By Greg Hughes Three boiler types loom large among conventional (non-condensing) commercial water boilers used for process or space heat, with input sizes of 400 MBH and up: those with cast iron sectional, fire-tube and water-tube heat exchangers. For a variety of reasons, the latter two have been most prevalent in the commercial process heating Read more
Uncategorized
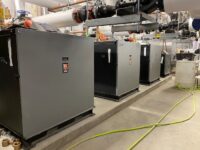
By Greg Hughes
Three boiler types loom large among conventional (non-condensing) commercial water boilers used for process or space heat, with input sizes of 400 MBH and up: those with cast iron sectional, fire-tube and water-tube heat exchangers.
For a variety of reasons, the latter two have been most prevalent in the commercial process heating market. Advantages include relatively compact size, lower standby heat loss, and the speed with which heat can be generated and delivered into distribution piping.
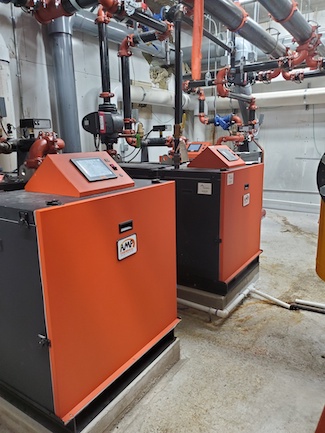
A Thermal Solutions AMP water-tube boiler is rated at 97% efficient. The stainless steel, modulating-condensing boiler line offers a size range of 1,000-4,000 MBH.
First out of the gate for a wide range of uses was the fire-tube boiler—with early design dating back centuries. Hollywood gave great prominence to horizontal fire-tube boilers, though few producers, actors or moviegoers were aware of it. Every time a steam locomotive—aka the iron horse—blew its whistle or raced across the great plains, an uncelebrated fire-tube boiler was doing its part.
Still today, fire-tube boilers offer a wide range of uses. Within these boilers, fire tubes are immersed in water; hot flue gases produced by the combustion chamber flow inside them. The hot flue gases transfer their heat to the outside water through the conduction.
Water-tube boiler designs, introduced later, essentially invert the fire-tube boiler construct: water is contained within the boiler’s internal tubes.
Water-tube advantages
In water-tube boilers, combustion occurs within the shell that surrounds the tubes, forcing combusted gas over the water tubes for exceptionally fast, efficient heat transfer.
Water-tube boilers offer quick startup and response time to changing conditions with very little standby loss. By design, comparatively little water passes through the heat exchanger; this translates into a smaller footprint and broader range of capabilities and output ranges.
“Their ability to make steam, or hot water, very rapidly, from a cold start, and without damaging the boiler is a beneficial asset,” said Lane Blackwell, Sales Engineer, Service, for Peru, Ind.-based Thornton & Associates,. Inc., a manufacturer’s rep firm. “This is valuable in applications where the systems aren’t running 24/7.”
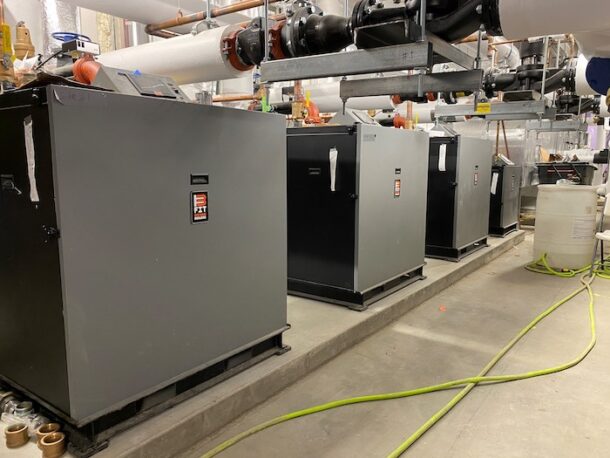
Bryan Boilers’ BFIT commercial condensing water-tube boiler series is a stainless steel, modulating-condensing boiler line with ranges from 1,000-4,000 MBH with optional racking system. Image courtesy of Bryan Boilers.
Because the burner in a water-tube boiler is located centrally, most water-tube designs provide higher temperature outputs and higher operational pressures than fire-tub boilers—key advantages for process heating application. Another advantage to the design of these systems is that, as a result of the requirement for water to flow continuously during operation, hot spots in the heat exchanger don’t threaten the operation or lifespan of the boiler.
Water-tube heat exchangers also operate at higher pressures, a capability that can—for steam-producing systems—produce saturated or superheated steam depending on the design and application they’re required for.
Blackwell also points to the advantage of water-tube maintenance, “Or, rather, lack of it. A surprisingly high number of water-tube systems may go several years without more than occasional attention to the water quality [within them], he said. “And, if there would be a need to replace individual tubes, that can be accomplished with hand tools; no rolling or welding. It’s not uncommon for a well-maintained water-tube boiler to last 40+ plus years with little maintenance.”
