In Pennsylvania, poultry is the state’s biggest agricultural business. And that means giant piles of bird waste: manure. Typically, farmers spread it on the fields. Chicken farmer Earl Ray Zimmerman was exploring ways to increase his farm’s sustainability and profitability. At the same time, a local energy-solutions company was putting the pieces together for a Read more
Heating & Cooling
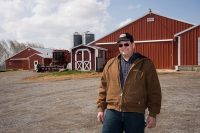
In Pennsylvania, poultry is the state’s biggest agricultural business. And that means giant piles of bird waste: manure. Typically, farmers spread it on the fields.
Chicken farmer Earl Ray Zimmerman was exploring ways to increase his farm’s sustainability and profitability. At the same time, a local energy-solutions company was putting the pieces together for a heating system plan that would take the need for heat, and the need to dispose of manure, and cancel them both out.

The manure burning heating system fits well with the overall sustainability theme Zimmerman has applied to his organic farm.
Not too long ago, Zimmerman’s two, 500-foot long chicken houses were entirely heated by direct-combustion unit heaters.
Today, with state-of-the-art, bio-fueled hydronic technology, he’s burning chicken manure instead.
Chicken manure contains roughly 3,500 BTUs per pound,” said Matt Aungst, co-owner of Total Energy Solutions, LLC in Willow Street, PA, the company behind the entire design of the heating system.

System designers, Matt Aungst and John Albright stand next to their brainchild. The heating solution depends upon the ability to precisely monitor flow rates via Taco KV series sensorless pumps with variable frequency drives.
Over several months, TEC designed a system that would burn manure to fire a large hydronic system that serves both large chicken houses.
“For this project, we teamed up with two companies who lead their markets in craftsmanship and ingenuity,” continued Aungst. “Farmer Boy Ag Supply, in Myerstown, PA, provided installation talent, and Taco Inc., in Cranston, RI, provided the engineering brainpower to get the BTUs where they need to be with Taco KV series of SelfSensing pumps.”

From any web-enabled device, Zimmerman can make extremely precise changes to the temperature within the houses. The Danfoss PICV (pressure independent control valves) modulate to a specific flow rate, and the sensorless Taco pumps in the mechanical room change speed accordingly.
One chicken house can call for up to 600 MBH at any given time, but an average heat load in the winter is likely to be around 200-300MBH per house. At the center of the new hydronic system is a 1.5 million BTU, manure-burning boiler. The system was designed and engineered to provide 100% of the heat load.
The boiler is the size of a service van, and occupies its own remote building. An auger feeds dry manure from the hopper into the boiler, which doesn’t produce strong odors or much smoke.
The heart of the distribution system is also in the mechanical building. Two redundant VFD-powered Taco SelfSensing pumps are plumbed in parallel. Three-inch PEX water lines run 300 feet to a distribution manifold between the two chicken houses. The new Taco SKV3009 SelfSensing pumps accurately respond to changes in system demand without the need for pressure sensors.
Inside each chicken house, eight CUBO unit-heaters hang from the ceiling, providing the water-to-air heat exchange. The units are designed exclusively for the poultry industry and provide air mixing, destratification, and lateral heat distribution.

Matt Aungst, who designed the distribution portion of the project tests redundancy of the only two pumps on the entire project. Pump A runs as “duty”, leaving pump B for backup. After 84 hours of run-time, the pumps automatically switch roles.
Each one of these unique unit heaters has its own Danfoss PICV (pressure independent control valve). The PICVs act as variable zone valves, with the ability to modulate flow depending on the temperature at the nearest thermistor.
But the PICVs and CUBOs need a circulation system that’s compatible. The Taco pumps react to the specific call for water — regardless of the number of valves calling or how far open the valves are.

John Albright, of Total Energy Solutions, LLC, and chicken farmer Earl Zimmerman watch the biofuel boiler cycle.
The seven-and-a-half horsepower pumps are each programmed to supply a maximum of 125 GPM at 85 feet of head. According to Jeff Pitcairn, Taco’s commercial regional manager, pump A runs as “duty,” leaving pump B for backup. After 84 hours of run-time, the pumps automatically switch roles.

