Fellow Hydronic Professionals,, I have been the director of the RPA now for 2 and 1/3 years. It has been an arduous journey, with some ups and some downs, mostly ups, but we (I especially) do this for the industry. We now have in place one of the most dynamic group of people (members on Read more
Radiant Energy Systems
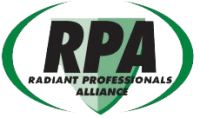
Fellow Hydronic Professionals,,
I have been the director of the RPA now for 2 and 1/3 years. It has been an arduous journey, with some ups and some downs, mostly ups, but we (I especially) do this for the industry.
We now have in place one of the most dynamic group of people (members on committees and members in general) and are kicking butt and taking names. We have an actual Hydronics/Radiant Code that is part of the Uniform family of codes (Uniforms Solar Energy Hydronics Code) and are in the final stages of developing an ANSI recognized, ASSE developed Professional Certification program for designers and installers.
We have and continue to add instructors to, our online university, RPAU, with HeatSpring offering some of the best instructors time and money can buy, making education of yourself and your employees available at YOUR convenience.
We recently inked a deal with Tom Grandy and Associates to help show experienced contractors how to turn their hard work into a good profit margins so they can retire comfortably or live well before retirement.
We have inked a deal with Kilowatt Financial to provide low interest, high dollar (up to $30K) financing IN THE CONSUMERS HOUSE. (less than 30 minute approvals online)
We have renewed commitments from UPS offering our members a significant discount on shipping less than truck loads.
We have a monthly newsletter available to members only.
We have printed magazines to help you sell radiant comfort (walls floors and ceilings) to the consumers.
We have monthly Lunch and Learn webinars to keep you abreast of the latest and greatest in our industry.
We have HydroniX Talk (which is on summer vacation) which is also available to members only, and will now be taking place early evenings during the week, beginning this coming fall, featuring the likes of Dan Holohan and many other notable hydronics pioneers.
All of this for a contractor for less than $1.00 per day (actually less than that because the $300/year fee is good for 3 employees) as well as access to some of the best minds this industry has to offer (locked access LinkedIn accounts).
And we continue to look for ways to promote this wonderful industry of ours so that we can prove to the world something that most people here have known for a long time, that being that hydronics is THE most efficient method of transferring energy from point A to point B, or from point B to point A.
We have legislative power in Washington DC looking out for our industry’s interests. (The old RPA was not allowed to lobby)
There’s only one major missing component…..
>>> YOU! <<<
I and my membership committee (and the other 7 committees) are baffeled as to why former members of the old RPA and new potential members are not coming back into the fold.
So, I’d like to ask some questions and clear up some rumors.
Rumor 1: IAPMO runs the RPA. Wrong, WE run the RPA. IAPMO owns it lock stock and barrel, and provides us with all of the tools and support we need to further its goals, but the RPA is run by its members. It is an organization OF the members, BY the members, FOR the members.
Rumor 2: RPA is dead. Wrong, it came extremely close to going under during the economic down turn, and if IAPMO had not intervened, it would have gone down in flames. Fortunately, IAPMO caught it before it plowed into the ground, gave it a soft landing, re-painted the plane, refueled it and sent it back up into the air.
Rumor 3: IAPMO is dead. This couldn’t be further from the truth. IAPMO is the largest CDO (Code Development Organization) in the world. In fact they are expanding and now have offices around the world, helping to establish plumbing and mechanical codes around the world.
Rumor 4: IAPMO and the RPA are too big for me to consider joining. WRONG, these organizations are here to support you, not fight you. Every code and standard that is developed by these organizations are done so under a very tightly watched and controlled ANSI Open Consensus process. No complaint goes unattended or ignored. All concerns are addressed until there are no more concerns.
So, my question to you is why have you (contractors, designers, installers, equipment manufacturers, manufacturer rep agencies and others) not joined, or rejoined this fantastic organization? There is strength in numbers, and if we as an industry don’t band together real soon, there is a real possibility that our industry will be put out of business by some very savvy foreign interests who have stated publicly that their intent is to take over ALL methods of heating and cooling.
Tell me what rumors you’ve heard, or why it is that you haven’t joined this organization. We are all ears, and we want to make certain that this machine is your machine, and that it does work for YOU, the industry.
