Recently, the Mechanical Hub team took part in a two-phase, two-state trip to visit Viega’s North American manufacturing in McPherson, Kansas, and toured the brand new HQ and Seminar Center in Broomfield, Colo. Impressive is the first thing that comes to mind when describing both facilities. The McPherson manufacturing facility exudes the company’s philosophy of Read more
Radiant Cooling
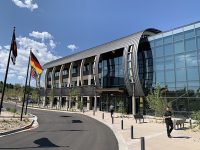
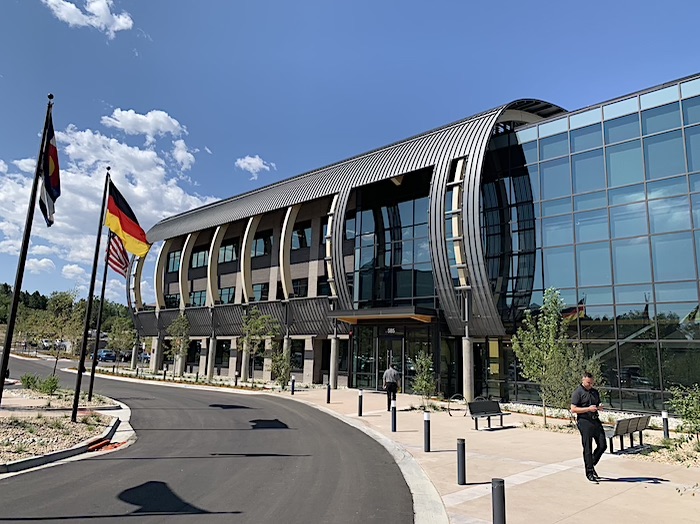
The new Viega North American headquarters in Broomfield, Colo., was designed to look like a fitting.
Recently, the Mechanical Hub team took part in a two-phase, two-state trip to visit Viega’s North American manufacturing in McPherson, Kansas, and toured the brand new HQ and Seminar Center in Broomfield, Colo. Impressive is the first thing that comes to mind when describing both facilities.
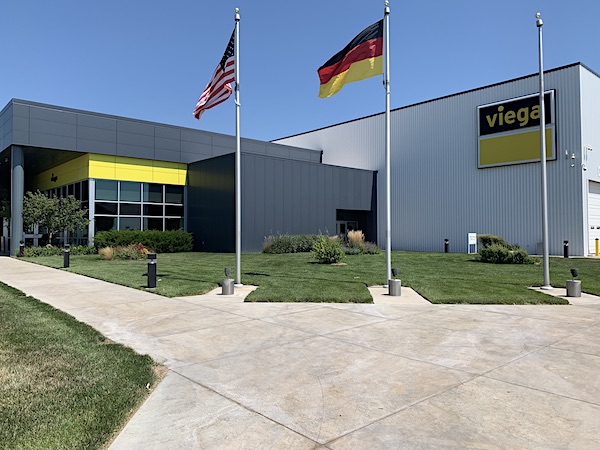
One of the Viega manufacturing facilities in McPherson, Kansas.
The McPherson manufacturing facility exudes the company’s philosophy of both progress and vision for the future. “We are constantly looking past the immediate future and into the distant future,” Eric Wicker, director, manufacturing, Viega.
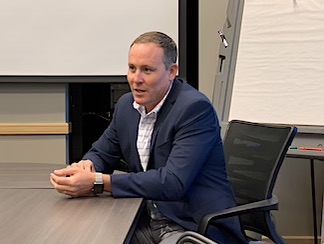
Eric Wicker, director, manufacturing, Viega
This summer, Viega completed a two-year building program in McPherson that included: a 90,000-sq. ft. expansion of a manufacturing plant, completed in Dec. 2017; a new 205,000-sq.-ft. manufacturing plant, completed in June; and a new 25,000-sq.-ft. tool shop and apprentice building, completed in July. And, the company is currently building a 55,000-sq.-ft. logistics expansion—a high-bay storage and retrieval area for inventory.