Left to right – Matt Aungst and John Albright, owners of Total Energy Solutions, LLC, in Willow Street, Pennsylvania, designed the hydronic biofuel system that now serves two chicken houses at Zimmerman’s farm.
According to Zimmerman, chickens are extremely temperature sensitive. In a chicken house, even a 10°F drop for an hour could seriously affect his bottom line. The SelfSensing pumps, PIC valves and CUBO unit heaters work harmoniously to deliver the exact temperature needed, 24/7/365.

There’s little doubt that Zimmerman’s installation achieves energy savings, heat distribution and farm production benefits that surpass any other hydronic poultry heating system available.
And now, as Americans learn more about the impact of a national bird flue epidemic that’s forced higher prices for all poultry products, Zimmerman’s fighting back with smarter systems that have the ability to produce more food with less cost and lower environmental impact. That’s smart farming.
Boiler — Blue Flame Stoker, 1.5 MMBTU
Design software — Taco HSS
Radiation — CUBO unit heaters
Pumps — Taco KV SelfSensing
PIC valves — Danfoss
Balancing valves — Taco Plus Two valves
PEX — Logstor
Expansion tank — Taco, 125 gallon
Air separator — Taco 4903
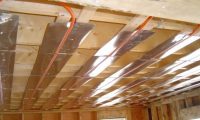
Radiant cooling has been utilized in commercial cooling settings for more than 20 years. A very active, very large airport — Suvarnabhumi International Airport in Thailand — has been successfully using radiant cooling for two decades. Radiant cooling works in much the same way that radiant heating works. Most people who have basements have experienced Read more
Radiant cooling has been utilized in commercial cooling settings for more than 20 years. A very active, very large airport — Suvarnabhumi International Airport in Thailand — has been successfully using radiant cooling for two decades. Radiant cooling works in much the same way that radiant heating works. Most people who have basements have experienced radiant cooling without even being aware of it. In older homes without concrete wall insulation, the ground temperatures below grade dictate the Mean Radiant Temperature (MRT) in a basement setting. When a person walks from upstairs to down into the basement, the body’s sensors sense this lower MRT, and it “feels” cooler than the upper floors, even though the air temperature is nearly the same.
The three major environmental factors that dictate human comfort are MRT, which is the average surface temperature of the surfaces surrounding our bodies, relative humidity, and air temperature. Maintaining all three of these in a radiant cooling application is different than what is required when using a conventional air conditioning system. By lowering the mean radiant temperature and controlling the humidity, good human comfort is achievable for cooling at air temperatures that are significantly higher than we typically see with a conventional air conditioning system. This is because RT is one of the primary factors that dictates human comfort. The air temperature and relative humidity can be perfect, but if the MRT is off in one direction or another most people will be uncomfortable. Control of the relative humidity in a radiantly cooled environment is not just a good idea, it is mandatory in order to avoid the production of condensation on the surfaces of the radiant panel.
Residentially speaking, this requires the use of window and door proximity switches, and if any of these openings are left open no radiant cooling is provided. If humidity is controlled and maintained between 30% and 60%, and the chilled water temperatures are kept between 50 and 70 degrees F, then condensation production is not possible under these conditions. The use of a dew point controller is also a minimum requirement whenever radiant cooling is to be employed.
In commercial settings, rarely are windows operable and doors are always on auto closers, so the production of condensation on the radiant sources is not an issue where humidity is being controlled between 30% and 60%.
In certain areas of the country, it is entirely possible to use the building’s irrigation system during the summer months to provide a coolth source for augmenting the cooling of a given structure utilizing radiant cooling. This will obviously require the addition of heat exchangers and pumps, but still represents a free source of cooling. Another potential source that is being exploited is “Night Sky Re-radiation Cooling.” This requires the placement of unglazed solar collectors on the roof of a dwelling to reject built up heat into the night sky. I have personally witnessed collector absorber temperatures that are as much as 20 degrees F. cooler than the lowest ambient temperature seen for the same period of time.