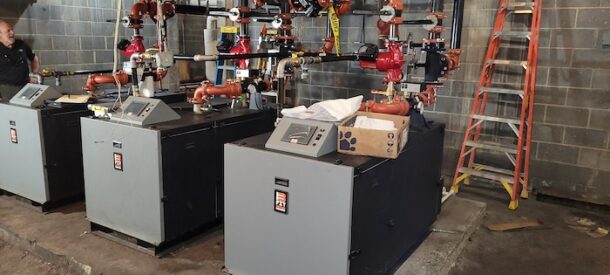
– Bryan Boilers’ BFIT commercial condensing water-tube boiler series is a stainless steel, modulating-condensing boiler line with ranges from 1,000-4,000 MBH with optional racking system. Image courtesy of Bryan Boilers.
“A few years ago, we specified two non-condensing water-tube boilers for a high school expansion project in Cass County [IN],” added Blackwell. “The boilers were 72 and 50 HP in size, and it wasn’t long before facility managers found that they could provide heat for the rest of the school with them, so they decommissioned two old, enormous—and way oversized—firetube boilers. The following year, they added another 100 HP water-tube system and, within a few years, they verified 30 to 40 percent annual fuel savings. I could reel-off countless instances where water-tube boilers have exceeded expectation.”
Water-tube systems are designed to work with high-ash fuels that, when combined with soot blowers, typically meet environmental regulations. This also means that they’re well-suited for biomass applications and waste-to-energy plants.
The primary factor that determines heat transfer is the heat transfer coefficient, based on the transfer fluid’s flow pattern, characteristics and chemistry (including density, conductivity and viscosity), geometry of the flow passage, and surface conditions. Of these factors, the most important to thermal efficiency in a water-tube boiler is flow through the water tubes and the fluid’s velocity and density. When all of these variables are optimal, water-tube boilers provide exceptionally reliable operation, while offering performance and efficiency that is difficult to match with any other heat exchanger design.
For these and other reasons, water-tube boilers are the equipment of choice for many industrial process applications. Their ability—in a steam boiler configuration—to handle greater pressures and very high temperatures provides superior steam generation in the millions of pounds/hr.
Caveats
Most advantages come with a counterbalance; water-tube boilers are no exception.
The initial cost for a water-tube boiler is usually higher than that of a fire-tube boiler of similar capacity. And, depending on size, some water-tube boilers can be assembled on site, which can add to the cost and the time required for installation.
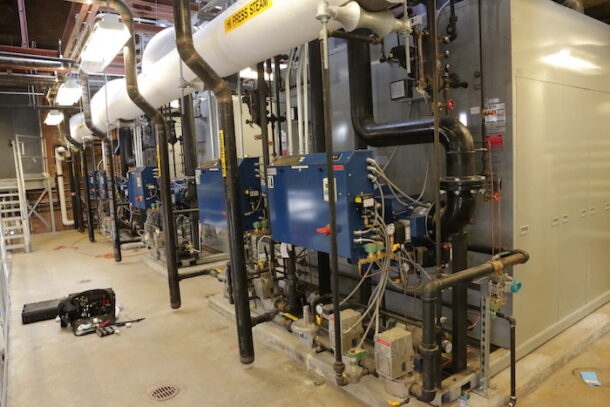
Bryan’s RV600 flexible water-tube steam boilers are a great fit for many commercial heat or process steam application. The systems offer 3,500,000 to 8,000,000 BTUH with forced-draft gas, oil or dual fuel. Image courtesy of Bryan Boilers.
By design, the concern of heat transfer fouling—typically in the form of accumulated mineral scale—is heightened. For that reason, fill-water quality and the steady monitoring and maintenance of water chemistry are essential to peak operation.
The accumulation of scale is by no means specific only to the water-tube design. Scale can accumulate faster because of the water-tube boiler’s lower water mass, but it’s still a concern across all heat exchanger types. “But, reduced water volume also equates to savings on chemical treatment,” added Blackwell.
Finally, the reduced volume of water affects the water-tube boiler’s ability to meet the call for sudden changes in heat demand. This shortcoming is often remedied by the addition of an indirect water storage tank.
Fire-tube advantages
Advantages include their simple construction and the ability to easily meet rapid fluctuations in the need for heat. As a lower cost alternative to water-tube boilers, they’re often used for smaller commercial or industrial facilities with lower operating pressures.
Fire-tube boilers are designed with water in the unit’s main vessel, achieving higher mass. Because of their higher water volume, system design also offers the benefit of a less urgent need to maintain tight control of water quality. If water quality deteriorates and isn’t corrected quickly, there’s less chance— when compared to water-tube technology—that system performance will be affected.