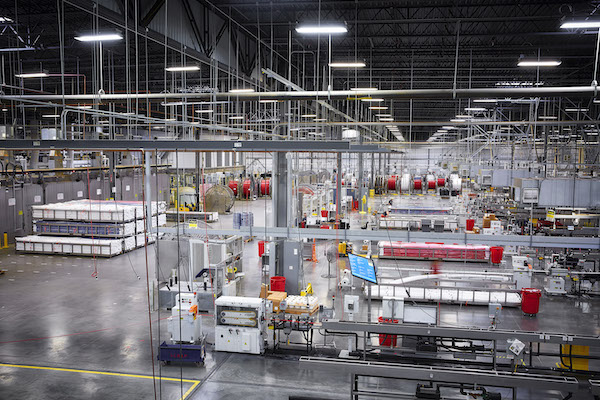
The manufacturing floor at the McPherson facility is as meticulous as it gets.
Mimicking some of the processes from its global HQ in Germany, robotics and machining take center stage throughout the meticulous McPherson plant. Fear not, all of this new-fangled technology is not taking jobs away, rather increasing them. Currently at approximately 300 employees, the company hopes to hit the 500 mark by years ’23-’24.
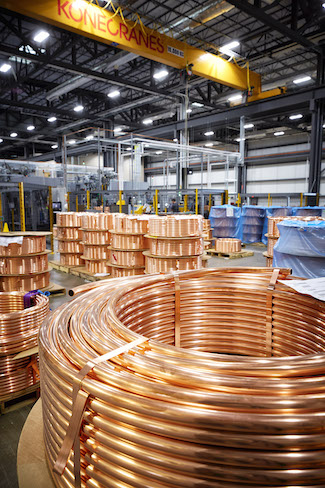
Some of the copper inventory, now produced in the states.
McPherson is where Viega produces its PureFlow line of PEX product, as well as select fittings from the ProPress Copper and 80,000 sq. ft. dedicated to its MegaPress product lines. McPherson is also home to Viega’s master distribution center for North America.
Continued expansion is a testament to the company’s progressive philosophy. For instance, the company has dedicated 270,000 sq. ft. to the copper fitting production. “The goal is to be producing the majority of copper fittings sold in the U.S. right here in the states,” says Wicker.
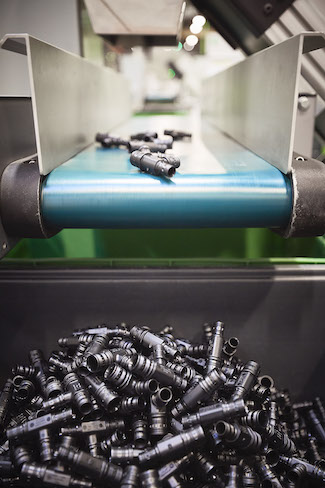
Plastic fittings rolling off the line. Seven million per month made in Kansas.
The state-of-the-art distribution center incorporates the latest technology and automation, as well as an upgraded warehouse management system that provides faster product turnaround. With additional metals products being manufactured in McPherson, a larger distribution center for both metals and PEX products was necessary.
Although media wasn’t allowed to shoot photography inside the plants—understandably—the tour started in the 36,000-sq.-ft. Plastic Injection Molding area which exemplified the company’s high investment in tooling. Twenty machines produce approximately seven million fittings per month. This particular building was well lit and comfortable, due, in part, by the implementation of its own radiant heating and cooling technology.
Quality is never understated at Viega; we strolled through the Quality Assurance Lab where dedicated staff monitor product and equipment through a series of rigorous testing.
