Wichita, Kan. — Viega announces vertical integration of its PEX tubing manufacturing process. The company’s resource consolidation includes producing resin and extruding PEX tubing, which makes Viega the only manufacturer to quality control PEX tubing from the raw-material stage through the finished product. ViegaPEX Ultra tubing, which offers the highest industry ratings for UV exposure Read more
Hydronics
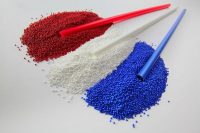
Wichita, Kan. — Viega announces vertical integration of its PEX tubing manufacturing process. The company’s resource consolidation includes producing resin and extruding PEX tubing, which makes Viega the only manufacturer to quality control PEX tubing from the raw-material stage through the finished product.
ViegaPEX Ultra tubing, which offers the highest industry ratings for UV exposure and chlorine resistance, is extruded from Viega’s own resin. This step creates higher quality product that will provide excellent performance and offers increased flexibility compared to tubing made from third-party resins. ViegaPEX Ultra tubing can withstand up to six months of exposure to sunlight without damaging its performance.
The increased flexibility of Viega’s PEX tubing helps installers reduce labor costs and minimize materials costs by needing fewer fittings. This also decreases the potential for leak points in a plumbing system.
“Beyond offering higher UV exposure ratings and cost savings to our customers, making PEX from our own resin increases Viega’s freedom to research product quality,” said Paige Riddle, product manager, Viega. “By controlling the quality of PEX tubing from start to finish, Viega has taken another step in keeping our quality the highest and providing innovative opportunities for our partners.”
Viega has a heritage of manufacturing excellent high-performance products and innovative concepts such as its PEX solutions which include ViegaPEX Ultra tubing, Viega ManaBloc and Viega PEX Press fittings.
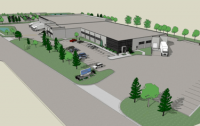
Uponor North America (Uponor) is expanding its manufacturing facility in Apple Valley, Minn. beginning late spring 2015, with completion expected by Dec. 1, 2015. The $18 million investment will be used toward the renovation and expansion of an additional 88,000 square feet to accommodate lean manufacturing and office space, as well as additional manufacturing equipment Read more

The new facility will add an additional 88,000 square feet of manufacturing and office space to support Uponor’s PEX piping business.
Uponor North America (Uponor) is expanding its manufacturing facility in Apple Valley, Minn. beginning late spring 2015, with completion expected by Dec. 1, 2015. The $18 million investment will be used toward the renovation and expansion of an additional 88,000 square feet to accommodate lean manufacturing and office space, as well as additional manufacturing equipment that is required.
Uponor’s North American headquarters are also located in Apple Valley, and the company has a distribution center and resin-processing center located in nearby Lakeville, Minn. By year-end, the total Twin Cities metro area footprint will amount to 654,738 square feet on approximately 50 acres of total property.
The building expansion, in which the company will pursue LEED® certification, is required to meet forecasted growth for its crosslinked polyethylene (PEX) tubing in plumbing, fire sprinkler, radiant heating and cooling and hydronic piping systems used in residential and commercial building.

The new facility, which is located adjacent to the Uponor North America headquarters, consists of a 34,000-square-foot remodel to an existing structure along with a 54,000-square-foot addition.
“It’s a very exciting time in the building industry, especially after the downturn we experienced in the market just a few years ago,” says Bill Gray, Uponor North America president. “We’re seeing significant growth in commercial and residential construction, and this expansion will ensure we match forecasted growth and demand for our PEX systems.”
Uponor CEO and President Jyri Luomakoski adds, “Our North American region has consistently boosted profits and seized market share, both in the residential commercial segments. The team’s success is driven by always doing what’s best for our customers, looking for better ways to perform, innovation, hard work and diligent execution.”
Uponor’s decision to expand again in Apple Valley was partly due to the cooperation of the State of Minnesota and the City of Apple Valley in joining together in providing an attractive incentive package. Uponor has applied for financial support from the City of Apple Valley as well as state assistance from the Minnesota Department of Employment and Economic Development’s Minnesota Job Creation Fund and the Minnesota Investment Fund to assist the expansion.
“Uponor has been an outstanding job creator since opening its North American headquarters in Apple Valley in 1990,” says DEED Commissioner Katie Clark Sieben. “With such a large global presence, we are grateful for the company’s decision to make further investments in Minnesota.”
Apple Valley Mayor Mary Hamann-Roland adds, “I’m honored that Uponor has made a deliberate decision to expand again in Apple Valley. Uponor is a global, innovative partner with their compass focused on a bright future and our shared values for healthy people, planet and a profitable economy.”
Uponor’s physical space is not the only thing that is expanding. They have created more than 130 new jobs in the Twin Cities over the past three years and anticipate adding a significant number of jobs as a result of the manufacturing expansion — contributing toward the economic development in the metro area. Uponor Group employs 4,000 employees worldwide, with about 500 employees located in the Twin Cities.
This year marks Uponor’s 25-year anniversary in Apple Valley. Uponor chose to continue to invest in the Twin Cities because of its location, access to a wealth of talent and the continued support from both the City of Apple Valley and the State of Minnesota.
Gray adds that he is grateful for the City of Apple Valley, the State of Minnesota, the Uponor Board of Directors and Uponor CEO Jyri Luomakoski for their confidence in Uponor North America. “Our success is a result of connecting and building solid relationships with all our partners: the city, the state, our employees, manufacturer representatives, wholesale distributors, builders, architects, contractors and plumbing professionals.”
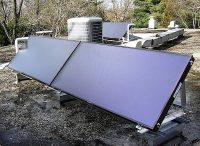
Located in Bethesda, Md., the Seymour Krieger House is listed on the National Register of Historic Places, and was designed in the 1950s by internationally renowned modernist architect Marcel Breuer. The house currently is owned by an architect, and he wanted to restore the mechanical system while keeping the architectural integrity of the structure intact Read more
Located in Bethesda, Md., the Seymour Krieger House is listed on the National Register of Historic Places, and was designed in the 1950s by internationally renowned modernist architect Marcel Breuer.

