Skimming a steam boiler is the process of removing any oil from the water volume. If not completed properly, the presence of oil can cause the boiler to surge, as the water’s ability to flash to steam is affected. While US Boiler doesn’t use oil in the production of sections, oil can come from the Read more
Industry Blogs
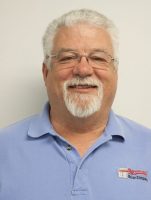
Skimming a steam boiler is the process of removing any oil from the water volume. If not completed properly, the presence of oil can cause the boiler to surge, as the water’s ability to flash to steam is affected.
While US Boiler doesn’t use oil in the production of sections, oil can come from the inside of black pipe and also from the threading process.
In my past life, we installed many steam boilers, following the installation instructions to a “T”. When we started doing it by the book, it was a tough transition from our old ways to re-educate ourselves. For years, we never did proper near boiler piping, even though we thought we were. We just did it our way because that’s the way the company had always done it.
Our way worked OK and was easier. Usually after a few trips to the surging steam boiler and re-piping, adding chemicals, trying check valves or just skimming, we were able to resolved most of the problems.
Of course, all these additional trips were not included in the installation price, so it became a financial loss for us. I realized most surging problems can be resolved just by skimming properly.
I finally looked into the skimming procedures. After asking a lot of old-timers, I found that there were many ways to skim a steam boiler. Some seemed to work better than others.
As we gathered the information, there were many similarities between the techniques that the older techs were using. And of course there some differences. We decided to combine all the similar steps and added a few others we had heard.
With some trial and error we found that on most jobs we only had to skim one time and usually only for about an hour or so. We also realized we didn’t need to use chemical additives. Prior to this we always used chemicals after skimming.
If you don’t do much steam work you may ask what surging is? This is when the water level in the gage glass is bouncing excessively. The bounce should not be more than about 1/2″- 1″ When surging, the water bounce will normally be most of the sight glass and the water can even completely disappear. The water may just keep dropping and disappear without much bounce. Remember this, the action inside the boiler is worse than what you are seeing in the gage glass.
Here’s the proper skimming procedure we used:
1. Turn the boiler on and run it until it gets hot starts making steam.
2. Turn the boiler off. DO NOT TURN THE BOILER BACK ON DURING SKIMMING PROCESS. This is important. If you fire the boiler again, it’ll cause turbulence within the water volume, drawing oiler away from the surface.
3. Only after lifting the relief valve to verify there is no steam pressure in the boiler, find the skim tapping or a plug you can safely remove above the water level. If the relief valve is on the side of the boiler you could even use that taping. Not taping can be used on top of the boiler, only on the sides. The tapping must be at least 3/4″.
4. Install a nipple with a valve into the boiler taping. The valve is a “just-in-case” valve. You won’t close this after the skimming process starts. This pipe nipple must be horizontal, and must come straight out. It cannot elbow up. We are trying to skim the water surface, so the water must come out of a horizontal pipe. There shouldn’t be water at this level yet.
5. Open the valve you installed and hang a bucket on the pipe.
6. Find the manual fill valve. If there is no manual valve you can add the water into the boiler from a low drain valve.
7. Open the manual fill valve until the water starts to flow out of the pipe nipple and valve you just installed. When water starts to flow out the pipe nipple, close the fill valve and wait until the flow stops.
8. Reopen the manual fill valve slightly so the stream of water coming from the pipe nipple is no larger than a wooden pencil. A little faster for commercial boilers. The slower the better.
9. Continue to skim until the bucket is almost full and remove the full bucket and use the second bucket while you dump the first bucket. Do not shut off the valve while doing this. You cannot not stop the water flow once started. Remember – Do not re-fire the boiler.
10. Keep skimming until the water temp falls low enough that you can comfortably keep your hand under the skimmed water flow. I know jobs that were skimmed 2 – 3 hours depending on boiler water volume. Many times this is about an hour on residential boilers.
11. When done, close manual water feed, remove pipe nipple and valve, reinstall plug or relief valve, drain water to proper fill level.
