After we’ve finally reached the point of “Peak Oil,” global petroleum production may no longer meet demand. In the meantime, the burning of fossil fuels releases the greenhouse gases responsible for global warming into the atmosphere. It is therefore critical to switch to renewable sources of energy. Geothermal is one such source, and its popularity Read more
Industry Blogs
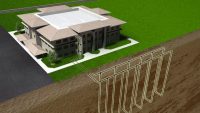
After we’ve finally reached the point of “Peak Oil,” global petroleum production may no longer meet demand. In the meantime, the burning of fossil fuels releases the greenhouse gases responsible for global warming into the atmosphere. It is therefore critical to switch to renewable sources of energy. Geothermal is one such source, and its popularity has been increasing in recent years—but are we training enough technicians to service the eco-friendly systems that utilize it?
Background of Geothermal Energy
Geothermal energy taps the naturally produced heat of the Earth, which is virtually unlimited. The Geothermal Energy Association estimates that the heat coming from the interior of the Earth is equivalent to over 40 million megawatts of electricity. This energy supply is stable and will last for billions of years. RSI notes that in 2009, geothermal energy made up only 1% of global energy needs, yet the expectation is that this number will increase to between 10% and 20% by 2050.
Geothermal Energy Power Plants
The Annual U.S. & Global Geothermal Power Production Report by the Geothermal Energy Association notes that the total amount of geothermal power plant electricity generated in the United States during 2013 was 3,442 megawatts. The states with the most geothermal power plant installations are California, Nevada, and Utah. Over 50% of the geothermal energy potential in those states remains available for utilization.
Geothermal Use Heat Pump Systems
When most people think of geothermal energy, they naturally assume it requires hot springs, geysers, or underground reservoirs of hot water to use for running turbines that create electricity. This is true for geothermal power plants. Nevertheless, there is also a terrific use of geothermal conditions that can be tapped anywhere, using heat pumps.
Just below the “frost line,” about ten feet below the surface, the temperature of the Earth stays constant in the range of between 45°F to 75°F. The ground is warmer than the air above it during winter and cooler during summer. This works all over the world, even in the hottest deserts or the coldest areas, though systems in some areas will be more effective than in others. Heat pump systems use ground heat exchangers to transfer heat into the home in the cold months and out of it during the warm ones, resulting in energy efficiency in the range of 300% to 600%.
Energy.gov offers this video that shows how heat pump systems work with the stable temperatures of the Earth to provide a reliable, clean source of energy for heating and cooling homes.
Geothermal Job Prospects
A May 2014 report by the International Renewable Energy Agency indicated that the geothermal industry supported 35,000 direct and indirect American jobs from 2012 to 2013. According to the Geothermal Energy Association, people directly employed by the geothermal energy sector include welders, pipe fitters, electricians, and HVAC technicians.
The Bureau of Labor Statistics reported that during 2012, there were 130 new geothermal projects installed in fifteen states, most of them in the western United States. As this technology is further developed and becomes more cost effective, the BLS notes that this sector could experience job growth. Moreover, the Natural Resources Defense Council notes that the near-term development of 5,600 megawatts of geothermal energy would create nearly 100,000 jobs.
As with other emerging renewable energy technologies like solar, it will likely be necessary to train more men and women to install, maintenance, and repair commercial and residential geothermal systems to meet future demand.
Monica Gomez is freelance writer, pursuing a bachelor’s degree in journalism at Cal State Long Beach. Subjects covered include healthcare, career, environmental sustainability, welding, HVAC and manufacturing. She can be reached at gomezmonica53@gmail.com.
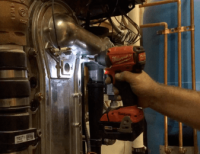
Mod/Con goes 10 years without service The middle of July might not be the most common time of the year to perform annual boiler services but a recent “no hot water” service call had me scrambling for parts and time in the schedule to hopefully erase What turned out to be over ten years of Read more
Mod/Con goes 10 years without service
The middle of July might not be the most common time of the year to perform annual boiler services but a recent “no hot water” service call had me scrambling for parts and time in the schedule to hopefully erase What turned out to be over ten years of neglect.
You read that right, over ten years without service.
