Wichita, Kan. — Viega announces its partnership with the Center for the Built Environment (CBE) at University of California, Berkeley. The association will enable CBE and Viega to work together in educating the industry on new and more efficient technologies for commercial integrated hydronics systems. CBE is a place where industry leaders and internationally recognized Read more
Heating & Cooling
Wichita, Kan. — Viega announces its partnership with the Center for the Built Environment (CBE) at University of California, Berkeley. The association will enable CBE and Viega to work together in educating the industry on new and more efficient technologies for commercial integrated hydronics systems.
CBE is a place where industry leaders and internationally recognized researchers cooperate to produce substantial, holistic and far-sighted research on buildings.
Fred Bauman, P.E., a prominent scientist at CBE, is leading a research program on advanced integrated systems with a focus on radiant slab cooling, also known as thermally activated building systems (TABS). CBE recently accepted a $3 million grant over the next three years on radiant slab systems to research methods for optimizing radiant systems for energy efficiency and comfort. Research provides more performance data that allows for guidelines for design and controls.
Viega and CBE are collaborating to develop training sessions and use the research for innovative product advancements and design guidelines.
“We are honored to be associated with CBE,” said Mark Parent, director of product management, Viega. “There is a lack of industry knowledge when it comes to radiant heating and cooling. Our hope is to help educate the industry on newer and more efficient technologies when designing commercial integrated hydronics systems.”
Viega provides versatile radiant heating and cooling systems in the industry. Suitable for residential, commercial or industrial applications, Viega ProRadiant™ heating and cooling solutions include ViegaPEX™ Barrier tubing, Viega FostaPEX® tubing, Viega PEX Press fittings, manifolds, controls, mixing stations, sensors, mats, panels, tracks and plates.
CBE’s mission is to improve the environmental quality and energy efficiency of buildings by providing timely, unbiased information on building technologies, design and operation techniques.
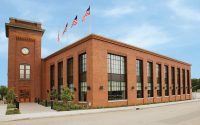
The Taco Innovation and Development Center (IDC), which opened in mid-2012, has been awarded LEED Gold certification by the United States Green Building Council (USGBC). The 24,037-sq.-ft. facility, which houses classrooms and meeting spaces for training and educational purposes, achieved 62 points out of a total of 79 possible points for LEED Gold.   Read more
The Taco Innovation and Development Center (IDC), which opened in mid-2012, has been awarded LEED Gold certification by the United States Green Building Council (USGBC). The 24,037-sq.-ft. facility, which houses classrooms and meeting spaces for training and educational purposes, achieved 62 points out of a total of 79 possible points for LEED Gold.

Points were awarded under the following categories: Sustainable Sites (20), Water Efficiency (4), Energy & Atmosphere (15), Materials & Resources (6), Indoor Environmental Quality (10), Innovation & Design Process (5) and Regional Priority Credits (2).
The Taco IDC, in addition to its instructional/educational focus for both Taco employees and HVAC industry professionals who visit the facility, was designed to be a showcase for energy-saving and sustainable products and systems, which are visible throughout the building for close-up viewing, hands-on learning and teaching.
Products and systems installed in the IDC include chilled beams (active and passive), radiant ceiling heating and cooling, fan coils, water-source heat pumps, perimeter radiation, radiant-floor heating, solar hot water, snow melt and geothermal. The mechanical design goal was to optimize hydronic-side design and remove/add as much heat as possible using chilled beams, flat-panel radiation along the IDC’s walls, and radiant floor systems. All equipment and systems are controlled by Taco’s proprietary iWorx Web-based building management product line and monitored by a host of sensors and meters throughout the building.
Taco achieved 15 out of a possible 20 points total in the Energy & Atmosphere category and 8 out of 11 possible points for optimization of energy performance. In fact, the IDC’s operation performance since its opening has exceeded expectations.
The performance of the IDC mechanical and electrical systems are monitored continuously via dedicated measurement and verification systems. Since the building was completed several new measurement stations were added including hydronic BTU metering systems, electrical sub-meters and building automation monitoring systems. These measurement systems have allowed Taco to monitor energy consumption in real time and compare those actual energy measurements against the initial energy model. All indications are that the building is meeting or exceeding the projected energy savings.
