By John Mesenbrink Recently, Ron Passafaro, president & CEO of ECR International, was re-elected as Chairman of the Hydronics Institute through 2017. Passafaro, who has been a member of the Hydronics Institute his entire career and has served on its Executive Board since 2007, said, “I am honored and humbled to be re-elected by my Read more
Heating & Cooling
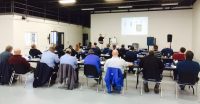
By John Mesenbrink
Recently, Ron Passafaro, president & CEO of ECR International, was re-elected as Chairman of the Hydronics Institute through 2017.
Passafaro, who has been a member of the Hydronics Institute his entire career and has served on its Executive Board since 2007, said, “I am honored and humbled to be re-elected by my competitors and industry peers. Our industry continues to face increasing Federal and State regulation governing residential and commercial boiler efficiency standards. I am committed to working with both our government representatives and member companies to meet and exceed the North American market’s expectations.”
In the wake of this news, Mechanical Hub recently talked with Passafaro about ECR and the industry. The following is Ron Passafaro in his own words.
How did you get involved in the industry?
During the 1980s I was working for Abbott Laboratories selling medical equipment in New England when I received a phone call from John Reed of Dunkirk Radiator. John and I grew up together in the Dunkirk area and he told me that Dunkirk Radiator wanted to establish its own brand and start a national distribution channel to supplement their historical OEM business I had lived in Boston for five years and had no vision of ever moving back home to western New York but I took the time to meet with the Dunkirk management team and we talked about their objectives. After learning what they wanted to accomplish I found it very exciting and challenging to have the opportunity to create a national brand and distribution channel at age 29. I jumped at the opportunity and had a ball doing it. Clearly it turned out to be the best decision of my professional career.
What are some things you’ve learned throughout your career that have helped you in your current position?
I learned a long time ago about Servant Leadership and it is a philosophy that I very much believe in and try to live — not always successfully. Servant leadership is best explained graphically by turning the conventional corporate hierarchical triangle upside down. The most important persons in priority within a company is the customer and then those that interact and serve the customer directly (sales, tech support etc.) and then those that support the people that interact with the customer and so on. The CEO realizes that he or she is simply there to serve all the others and does so by ensuring they have the resources and support necessary.
Care — You won’t always be right and you won’t always get it right but if you care you’ll try hard enough to fix the times you miss.
Be Genuine — Don’t be who you think they want you to be because you’ll never be any good at it. No matter our position in life we are only good at being ourselves besides employees and customers can sniff out a phony in a heartbeat and you can’t ever recover from that. People forgive mistakes they don’t forgive deceit.
How has ECR navigated through the tough economy?
The tough economy has required us to get back to basics. We truly need to understand what the customer wants and what they are willing to pay for and that means asking good questions and listening. There isn’t time or resource to miss the mark on what the customer is willing to buy. In order for us to capitalize we need to develop solution based products that meet needs of today and the near future.
The market is changing so much faster than when I first started in the industry nearly 30 years ago. That is why roughly 1/3 of our salary workforce is dedicated to engineering and product development. Over the past four years we have been averaging three to four new or heavily modified product introductions per year. That’s pretty astounding when you think about it but that is what’s required by this demanding market. With that type of development activity we need to hold costs down and have done so by investing in our manufacturing operations to improve process control which increases throughput while increasing quality and reducing costs all at the same time.
How does business in the near term look?
We’re fairly bullish on the market over the near term and feel like the boiler market will continue to grow. I was traveling in New England during February calling on contractors this year and the common response to my question, “how’s business?” was if they could even get to the basements through the snow they had to repair versus replace because they couldn’t leave the homes without heat for that long. We have had two very cold, long winters in a row which has driven a lot of repair work that normally would have been replacement so I think the patch work is likely to give way to replacement in the near term.
Any new products or news in the offing?
Absolutely. We will be keeping with our recent trend of new product introduction and over the course of the next 12 months you’ll see us introduce a new product in each of our technology categories.
On the boiler side we’ll be introducing our first light commercial condensing models featuring our unique stainless steel heat exchanger design. Our Argo control platform will add the “Universal” switching relay that will feature a host of new features and technology in that segment.
The Olsen and Airco furnace platforms added a high efficiency, multi-positional low profile oil furnace this month that I suspect will redefine that segment.
And last we have just added our new 4-pipe chilled water recessed cassette air handler to our Comfortwave chilled water air handler line.
Describe the importance of contractor training.