When I took the call I vaguely recalled the address of the home but knew that the owner was not the original; when I pulled down the long driveway into the woods I recalled installing the plumbing and in-floor heating [while working for my last employer] for the home. The new owner had purchased the home through a short sale and was eager to find a remedy to his lack of hot water and the mysterious, random explosion-like noises coming from the mechanical room.
You know that feeling as you stand outside a home or building you were at years prior, that sort of recalling of events or challenges? It only took me a minute to remember back to the time of its construction and that this place had over a mile of in-floor tubing along with a rather large (80 gallon) indirect. At the heart of the heating plant was an aluminum boiler; a series 1 aluminum boiler that, in my experience over the years has had me replacing whole heat exchangers, controls and sensors galore. As we introduced ourselves we walked downstairs while he described the issues he was aware of and his concern that the boiler may have never been touched since its original installation.
Our timing couldn’t have been better, as we entered the room the boiler was making an attempt to ignite on a call for DHW. Just a few minutes prior to my arrival the owner had reset the control from a soft lockout stemming from an ignition issue because there was no hot water for his shower. Ugh, I *hate it when that happens.
*Love. I love it when that happens. I need that to happen, we all do, its how we feed our families!
On what may have been its third or fourth attempt to fire up we were startled by the nearly room shaking explosion from within the combustion chamber. “That’s a safety issue and needs addressed immediately!” –were the first words out of my mouth as the owner explained that he had only been hearing that noise for a couple weeks. I guess what prompted him to call was the annoyance of having to walk downstairs into the basement to reset the boiler so he could shower. Nevertheless, I was there and already had a couple ideas of what was the problem.
The first place to start was to remove the ignitor; that gave me a tiny window of sight into the combustion chamber. However small it was, it was better than the completely opaque site glass mounted on the front of the heat exchanger. As it turns out, after pulling the igniter out, it was clear a couple calls would be needed for OEM parts to complete the necessary service. Here’s what I saw first:

Now I’m sure many of you reading this have experience cleaning heat exchangers but for those who have not performed this service I’ve put together a quick overview video of what it entails.
It should be noted that cleaning the combustion chamber of any gas appliance is a process that each manufacturer spells out clearly within their service manuals and through either in-person or online training/certification programs. The manual for this particular boiler states clearly that at the end of one year this service is required and then based on the findings at that time a judgment call by the trained professional is in order to determine cleaning intervals moving forward. Had this boiler been serviced properly at the one-year mark the expense of replacing the burner and added labor costs might have been avoided.
As an aside, I’ve been vocal about my thoughts on aluminum heat exchangers in other forums in the past. Considering the current operational state [after this service] of this particular boiler I’d have to give credit where credit is due. This thing has been neglected for a long time and it’s not only free of leaks but its also performing in the 90-93% efficient range. Not bad but, you can bet the owner signed a service agreement as he wrote out the check.
Eric Aune, Mechanical-Hub & Aune Plumbing
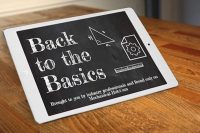
When Eric and John asked me to write a blog post on “Hydronics 101,” I have to admit I was a bit overwhelmed. Where on earth do you start? There’s boiler piping, pipe sizing, circulator selection, heat emitter selection, controls wiring, and so on. There are so many avenues to take when it comes to Read more
When Eric and John asked me to write a blog post on “Hydronics 101,” I have to admit I was a bit overwhelmed. Where on earth do you start? There’s boiler piping, pipe sizing, circulator selection, heat emitter selection, controls wiring, and so on.
There are so many avenues to take when it comes to “Hydronics 101” that choosing a starting point becomes quite a daunting task.
But then I thought of one of the very first training classes I ever did.
It was 1995 during a full-day program on radiant floor heating. We were going through the process of radiant design — figuring out installation method, tube spacing and water temperature. We were looking over charts and graphs to make heads or tails out of this radiant job when a fellow in the back of the room raised his hand.
“Don’t you have computer software that figures all this stuff out?”
Yep, we do.
“Then why are you wasting our time telling us all this? Just give us the software and we can go home.”
Ummm, it doesn’t quite work that way.