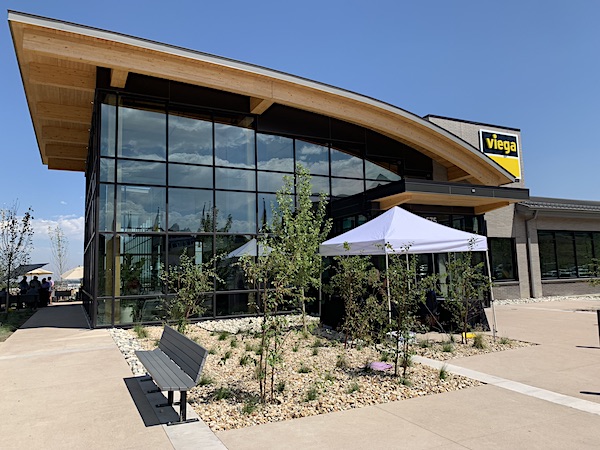
The Broomfield Seminar Center
Next, we toured the 200,000-sq.-ft. Extrusion Area where the plastic piping is made. Once made and exported from Georgia, Viega now produces its own resin—which is transformed into pellets—onsite. The rejected pellets are not repurposed, yet recycled and sold.
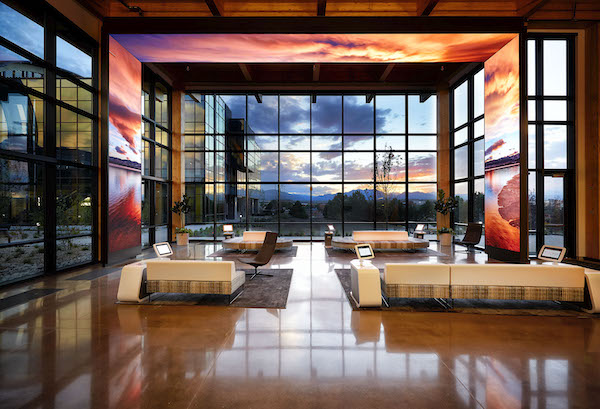
Whoa! Check out the beautiful seminar center, and the frickin’ view!
There is a Special Extrusion Area where plastic metal plastic tubing extrusion is performed. The only company in America making this, the plastic piping is integrated with aluminum so it can better hold its shape rather than returning back to its original form. (Nearby is a 40,000-sq.-ft. dedicated machine shop.)
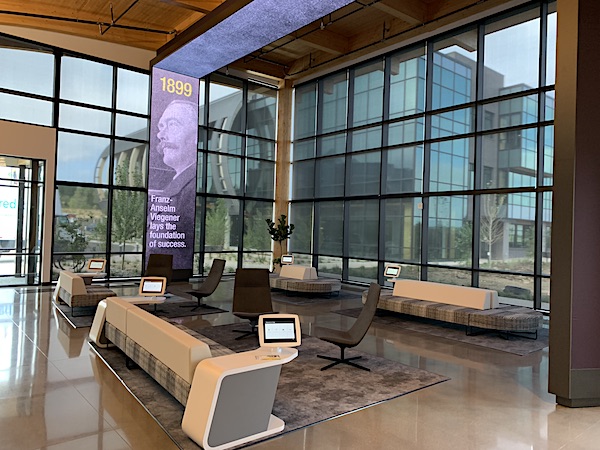
Another angle of the entrance to the seminar center with the HQ in the background.
We then toured the 270,000 sq. ft. of ProPress copper fittings production area and 80,000 sq. ft. of the MegaPress/Metals production area. Strategically, it makes sense for Viega to start producing here in the states. With press technology introduced here in 1999, education and awareness of the process and technology have helped contractors nationwide run a more efficient business. Viega system solutions are designed to work together in plumbing, heating, cooling and pipe joining applications, making the contractor’s work fast, easy and safe.
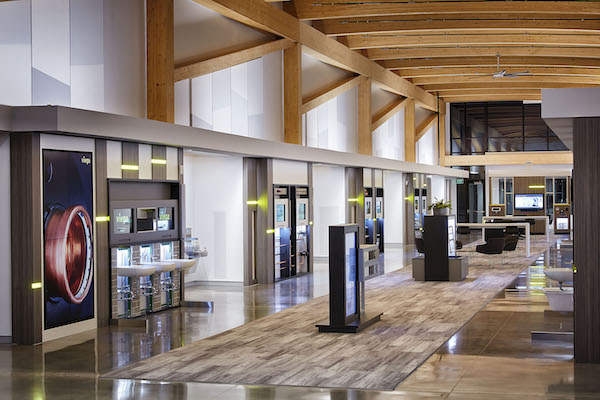
The seminar center features an interactive display area chock full of Viega products.