I’d also like to thank all of our volunteers and our board of directors for their guidance in getting the ship to this point. Without your help, we wouldn’t have gotten this far. THANK YOU.
Now, tell me what your concerns are?
If you’d like to join, go to www.radiantprofessionalsalliance.org and click on the JOIN button, or simply call Alan Wald, our Vice President of Memberships at 909-472-4211and he or one of his staff can get you signed up over the phone. Easy squeasy lemon peasy.
Thank you for your consideration, and thanks to the Mechanical Hub for being a member and allowing us to use this venue.
Mark Eatherton
Executive Director, Radiant Professionals Alliance
18927 Hickory Creek Drive, Suite 220
Mokena, IL 60448
Desk: 708-995-3001
Toll free: 877-427-6601
www.radiantprofessionalsalliance.org
Email: mark.eatherton@radiantprofessionalsalliance.org
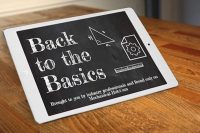
When Eric and John asked me to write a blog post on “Hydronics 101,” I have to admit I was a bit overwhelmed. Where on earth do you start? There’s boiler piping, pipe sizing, circulator selection, heat emitter selection, controls wiring, and so on. There are so many avenues to take when it comes to Read more
When Eric and John asked me to write a blog post on “Hydronics 101,” I have to admit I was a bit overwhelmed. Where on earth do you start? There’s boiler piping, pipe sizing, circulator selection, heat emitter selection, controls wiring, and so on.
There are so many avenues to take when it comes to “Hydronics 101” that choosing a starting point becomes quite a daunting task.
But then I thought of one of the very first training classes I ever did.
It was 1995 during a full-day program on radiant floor heating. We were going through the process of radiant design — figuring out installation method, tube spacing and water temperature. We were looking over charts and graphs to make heads or tails out of this radiant job when a fellow in the back of the room raised his hand.
“Don’t you have computer software that figures all this stuff out?”
Yep, we do.
“Then why are you wasting our time telling us all this? Just give us the software and we can go home.”
Ummm, it doesn’t quite work that way.
Design software, whether it’s for hydronics or forced air, is really nothing more than a fancy calculator. It does the arithmetic for you, and that’s about it. It doesn’t think for you, it doesn’t make decisions for you and it doesn’t tell you if you’ve input the wrong data.
It’s a calculator.
That’s it.
I like to ask folks in my classes how many of them have been formally trained in how to perform heat loss calculations. We call it “doing the math.”
As the years have gone by, fewer and fewer people raise their hands. No one’s teaching heat loss anymore, and I think it’s a shame. Knowing the actual heating load of a house or of a zone is the real “starting point” for beginning hydronics or for advanced hydronics.
How can you size a boiler if you don’t know the load? You can guess, but it’s just that: a guess. You can base your load on a standard BTU-per-square-foot multiplier, but that’s not a heat loss calculation. That’s just a guess with better PR. You can even measure the radiation, multiply by whatever multiplier you care to use and call that the load. But all that tells you is how much radiation is installed.
Good to know, but it doesn’t tell you the actual load of the house.
There’s no way around it: a good old-fashioned heat loss calculation is the only way of getting anywhere close to what the actual load of the house really is. Are “by-the-book” heat loss calculations 100% accurate? Nope — there’s so much fudge built in to the calculation methods out there that it’s a wonder we’re not all diabetic. But they’re still better than guessing.
During one of Taco’s Heat Loss classes a while back, the class was presented with a set of blueprints for normal, stick-framed house. There was nothing special about this house. It wasn’t super-insulated with super-low E windows or anything. It was a basic 2200 square foot ranch, with an outdoor design temperature of 7 degrees above Zero.
I asked the group, based on their years of knowledge and experience, to come up with their best, most accurate estimate for the heating load of the house. Their responses ranged anywhere from 55,000 BTUH on the low end to 125,000 BTUH on the high end.
The class then worked through an I-B-R based heat-loss analysis using the H-22 Heat Loss Design Guide (find it on Amazon under “Freaking Awesome Heat Loss Book!”). Using charts, graphs and real live, honest-to-goodness math, the class calculated the heat loss of that house to be a whopping 31,000 BTUH.