I believe condensing furnaces were first introduced back in the late 1980s and over the past 30 years or so they have become a significant portion of the annual installed furnace base. Boiler installers didn’t have 30+ years to digest and get familiar with condensing technology. Though ECR was the first to offer a 95% AFUE boiler back in 1996 the rise of condensing boilers really has taken place over the last 10 years or so. Between technology and regulatory changes the entire residential boiler market has changed over the past several years. I have a tremendous amount of empathy for boiler installers today trying to keep up with that pace of change. The only way to keep up is through education so contractor training is hugely important to the dealer and the manufacturer. The contractor needs to understand the nuances of new equipment and technologies but more importantly how these new products are applied and what unforeseen challenges might result.
Our preferred method of training is to have contractors visit our corporate training center. This is our best venue for training hands on and they also see our research laboratory and manufacturing operations. Unfortunately, coming to Utica, N.Y., is not always possible so we have invested in additional live fire training centers at our newly opened offices in Hopkinton, Mass. and at in Dunkirk, N.Y. We believe in providing resources at the point of use so we invested in these additional facilities to spread our geographic coverage. Likewise, we continue to offer training in conjunction with our distributor partners at various locations around the country.
New for 2015, we introduced the Hydronic Boot Camp, which is a whole system approach to training our professional trade partners. We cover our condensing boiler products and technology but spend as much time covering system application and how to overcome commonly seen field installation issues. We bring together other component manufacturers like Taco, Centrotherm, Grundfos, Caleffi, Sentinel and others so that system component providers that installers use are in the same room training in a holistic, system approach. Ideally, students attend training at one of our 3-live fire facilities where they will learn while operating products. When contractors can’t come to training our locations we do offer many seminars around the country. If dealers go to www.hydronicbootcamp.com they can choose from the many dates and places for training by brand.
Boilers are now transforming themselves into intelligent, communicative integrated systems. In this era of the Internet of Things, how have ECR boilers and controls evolved?
So far most communicative controls have been focused on temperature monitoring and adjustment which has some sizzle for the end user but the actual value and utility to the trade is questionable.
Our Argo AR500 line has offered remote temperature monitoring with adjustment capability since the 1990s, mostly for snowbirds, so that functionality isn’t all that new. We have already proven out and deployed remote operation monitoring in one of our joint ventures the question is how to take that technology and know-how and adapt it in the boiler world where we typically do not develop the operating board.
More likely we will see boiler control intelligence sooner in the area of self-commissioning and adjustment within the modulating condensing segment. European control manufacturers are quickly developing these capabilities in an integrated structure that amalgamates all electronic and control functionality. This type technology begins to create a greater amount of value for the installer which is the customer group we are primarily focused on.
Finally, the last time you said, “Today is a great day,” you were doing what?
I’ve been very lucky and have been able to say that many times, but likely it would be just after sun up on an Adirondack lake ready to make my first cast or then again it might be on the first tee. Like I say, I’ve been lucky.
ECR International — In 1928 Earle C. Reed founded two separately owned and operated New York State companies, Utica Boiler and Dunkirk Radiator, the companies merged in 1999 and took our common founder’s initials as its corporate name — ECR International.
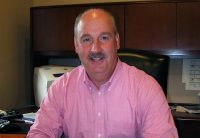
Utica, N.Y. — ECR International, Inc. announced that president & CEO, Ron Passafaro, has been re-elected as Chairman of the Hydronics Institute through 2017. Re-election to the Chairmanship in consecutive terms is rare and likely due to the three significant issues which began during Passafaro’s first term: US DOE 2020 Minimum Efficiency regulations, US DOE Read more
Utica, N.Y. — ECR International, Inc. announced that president & CEO, Ron Passafaro, has been re-elected as Chairman of the Hydronics Institute through 2017.
Re-election to the Chairmanship in consecutive terms is rare and likely due to the three significant issues which began during Passafaro’s first term: US DOE 2020 Minimum Efficiency regulations, US DOE Testing Procedures and Protocols and EPA ENERGY STAR Efficiency Tiers. Ron’s management of these complex challenges facing the industry thus far has moved the Institute’s members to call upon him to finish this important work during a second term.
Passafaro has been a member of the Hydronics Institute his entire career and has served on its Executive Board since 2007. The Institute is comprised of 69 domestic and international manufacturers of boilers and related components. The Hydronics Institute develops standards, conducts certification testing and works with Federal agencies, specifically the US Department of Energy, in regard to regulations governing efficiency and safety standards for the North American boiler industry.
Passafaro, who looks forward to his new term, said, “I am honored and humbled to be re-elected by my competitors and industry peers. Our industry continues to face increasing Federal and State regulation governing residential and commercial boiler efficiency standards. I am committed to working with both our government representatives and member companies to meet and exceed the North American market’s expectations.”
The Hydronics Institute has been representing the North American boiler industry since 1915 and is celebrating its Centennial this September in Absecon, NJ. It is a sub-section of the Air Conditioning, Heating and Refrigeration Institute (AHRI) which represents 314 member companies with over 1 million US workers dedicated to excellence in product manufacturing to meet the heating, cooling and refrigeration needs of the world.
Passafaro also has served on the AHRI board of directors since 2011.