12. Turn the boiler switch on. Let the boiler create steam. Did the surging stop or at least improve? Duplicate if needed but normally once is enough. If after two tries there’s no improvement, the problem is not oil. Check near boiler piping, flame impingement, and water pH. Water pH issues can be caused by chemicals added to the boiler.
Ron Beck is the outside Technical Advisor and manager of Training for U.S. Boiler Company, where he’s been since 1998. Ron’s 38 years of experience in the heating industry include climbing the ranks of a HVAC company, from apprentice to service manager.
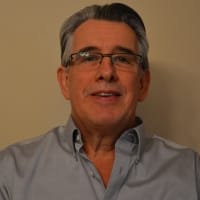
During the past decade, the number of condensing boilers, furnaces and water heaters being installed has continued to rise every year. All indications are that this trend will continue and in some cases is already mandated by federal authorities. Provisions for dealing with the corrosive condensate from these appliances are covered by the Plumbing Codes Read more
During the past decade, the number of condensing boilers, furnaces and water heaters being installed has continued to rise every year. All indications are that this trend will continue and in some cases is already mandated by federal authorities. Provisions for dealing with the corrosive condensate from these appliances are covered by the Plumbing Codes on the national, state and local levels. Because of the long term effects of the sustained introduction of this corrosive condensate into drains and sewer lines, there is a growing awareness of the need to educate code enforcement officials, contractors and homeowners of the need and the means to neutralize this corrosive outflow.
Multiply by 10
When condensing appliances first appeared in the US, some manufacturers stated that the condensate had a pH of between 3.8 and 4.2 which is lower than the generally accepted range of between 5 and 10 or sometimes 12, for the disposal of aqueous solutions into drainage, sewer and septic systems. Any aqueous solution with a pH below 5 is considered corrosive. We have found some condensate to have a pH as low as 2 which means that it is 1000 times more acidic than the minimum of 5, which allows disposal without treatment. How can this be? The pH scale goes from 0-14 with 7 being neutral. Anything below 7 is considered acidic. The pH scale is logarithmic, meaning that each jump of one is a tenfold increase or decrease in acidity. Many of us have seen the damage that this condensate can cause and realize why it must be treated.
How to Treat Condensate
There are basically two ways to treat this condensate; neutralization or dilution.
• Dilution is accomplished by mixing the condensate with pure water to raise the pH. An example would be 1 gallon of condensate at a pH of 3 would need to mix with 10 gallons of pure water to bring it to a pH of 4. Then you would have 11 gallons with a pH of 4 and it would take 110 more gallons of pure water to bring the pH up to 5 to meet the disposal requirement. Now you have used 120 gallons of pure water to dilute one gallon of condensate with a pH of 4. If the original gallon of condensate had a pH of 2 you would have needed an additional 1210 gallons or a total of 1330 gallons to dilute one gallon of condensate! As you can see, this is not a very environmentally sound way of doing it and in some, if not most areas, there are clean water regulations that would make this process illegal. This brings us to the alternative – neutralization.
• Neutralization is accomplished by running the condensate through a container of some kind which is filled with media to raise the pH to an acceptable level. At first, most thought that regular limestone or marble rock or chips could be used to do this. Many got their own
containers or drum traps and went to the big box home store and bought a bag of landscape marble or limestone chips. Although these chips contain one of the compounds used for neutralization – calcium carbonate – the material itself is so hard that it does not dissolve and the surface of the rock becomes coated with salts and loses its effectiveness. Performance is also adversely impacted by rock size; a collection of large rocks will have less surface area than an equal quantity of smaller rocks.
The Correct Mix is Important
Calcium carbonate is found in all marble, limestone and even sea shells. Calcium carbonate is regarded as being self-regulating which means that it cannot over correct and cause an alkaline condition. Calcite, a very common and widespread mineral form of calcium carbonate is best recognized by its relatively low Mohs hardness (3) and its high reactivity with even weak acids, such as vinegar. The low Mohs hardness allows it to dissolve as it reacts with the acidic solution thus reducing the likelihood of coating the surface as with the harder marble chips. Magnesium oxide and magnesium hydroxide are also used to raise pH in an aqueous solution. Magnesium hydroxide is basically magnesium oxide that has not had all of the water removed. Magnesium oxide and magnesium hydroxide are not self-regulating and care must be taken not to cause an alkaline condition. The magnesium products are quicker acting than the calcium carbonate and help to increase the performance. In a proper mix these two materials do an excellent job in neutralizing acidic aqueous solutions. Calcite, magnesium oxide and magnesium hydroxide are all used in the treatment of potable (drinking) water and are environmentally friendly.