The following day we were flown to Denver to tour the recently opened Viega North American headquarters and Seminar Center in Broomfield, Colo. The 55,000-sq.-ft. headquarters resembles a pipe fitting, and its interior is the real testament to Viega innovation. I can’t express enough how beautiful these two buildings are, and, of course, amid the breathtaking backdrop of the Rocky Mountains. The HQ building opened in January and the first official training took place April 8, and weekly training is booking fast. “Viega is absolutely committed to its customers and their success in the field,” says Bo DeAngelo, manager, technical training at the center.
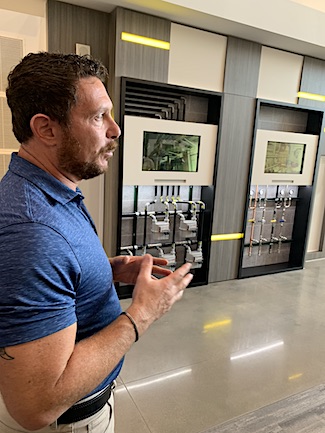
Like a proud new papa, Bo DeAngelo gives the tour of the new seminar center.
Yet, I am always interested: when a new facility is built, does it incorporate its own products? While the cross-laminated timber beams are imported from Austria, the exposed ceilings give employees and visitors a clear view of the many uses of Viega’s innovative technology.
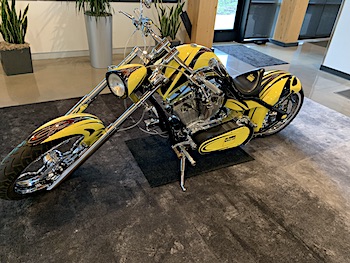
We’ve located the custom Viega chopper! It was taken in the middle of the night from the McPherson facility and relocated to Broomfield where it sits proudly on display. Who has the keys?
Potable water is carried through copper pipes connected with ProPress fittings. The carbon steel fire sprinkler system is joined with MegaPress fittings. Radiant heating and cooling keeps the building comfortable, while a snowmelt system keeps the courtyard free of ice and snow. Manifolds ensure the systems operate smoothly and efficiently. The restrooms feature wall-hung bowls and no exposed tanks, thanks to in-wall carrier systems and Visign style flush plates.
The new 23,000-sq.-ft. Broomfield Seminar Center next door supplements Viega’s Nashua, New Hampshire Seminar Center, which has trained thousands of people since opening in 2006. The new center is an innovative training experience and is equipped with four classrooms, two hands-on labs, and interactive displays throughout, which allows attendees to see, touch and experience Viega products. “Demand for training has been increasing steadily. This facility will allow us to continue to provide and expand on the training that our industry deserves,” says CEO Dave Garlow.
Viega experts lead single- and multi-day classes in everything from radiant system design and fire protection to hydronics and pathogen prevention. Despite being open only since April, it is on track to host more than 2,100 students this year, says DeAngelo.
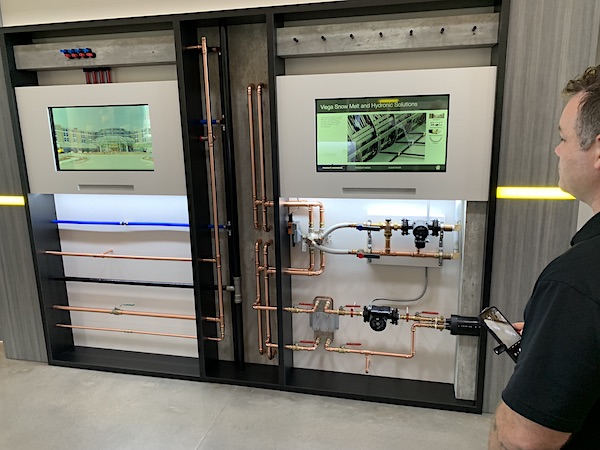
The Hub’s Eric Aune checks out the hydronics and snowmelt display.
