Pumps are mechanical workhorses that are essential, smoothly transporting fluids needed for many industries. This includes manufacturing, agriculture, energy, and more. Let’s learn the fundamental ideas of industrial pump technology, acting as a primer. It examines the fundamental principles, classifications, and mechanics of these devices. Types Of Pumps There are five types of industrial pumps Read more
Whats New
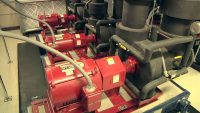
Pumps are mechanical workhorses that are essential, smoothly transporting fluids needed for many industries. This includes manufacturing, agriculture, energy, and more.
Let’s learn the fundamental ideas of industrial pump technology, acting as a primer. It examines the fundamental principles, classifications, and mechanics of these devices.
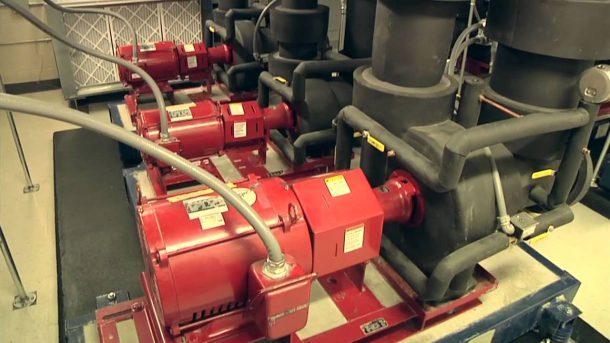
Types Of Pumps
There are five types of industrial pumps (check out Industrial Pumps Texas for more details). They are as follows:
- Centrifugal Pumps: To increase fluid velocity and pressure for uses such as water delivery, wastewater treatment, and HVAC systems, revolving impellers are used.
- Positive Displacement Pumps: Reciprocating or rotating mechanisms are utilized to transfer set amounts of fluid, making them perfect for precision applications in sectors including food processing, oil and gas, and pharmaceuticals.
- Diaphragm Pumps: These pumps are great for handling corrosive, abrasive, or viscous fluids, which are frequently found in chemical processing and sewage applications. They work by using a flexible diaphragm to create fluid movement.
- Gear Pumps: Gear Pumps are widely used in fuel transfer and hydraulic systems, and they work well with high-viscosity fluids by using revolving gears to transfer fluids by displacement.
- Peristaltic Pumps: Their gentle pumping action makes them ideal for delicate pumping tasks in food processing, labs, and pharmaceuticals. They work by using a flexible tube and rollers to generate fluid movement.
Operating Mechanisms
- Suction Phase: The suction phase starts with pump-priming, or generating low pressure, which allows fluid to enter through the suction part.
- Pressurization: It involves the pump’s operation, which uses reciprocating parts or rotating impellers to pressure or shift the fluid inside the pump.
- Pressure Generation: Pressure inside the pump rises as the pump works, giving the fluid energy and allowing it to pass through the discharge port and be used for its intended purpose.
- Fluid Movement: Propelled by the pump’s action, the pressurized or displaced fluid travels through the system, supplying vital fluid transport for a variety of industrial processes, including chemical processing, oil refining, and water supply.
Critical Components
The following crucial parts of industrial pumps are necessary to guarantee their effectiveness and functionality:
- Impellers/Rotors: In centrifugal pumps, these rotating parts give the fluid kinetic energy. This helps in raising the fluid velocity and pressure. To accommodate varied applications and flow requirements, they are available in a variety of designs.
- Casings/Housings: The components are vital for preserving pressure and preventing leaks in the pump system. They guarantee a tight seal between moving parts, guarding against fluid leaks and contamination.
- Seals And Gaskets: These components are vital for preserving pressure and preventing leaks in the pump system. They guarantee a tight seal between moving parts, guarding against fluid leaks and contamination.
- Motors or Drivers: Electric motors, engines, or turbines are examples of power sources that propel the pump‘s motion and supply the energy required for pressurization or fluid displacement.
- Bearings And Shafts: Support systems that reduce friction and guarantee smooth operation by preserving the alignment and stability of rotating parts.
Performance Parameters
The following performance metrics are essential for evaluating the efficacy and efficiency of industrial pumps:
- Flow Rate: This parameter indicates the pump’s capacity and ability to meet necessary demands by measuring the volume of fluid that passes through the pump in a given amount of time.