In Conclusion
We know that condensate from condensing appliances is acidic and corrosive to many materials and should be treated to bring the pH up to at least 5 before disposal. We know that dilution is not an environmentally acceptable method of treating this corrosive aqueous solution. We know that calcite, magnesium oxide and magnesium hydroxide are good sources of media to treat condensate. We also know that there can be a wide variation of the pH of condensate from condensing appliances due to the chemical make-up of the gas being combusted or from the way in which the appliance is operating in a particular application. And let’s not forget that a fully condensing appliance will produce up to 1 gallon of condensate per hour for every 100,000 BTUH input.
Neutralizer manufacturers provide sizing guidelines but because of the varying range of condensate pH, it is necessary for the contractor to verify that the particular unit he has installed will work on that application. Remember that the media is reacting with the solution to raise the pH and does need to be replaced. Most manufacturers recommend replacing media and checking operation at least annually. This can be done along with the annual servicing of the appliance as recommended by appliance manufacturers.
Mike Bernasconi is VP and co-owner of Neutrasafe Corporation, a Massachusetts based manufacturer of condensate neutralizers. Bernasconi, a licensed Master Plumber and hydronics specialist, has been working in the HVAC industry for 35+ years and is well known in the industry for hydronics design and execution. With the onset of condensing boilers, furnaces and hot water heaters, the installation of a condensate neutralizer is now a mandatory requirement. Bernasconi designed a condensate neutralizer with the installer in mind. His product contains a clear body, clean, consistent sized high quality media and offers ease of servicing. Neutrasafe Corporation partners with manufacturer representatives throughout the U.S. to distribute its products. Products can be viewed at www.neutrasafe.com. He can be reached at mike@neutrasafe.com
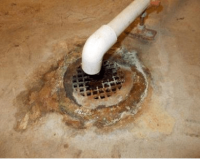
Most new residential and commercial heating and hot water systems include a furnace, boiler or domestic water heater of the high efficiency condensing type. Condensing appliances extract additional BTUs from the water vapor in the flue gas. When the flue gas drops below its dew point of approximately 135 degrees Fahrenheit, it starts to condense Read more
Most new residential and commercial heating and hot water systems include a furnace, boiler or domestic water heater of the high efficiency condensing type. Condensing appliances extract additional BTUs from the water vapor in the flue gas. When the flue gas drops below its dew point of approximately 135 degrees Fahrenheit, it starts to condense and the resulting liquid is acidic and requires treatment to avoid damage to piping systems, sewerage systems, treatment facilities, septic systems and other items it may come in contact with.
A general rule of thumb, one gallon of condensate is produced for every 100,000 BTUs of input providing the appliance is operating in full condensing mode. If an appliance having 100,000 BTUs of input operates for 1200 hours annually, it will produce approximately 1200 gallons of condensate.
The acidic level of the condensate is measured as its pH. Most condensate from natural gas appliances will have a pH of between 2.9 and 4 with 7 being neutral. The actual pH will vary according to the actual chemical makeup of the fuel that is being burned. Condensate contains different types of acids that are corrosive to many materials. The products of natural gas combustion generally include nitrogen oxides, sulfur oxides and hydrogen chloride, as well as water vapor and carbon dioxide. Hydrogen chloride is a result of the combustion of chlorides. These chlorides (salts) are contained in the combustion air.
Taking combustion air from outside generally reduces the amount of chlorides. Nitrogen oxides are a normal by product of combustion. Sulfur compounds are added to the natural gas in small amounts as an odorant.
Condensation of flue gas produces an acidic solution containing concentrations of nitric, nitrous, sulfuric, and sulfurous and hydrochloric acids. These acids can become more concentrated by repeated condensing and evaporation on heat exchangers and flues. Some say condensate from natural gas appliances is no more acidic than vinegar, urine and some citrus juices. Although the pH may be similar, it is a different type of acid and you can be certain no one is dumping thousands of gallons of these liquids into their drains.
