Wichita, Kan. — Viega announces vertical integration of its PEX tubing manufacturing process. The company’s resource consolidation includes producing resin and extruding PEX tubing, which makes Viega the only manufacturer to quality control PEX tubing from the raw-material stage through the finished product. ViegaPEX Ultra tubing, which offers the highest industry ratings for UV exposure Read more
PEX
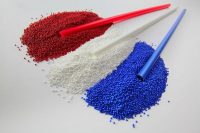
Wichita, Kan. — Viega announces vertical integration of its PEX tubing manufacturing process. The company’s resource consolidation includes producing resin and extruding PEX tubing, which makes Viega the only manufacturer to quality control PEX tubing from the raw-material stage through the finished product.
ViegaPEX Ultra tubing, which offers the highest industry ratings for UV exposure and chlorine resistance, is extruded from Viega’s own resin. This step creates higher quality product that will provide excellent performance and offers increased flexibility compared to tubing made from third-party resins. ViegaPEX Ultra tubing can withstand up to six months of exposure to sunlight without damaging its performance.
The increased flexibility of Viega’s PEX tubing helps installers reduce labor costs and minimize materials costs by needing fewer fittings. This also decreases the potential for leak points in a plumbing system.
“Beyond offering higher UV exposure ratings and cost savings to our customers, making PEX from our own resin increases Viega’s freedom to research product quality,” said Paige Riddle, product manager, Viega. “By controlling the quality of PEX tubing from start to finish, Viega has taken another step in keeping our quality the highest and providing innovative opportunities for our partners.”
Viega has a heritage of manufacturing excellent high-performance products and innovative concepts such as its PEX solutions which include ViegaPEX Ultra tubing, Viega ManaBloc and Viega PEX Press fittings.
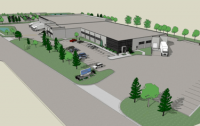
Uponor North America (Uponor) is expanding its manufacturing facility in Apple Valley, Minn. beginning late spring 2015, with completion expected by Dec. 1, 2015. The $18 million investment will be used toward the renovation and expansion of an additional 88,000 square feet to accommodate lean manufacturing and office space, as well as additional manufacturing equipment Read more

The new facility will add an additional 88,000 square feet of manufacturing and office space to support Uponor’s PEX piping business.
Uponor North America (Uponor) is expanding its manufacturing facility in Apple Valley, Minn. beginning late spring 2015, with completion expected by Dec. 1, 2015. The $18 million investment will be used toward the renovation and expansion of an additional 88,000 square feet to accommodate lean manufacturing and office space, as well as additional manufacturing equipment that is required.
Uponor’s North American headquarters are also located in Apple Valley, and the company has a distribution center and resin-processing center located in nearby Lakeville, Minn. By year-end, the total Twin Cities metro area footprint will amount to 654,738 square feet on approximately 50 acres of total property.
The building expansion, in which the company will pursue LEED® certification, is required to meet forecasted growth for its crosslinked polyethylene (PEX) tubing in plumbing, fire sprinkler, radiant heating and cooling and hydronic piping systems used in residential and commercial building.