Another advantage to fire-tube boilers may be lower upfront cost. “However, said Blackwell, “In our market, there’s very little, if any, difference in pricing.”
Caveats
A fire-tube boiler’s higher water volume and lower flow rates also mean that they may offer less efficient heat transfer. Likewise, the greater water volume requires a longer wait for system start-up, and may also challenge the boiler’s ability to meet demand for constant water flow—and heat transfer—at peak conditions. Standby losses are greater because of the boiler’s higher volume of water.
The main disadvantage of fire-tube boilers is that they tend to have smaller capacities and can’t handle internal pressures over 250 psig (the steam capacity range of fire-tube steam boilers is approximately 5,000 to 75,000 pounds/hr.) Or, if configured as a hot water boiler, hot water capacity is between 2 million to 100 million BTUs.
Traditional, horizontal fire-tube steam boilers may offer a capacity as low as 690 pph—pounds (of steam) per hour. Traditional fire-tube steam boilers in a vertical configuration will go smaller—offering as little as 207 pph, for example.
Boiler Safety—be warned
Operationally, water-tube boilers are known to be safer than fire-tube systems. This is because of the much greater volume of water held within fire-tube boilers—containing as much as 10 times the volume of a water-tube boiler of similar capacity.
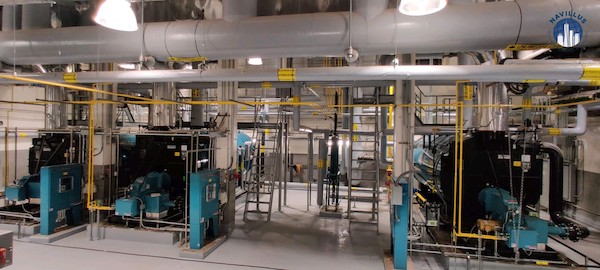
Burnham Commercial Boilers offers a convenient solution with efficient, easily portable, mobile boilers. Image courtesy of Burnham Commercial Boilers
When fire-tube boilers are inadvertently operated with low water volume, very dangerous risks can develop. Initially, the metal in the boiler warps and contracts. Then, if cold fill-water enters the boiler in a hot, low-water condition, the metal could rapidly expand, causing an explosion.
Should a similar scenario take place in a water-tube boiler with lower internal water volume, an explosion would be much less severe. In most instances— should fill-water enter a hot water-tube boiler with an insufficient fluid level— conditions would likely lead to metal fatigue, a crack, and leakage.
Service and maintenance
Some boiler designs are built to facilitate ease of service and maintenance. The assumption, however, is that a newly-installed boiler is ready for the rigors of duty, 24-7-365. Yet, all mechanical equipment is not created equal. Service and maintenance work ideally happens systematically to maintain optimal performance and efficiency—not to deal with challenges that arise as a result of faulty or compromised design.
Commercial boilers should be designed to ensure long-term durability and optimal performance. Ideally, the burner is mounted front and center, fully accessible and serviceable. Removable panels around the boiler should provide access to the burner chamber and entire heat exchanger. There should be no need to disconnect blowers or gas piping.
Commercial Condensing Systems
As with all technology, improvements emerge to enhance operation, durability or efficiency. The emergence of condensing capability—often going hand-in-hand with “turn-down” (or modulation, offering very efficient, partial firing)— are the most substantial enrichments to boiler systems in decades.
Condensing boilers are based on a remarkably simple concept. They achieve higher efficiencies by condensing the flue gasses. In contrast—in a conventional boiler, latent heat contained in the flue gas escapes through the flue vent. They’re also quite effective at reducing NOx, COx and other harmful emissions.
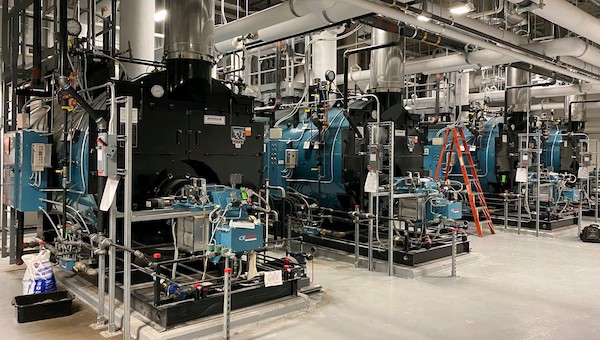
Burnham Commercial Boilers offers a convenient solution with efficient, easily portable, mobile boilers. Image courtesy of Burnham Commercial Boilers
Modulating condensing boilers (AKA “mod-con” boilers) earned “greatest achievement” recognition as a result of their dramatic contribution—pushing fuel efficiency from 80 percent for non-condensing boilers, and up into the 90+ percent range for mod-con systems. Condensing water-tube boilers achieve efficiencies of up to 98 percent, higher than most condensing fire-tube systems—a result of their better heat transfer. With modulation, they provide a range of firing rates to match the variable heating load of the building.