- Pressure: Pressure represents the force that the pump applies to the fluid; this force is essential for getting the fluid through obstacles in pipelines or other systems and to its final destination.
- Efficiency: Pump efficiency affects system reliability and operating costs. It is the ratio of input energy to output energy. In other words, it is how well the pump transforms energy into fluid power.
- Net Positive Suction Head (NPSH): NPSH shows the pressure margin that can be used to keep the pump from cavitation or creating vapor bubbles, ensuring damage-free operation.
Conclusion
To sum up, industrial pumps are vital components that power various industries in Texas and stimulate the state’s economy. It is essential to comprehend their workings, parts, and performance criteria to maximize productivity in industrial operations throughout the state.
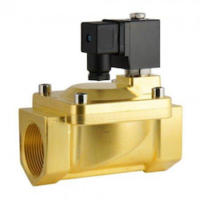
Solenoid valves are crucial components that offer precise and efficient regulation of fluids like water, gas, and air. These versatile devices find applications in various industries, including manufacturing, automotive, medicine, and everyday household appliances. Solenoid valves play a significant role in automating processes, enhancing safety, and improving overall system performance. This article explores solenoid valves Read more
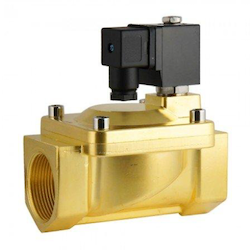
2/2-way solenoid valve
Solenoid valves are crucial components that offer precise and efficient regulation of fluids like water, gas, and air. These versatile devices find applications in various industries, including manufacturing, automotive, medicine, and everyday household appliances. Solenoid valves play a significant role in automating processes, enhancing safety, and improving overall system performance. This article explores solenoid valves, their features, and their types.
What is a solenoid valve?
A solenoid valve is an electromechanical device that operates as a controlled switch for fluid flow. It consists of a coil, often referred to as a solenoid, which generates a magnetic field when energized. This magnetic field acts upon a plunger or a movable core inside the valve, causing it to shift position and either open or close it. When the valve is open, the fluid can flow through the passage; when it’s closed, the flow is blocked.
Features
- Solenoid valves are specifically engineered to handle clean liquids and gases, ensuring optimal performance with these fluids.
- Their precise flow control capabilities make them well-suited for sensitive processes in medical devices and manufacturing, where accurate regulation of fluids or gases is essential.
- One of the key advantages of solenoid valves is their fast response time, enabling quick opening and closing actions. This characteristic is critical for safety applications, allowing for swift reactions to potential hazards.
- Solenoid valves offer a long service life, reducing the need for frequent maintenance and ensuring reliable performance even in demanding usage scenarios.
- The versatility of solenoid valves makes them applicable in a wide range of industries, including water treatment, automotive, and food processing, where their precise control and reliable operation are highly valued.
Working
When an electric current is applied to the coil, it creates a magnetic field that moves the plunger or core. Depending on the valve type and configuration, this movement either opens or closes the valve. The speed and precision of the valve’s operation make it suitable for various control applications, providing an efficient means of regulating fluid flow.
Solenoid valve types
Solenoid valves are classified based on their circuit function, configuration, and mode of operation.
Based on the mode of operation
Solenoid valves can be classified as normally closed (NC) or normally open (NO) based on their default state when not energized. In normally closed valves, the flow is blocked when the solenoid is de-energized, and when it’s energized, the valve opens to allow fluid flow. In normally open valves, the flow is allowed by default when the solenoid is de-energized, and it closes to stop the flow when energized.
Based on configuration
- Direct-acting solenoid Valve: In a direct-acting solenoid valve, the solenoid directly controls the movement of the plunger. When the solenoid is energized, it lifts the plunger, allowing fluid to flow through the valve. These valves are ideal for low-pressure applications and are known for their simplicity and reliability.
- Pilot-operated solenoid valve: Pilot-operated solenoid valves use a two-step process for opening and closing the main valve. When the solenoid is energized, it allows a small amount of fluid to flow, which in turn exerts pressure on a diaphragm or piston, leading to the opening of the main valve. These valves are suitable for high-pressure applications and require less power to operate.