And, of course, there is always ground source heat pump systems, which have a proven track record of efficiency and reliability. There are some new variations of this age old system bubbling to the surface, and they are showing a huge potential as it pertains to radiant heating and cooling applications. (Thermal Battery Storage systems, for instance.) It is also entirely possible to utilize the ground source vertical bore fields as a cooling source under the right conditions without the need to fire a compressor. Remember, the typical approach temperatures for a radiant panel vary between 50 and 70 degrees F.
Having too much or too little much humidity will also significantly sway the human comfort factors, regardless of what is happening with the MRT and air temperature. In areas of high humidity, it is necessary to maintain the relative humidity between 30% and 60%. This not only provides better human comfort, but also has to do with the control of microbial bacteria, dust mites and preservation of fine wood products. In humid climates, it will be necessary to dry the air out. For make up air units, a method known as DOAS (Dedicated Outdoor Air Systems) is used to wring the humidity out of the incoming air before introducing it into the controlled environment. Internally generated humidity is controlled and removed through the use of refrigerant-based direct expansion dehumidification systems, where the room air is first run across an evaporator coil to remove excess humidity and then the condenser reheats the stream of air. This avoids overcooling the air and creating “cold 70” conditions.
Conversely, in areas with low humidity it may be necessary to introduce humidity into the controlled environment. This can be done with the use of direct evaporative cooling, or direct humidity injection systems. There are even some newer classifications of indirect evaporative cooling systems known as Maisotsenko M-Cycle cooling systems. This type of system uses an indirect heat exchanger to avoid the possible generation of humidity into the conditioned air stream, which in some cases can cause discomfort or mugginess.
In conventionally “air conditioned” systems, there is the need to not only cool down the air, but also to control the relative humidity within the controlled space. At times, the demand for air dehumidification causes the air conditioning system to over cool the air, resulting in more complaints about the air being excessively cold.
In a radiantly cooled controlled environment, the majority of the sensible cooling demand is handled by the control of the MRT surfaces. By allowing the radiant cooling system to handle the majority of the sensible demand, the amount of air movement required to handle the latent (humidity control) demand is significantly smaller. This can result in a significant decrease in cooling energy, resulting in energy savings of 50% or more depending upon the application.
It also opens up more “off peak” ice generation/storage options because the approach temperatures of the water used in radiant cooling systems typically vary between 50 and 70 degrees F. By shifting the electrical and mechanical energy consumption to “off peak” periods, additional monetary savings can be achieved.
Another area that is receiving major attention is the use and application of Phase Change Materials. This method is incorporated into the structure of the building, and in some cases uses free nighttime cooling or off peak electricity to “freeze” the phase change materials. As the materials absorb heat energy, they go through the reverse phase change and “melt,” absorbing significant amounts of thermal energy. They can reduce peak loading by as much as 30% in a hot climate. Although they do not and cannot address the latent energy loads, they do a fantastic job of addressing the sensible loads, which are the biggest load in most commercial buildings. These compounds can be custom tailored to operate at any temperature that is normally used to maintain comfort in a given structure.
Mark Eatherton is the executive director for the Radiant Professionals Alliance (RPA).
References:
http://www.coolerado.com/company/faq/ Indirect evaporative coolers
http://www.phasechange.com/index.php/en/ Phase Change Materials
http://www.solarthermalbiz.com/archives/3710 Night Sky Radiational cooling
http://www.healthyheating.com/Page%2055/Page_55_i_cooling_eq.htm#.VJGsiCcBg Radiant Cooling
http://www.healthyheating.com/solutions.htm#.VJIX7CcBg Comfort Calculator
http://www.aeecenter.org/files/newsletters/ESMS/Sastry.pdf Side by side comparison of radiant cooling versus regular cooling
http://thermalbatterysystems.com/2013/03/22/seasonal-thermal-energy-storage/#.VJIbWCcBg Thermal Battery Storage Systems Inc.