A very tight mechanical room displaying a Triangle Tube Prestige boiler, Grundfos ALPHA pump, Caleffi hydro-separator and REHAU radiant tubing and manifold.
The house currently is owned by an architect, and he wanted to restore the mechanical system while keeping the architectural integrity of the structure intact. Originally heated by a radiant floor heating system, the original boiler was still in place and operational, but the wrought iron radiant piping has corroded and was leaking in multiple locations.
“We discussed multiple alternatives,” says Dan Foley, Foley Mechanical, Inc. “But in the end, the owner decided to go back with radiant floor heat.
The bluestone floor tiles were painstakingly numbered and removed. The concrete overpour, along with the original wrought iron radiant tubing, was removed.
New REHAU PEX radiant tubing system was installed, and a new concrete slab was poured. The flagstones were carefully placed back in exactly their original positions.
The entire mechanical system was updated by installing a new Triangle Tube Prestige boiler, HTP DHW tank, Viessmann solar heat and DHW system, Grundfos ALPHA pump, Caleffi hydro-separator, REHAU radiant tubing and manifold, and new Carrier high-efficiency AC system.

Four Viessmann flat panel solar collectors were mounted on the flat roof along with a Carrier 17 SEER AC unit.
To allow for multiple zones, Foley and his team re-piped and re-controlled the radiant system. The Viessmann solar system will contribute to space heat when the DHW load is satisfied.
“The clients were a joy to work for and appreciated the hard work done by my crew on this difficult and challenging project,” says Foley.
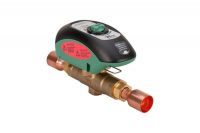
Taco’s newest Zone Sentry Zone Valve – with an inverted flare – is ideally suited to retrofit and new construction work. The zone valves improve the overall performance of any hydronic system that uses a zone valve. Uniquely, Taco’s zone valve line uses microcircuit-based logic to control a gear-driven electronic actuator that drives a ball Read more
Taco’s newest Zone Sentry Zone Valve – with an inverted flare – is ideally suited to retrofit and new construction work. The zone valves improve the overall performance of any hydronic system that uses a zone valve. Uniquely, Taco’s zone valve line uses microcircuit-based logic to control a gear-driven electronic actuator that drives a ball valve-based body design.

Taco’s Zone Sentry valve is available with either a normally open or normally closed actuator. The valve can be installed in any direction, in any orientation. Snap-in quick connects on the back of the valve make for a simple, secure wiring hook-up. A green LED shows full functionality of valve operation.
Ideal for use with a wide variety of heating and cooling applications, Zone Sentry valves were designed primarily for baseboard, fan coil, radiator, convector, heat pump and radiant applications. The valves are now available in ½”, ¾”, 1”sweat or NPT and inverted flare (less fittings) and inverted flare (with ¾” sweat fittings) and draw only 1.44 watts.
The Zone Sentry is easy to install and operate, and the one-handed liftoff actuator means that tight space is no longer a concern.
The addition of this connection to the Zone Sentry line allows contractors to replace an existing inverted flare valve with the Zone Sentry without having to cut and sweat pipe, greatly reducing retrofit time. For new installations, it allows the installer to use the type of product he prefers, with improved performance.
Wichita, Kan. — Viega announces its partnership with the Center for the Built Environment (CBE) at University of California, Berkeley. The association will enable CBE and Viega to work together in educating the industry on new and more efficient technologies for commercial integrated hydronics systems. CBE is a place where industry leaders and internationally recognized Read more
Wichita, Kan. — Viega announces its partnership with the Center for the Built Environment (CBE) at University of California, Berkeley. The association will enable CBE and Viega to work together in educating the industry on new and more efficient technologies for commercial integrated hydronics systems.
CBE is a place where industry leaders and internationally recognized researchers cooperate to produce substantial, holistic and far-sighted research on buildings.
Fred Bauman, P.E., a prominent scientist at CBE, is leading a research program on advanced integrated systems with a focus on radiant slab cooling, also known as thermally activated building systems (TABS). CBE recently accepted a $3 million grant over the next three years on radiant slab systems to research methods for optimizing radiant systems for energy efficiency and comfort. Research provides more performance data that allows for guidelines for design and controls.
Viega and CBE are collaborating to develop training sessions and use the research for innovative product advancements and design guidelines.
“We are honored to be associated with CBE,” said Mark Parent, director of product management, Viega. “There is a lack of industry knowledge when it comes to radiant heating and cooling. Our hope is to help educate the industry on newer and more efficient technologies when designing commercial integrated hydronics systems.”
Viega provides versatile radiant heating and cooling systems in the industry. Suitable for residential, commercial or industrial applications, Viega ProRadiant™ heating and cooling solutions include ViegaPEX™ Barrier tubing, Viega FostaPEX® tubing, Viega PEX Press fittings, manifolds, controls, mixing stations, sensors, mats, panels, tracks and plates.
CBE’s mission is to improve the environmental quality and energy efficiency of buildings by providing timely, unbiased information on building technologies, design and operation techniques.