Design software, whether it’s for hydronics or forced air, is really nothing more than a fancy calculator. It does the arithmetic for you, and that’s about it. It doesn’t think for you, it doesn’t make decisions for you and it doesn’t tell you if you’ve input the wrong data.
It’s a calculator.
That’s it.
I like to ask folks in my classes how many of them have been formally trained in how to perform heat loss calculations. We call it “doing the math.”
As the years have gone by, fewer and fewer people raise their hands. No one’s teaching heat loss anymore, and I think it’s a shame. Knowing the actual heating load of a house or of a zone is the real “starting point” for beginning hydronics or for advanced hydronics.
How can you size a boiler if you don’t know the load? You can guess, but it’s just that: a guess. You can base your load on a standard BTU-per-square-foot multiplier, but that’s not a heat loss calculation. That’s just a guess with better PR. You can even measure the radiation, multiply by whatever multiplier you care to use and call that the load. But all that tells you is how much radiation is installed.
Good to know, but it doesn’t tell you the actual load of the house.
There’s no way around it: a good old-fashioned heat loss calculation is the only way of getting anywhere close to what the actual load of the house really is. Are “by-the-book” heat loss calculations 100% accurate? Nope — there’s so much fudge built in to the calculation methods out there that it’s a wonder we’re not all diabetic. But they’re still better than guessing.
During one of Taco’s Heat Loss classes a while back, the class was presented with a set of blueprints for normal, stick-framed house. There was nothing special about this house. It wasn’t super-insulated with super-low E windows or anything. It was a basic 2200 square foot ranch, with an outdoor design temperature of 7 degrees above Zero.
I asked the group, based on their years of knowledge and experience, to come up with their best, most accurate estimate for the heating load of the house. Their responses ranged anywhere from 55,000 BTUH on the low end to 125,000 BTUH on the high end.
The class then worked through an I-B-R based heat-loss analysis using the H-22 Heat Loss Design Guide (find it on Amazon under “Freaking Awesome Heat Loss Book!”). Using charts, graphs and real live, honest-to-goodness math, the class calculated the heat loss of that house to be a whopping 31,000 BTUH.
Well ain’t that a kick in the head!
Bottom line gang: any fundamentally sound hydronics system starts with the math. Heat load allows us to size our boiler and all of our piping as accurately as possible, which can have a major impact on materials costs. And only when we know the heating load and the size and length of the pipe that heat has to go through can we figure out what we need for a circulator, because load determines flow and pipe size and length determine head loss.
And weather impacts it all.
From there we can look at all the different types of circulators (steep curve, flat curve, single-speed, 3-speed, variable speed, Delta-T, Delta-P) and try to determine which one best fits the job we’re looking at – and no, there’s NO SUCH THING as “the only circulator you’ll ever need.” That’s a load of hogwash.
So where does “Hydronics 101” start? It must start with an accurate idea of what you’re trying to accomplish, which is to make sure this structure heats on what’s commonly referred to as “the coldest day of the year.” Now, if you’re simply replacing a dead circulator, there’s precious little math that needs to be done (but you still have to know about circulators and their impact on systems – that’s a future segment). But if you’re replacing a boiler or actually starting from scratch, the only right way to start is with a pad of paper, a scaled ruler, a pencil and a calculator. If John and Eric invite me back, we’ll walk through simple heat loss calculations done the old fashioned way. Software will do it quicker, but in order for software to be a tool and not a convenience item, it’s important to know why it came up with the numbers that it did.
As my old man used to say, “Knowing how is good, but know why is better. Because those who know ‘how’ will always work for those who know ‘why.’”
John Barba is training manager for Taco Inc.
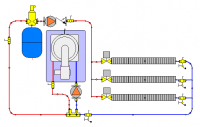
It’s a pretty common belief, at least in my neck of the woods, that condensing boilers and baseboard don’t “work well together” and the most cited reason is the need for high operating temperatures with baseboard. Of course they work, but how well? Awfully well in the vast majority of cases! Traditional boilers in the Read more
It’s a pretty common belief, at least in my neck of the woods, that condensing boilers and baseboard don’t “work well together” and the most cited reason is the need for high operating temperatures with baseboard. Of course they work, but how well? Awfully well in the vast majority of cases!
