https://www.youtube.com/watch?v=8-oEEpWgeNY Read more
Pumps
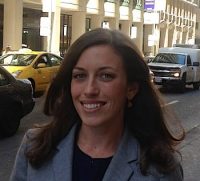
The Department of Energy (DOE) formally proposed the first-ever standards for commercial and industrial pumps, which are projected to produce up to $1.1 billion in net energy bill savings from pumps sold in the next 30 years and are supported by both industry and efficiency advocates. The proposed standards, which were published in today’s Federal Read more
The Department of Energy (DOE) formally proposed the first-ever standards for commercial and industrial pumps, which are projected to produce up to $1.1 billion in net energy bill savings from pumps sold in the next 30 years and are supported by both industry and efficiency advocates.
The proposed standards, which were published in today’s Federal Register, will cover clean water pumps ranging from 1 to 200 horsepower in size, that are generally used in commercial, industrial, agricultural, and municipal applications. Examples include pumps used in agricultural irrigation, building heating and cooling systems, and water treatment plants.
Commercial and industrial pumps and pump systems are responsible for about 0.6 percent of U.S. annual energy use – while this number may sound small, it is significant for a single product category and therefore, improvements in pump efficiency offer potentially large energy savings. The proposed standard is a good step forward in capturing the energy savings opportunity from this important product and is the result of a DOE-led negotiated rulemaking that was comprised of representatives from the pump and motor industries, utilities, and efficiency advocates, including NRDC.
The Savings
Overall, the proposed standards will save about 30 billion kilowatt-hours from pumps sold over the next 30 years, equivalent to the annual electricity use of 2.8 million U.S. households, and result in 16 million metric tons of carbon pollution emissions reductions. For most pump types, life cycle cost savings range from $92 to $173 per pump, with simple paybacks under three years.
These standards are also an important step toward meeting President Obama’s goal of achieving 3 billion metric tons of carbon pollution emissions reductions by 2030. Over 2 billion metric tons are already on the books from standards finalized since 2009. The pump standards would add another 2.5 million metric tons of reductions through 2030, equivalent to the annual emissions from the electricity used by 360,000 homes in one year.
Pumps would be required to meet the new standards four years after the final rule is published, which is expected by the end of 2015.
Required Pump Efficiency
For most pump types, the proposed standards would raise the efficiency floor to remove the worst 25 percent of pumps on the market. The efficiency levels were determined using a similar approach to the EU which involves taking an inventory of the efficiency levels of all the pumps on the market and using this information to create a floor that can be moved up and down to achieve the desired level of efficiency, balancing energy savings, consumer benefits, and manufacturer impacts. The levels agreed on in the negotiations represent a balance of all these factors.
In order to meet the standards, manufacturers can either improve their pump models through hydraulic redesign, polishing, or other design improvements — or choose to drop inefficient pumps from their product line (a manufacturer might make this decision if they have another more efficient model in their line that can meet the same pressure and flow requirements).
The metric for pump standards is called the “Pump Efficiency Index or PEI.” The PEI compares the power consumption of the pump to a reference pump that just meets the standard: a pump that just meets the standard would have a PEI of 1, a pump that is 10% better than the standard would have a PEI of 0.9. The standards would apply to pumps however they are sold: either as a bare pump (just the hydraulic component) or the pump plus motors and controls if present. For pumps sold with motors and controls, the PEI gives credit to motor and control systems (such as variable speed drives, or VSDs) that can reduce the power consumed by the pump when the pump is not operating at full speed. This will help reduce energy even further: currently many pumps systems are controlled using throttling valves on pipes, rather than controlling the speed and flow of the pump. This is analogous to controlling the speed of your car with the brake alone, while keeping your foot fully on the gas. Variable speed drives have the potential to offer significant energy savings in many applications by reducing the pump’s speed and therefore electricity use!
As part of the negotiated agreement, committee members recommended that DOE also initiate rulemakings for circulator pumps (pumps used to circulate water in buildings) and pool pumps, which were not covered in this rulemaking and represent additional opportunities for energy savings. DOE should move forward on these rulemaking to capture these additional energy savings opportunities.
It’s great to see DOE move forward on another efficiency standard that will add to the long history of the DOE standards program delivering benefits to consumers and the environment!
