RWC is a leading global manufacturer and supplier of premium-branded engineered water delivery, control and optimization products and solutions for residential and commercial plumbing applications and is the premier manufacturer in the world of brass push-to-connect (“PTC”) plumbing fittings. John Guest is a global leader in plastic push-fit fittings and pipe with products distributed worldwide Read more
PVF
RWC is a leading global manufacturer and supplier of premium-branded engineered water delivery, control and optimization products and solutions for residential and commercial plumbing applications and is the premier manufacturer in the world of brass push-to-connect (“PTC”) plumbing fittings.
John Guest is a global leader in plastic push-fit fittings and pipe with products distributed worldwide. The company operates three purpose-built manufacturing facilities in the UK and has a well-established international sales and distribution network. Its product portfolio services three end markets: Plumbing & Heating, Water Quality & Fluid Dispense and Industrial PTC. Its portfolio of well recognized brands includes JG John Guestâ, Speedfitâ, JG ProLockTM, and POLAR CLEANâ.
The acquisition of John Guest is a strong strategic fit and aligns with RWC’s strategy to add complementary products which broaden the solutions offered to end users and expand its market presence, particularly in Europe. The combined business will provide an end-to-end solution with applications from meter to fixture and floor to ceiling from a single manufacturer. The combined product offering will serve to improve end user efficiency by reducing installation times, improve reliability and durability.
Heath Sharp, RWC Chief Executive Officer, said:
“We are excited to bring these two great companies together. Our team is genuinely impressed with John Guest’s people and the culture within the organization. The company comes with a long history of innovation and industry leading execution. John Guest has created strong, well-respected brands that are highly regarded in their key markets globally. They bring innovative, clever products that we believe we can successfully leverage through our wellestablished international distribution network.
“We see alignment between our operations, products, and markets which will bring future growth opportunities for the combined group, particularly in the UK and continental Europe.
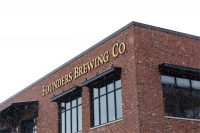
To say that Michiganders take beer brewing seriously is an understatement. The state of Michigan has over 185 craft breweries and even has their own song entitled, “The Michigan State Beer Fight Song.” Many cities in the state offer their own version of pub-crawls and craft brewery tours to give tourists a taste of what Read more
To say that Michiganders take beer brewing seriously is an understatement. The state of Michigan has over 185 craft breweries and even has their own song entitled, “The Michigan State Beer Fight Song.”
Many cities in the state offer their own version of pub-crawls and craft brewery tours to give tourists a taste of what this great state has to offer. One city in particular, is so densely packed with microbreweries; it was named Beer City USA for two years in a row by an annual Beer City USA poll. Beer City USA, otherwise know as Grand Rapids, is home to Founders Brewery.

Approximately 700-ft of Aquatherm Blue pipe was used in 2-in., 3-in., 4-in., and 6-in., sizes for heat reclaim for the 75,000-sq-ft brewery.
Founded in 1997, Founders Brewery has evolved into one of the most recognized breweries in the U.S. The brewery started out as a package brewery and has grown significantly in the past few years. Currently Founders is in restaurants, bars, and stores in 32 states and 13 export markets of distribution. According to Chief Production Officer Brad Stevenson, Founders has averaged over 70% annual growth in the past six years.
With around 300 members of the Founders team, the brewery is making accommodations for the higher demand of its product. “With our growth, we’ve had to buy a lot of new gear,” Stevenson explained. “Most of the new gear has helped us focus on making more product and adding capacity. We’ve now hit a volume that’s allowed us to look at process improvements and other things we’re interested in, like energy conservation.”
Heat Reclaim Process
According to Stevenson, brewing is a very energy intensive process. “We invest an enormous amount of energy and money into heating the product up, and then we turn right around and invest more energy and money into cooling it back down. Anytime we can take that energy that has already been invested in, and port it off to a secondary use, we want to take advantage of doing that. We’ve done that systematically throughout the brewery. We have heat reclaim on our hot side in our brewing system that’s been phenomenal. This was a drive to put heat reclaim in our fermentation process and take the byproduct of fermentation heat and use it to assist in building heat.”
