When most people think of radiant heat or hydronic snow melt, the usual applications come to mind: warm floors, heated sidewalks and snow-free driveways. The Big Bear Area Regional Wastewater Agency (BBARWA) in Big Bear, Calif., contacted Viega Radiant Design Services with a project that needed an innovative solution. A byproduct of the water treatment Read more
Radiant Energy Systems
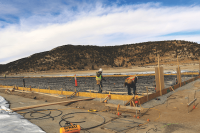
When most people think of radiant heat or hydronic snow melt, the usual applications come to mind: warm floors, heated sidewalks and snow-free driveways. The Big Bear Area Regional Wastewater Agency (BBARWA) in Big Bear, Calif., contacted Viega Radiant Design Services with a project that needed an innovative solution. A byproduct of the water treatment process is sludge which must be hauled by a truck to an off-site disposal area. BBARWA needed to reduce the water content and weight of the sludge, making it less expensive to haul. BBARWA tried several different methods to dry the sludge with only marginal success, so they decided to devise a new system that would be more effective, more efficient and would reduce the odor complaints.
Viega Radiant Design Services worked on the specifics of the slab-heating system design, focusing on what would be required to generate enough heat from the slab to meet the sludge-drying objectives. Viega design engineers used finite element analysis (FEA) to determine the optimum tubing size, spacing and install-depth in the slab based on the water temperature supplied from the diesel generator’s exhaust. Due to the shape and size of the 315- by 60-foot heated slab, it was clear that this project was an excellent application for Viega’s revolutionary Viega Climate Mat® system.

Within the first year alone, the new system saved approximately $200,000 in transportation and fuel costs. Additionally, the project received the California Water Association Desert Mountain Award for Innovation.

For more information on Viega system solutions, visit Viega.us.
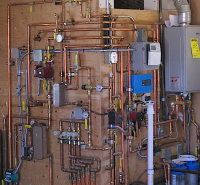
A leading solar integrator in the San Luis Valley of southern Colorado, Solar Gain Services has been offering solar thermal and photovoltaics to commercial and residential clients since 2007. When co-owner Luke Christy—NABCEP certified as both a solar heating installer and as a PV installation professional—received a call from a homeowner in Sagauche, Colo., to Read more
A leading solar integrator in the San Luis Valley of southern Colorado, Solar Gain Services has been offering solar thermal and photovoltaics to commercial and residential clients since 2007.
When co-owner Luke Christy—NABCEP certified as both a solar heating installer and as a PV installation professional—received a call from a homeowner in Sagauche, Colo., to reduce the overall energy usage footprint as low as reasonably possible, he had the tools and pedigree to meet the energy challenge. The 2,000-sq.-ft. home was built to LEED Gold standards, is heavily insulated, incorporates passive solar features, and has a grid-tied solar electric system to help offset the electrical energy consumption.

The solution, after taking into account available budgets and the highly efficient home, was to install a hybrid combi-system—for domestic hot water (DHW) and radiant floor heat—with a large amount of thermal storage. A copper single pass tube coiled within the tank serves as the primary means of heating DHW. Since the tank is purposely stratified, with the top of the tank always being charged first. “This technique works very well,” says Christy. A setpoint control activates a Caleffi 3-way valve to divert water from the single-pass through the tankless heater when the tank temperature is low.
Eight installed Viessmann Vitosol 100 solar collectors heat a 700-gallon custom stainless steel tank through a brazed plate heat exchanger, and Christy opted to go without a mod-con boiler for back-up heat to reduce costs. Instead, a gas-fired tankless water heater paired with a plate heat exchanger and some control logic serves as a back-up heat source.
A Caleffi iSolar BX solar controller charges the storage tank in two vertical stages to ensure that the top of the tank is always as hot as possible, even in winter. This helps preheat DHW through a single-pass copper coil heat exchanger, and in practice the thermal system is able to supply solar heated DHW for most of the year without any assistance from the gas water heater. “A Caleffi BX differential controller was selected because of its ability to charge the tank in upper and lower stages. This is accomplished via a Caleffi 3-way valve that diverts the flow to the tank from the water side of the heat exchanger. This helps the upper stage stay hotter at times of low solar harvest,” says Christy.