I walked away very impressed, telling DeAngelo I—and I’m sure the clients that visit—can’t help but feel energized the minute I walk in this facility. Shaking his head in agreement, “That’s what Dave Garlow tells me every day he walks in here,” responded DeAngelo.
Make no mistake, there is a lot of money, time and resources invested in Viega North America. But it’s a huge testament to the dedication the company believes is its biggest investment: its customers and its employees.
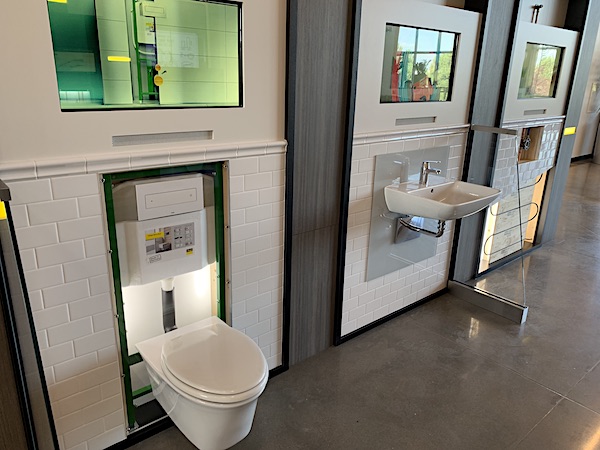
The interactive display at the Broomfield Seminar Center features a breadth of innovative Viega products.

The Wasserman Eye Research Center is a culmination of a 50-year vision to house a world-class research and care center on the UCLA campus to preserve and restore eyesight. With offices in New York and Los Angeles, renowned architectural firm Richard Meier & Partners Architects designed the six-story, 100,000-square-foot Edie and Lew Wasserman building. Completed Read more
The Wasserman Eye Research Center is a culmination of a 50-year vision to house a world-class research and care center on the UCLA campus to preserve and restore eyesight. With offices in New York and Los Angeles, renowned architectural firm Richard Meier & Partners Architects designed the six-story, 100,000-square-foot Edie and Lew Wasserman building. Completed in April 2013, the three lower floors are dedicated to the expansion of the Jules Stein Eye Institute, making it a world-class research and treatment facility.
To accommodate for the Wasserman building, a plan was developed to demolish a seismically deficient portion of the adjacent Semel Institute building. Lead architect Michael Palladino was the principle-in-charge and Tom Goffigon, the project manager, worked closely with the Wasserman Foundation, overseeing the demolition project and design and construction of the new building. With a keen eye to detail, the architects kept sustainability top-of-mind. In fact, the University of California system recently became the first American university to have 100 LEED®-certified facilities – an impressive milestone and a testament to the university system’s dedication to responsible building practices.
Radiant System Takes Load off Forced Air
The first three floors were specified to include radiant heating and cooling, and Uponor was asked to help with design and product guidance. Working closely with Circulating Air, a Los Angeles-based mechanical contractor, Uponor helped design the system in conjunction with engineers and architects.
“The contractor had not worked with Uponor prior to this project so we helped them get trained and comfortable with our system on site,” said Jacob Ford of Keyline Sales, a local Uponor rep firm. “It didn’t take long for them to catch on, and they quickly advanced and found innovative methods to speed up installation.”
According to Ford, the building’s southern facing is a wall of glass, and the radiant heating and cooling system takes a huge load off the forced air system.
The four-man Circulating Air crew worked closely with Keyline Sales to ensure they installed the 16,000 feet of Uponor’s Wirsbo hePEX™ tubing efficiently.