For example, during the period from September 1, 2014 to December 31, 2014 the building consumed 126,290 KBTU from the hot water heating system or approximately 150,345 KBTUS of natural gas at 84% boiler efficiency. Taco estimates that this is approximately 75% of the annual gas consumption for heating BTUS. Natural gas consumption prorated for the entire year is approximately 200,460 KBTUS. The energy model predicted that the building would consume 296,900 KBTUS annually. The actual consumption is estimated at 67.5% of the projected consumption. These numbers will be refined as more data is collected.
In considering its LEED application, Taco’s objective was always to implement a system approach to achieving energy efficiency rather than chase individual LEED points. The company wanted to design the most efficient building possible and to see how the design translated into LEED points.
At the time of construction, project manager Chris Integlia, Taco’s executive vice president, said, “Our approach to this project has always been to have LEED certification as a public validation of the efforts we’ve put into the project, and as a confirmation that our products and technologies will help not only Taco but others in our industry achieve highly sustainable green buildings.
“We’re going to do the right things by Taco, and we’ll see how far we can go with that in terms of the LEED scorecard. We do know, however, that the products and technologies we intend to put into the building will achieve a very high level of certification.”
The IDC has been a busy place since it opened and has provided training and education to Taco’s workforce as well as more than 3,000 visitors attending over 50 courses for both residential and commercial training.
The IDC is the second LEED certified project for Taco. In 2009 the company received LEED certification for a new 60,000-sq.-ft. warehouse-distribution center addition to its facility.
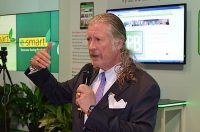
I noticed a slight tremble in his fingers as he raised his hand to wipe his brow. It wasn’t because he was nervous; he has conducted hundreds of press conferences throughout his career. But on the day of the announcement of Taco’s partnership with Italian manufacturer Askoll last November, Taco CEO John White’s words resonated Read more
I noticed a slight tremble in his fingers as he raised his hand to wipe his brow. It wasn’t because he was nervous; he has conducted hundreds of press conferences throughout his career. But on the day of the announcement of Taco’s partnership with Italian manufacturer Askoll last November, Taco CEO John White’s words resonated a theme he’s carried with him since he took over the company from his father. The room filled with press and, more importantly, Taco employees, the message was about them, and how much really loves each and every one in the room that morning, and all of Taco’s employees throughout.

“My primary responsibility is to find ways to grow, develop and protect this company,” said White at the Taco/Askoll press conference. “We have very big, very tough competitors, very good companies. Good competitors, but tough. And so as time has evolved, I’ve learned that one thing I can do is to go and seek relationships, seek opportunities to continue to provide this company with avenues to prosperity and avenues to protection.”
So, continues White, sometime over the last 10 years, there’s been tremendous technological advancement in the area of circulators and we are now moving into government regulations on pumps and circulators for energy efficiency.
Under the terms of the Taco/Askoll agreement, the two companies will collaborate on research and development relating to new circulating pump designs and other joint product and marketing initiatives.
Taco has already begun assembling a new high efficiency circulator for residential and light commercial applications — the VR1816 — which employs Askoll’s variable speed technology, at its Cranston, R.I. plant, and the future calls for the VR1816 to be manufactured entirely by Taco.
The VR1816 is an extension of Taco’s Viridian line of circulators, which is a wet rotor circulator with an ECM permanent magnet motor that uses up to 85% less electricity. It features an infinitely variable speed setting capability for fine-tuning the flow of any hydronics-based system, and six pressure presets to fit the job.
“This is very exciting because No. 1, it protects us. It protects our product line technologically. Secondly, it protects the jobs in Rhode Island. I’m all about protecting these jobs and so this is a chance to do that. And finally, it allows us to form a relationship with a fine company who shares many of the same values as we do,” said White.
The One-on-One
After the press conference, I had a chance to sit down with White in his office, but not until after he made his way through the production floor, addressing the employees he saw by name, shaking hands and giving hugs.
When we sat down, White began to tell a story about when he was in college working in the shipping department, “I’ll never forget one day, I was sitting on a palette of circulators, having my coffee break and a cigarette, and a guy came around with the paychecks. I never saw people so happy in my life. I knew that someday I wanted to run this place. There’s something more to it. When I began running this place I began to pour my heart and soul into the people.”