However, mod-con boiler efficiency depends on the temperature of the water returning to the boiler. The lower the return water temperature, the higher the efficiency. Low boiler return water temperature depends on the overall boiler system design, not just the boiler.
Condensing boilers cost 40 to 50 percent more, on average, than conventional systems. However, the difference in cost is typically recovered in four months to four years, depending on a wide range of variables. Substantial cost-saving incentives may apply.After the initial cost recovery period, the fuel savings are quite significant over the life of the boiler.
There are a few disadvantages. For instance, one fire-tube boiler design change involved the arrangement of internal tubing from a horizontal format, to vertical. The revision was warmly welcomed by facility owners and installers alike because their now-smaller size permitted movement through a standard door frame. As a result, the products of combustion and condensate were redirected: rather than gradually absorbing heat as flue gas passes through tubes, the contemporary vertical fire-tube burner sits inches away, forcing heat directly on the tube sheet, welds, and tube tops. All materials expand and contract as they’re heated and cooled, and these internal components of the vertical fire-tube boiler are no exception. The design tends to concentrate too much heat on metal components.
Cleanings and reparability
If a condensing boiler’s panels are easily removed, providing complete access to the entire heat exchanger, byproducts of combustion can be easily removed with a service brush. This is an important facet to maintaining a boiler’s original high-efficiency rating.
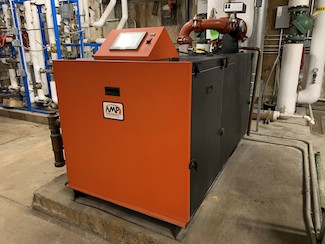
A Thermal Solutions AMP water-tube boiler is rated at 97% efficient. The stainless steel, modulating-condensing boiler line offers a size range of 1,000-4,000 MBH.
Should repair work be required, all components of the heat exchanger should be easily accessible for service or replacement—including even the possibility of changing one or more internal tubes in the field.
With properly isolated equipment, service work could and should be completed within hours, not days or weeks.
Systems that offer the greatest resistance to cleaning are those with tight, top access and—when opened—may have many welded tubes. Those that do typically require entirely new heat exchangers, sometimes costing as much as 60 percent of the original install.
Knockdown rewards
Knockdown condensing boilers were, for good reason, greeted enthusiastically by the commercial market. Some of these systems use no welds in securing tubing to the header.
The “knockdown” moniker stems from the ability to assemble or disassemble a boiler of any size with relative ease and precise repeatability. The systems arrive on jobsites, similar to old cast iron sectional boilers, or partially assembled based on space requirements.
Even elevator weight constraints pose no challenge to getting the boilers in place. If there’s a need to maximize mechanical room space, some systems are available with reverse construction models to optimize clearance space between units or to be placed side by side, to be serviced from outside.
Greg Hughes is the Internal Sales Manager, Thermal Solutions and Burnham Commercial. He can be reached at ghughes@heatingsolutionssales.com
Additional sources:
Jim Knauss – jknauss@burnhamcommercial.com (retired but now consulting) Engineer for Burnham Commercial (firetube merits)
Joe Tinney – jtinney@heatingsolutionssales.com Internal Sales Manager for Bryan Boilers (watertube merits)
Rick Constantino (rconstantino@bresales.com) – Owner/COO Boileroom Equipment Company
Theodore (Ted) Dreyer (TDreyer@WHGardiner.com) – Sales for Gardiner
Healthy growth in building construction offsets infrastructure weakness Total construction starts rose 3% in April to a seasonally adjusted annual rate of $945.8 billion, according to Dodge Construction Network. Nonresidential building starts rose 6% and residential starts increased by 4%, while nonbuilding starts fell 4%. Year-to-date, total construction was 6% higher in the first four Read more
Healthy growth in building construction offsets infrastructure weakness
Total construction starts rose 3% in April to a seasonally adjusted annual rate of $945.8 billion, according to Dodge Construction Network. Nonresidential building starts rose 6% and residential starts increased by 4%, while nonbuilding starts fell 4%.
Year-to-date, total construction was 6% higher in the first four months of 2022 compared to the same period of 2021. Nonresidential building starts rose 19%, residential starts gained 3%, while nonbuilding starts were 2% lower. For the 12 months ending April 2022, total construction starts were 12% above the 12 months ending April 2021. Nonresidential starts were 24% higher, residential starts gained 11% and nonbuilding starts were down 1%.
