By Kolyn “Coach” Marshall No matter where we go these days it seems as if there’s always someone trying to upsell us on something. Truth is, the art of upsell is nothing new. Walk into a fast food restaurant and you’re asked if you want to super-size it. Go to the theater and you’re asked Read more
Radiant Cooling
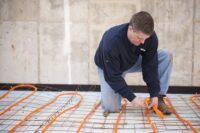
By Kolyn “Coach” Marshall
No matter where we go these days it seems as if there’s always someone trying to upsell us on something.
Truth is, the art of upsell is nothing new. Walk into a fast food restaurant and you’re asked if you want to super-size it. Go to the theater and you’re asked if you want to make your popcorn a combo deal. Heck, even Amazon’s in on the program.
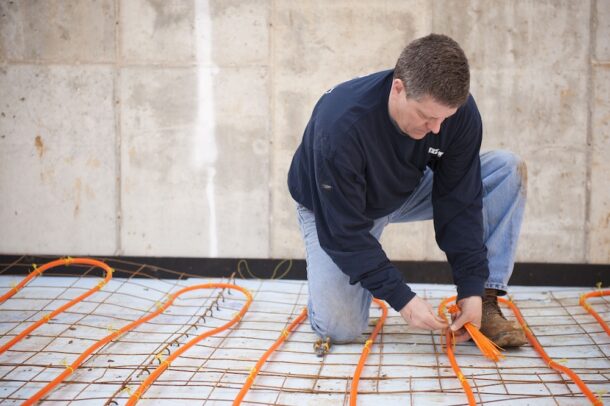
Ubiquitous upsells can be awfully annoying, especially when it’s something you know a lot about. But, what if it’s something you know nothing about? Or, better yet, didn’t know to even ask?
This last question is where I find a lot of potential radiant buyers. They simply don’t know enough about what’s out there to ask.
This is where you—Neighborhood Radiant Installer—come into play.
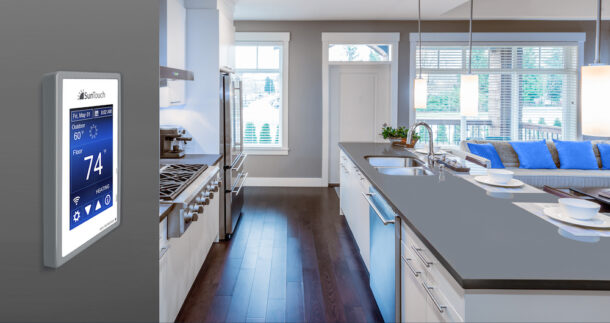
It’s your opportunity to throw out the option of radiant floor heating or snowmelting. Sounds easy, right? Well . . . sort of. In order for you to be able to effectively talk about radiant, it can be helpful to know what there is to talk about.
Understanding the want
Depending on the audience, say, home or a business owner, the want or need may vary. For homeowners, they may want to be more comfortable. There’s a factor of efficiency or cost savings, but those are typically secondary to comfort. People really don’t like being cold.
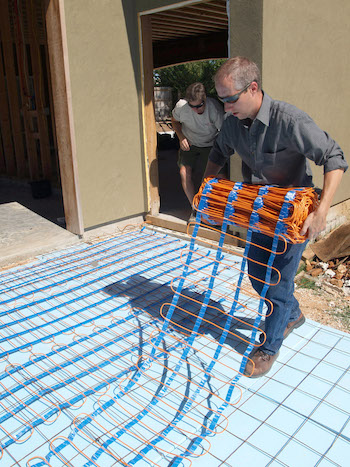
Comfort, however, takes on many forms. But, as the Neighborhood Radiant Installer, it’s important to know what comfort means. One aspect is keeping the room temperature between 68 and 70 degrees. The other facet is knowing how occupants interact with the interior space. The key driver for comfort is floor temperature.