In order to achieve that goal, Stevenson enlisted the help of Seaman’s Mechanical, also located in Grand Rapids, Mich.. CJ Fox, Design Engineer for Seaman’s explained how Aquatherm piping was suggested for use on this project. “The main reason we chose Aquatherm Blue® piping was for the insulating value. We’re sending 120°F degree water out to the chillers or the air handlers, to preheat the air and we want to try to keep as much heat in the pipe as possible. We also needed something that could be washed down.”

The Founders heat reclamation system designed by Seaman’s Mechanical uses heat from the fermentation process to help heat the facility. Seaman’s selected polypropylene-random pipe as an ideal fit for the project because it could handle 120°F degree water while providing an inherent insulation factor and it could also be washed down.
The space is wash-down rated so the pipes need to be easily washed and maintained. Breweries are known for having mold issues and with insulation and other products in the brewing area, there’s always the possibility of mold. “Black piping was out of the question. We were left with using copper pipe, stainless steel pipe or the Aquatherm product. Aquatherm made the most sense to use on this application,” Stevenson added.
Approximately 700-ft of Aquatherm Blue pipe was used in 2-in., 3-in., 4-in., and 6-in., sizes for heat reclaim for the 75,000-sq-ft brewery. According to Brad Strouse, account manager, Seaman’s, Aquatherm pipe was introduced to them by Justin Anes with Columbia Pipe & Supply Co. “We chose this product because of its unique ability to handle the 80-120°F fluid with minimal expansion and contraction. The fusion process was also a significant factor as this ensures structural integrity for an eco-friendly cost.”
Anes provided training on the Aquatherm piping and the team used Aquatherm welding equipment rented from Columbia Pipe & Supply Co. to install the piping.
Strouse explained in further detail the process of the heat recovery system. “We are using rejected heat from water-cooled 100 and 150-ton chillers. The largest cooling load of beer occurs during the initial cool-down period or fermentation period of the beer. This coincides with the highest CO2 emissions as part of the fermentation process, which requires the building HVAC system to supply outdoor/fresh air to reduce the CO2 level. During the heating season, the rejected heat is used to pre-heat the outdoor air creating a very nice balance in transfer of energy.”
“The transfer of energy starts with the initial heating of ingredients using a steam boiler. The heat is absorbed by the beer, and once the beer is transferred to a fermenter tank, the heat is absorbed by the chilled water surrounding the beer, and transfers it to the outdoor air – supplying pre-heated fresh air into the building. This greatly reduces the use of natural gas for heating,” Strouse explained.

Roughly 2,000-ft of Aquatherm Blue Pipe (shown here connecting a flange adapter and a valve that tie into a process water pump) was used to pipe Founders Brewery’s heat reclamation system. Blue Pipe was selected because of its thermal expansion capabilities and also the reliability of the heat fusion process used to connect it.
According to Strouse, the design surpassed the initial energy calculations and ROI of around four years because of the extremely cold Michigan winters. Six-inch George Fischer COOL-FIT® ABS Plus piping was used for the chilled water mains because it comes pre-insulated and is wash-down rated. Two AAON Roof-top units were also utilized on this project.
The team at Founders takes a lot of pride in keeping their brewery clean. “This was the cleanest brewery we’ve ever set foot in,” Strouse explained. “That is what led us to install Aquatherm piping in this facility. It’s wash-down rated and leak free after you install it.” Strouse added that using Aquatherm over copper provided some material savings, though specific figures weren’t available.
“We wanted to make a good business decision and do the right thing (environmentally),” Stevenson added. “With the heat reclaim process and Aquatherm piping, we were able to do both.”
As Founders continues to grow, Aquatherm will be part of their piping plan. In fact, Aquatherm is again being used in the heat reclaim process, this time to connect to three new 190-ton chillers.
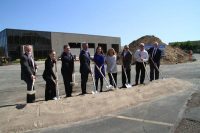
On May 21, Uponor North America (Uponor) held an official groundbreaking ceremony to commemorate the company’s seventh expansion in the greater Twin Cities area. The $18 million expansion project will add an additional 88,000 square feet for lean manufacturing, office space and additional manufacturing equipment for producing crosslinked polyethylene (PEX) pipe used in plumbing, radiant Read more
On May 21, Uponor North America (Uponor) held an official groundbreaking ceremony to commemorate the company’s seventh expansion in the greater Twin Cities area. The $18 million expansion project will add an additional 88,000 square feet for lean manufacturing, office space and additional manufacturing equipment for producing crosslinked polyethylene (PEX) pipe used in plumbing, radiant heating/cooling and fire safety systems.