White began his career working for a Taco sales rep in the Bay Area, which he refers to as Taco West. He eventually made his way East and began working as a Taco rep. “As a rep, I learned the actual value of what we provided to the Tacos. When I came back here, I was the Lone Ranger, as I always understood the value of reps, and that has been very valuable to the evolution of this company.”

As the conversation continued, I asked White about the love for his employees, and his will to protect the company. “That comes from several different perspectives,” said White. “One is that we are a very competitive market. I have competitors that don’t want to see me stay around, which they have made abundantly clear. But they haven’t been able to beat us yet. So I always find a need to find the right things to allow us to continue to grow — whether they are new products, new concepts, designs — we do it all. I spend a lot of my life thinking about this. How are we going to move forward? I have to find ways to be effective with the resources that I have, and I don’t have the chance to make many mistakes. Believe me, I have made a few misjudgments—diverting resources to the thing that didn’t pan out—and I have to be careful with that.
“Another perspective is that I’ve chosen the state of Rhode Island—we are always in the bottom two in terms of business unfriendly—politics, tax prohibitive, to name a few. When I began running the company in 1992, we were about $35M in sales and we had 500 employees, closer to 600. Now we are $250M and we have 500 employees. We have been able to grow the business without adding lots of people, and now we are beginning to add again on the IT, engineering and the human resources side. Our average tenured employee is 20 years and Rhode Island is full of good, hard working skilled workers. It is the best workforce I have seen anywhere in the world.
“The growth this company has incurred and the upgrade in process and efficiency and quality, it’s been done by the same people. We’ve all done it together. Think about that. Those 500 people, a lot of them have been here for the 20 years I’ve been running this company. I feel like to the best of my ability, I owe it to them. Remember, protecting those 500 jobs is protecting the livelihood of thousands —families, suppliers, etc. It’s a pleasurable burden to be able to fulfill.”
Legacy? “My dad’s legacy was the learning center. My legacy would just be able to have allowed people to grow and prosper in their lives. It’s not about money.”
Wrapping up, White told me one last thing, “I’ve learned in life that everybody has a story. If we just took the time to listen to them. The stories I’ve heard throughout my journey, they’ve taught me so many things in life.”
The company’s future looks bright. With the introduction of Wil VandeWiel as the new president & COO of Taco, VandeWiel will oversee daily operations of Taco and work with John White, Jr. and his board of directors in steering Taco’s growth forward in the years ahead. White will remain as company CEO but will refocus his responsibilities on building new partnerships and strategic acquisitions worldwide in pursuit of company growth and diversification. And let’s not forget about John White’s two sons, John White III and Ben White, great men full of potential, at the ready to make great things happen for the future of the company.
The Message Comes Full Circle
Fast forward, the message again was clear as he spoke at last month’s AHR Show, conveying the fact that the company is looking toward future growth — through organic, inorganic and global growth. “With Taco, it’s not just about pumps and valves, it’s about a community. We are in the business of making peoples’ lives better. When a customer buys a Taco product, they are buying into someone’s future, as well,” said White.
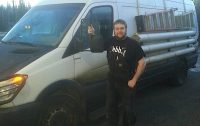
The first installment of the Hydronics CSI was won by Nathan White, Whites Plumbing & Heating, Kenai, AK. His well-thought, concise answer earned him a Lochinvar Jacket. Congratulations to Nathan. Please stay tuned for more Hydronics CSI opportunities. The Flaw: Nathan White’s response: First let’s use a Knight Mod con boiler for this application where Read more
The first installment of the Hydronics CSI was won by Nathan White, Whites Plumbing & Heating, Kenai, AK. His well-thought, concise answer earned him a Lochinvar Jacket. Congratulations to Nathan. Please stay tuned for more Hydronics CSI opportunities.