“The construction sector is seemingly shrugging off the fear of higher interest rates and a potential recession,” said Richard Branch, chief economist for Dodge Construction Network. “Many building sectors have made the turn from weakness to recovery as underlying economic growth and hiring are solid. With the pipeline of projects in planning continuing to expand, this trend should continue in the months to come. However, the concern that the Federal Reserve will force the U.S. into recession later this year may thwart the momentum in construction starts. While recession is not our baseline forecast, it can not be fully discounted.”

Below is the breakdown for construction starts:
- Nonbuilding construction starts fell 4% in April to a seasonally adjusted annual rate of $187.1 billion. Starts in the environmental public works category rose 8%, while utility/gas plant starts moved 10% higher. Starts for highway and bridge projects fell 14% and miscellaneous nonbuilding starts dropped 2% during the month. Through the first four months of the year, total nonbuilding starts were 2% lower than in 2021. Highway and bridge starts gained 28% through four months and environmental public works projects were 2% higher. At the same time, miscellaneous nonbuilding and utility/gas plants starts dropped 37% and 39% (respectively) through four months.
For the 12 months ending April 2022, total nonbuilding starts were 1% lower than in the 12 months ending April 2021. Environmental public works starts were up 10%, and street/bridge starts gained 6%. Miscellaneous nonbuilding starts were 33% lower and utility/gas plant starts were down 3%.
The largest nonbuilding projects to break ground in April were the $531 million Gross Reservoir Expansion in Golden, CO, the $450 million Seven Cowboy wind project in Washita and Kiowa counties, OK, and the $338 million Great Pathfinder wind farm in Boone and Hamilton counties, IA.
- Nonresidential building starts rose 6% in April to a seasonally adjusted annual rate of $295.9 billion. In April, commercial starts rose 2%, institutional starts gained 8% and manufacturing starts increased 16%. Through the first four months of 2022, nonresidential building starts were 19% higher than during the first four months of 2021. Commercial starts advanced 11% and institutional starts 1%, while manufacturing starts soared 189% on a year-to-date basis.
For the 12 months ending April 2022, nonresidential building starts were 24% higher than in the 12 months ending April 2021. Commercial starts grew 19%, institutional starts rose 11%, and manufacturing starts swelled 163% on a 12-month rolling sum basis.
The largest nonresidential building projects to break ground in April were the $500 million Caesar Virginia hotel and casino in Danville, VA, the $430 million Aggie Square Life science building in Sacramento, CA, and the $400 million The Rose Gaming Resort in Dumfries, VA.
- Residential building starts rose 4% in April to a seasonally adjusted annual rate of $462.9 billion. Single family starts gained 1% and multifamily starts rose 13%. Through the first four months of 2022, residential starts were 3% higher than in the first four months of 2021. Multifamily starts were up 16%, while single family housing slipped 2%.
For the 12 months ending April 2022, residential starts improved 11% from the same period ending March 2021. Single family starts were 6% higher and multifamily starts were 27% stronger on a 12-month rolling sum basis.
The largest multifamily structures to break ground in April were the $420 million 2-10 54th Avenue apartments in Long Island City, NY, the $400 million Civic Square condominiums in Seattle, WA, and a $300 million mixed-use building in Long Island City, NY.
Regionally, total construction starts in April rose in the Northeast, South Atlantic, and South Central regions, but fell in the Midwest and West.
WAVE will help Sloan improve and credibly report water stewardship performance The Water Council is pleased to announce Sloan, a global manufacturer of commercial plumbing systems based in Franklin Park, Ill., has signed onto The Water Council’s WAVE program. Sloan is the first company to initiate the program since its formal launch in February. WAVE Read more
WAVE will help Sloan improve and credibly report water stewardship performance
The Water Council is pleased to announce Sloan, a global manufacturer of commercial plumbing systems based in Franklin Park, Ill., has signed onto The Water Council’s WAVE program.
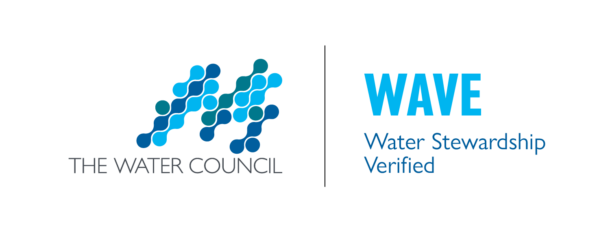
Sloan is the first company to initiate the program since its formal launch in February. WAVE will help Sloan improve its enterprise-level water stewardship performance and public reporting, concluding with independent verification of its progress.
“Water is earth’s most precious resource, and it’s important to understand and prioritize our water risks and shared water challenges in order to become better stewards,” said Patrick Boyle, Sloan director of sustainability. “Sloan’s historic partnership with The Water Council’s WAVE program provides us with an exciting opportunity to lead by example by communicating our corporate water stewardship efforts.”