Well ain’t that a kick in the head!
Bottom line gang: any fundamentally sound hydronics system starts with the math. Heat load allows us to size our boiler and all of our piping as accurately as possible, which can have a major impact on materials costs. And only when we know the heating load and the size and length of the pipe that heat has to go through can we figure out what we need for a circulator, because load determines flow and pipe size and length determine head loss.
And weather impacts it all.
From there we can look at all the different types of circulators (steep curve, flat curve, single-speed, 3-speed, variable speed, Delta-T, Delta-P) and try to determine which one best fits the job we’re looking at – and no, there’s NO SUCH THING as “the only circulator you’ll ever need.” That’s a load of hogwash.
So where does “Hydronics 101” start? It must start with an accurate idea of what you’re trying to accomplish, which is to make sure this structure heats on what’s commonly referred to as “the coldest day of the year.” Now, if you’re simply replacing a dead circulator, there’s precious little math that needs to be done (but you still have to know about circulators and their impact on systems – that’s a future segment). But if you’re replacing a boiler or actually starting from scratch, the only right way to start is with a pad of paper, a scaled ruler, a pencil and a calculator. If John and Eric invite me back, we’ll walk through simple heat loss calculations done the old fashioned way. Software will do it quicker, but in order for software to be a tool and not a convenience item, it’s important to know why it came up with the numbers that it did.
As my old man used to say, “Knowing how is good, but know why is better. Because those who know ‘how’ will always work for those who know ‘why.’”
John Barba is training manager for Taco Inc.
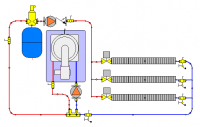
It’s a pretty common belief, at least in my neck of the woods, that condensing boilers and baseboard don’t “work well together” and the most cited reason is the need for high operating temperatures with baseboard. Of course they work, but how well? Awfully well in the vast majority of cases! Traditional boilers in the Read more
It’s a pretty common belief, at least in my neck of the woods, that condensing boilers and baseboard don’t “work well together” and the most cited reason is the need for high operating temperatures with baseboard. Of course they work, but how well? Awfully well in the vast majority of cases!
Traditional boilers in the USA are “non-condensing,” which means that they discharge flue gases at a high enough temperature that all water vapor is carried out of the flue. The water vapor is discharged with the other flue gases and never has a chance to condense to a liquid. The problem is that the hotter the flue gases, the more fuel is wasted and the less efficient the boiler.
So how does a condensing boiler work?
They absorb enough heat from the flue gases to drop the exhaust temperature below the point that the water vapor in the gases condenses into liquid and gives up its latent energy. Sounds great but the flue gas can only condense when the return water temperatures are 135F or less. The rated output of baseboard is realized at 180F.
How can this work at all, much less well? A few reasons!
First and foremost is the use of outdoor reset; can’t say I’m aware of any mod/con without integral ODR. Lowering the supply temperature by the use of ODR will of course yield lower return water temps, low enough to provide operation in the condensing mode for quite a bit of the heating season.
The second contributor to the viability of condensing technology with baseboard is the over-sizing of the baseboard itself; people have a pretty strong tendency to put in more baseboard than a heat loss calculation would indicate. While not as strong as the desire to over size boilers, the baseboard over sizing drive is definitely very dominant in the heating contractor genome. This, unlike boilers that are too big, is actually a good thing; more baseboard means the load can be met with lower water temperatures.
The third main factor is the design temperature; it really doesn’t get that cold all that often! That means the rest of the time, we don’t need to run 180F supply temperatures. Combine these and you will be running in the condensing range for the majority of the heating season, although certainly not all of it.
Dr T. Butcher of Brookhaven National Labs did a study on this topic in 2004 and found that 94% of the heating season time could be spent in condensing mode. It’s not light reading but if you are interested in an in-depth exploration of this topic, it’s available here: http://www0.bnl.gov/isd/documents/28709.pdf
There is another avenue of savings that mod/cons provide that is quite often overlooked: modulation. Modulation is varying the size of the fire in relation to the load. A cast iron boiler has two speeds — on and off. In comparison, a modulating boiler can vary its input, usually at a 4:1 or 5:1 ratio. A 100K Btu modulating boiler can operate from approx 20K Btu to 100K Btu. There is quite a bit of fuel to be saved by having the “right” size boiler on almost every day. I don’t know of any studies done to quantify the savings with modulation but based on anecdotal evidence over many years, I would place it in the 15% range.