The Flaw:

Nathan White’s response:
First let’s use a Knight Mod con boiler for this application where we can take advantage of the low return water temp, modulation , outdoor rest features for a high efficiency package. But since it is a solution boiler here’s what needs changed. 1) need closely spaced tees (the ones in the picture are incorrect as you need min 10 pipe dia of straight pipe from each branch and a maximum of 4 pipe dia between the branches) or use my personal favorite a Caleffi Sep4 hydro separator to hydraulically decouple the two circulators, eliminate air, dirt and magnetic particles. 2)The solution boiler with its copper fin construction needs a Low temperature bypass valve in constant low temperature application. This valve would be placed before the suction side of the boiler pump which need to have a(3) integral check or a check valve on the discharge side of it. (4) if not using the Caleffi Sep4 then you will need a Y strainer as well on the return side of the boiler to protect the heat exchanger. (5) The air separator could be removed from the system if a Caleffi Sep4 was used. (6) A system sensor also needs to be hooked up when the solution is ran in a low temp application with the LBV. (7) lets put some valve in this design Paul for the poor guy that has to service it in the future doesn’t have to drain the world to replace a pump. So iso valves on both sides of each pump and ball valves with purge drains on the other lines as a bare minimum to make for easy filling and purging of the system. (8) The boiler pressure relief valve needs to be turned down toward the floor.
The Correction:

The Answer:
1) The closely spaced tee’s separating the boiler loop from the secondary loop do not isolate the differential pressure from the boiler pump. In short, the boiler pump was in series with the zone pump.
2) The boiler is a non-condensing boiler and the (typical) low-return water temperatures from the radiant floor heat would cause the boiler to condense. Sustained flue gas condensation would over-time cause the heat-exchanger in the boiler to fail and the vent could degrade and allow CO to fill the structure. The LTV (Low Temp Valve) will ensure the water temperature entering the boiler will be 140°F or higher.
3) The boiler will produce temperatures above that of low temperature radiant floor heat requirements. The use of a 3rd party mixing valve to provide outdoor reset will allow the proper mixing. (One of several methods of OD reset mixing)
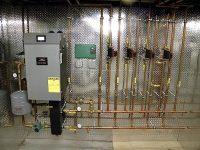
Natick, Mass is located just 15 miles west of Boston. Settled in 1651, the old town’s history is vividly displayed through its infrastructure and architecture. After 134 years, the Bacon Free Library is still just that — a red brick beacon to education and exploration. Not far away, the Eliot Church of Natick was founded Read more
Natick, Mass is located just 15 miles west of Boston. Settled in 1651, the old town’s history is vividly displayed through its infrastructure and architecture.
After 134 years, the Bacon Free Library is still just that — a red brick beacon to education and exploration. Not far away, the Eliot Church of Natick was founded as a church and meetinghouse in 1651, where native Praying Indians and white settlers would come together in worship.
The Station tree, a 500-year-old, black oak, was respectfully left standing over the centuries, marking the boundary between Natick and Needham, MA. The age of the town — and its regard for all things antiquated — can be seen in almost every element. Even its heating elements.
“Most of the homes in Natick are hydronic museums,” said Derek Nord. “Steam of every variety is still used, and is still comfortable. But when the old steam boilers fail, most homeowners look to hot water as a replacement.”
Nord is a one-man boiler band. His laser-like focus on all things hydronic, paired with meticulous attention to detail, have kept him busy since starting Nord Plumbing & Heating in 2010.
Collaboration
“I love boilers,” he continued. “Hydronics and plumbing are all that I do. I know some really great guys if I encounter a job that needs AC or ductwork.” And those guys often return the favor when they need a boiler mastermind. According to Nord, he’s friends with a number of other tradesmen in town. They collaborate on projects if need be – even to the point of handing their calls off to each other when they’re on vacation.
With real estate at a premium around Boston, many homeowners in Natick improve and add onto existing homes instead of relocating. A recent remodel of Nord’s own 75-year-old Cape Colonial required the kind of collaboration Nord is used to.

Quik Trak radiant panel system was installed throughout the lower level of the home before hardwood was installed.
The 1,400-square-foot home used steam heat and lacked any sort of air conditioning when he and his wife purchased it. The downstairs was gutted, and the existing porch was closed in to create a master bedroom, adding about 300 square feet.
Nord not only did his own mechanical work, but also opted to do the framing for the project himself. After carefully considering what it was he wanted to accomplish, Nord had the heating system mapped out, and called a friend for help with the AC.
“Given the lack of space, we decided against a regular ducted system,” said Nord. “We didn’t like the idea of evaporators hanging on the walls, so we chose a SpacePak high-velocity AC system over mini-splits.”
