When Eric and John asked me to write a blog post on “Hydronics 101,” I have to admit I was a bit overwhelmed. Where on earth do you start? There’s boiler piping, pipe sizing, circulator selection, heat emitter selection, controls wiring, and so on. There are so many avenues to take when it comes to Read more
Heating & Cooling
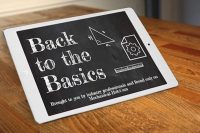
When Eric and John asked me to write a blog post on “Hydronics 101,” I have to admit I was a bit overwhelmed. Where on earth do you start? There’s boiler piping, pipe sizing, circulator selection, heat emitter selection, controls wiring, and so on.
There are so many avenues to take when it comes to “Hydronics 101” that choosing a starting point becomes quite a daunting task.
But then I thought of one of the very first training classes I ever did.
It was 1995 during a full-day program on radiant floor heating. We were going through the process of radiant design — figuring out installation method, tube spacing and water temperature. We were looking over charts and graphs to make heads or tails out of this radiant job when a fellow in the back of the room raised his hand.
“Don’t you have computer software that figures all this stuff out?”
Yep, we do.
“Then why are you wasting our time telling us all this? Just give us the software and we can go home.”
Ummm, it doesn’t quite work that way.
Design software, whether it’s for hydronics or forced air, is really nothing more than a fancy calculator. It does the arithmetic for you, and that’s about it. It doesn’t think for you, it doesn’t make decisions for you and it doesn’t tell you if you’ve input the wrong data.
It’s a calculator.
That’s it.
I like to ask folks in my classes how many of them have been formally trained in how to perform heat loss calculations. We call it “doing the math.”
As the years have gone by, fewer and fewer people raise their hands. No one’s teaching heat loss anymore, and I think it’s a shame. Knowing the actual heating load of a house or of a zone is the real “starting point” for beginning hydronics or for advanced hydronics.
How can you size a boiler if you don’t know the load? You can guess, but it’s just that: a guess. You can base your load on a standard BTU-per-square-foot multiplier, but that’s not a heat loss calculation. That’s just a guess with better PR. You can even measure the radiation, multiply by whatever multiplier you care to use and call that the load. But all that tells you is how much radiation is installed.
Good to know, but it doesn’t tell you the actual load of the house.
There’s no way around it: a good old-fashioned heat loss calculation is the only way of getting anywhere close to what the actual load of the house really is. Are “by-the-book” heat loss calculations 100% accurate? Nope — there’s so much fudge built in to the calculation methods out there that it’s a wonder we’re not all diabetic. But they’re still better than guessing.
During one of Taco’s Heat Loss classes a while back, the class was presented with a set of blueprints for normal, stick-framed house. There was nothing special about this house. It wasn’t super-insulated with super-low E windows or anything. It was a basic 2200 square foot ranch, with an outdoor design temperature of 7 degrees above Zero.
I asked the group, based on their years of knowledge and experience, to come up with their best, most accurate estimate for the heating load of the house. Their responses ranged anywhere from 55,000 BTUH on the low end to 125,000 BTUH on the high end.
The class then worked through an I-B-R based heat-loss analysis using the H-22 Heat Loss Design Guide (find it on Amazon under “Freaking Awesome Heat Loss Book!”). Using charts, graphs and real live, honest-to-goodness math, the class calculated the heat loss of that house to be a whopping 31,000 BTUH.
Well ain’t that a kick in the head!
Bottom line gang: any fundamentally sound hydronics system starts with the math. Heat load allows us to size our boiler and all of our piping as accurately as possible, which can have a major impact on materials costs. And only when we know the heating load and the size and length of the pipe that heat has to go through can we figure out what we need for a circulator, because load determines flow and pipe size and length determine head loss.
And weather impacts it all.
From there we can look at all the different types of circulators (steep curve, flat curve, single-speed, 3-speed, variable speed, Delta-T, Delta-P) and try to determine which one best fits the job we’re looking at – and no, there’s NO SUCH THING as “the only circulator you’ll ever need.” That’s a load of hogwash.
So where does “Hydronics 101” start? It must start with an accurate idea of what you’re trying to accomplish, which is to make sure this structure heats on what’s commonly referred to as “the coldest day of the year.” Now, if you’re simply replacing a dead circulator, there’s precious little math that needs to be done (but you still have to know about circulators and their impact on systems – that’s a future segment). But if you’re replacing a boiler or actually starting from scratch, the only right way to start is with a pad of paper, a scaled ruler, a pencil and a calculator. If John and Eric invite me back, we’ll walk through simple heat loss calculations done the old fashioned way. Software will do it quicker, but in order for software to be a tool and not a convenience item, it’s important to know why it came up with the numbers that it did.