Neutrasafe Corp. has added new products to their line of high-quality condensate neutralizers to fit almost any hi-efficiency, gas fired application. Improvements have also been made to all tube-type and tank-type neutralizers, enhancing ease of maintenance and/or performance. Tube-type condensate neutralizers are now offered in four sizes from 220,000 to 2 million BTUH. Addition of Read more
Neutrasafe Corp. has added new products to their line of high-quality condensate neutralizers to fit almost any hi-efficiency, gas fired application. Improvements have also been made to all tube-type and tank-type neutralizers, enhancing ease of maintenance and/or performance.
Tube-type condensate neutralizers are now offered in four sizes from 220,000 to 2 million BTUH. Addition of the largest size now fills the gap between the company’s 1.2 million BTUH tube-type unit and the smallest tank-type neutralizer. Tank configurations are available with capacity guidelines of 4 million and 6 million BTUH.
The new patent pending tube-type neutralizers feature integral unions with O-ring seals that greatly simplify removal for service and recharging. Unclasping a lock ring on either end of the unit allows the main body to be removed without disturbing the drain line. Replacement O-rings are included with tube model recharge kits and all tube model neutralizers are available with a snap-in mounting clamp option. The new model was designed by a Master Plumber with more than 30 years in the industry and is completely manufactured in the US.
Along with Neutra-Safe’s upgraded and expanded product line, the neutralization media for all units has been improved. A mix of calcite and magnesium oxide pellets is now used for enhanced performance and is also available in recharge kits for any of Neutra-Safe’s condensate neutralizers.
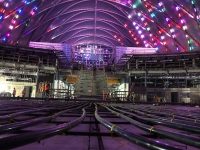
Centrally located in Orange County, California, the Anaheim Regional Transportation Intermodal Center (ARTIC) provides transportation service for three million local residents as well as 40 million annual visitors. A LEED Platinum-certified building, the structure is 67,000 square feet with three levels. ARTIC’s unique architecture includes a large number of windows and a dome-shaped structure, which Read more