The radiant floor distribution system extracts heat from the storage tank until a low temperature setpoint is reached, at which point the gas-fired backup is enabled. “We have used Caleffi products since 2007, when they were introduced to us by Low Energy Systems in Denver. As a system designer I appreciate the extremely high level of quality of the products, as well as the comprehensive range of products available,” says Christy.
In addition to the solar controller, Christy relied on Caleffi components throughout the install, including four Caleffi thermostatic operator zone valves, an air separator, a backflow preventer and pressure reducing valve, a balancing valve, two thermostatic mixing valves, two 3-way zone valves, flowmeter, eight sweat union connectors—used for making plate heat exchanger connections—and a small automatic air vent. In fact, the radiant loop extracts heat from the storage through a second plate heat exchanger, and delivers it to the radiant slab through an assortment of Caleffi products — a thermostatic mixing valve, a balancing valve, a bypass valve and zone valves.
Challenges Met
One challenge in particular was the lack of a proper mechanical space for the system piping and components. Once the solar storage tank was in place, Christy realized that the space could be sheathed in plywood and used as a substrate for mounting components. However, we ended up needing all the available area of the tank exterior, which resulted in the system completely covering and wrapping around the tank.
Another challenge was the homeowners desire for solar collectors in a specific place, which was about 150’ away from the mechanical area. This resulted in a very long pipeline to and from the collectors, with potential flow and heat loss issues. These issues were resolved by using oversized and heavily insulated underground piping, as well as a larger collector loop pump.
Customer ‘Pipes’ In
This system has just gone through its third winter of operation and has been an outstanding success, with a glowing report from the homeowners and zero service calls. The homeowners report that they are comfortable all year round and only refill their 250-gallon propane tank once a year. The single tank supplies all the fuel for the heating and DHW backup, as well as a gas range and a gas fired clothes dryer, so the savings would seem to be significant. On future installations of this kind we will be installing a web-connected energy meter, which will enable us to collect enough system data to translate the daily energy harvest into the corresponding economic benefits.
“The homeowners have had nothing but good things to say about the system. We did not have a single callback on the system until a severe windstorm damaged some collector mounting hardware three years after the system was commissioned. When we checked system operation at that point, everything was still performing properly, with no leaks or control glitches,” says Christy.
Caleffi Excellence
According to Christy, Callefi’s commitment to innovation and constant improvement is extremely important, as is their commitment to education and training. The Coffee with Caleffi webinar series and their Idronics publications are a really valuable resource for the hydronics professional constantly looking to hone his/her skills.
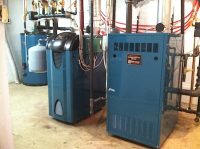
Long Island’s rich hydronic heritage can be seen in the houses that cover the island, as well as the plumbing and heating shops that serve them. Common is the moderately sized, turn-of-the-century house that’s seen addition after addition, with as many changes to the heating system. The family-owned hydronic shops run by passionate “wet-heads” continue Read more
Long Island’s rich hydronic heritage can be seen in the houses that cover the island, as well as the plumbing and heating shops that serve them. Common is the moderately sized, turn-of-the-century house that’s seen addition after addition, with as many changes to the heating system. The family-owned hydronic shops run by passionate “wet-heads” continue to leave their mark on the heating landscape.
Hunter Botto will be the first to attest to this. He and his brother, Roger, are third generation owners of Botto Bros. P&H, in Hicksville, NY. Their grandfather started the company in 1937, and they purchased ownership in the ’80s. Today, it’s a 10-person, multi-faceted firm that’s commercially and residentially focused. Plumbing and heating is their bread and butter, but kitchen and bath remodels and generator installations keep them busy year-round.
“One thing we’ve found is that diversifying helps build a bigger network of clients,” said Hunter. “We’ll land a remodeling job, and later in the year they’ll call us back to service a boiler or install a generator.”