Ever step out of the shower onto a cold tile floor? In that instant it’s pretty easy to connect to what cold is. Oddly enough, our feet dictate our comfort more than air temperature. It’s the main reason why we have slippers and wool socks. If our feet are warm we feel warmer.
So the easiest way to feeling comfortable is to keep the floors from being cold. Radiant heat does that with most radiant systems maintaining a floor temperature between 75 and 85 degrees.
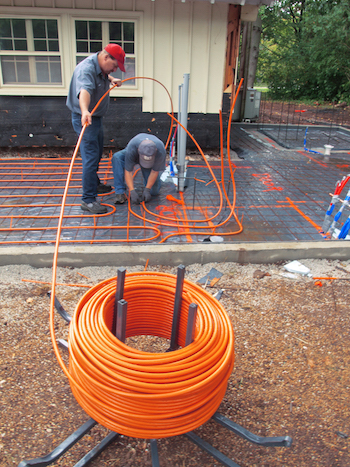
Business owners tend to have a slightly different goal in mind. Their focus is more on customer safety, especially when the weather turns cold and the freezing rain and snow start to fall. Or: employee satisfaction, a great incentive in retaining, and attracting, employees.
As for safety, injuries due to slips and falls plague business owners constantly. It’s a seasonal risk, and source of concern.
Radiant snowmelting systems help keep walkways, parking lots, and access ramps ice and snow free all winter long. This means no more early morning labor; shoveling snow is a thing of the past. No more chemical ice melt. This alone eliminates another key concern: icemelt tends to get picked up by customer’s shoes and tracked inside, eventually taking its toll on the floor.
The upgrade package
So a spark is struck. Warm floors are something that wasn’t expected but is now very much wanted.
How are these once cold floors now warmed? There are two main ways to provide radiant floor heat: hydronically with water, or through electric resistance.
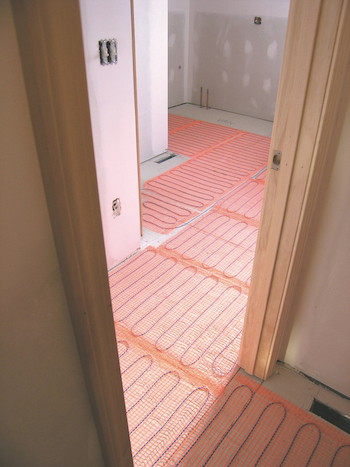
Hydronic systems rely on tubing being installed in the floor and connected to a heat source. Tubing options range from PEX, to PE-RT, to EPDM rubber. Tubing is connected to a series of manifolds, then those manifolds connect to a boiler, or other equivalent heat source.
If the area to be heated is small, say only a kitchen or bathroom, then an electric product may be best; these use electrical resistant wire or cable to generate heat. Wire is embedded in a lightweight concrete or thinset generally under tile or other masonry material. One of the advantages of electric is there is no need for a mechanical room and no need to physically run piping back through a home or facility. Electrical installations tend to be less invasive but also tend to be reserved for smaller areas.
With both electric and hydronic systems there are options for controls and thermostats. Most of today’s systems incorporate some form of connectivity feature, giving remote access to users.
Delivering the Goods
Congratulations Neighborhood Radiant Installer! The Enlightened Customer has decided to go with the radiant upgrade. Now what?
Now it’s time to figure out how to get all those tubes and wires where they’re supposed to go.
Hydronic tubing is generally installed in one of two ways, either in a concrete slab or under a frame floor. In a concrete slab, tubing is typically 6, 9, or 12 inches on center with the tubing approximately 2 inches down from the top. In a frame floor, the tubing is secured to the subfloor, often with heat transfer plates. These plates secure the tubing (usually PEX or PE-RT) to the subfloor while providing good conductive heat transfer to the floor.