This post originally appeared on NRDC’s Switchboard
Meg Waltner is Manager, Building Energy Policy, San Francisco, Calif. As an energy efficiency advocate at NRDC, Waltner focuses on ways to promote energy efficiency in buildings and appliances in California, at the Federal level,and internationally. Waltner primarily works to advance efficiency through grant programs, tax incentives, buildings energy codes and appliance efficiency standards. She joined NRDC’s DC office in August 2009, after graduating from Stanford with an MS and BS in Civil Engineering, with a focus on efficiency in buildings and renewable energy technologies, and moved to NRDC’s SF office in 2013.
As a native Californian, Waltner grew up hiking in the parks around the Bay Area and in the Sierras and have always loved spending time outdoors. When she’s not in the office, she like to spend my time hiking and camping, going on long runs, cooking new things and being with friends and family.
You can read more blogs from Meg here.
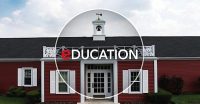
Morton Grove, Ill. — The second-quarter 2015 seminar schedule is now available for Bell & Gossett’s Little Red Schoolhouse in Morton Grove. The training center’s seminars provide systems design training to engineers, wholesalers and contractors in the plumbing and hydronic heating and cooling industries. “Xylem is at the forefront of providing education to current Read more
Morton Grove, Ill. — The second-quarter 2015 seminar schedule is now available for Bell & Gossett’s Little Red Schoolhouse in Morton Grove. The training center’s seminars provide systems design training to engineers, wholesalers and contractors in the plumbing and hydronic heating and cooling industries.
![LRS_education3[1]](http:hydronicshub.com/wp-content/uploads/2015/03/LRS_education31.jpg)
“Xylem is at the forefront of providing education to current and future engineers,” said Larry Konopacz, Manager, Training and Education, Little Red Schoolhouse, Xylem. “Little Red Schoolhouse seminars — whether taken online or in person — equip attendees with the knowledge and confidence to take a systems solutions approach for HVAC and plumbing applications. In an ever-changing industry, education is key to staying on top of new technologies and advancements.”
Online Little Red Schoolhouse
Bell & Gossett’s commitment to education continues with virtual curriculum. At the 2015 AHR Expo, the brand introduced the Online Little Red Schoolhouse — an interactive, self-paced series of free educational courses. This is the first time the iconic pump systems training and educational programming will be available to a global audience via the Internet.
Little Red Schoolhouse second quarter schedule
Modern Hydronic Heating Systems – Basic Seminar* April 20-22
Design & Application of Water Based HVAC Systems Seminar* April 27-29
Service & Maintenance of Water Based HVAC Systems Seminar May 18-20
Modern Hydronic Heating Systems – Basic Seminar* June 1-3
Design & Application of Water Based HVAC Systems Seminar* June 8-10
Large Chilled Water System Design Seminar* June 15-17
* Seminar approved by Green Building Certification Institute to provide credit toward the credential maintenance requirements of the LEED Green Associate and LEED AP certifications.
For continuing education credit information, seminar descriptions, representative information and enrollment, visit www.bellgossett.com/training-education.
To sign up for seminars via the Online Little Red Schoolhouse, visit: http://training.bellgossett.com/.
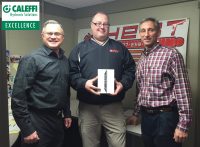
Challenged by an improperly installed heating system resulting in a house that was either above 80° or below 60°F, Joseph Keyes of Heat Tek Heating and Plumbing (Johnson City, N.Y.) was tasked with solving the problem. He first separated the house into four zones. He then created a primary/secondary system using a Caleffi hydraulic separator Read more
Challenged by an improperly installed heating system resulting in a house that was either above 80° or below 60°F, Joseph Keyes of Heat Tek Heating and Plumbing (Johnson City, N.Y.) was tasked with solving the problem. He first separated the house into four zones. He then created a primary/secondary system using a Caleffi hydraulic separator and sized all circulators for precise flow. A Caleffi AutoFill fill valve and QuickSetter balancing valve were also utilized. Not only were the expectations of the home owner AND Mr. Keyes’ himself exceeded, his installation was the January winning entry in the Caleffi Excellence contest.
