1) The closely spaced tee’s separating the boiler loop from the secondary loop do not isolate the differential pressure from the boiler pump. In short, the boiler pump was in series with the zone pump. 2) The boiler is a non-condensing boiler and the (typical) low-return water temperatures from the radiant floor heat would cause Read more
Heating & Cooling
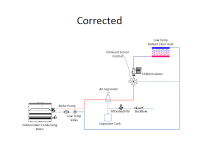

1) The closely spaced tee’s separating the boiler loop from the secondary loop do not isolate the differential pressure from the boiler pump. In short, the boiler pump was in series with the zone pump.
2) The boiler is a non-condensing boiler and the (typical) low-return water temperatures from the radiant floor heat would cause the boiler to condense. Sustained flue gas condensation would over-time cause the heat-exchanger in the boiler to fail and the vent could degrade and allow CO to fill the structure. The LTV (Low Temp Valve) will ensure the water temperature entering the boiler will be 140°F or higher.
3) The boiler will produce temperatures above that of low temperature radiant floor heat requirements. The use of a 3rd party mixing valve to provide outdoor reset will allow the proper mixing. (One of several methods of OD reset mixing)
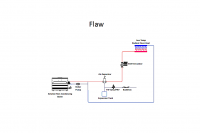
Mechanical Hub and Lochinvar are proud to team up to bring you a new feature called “Hydronics CSI.” Hub friend Paul Rohrs, design and application specialist for Lochinvar, has produced a hydronics design with intentional flaws in it. There are multiple mistakes with this diagram and it is up to you to use your hydronics Read more

Mechanical Hub and Lochinvar are proud to team up to bring you a new feature called “Hydronics CSI.” Hub friend Paul Rohrs, design and application specialist for Lochinvar, has produced a hydronics design with intentional flaws in it. There are multiple mistakes with this diagram and it is up to you to use your hydronics knowledge to figure out what they are.
The contestants who come closest to the answers will be put into a drawing to win a jacket from Lochinvar.
The above is our first installment. Good luck!

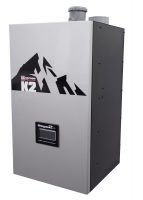
The new Burnham K2 condensing boiler was designed based on feedback from field professionals who were asking for an easier boiler to service and install. In addition, the combination of high efficiency, performance and high value make the K2 ideal for households that might otherwise opt for a traditional boiler. At up to 94 percent Read more
The new Burnham K2 condensing boiler was designed based on feedback from field professionals who were asking for an easier boiler to service and install. In addition, the combination of high efficiency, performance and high value make the K2 ideal for households that might otherwise opt for a traditional boiler.
At up to 94 percent AFUE, this ENERGY STAR rated boiler uses a proven stainless steel heat exchanger and cutting edge Sage 2.1 Control System with factory pre-sets to speed installation.Touch screen diagnostic display and free five-year parts & limited labor warranty offer additional benefit.
The K2 is available in five sizes ranging from 80 to 180 MBH, and offers features such as 5:1 turndown and a “cold burner door” that’s safe to touch even while firing. The boiler’s simplified design includes a hinged inner door that isolates electronics and controls from combustion and waterside components, making for fast, clutter-free service access.
A pre-installed, high capacity boiler loop circulator is included, as is an innovative split-voltage junction box, enabling simple, error-free wiring connections. Venting the K2 is simple as well, regardless of whether one pipe, two pipe, horizontal or vertical configurations are needed.

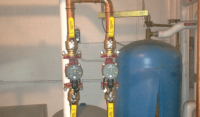
This story has to do with a lot of people doing the wrong thing at different points in time, and the waste and consequences, and eventual satisfactory resolution to the problem. The story begins back in the late 1960s. A young, first-year engineer was given the task of designing the hydronic heating system for a Read more
This story has to do with a lot of people doing the wrong thing at different points in time, and the waste and consequences, and eventual satisfactory resolution to the problem.
The story begins back in the late 1960s. A young, first-year engineer was given the task of designing the hydronic heating system for a Catholic Outreach facility that housed employees who worked to help the homeless find homes, employment and other resources—to help them get through rough times. The young M.E. in training had performed the calculation required to not only provide heat to the administrative offices, but also provide DHW through two indirect heaters. Being his first commercial job, he didn’t want to ever get a call from the end users telling him that the system was insufficient, so as he was adding up the thermal load flow requirements, he was also adding up the required feet of head. He was confused, and thought that the feet head required to overcome the thermal loads, was accumulative. He chose a circulator that could match the accumulative GPM requirements, as well as the accumulative feet of head. This was the first of many mistakes made by many people.