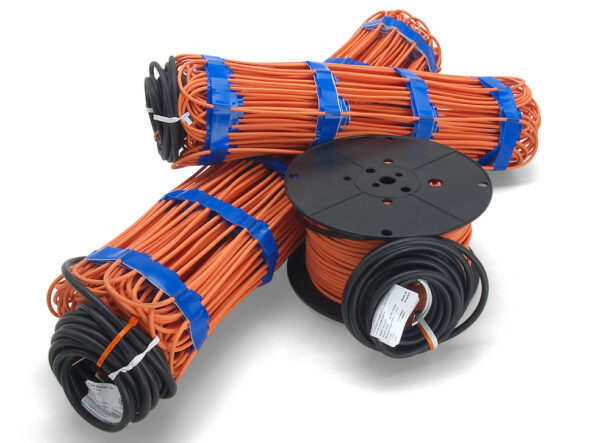
Electric systems are installed in a similar fashion to hydronic slabs with the difference being the wire is generally installed on top of the floor in ½ inch thinset with tile or other stone material as the finished floor covering. An electric system is then connected a controller or thermostat.
Both hydronic and electric systems then operate in the same way any forced air system does. The controller or thermostat is set to the desired temperature and the system operates automatically.
Satisfied Customers
So how does our Neighborhood Radiant Installer know the system is working as expected and the customer is happy? It’s simple: our Honorable Customer won’t be able to stop talking about the most comfortable heat they’ve ever experienced.
Becoming the go-to radiant expert is the best way to keep the future looking warm and bright.
Kolyn “Coach” Marshall, based in Springfield, Mo., is Systems Engineering Manager at Watts Radiant.
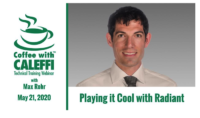
Playing it Cool with Radiant Thursday, May 21, 2020 12 p.m. – 1:00 p.m. CDT Radiant heating is a widely recognized technology, one that’s respected for delivering superior comfort and energy-efficient operation. But what about the ability for radiant cooling solutions? Take good notes! Guest speaker Max Rohr, REHAU Marketing and Academy Manager, will explain the Read more
Playing it Cool with Radiant
Thursday, May 21, 2020
12 p.m. – 1:00 p.m. CDT
Radiant heating is a widely recognized technology, one that’s respected for delivering superior comfort and energy-efficient operation. But what about the ability for radiant cooling solutions? Take good notes! Guest speaker Max Rohr, REHAU Marketing and Academy Manager, will explain the physics of absorbing heat energy through a network of pipes and discuss application considerations for an energy efficient system design for radiant cooling.
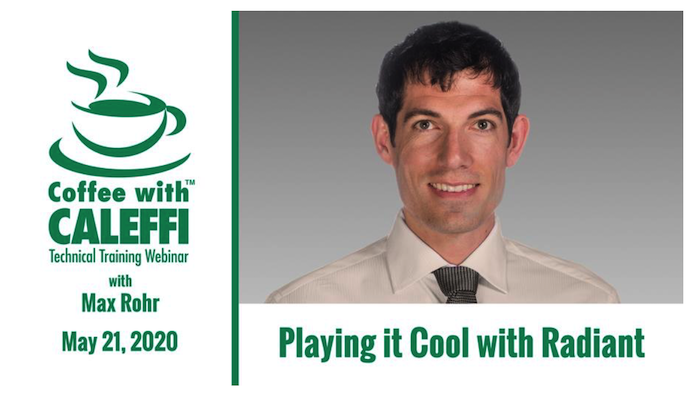
You’ll learn:
→ Is comfort a number on a thermostat? Do designers have more or less more control options?
→ Why are hybrid radiant/forced-air systems the best way to handle sensible and latent loads?
→ Condensation?! No sweat. How do you avoid condensation in a radiant cooling system?
→ What is the most humid U.S. city with a radiant cooling project?
→ What inputs does your control system need to operate a radiant cooling system?
→ What are the most common installation types for radiant cooling projects?