Based on the circuit function
- Two-way solenoid valve: The two-way solenoid valve is the most common type and consists of two ports: an inlet and an outlet. When the solenoid is energized, the plunger or core is pulled, allowing fluid to flow from the inlet to the outlet. Conversely, when the solenoid is de-energized, a spring or other mechanism pushes the plunger back, closing the valve and stopping the flow. Two-way solenoid valves are used in on/off applications and are found in various household appliances like washing machines and dishwashers.
- Three-way solenoid valve: A three-way solenoid valve has three ports: one inlet and two outlets. When energized, the valve directs fluid from the inlet to one of the outlets, and when de-energized, it redirects the flow to the other outlet. This valve type is commonly used in applications where fluid must be diverted between two paths, such as in pneumatic systems or certain medical devices.
- Four-way solenoid valve: As the name suggests, the four-way solenoid valve has four ports: two inlets and two outlets. It is commonly used in applications where the flow needs to be switched between two separate paths, and it allows for bi-directional flow control. Four-way solenoid valves are often employed in hydraulic and pneumatic systems.
Conclusion
Solenoid valves are indispensable devices in fluid control systems, offering precise and rapid control over fluid flow. With their diverse types and configurations, they cater to a wide range of applications in different industries. From household appliances to complex industrial processes, solenoid valves continue to play a critical role in automating and optimizing fluid control. Understanding the different types and how they work enables engineers and designers to select the most appropriate solenoid valve for their specific applications, ensuring efficient and reliable operation.
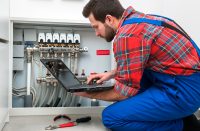
The construction industry is dynamic, fast-paced, and challenging. You’ll need to stay on your game to succeed as a business owner. Construction contracting generally involves working with clients to complete construction projects and sometimes as a sub-contractor helping to fill a smaller niche within a larger job. As such, you may have limited control over Read more
The construction industry is dynamic, fast-paced, and challenging. You’ll need to stay on your game to succeed as a business owner. Construction contracting generally involves working with clients to complete construction projects and sometimes as a sub-contractor helping to fill a smaller niche within a larger job.
As such, you may have limited control over the final scope of the project and how much money you stand to make. Without the right coverage in place, this could leave your business vulnerable. Contracting is a risky business, which is why contractors need protection.
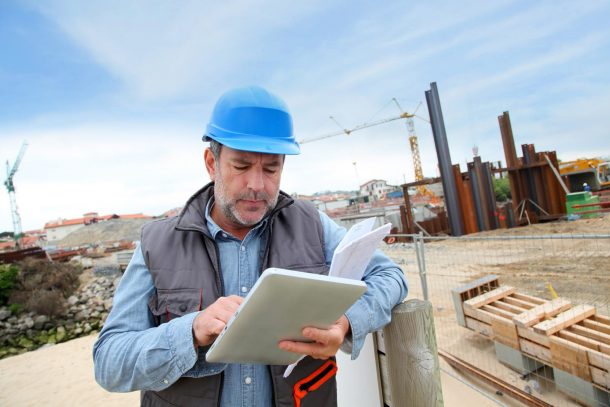
1. Have the Right Insurance in Place
Contractors need to get the right insurance coverage in place before they start working on a project. Without insurance, your business will pay for damages and injuries during work. Make sure you have general liability insurance that covers your business’s operations.
If you are involved in building a new home, you’ll want construction insurance. Homeowners’ insurance will not cover any contractors working on your property. If you own heavy equipment, get the proper insurance for it.
You should also have workers’ compensation insurance and surety bond insurance. This coverage ensures ethical business practices and compliance with building codes. You’ll want to find an insurance company that specializes in contractor insurance.
2. Stay Current on Training and Education
You should seek out training and education opportunities that will help you to improve your business. Don’t just focus on traditional education, but also on staying up to date on the latest technology and best practices.
You can do this by joining industry trade associations. These associations will help you stay connected with other contractors and the latest information; you should also consider taking classes and attending workshops. There are many training and education opportunities available to help build your skills.
Check with your state’s licensing board to see if they offer any training programs. Training and education opportunities can help you improve your time management skills, paperwork processes, and client communication skills.