A word of advice, don’t over size condensing boilers assuming the modulation will take care of it. I’ve seen 150K mod/cons in 50K heat loss homes and they never get off low fire except on DHW calls, not a recipe for efficiency. Properly applied mod/cons and baseboard can make for a long and happy marriage!
Robert C. O’Brien is the owner of Technical Heating Co. LLC in Mt. Sinai, NY. Robert serves as the Vice President of the national OESP chapter. See more from Robert in his blog “Boiler Sizing & Indirect Water Heaters”, “Converting from Oil to Natural Gas“ & “Heat Loss Calculation on Every Replacement?”

REHAU was awarded with the Plastics Pipe Institute (PPI) Building & Construction Division’s Project of the Year earlier this month at the organization’s annual meeting. The award recognizes the company’s role in the École Secondaire Jeunes sans Frontiers (Secondary School for Youth Without Frontiers) project in Brampton, Ontario. The school, which has earned the Read more

JSF High School features a REHAU radiant slab heating and cooling system installed throughout the building. Photo © Patrick Kennedy.
REHAU was awarded with the Plastics Pipe Institute (PPI) Building & Construction Division’s Project of the Year earlier this month at the organization’s annual meeting. The award recognizes the company’s role in the École Secondaire Jeunes sans Frontiers (Secondary School for Youth Without Frontiers) project in Brampton, Ontario. The school, which has earned the Canadian Green Building Council’s LEED® Silver certification, is the first secondary school building in Ontario to have achieved this status.
Designed by Robertson Simmons Architects, the French language high school, which encompasses approximately 91,000 sq. ft., is dedicated to fostering an enriched, student-focused learning experience by providing a healthy and sustainably designed environment. To achieve this, the design includes indoor spaces integrated with outdoor landscapes, a green roof, expansive daylighting, water-conserving plumbing fixtures, lighting with occupancy sensors and displacement ventilation.

The system consists of 104,700 ft (32,000 m) of RAUPEX® 5/8-in. O2 Barrier pipe and 42 PRO-BALANCE® manifolds. Photo courtesy Klimatrol.
To achieve maximum HVAC efficiency, the design includes a REHAU radiant slab heating and cooling system, which circulates a heated or chilled water-glycol solution through a network of PEX piping installed in the floors throughout the entire facility. The radiant system enables the school to meet indoor environmental criteria related to air quality, noise reduction and occupant comfort while also maximizing space efficiency by eliminating bulky convectors and ductwork.
“To help the school recognize the benefits of a combined radiant heating and cooling system, we supplied a finite element analysis to model the floor heating and cooling output,” explained Mark Euteneier, president of Klimatrol Environmental Systems, the project’s designer and supplier. “The results predicted a significant energy savings due to reduced heating and cooling loads and increased efficiencies of the heated and chilled water sources,” he said. “Coupled with the comfortable, even method of heating and cooling, this analysis made the REHAU radiant system a must-have for the project.”
The system consists of 104,700 ft (32,000 m) of RAUPEX® 5/8-in. O2 Barrier pipe and 42 PRO-BALANCE® manifolds pre-piped with 3-way valves into recessed manifold distribution cabinets. The PEX pipe was installed at the ground level in a concrete slab-on-grade design using a counter-flow spiral pattern to promote even surface temperatures.
To accommodate precast concrete floors on the second level, the pipe was affixed using plastic rails of recycled PVC and covered with a 2 to 3 in (5 to 8 cm) concrete layer.
REHAU has been previously recognized with PPI Building & Construction Division Project of the Year awards for the Denver Zoo Asian Tropics Complex as well as for the Vail, Colorado town center project, Solaris.
Plastics Pipe Institute Inc. (PPI) is a non-profit trade association dedicated to the advocacy and advancement of use of plastics in pipe infrastructure systems because they are smart, economical and sustainable solutions. The association is comprised of approximately 300 members and associates. The mission of PPI is to promote plastics as the material of choice for piping applications.