“We were truly amazed at how quickly and easily we installed the piping for the radiant heating and cooling system,” Matt Fitzgerald, Circulating Air job foreman, said. “Receiving training on site really helped us, and our crew felt up-to-speed very quickly.” Also, Fitzgerald said that prior to training he was unaware how easy it was to make the connections to the manifolds and fittings. “I love how fast and easy the system is,” he said.
Uponor’s Wirsbo hePEX tubing uses ProPEX® expansion fittings which require one simple expander tool to make fast, easy connections that hold tight with up to 1,000 pounds of radial force. For contractors familiar with traditional copper or other rigid pipe connections, the ProPEX fitting system is a much easier, more reliable connection method.
The system hooked up to six manifolds and six cabinets divided between the three lower floors. “The installation was fairly straight forward,” Fitzgerald said. “And we didn’t encounter any obstacles that we couldn’t overcome.”
The Wasserman Eye Research Center is a culmination of a 50-year vision to house a world-class research and care center on the UCLA campus to preserve and restore eyesight. With offices in New York and Los Angeles, renowned architectural firm Richard Meier & Partners Architects designed the six-story, 100,000-square-foot Edie and Lew Wasserman building. Completed Read more
The Wasserman Eye Research Center is a culmination of a 50-year vision to house a world-class research and care center on the UCLA campus to preserve and restore eyesight. With offices in New York and Los Angeles, renowned architectural firm Richard Meier & Partners Architects designed the six-story, 100,000-square-foot Edie and Lew Wasserman building. Completed in April 2013, the three lower floors are dedicated to the expansion of the Jules Stein Eye Institute, making it a world-class research and treatment facility.

To accommodate for the Wasserman building, a plan was developed to demolish a seismically deficient portion of the adjacent Semel Institute building. Lead architect Michael Palladino was the principle-in-charge and Tom Goffigon, the project manager, worked closely with the Wasserman Foundation, overseeing the demolition project and design and construction of the new building. With a keen eye to detail, the architects kept sustainability top-of-mind. In fact, the University of California system recently became the first American university to have 100 LEED®-certified facilities – an impressive milestone and a testament to the university system’s dedication to responsible building practices.
Radiant System Takes Load off Forced Air
The first three floors were specified to include radiant heating and cooling, and Uponor was asked to help with design and product guidance. Working closely with Circulating Air, a Los Angeles-based mechanical contractor, Uponor helped design the system in conjunction with engineers and architects.
“The contractor had not worked with Uponor prior to this project so we helped them get trained and comfortable with our system on site,” said Jacob Ford of Keyline Sales, a local Uponor rep firm. “It didn’t take long for them to catch on, and they quickly advanced and found innovative methods to speed up installation.”

According to Ford, the building’s southern facing is a wall of glass, and the radiant heating and cooling system takes a huge load off the forced air system.
The four-man Circulating Air crew worked closely with Keyline Sales to ensure they installed the 16,000 feet of Uponor’s Wirsbo hePEX™ tubing efficiently.
“We were truly amazed at how quickly and easily we installed the piping for the radiant heating and cooling system,” Matt Fitzgerald, Circulating Air job foreman, said. “Receiving training on site really helped us, and our crew felt up-to-speed very quickly.” Also, Fitzgerald said that prior to training he was unaware how easy it was to make the connections to the manifolds and fittings. “I love how fast and easy the system is,” he said.

Uponor’s Wirsbo hePEX tubing uses ProPEX® expansion fittings which require one simple expander tool to make fast, easy connections that hold tight with up to 1,000 pounds of radial force. For contractors familiar with traditional copper or other rigid pipe connections, the ProPEX fitting system is a much easier, more reliable connection method.
The system hooked up to six manifolds and six cabinets divided between the three lower floors. “The installation was fairly straight forward,” Fitzgerald said. “And we didn’t encounter any obstacles that we couldn’t overcome.”