Max Rohr is a graduate of the University of Utah. He currently serves as REHAU Academy Manager (Leesburg, Va.). Max is a self-described hydronics and thermostat nerd. He has worked in the hydronics and solar industries for 20 years (or however many years Hot Rod is willing to admit to the Division of Child Labor) in the installation, sales and manufacturing sectors.
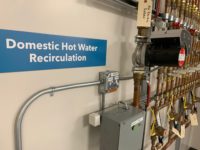
Hydronic systems outperform VRF, study finds In a study commissioned by Xylem Inc. that evaluated HVAC systems in a number of South Carolina school buildings, hydronic systems outperformed all other systems, including VRF, in terms of lower energy use, cost and life expectancy, by as much as 24%. “With HVAC systems dictating a substantial amount Read more
Hydronic systems outperform VRF, study finds
In a study commissioned by Xylem Inc. that evaluated HVAC systems in a number of South Carolina school buildings, hydronic systems outperformed all other systems, including VRF, in terms of lower energy use, cost and life expectancy, by as much as 24%.
“With HVAC systems dictating a substantial amount of the overall energy use of commercial buildings, the results shed light on the importance of evaluating varying system-to-system costs before installation,” said Kyle DelPiano, Business Development Director, CBS Market, Xylem. “More than ever, energy-efficient practices are driving the construction industry toward more sustainable solutions, and this study proves long-term cost savings that can’t be overlooked when making the choice between hydronic and VRF systems.”
To compare and contrast HVAC systems according to their 30-year life-cycle cost analysis (LCCA), the Xylem study analyzed seven elementary and middle schools located in South Carolina Climate Zone 3A, a humid, warm climate. The cost analysis included upfront installed cost, replacement cost allocations and ongoing energy and maintenance cost of the following system types:
- Variable refrigerant flow heat pumps (VRF)
- Water source heat pumps (WSHP)
- Ground source heat pumps (GSHP)
- Direct expansion rooftop units (DX RTU)
- Water cooled chillers (WCC)
- Air-Cooled Chillers (ACC)
The findings of the study revealed that the schools with WSHP, GSHP and WCC systems displayed energy use levels that were 30%, 41% and 25% better than the national median for elementary and middle schools, respectively. The replacement cost allocation also acknowledged that the tested hydronic systems operate effectively for approximately 25 years, as opposed to the 15-year replacement estimation for VRF systems.
The tested VRF systems required replacement a decade earlier because of their tendency to work harder during heating cycles, bringing proof of long-term cost savings to the forefront of the conversation surrounding sustainability and hydronic HVAC system efficiency.
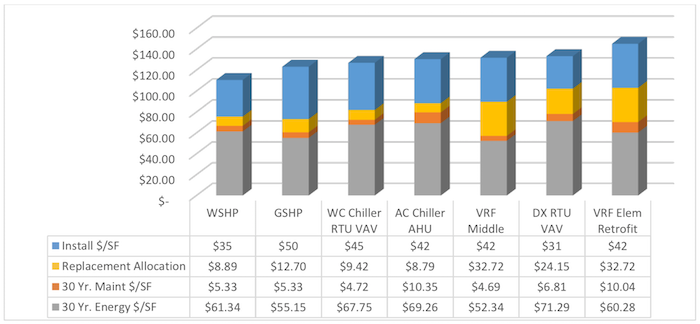
Replacement allocations had an impact on the life-cycle cost analysis (see yellow bars) and drastically reduced the cost effectiveness of equipment with 15-year life expectancies.
Considerable benefits of the hydronic HVAC systems included lower energy usage intensity and cost, wider range of maintenance flexibility and longer life expectancy.
The full research study can be found here: https://bit.ly/35AtpXb. For more information about Xylem, visit www.xylem.com.