3. Run a Background Check on Potential Employees
Workers play a critical role in the success of your contracting business. You must maintain a safe work environment; it starts with hiring the best possible employees. You can screen potential employees by conducting a background check.
It will help you gauge an applicant’s character and potential risk to your business. It can also help you avoid hiring somebody who has questionable work history. Make sure to conduct thorough and accurate background checks.
Background check services are available to help you with this process. Also, talk to your insurance company about any coverage they offer for hiring employees. Some insurance companies will provide coverage against negligent hiring.
4. Maintain a Strong Payment System
Contractors rely on getting paid for their work. A strong payment system is essential to keeping cash flowing smoothly. You should have a payment system in place before you start working on a project. Some contractors prefer a payment system that is a percentage of the project’s cost.
Other contractors prefer a fixed-price system. Before you choose a payment method, you need to consider how much experience and expertise you have working on that particular type of project. You should work with your client to establish a payment plan.
You should also create a payment plan that is realistic for your business. Take into account how much work is left to be completed, any costs involved in the project, your employees’ time, and other expenses.
5. Utilize Technology to Stay Protected
Protecting your data, equipment and employees goes beyond a strong payment system. Contractors can use technology to stay protected. Make sure to have a data backup system that protects your information during a disaster.
Modern contracting involves technology, so make sure all your hardware and software are up to date. It includes computers, software, cell phones, and other devices used in your business.
It will help decrease frustration and provide a better experience for your clients. Also, using technology in construction has made it much easier for contractors to stay in contact with their clients.
Conclusion
Much has changed in the construction industry over the years. Technology, insurance, and training are just a few examples. Fortunately, all of these changes have the same underlying theme; better protection for all parties involved. As a contractor, it is important to stay protected and keep up-to-date on industry trends to ensure the longevity of your business.
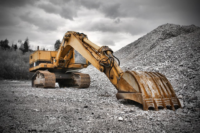
Introduction Construction equipment is a vital component of any construction project. It helps to perform tasks necessary for construction projects, such as moving materials, preparing the soil, and building. You might already know that it’s essential to choose the right equipment when purchasing a new piece of construction equipment. But have you ever thought about Read more
Introduction
Construction equipment is a vital component of any construction project. It helps to perform tasks necessary for construction projects, such as moving materials, preparing the soil, and building. You might already know that it’s essential to choose the right equipment when purchasing a new piece of construction equipment.
But have you ever thought about buying used construction equipment? There are many advantages to buying used over new, including reduced costs, lower operating costs, and increased resale value. This article will share some of the key factors you should consider when purchasing used construction equipment.
Not only can buying used construction equipment save you money on new machine purchases, but it also helps to reduce your carbon footprint and improve the environment because less machinery is being manufactured and transported from other parts of the world. For these reasons, along with many others listed below, now may be an ideal time for people to buy a piece or two of their own!
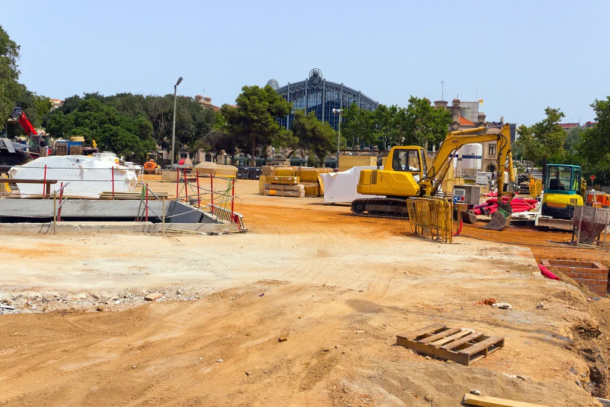
Things you should consider before buying used construction equipment
1. Consider Your Specific Requirements
When you consider buying used construction equipment, the first thing that needs to be done is to understand exactly what type of projects your company performs. This will help narrow down which pieces of equipment have a better fit with your business and make it much easier for you to find the right pieces of equipment.
The more specific your business requirements, the more likely it is that you can find a better fit between what you are looking for and precisely what used construction equipment is available. For trade professionals, this will help you to narrow down what types of machines are needed for your industry.
2. Evaluate the Service History
Once you know what type of equipment your company needs and how specific the requirements are for it, then consider evaluating the service history. This is a very important factor when purchasing used construction equipment as most machines have varying amounts of hours on them.