Heat Tek’s winning entry was determined by most audience votes received during a recently held Coffee with Caleffi webinar. Mr. Keyes was presented with an iPadTM mini by Tom Mahon (Northeast Sales Associates) and Roger Corrente (Caleffi North America). Joe is now a contender for the grand prize: a trip to our global headquarters in Italy. After 12 months, the grand prize winner will be chosen from the 12 monthly winners by a panel of industry experts and Caleffi executives.
It’s not too late to share your design innovation in the Excellence contest. Visit us.caleffiexcellence.com for contest details.

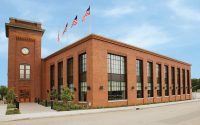
The Taco Innovation and Development Center (IDC), which opened in mid-2012, has been awarded LEED Gold certification by the United States Green Building Council (USGBC). The 24,037-sq.-ft. facility, which houses classrooms and meeting spaces for training and educational purposes, achieved 62 points out of a total of 79 possible points for LEED Gold. Read more
The Taco Innovation and Development Center (IDC), which opened in mid-2012, has been awarded LEED Gold certification by the United States Green Building Council (USGBC). The 24,037-sq.-ft. facility, which houses classrooms and meeting spaces for training and educational purposes, achieved 62 points out of a total of 79 possible points for LEED Gold.

Points were awarded under the following categories: Sustainable Sites (20), Water Efficiency (4), Energy & Atmosphere (15), Materials & Resources (6), Indoor Environmental Quality (10), Innovation & Design Process (5) and Regional Priority Credits (2).
The Taco IDC, in addition to its instructional/educational focus for both Taco employees and HVAC industry professionals who visit the facility, was designed to be a showcase for energy-saving and sustainable products and systems, which are visible throughout the building for close-up viewing, hands-on learning and teaching.
Products and systems installed in the IDC include chilled beams (active and passive), radiant ceiling heating and cooling, fan coils, water-source heat pumps, perimeter radiation, radiant-floor heating, solar hot water, snow melt and geothermal. The mechanical design goal was to optimize hydronic-side design and remove/add as much heat as possible using chilled beams, flat-panel radiation along the IDC’s walls, and radiant floor systems. All equipment and systems are controlled by Taco’s proprietary iWorx Web-based building management product line and monitored by a host of sensors and meters throughout the building.
Taco achieved 15 out of a possible 20 points total in the Energy & Atmosphere category and 8 out of 11 possible points for optimization of energy performance. In fact, the IDC’s operation performance since its opening has exceeded expectations.
The performance of the IDC mechanical and electrical systems are monitored continuously via dedicated measurement and verification systems. Since the building was completed several new measurement stations were added including hydronic BTU metering systems, electrical sub-meters and building automation monitoring systems. These measurement systems have allowed Taco to monitor energy consumption in real time and compare those actual energy measurements against the initial energy model. All indications are that the building is meeting or exceeding the projected energy savings.
For example, during the period from September 1, 2014 to December 31, 2014 the building consumed 126,290 KBTU from the hot water heating system or approximately 150,345 KBTUS of natural gas at 84% boiler efficiency. Taco estimates that this is approximately 75% of the annual gas consumption for heating BTUS. Natural gas consumption prorated for the entire year is approximately 200,460 KBTUS. The energy model predicted that the building would consume 296,900 KBTUS annually. The actual consumption is estimated at 67.5% of the projected consumption. These numbers will be refined as more data is collected.
In considering its LEED application, Taco’s objective was always to implement a system approach to achieving energy efficiency rather than chase individual LEED points. The company wanted to design the most efficient building possible and to see how the design translated into LEED points.
At the time of construction, project manager Chris Integlia, Taco’s executive vice president, said, “Our approach to this project has always been to have LEED certification as a public validation of the efforts we’ve put into the project, and as a confirmation that our products and technologies will help not only Taco but others in our industry achieve highly sustainable green buildings.
“We’re going to do the right things by Taco, and we’ll see how far we can go with that in terms of the LEED scorecard. We do know, however, that the products and technologies we intend to put into the building will achieve a very high level of certification.”
The IDC has been a busy place since it opened and has provided training and education to Taco’s workforce as well as more than 3,000 visitors attending over 50 courses for both residential and commercial training.
The IDC is the second LEED certified project for Taco. In 2009 the company received LEED certification for a new 60,000-sq.-ft. warehouse-distribution center addition to its facility.