Traditional boilers in the USA are “non-condensing,” which means that they discharge flue gases at a high enough temperature that all water vapor is carried out of the flue. The water vapor is discharged with the other flue gases and never has a chance to condense to a liquid. The problem is that the hotter the flue gases, the more fuel is wasted and the less efficient the boiler.
So how does a condensing boiler work?
They absorb enough heat from the flue gases to drop the exhaust temperature below the point that the water vapor in the gases condenses into liquid and gives up its latent energy. Sounds great but the flue gas can only condense when the return water temperatures are 135F or less. The rated output of baseboard is realized at 180F.
How can this work at all, much less well? A few reasons!
First and foremost is the use of outdoor reset; can’t say I’m aware of any mod/con without integral ODR. Lowering the supply temperature by the use of ODR will of course yield lower return water temps, low enough to provide operation in the condensing mode for quite a bit of the heating season.
The second contributor to the viability of condensing technology with baseboard is the over-sizing of the baseboard itself; people have a pretty strong tendency to put in more baseboard than a heat loss calculation would indicate. While not as strong as the desire to over size boilers, the baseboard over sizing drive is definitely very dominant in the heating contractor genome. This, unlike boilers that are too big, is actually a good thing; more baseboard means the load can be met with lower water temperatures.
The third main factor is the design temperature; it really doesn’t get that cold all that often! That means the rest of the time, we don’t need to run 180F supply temperatures. Combine these and you will be running in the condensing range for the majority of the heating season, although certainly not all of it.
Dr T. Butcher of Brookhaven National Labs did a study on this topic in 2004 and found that 94% of the heating season time could be spent in condensing mode. It’s not light reading but if you are interested in an in-depth exploration of this topic, it’s available here: http://www0.bnl.gov/isd/documents/28709.pdf
There is another avenue of savings that mod/cons provide that is quite often overlooked: modulation. Modulation is varying the size of the fire in relation to the load. A cast iron boiler has two speeds — on and off. In comparison, a modulating boiler can vary its input, usually at a 4:1 or 5:1 ratio. A 100K Btu modulating boiler can operate from approx 20K Btu to 100K Btu. There is quite a bit of fuel to be saved by having the “right” size boiler on almost every day. I don’t know of any studies done to quantify the savings with modulation but based on anecdotal evidence over many years, I would place it in the 15% range.
A word of advice, don’t over size condensing boilers assuming the modulation will take care of it. I’ve seen 150K mod/cons in 50K heat loss homes and they never get off low fire except on DHW calls, not a recipe for efficiency. Properly applied mod/cons and baseboard can make for a long and happy marriage!
Robert C. O’Brien is the owner of Technical Heating Co. LLC in Mt. Sinai, NY. Robert serves as the Vice President of the national OESP chapter. See more from Robert in his blog “Boiler Sizing & Indirect Water Heaters”, “Converting from Oil to Natural Gas“ & “Heat Loss Calculation on Every Replacement?”
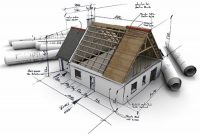
Do you do a heat loss calculation on every replacement job? Should you? Everyone will say you absolutely, positively a must! At the risk of being excommunicated from the Hydronic Brethren, I’ll say not always, and, depending on the type of work you do, maybe never. How can that be possible?
By Robert C. O’Brien, Owner of Technical Heating Co. LLC
Do you do a heat loss calculation on every replacement job? Should you? Everyone will say you absolutely, positively a must! At the risk of being excommunicated from the Hydronic Brethren, I’ll say not always, and, depending on the type of work you do, maybe never. How can that be possible?
I live and work on that lengthy, narrow atoll that Dan Holohan refers to as the Isle of Long, aka Long Island. It’s full of subdivisions built mostly between 1950-1980; these developments are invariably comprised of a very few models of homes. Ranches, capes and colonials primarily with a smattering of variations on that theme, splanches, high ranches and split levels. Probably 90% of the homes will fit one of these categories.
