc.).
JHW: The short-term economy appears to be healthy. Orders remain strong and backlogs are at all-time highs. Data such as housing starts point to continued growth in 2022, with low inventory levels and a tight rental market driving that growth. In addition, manufacturing construction is on the rise to meet capacity demands.
MH: Where are you seeing signs of positivity, if any?
JHW: Short-term, the economy appears to still be growing, but at a slower pace. Although the last two years have been very challenging, these challenges can also serve as a catalyst for improvement. Companies are reinventing their structures and processes to adapt to a much faster business pace. We’re seeing step changes in productivity, efficiency, and innovation to keep up with today’s challenges and changing business environment.
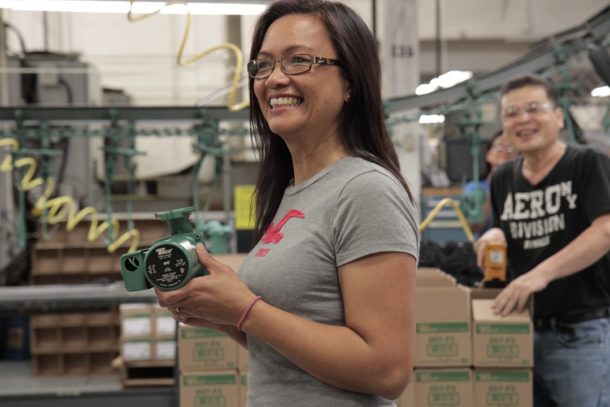
MH: How do you as manufacturers work with customers who are dealing with longer lead times and/or higher prices? Is it a matter of open lines of communication?
JHW: Constant communication and strong partnerships are great ways to manage through the current supply chain and production issues. Most customers understand the challenges that all manufacturers are currently dealing with – they just want to be kept informed to minimize surprises and plan their projects accordingly.
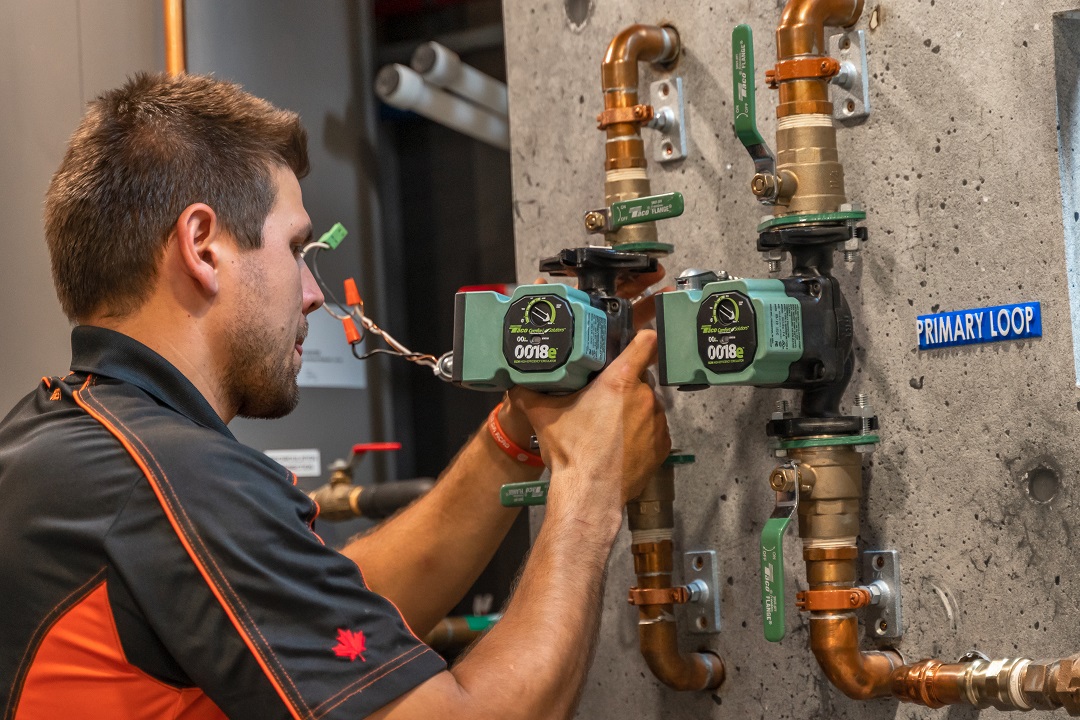
MH: It seems that in today’s employment landscape, it’s hard to find good labor, whether it’s truck drivers, waiters at restaurants, etc. In our industry, how do we continue the fight to highlight the trades as a great career choice?
JHW: Social media is a great way to reach future tradesman of our industry. We have been running a social media campaign called #TradePower, which highlights successful contractors in the industry and the pride they take in their craftsmanship and service. Above all else, Taco has benefited by continuing to do what we always do – treat people right.
MH: In spite of COVID, people must move on. How has your company evolved—or continued to march forward—over the past two years, and talk about any new initiatives, expansions, etc.
JHW: The sudden disruption of COVID restrictions in 2020 forced a much faster adoption of planned technology upgrades. A planned rollout of organizational digitization was condensed from 18 month to two weeks, which gave us the ability to continue functioning and growing in the new work-from-home reality. One of the biggest positives we saw during the pandemic was the rise of global collaboration. The quick adoption of virtual meetings boosted our collaboration with our entire global workforce, ensuring the best players were part of any team meeting. This has led to an increased sharing of ideas on everything from safety protocols to operational improvements. More than ever, we are thinking globally to optimize our resources and maximize our growth.