The new facility, which is located adjacent to the Uponor North America headquarters, consists of a 34,000-square-foot remodel to an existing structure along with a 54,000-square-foot addition.
“It’s a very exciting time in the building industry, especially after the downturn we experienced in the market just a few years ago,” says Bill Gray, Uponor North America president. “We’re seeing significant growth in commercial and residential construction, and this expansion will ensure we match forecasted growth and demand for our PEX systems.”
Uponor CEO and President Jyri Luomakoski adds, “Our North American region has consistently boosted profits and seized market share, both in the residential commercial segments. The team’s success is driven by always doing what’s best for our customers, looking for better ways to perform, innovation, hard work and diligent execution.”
Uponor’s decision to expand again in Apple Valley was partly due to the cooperation of the State of Minnesota and the City of Apple Valley in joining together in providing an attractive incentive package. Uponor has applied for financial support from the City of Apple Valley as well as state assistance from the Minnesota Department of Employment and Economic Development’s Minnesota Job Creation Fund and the Minnesota Investment Fund to assist the expansion.
“Uponor has been an outstanding job creator since opening its North American headquarters in Apple Valley in 1990,” says DEED Commissioner Katie Clark Sieben. “With such a large global presence, we are grateful for the company’s decision to make further investments in Minnesota.”
Apple Valley Mayor Mary Hamann-Roland adds, “I’m honored that Uponor has made a deliberate decision to expand again in Apple Valley. Uponor is a global, innovative partner with their compass focused on a bright future and our shared values for healthy people, planet and a profitable economy.”
Uponor’s physical space is not the only thing that is expanding. They have created more than 130 new jobs in the Twin Cities over the past three years and anticipate adding a significant number of jobs as a result of the manufacturing expansion — contributing toward the economic development in the metro area. Uponor Group employs 4,000 employees worldwide, with about 500 employees located in the Twin Cities.
This year marks Uponor’s 25-year anniversary in Apple Valley. Uponor chose to continue to invest in the Twin Cities because of its location, access to a wealth of talent and the continued support from both the City of Apple Valley and the State of Minnesota.
Gray adds that he is grateful for the City of Apple Valley, the State of Minnesota, the Uponor Board of Directors and Uponor CEO Jyri Luomakoski for their confidence in Uponor North America. “Our success is a result of connecting and building solid relationships with all our partners: the city, the state, our employees, manufacturer representatives, wholesale distributors, builders, architects, contractors and plumbing professionals.”
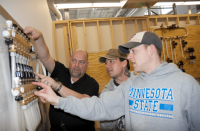
Whether you’re listening to the top of the hour news on the radio while stuck in traffic, reading about the economy online or sitting in your EZ chair at home watching the national news, it’s hard to escape the daily coverage of a sluggish economy. My recent visit to Uponor’s North American headquarters in Apple Read more
Whether you’re listening to the top of the hour news on the radio while stuck in traffic, reading about the economy online or sitting in your EZ chair at home watching the national news, it’s hard to escape the daily coverage of a sluggish economy. My recent visit to Uponor’s North American headquarters in Apple Valley, Minnesota, had me questioning most reports heard via the news media on the topic of job loss and spending holds.
Just last month I made the drive to the southeast Minneapolis suburb of Apple Valley to tour Uponor’s training and manufacturing facility. This world-class facility has been an ever-growing asset to the local economy. Employment numbers have increased by almost one hundred over the last year alone as the growth of product lines [Large diameter PEX-a tubing, fittings and Fire Sprinkler system components] has positioned Uponor to expand its campus for the fifth time since beginning operations in 1990.
The timing of my visit couldn’t have been more perfect as the on-campus training facility was filled with contractors from all over the U.S. Training manager Wes Sisco had a packed classroom of experienced contractors looking to further their knowledge of hydronic heating systems in Wes’ Advanced Hydronics with ADS (Advanced Design Suite Software) course. I sat in on his class for a short time and it didn’t take long to recognize Wes’ ability to engage his students and have everyone participating eagerly as each skill set was covered right down to the smallest detail.

Steve Swanson works with students from the VoTech Radiant Floor Training at Uponor Academy in Apple Valley, MN.
The quality and type of training happening at Uponor is first class. Product knowledge is part of each training session but is presented merely as a solution to a problem scenario studied in class. In today’s highly competitive business market a contractor doesn’t have the time to travel out of town for a two- or three-day trip to hear a sales pitch, and Uponor knows that.
When talking with a plumbing contractor from Massachusetts attending Wes’ class I asked about his experience so far, what was his overall opinion of the program? “This is my second time traveling all the way out here. I attended the Radiant Hydronics with Design class a couple of years ago. It was fabulous, and it got me started in the right direction at a time when I was just starting out in the hydronics business. I couldn’t wait to return and take my training to the next level.”
Right across the hall from Wes and all of his new contractors friends is a state-of-the art, stadium-style classroom where longtime Uponor trainer Steve Swanson holds court as the training instructor for the couple dozen or so contractors in attendance that day for the Radiant Hydronics with Design course. While sitting in on Steve’s class I noticed right away the technology built into the room. On display was complex piping diagram projected on a high definition screen that could be easily seen from each seat.
Classroom time may be the bulk of a contractor’s visit to the Uponor training center but hands-on labs are part of the training program as well. Working controls, manifolds and other system components are at the ready for all to apply what’s learned in the classroom in both the Controls and Applications Labs. The Applications Lab is a specially built rough-framed space for hands-on installation. It is in this space where attendees can actually install radiant tubing, fire sprinkler systems and work with manifold balancing and more.