Small, but not simple
The job resembles Nord’s company and capabilities well; small, but by no means simple.
One of the complaints about the original system was that it was hard to control during the wild temperature swings that New England can experience. Nord wanted to make sure they were curbing expense while also optimizing comfort.
In the basement, Nord tore apart and removed the old 80,000 BTU steam boiler. Much to his surprise the unit was undersized. He hung several pieces of diamond plate aluminum and a 95 percent efficient, 105 MBH Burnham Alpine condensing boiler on a nearby wall, to be joined shortly by a number of other hi-tech, high efficiency products.

The boiler would eventually supply heat to four zones; upstairs fin-tube baseboard, downstairs radiant in-floor tubing, European-style panel radiation in the master bedroom and a 60-gallon indirect tank for DHW. Directly under the Alpine, Nord used a low-loss header, or hydro separator, to create a secondary loop from which all connected load draws. This allows for numerous zones to pull from the boiler at different flow rates simultaneously. It also adds a little extra water volume to the system.
“Controlled by the boiler’s outdoor reset, hi-temp water is supplied to a secondary loop,” explained Nord. “Via injection pumping, the hi-temp loop feeds fin-tube radiation upstairs, a single, six-foot long, three-panel Runtal panel in the well-insulated master addition, and the water heater.”
The primary loop uses a three-speed Taco 00R circulator, while each zone operates off its own Grundfos circulator. There is an extra circulator and set of closely-spaced tees installed but capped off for future use in the basement.
The secondary loop also supplies hi-temp water to a Viega hydronic mixing block, which selects a supply temperature for the five in-floor radiant loops based on its own ODR sensor. Very often, this runs between 100 – 115°F.
Careful selection
“Any time you’re putting together an intricate system like this, regardless of size, you really need to select components based on their individual performance as well as their ability to mesh well with each other,” said Nord. “Overall system performance can be tricky to perfect, but it’s a beautiful thing!”
Nord says he selected the Alpine boiler based on a number of factors, the first of which is that he simply doesn’t get any callbacks when he installs them. He initially switched to the Alpine because he wanted a stainless steel heat exchanger instead of aluminum. Since then, he’s found that the broad size range – from 80 to 399 MBH – means that the unit fits just about application he’s come across.
“The Alpine is very easy to install, and readily available through The Portland Group,” said Nord. “I use it on most of my hot water jobs.”
With the exception of the master bedroom, the downstairs is heated by Uponor 5/16 PEX in Quik Trak subfloor paneling under quarter-sawn oak flooring.
Last winter, Nord saw a roughly 40 percent savings on energy, despite the added living space and much improved comfort. “It’s not unheard-of for one of these oil-to-Alpine jobs to save upwards of 75 percent,” said Nord. “A few years ago I had a family tell me they were spending $800 per month on oil during the coldest part of the season. After the retrofit the following year, they were spending roughly $200 to $250 for gas each month.
Space at a premium
The job progressed slowly but deliberately. When the walls were torn out, they installed supply lines to the upstairs radiators and roughed in the high-velocity AC. Radiant tubing went down at a different time, and the bedroom panel radiator was installed late in the game.
“One of the biggest challenges was running supply and return lines through the basement,” said Nord. “The old, load-bearing posts and beams in the basement were tough to work around.”
But it’s Nord’s ability to work hydronic magic in historic homes that makes him a real asset to his community, whether that includes optimizing antiquated systems or installing cutting edge equipment in turn-of-the-century structures.
Date started: August, 2012
Date Finished: May, 2014
Size of Project: 1,400 square-feet
Workers onsite: 2
Boiler — Burnham Alpine condensing boiler, 105k BTU input
Mixing Block — Viega
Panel radiator — Runtal
Fin-tube radiation — Slant/Fin
Pumps — Taco primary, Grundfos secondary
Relays — Taco
Manifolds — Uponor 5-loop EP radiant heat manifold
Piping — Uponor 5/16 PEX
Radiant panels– Uponor Quik Trak
Tools Used — Viega ProPress
Valves — Watts and Webstone ball valves
Separators — Taco vent on primary, Spirotherm on secondary loop
Air conditioning — SpacePak high-velocity system