A pH of 4 can damage drainage pipes, septic tanks, treatment plants and other materials handling waste water. The pH scale is not linear. Each whole number step below 7 is 10 times more acidic than the next higher number.
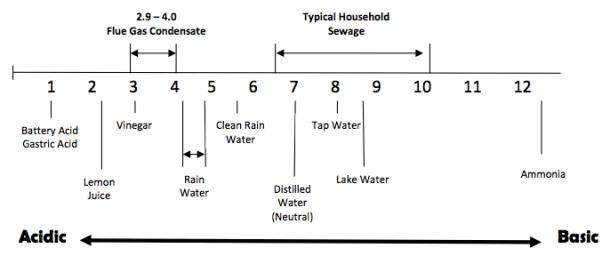
Update:
Treated condensate should be as close to neutral as possible with 5 being the minimum. Most national and state codes [1] prohibit anyone from allowing acidic liquid into a drainage system without treating it to raise its pH.
Treatment of this condensate is accomplished by exposing the liquid to a media containing different materials. We prefer a high quality calcite in combination with magnesium oxide. This blend takes advantage of the self-regulating calcite while adding in some fast acting magnesium oxide.
The acid is converted to water, carbon dioxide and mineral salts when exposed to the media. The carbon dioxide will generally stay diluted in the water and pass out of the neutralizer. The mineral salts generally settle at the bottom of the neutralizer. Over time the media dissolves and must be replenished.
How do you know if the neutralizer is working? Manufacturers of condensate neutralizers provide sizing guide lines and recommended maintenance (media replacement) intervals. The application should be monitored and checked periodically for optimal results. Sizing and maintenance intervals should be adjusted accordingly.
It is the responsibility of the plumbing professional to follow state and local plumbing codes including proper disposal of condensate and equally important for the end user to provide ongoing maintenance ensuring proper function of the unit. An example of damage caused by improperly treated condensate can be seen in the picture at the beginning of this paper. Damage can occur underground and in unseen, remote locations. Imagine digging up your basement floor to replace a rotted out metallic drain line!
[1] National Standard Plumbing Code Chapter 6; Massachusetts Plumbing Code CMR248 Chapter 10. IPC code 803.2
Mike Bernasconi is VP and co-owner of Neutrasafe Corporation, a Massachusetts based manufacturer of condensate neutralizers. Bernasconi, a licensed Master Plumber and hydronics specialist, has been working in the HVAC industry for 35+ years and is well known in the industry for hydronics design and execution. With the onset of condensing boilers, furnaces and hot water heaters, the installation of a condensate neutralizer is now a mandatory requirement. Bernasconi designed a condensate neutralizer with the installer in mind. His product contains a clear body, clean, consistent sized high quality media and offers ease of servicing. Neutrasafe Corporation partners with manufacturer representatives throughout the U.S. to distribute its products. Products can be viewed at www.neutrasafe.com. He can be reached at mike@neutrasafe.com
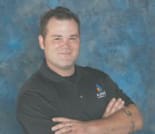
Radiant floors have long been popular in new construction and retrofit projects. In the face of huge popularity, growing success and satisfied customers, it’s difficult to criticize radiant floor heating technology. When radiant floors are installed well under the proper circumstances, radiant floors are among the most comfortable and efficient means of distributing heat in Read more
Radiant floors have long been popular in new construction and retrofit projects. In the face of huge popularity, growing success and satisfied customers, it’s difficult to criticize radiant floor heating technology.
When radiant floors are installed well under the proper circumstances, radiant floors are among the most comfortable and efficient means of distributing heat in most homes. Operating within their capabilities, radiant floors can easily meet the heating loads of well-designed modern structures.
For nearly 20 years I have been installing hydronic-based heating systems. Over the last two decades I have been faced with many situations where radiant floors are either not the best choice for a certain space or heat source no matter how well thought out. However, I have seen many projects where designers have exceeded the capability of the radiant floors and have had to face some harsh realities. Thermodynamics is not just a good idea….it’s the law.