PEX-a extrusion machines working around the clock to meet the ever-growing demand of Uponor’s product offering.
Plumbing and hydronics product innovation has been the main focus of Uponor for decades. As I toured the manufacturing floor it was immediately apparent that the scale at which Uponor produces their signature PEX-a tubing is indicative of their marketplace position. My tour continued to the quality control lab where countless samples of tubing are tested against numerous industry standards every day. Every time an extrusion machine receives a tool or die change a sample of tubing is taken, logged into an extensive computer system and tests are performed by Mark Usselman and his team of strict quality control engineers. Hydrostatic testing to levels far exceeding the expected operating parameters of each PEX-a sample are performed in addition to highly intensive heat tests in ovens reaching 250 degrees to simulate aging. Usselman takes the quality testing procedures his team performs very seriously, noting the various ASTM, CSA & UL specifications and standards that must be maintained within the Uponor manufacturing process. I can’t help but take him seriously as I watched close up, he cites those industry standards as just the starting point in Uponor’s quality control, stating, “There is an ASTM standard we MUST meet but then there is the Uponor standard. A standard he says keeps their tubing and fitting system at the top of the supply chain for quality.”
My tour concluded as we entered the new 20,000+-square-foot expansion. This expansion space will allow for an additional 17,500 square feet of manufacturing space. Space that will quickly be filled with new state of the art extrusion machines for large diameter commercial PEX-a product. Also in this new addition is 3,000 square feet for an employee services area. The town of Apple Valley, the state of Minnesota and all of the contractors installing Uponor’s products can be proud to have such a world-class American manufacturer, employer and industry innovator keeping jobs here in the United States and actually expanding operations.
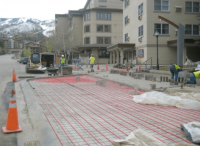
On a late winter afternoon in early 2012, a crowd of 3,000 people gathered at the base of the ski area in Steamboat Springs, Colorado, where a “Promenade” had been completed the previous fall. As the sun dropped low and lifts began shutting down, people popped off skis and boards and wandered over to listen Read more
On a late winter afternoon in early 2012, a crowd of 3,000 people gathered at the base of the ski area in Steamboat Springs, Colorado, where a “Promenade” had been completed the previous fall. As the sun dropped low and lifts began shutting down, people popped off skis and boards and wandered over to listen to live music pouring from a stage, while others gathered around the fire pits and enjoyed after-ski refreshments. Few visitors were aware that beneath the pavers and concrete underfoot, a sophisticated array of pipes and manifolds melted snow and ice in real time, making the evening’s activities possible.

In 2011, just on time for the fall ski season, workers finished laying 112,000 ft (34,138 m) of 5/8 in. RAUPEX® crosslinked polyethylene (PEXa) pipe under more than 70,000 ft2 (6,503 m2) of walkway area. An additional 3,345 ft (1,020 m) of 1 in. through 4 in. REHAU INSULPEX® energy transfer pipe was installed to deliver heat to the complete system from 43 1 1/4 in. PRO-BALANCE® manifolds. The piping was connected to two separate boiler plants, each with a 12 million Btu capacity.
David Young, president of R&H Mechanical, was keen on incorporating the REHAU system from previous experience with it, and estimated that using RAUPEX and INSULPEX saved him hundreds of hours of labor costs as the mechanical contractor on the Promenade project.
“Anytime you use pre-insulated PEX it’s 100 times easier than using pre-insulated steel,” Young said. Also according to Young, it was the ease of installing REHAU’s fittings that provided the majority of time savings in installation. “We might save 40 minutes to an hour on every fitting,” Young said. “On a project this size, that’s big savings.”
The REHAU snow and ice melting system provides additional energy efficiency and environmental benefits in Steamboat as harsher melting agents and heavy equipment are no longer necessary for clearing snow. It has also helped transform an area once characterized by discontinuous sidewalks and dirty snow.
According to Janet Hruby, assistant director of public works for the city of Steamboat Springs, prior to the snow and ice melting system installation guests were required to navigate through significant snow accumulation to get between hotels and restaurants. “Where there were sidewalks, it was a challenge to keep them plowed from morning until late in the evening,” Hruby said.

It was also challenging to figure out where to put all the snow, according to Jim Schneider, vice president of skier services at property owner Steamboat Ski & Resort Corp. “We’d have to plow and put snow on snow, and that gets dirty, and we sometimes had to haul the snow off,” Schneider said.
Although Steamboat Ski & Resort Corp. is still collecting data on the cost savings of the snow and ice melting system versus manual snow removal, according to Schneider the base area redevelopment project might not have been possible without its installation.
“We added 70,000 ft2. That would have been a lot to maintain, to keep the snow off,” Schneider said. “It might have been a decision point for the development.”