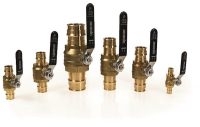
Uponor North America (Uponor) is now offering a new, more cost-effective ball valve option for radiant heating/cooling and hydronic piping applications. These code-listed, commercial-grade, PEX-to-PEX, full-port ball valves are available in ½” to 2″ sizes and are appropriate for non-potable PEX piping applications. The valves are available on-demand in CAD and BIM design files Read more
Uponor North America (Uponor) is now offering a new, more cost-effective ball valve option for radiant heating/cooling and hydronic piping applications. These code-listed, commercial-grade, PEX-to-PEX, full-port ball valves are available in ½” to 2″ sizes and are appropriate for non-potable PEX piping applications.

The valves are available on-demand in CAD and BIM design files via www.uponorengineering.com or www.arcat.com to make designing and specifying fast and easy. Additionally, they are listed to ANSI/NSF 14 and cNSFus-rfh and tested to ASTM F877, ASTM F1960, CSA B137.5 and NSF 359, allowing professionals the flexibility to add a reliable, code-listed valve anywhere in a commercial radiant heating/cooling or hydronic piping system.
Stem Extension Valves
“We are continuing to see growth in our indoor climate business, especially with hydronic piping applications,” says Mark Hudoba, director, Heating and Cooling at Uponor. “Offering these cost-effective, code-listed valves provides professionals in the industry with a trusted, reliable product for hydronic piping as well as radiant heating and cooling applications.”
The valves, which are compatible with systems containing up to 50 percent propylene glycol, feature blow-out-proof stems and are available with stem extension kits to accommodate up to 2″ of insulation in insulated piping applications. Additionally, both ends of the valves are manufactured with Uponor’s proven ProPEX® fitting system for expansion connections that cannot be dry fit and hold tight with up to 1,000 pounds of radial force.
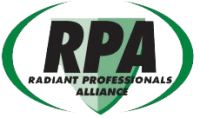
Fellow Hydronic Professionals,, I have been the director of the RPA now for 2 and 1/3 years. It has been an arduous journey, with some ups and some downs, mostly ups, but we (I especially) do this for the industry. We now have in place one of the most dynamic group of people (members on Read more
Fellow Hydronic Professionals,,
I have been the director of the RPA now for 2 and 1/3 years. It has been an arduous journey, with some ups and some downs, mostly ups, but we (I especially) do this for the industry.
We now have in place one of the most dynamic group of people (members on committees and members in general) and are kicking butt and taking names. We have an actual Hydronics/Radiant Code that is part of the Uniform family of codes (Uniforms Solar Energy Hydronics Code) and are in the final stages of developing an ANSI recognized, ASSE developed Professional Certification program for designers and installers.
We have and continue to add instructors to, our online university, RPAU, with HeatSpring offering some of the best instructors time and money can buy, making education of yourself and your employees available at YOUR convenience.
We recently inked a deal with Tom Grandy and Associates to help show experienced contractors how to turn their hard work into a good profit margins so they can retire comfortably or live well before retirement.
We have inked a deal with Kilowatt Financial to provide low interest, high dollar (up to $30K) financing IN THE CONSUMERS HOUSE. (less than 30 minute approvals online)
We have renewed commitments from UPS offering our members a significant discount on shipping less than truck loads.
We have a monthly newsletter available to members only.
We have printed magazines to help you sell radiant comfort (walls floors and ceilings) to the consumers.
We have monthly Lunch and Learn webinars to keep you abreast of the latest and greatest in our industry.
We have HydroniX Talk (which is on summer vacation) which is also available to members only, and will now be taking place early evenings during the week, beginning this coming fall, featuring the likes of Dan Holohan and many other notable hydronics pioneers.
All of this for a contractor for less than $1.00 per day (actually less than that because the $300/year fee is good for 3 employees) as well as access to some of the best minds this industry has to offer (locked access LinkedIn accounts).
And we continue to look for ways to promote this wonderful industry of ours so that we can prove to the world something that most people here have known for a long time, that being that hydronics is THE most efficient method of transferring energy from point A to point B, or from point B to point A.