In early February, Botto technicians were completing a generator installation when the owner asked them to check their radiant heating, and if a gas $1,400 gas bill was normal for a 3,500-square-foot home in January. When they stepped into the home’s mechanical room, what they found was so bizarre that they texted Hunter a bunch of photos.
Steam to radiant disaster
The circa-1910 house had been expanded and remodeled a number of times, with the heating system constantly gaining complexity. The original cast-iron steam radiation was accompanied by a jumble of air handlers and two different in-floor systems, none of which operated properly. The floor didn’t heat well, and the two-pipe steam system was banging. Oddly enough, the entire system was served by one oversized steam boiler.

A Burnham Independence supplies steam to cast-iron radiators, while an ES2 heats in-floor zones and DHW via a Burnham Alliance sidearm tank.
“I had to check it out myself,” said Hunter. “The boiler – which was 20 years old – was twice the size it needed to be. There was no proper equalizer; the four-inch header went right into the boiler, and three, two-inch supplies Teed off the big main. But it gets better.”
“Instead supplying DHW, the steam boiler’s internal coil was piped out to a 30-gallon buffer tank – which was just an old indirect-fired water heater. A circulator moved water from the tank to two radiant supply manifolds; one which supplied PEX under the marble kitchen floor, another for a staple-up zone in the dining room. The PEX didn’t receive the flow or temperature it needed. DHW was supplied by an old gas-fired water heater, and an upstairs den was heated by a single gas-fired air handler.”

Because the home uses both water and steam heating elements, Botto Brothers used two boiler to share the load.
During Hunter’s visit, the homeowner decided she wanted to lower her fuel bills and restore heating function by replacing the system. To hold her over for a few weeks until they could design and install a new system, Hunter de-rated the existing boiler to 50 percent of its 300,000 BTUH capacity. He then completed a heat load calculation in the rooms with radiant heat, and measured the radiators.
Share the load
“Instead of converting the radiators to water, we decided to divide the load between a new steam boiler and a new water boiler,” said Hunter. “We started on February 17th and finished five days later. The homeowner headed to Costa Rica during the process, which made life easier for us.”
Once the old boiler was removed, Botto Bros technicians Mike Depaulis, Bryan Scheafer and Brian Single installed a 105 MBH, natural gas-fired Burnham ES2 water boiler. The unit now supplies DHW via a 50-gallon, Burnham Alliance indirect-fired water heater, and working heat for the in-floor system.
“The ES2 is a real workhorse,” said Hunter. “Efficient, easy to install, and ridiculously dependable. What else do you want from a boiler?” Updating the radiant system included the addition of a pump; one for each manifold. Mixing valves are now used to temper down the 180°F supply temperature. The kitchen supply temperature averages 115°F, while the dining room – with wood floors – requires 140°F.
After the water side was squared away, they turned their attention to the radiators. Any air vents were removed, and supply valves were replaced. Next to the ES2, a 140 MBH Burnham Independence was installed for the 310 square feet of connected radiation.
“We couldn’t promise the owner of this job tropical weather upon her return, but a comfortable house and a lower heating bill were a given. The project even qualified for a 900.00 dollar rebate from National Grid, the local utility,” said Hunter. “
Worthwhile affiliations
Hunter is a 15-year PHCC member who has served as local and state president, and has been on the National PHCC Board of Directors. Currently, he serves as the local Zone Director.
“PHCC has allowed me to have open communications with contractors from all around the country,” said Hunter. “Over the years, their guidance and recommendations have proven an invaluable asset to have.”