Centrally located in Orange County, California, the Anaheim Regional Transportation Intermodal Center (ARTIC) provides transportation service for three million local residents as well as 40 million annual visitors. A LEED Platinum-certified building, the structure is 67,000 square feet with three levels.

ARTIC’s unique architecture includes a large number of windows and a dome-shaped structure, which results in high solar gains. Due to ARTIC’s size, controlling the climate inside the building with a conventional forced-air system would have been nearly impossible.

Instead, HVAC designers for the project chose to implement a radiant heating and cooling system. Radiant cooling allows instantaneous removal of heat through absorption. Installing ViegaPEX™ Barrier tubing at tightly spaced increments (6 inches on-center) allows it to be within two inches of the finished surface floor, which gave the engineer the ability to immediately remove the solar sensible gain. For the ARTIC project, the cooling capacity ranges up to 40 btuh/sq. ft. This provides an energy savings of 34 percent over ASHRAE 90.1-2007.

“We installed 44,000 feet of in-slab heating and cooling pipe, 18 manifolds and 12 pumps,” said Paul Redgate, Pipe Fitting Superintendent for California Comfort Systems. “We’ve done some smaller stuff but nothing on this scale.”

REHAU was awarded with the Plastics Pipe Institute (PPI) Building & Construction Division’s Project of the Year earlier this month at the organization’s annual meeting. The award recognizes the company’s role in the École Secondaire Jeunes sans Frontiers (Secondary School for Youth Without Frontiers) project in Brampton, Ontario. The school, which has earned the Read more

JSF High School features a REHAU radiant slab heating and cooling system installed throughout the building. Photo © Patrick Kennedy.
REHAU was awarded with the Plastics Pipe Institute (PPI) Building & Construction Division’s Project of the Year earlier this month at the organization’s annual meeting. The award recognizes the company’s role in the École Secondaire Jeunes sans Frontiers (Secondary School for Youth Without Frontiers) project in Brampton, Ontario. The school, which has earned the Canadian Green Building Council’s LEED® Silver certification, is the first secondary school building in Ontario to have achieved this status.
Designed by Robertson Simmons Architects, the French language high school, which encompasses approximately 91,000 sq. ft., is dedicated to fostering an enriched, student-focused learning experience by providing a healthy and sustainably designed environment. To achieve this, the design includes indoor spaces integrated with outdoor landscapes, a green roof, expansive daylighting, water-conserving plumbing fixtures, lighting with occupancy sensors and displacement ventilation.

The system consists of 104,700 ft (32,000 m) of RAUPEX® 5/8-in. O2 Barrier pipe and 42 PRO-BALANCE® manifolds. Photo courtesy Klimatrol.
To achieve maximum HVAC efficiency, the design includes a REHAU radiant slab heating and cooling system, which circulates a heated or chilled water-glycol solution through a network of PEX piping installed in the floors throughout the entire facility. The radiant system enables the school to meet indoor environmental criteria related to air quality, noise reduction and occupant comfort while also maximizing space efficiency by eliminating bulky convectors and ductwork.
“To help the school recognize the benefits of a combined radiant heating and cooling system, we supplied a finite element analysis to model the floor heating and cooling output,” explained Mark Euteneier, president of Klimatrol Environmental Systems, the project’s designer and supplier. “The results predicted a significant energy savings due to reduced heating and cooling loads and increased efficiencies of the heated and chilled water sources,” he said. “Coupled with the comfortable, even method of heating and cooling, this analysis made the REHAU radiant system a must-have for the project.”
The system consists of 104,700 ft (32,000 m) of RAUPEX® 5/8-in. O2 Barrier pipe and 42 PRO-BALANCE® manifolds pre-piped with 3-way valves into recessed manifold distribution cabinets. The PEX pipe was installed at the ground level in a concrete slab-on-grade design using a counter-flow spiral pattern to promote even surface temperatures.
To accommodate precast concrete floors on the second level, the pipe was affixed using plastic rails of recycled PVC and covered with a 2 to 3 in (5 to 8 cm) concrete layer.
REHAU has been previously recognized with PPI Building & Construction Division Project of the Year awards for the Denver Zoo Asian Tropics Complex as well as for the Vail, Colorado town center project, Solaris.
Plastics Pipe Institute Inc. (PPI) is a non-profit trade association dedicated to the advocacy and advancement of use of plastics in pipe infrastructure systems because they are smart, economical and sustainable solutions. The association is comprised of approximately 300 members and associates. The mission of PPI is to promote plastics as the material of choice for piping applications.
For additional information, visit www.na.rehau.com/mp