As my old man used to say, “Knowing how is good, but know why is better. Because those who know ‘how’ will always work for those who know ‘why.’”
John Barba is training manager for Taco Inc.
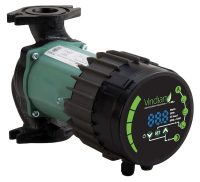
Taco’s now-expanded ECM, wet rotor Viridian line includes the VR3452 high efficiency wet rotor variable speed circulator for chilled and hot water applications, offering up to 34 feet of shut-off head and 52 gpm flow. All settings are accomplished with the user-friendly interface. The permanent magnet ECM motor saves up to 85% of the electrical Read more
Taco’s now-expanded ECM, wet rotor Viridian line includes the VR3452 high efficiency wet rotor variable speed circulator for chilled and hot water applications, offering up to 34 feet of shut-off head and 52 gpm flow. All settings are accomplished with the user-friendly interface. The permanent magnet ECM motor saves up to 85% of the electrical energy compared to conventional pumps.
The circulator offers auto mode (default), and proportional pressure control, constant pressure control, constant speed and night setback turndown. The LED displays watts, flow and RPM. It’s available in 115 or 230 volts and has standard flanges and is for easy installation.
The optional communication module provides: Ethernet and Modbus RTU communication, analog control input 0 – 10 V, three analog inputs/outputs, one relay output, main and standby operation. The VR3452 also comes with an industry standard flange.
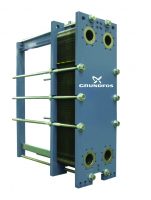
Grundfos provides a full range of gasketed and brazed plate heat exchangers designed for heating, ventilation, air-conditioning and cooling applications. Versatile and reliable gasketed plate heat exchangers feature wavelike corrugation for optimal fluid distribution, leading to the highest heat transfer rates at the lowest pressure drops. A compact and economic option, brazed heat exchangers are Read more
Grundfos provides a full range of gasketed and brazed plate heat exchangers designed for heating, ventilation, air-conditioning and cooling applications. Versatile and reliable gasketed plate heat exchangers feature wavelike corrugation for optimal fluid distribution, leading to the highest heat transfer rates at the lowest pressure drops. A compact and economic option, brazed heat exchangers are made of individually connected corrugated stainless steel plates for simple assembly.

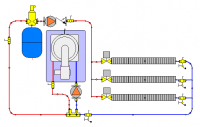
It’s a pretty common belief, at least in my neck of the woods, that condensing boilers and baseboard don’t “work well together” and the most cited reason is the need for high operating temperatures with baseboard. Of course they work, but how well? Awfully well in the vast majority of cases! Traditional boilers in the Read more
It’s a pretty common belief, at least in my neck of the woods, that condensing boilers and baseboard don’t “work well together” and the most cited reason is the need for high operating temperatures with baseboard. Of course they work, but how well? Awfully well in the vast majority of cases!
Traditional boilers in the USA are “non-condensing,” which means that they discharge flue gases at a high enough temperature that all water vapor is carried out of the flue. The water vapor is discharged with the other flue gases and never has a chance to condense to a liquid. The problem is that the hotter the flue gases, the more fuel is wasted and the less efficient the boiler.
So how does a condensing boiler work?
They absorb enough heat from the flue gases to drop the exhaust temperature below the point that the water vapor in the gases condenses into liquid and gives up its latent energy. Sounds great but the flue gas can only condense when the return water temperatures are 135F or less. The rated output of baseboard is realized at 180F.
How can this work at all, much less well? A few reasons!
First and foremost is the use of outdoor reset; can’t say I’m aware of any mod/con without integral ODR. Lowering the supply temperature by the use of ODR will of course yield lower return water temps, low enough to provide operation in the condensing mode for quite a bit of the heating season.
The second contributor to the viability of condensing technology with baseboard is the over-sizing of the baseboard itself; people have a pretty strong tendency to put in more baseboard than a heat loss calculation would indicate. While not as strong as the desire to over size boilers, the baseboard over sizing drive is definitely very dominant in the heating contractor genome. This, unlike boilers that are too big, is actually a good thing; more baseboard means the load can be met with lower water temperatures.