Back in the early ’80s I was told a Manual J was the proper way to size boilers and I decided that I would do it that way. The Manual J is very aptly named because it entails a lot of manual labor to gather the data and then do the calculation the old school way on worksheets. After slightly more than four hours into it, I arrived at a number that was approximately one third that of the existing boiler? Impossible! I did the math again with the same result. I thought my scientific approach would impress the prospective client and win me the job, not quite! I presented my proposal to the homeowner along with the heat loss worksheet showing a boiler size of 59,000 BTU/hr. It wasn’t received very well. After he stopped laughing and regained his composure, he showed me the three other quotes he had gotten. The existing boiler was 160K, the quotes were from 160-225K — all from reputable local companies, who at that point in time had been in business a lot longer than me. Long story short, he went with the company proposing the 225K boiler. “That way it doesn’t have to work as hard”
That turned me off heat loss calculations for quite awhile, until I got my first computer, an IBM XT. Some very expensive heat loss software and I was back in the game, only now with very official looking reports printed with my daisy wheel printer! I had a little bit better luck this time around, and while not everyone was buying this method of boiler sizing, enough were. I’d be lying if I wasn’t nervous when the first stretch of design temp weather set in but amazingly enough, no complaints! I started doing quite a few with the new computer but after awhile I noticed something: the numbers were almost all the same. No sense spending time measuring another ranch when you’ve already done 10 of them and they are all within 5% of each other!
There was and still is a very substantial proportion of oil heated homes on Long Island, and unfortunately, there aren’t a lot of choices size wise in oil boilers. Even today, 65K is about the smallest and many manufacturers smallest are in the 85K range. Doesn’t make a lot of sense measuring a house you know from doing many heat loss calcs on similar homes is less than 50K when the smallest boiler available is 85K!
Yeah, but what about the oddball home? The mid-’80s contemporaries or the circa homes? I have an answer to those as well and no measuring required! You need some information; the heating degree days over a known period of time; I’d recommend a year and the fuel consumption over that same time period. Degree days can be found at http://www.weatherdatadepot.com/
Step 1. Add up all the BTUs of the fuel you used and multiply by the AFUE rating of your heating appliance. A gallon of oil has 139,000 BTUs/gallon, a therm of natural gas has 100,000 BTUs/therm, and gallon of propane contains 91,000BTUs/gallon. Some gas utilities measure their consumption in CCF, which is 100 cubic feet, which is 102,000 BTUs
Step 2. Divide the total number of BTUs by the number of heating degree days. The result is a measure of how many BTUs your home lost per Heating-Degree-Day. Now divide that result by 24 to obtain the number of BTUs your home loses per heating-degree-hour. Lastly, multiply the result by the difference between 70°F and the design temp. For example, if the design temp is 0°F, then the difference you multiply your heating-degree-hours by is 70°F.
An example:
Home using 1000 therms/year in a 80% boiler in a 6000 Degree day climate per year
1000 x 100,000 ( BTU per therm) = 100,000,000 BTU’s
100,000,000 x .80 (AFUE) = 80,000,000
80,000,000 ÷ 6000( Degree Days) = 13,333.33
13,333.33 ÷ 24 (hours per day) = 555.555
555.555 x 70 ( desired indoor delta T) = 38,888 BTU/Hr
38,888 = heat loss of home
A couple of big advantages to this system, it gives you an actual heat loss on an actual home, not a calculation based on factors that may or may not be correct. How do you know the infiltration or do anything other than guess at an R value? No tape measure required! There a few caveats, however; if they use supplemental heating, mini split heat pumps, pellet stoves, etc., the number will not be correct and depending on how much they supplemented may not even be close.
Caveat number two: they kept the house colder than they would have liked due to fuel cost; this one is pretty common in oil and propane heated homes and will skew the number lower because of the abnormally low fuel consumption. Ask these questions upfront and when you get the final number, ask yourself if it makes sense. The average number around here is 20 BTU/sq ft. If I am much off that in either direction, I look for a reason why. As a last resort you can always break out the tape measure!
Robert C. O’Brien is the owner of Technical Heating Co. LLC in Mt. Sinai, NY. Robert serves as the Vice President of the national OESP chapter. See more from Robert in his blog “Boiler Sizing & Indirect Water Heaters“ & “Converting from Oil to Natural Gas“.