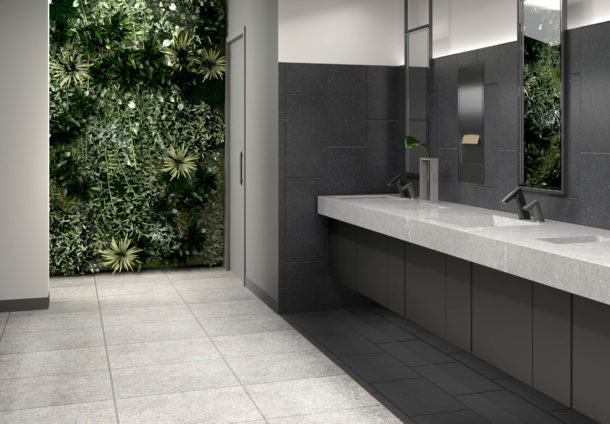
The Water Council, an internationally acclaimed nonprofit dedicated to freshwater innovation, has helped companies of all sizes and industries improve water stewardship. It created the WAVE program to help businesses anywhere in the world address water on an enterprise level, moving beyond non-contextual water management targets to develop meaningful strategies, goals and actions.
Through WAVE, participating companies learn about their water uses, impacts and risks; approve a corporate water stewardship policy; prioritize sites where water-related risks can be mitigated; and communicate a corporate action plan, goals and timeline. Their efforts are then independently verified by SCS Global Services, an international leader in third-party sustainability verification. Verified companies can confidently state they are credibly and strategically addressing water challenges and opportunities where it matters most.
“Sloan is a market leader and global influencer when it comes to sustainability, and we’re proud to welcome them as the first official WAVE client,” said Dean Amhaus, The Water Council president and CEO. “We designed WAVE to benefit a variety of companies, whether you’re just starting on your water stewardship journey or already addressing water risks like Sloan.”
As a water technology company, Sloan has prioritized water stewardship and sustainability since its founding in 1906. The company joined The Water Council in 2011, and in 2021, it certified its Franklin Park headquarters to the International Water Stewardship Standard. Participation in WAVE will help Sloan expand on that work and strategically address water stewardship across all its sites and its supply chain.
Prior to WAVE’s launch in February, The Water Council pilot tested the program with A. O. Smith Corporation, Badger Meter, Nutrien and Watts Water Technologies.
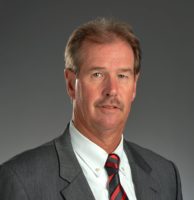
A. O. Smith Corporation (NYSE: AOS) announced today that Eddie Goodwin, senior vice president, president of Lochinvar, will retire July 1, and Stephen O’Brien, chief operating officer, has been named the successor. “Since joining the company over 40 years ago, Eddie’s vast experience and steadfast leadership has helped shape Lochinvar into the industry-leading, high efficiency boiler and Read more
A. O. Smith Corporation (NYSE: AOS) announced today that Eddie Goodwin, senior vice president, president of Lochinvar, will retire July 1, and Stephen O’Brien, chief operating officer, has been named the successor.
“Since joining the company over 40 years ago, Eddie’s vast experience and steadfast leadership has helped shape Lochinvar into the industry-leading, high efficiency boiler and water heater manufacturer it is today,” said Kevin Wheeler, chairman, president and CEO. “He has built a strong team committed to designing, manufacturing and selling high quality, innovative products that meet our customer’s needs. We thank him for his vision and commitment to our customers, our employees and the A. O. Smith values over the past four decades.”
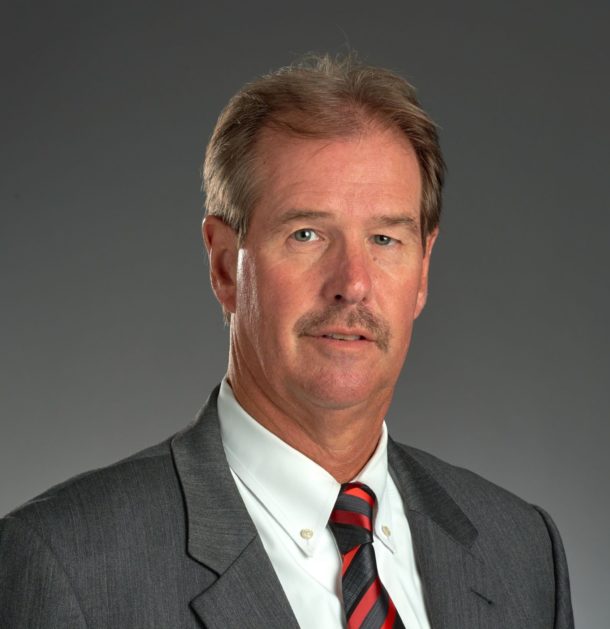
Eddie Goodwin
In his new role, O’Brien will build on the strong foundation Goodwin and his team have established, by implementing the strategic vision for the organization and further expanding Lochinvar’s innovative product lines. O’Brien has served as chief operating officer for Lochinvar since August of 2021 and is uniquely qualified to assume the role of president going forward. O’Brien joined Lochinvar from Mitsubishi Electric Trane HVAC US (METUS) and prior to that, worked for A. O. Smith Electrical Products Company for 14 years before the company was sold to Regal Beloit Corporation. He holds an MBA from the University of Dayton in Ohio and a bachelor’s degree in mathematics from State University of New York at Potsdam.