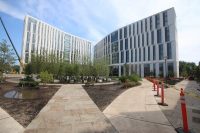
Irving, Tex. — The Plastic Pipe, Inc. (PPI) announced that REHAU has been awarded the PPI Building & Construction Division Project of the Year. The University of Chicago Residence Hall and Dinning Commons used 300,000 feet of REHAU PEX pipe for the hydronic radiant heating and cooling systems in three building that make up with Read more
Irving, Tex. — The Plastic Pipe, Inc. (PPI) announced that REHAU has been awarded the PPI Building & Construction Division Project of the Year. The University of Chicago Residence Hall and Dinning Commons used 300,000 feet of REHAU PEX pipe for the hydronic radiant heating and cooling systems in three building that make up with University’s Residence Hall and Dining Commons.

David Nickelson (r) of REHAU receives the Building & Construction Division Project of the Year from PPI president Tony Radoszewski.
Project of the Year award for the Plastics Pipe Institute’s Building and Construction Division is REHAUThe project is being considered for US Green Building Council LEED Gold certification. Stations of pre-fabricated PEX tubing circuits and manifolds were assembled onsite in centralized locations in order to reduce the installation time and keep up with floor-by-floor construction. The project followed an approach designed to meet Energy Use Intensity (EIU) in the low 50s. The target represents a 41% reduction for energy usage, eliminating 1,920 tons of CO2 emission per year.

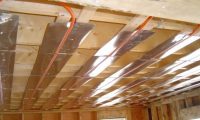
Radiant cooling has been utilized in commercial cooling settings for more than 20 years. A very active, very large airport — Suvarnabhumi International Airport in Thailand — has been successfully using radiant cooling for two decades. Radiant cooling works in much the same way that radiant heating works. Most people who have basements have experienced Read more
Radiant cooling has been utilized in commercial cooling settings for more than 20 years. A very active, very large airport — Suvarnabhumi International Airport in Thailand — has been successfully using radiant cooling for two decades. Radiant cooling works in much the same way that radiant heating works. Most people who have basements have experienced radiant cooling without even being aware of it. In older homes without concrete wall insulation, the ground temperatures below grade dictate the Mean Radiant Temperature (MRT) in a basement setting. When a person walks from upstairs to down into the basement, the body’s sensors sense this lower MRT, and it “feels” cooler than the upper floors, even though the air temperature is nearly the same.
The three major environmental factors that dictate human comfort are MRT, which is the average surface temperature of the surfaces surrounding our bodies, relative humidity, and air temperature. Maintaining all three of these in a radiant cooling application is different than what is required when using a conventional air conditioning system. By lowering the mean radiant temperature and controlling the humidity, good human comfort is achievable for cooling at air temperatures that are significantly higher than we typically see with a conventional air conditioning system. This is because RT is one of the primary factors that dictates human comfort. The air temperature and relative humidity can be perfect, but if the MRT is off in one direction or another most people will be uncomfortable. Control of the relative humidity in a radiantly cooled environment is not just a good idea, it is mandatory in order to avoid the production of condensation on the surfaces of the radiant panel.
Residentially speaking, this requires the use of window and door proximity switches, and if any of these openings are left open no radiant cooling is provided. If humidity is controlled and maintained between 30% and 60%, and the chilled water temperatures are kept between 50 and 70 degrees F, then condensation production is not possible under these conditions. The use of a dew point controller is also a minimum requirement whenever radiant cooling is to be employed.
In commercial settings, rarely are windows operable and doors are always on auto closers, so the production of condensation on the radiant sources is not an issue where humidity is being controlled between 30% and 60%.
In certain areas of the country, it is entirely possible to use the building’s irrigation system during the summer months to provide a coolth source for augmenting the cooling of a given structure utilizing radiant cooling. This will obviously require the addition of heat exchangers and pumps, but still represents a free source of cooling. Another potential source that is being exploited is “Night Sky Re-radiation Cooling.” This requires the placement of unglazed solar collectors on the roof of a dwelling to reject built up heat into the night sky. I have personally witnessed collector absorber temperatures that are as much as 20 degrees F. cooler than the lowest ambient temperature seen for the same period of time.