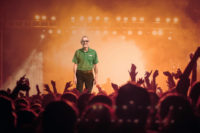
For the past 11 years, my job as a technical trainer has taken me from Alaska to Cuba, with many stops in between—I have been to all 50 states. Transitioning from a hands-on plumber to a talking head, standing in the front of the room addressing thirsty-for-knowledge contractors, took some getting used to. No doubt Read more
For the past 11 years, my job as a technical trainer has taken me from Alaska to Cuba, with many stops in between—I have been to all 50 states. Transitioning from a hands-on plumber to a talking head, standing in the front of the room addressing thirsty-for-knowledge contractors, took some getting used to.
No doubt the travel part of a “traveling trainer” job is the most challenging. Hours spent squeezed inside an aluminum sausage, aka big, old jet-airliner, can be frustrating. I do love the views and amazing sunset and sunrises I have seen. Lightning show, massive clouds are incredible, but they never look the same on the phone camera. For the most part the airline folks have been helpful and accommodating.
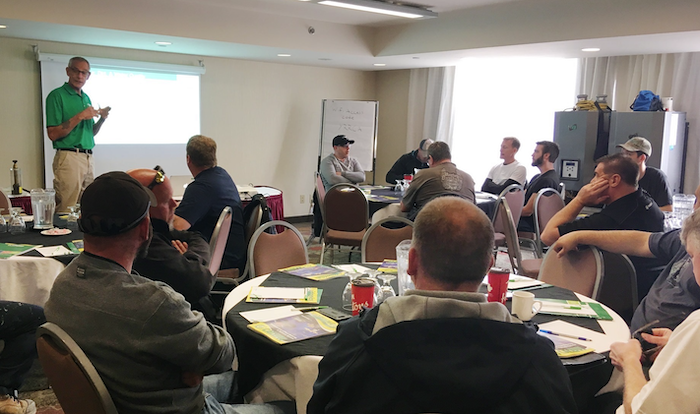
When they see the miles you rack up as a business traveler, they will almost always accommodate your request. Approaching them without a chip on your shoulder helps the outcome. Maybe it’s me, but it seems like a lot more delays and cancelations lately, busy times in the air travel business. So, I usually plan for some shuffling and exercise some chill skills. But I digress.
Once at the location, the fun part begins for me. I enjoy sharing what I have learned and listening to stories from attendees. For sure, my favorite parts of the job are the shop and jobsite visits. I learn from seeing how the new products and technology are actually being blended together on actual jobs. Browsing through the back rooms of the wholesaler and rep buildings can provide some good intel.
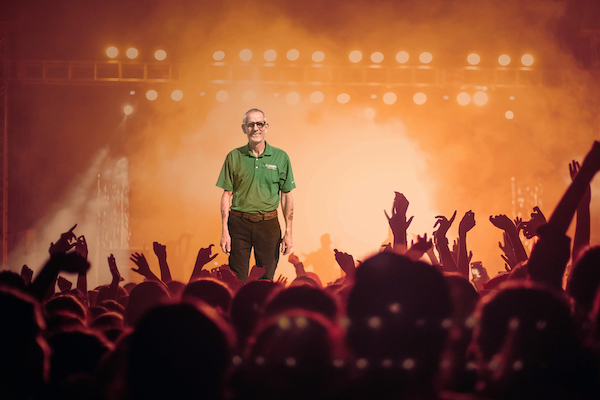
Living the Rock Star life.
I try to balance my training between product pitch and theory, applications, tips and tricks. It is important that the training sponsors advertise and promote the training accurately. If the training is intended to be all product and sales, that needs to be clear, so the folks attending know what to expect. Technical guys and gals prefer technical topics, from my experience.
I try to engage the group as much as possible, learn their skill level and expected outcome. Training for me is a give and take experience, as nobody knows it all. Except perhaps my wife. (Shhhh!) Generally, the room is a mix of expertise levels, so try to include info for everyone to leave with. Know your audience!