Stephen O’Brien
“With his extensive experience in the HVAC industry, his strong leadership skills and focus on customer satisfaction, Steve is the ideal person to lead our Lochinvar business unit going forward,” Wheeler added. “I am confident the transition will be seamless, and Steve’s extensive background and business development skills will further strengthen Lochinvar’s channel partnerships and our presence in the market.”
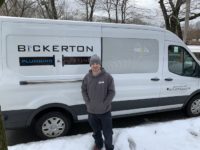
It’s been quite the start to 2022 for Ryan Bickerton, owner/operator of Bickerton Plumbing and Heating LLC, Boston. Recently recovered from COVID, his phone hasn’t stopped ringing. He’s been busy, and that’s a good thing. Mostly specializing in high-end renovations, old houses in the historic areas of Boston and high-efficiency boilers, Bickerton has run his Read more
It’s been quite the start to 2022 for Ryan Bickerton, owner/operator of Bickerton Plumbing and Heating LLC, Boston. Recently recovered from COVID, his phone hasn’t stopped ringing. He’s been busy, and that’s a good thing.
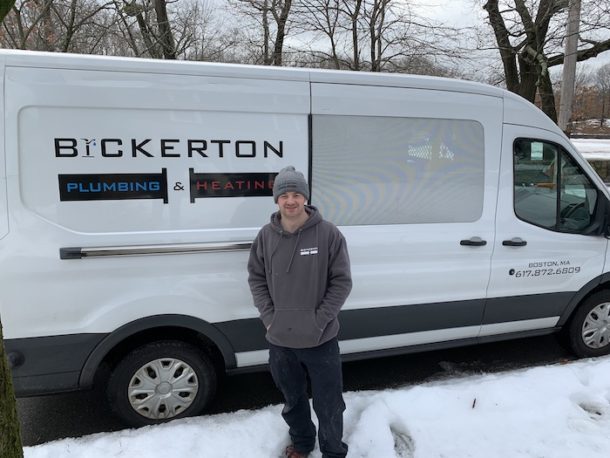
Mostly specializing in high-end renovations, old houses in the historic areas of Boston and high-efficiency boilers, Bickerton has run his own company since 2014. At the age of 18, Bickerton started into plumbing, working for a larger residential company doing large multi-unit buildings where he worked for 2 1/2 years before moving to a smaller company doing mainly commercial work.
The itch started for Bickerton when he started in construction over the summers during high school, working for a roofing company and a general contractor, basically doing whatever was needed on a job site. “I tried helping whoever needed to be helped on the site—plumbers, electricians, carpenters—cleaning up, making coffee runs, etc. I remember those summers working for the GC and I enjoyed helping the plumbers more than anything else. I realized I was falling in love with the industry, and the rest is history,” says Bickerton.
Nevertheless, Bickerton was encouraged to make an attempt at college even though he didn’t really want to; he gave it a shot anyway. He lasted less than a year and decided that was it. “For me, it was a waste of time and money,” says Bickerton. “My parents were okay with me leaving after giving it a valiant effort, but my father said ‘pick a trade because you’re not going to be sitting around here all day.’”
Bickerton recalls speaking to his father, and a few other people he knew who worked in the trades, and was pushed in the direction of electrical or plumbing mainly because, “you’ll never be looking for work.”
After obtaining his Journeyman Plumbing and Gas Fitting License in 2008, Bickerton completely shifted gears and joined the United States Marine Corps where he was deployed to Afghanistan. It was a difficult decision but joining the military was something Ryan had always wanted to do. In 2008, it was the right time. After six years of service with the Marines, Bickerton returned to plumbing and got his Master Plumbing and Gas Fitting License. “I started doing more and more side work until I landed a few bigger jobs that motivated me to leap into owning my own company. I haven’t look back since,” says Bickerton.