The older or more utilized some piece of machinery may be, there will obviously be less wear and tear on it which means that if anything does break down in use, you will not need to replace any equipment immediately.
3. Inspect Important Systems
When you buy a house, you check every aspect, such as the window size, wall colors, or the type of flooring, which is made of polished concrete or hardwood. Similarly, before purchasing used construction equipment it is important to do a thorough inspection of the machine in order to ensure that everything will function properly and efficiently.
If something doesn’t work correctly, then this means that your company might need more than one piece of machinery or could even be forced into buying new machines due to a lack of functionality.
It’s because all these factors are so important that most companies like yours would want a closer look at each individual piece before making any final decisions.
4. Consider Operating Hours
Construction equipment that is used frequently can be a great asset to your company in the long run, but if it’s not something you actually need then perhaps this isn’t the best option for you.
If however, most of your operations revolve around heavy-duty machinery such as cranes or excavators, then these machines will require much more maintenance time than those which are less intensive on labor and materials.
In addition to using up resources like fuel oil, these powerful machines will also require frequent repairs and replacements which can often be very costly.
For trade professionals, this can often mean that the longer you own a piece of machinery, the more money it will cost to run. Because of these factors, construction equipment which is used on a regular basis is much more likely to be sold during your first year in operation.
5. Know the Warning Signs
Despite the fact that construction machinery does not need to be taken care of as carefully and diligently as other types of machines, it is still important for you to know what signs can help you determine whether or not a purchase would actually benefit your company.
If there are any loud noises coming from the machine all day long then this might mean something’s wrong. While this may seem like nothing more than normal everyday wear and tear, but in terms of purchasing used equipment, this is a major red flag you should look out for.
6. Choose a Reputable Manufacturer
When you’re buying used construction equipment, make sure that the manufacturer of the unit is reputable. Many companies will not be honest about their machines as well as any problems they may have had with them in order to get rid of them at a reduced price.
This can lead to serious safety issues for both your employees and customers alike which could result in reputations being damaged for years or even decades after the fact.
7. Purchase Through Trusted Dealer
Products used in construction are subject to specific codes and regulations that govern their use. For example, when building a house, it’s essential to use the proper materials, or you could potentially risk giving your customer unsafe products which could harm them.
To avoid these types of problems, we recommend purchasing from a trusted dealer rather than doing an internet search for the best prices. It is essential to buy construction trade professional equipment from the manufacturer or a trusted dealer if you are looking for an affordable and reliable option.
The advantages of buying through an authorized dealer include renting the equipment for a discounted price, having access to service and parts that are readily available, and being confident in the quality of their products.
8. Check the Fluids
The most common problem with used construction equipment is there’s a leak. You must determine how much of the fluid leaks and where it leaked from. You should also note when this happened so you can avoid future problems like that in the first place by ensuring your used machines are maintained properly or replaced if possible.
Some fluids will dry up over time, but some cannot be flushed out to prevent leaking at other places for example transmission lines or bearings, etc. Look for grease on the drive shafts. Many machines do not come with it from the factory, so you know how well maintained your machine is and if there are problems of any kind before it gets to you or yourself.
Many trade professionals recommend using an oil additive and have found that it has greatly improved their machines. If you can’t find a used machine with the fluids intact, they recommend having them flushed out to ensure no leaks are occurring in the first place or from there on out.
Conclusion
Buying used construction equipment can be a daunting task, but it doesn’t have to be. By reading this blog post, you’ll learn how to evaluate a used piece of equipment before buying it and what things you should consider before making your purchase.
A well-loved piece of equipment can often prove to be the most reliable option, so if you are looking for a used construction machine that is used occasionally, then this would be an excellent way to go.
However, we recommend purchasing through a trusted dealer as they will have all of your needs covered and provide consistent quality products that come with warranties. If you are in the market for used construction equipment, we hope that this blog post will help guide you in the right direction!
Move your plumbing and hydronic projects forward with new Uponor products View in your browser Move your plumbing and hydronic projects forward with new Uponor products New products available now ProPEX® EP male threaded adapters Combine the durability of engineered polymer with the reliability of the ProPEX® connection system for a competitive alternative designed for Read more
|