Fast forward to 2010. The building was a candidate for an energy upgrade that was to be financed by a division of the federal government, tasked with distributing funds to low income and non-profit organizations. The local non-profit organization charged with the final distribution of funds had hired a local energy conservation consultant to assist in the preparation of bid documents to allow local heating contractors to bid on a level playing field. Essentially, they went in and documented the existing equipment, and prepared a bid document asking the bidding contractors to replace the existing equipment, with higher efficiency equipment. Mistake number 2.
The local contractors bid their work based on the information provided by the conservation consultant. The general thought was, that due to the fact that it was originally an engineered system, it has to be right. Mistake number 3.
The recipient of the bid decided that he would match equipment, spec for spec, but use state-of-the-art equipment with higher efficiencies. He replaced the 3-phase circulator with a circulator of similar performance characteristic, but a more efficient 3-phase motor. He replaced the existing cast iron fire-breathing dragon with two modulating condensing boilers. Mistake number 4.
Shortly after the replacement with the high efficiency pump and boilers, the occupants of the building began complaining of over heating in the administrative building. The nun in charge of the operations complained to the installing contractor. The installing contractor pointed the finger of blame at the conservation consultant who determined the equipment needs. The consultant pointed his finger at the blueprints that they were given, which resulted in the selection of the replacement equipment. The plans had an engineer’s stamp on them, so they had to be correct, right? Mistakes 5,6 and 7.
Somehow, the electrical contractor got involved, and even he stated that due to the fact that 208-volt, 3-phase power was provided, that he had to use the 3-phase pump provided by the heating contractor. Mistake number 8.
The poor nun had given up all hope of ever getting the problem resolved, and took matters into her own hands, and began opening and closing ball valves serving the baseboard convectors in the administrative offices. When she was gone, her assistant took over and handled the daily task of opening and closing valves in an effort to maintain comfort conditions.
Enter a forensic hydronic heating expert. His specialty was taking other peoples seemingly impossible to resolve problems, and solve them.
He performed a reverse engineering program, and checked the convectors against the square footage of building served, and determined that they were slightly oversized, which is good when you are utilizing a modulating/condensing appliance. He calculated the other connected loads and determined the highest pressure drop to be serviced by the pump. The individual space heating zones located throughout the administrative building are controlled by a conventional Honeywell zone valve, which has a“close off against” pressure of 8 PSI, or 18 feet of head. The space heating circulator is capable of generating 35 feet of head at its mid curve point, and almost 50 feet of head in a no flow condition (dead head).
There are no piping bypasses nor pressure-activated bypasses in the hydronic distribution piping network. The zone valves are consequently bypassing, causing significant overheating of the offices in the building.
The main space heating pump is consuming 2,992 watts per hour, and is running 24 hours per day, 365 days per year for a total of approximately 26,218 KWH’s per year. At $0.10 per KWH, this results in an annual electrical cost of $2,621.00.
The pump was replaced with two Grundfos ALPHA pumps piped in parallel reverse return. Their maximum energy consumption was seen at 43 watts each, for a total of 86 watts, peak. Based on the above calculated run times, the annual energy consumption of the two parallel Alphas would be 86 * 24 * 365 for a total of 753 kilowatt hours per year. At $0.10 this will cost $75.33 per year, resulting in an annual savings of $2,546 per year. This is money that can and will go towards feeding and clothing the homeless. None of these calculations takes into consideration the reduction in KW demand charges from the local electrical utility, or the reduction in waste associated with over heating spaces at night when the manual ball valves were left open.
The moral of the story is this. If someone, especially a 75-year-old nun complains about the comfort conditions in a given space, trust her. She’s not telling a fib. NEVER EVER take a system for granted just because a blueprint has an engineer’s stamp on it; it doesn’t really mean it was done right.
Think outside of the box, and don’t be afraid to try something that would work, but isn’t the norm (parallel variable speed constant pressure pumps).
Many thanks to the good folks of Grundfos, who donated their product to this excellent non-profit agency, and showed how to conserve pumping energy, and increase human comfort.
By the way, the Nun has joined a local health club because she is no longer running around, stooping down, closing valves and standing up and running to the next zone.