The output of a radiant floor is limited in two ways. First, the maximum surface temperature of a radiant floor is limited to around 87F (about 45 Btu per square foot). If the floor is operated above this temperature, the occupants are likely to complain of uncomfortably hot and sweaty feet.
The second limitation of radiant floors is the amount of energy that can penetrate highly resistant floor coverings, such as certain carpeted and wood floors. Often, these materials limit the actual output to less than 20 Btu per square foot. Unfortunately, these beautiful and thermally resistant floor coverings are often used in the more elegant rooms, with large windows and high heating loads. As a contractor/designer we often must push the limits to meet the load in such spaces. Also, floor coverings are likely to change significantly over the life of the building, leading to the comment “It worked until the owners placed a thick Persian rug over the wood floor”.
How about a radiant floor alternative?
Radiant ceilings can easily operate at surface temperatures up to 100 F, delivering in excess of 55 Btu per square foot. Since ceilings are typically constructed of gypsum based sheet rock, they offer very little resistance to thermal transfer. Unless interior designers regress to the 1960’s and resume putting shag carpeting on the ceilings it’s likely the output of the ceiling won’t change during the life of the home.
In any discussion of radiant ceilings and comfort, there seems to be some ingrained misunderstandings of the concepts. Someone will say that “heat rises, therefore you’ll have a hot head and cold feet”. Not true. Heat doesn’t rise. Hot air rises. In radiant systems objects of mass are heated without heating the air. In fact, there is typically more hot air rising with a radiant floor than with a radiant ceiling. This is because air molecules that come into contact with the radiant ceiling already occupy the highest strata. In radiant floors, the cooler molecules sink and come into contact with the warm floor surface and rise as their density changes with heat, driving the convective forces that cause stratification. Under normal conditions neither radiant floors nor radiant ceilings heat the air to an uncomfortable level like in forced air systems.
Another myth about radiant floors and ceilings involves the surface temperatures that are achieved. Just as the beach sand absorbs the overhead rays of the sun, radiant ceilings warm the floor. There are no cold floors in radiant ceiling projects. You can put a piece of Tahiti in your living room with radiant ceilings.
I also hear radiant ceilings criticized for what is termed “shadowing affects”. This is the belief that legs under tables or desks are shielded from the radiant heat and are, therefore, cold. Radiant ceilings, like floors both radiate and re-radiate. The invisible heat rays emit from the heated surface to other colder unheated surfaces. The total affect of all of this bouncing of energy is very even heat distribution. If a person is seated at a table near an outside wall, there could be some shadowing from above with a radiant ceiling, just as there might be shadowing from below with a radiant floor when seated on a sofa near the outside wall. In most situations, shadowing for radiant ceilings or floors is negligible.
More significant, however is the possibility that objects placed on the radiant floor will impede the flow of energy. Area rugs, and some furnishings such as certain sofas and beds can reduce the usable floor area, increasing the Btu load per square foot and, perhaps, exceeding the system capability. Radiant ceilings are not subject to these types of problems.
Radiant ceilings accelerate fast when needed to meet a big change in heating load. They dissipate energy fast as well. The responsiveness of radiant ceilings makes them excellent for modern controls, placing energy where it is needed when it is needed, and achieving superior comfort and efficiency. Some high mass radiant floors are sluggish in that they take a long time to meet the load.
In modern heating systems too much emphasis has been placed on energy efficiency of the heat plant while wasting energy on poor distribution. This is like putting a Viper engine in a Yugo. Far more heat energy can be salvaged by not wasting it in poorly controlled buildings, than can be achieved by squeezing another Btu per hour out of a heat plant. There are some pretty interesting solutions to heat distribution problems by using radiant floors in conjunction with radiant ceilings. In this way the floors are not required to meet the entire load, yet are conditioned to provide comfortable surface temperatures. The ceilings are heated, where necessary, to take on the severe conditions and give everyone involved the peace of mind that the system will keep up with the heat loss under severe conditions.
Without a doubt, radiant ceilings cost far less than radiant floors. In most cases they cost less than half of a radiant floor. Lower cost means more opportunity. They take less effort to design and install. Radiant ceilings are perfect for retrofit situations. It is very inexpensive and easy to lower a ceiling to accommodate the radiant ceiling, but difficult to raise a floor.