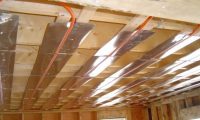
Radiant cooling has been utilized in commercial cooling settings for more than 20 years. A very active, very large airport — Suvarnabhumi International Airport in Thailand — has been successfully using radiant cooling for two decades. Radiant cooling works in much the same way that radiant heating works. Most people who have basements have experienced Read more
Radiant cooling has been utilized in commercial cooling settings for more than 20 years. A very active, very large airport — Suvarnabhumi International Airport in Thailand — has been successfully using radiant cooling for two decades. Radiant cooling works in much the same way that radiant heating works. Most people who have basements have experienced radiant cooling without even being aware of it. In older homes without concrete wall insulation, the ground temperatures below grade dictate the Mean Radiant Temperature (MRT) in a basement setting. When a person walks from upstairs to down into the basement, the body’s sensors sense this lower MRT, and it “feels” cooler than the upper floors, even though the air temperature is nearly the same.
The three major environmental factors that dictate human comfort are MRT, which is the average surface temperature of the surfaces surrounding our bodies, relative humidity, and air temperature. Maintaining all three of these in a radiant cooling application is different than what is required when using a conventional air conditioning system. By lowering the mean radiant temperature and controlling the humidity, good human comfort is achievable for cooling at air temperatures that are significantly higher than we typically see with a conventional air conditioning system. This is because RT is one of the primary factors that dictates human comfort. The air temperature and relative humidity can be perfect, but if the MRT is off in one direction or another most people will be uncomfortable. Control of the relative humidity in a radiantly cooled environment is not just a good idea, it is mandatory in order to avoid the production of condensation on the surfaces of the radiant panel.
Residentially speaking, this requires the use of window and door proximity switches, and if any of these openings are left open no radiant cooling is provided. If humidity is controlled and maintained between 30% and 60%, and the chilled water temperatures are kept between 50 and 70 degrees F, then condensation production is not possible under these conditions. The use of a dew point controller is also a minimum requirement whenever radiant cooling is to be employed.
In commercial settings, rarely are windows operable and doors are always on auto closers, so the production of condensation on the radiant sources is not an issue where humidity is being controlled between 30% and 60%.
In certain areas of the country, it is entirely possible to use the building’s irrigation system during the summer months to provide a coolth source for augmenting the cooling of a given structure utilizing radiant cooling. This will obviously require the addition of heat exchangers and pumps, but still represents a free source of cooling. Another potential source that is being exploited is “Night Sky Re-radiation Cooling.” This requires the placement of unglazed solar collectors on the roof of a dwelling to reject built up heat into the night sky. I have personally witnessed collector absorber temperatures that are as much as 20 degrees F. cooler than the lowest ambient temperature seen for the same period of time.
And, of course, there is always ground source heat pump systems, which have a proven track record of efficiency and reliability. There are some new variations of this age old system bubbling to the surface, and they are showing a huge potential as it pertains to radiant heating and cooling applications. (Thermal Battery Storage systems, for instance.) It is also entirely possible to utilize the ground source vertical bore fields as a cooling source under the right conditions without the need to fire a compressor. Remember, the typical approach temperatures for a radiant panel vary between 50 and 70 degrees F.
Having too much or too little much humidity will also significantly sway the human comfort factors, regardless of what is happening with the MRT and air temperature. In areas of high humidity, it is necessary to maintain the relative humidity between 30% and 60%. This not only provides better human comfort, but also has to do with the control of microbial bacteria, dust mites and preservation of fine wood products. In humid climates, it will be necessary to dry the air out. For make up air units, a method known as DOAS (Dedicated Outdoor Air Systems) is used to wring the humidity out of the incoming air before introducing it into the controlled environment. Internally generated humidity is controlled and removed through the use of refrigerant-based direct expansion dehumidification systems, where the room air is first run across an evaporator coil to remove excess humidity and then the condenser reheats the stream of air. This avoids overcooling the air and creating “cold 70” conditions.
Conversely, in areas with low humidity it may be necessary to introduce humidity into the controlled environment. This can be done with the use of direct evaporative cooling, or direct humidity injection systems. There are even some newer classifications of indirect evaporative cooling systems known as Maisotsenko M-Cycle cooling systems. This type of system uses an indirect heat exchanger to avoid the possible generation of humidity into the conditioned air stream, which in some cases can cause discomfort or mugginess.