The third main factor is the design temperature; it really doesn’t get that cold all that often! That means the rest of the time, we don’t need to run 180F supply temperatures. Combine these and you will be running in the condensing range for the majority of the heating season, although certainly not all of it.
Dr T. Butcher of Brookhaven National Labs did a study on this topic in 2004 and found that 94% of the heating season time could be spent in condensing mode. It’s not light reading but if you are interested in an in-depth exploration of this topic, it’s available here: http://www0.bnl.gov/isd/documents/28709.pdf
There is another avenue of savings that mod/cons provide that is quite often overlooked: modulation. Modulation is varying the size of the fire in relation to the load. A cast iron boiler has two speeds — on and off. In comparison, a modulating boiler can vary its input, usually at a 4:1 or 5:1 ratio. A 100K Btu modulating boiler can operate from approx 20K Btu to 100K Btu. There is quite a bit of fuel to be saved by having the “right” size boiler on almost every day. I don’t know of any studies done to quantify the savings with modulation but based on anecdotal evidence over many years, I would place it in the 15% range.
A word of advice, don’t over size condensing boilers assuming the modulation will take care of it. I’ve seen 150K mod/cons in 50K heat loss homes and they never get off low fire except on DHW calls, not a recipe for efficiency. Properly applied mod/cons and baseboard can make for a long and happy marriage!
Robert C. O’Brien is the owner of Technical Heating Co. LLC in Mt. Sinai, NY. Robert serves as the Vice President of the national OESP chapter. See more from Robert in his blog “Boiler Sizing & Indirect Water Heaters”, “Converting from Oil to Natural Gas“ & “Heat Loss Calculation on Every Replacement?”

Boston Standard Plumbing & Heating Inc. — a Master Plumbing, Gas-fitting & Sheet Metal Corp. with the State of Massachusetts — was called to a Quincy residence with a boiler problem, during the beginning of a Northeast winter last year. The 100,000 BTU/hr, 2-bath home was in dire need of a heating/hot water system. The Read more
Boston Standard Plumbing & Heating Inc. — a Master Plumbing, Gas-fitting & Sheet Metal Corp. with the State of Massachusetts — was called to a Quincy residence with a boiler problem, during the beginning of a Northeast winter last year. The 100,000 BTU/hr, 2-bath home was in dire need of a heating/hot water system. The existing oil boiler was more than 40 years old, leaking at multiple points, and subsequently, the heating bills were “through the roof.” In addition, a tankless coil inside old boiler was plugged and water pressure was poor.

The solution? A Navien NCB-240 combi-boiler was installed to take care of the home’s heating and hot water needs. According to installing contractor, Joseph C. Wood, for this client, the “combi” was perfectly suited to their lifestyle, especially coming over from an old oil system. They were already used to “tankless” due to the old immersion coil in the old boiler and their home’s heating needs fit within the capabilities of the combi.
Also, while they have two standard full bathrooms, the home is occupied by an older couple who aren’t filling huge tubs or running hot water at multiple fixtures at the same time, so hot water wasn’t a concern even with our 38 degree incoming temperature water in Boston. Lastly, they didn’t want to take up the whole basement, so the new Navien NCB-240 fit right on the wall and could be closed in, if they desired, for a cleaner appearance.
“We chose to use a Navien product for a few reasons: First, we send all of our installers to the factory training course and as a result, we can easily get a customer up and running no matter the time of day or night. Second, we have a great track record with the Navien line. As a service and repair type of business, it all comes down to getting it fixed right the first time, and Navien provides us with “parts kits” that we keep in the shop or the on-call truck and that way we’re prepared even when our vendors are closed. Third, they’re the market leaders for this sort of stuff. Navien was the first to bring condensing tankless to the market and we want to stay aligned with companies that lead the way, the same way we’re trying to do. Boston Standard likes to use products that put us out there as a market leader,” said Wood.
In addition, Wood was presented with some unique challenges. “We needed to run a new gas line from the street and get it done before they closed the street down for dig work. We squeezed it in right before the season ended. Also, the piping system was done wrong and needed alteration,” said Wood.
According to Wood, the customer was using $500 of oil every 2-3 weeks in the years prior. In the end, “The customer has been thrilled with the new system for both energy savings — 30-35% (reported by customer) — and operation. He loves the hot water, especially,” says Wood.

Name of Project: Navien NCB-240 “combi” project
Location (City, State): Quincy, MA
Date started: 11/17/2014
Date Finished: 11/21/2014
Workers onsite: 2