Political and community leaders celebrate the groundbreaking for Uponor’s new facility in Apple Valley, Minn., which is pursuing LEED®-Silver certification. From left to right: Tom Lawell, Apple Valley City Administrator; Anna Wills, State Representative; Ed Kearney, Apple Valley Chamber President; Bill Gray, President, Uponor North America; Apple Valley Mayor Mary Hamann-Roland; Ruth Grendahl, Apple Valley City Council Member; Clint Hooppaw, Apple Valley City Council Member; John Bergman, Apple Valley City Council Member; Senator Greg Clausen.
“While this is our latest expansion, it is certainly not our last,” said Bill Gray, president, Uponor North America. “This year marks our 25th anniversary in Apple Valley and we are grateful to the leaders of this local community as well as the state of Minnesota for their support as we continue to grow.”
New Facility
Several political and community leaders were in attendance for the groundbreaking ceremony. Apple Valley Mayor Mary Hamman-Roland and Apple Valley Chamber President Ed Kearney took to the podium to talk about Uponor’s partnership with the city and the importance of the expansion to the local economy.
“Our futures are bright because of our partnerships, and businesses like Uponor are key to the strength and growth of our community,” said Mayor Hamann-Roland.
After the expansion is complete, the North American headquarters in Apple Valley along with the company’s distribution center and resin-processing center in nearby Lakeville will bring the total Twin Cities metro area footprint to 654,738 square feet on approximately 50 acres.
The new facility, which is pursuing LEED®-Silver certification, is expected to be complete at the end of 2015 and will provide more than 100 jobs to the local area over the next few years.
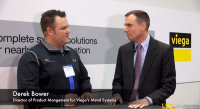
https://youtu.be/gYqjnu6qclo?list=UUy5qVwECeKwWlUhga7bis1w The Hub’s Eric Aune talks with Derek Bower about Viega’s water quality initiative campaign to reduce water stagnation, “dead legs,” and potential harmful bacteria such as Legionella in plumbing systems Read more
https://youtu.be/gYqjnu6qclo?list=UUy5qVwECeKwWlUhga7bis1w
The Hub’s Eric Aune talks with Derek Bower about Viega’s water quality initiative campaign to reduce water stagnation, “dead legs,” and potential harmful bacteria such as Legionella in plumbing systems.
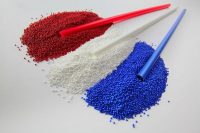
Wichita, Kan. — Viega announces vertical integration of its PEX tubing manufacturing process. The company’s resource consolidation includes producing resin and extruding PEX tubing, which makes Viega the only manufacturer to quality control PEX tubing from the raw-material stage through the finished product. ViegaPEX Ultra tubing, which offers the highest industry ratings for UV exposure Read more
Wichita, Kan. — Viega announces vertical integration of its PEX tubing manufacturing process. The company’s resource consolidation includes producing resin and extruding PEX tubing, which makes Viega the only manufacturer to quality control PEX tubing from the raw-material stage through the finished product.
ViegaPEX Ultra tubing, which offers the highest industry ratings for UV exposure and chlorine resistance, is extruded from Viega’s own resin. This step creates higher quality product that will provide excellent performance and offers increased flexibility compared to tubing made from third-party resins. ViegaPEX Ultra tubing can withstand up to six months of exposure to sunlight without damaging its performance.
The increased flexibility of Viega’s PEX tubing helps installers reduce labor costs and minimize materials costs by needing fewer fittings. This also decreases the potential for leak points in a plumbing system.
“Beyond offering higher UV exposure ratings and cost savings to our customers, making PEX from our own resin increases Viega’s freedom to research product quality,” said Paige Riddle, product manager, Viega. “By controlling the quality of PEX tubing from start to finish, Viega has taken another step in keeping our quality the highest and providing innovative opportunities for our partners.”
Viega has a heritage of manufacturing excellent high-performance products and innovative concepts such as its PEX solutions which include ViegaPEX Ultra tubing, Viega ManaBloc and Viega PEX Press fittings.