For additional information, visit www.na.rehau.com/mp
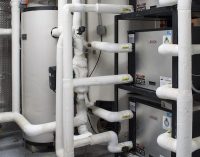
Homes on Providence’s historic East Side often come with an enviable address, lovely views and antiquated heating systems. Such was the case last year with a 12,000-sq.-ft. home on the East Side with a view overlooking the state capitol. A new buyer decided to completely renovate the home and install a new HVAC system using Read more

Homes on Providence’s historic East Side often come with an enviable address, lovely views and antiquated heating systems. Such was the case last year with a 12,000-sq.-ft. home on the East Side with a view overlooking the state capitol. A new buyer decided to completely renovate the home and install a new HVAC system using state-of-the-art technologies including geothermal, in-floor radiant and hydro-air.
Going with Geothermal
TJ’s Plumbing and Heating, Inc., Attleboro, Mass., a firm with expertise in designing and installing geothermal, radiant and solar thermal systems, was the HVAC contractor awarded the contract by the owner, in conjunction with the home renovation contractor, Parker Construction of East Providence, R.I., which specializes in custom luxury homes. Tim Cutler, owner of TJ’s, has been doing geothermal installations for around 10 years, mostly for high-end homes, both new construction and retrofits, and he has seen a 30% growth in his firm’s business stemming directly from geothermal.
With an aged heating system fired by an oil-fired steam boiler, coupled with the new owner’s desire not to have any HVAC equipment situated outside the home for aesthetic reasons, TJ’s challenge was to deliver the ultimate comfort system without compromising the home’s integrity. To accomplish this task they provided a design-build alternative energy system for both heating and cooling, attaining a comfortable indoor environment year-round with a water-to-water geothermal system as the centerpiece of the home energy system.
According to Cutler, vertical bore holes work best in New England’s rocky soil. With sufficient property available for drilling six 550-ft. bore holes for the geothermal system, TJ’s selected and installed three Bosch-FHP 6-ton, two-stage water-to-water TW071 Series heat pumps in the home’s mechanical room. TW Series units feature a two-stage scroll compressor and floating base pan for quiet, high efficiency performance. Unless peak capacity is required, the units can run at roughly two-thirds capacity, at significantly higher efficiencies than other geothermal heat pumps. For backup heat and domestic hot water needs, TJ’s installed a Viessmann gas-fired condensing boiler.
The home has a total eight bathrooms on three floors, and to keep its floors warm underfoot, as well providing in-floor heat for most of the first floor, TJ’s installed a Viega radiant heat system. The firm also installed seven zones of hydro-air using chilled water for cooling and 120° design water temperature for heating. Custom designed sheet metal was used to fit into the home without compromising the home’s integrity or elegance.
Ensuring high indoor air quality
To ensure the highest IAQ and to also provide radon removal, TJ’s installed a Zehnder ComfoAir 350 unit to constantly change the home’s indoor air. This system works continuously to extract moist, stale air from wet rooms (kitchen, bathrooms, utility rooms and closets) and supply fresh, filtered air to habitable rooms. Up to 90% of the heat in the extracted air, which would otherwise be exhausted outside the home, is recovered by the heat exchanger in the ComfoAir unit to temper incoming supply air. To manually increase airflow if needed, TJ’s installed a wall-mounted Zehnder control.
The Federal tax credit’s importance
Since the home’s completion and occupancy last fall, TJ’s reports that the geothermal system has operated as designed and has fully met the client’s expectations. In addition to the concerns about energy efficiency savings and environmental considerations, a driving factor for many of TJ’s geothermal clients is the 30% federal tax credit, a credit that Cutler, and the geothermal industry, would like to see continued beyond 2016.
Project Details:
General Contractor: Parker Construction, East Providence, RI
HVAC: TJ’s Plumbing and Heating, Attleboro, MA
Geothermal Well Driller: Skillings & Sons, Amherst, MA
Interior Designer: Scarborough Phillips Design, West Warwick, RI
Wholesaler: Delta T, Warwick, RI
Bosch Thermotechnology and TJ’s Plumbing and Heating supplied information for this case study. Tim Cutler, owner of TJ’s, is an Accredited Bosch Contractor. He is also IGSHPA and NATE Geo certified.