In conventionally “air conditioned” systems, there is the need to not only cool down the air, but also to control the relative humidity within the controlled space. At times, the demand for air dehumidification causes the air conditioning system to over cool the air, resulting in more complaints about the air being excessively cold.
In a radiantly cooled controlled environment, the majority of the sensible cooling demand is handled by the control of the MRT surfaces. By allowing the radiant cooling system to handle the majority of the sensible demand, the amount of air movement required to handle the latent (humidity control) demand is significantly smaller. This can result in a significant decrease in cooling energy, resulting in energy savings of 50% or more depending upon the application.
It also opens up more “off peak” ice generation/storage options because the approach temperatures of the water used in radiant cooling systems typically vary between 50 and 70 degrees F. By shifting the electrical and mechanical energy consumption to “off peak” periods, additional monetary savings can be achieved.
Another area that is receiving major attention is the use and application of Phase Change Materials. This method is incorporated into the structure of the building, and in some cases uses free nighttime cooling or off peak electricity to “freeze” the phase change materials. As the materials absorb heat energy, they go through the reverse phase change and “melt,” absorbing significant amounts of thermal energy. They can reduce peak loading by as much as 30% in a hot climate. Although they do not and cannot address the latent energy loads, they do a fantastic job of addressing the sensible loads, which are the biggest load in most commercial buildings. These compounds can be custom tailored to operate at any temperature that is normally used to maintain comfort in a given structure.
Mark Eatherton is the executive director for the Radiant Professionals Alliance (RPA).
References:
http://www.coolerado.com/company/faq/ Indirect evaporative coolers
http://www.phasechange.com/index.php/en/ Phase Change Materials
http://www.solarthermalbiz.com/archives/3710 Night Sky Radiational cooling
http://www.healthyheating.com/Page%2055/Page_55_i_cooling_eq.htm#.VJGsiCcBg Radiant Cooling
http://www.healthyheating.com/solutions.htm#.VJIX7CcBg Comfort Calculator
http://www.aeecenter.org/files/newsletters/ESMS/Sastry.pdf Side by side comparison of radiant cooling versus regular cooling
http://thermalbatterysystems.com/2013/03/22/seasonal-thermal-energy-storage/#.VJIbWCcBg Thermal Battery Storage Systems Inc.
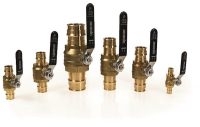
Uponor North America (Uponor) is now offering a new, more cost-effective ball valve option for radiant heating/cooling and hydronic piping applications. These code-listed, commercial-grade, PEX-to-PEX, full-port ball valves are available in ½” to 2″ sizes and are appropriate for non-potable PEX piping applications. The valves are available on-demand in CAD and BIM design files Read more
Uponor North America (Uponor) is now offering a new, more cost-effective ball valve option for radiant heating/cooling and hydronic piping applications. These code-listed, commercial-grade, PEX-to-PEX, full-port ball valves are available in ½” to 2″ sizes and are appropriate for non-potable PEX piping applications.

The valves are available on-demand in CAD and BIM design files via www.uponorengineering.com or www.arcat.com to make designing and specifying fast and easy. Additionally, they are listed to ANSI/NSF 14 and cNSFus-rfh and tested to ASTM F877, ASTM F1960, CSA B137.5 and NSF 359, allowing professionals the flexibility to add a reliable, code-listed valve anywhere in a commercial radiant heating/cooling or hydronic piping system.
Stem Extension Valves
“We are continuing to see growth in our indoor climate business, especially with hydronic piping applications,” says Mark Hudoba, director, Heating and Cooling at Uponor. “Offering these cost-effective, code-listed valves provides professionals in the industry with a trusted, reliable product for hydronic piping as well as radiant heating and cooling applications.”
The valves, which are compatible with systems containing up to 50 percent propylene glycol, feature blow-out-proof stems and are available with stem extension kits to accommodate up to 2″ of insulation in insulated piping applications. Additionally, both ends of the valves are manufactured with Uponor’s proven ProPEX® fitting system for expansion connections that cannot be dry fit and hold tight with up to 1,000 pounds of radial force.