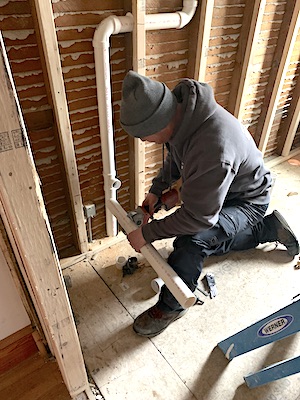
Part of that drive came from his biggest role model, his father, who worked most of his life in a power plant in South Boston as a general mechanic—he could pretty much fix anything and everything that needed fixing. “My father is the hardest working person I know. I remember as a young kid not seeing him for days at a time because he was getting home late and leaving early before we were awake. I knew he was out working hard taking overtime to provide for us. He could and would fix most things around the house. I remember one year our water heater went out on Thanksgiving and he took care of it by himself. I thought that was pretty cool, and still do,” says Bickerton.
As for Ryan, he never considered himself a role model, but he tries to conduct himself that way. Any chance he gets, he’ll speak highly of the trades. “If any young kids ask me about the trades, I do my best to steer them in the right direction and let them know it’s a very viable option. It’s a rewarding career choice, and college and white-collar work doesn’t have to be for everyone,” says Bickerton.

Bickerton does rough-ins to beautiful renovations.
Bickerton’s trade role model was his first foreman, Mike Sheehan, a plumber for 30+ years, his body broken from years of moving massive boilers and extra heavy cast-iron pipe. “But he still loved the trade. He taught me a lot of my early skills, and he would say that this trade has all the potential to do anything you want with it, which has really stuck with me to this day,” says Bickerton.
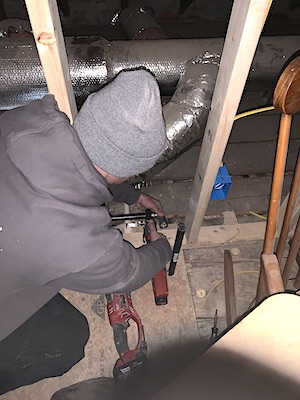
Bickerton’s go-to tool has been the ProPress/MegaPress. “Don’t get me wrong, I loved to solder and took great pride in having clean joints, and still think it’s a necessary skill to have, but the press system is a complete game changer.”
While respecting these two men’s work ethic, Bickerton knows that balancing work and family life is important. It’s probably his most difficult task, says Bickerton. “I’m usually out the door by 5 am and home around 5 pm, and the kids go to bed between 7:30-8 pm and then most nights I have to do estimates or invoices when they’re in bed so I don’t have as much ‘leisure time’ as I’d like. I try to make every second I’m home count.”
And the weekends are for family. Bickerton used to work every Saturday and even some Sundays. Lately, however, Ryan doesn’t work Sunday unless it’s a catastrophic emergency, and on Saturdays he tries to be done by 12 or sometimes not at all. “Like I said before, I love plumbing and working but I don’t think I’ll ever regret not working more and spending less time with my family so I try to best divide my time in the fairest manner possible.”
It’s clear that family time is most important. “In my spare time, more than anything, I enjoy hanging out with my wife and our children. My wife Micayla and I have been married for six years and our three kids are growing up fast. If I’m not working, I’m with them. They are starting to get into different activities, hockey, baseball, football, swimming, horseback riding, and I just enjoy every second of that. Even if it’s just hanging out and watching a movie, it’s never wasted time for me,” says Bickerton.
Perhaps family means a bit more to Bickerton because his daughter, Mallory, was diagnosed with a rare genetic disorder called Rubenstein Taybi Syndrome (RTS). In 2017, Ryan and Micayla, along with some close friends, started a non-profit organization called Mals Pals Foundation. “We have been very fortunate with Mallory. We live in the epicenter for healthcare; she has had an inclusive educational opportunity here in Boston and it helps that we are able to pay for anything and everything she has needed in order to thrive,” says Bickerton.
Mal’s Pals Foundation aims to ease the burden of other families who maybe are not as fortunate. The Bickertons raise awareness for rare diseases like RTS, and they help educate newly diagnosed families. “We are trying to make difference in other people’s lives even if it’s just a small one. You can check us out at malspalsfoundation.org.”
Mallory is now seven-years-old and doing well. “Initially, there were concerns, but honestly, I wouldn’t have it any other way,” says Bickerton.
Bickerton looks forward to going to work every day. “But the most rewarding to me is being able to sit back at the end of the day or at the end of a job and look at what I’ve done,” says Bickerton. “I like having something tangible, that I can look at and touch and say I did that, or I fixed that or I created that. Whether it’s fixing a leaking faucet, creating a bathroom where there wasn’t one before, plumbing a 5-unit building completely from scratch or providing someone with heat and hot water for the next 20-30 years. That’s pretty cool.”
In the end, Ryan really loves plumbing, even if he’s stressed out and jobs are behind, or he’s behind on paperwork, or he’s made a mistake and or redo something. “I still consider myself lucky to be doing what I love every day. And on those harder work days, I still get to come home to three beautiful children and a wife who loves me. Every time I walk in the door and they scream ‘DAD!’ all that stress lifts off instantly, and it’s all worth it.”