And, of course, there is always ground source heat pump systems, which have a proven track record of efficiency and reliability. There are some new variations of this age old system bubbling to the surface, and they are showing a huge potential as it pertains to radiant heating and cooling applications. (Thermal Battery Storage systems, for instance.) It is also entirely possible to utilize the ground source vertical bore fields as a cooling source under the right conditions without the need to fire a compressor. Remember, the typical approach temperatures for a radiant panel vary between 50 and 70 degrees F.
Having too much or too little much humidity will also significantly sway the human comfort factors, regardless of what is happening with the MRT and air temperature. In areas of high humidity, it is necessary to maintain the relative humidity between 30% and 60%. This not only provides better human comfort, but also has to do with the control of microbial bacteria, dust mites and preservation of fine wood products. In humid climates, it will be necessary to dry the air out. For make up air units, a method known as DOAS (Dedicated Outdoor Air Systems) is used to wring the humidity out of the incoming air before introducing it into the controlled environment. Internally generated humidity is controlled and removed through the use of refrigerant-based direct expansion dehumidification systems, where the room air is first run across an evaporator coil to remove excess humidity and then the condenser reheats the stream of air. This avoids overcooling the air and creating “cold 70” conditions.
Conversely, in areas with low humidity it may be necessary to introduce humidity into the controlled environment. This can be done with the use of direct evaporative cooling, or direct humidity injection systems. There are even some newer classifications of indirect evaporative cooling systems known as Maisotsenko M-Cycle cooling systems. This type of system uses an indirect heat exchanger to avoid the possible generation of humidity into the conditioned air stream, which in some cases can cause discomfort or mugginess.
In conventionally “air conditioned” systems, there is the need to not only cool down the air, but also to control the relative humidity within the controlled space. At times, the demand for air dehumidification causes the air conditioning system to over cool the air, resulting in more complaints about the air being excessively cold.
In a radiantly cooled controlled environment, the majority of the sensible cooling demand is handled by the control of the MRT surfaces. By allowing the radiant cooling system to handle the majority of the sensible demand, the amount of air movement required to handle the latent (humidity control) demand is significantly smaller. This can result in a significant decrease in cooling energy, resulting in energy savings of 50% or more depending upon the application.
It also opens up more “off peak” ice generation/storage options because the approach temperatures of the water used in radiant cooling systems typically vary between 50 and 70 degrees F. By shifting the electrical and mechanical energy consumption to “off peak” periods, additional monetary savings can be achieved.
Another area that is receiving major attention is the use and application of Phase Change Materials. This method is incorporated into the structure of the building, and in some cases uses free nighttime cooling or off peak electricity to “freeze” the phase change materials. As the materials absorb heat energy, they go through the reverse phase change and “melt,” absorbing significant amounts of thermal energy. They can reduce peak loading by as much as 30% in a hot climate. Although they do not and cannot address the latent energy loads, they do a fantastic job of addressing the sensible loads, which are the biggest load in most commercial buildings. These compounds can be custom tailored to operate at any temperature that is normally used to maintain comfort in a given structure.
Mark Eatherton is the executive director for the Radiant Professionals Alliance (RPA).
References:
http://www.coolerado.com/company/faq/ Indirect evaporative coolers
http://www.phasechange.com/index.php/en/ Phase Change Materials
http://www.solarthermalbiz.com/archives/3710 Night Sky Radiational cooling
http://www.healthyheating.com/Page%2055/Page_55_i_cooling_eq.htm#.VJGsiCcBg Radiant Cooling
http://www.healthyheating.com/solutions.htm#.VJIX7CcBg Comfort Calculator
http://www.aeecenter.org/files/newsletters/ESMS/Sastry.pdf Side by side comparison of radiant cooling versus regular cooling
http://thermalbatterysystems.com/2013/03/22/seasonal-thermal-energy-storage/#.VJIbWCcBg Thermal Battery Storage Systems Inc.