Radiant ceilings are not optimal over a concrete slab placed on the grade of the earth although high r-value flooring can. Radiant floors are best for these situations. I also prefer radiant floors in rooms with smooth surface floors, such as bathrooms where occupants are often barefoot. It is a real nice touch. But when the going gets tough, the heat losses are high and the floor coverings are plush, radiant ceilings cannot be beat.
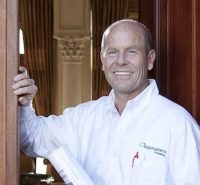
I don’t like to admit it, but I’m becoming an “old-timer” in the geothermal HVAC industry. Regardless, I have made a commitment to continue to look for better ways to do things. If you need a quick review of geothermal heating and cooling, this article is a quick and fun read from Mechanical Hub; it Read more
I don’t like to admit it, but I’m becoming an “old-timer” in the geothermal HVAC industry. Regardless, I have made a commitment to continue to look for better ways to do things. If you need a quick review of geothermal heating and cooling, this article is a quick and fun read from Mechanical Hub; it should get you right up to speed.
Most geothermal systems start with a vertical closed loop-field. The biggest expense relative to geothermal systems is often the unseen, underground heat exchanger, made of High Density Poly Ethylene (HDPE). Drilling, HDPE pipe and labor combine to cause these loop-fields run up the cost of a geothermal HVAC system to roughly 3 times what a standard air sourced system might cost.
When pipe manufacturer, “Versaprofiles” sent me some information on their “thermally enhanced HDPE pipe”, I didn’t have especially high hopes. The pipe costs about twice what standard HDPE costs. It is however 75% more conductive that standard HDPE pipe. That translates to about 11% less drilling. That doesn’t sound like much, but I went ahead a looked a little further.
I called an engineer that had specified the thermally enhanced pipe on the College of Lake County, Grayslake, IL Campus. Norbert Repka, PhD was hard to pin down, and when I did get him on the phone, his first comment was, “I don’t know what I’ve got to tell you about the pipe; we’ve only just finished the drilling.” What I wanted to know was what made Norbert choose the pipe, and did he see an advantage. Norbert spent about 10 minutes on the phone with me.
Norbert’s calculations showed that for their purposes, the pipe provides a 25% improvement in performance, and that they could save about 5% on borehole length. He said that with nearly 100 boreholes drilled they saved (eliminated) 5 boreholes due to the higher thermal conductivity of the thermally enhanced HDPE.
I looked into multiple projects, many of which showed even better results. St. Laurent Sports Complex completed in 2013 is another example of a project that saved considerable resources on loop-field costs.
New York City Transit Authority is planning a test with the thermally enhanced HDPE pipe on their facilities. It’s no secret that New York is a hot bed of activity for geothermal efforts, thanks in part to the efforts of NY-Geo. Anything that can save space and first cost is getting noticed.
Even with Norbert’s conservative calculations, he said the net savings were about $64,000. That means that if they followed the manufacturer’s estimated 11% reduction in borehole length (rather than the 5% they conservatively used), the savings might have been closer to $130,000. Either way, it was a win; both in time and money. In my opinion the pipe is a winner.
This not-so-new pipe (it’s been around since 2009) will be featured in a product showcase on Wednesday at 3:30 at the IGSHPA Expo in Kansas City.
Industry Stakeholders have created a website with vast resources to educate the public on geothermal heat pumps. The “Geothermal Day” Website http://www.geothermalday.com/ aims to raise awareness about environmental and economic benefits of geothermal energy and its vital role in building a clean and secure energy future. We are inviting industry partners, communities, businesses and educators to join efforts to advance further understanding and acceptance of geothermal technology as an unlimited, renewable form of energy. Join us by co-creating and sharing educational resources and participating in interactive activities in local communities and online.
Jay Egg is a geothermal consultant, writer, and the owner of EggGeothermal. He has co-authored two textbooks on geothermal HVAC systems published by McGraw-Hill Professional. He can be reached at jayegg.geo@gmail.com.