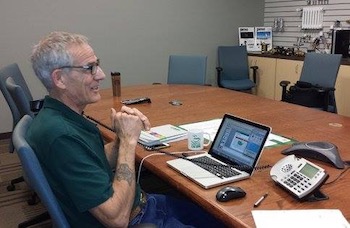
Hot Rod preparing for a Coffee with Caleffi webinar.
The dynamics of a room vary depending on the group. If you have a roomful of competitors, the questions do not flow so easily. Training at shops, reps and wholesalers always result in more interaction.
During the lunch break, spring for some food for the group, even if it is good pizza. Shop for the local brand favorite.
I’ve found a 4-hour maximum for tech heavy topics is a good lid for an event. It’s tough to keep a blue-collar person down as they need to keep moving. Their backs and knees make sitting for a long time challenging, too.
I always want to leave the attendees with a nice hard copy of the material we covered. The Caleffi Idronics are perfect handouts: They are a reference, both as a hard copy and online version. Also, it’s always nice to see the group taking notes in the margins.
Back at the office—in-house—I help produce the Coffee with Caleffi series, a webinar that cover important topics in the plumbing and hydronics industry.
If we haven’t met or shared a gab session together, I hope to do so soon. I’ll keep in communication with the Mechanical Hub community about dates and times for upcoming seminars, and webinars!
Bob ‘Hot Rod’ Rohr is director of training and education at Caleffi.
More speakers, more topics, plus a sold-out trade show The Canadian Hydronics Conference (CHC2019) opens in Ottawa, Canada in just four weeks (September 24-25). The two-day conference includes a sold-out trade show and is attracting contractors, wholesalers and engineers from across Canada. The Conference is presented for the industry by the Canadian Hydronics Council (CHC) Read more
More speakers, more topics, plus a sold-out trade show
The Canadian Hydronics Conference (CHC2019) opens in Ottawa, Canada in just four weeks (September 24-25). The two-day conference includes a sold-out trade show and is attracting contractors, wholesalers and engineers from across Canada. The Conference is presented for the industry by the Canadian Hydronics Council (CHC), a council of the Canadian Institute of Plumbing & Heating. CHC has be representing Canada’s hydronics (modern hot water heating) industry for more than 40 years.
“With 20 presenters from across Canada and the U.S. it’s an exciting program”, stated Conference Co-Chair Mike Wills of Wolseley Canada. “Whether you are a seasoned pro or newer to the industry, CHC2019 will give you the technical training, business insights, product information and industry contacts you need to succeed”.
“It’s going to be an incredible opportunity to meet North America’s leading hydronics industry leaders”, added Conference Co-Chair Dave Harrison of Jess-Don Dunford Limited. “It’s also a fantastic way to meet other industry members from across Canada and share ideas”.
CIPH Chairman of the Board Andrew Dyck of Barclay Sales Ltd. along with the Canadian Hydronics Council Chairman Dave Hughes will attend the conference and present the 2019 Canadian Hydronics Council Award of Merit. The award recognizes an individual for their significant contributions over a lifetime to the Canadian hydronics industry; it is the hydronics industry’s highest honor. The presentation will take place at 1:30 pm on Wednesday, September 25.
For complete details about the Canadian Hydronics Conference and registration information, visit www.ciph.com/CHC2019 or email info@ciph.com.
Previous CHC Award of Merit Recipients
2018
Barry Cunningham, General Manager, Triangle Supply Ltd. (a division of Bartle & Gibson Co. Ltd.)
Kenneth Webster, formerly Director, Sales & Marketing, Viessmann Manufacturing Company Inc. (retired)
2017
Richard Peck, Vice President, Slant/Fin Ltd.
2014
Roy Collver, Contributing Editor – Hydronics, Plumbing & HVAC Magazine
Harald Prell, President, Viessmann Manufacturing Company Inc. (Canada)
2013
John Goshulak, Vice President, Sales and Marketing, Weil-McLain Canada Sales Inc.