We have legislative power in Washington DC looking out for our industry’s interests. (The old RPA was not allowed to lobby)
There’s only one major missing component…..
>>> YOU! <<<
I and my membership committee (and the other 7 committees) are baffeled as to why former members of the old RPA and new potential members are not coming back into the fold.
So, I’d like to ask some questions and clear up some rumors.
Rumor 1: IAPMO runs the RPA. Wrong, WE run the RPA. IAPMO owns it lock stock and barrel, and provides us with all of the tools and support we need to further its goals, but the RPA is run by its members. It is an organization OF the members, BY the members, FOR the members.
Rumor 2: RPA is dead. Wrong, it came extremely close to going under during the economic down turn, and if IAPMO had not intervened, it would have gone down in flames. Fortunately, IAPMO caught it before it plowed into the ground, gave it a soft landing, re-painted the plane, refueled it and sent it back up into the air.
Rumor 3: IAPMO is dead. This couldn’t be further from the truth. IAPMO is the largest CDO (Code Development Organization) in the world. In fact they are expanding and now have offices around the world, helping to establish plumbing and mechanical codes around the world.
Rumor 4: IAPMO and the RPA are too big for me to consider joining. WRONG, these organizations are here to support you, not fight you. Every code and standard that is developed by these organizations are done so under a very tightly watched and controlled ANSI Open Consensus process. No complaint goes unattended or ignored. All concerns are addressed until there are no more concerns.
So, my question to you is why have you (contractors, designers, installers, equipment manufacturers, manufacturer rep agencies and others) not joined, or rejoined this fantastic organization? There is strength in numbers, and if we as an industry don’t band together real soon, there is a real possibility that our industry will be put out of business by some very savvy foreign interests who have stated publicly that their intent is to take over ALL methods of heating and cooling.
Tell me what rumors you’ve heard, or why it is that you haven’t joined this organization. We are all ears, and we want to make certain that this machine is your machine, and that it does work for YOU, the industry.
I’d also like to thank all of our volunteers and our board of directors for their guidance in getting the ship to this point. Without your help, we wouldn’t have gotten this far. THANK YOU.
Now, tell me what your concerns are?
If you’d like to join, go to www.radiantprofessionalsalliance.org and click on the JOIN button, or simply call Alan Wald, our Vice President of Memberships at 909-472-4211and he or one of his staff can get you signed up over the phone. Easy squeasy lemon peasy.
Thank you for your consideration, and thanks to the Mechanical Hub for being a member and allowing us to use this venue.
Mark Eatherton
Executive Director, Radiant Professionals Alliance
18927 Hickory Creek Drive, Suite 220
Mokena, IL 60448
Desk: 708-995-3001
Toll free: 877-427-6601
www.radiantprofessionalsalliance.org
Email: mark.eatherton@radiantprofessionalsalliance.org
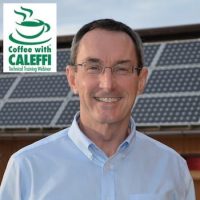
John Siegenthaler, P.E., a seasoned industry expert with over 30 years’ experience designing modern hydronic heating systems, author and popular guest speaker for the Coffee with Caleffi™ webinar series, returns on Thursday, July 23 at 12 noon CDT discussing Utilizing Thermal Buffering in Hydronic Systems. There are many types of hydronic systems where the rate Read more
John Siegenthaler, P.E., a seasoned industry expert with over 30 years’ experience designing modern hydronic heating systems, author and popular guest speaker for the Coffee with Caleffi™ webinar series, returns on Thursday, July 23 at 12 noon CDT discussing Utilizing Thermal Buffering in Hydronic Systems.
There are many types of hydronic systems where the rate of heat generation is different from the rate at which the building requires heat. When only one or two zones require heating, the output of the boiler far exceeds the rate of heat demand. This can lead to heat source short cycling, reduced efficiency and shorter equipment life. Siegenthaler will explore how to avert such conditions by adding thermal storage to the system.
The one-hour educational webinars are free and are intended for contractors, designers and wholesalers. Please visit Caleffi’s website at www.caleffi.com for schedule details and registration.